Bickerstaffe Pumping Station (2017)
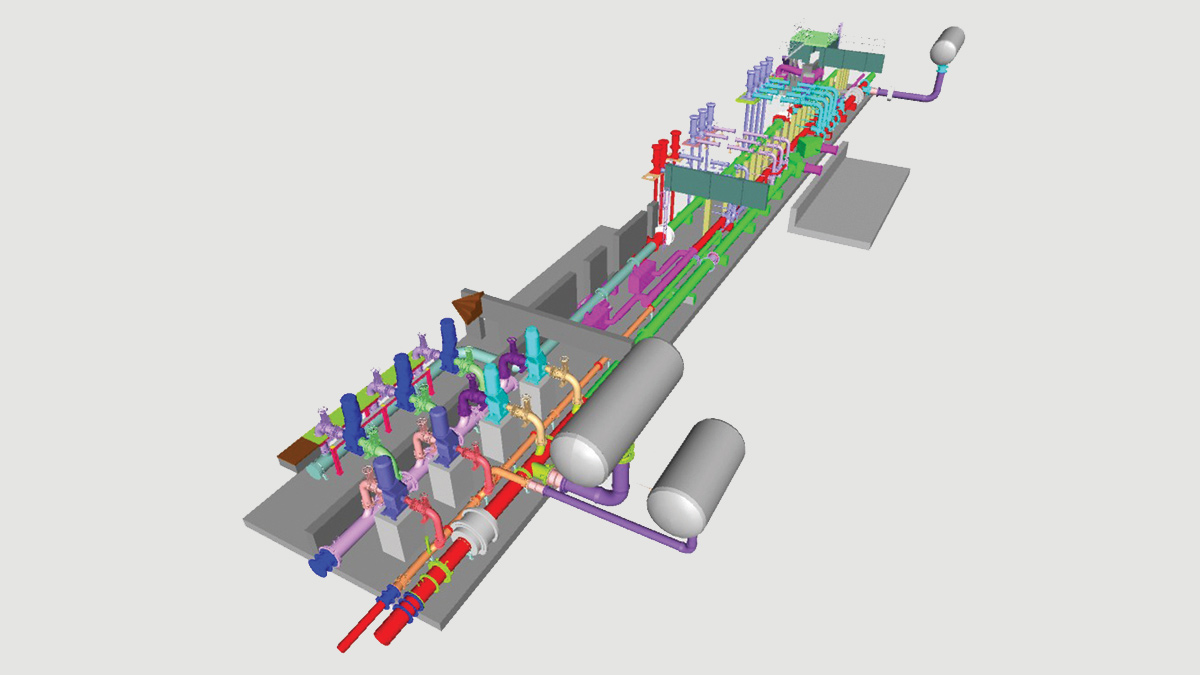
Bickerstaffe Pumping Station 3D model - Courtesy of MWH Treatment
The Southport Demand Monitoring Zone (DMZ) comprises ten supply zones with a population of approximately 245,000 covering the majority of the areas of the District Councils of West Lancashire and Sefton. Southport DMZ suffers from a number of issues including (i) peak demand during the summer months (ii) population growth (iii) water management. To overcome these issues, it was decided to construct a new water treatment works at Royal Oak with a capacity of 54Ml/d immediately adjacent to Bickerstaffe WTW which allows the decommissioning of the 5 (No.) existing direct filtration plants, by redirecting raw water from the existing boreholes (BH) into Royal Oak WTW. Treated water from Royal Oak WTW will discharge to the existing Bickerstaffe Service Reservoir (SR) and Pumping Station (PS) which will then serve as a hub through which the entire Southport DMZ will be supplied. The solution requires for the pumping station to be upgraded.
Project background
Planning for the Bickerstaffe Pumping Station refurbishment project was undertaken through the use of innovative technologies which included laser scanning, collaborative planning, 3D models and digital delivery as part of 4D Synchro. This was due to the level of complexity and the potential problems the pumping station refurbishment upgrade would present.
Bickerstaffe PS currently contains four sets of wet well pumps, which are supplied direct from Bickerstaffe Service Reservoir, and two sets of inline pumps which are supplied direct from the North Liverpool Trunk Main (NLTM). All four of the existing wet well pump sets are being removed, with three of them being replaced (the final set will no longer be required). Both the existing sets of inline pumps are being removed and replaced (in a different area of the PS) with an additional set installed.
