Irton WTW (2018)

Irton GAC - Courtesy of MS2JV
Yorkshire Water’s Irton Water Treatment Works (WTW) is located 5.5km southwest of Scarborough in North Yorkshire. The WTW abstracts water from an aquifer via numerous boreholes and supplies two local service reservoirs; Springhill and Low Mount, which feed Scarborough and the surrounding area. Demand profiles are seasonably variable. The site has an abstraction licence for 23.5 MLD. On average, the works supplies around 16 MLD. Due to a deterioration in raw water quality and increased risk of pesticides within the raw water, Yorkshire Water appointed Morgan Sindall Sweco Joint Venture (MS2JV) to investigate the installation of pesticide removal and pH correction equipment to achieve effective clarification and reduce cryptosporidium risk.
Background
Initially Yorkshire Water undertook investigations and developed a notional solution for the works required to address three business risks, namely:
- Pesticides (including isoproturon, chlorotoluron and MCPA but excluding metaldehyde).
- Cryptosporidium.
- Disinfection by-products (DBPs) which include THMs – Regulation 26 (1A).
The outline design/notional solution was to install a pesticide removal plant, based upon a granular activated carbon (GAC) adsorption and ozonation process. pH correction was also to be installed upstream of the ActifloTM plant to achieve effective clarification and reduce cryptosporidium risk. The costed proposal for this notional solution was outside of Yorkshire Water’s budgetary constraints and Yorkshire Water commissioned MS2JV to undertake an investigation and risk and value assessment on the business risks and proposed notional solution.
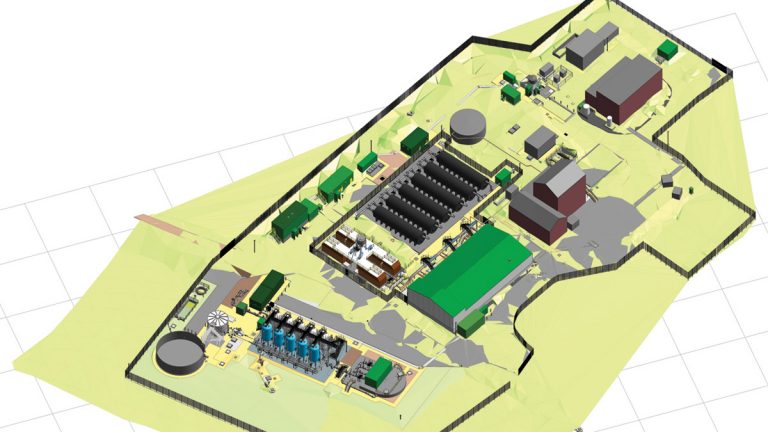
Irton WTW 3D model – Courtesy of MS2JV
Existing process
The existing treatment process consisted of:
- Borehole abstraction pumping station, aluminium sulphate and polymer dosing prior to an ActifloTM sludge removal, coagulation process.
- The flow then passes through a bank of rapid gravity filters (RGF) and into the contact tank.
- Sodium hydroxide is dosed for pH correction, sodium hypochlorite and sodium bisulphite dosing is used for disinfection and monosodium phosphate (MSP) dosing for plumbosolvency.
- The flow is pumped from a final water tank via the high lift pumping station to the off site service reservoirs.
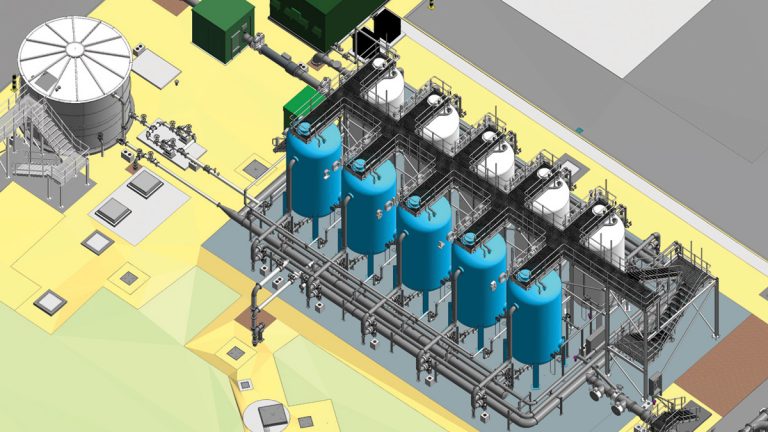
GAC plant 3D model – Courtesy of MS2JV
Solution
The investigation contract concluded that the proposed notional solution would not fully address the business risks and a detailed risk and value process was undertaken to identify alternative solutions and construction methods.
