Syleham WTW (2020)
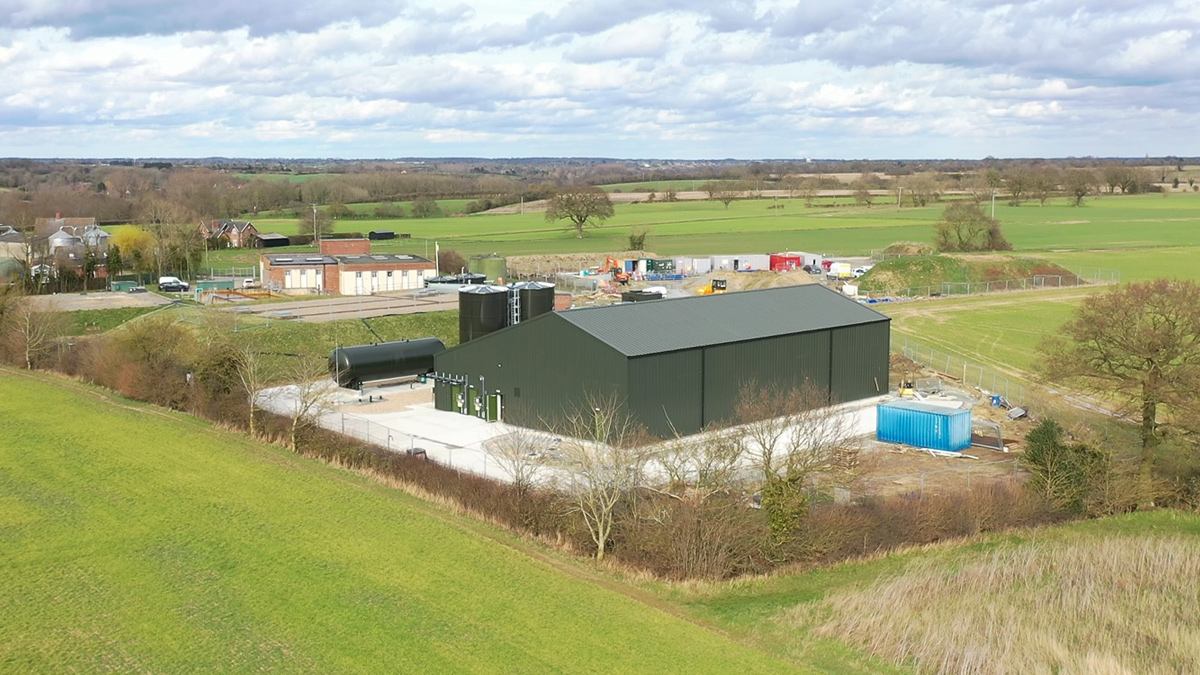
Syleham WTW capacity upgrade project (March 2020) - Courtesy of Essex & Suffolk Water
Essex and Suffolk Water’s Syleham Water Treatment Works is located in the north-east part of Hartismere in Suffolk. The works supplies water to the north side of Eye and to Fressingfield Water Tower, which in turn supplies approximately 4,000 properties (10,000 customers) throughout a number of villages. It was originally constructed in 1940 and raw water is abstracted from three bores, located within the site boundary. The 125m deep limestone chalk bore was commissioned c. 1940 and later bores in the 1950s, abstracted from 45m deep crag deposits that are common across East Anglia and include gravels, shelly sands, sands, silts and some laminar clays.
Existing works
The existing works had a two-stage filtration process, using biological rapid gravity filters (RGFs) as its primary stage and catalytic pressure filters for its secondary. The fundamental issue with the process capacity at Syleham was the primary iron filters which were converted from up flow to down flow rapid gravity filters during the 2004/5 refurbishment of the works. The process was constrained to being able to treat approximately 4.5 Ml/d (52 l/s), with interim process enhancements looking to deliver an increase to only 5.2 Ml/d (60 l/s).