The existing pipework/manifolds will be reused where possible, but significant sections will be removed and replaced as necessary. The reconfiguration of the PS requires a new Scarth Hill Rising Main from the opposite end of the PS to an existing rising main at Liverpool Road.
The PS refurbishment is part of the wider Southport Project involving the renewal and reconfiguration of approximately fifteen major assets over an 18km area.
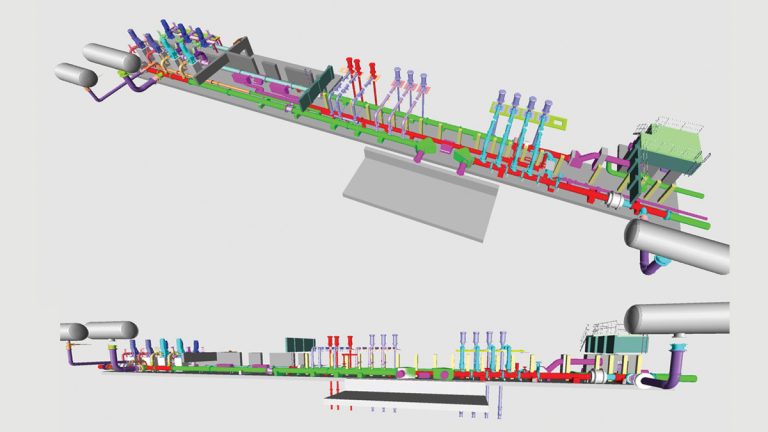
Bickerstaffe Pumping Station 3D models – Courtesy of MWH Treatment
Challenges and solutions through collaboration and technology
There are several challenges to consider with the PS upgrade such as physical complications and operational considerations.
Physical complications: There are two existing large standby diesel HV generators and a control panel that need to be removed from the space where the three new sets of inline pumps will be located. Once the existing standby generators have been removed, the existing reinforced floor (currently under the generators) needs to be removed and the existing floor (currently under the control panel) needs to be reinforced then have a significant slot cut through it. Without the laser scan of the existing structure the project team would not have been able to have such a detailed visual representation of what was needed.
The laser scan also helped in surveying the pipe gallery, which is located in the building basement and is approximately 70m long, 2.5 m high and 5m wide. There are numerous columns supporting the floor above and existing electrical cabling including HV cables running under the slab. Within the pipe gallery are 2 (No.) 27” mains, 1 (No.) 24” and 1 (No.) 12” main.
These mains predominately run the length of the gallery, with various connections crossing between them. The mains have concrete thrust blocks and supports. The detailed visualisation of the pipe gallery meant there was no need to go back on site and increase health and safety risks trying to get into tight spaces.
The access to the building is at ground floor level only. All pipework, equipment etc will therefore have to be lowered/raised through the floor (after it has been removed) and manually moved into place. This is where 4D Synchro helped depict how to accomplish moving the pipework and equipment without having to be on site.
Through the collaborative planning, laser scans and 3D models a visual timeline of how the moving, lifting and installation would be completed. The team know exactly what they are doing before taking on their tasks and health and safety risks are eliminated because of the reduced time on site.
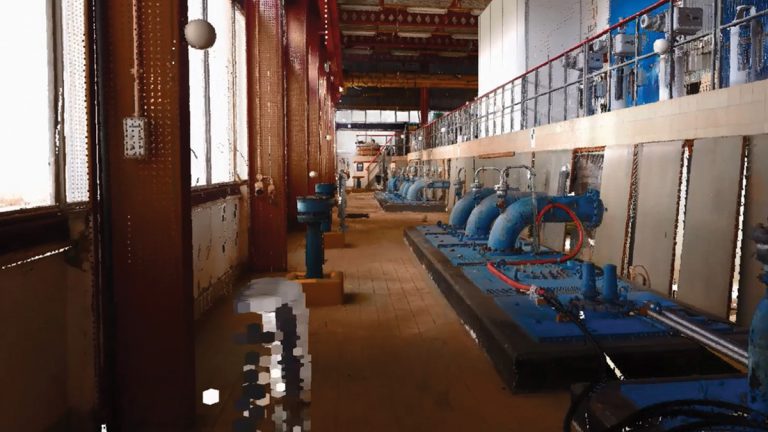
Bickerstaffe Pumping Station laser scan – Courtesy of MWH Treatment
Project implications and operational considerations: The project implications involved with the Bickerstaffe PS refurbishment were identified early on because of collaborative planning, as it became clear that there would be time constraints associated with the project. The pumping station principally supplies four destinations:
- Gorse Hill Service Reservoir.
