Inveraray WTW (2024)
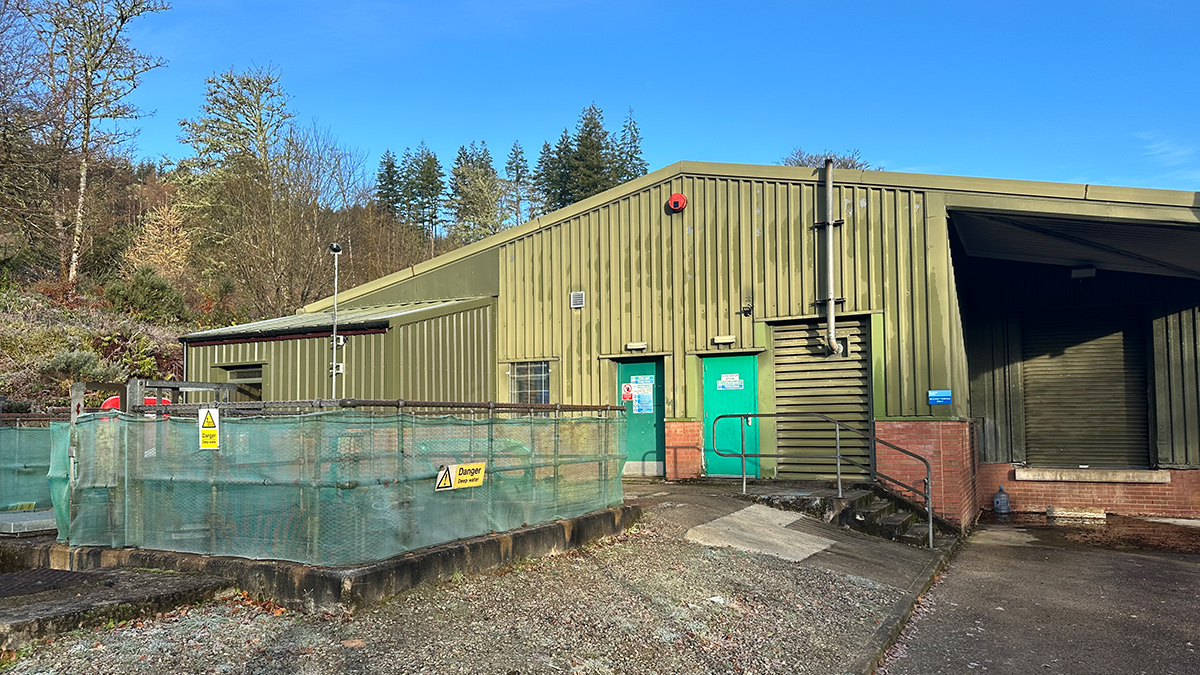
Inveraray WTW main building housing the inlet, saturation/coagulation and first stage filtration facilities - Courtesy of ESD
The Argyll SCADA (Supervisory Control & Data Acquisition) Project consists of control system replacement at four water treatment works in the Argyll & Bute region of Scotland: Inverary, Dhu Loch, Campbeltown and Kilchrenan. The project need was to address hardware obsolescence issues which presented Scottish Water with an unacceptable risk to continuity of supply. This case study focuses on one of the four projects, Inveraray Water Treatment Works, located on the western shore of Loch Fyne in Argyll & Bute.
Background to Inveraray WTW
Inveraray WTW treats raw water abstracted from Stellaire Ban Loch, which is supplemented from Loch Righeachan. Final water gravitates to supply the town of Inveraray and is also pumped to a nearby service reservoir. The works is a conventional two stage facility employing aluminium sulphate coagulation, dissolved air flotation, primary rapid gravity filtration and secondary pressure filtration.
