Embsay WTW (2024)
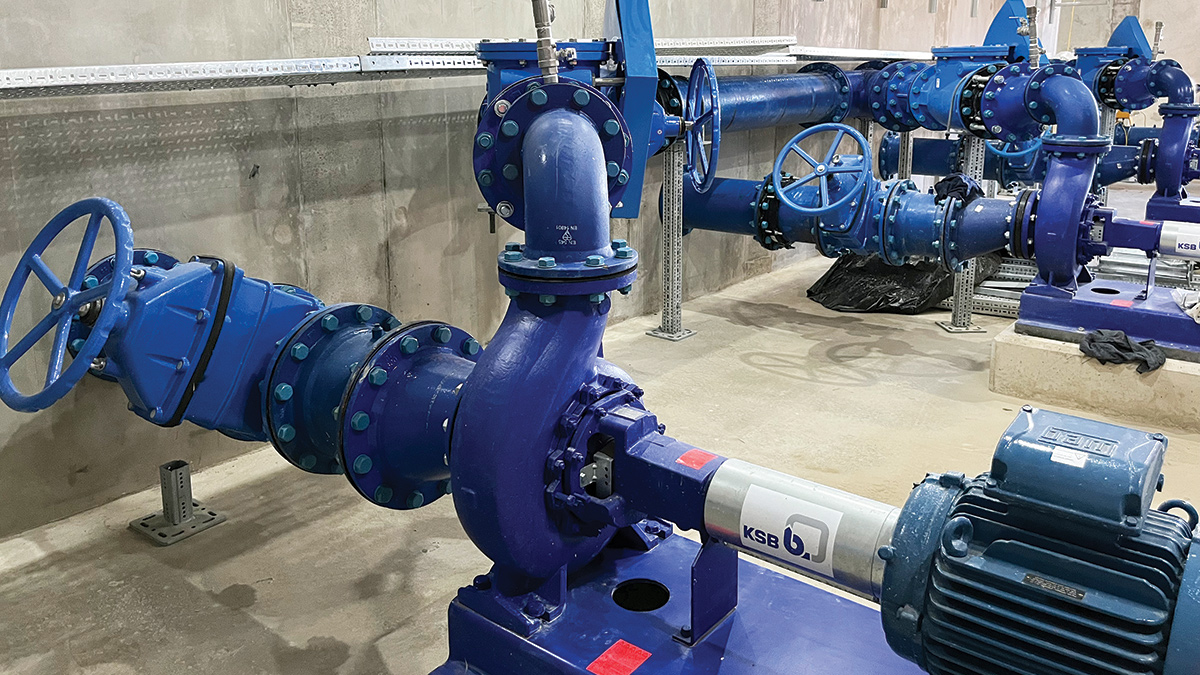
Clean backwash pumping station - Courtesy of Mott MacDonald Bentley
Embsay Water Treatment Works is a standalone 24 ML/d water treatment works operated by Yorkshire Water (YW) and located in the Yorkshire Dales National Park, providing clean water to over 15,000 people in Skipton and surrounding areas. The existing works comprises of clarifiers, rapid gravity filters and a chlorine contact tank with associated chemical dosing. The project scope was to address risks to drinking water quality associated with manganese, Cryptosporidium and disinfection by-products to secure a resilient and reliable supply of clean water. The project team ensured these solutions were affordable by implementing value engineering based upon PAS2080 design principles.
Scope of works
The outline solution brought forward to address these risks was to construct a new interstage pumping station to pump process water downstream of the site’s existing rapid gravity filters, to a new set of five manganese filters. Flow would then gravitate to a new contact tank which would then reconnect to the existing site upstream of the site’s service reservoirs.
A start-up-to-waste facility was also to be constructed to improve the site’s operational flexibility when returning into service following any shut-down events. This would enable site process water to run to a large storage tank for a period of time to ensure water quality is within parameters prior to bringing water back into service.