Additional business risks associated with failing/under-performing assets, access for maintenance and inadequate wastewater treatment capacity were highlighted during the investigation phase of the project.
The investigation and risk and value process concluded that the ozonation stage would not provide good value. GAC alone was considered ample to address the pesticide risk. An interstage pumping station and ten steel pressure vessels for GAC have been installed for pesticide removal.
DBP minimisation was addressed primarily by optimisation of coagulation/pH. This maximised the removal or organic matter that is a precursor for DBP formation. Optimisation involved the provision of the facility to dose either acid or alkali into new static mixers to ensure the optimum pH could always be maintained.
Cryptosporidium removal has been enhanced by optimised coagulation, improved flow control including more accurate flow splitting for the RGFs and by the provision of 3.5m deep GAC beds equipped with slow start facility.
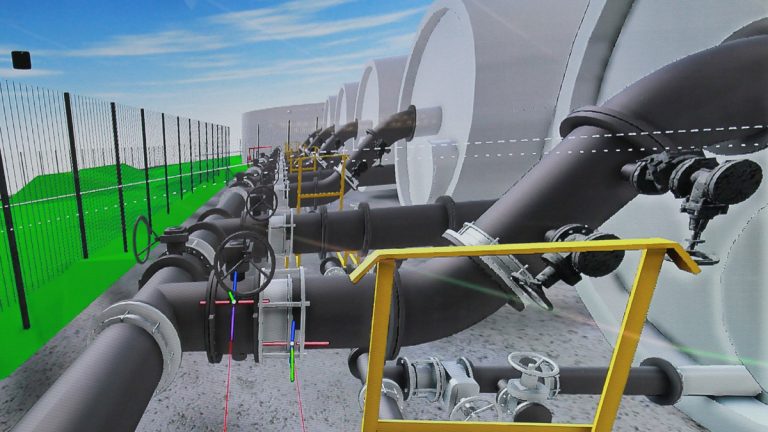
Irton WTW 3D model virtual realisation – Courtesy of MS2JV
New chlorine contact tanks address access and maintenance issues with an aging asset. Significant cost savings were made by using an innovative approach. Six cylindrical above-ground Weholite® tanks were constructed in high density polyethylene (HDPE). These tanks were hydraulically modelled and their inlet structures designed to ensure an enhanced plug flow. The tanks were sized on a 5+1 basis substantially reducing the overall required capacity compared with the traditional 1+1 (one in use one out for maintenance) basis.
The solution adopted at Irton following the risk and value process included the following:
- Modifications to ActifloTM sand silo.
- New inlet manifold to RGFs for equal flow distribution.
- New interstage pumping station.
- New GAC plant.
- New contact tanks.
- New chemical delivery, storage and dosing installations.
- Ancillary works, static mixer chambers, new internal roads and a de-chlorination chamber.
- High voltage/low voltage power upgrade.
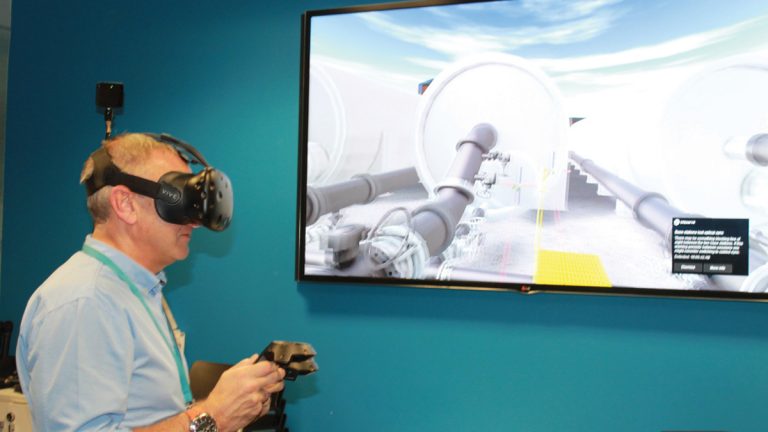
Irton WTW 3D model virtual realisation – Courtesy of MS2JV
Modifications to ActifloTM sand silo
Modifications to the existing micro-sand dosing silo to ensure effective sand dosing is achieved. The micro-sand is an essential aspect of high rate clarification enhancing the formation of robust flocs.