- Scarth Hill Water Tower.
- Elmers Green Service Reservoir.
- Maghull Distribution Zone.
Both Scarth Hill pump sets are the only supply to Scarth Hill Service Reservoir and therefore can only be isolated for minimal time. Both Gorse Hill pump sets supply to Gorse Hill Service Reservoir, but this is also supplied from 3 (No.) separate boreholes. Gorse Hill pump sets can therefore be isolated for a short time.
The 3 (No.) boreholes that currently supply direct to Gorse Hill SR will be altered to supply through Bickerstaffe PS as part of the larger Southport Project.
- Bickerstaffe Boiler House (BH) will eventually supply direct to Royal Oak WTW.
- Bickerstaffe BH will be offline for approximately 1 week prior to the ‘switchover’ to supplying Royal Oak WTW to allow for the control change etc.
- Blundell BH and Springfield BH will eventually be supplying direct to Royal Oak WTW. Both BH will be offline for approximately 1 week prior to the ‘switchover’ to supplying Royal Oak WTW to allow for the control change etc.
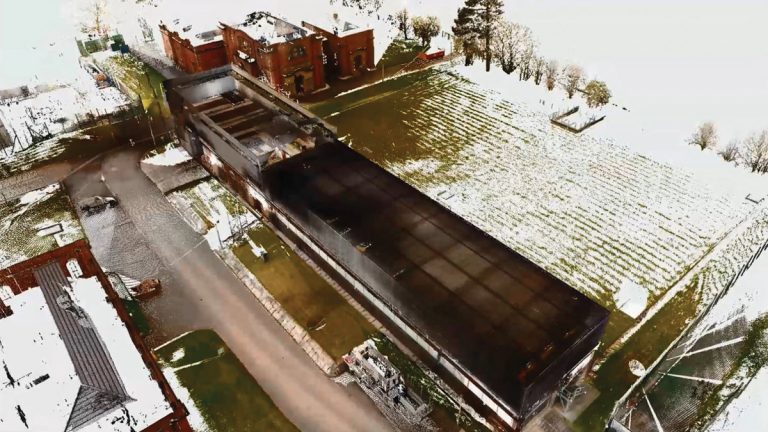
Bickerstaffe Pumping Station laser scans – Courtesy of MWH Treatment
If the existing Gorse Hill pipework and existing Gorse Hill wet well manifold have not been replaced prior to the 3 (No.) boreholes supplying to Royal Oak WTW, then the duration that the Gorse Hill pumps can be isolated for will be reduced.
Given all these factors and parameters the preparation for the Bickerstaffe PS refurbishment had to be exact and the 4D Synchro allowed the project team to create a detailed timeline of the process. If the timeline is not precise it can mean working longer than expected and disrupting water supplies to different locations.
The Synchro software gave a visual aid for United Utilities operations staff and allowed the Advance JV staff to look at access requirements, potential clashes etc, thus improving planning and keeping all stakeholders informed of the schedule. Keeping stakeholders informed of the schedule and having one version of the truth is vital to a project as complex as the pumping station.
The Synchro software is available to all stakeholders so any changes to the schedule is easier to approve than before given how included everyone is in the process. Collaboration is key when there are so many factors involved.
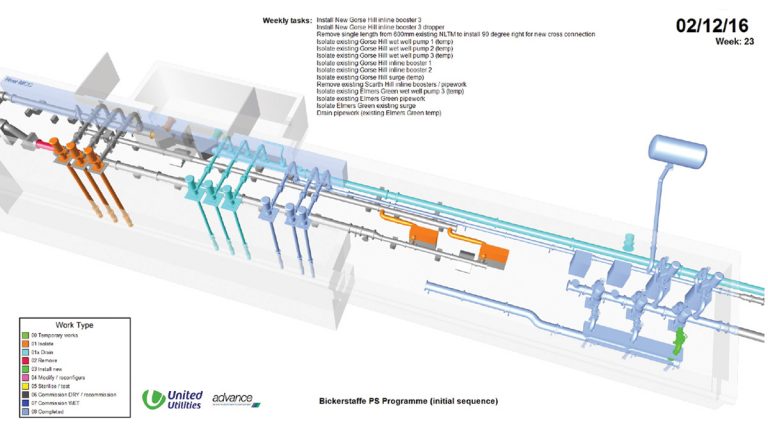
Bickerstaffe Pumping Station 4D Synchro Timeline – Courtesy of MWH Treatment
MCC considerations
The existing pumps are all operated by two separate Motor Control Centres (MCC). The high voltage (HV) MCC operates the wet well pumps, and the low voltage (LV) MCC operates the inline pumps.