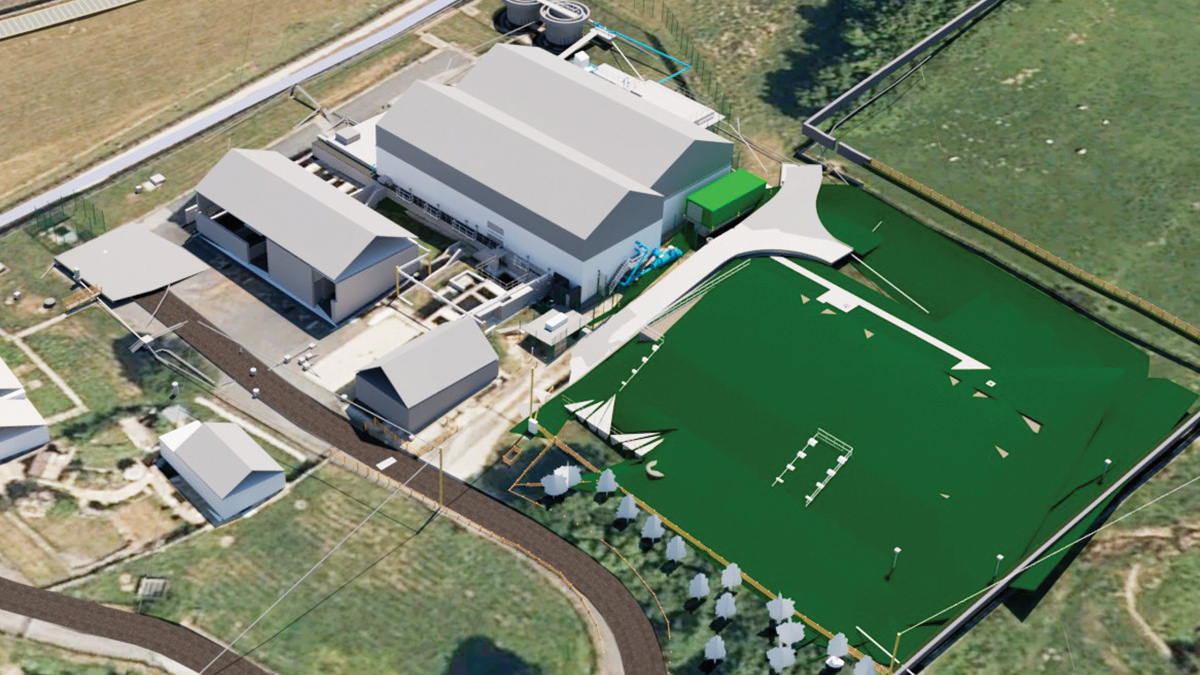
Embsay WTW site layout render – Courtesy of Mott MacDonald Bentley
Build nothing
Manganese contactors were required as part of the outline design to address an upward trend of raw water deterioration in historic data. However, the five years following this, treated water levels had seen an improvement which was attributable to wider ongoing catchment-based solutions Yorkshire Water had undertaken. In addition, the average data for manganese at 5 ug/l remained significantly below the regulatory requirements of 50 ug/l.
The manganese contactor’s secondary purpose was to reduce the generation of disinfection by-products as it enabled chlorine to be dosed at a point with lower levels of organic particles. Further investigations identified several process changes which would enable chlorine dosing levels to be reduced. These included:
- Addition of a rinse stage to the rapid gravity filters backwash cycle to prevent water with higher turbidity immediately following a backwash from going forward into supply. This also had the added benefit of reducing the risk of Cryptosporidium, which is able to escape chlorine in high turbidity environments.
- Addition of a rapid gravity filter outlet monitoring point to enable the chlorine dosing upstream of the sites rapid gravity filters to be optimised.
These considerations were used to build a proposal to the drinking water inspectorate to not build new manganese contactors and instead implement the above process optimisations to the existing plant.