RGF inlet manifold
To address the business risk of unequal flow split between the 6 (No.) RGF cells a pipework manifold was designed to reduce flow split discrepancies as far as possible and this was analysed using a computational fluid dynamic (CFD) model. The flow split differences between each RGF inlet was found to be negligible and the proposed arrangement deemed optimal for achieving an even flow split. Each individual pipe feed has a flow meter and actuated isolation valves. The individual RGF feed isolation valves can be modulated, as required, to finely adjust the flow.
Interstage pumping station
Due to the addition of new process units into the treatment works, a new interstage pumping station is required to increase the hydraulic head available to feed these new treatment processes. The pumping station is a 10.5m diameter precast concrete caisson construction approximately 4.0m deep.
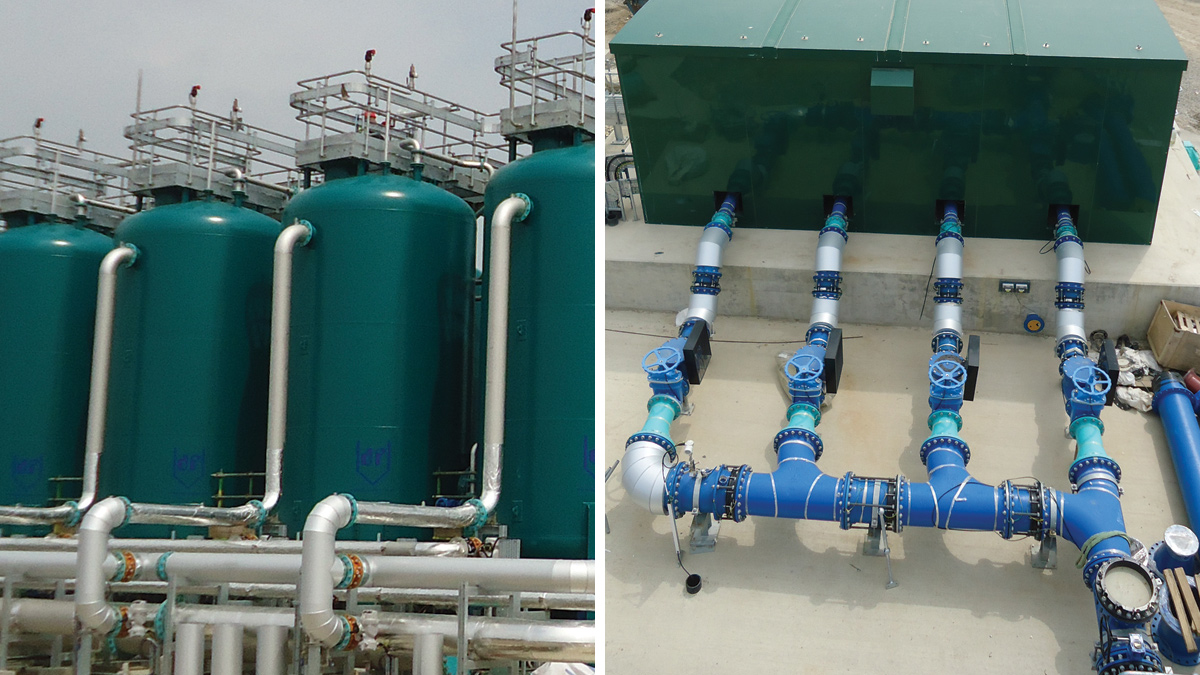
(left) Irton WTW GAC and (right) interstage pumping station – Courtesy of MS2JV
A physical 1:4 scale model was commissioned to model the hydraulic behaviour of the new pumping station. Internal baffles and stalls around the pumps were designed to optimise flow presentation and mitigate issues such as surface vortexes and pre-swirl into the pump intakes.
GAC area
The GAC area comprises 10 (No.), 3.0m diameter, 7m tall steel vessels with interconnecting process pipework. Each vessel is filled with GAC. A new clean backwash tank and pump set, dirty backwash water waste tank, as well as a new MCC is included in the scheme. There are a number of pressure sustaining valves to ensure the plant operates at an optimum pressure, as well as pressure relief valves to protect the system from over pressurisation.
Contact tanks
MS2JV has designed an innovative contact tank consisting of 6 (No.) above ground cylindrical vessels, each 3.5m diameter and 16m in length. The vessels are connected in series to allow for any combination to be taken offline or out of service.