The existing control system had reached the end of its serviceable life and was no longer supported by the manufacturer, presenting an unacceptable risk to continuity of supply from the WTW. To address this risk, Scottish Water initiated a project to replace the existing control system for the works
Inveraray WTW existing works process and control system overview
ESD was appointed as Principal Contractor to deliver the project. The initial focus was on appointing the right team to deliver the project. A Project Manager was appointed who had extensive experience in the EICA commissioning of critical water treatment works. A Design Lead was appointed who had 30 years’ experience in the manufacture, design and specification of MCC and Control System projects. A Principal Process Engineer who specialises in water treatment was assigned to review the documenting of the existing process control requirements. Experienced EICA Commissioning Engineers were consulted and appointed with the knowledge that the method of migration, testing and commissioning were a key focus. BGEN, as a Client Framework MCC/SI specialist, were appointed as the System Integrator Sub-contractor and awarded a contract to support the design of the project.
Project Challenges
The principal challenges were:
- Lack of existing information – limited drawings with no record of change in 30 years and initially no annotated programmable logic controller (PLC) software available.
- Loss of experienced control engineers who could have provided support to the project.
- Limited number of industry engineers with necessary experience.
- Remote location of each site, with plant shutdowns constrained.
- Operational constraints meaning work on two plants simultaneously was not possible.
- Special considerations to be made for seasonal changes in demand, making sure the plant was running efficiently and coping with the necessary requirements of both high and low demand periods during the summer and winter.
Project Planning
Leveraging the experience within the project team, the Project Manager and Design Lead worked with Scottish Water stakeholders to agree the deliverables required and methodology. Contrary to other projects on the client’s Investment Programme, it was agreed there were two key deliverables that were required ahead of agreeing a Target Price for the Project.
Firstly, a Programmable Logic Controller Migration Strategy document was produced by the subcontractor. BGEN had extensive experience in the development of this document, and specific experience in the migration of PLCs on live process plants. This document detailed all permanent and temporary equipment required to replace the Control System on site.
A Functional Design Specification (FDS) was the second key document. Previous project experience in utilising an FDS as a test document was recognised and, in order to capture existing functionality, ESD adopted a “bottom-up” approach to its development. Site surveys and interviews with site operations were undertaken to validate and update existing P&IDs which were 30 years old. These were then used as a basis to develop a Control Philosophy and FDS with Operations. BGEN and ESD worked together to develop the FDS against the minimal information available from the existing ICA installation – i.e. unannotated PLC software, SCADA mimics, wiring and site inspections.
As the Argyll project developed, parallel surveys and FDS development at another ESD site identified more annotation on similarly structured PLC software which allowed previously unknown functionality to be identified and captured in an updated FDS.
Once these outputs had been completed, the team worked with Client Technical Assurance to quantify risk and opportunity on the remaining unknowns. This in turn allowed ESD to agree a final version of an FDS & Migration Strategy with all parties prior to Factory Acceptance Testing (FAT). Having both key documents produced to detail allowed ESD to firm the scope with all parties and mitigate commercial risk.
Factory testing
With the FDS agreed and developed to a Software Design Specification by BGEN, full and comprehensive Factory Acceptance Testing of the software was undertaken at BGEN’s workshop facilities at Penketh. Drawing on previous industry experience and feedback from a variety of system integrators and water industry ICA Commissioning Engineers, a fully robust and complete Factory Test was critical to the success of on-site commissioning. It is more efficient and economical to correct errors prior to the connection of equipment to live process plant and equipment. The Client FAT was signed off to the satisfaction of all parties.