The no build solution for manganese contactors also enabled the site hydraulics to be redesigned to remove requirements for an interstage pumping station and instead gravity feed the proposed new structures. A further benefit to the removal of manganese contactors was that this reduced the quantities of wastewater the site would generate. This meant a dedicated dirty washwater removal facility did not need to be constructed.
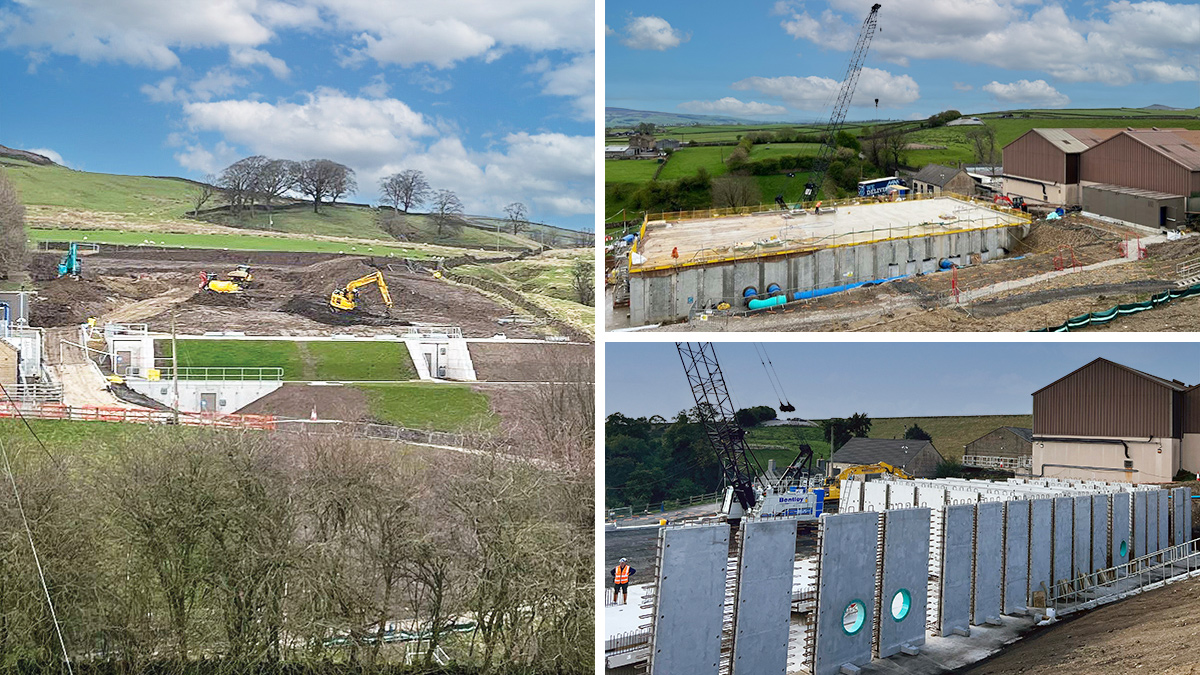
(left) Final backfilling and reinstatement, (top right) main structures under construction and (bottom right) precast concrete contact tank construction – Courtesy of Mott MacDonald Bentley
Build less
The outline design proposed a 3000m3 structure for startup-to-waste on the basis that this would provide three hours of storage at the site’s average flow rate. Further investigations concluded that these parameters could be reduced to two hours storage at the site startup flow of 8.64 Ml/d which would reduce the required structures working volume to 600m3.
This reduction in size also enabled the sites existing contact tank, which was to be decommissioned as part of this scheme, to be re-purposed as a startup-to-waste facility. Negating the requirement to build a new structure.
Build clever
- The contact tank remained essential to meeting the schemes DWI obligations. However, optimisations were made to reduce its carbon impact.
- A carbon calculator was used to compare the whole life carbon impact of the structure and was found to be lower than alternatives such as UV and HDPE tubular tanks due to site specific constraints and planning requirements.
- Precast concrete from FLI Precast Solutions and Flood Precast has been used instead of in situ concrete to ensure efficient and safe construction.