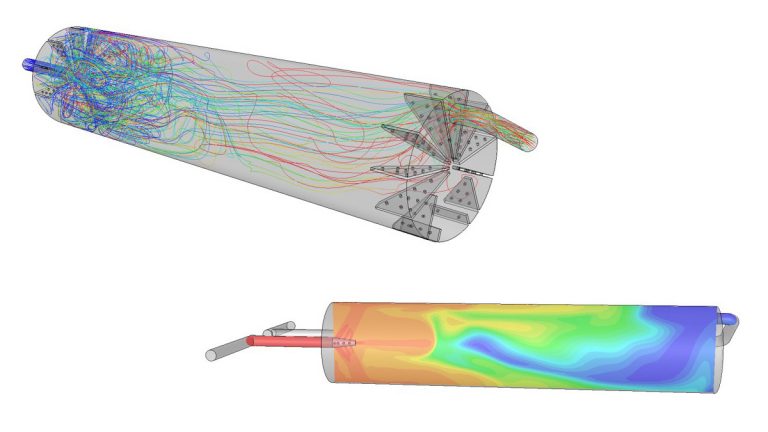
Contact tank CFD model – Courtesy of MS2JV
To comply with Yorkshire Water specifications and asset standard, a plug flow factor of 0.7 is required. This is difficult to achieve without numerous baffles and weir walls. This, however, would have made access for maintenance difficult and unsafe.
An inlet diffuser attached to the incoming pipework was designed to evenly disperse the flow through each contact tank. This exceeded the required plug flow factor without the requirement for any baffles or weir walls.
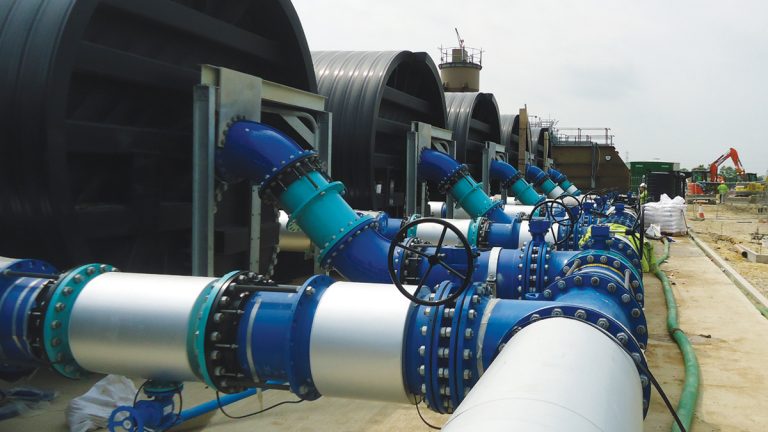
Contact tank inlet – Courtesy of MS2JV
Chemical delivery area
To ensure optimum operation of the process and the correct pH level is maintained throughout the process, new aluminium sulphate, sodium hydroxide, sulphuric acid and sodium hypochlorite chemical delivery, storage and dosing installations have been provided.
Supply chain involvement
Supply chain collaboration was key to the solution adopted and MS2JV worked closely with Glanua Group to design the GAC plant, Weholite® to design the contact tanks, and Galliford Try in designing the chemical dosing systems.
Table of designers, contractors and suppliers:
- Principal contractor/designer: Morgan Sindall Sweco (MS2JV)
- Civils installation: CPC Civils Ltd
- Mechanical installation: Staptina Engineering Services
- Electrical installation: Interface Contracts Ltd
- GAC plant: Glanua Group
- Chemical dosing plant: Galliford Try
- Contact tanks: Weholite®
- Motor control centres: Saftronics Ltd
- CFD modelling: Hydrotec Consultants Ltd
- Interstage pumps: SPP Pumps Ltd
Health and safety
The MS2JV delivery processes adopted for Irton WTW were compatible with the Yorkshire Water process safety requirements. The processes incorporated the IChemE 7-stage hazard study process, including regulatory/statutory compliance risk assessments. The project also utilised 3D models and virtual reality tools to assess human factor criteria as part of the hazard study/access lifting and maintenance (ALM) process.
A successful outcome
The solution provided by MS2JV contains innovative processes and construction materials that are new to Yorkshire Water including adsorption vessels constructed in steel for the GAC process and cylindrical above ground Weholite® tanks constructed in HDPE for the contact tank process.
MS2JV’s collaborative approach to a technically challenging scheme delivered a £17m cost saving against the £31m estimate for the notional solution. The saving being achieved through the rigorous implementation of an investigation phase and risk and value process that resulted in an alternative, innovative solution to address the business risks.
The project is due to be completed in December 2018.