A single new MCC will be installed prior to both the existing MCCs being removed. This will enable the existing pumps to remain in operation until all the new pumps have been installed. The existing MCCs will not be removed until the existing pumps have been removed/replaced with the new pumps.
The new MCC is approximately 30m long. This physical size restricts the location within the existing pumping station building, as well as difficulties manoeuvring the MCC into the pumping station building. The 4D Synchro allowed for a visual depiction of how the MCC would be moved into the PS and the digital rehearsals show exactly how it would work. Minimising the amount of time on site with a large move like this was important given the space restrictions inside the building and rehearsing gives everyone a detailed recreation without the risk.
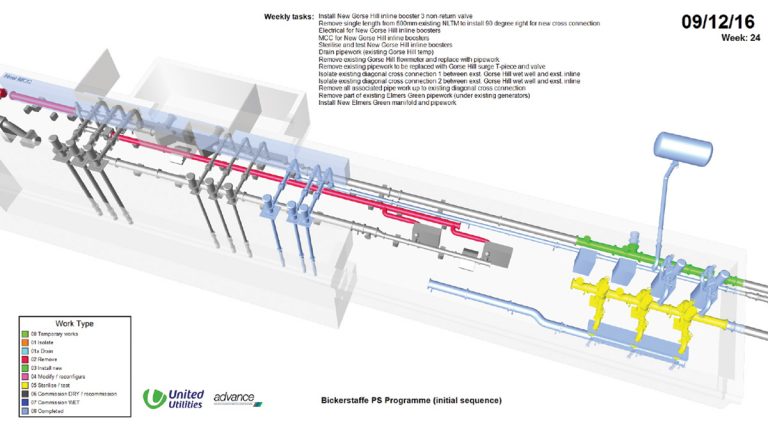
Bickerstaffe Pumping Station 4D Synchro Timeline – Courtesy of MWH Treatment
Benefits
There were numerous benefits to using the laser scan technology, 3D modelling and digital collaboration/rehearsals throughout the project. The collaborative planning was incredibly useful as numerous aspects of the overall project were considered while maintaining focus on the specific difficulty of the Bickerstaffe Pumping Station refurbishment. There was consideration for lifting, equipment removal and installation, commissioning and testing, all while working within the programme constraints.
The laser scan allows visualisations of the site to be constructed, eliminating the need for additional people to venture into the pipe gallery and with digital rehearsals the health and safety risks are significantly reduced, all while saving time and money on site.
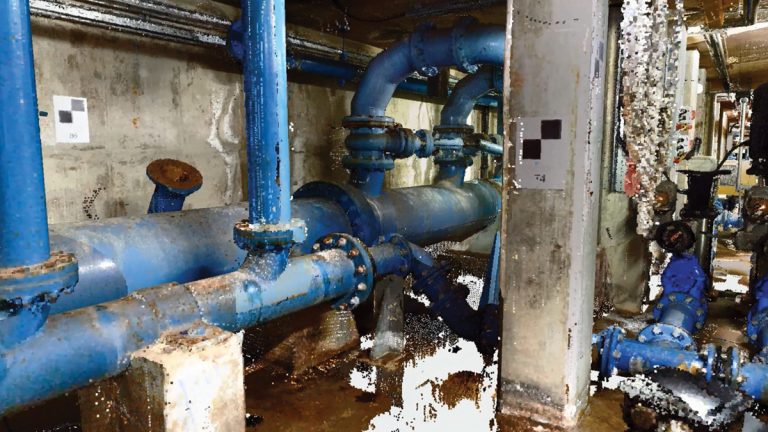
Bickerstaffe Pumping Station laser scans – Courtesy of MWH Treatment
From the 3D model a ‘story board’ can be produced giving a day/week/month per page activity. A colour code key was used to show on which day’s removal, installation, commissioning etc. work would be required and this document was included within the tender documents and as an appendix in the Subcontract documents.
The software gave a visual aid for United Utilities operations staff and allowed the advance JV staff to look at access requirements, potential clashes etc, thus improving planning and keeping all stakeholders informed of the schedule.