- The structure was designed with three compartments reducing the overall footprint by 25% in comparison to a more conventional two compartment tank.
- Design of the new contact tank, clean backwash tank and dry well was incorporated as a single structure, minimising excavation and simplifying the build sequence.
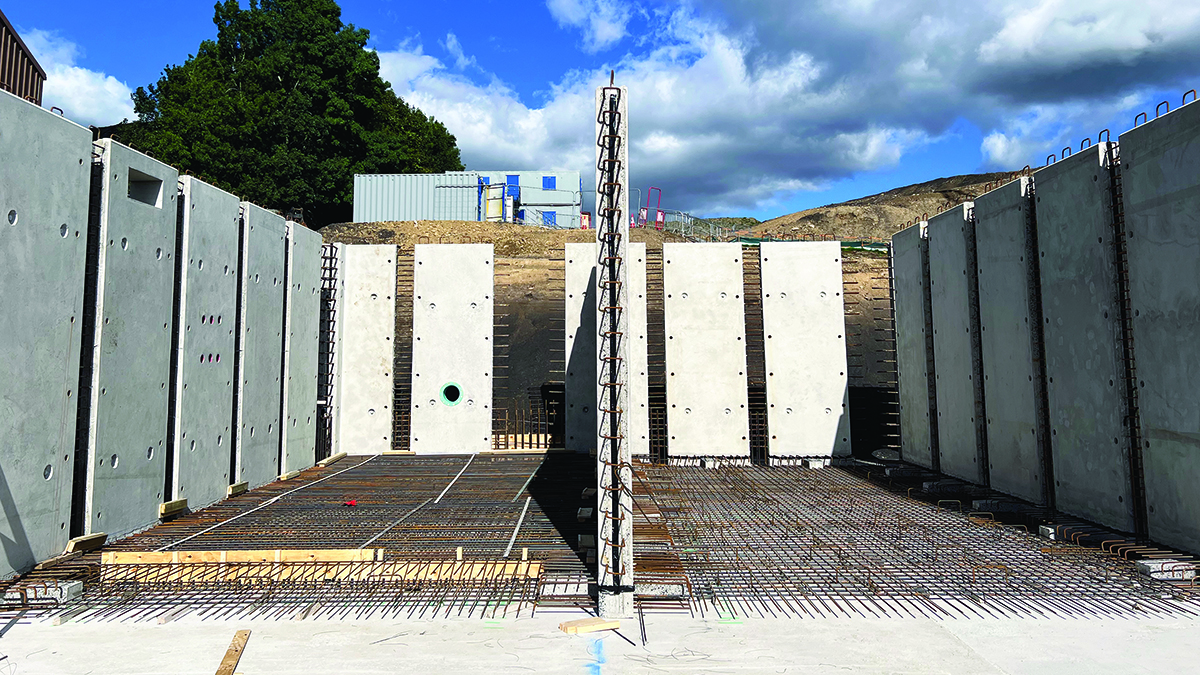
Backwash tank and pumping station construction – Courtesy of Mott MacDonald Bentley
Embsay WTW: Supply chain – key participants
- Client: Yorkshire Water
- Principal designer & contractor: Mott MacDonald Bentley
- Precast concrete (PCC) contact tank & dosing chamber design/supplier: FLI Precast Solutions
- PCC contact tank roof design/supplier: Flood Precast
- MCC & software integration: Total Automation & Power
- Mechanical installation: Alpha Plus Ltd
- Mechanical installation: NPS Engineering Group
- Electrical installation: Circle Control & Design Systems Ltd
- Mechanical decommissioning: STAL (UK) Ltd
- Run to waste & clean backwash pumps: KSB Ltd
- Motors/drives: WEG
- Metalwork: JHT Fabrications
- Waterproofing: Stonbury
- Pipework: George Green (Keighley) Ltd
- Pipework: Electrosteel Castings (UK) Ltd
- Static mixers: Statiflo
- Kiosks & access points: Technocover Ltd
- Generators: Central Power Services
- Fencing: Burn Fencing
Digital delivery
The project team implemented 4D modelling using SYNCHRO at tender design phase. By integrating the time element of the project with the 3D Revit model, the team were able to visualise the construction sequence prior to starting on site to optimise the programme logic, identify any potential issues and improve communication.