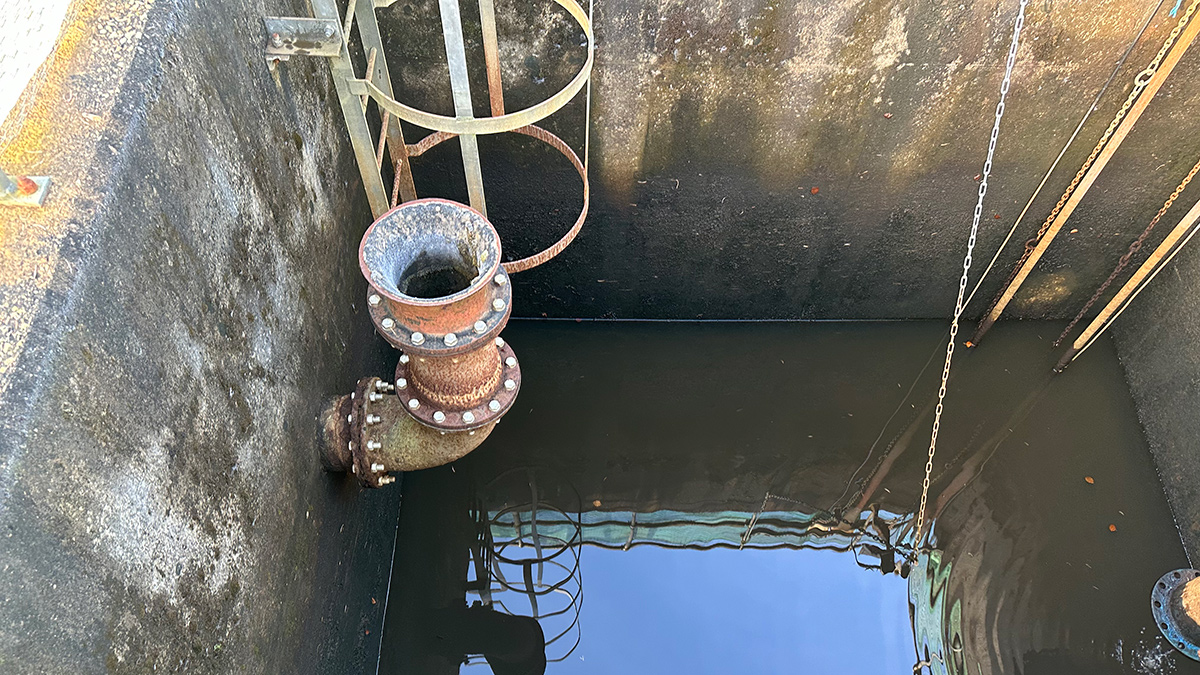
Dirty washwater tank – Courtesy of ESD
Implementation
The replacement process at Inveraray was carried out over the following stages:
- Installation
- Soak testing: In this stage, the plant processes are fully operational utilising the hybrid control for a timed period of ‘soak’ testing. This ensured the plant can be successfully operated under the new PLC and SCADA control. It also provided an opportunity for site operators to gain early familiarisation and training with the new Siemens SCADA system, preparing to take over once the replacement works are complete.
- I/O (input/output) migration: After confirming through ‘soak’ testing that the plant was successfully running with the new control system, the final stage involved replacing the existing PLC I/O with the new Siemens I/O. This stage was irreversible and only began once the new system was proven to be fully operational.
The I/O migration involved systematically isolating plant areas, disconnecting the field wiring from the existing PLC I/O modules and reconnecting it to the new Siemens I/O modules. The main concern during this process was minimising any disruption to plant operation.
Digital I/O was migrated, module by module, using new intermediate socket-to-terminal boards, making sure all the associated I/O of the new PLC was wired correctly on the new terminal boards which then have their sockets connected to the existing plugs wired to the existing field terminals. The existing field terminal wiring thus remained undisturbed. This digital I/O migration strategy was utilised due to very congested cable trunking in the rear sections of the MCC. Rewiring this section for the new I/O would have risked disturbing existing terminal connections, jeopardizing plant operations. Such disturbances are common during rewiring and can usually cause significant delays and disruptions. This technique, successfully used at Tobermory WTW, avoided unnecessary disturbance of existing field terminals.
Analogue I/O for each module was migrated signal by signal using existing field terminals and without congested cable trunking which were disconnected from the existing PLC modules and reconnected to the Siemens PLC modules by rewiring.
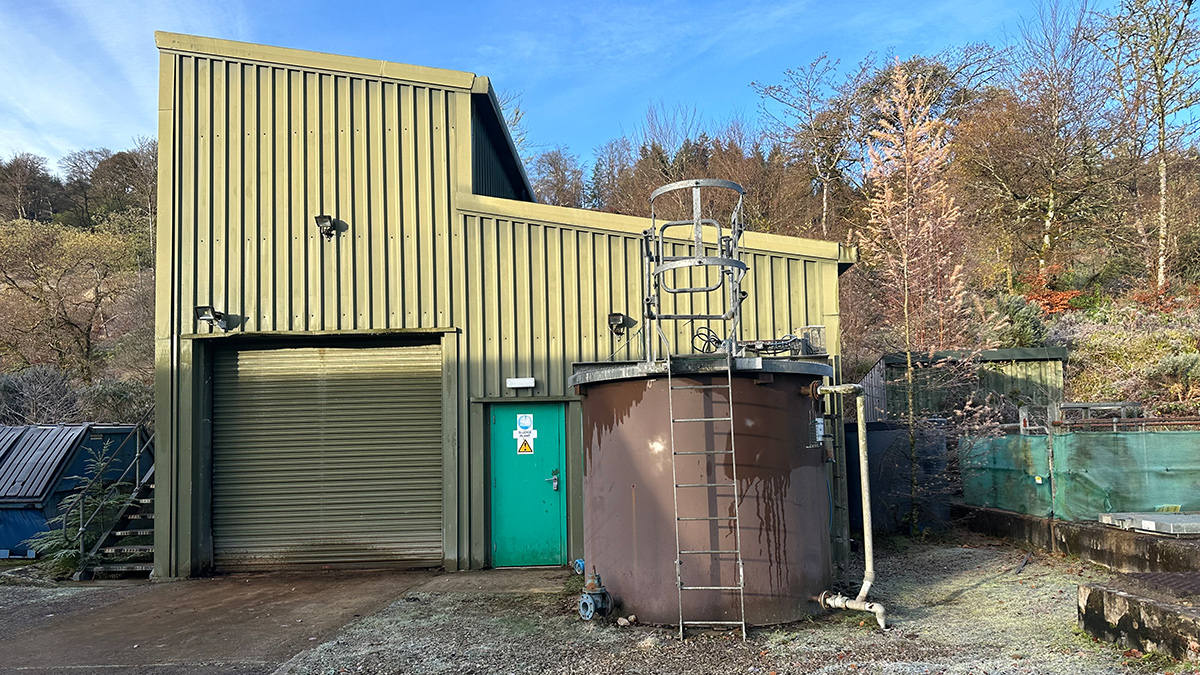
The sludge building – Courtesy of ESD
Project summary & innovations
The Argyll SCADA project was identified as a high risk project due to the critical nature of the process and the absence of any information that would have helped define the scope and the basis of the design. With all but one of the four projects handed over, the management of the process and commercial risk in delivering the project has been deemed a success for Scottish Water and its customer base.
Impactful decisions that supported the success of the projects:
- Resourcing key personnel with ICA, Process and Project Management experience in delivering PLC / SCADA replacement projects.
- Identifying the key risks prior to defining scope, including extensive, intrusive surveys to review and consolidate software condition and existing drawings and documentation.
- Regular and positive collaboration with the Client, agreeing the required process control with Site Operations and Client Technical Assurance to produce a documented Migration Strategy.
- Consideration on whether a document FDS was required prior to contract award for a more accurate Target Price.
- Validation and survey of existing field devices to provide I/O from existing drives, valves and instrumentation.
- Implementation of hybrid control prior to physical migration of I/O, providing further certainty on the new software configuration.
- Archiving of existing process control outputs for review, to consider rationalisation of the process – this was useful in the Argyll SCADA project as retuning process control resulted in an estimated 30% saving of operational costs.
Argyll WTW SCADA Project: Supply Chain – key participants
- Principal designer & contractor: ESD
- Systems integrator, electrical installer & telemetry contractor: BGEN
- Client: Scottish Water