For example, the structure was initially planned to be constructed from left to right, with tanks completed in pairs, due to the reach of the proposed crawler crane.
By re-working various options, the team identified a six-week saving on critical path by constructing the back half of the structure completely before pulling the crane forward to finish all tanks off. As this was conducted at tender stage, the saving was passed back to the client.
It also provided a visual explanation of key site operational interfaces to coordinate in the delivery phase to ensure the compliance date could be met.
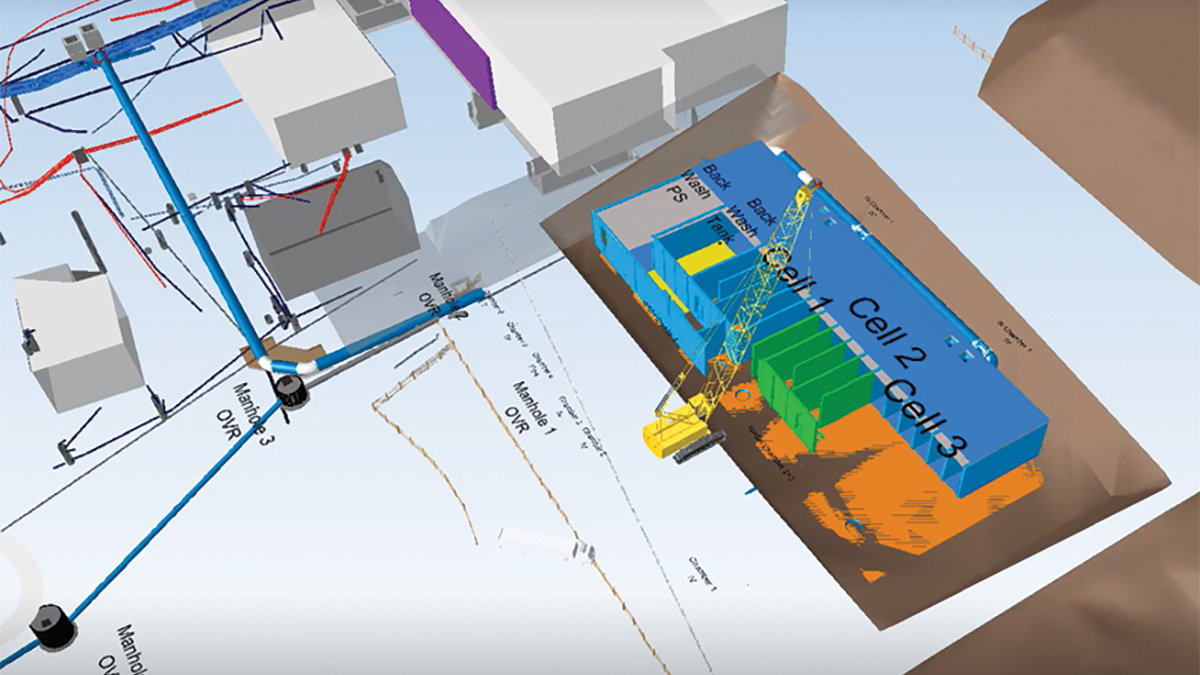
Synchro 4D Programming – Courtesy of Mott MacDonald Bentley
When undertaking the Access, Lifting and Maintenance (ALM) reviews on the project, the team implemented Virtual Reality (VR) technology to allow the design, construction and client teams to collaboratively review the proposed assets in a real-world environment and accurately assess physical access requirements.
Undertaking this in VR enhanced the safety and efficiency of the agreed proposals and ensured the outcomes delivered with a “right first time” mentality.
Whilst an integral part of the ALM review, the team also used this to collaborate with the client remotely. An example of this was reviewing the access to the dosing lance isolation valves in the new dosing chamber. With space at a premium on site, the chambers size was as lean as possible and risked introducing a hazard when removing and maintaining the lances.
The project leader reviewed the proposal in the 3D model using VR and made a short recording of valve location, orientation and access whilst simulating what the removal procedure looked like. This recording was circulated around key client stakeholders for comment and acceptance and showed an extended benefit to this digital approach.
Conclusion
Following an 18-month construction and commissioning period, the new contact tank successfully when into service in time for the regulatory compliance date. The solution has met the project drivers and is reliably producing quality water to the local area.
Overall this scheme has reduced the operational carbon by 70% from 1693 TCO2e to 495 TCO2e and reduced the operating carbon by 130 TCO2e annually, against the baseline design.
The reduction in construction scope has by extension reduced the number of construction activities and associated health and safety risks. Significant design development has led to this reduction in carbon impact.
These design evaluations and decisions were also the result of extensive collaborations with the integrated MMB design and build team; client project team, process engineers and site operations; and the supply chain.
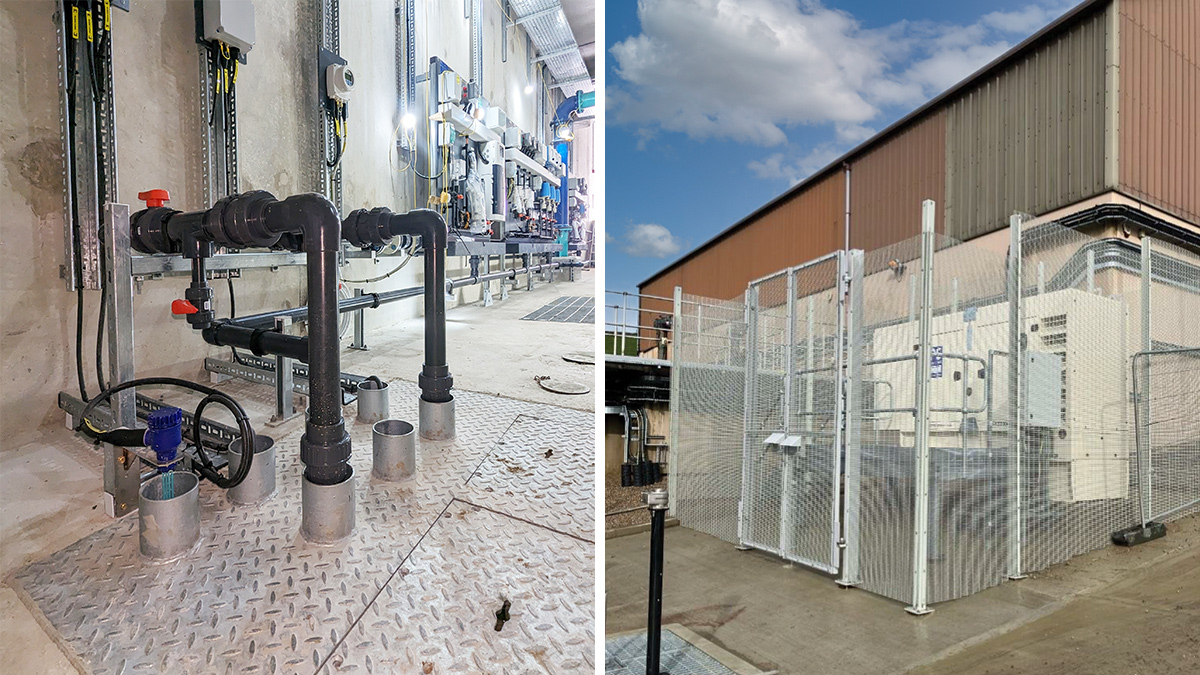
(left) Contact tank access and sampling and (right) new site generator compound - Courtesy of Mott MacDonald Bentley