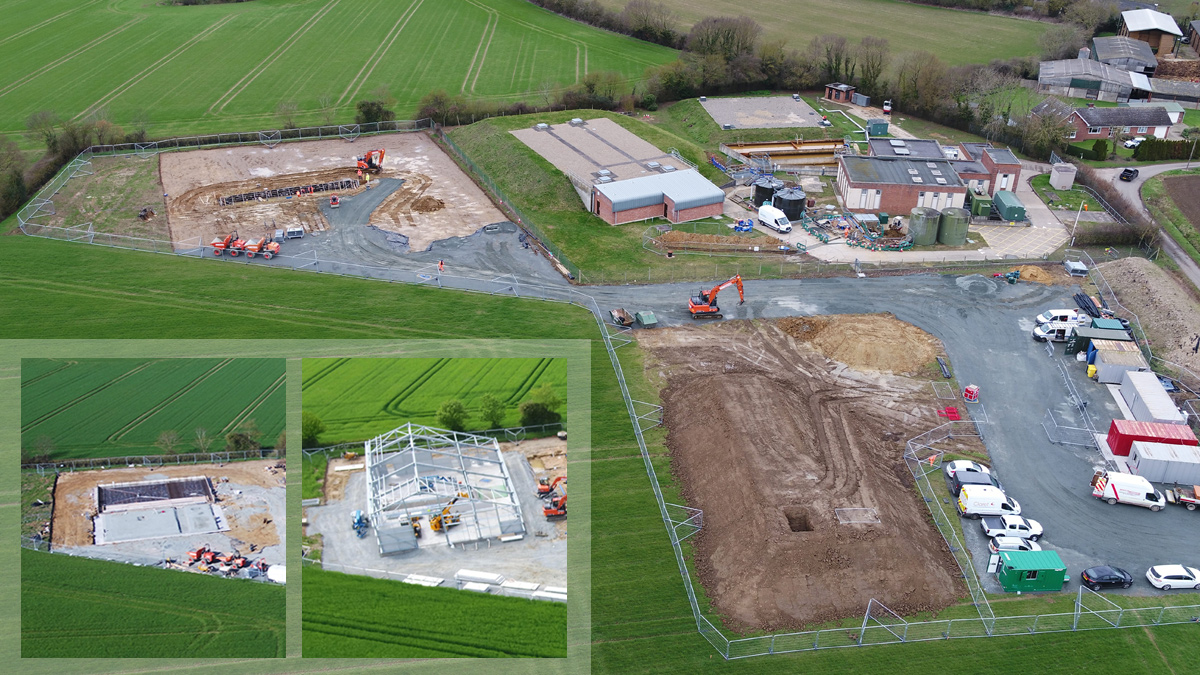
The main photograph (8 March 2019) shows the construction area for the new water treatment works. Top right shows the existing plant and bottom right shows the construction compound; rented for the duration of the build. The inset (left) shows progress on 1 April 2019 and the inset (right) from 16 May 2019 shows the steel frame of the WTW – Courtesy of Essex & Suffolk Water
The challenge
The £7m investment project delivered a new treatment stream capable of processing the site’s license, within an 18-month timeframe from inception to supply. The design needed to bypass the part-treated reservoir, which itself is in poor condition. Despite investment from the reservoir and towers programme of works, it would regularly fail during the annual inspection, as a result of rainwater ingress.
The original scope of the project was to utilise the existing secondary filters at Syleham, however the condition and viability of utilising these filters was unknown at the time and the requirement was highlighted as a project risk. During the I&D phase of the project, it became clear that connecting the new primary to the old secondary filters would be extremely complex and high risk, so therefore costly.
Two-stage filtration process project scope
For the same original budget, the team has been able to provide Essex & Suffolk Water with a new two-stage filtration process; the key elements of which are:
- Purchase of land adjoining the existing site.
- A new filter building.
- New primary pressure filters.
- New secondary filters.
- Twin cascade aeration tanks.
- Primary wash tank.
- Secondary back wash tank.
- Disinfection reaction vessel.
- Disinfection upgrade to include a provision to comply with Reg. 26.
- Motor control centre.
- Coagulation dosing plant.
- Back wash settlement tank.
- Interface with existing assets.
- Demolition of redundant assets.
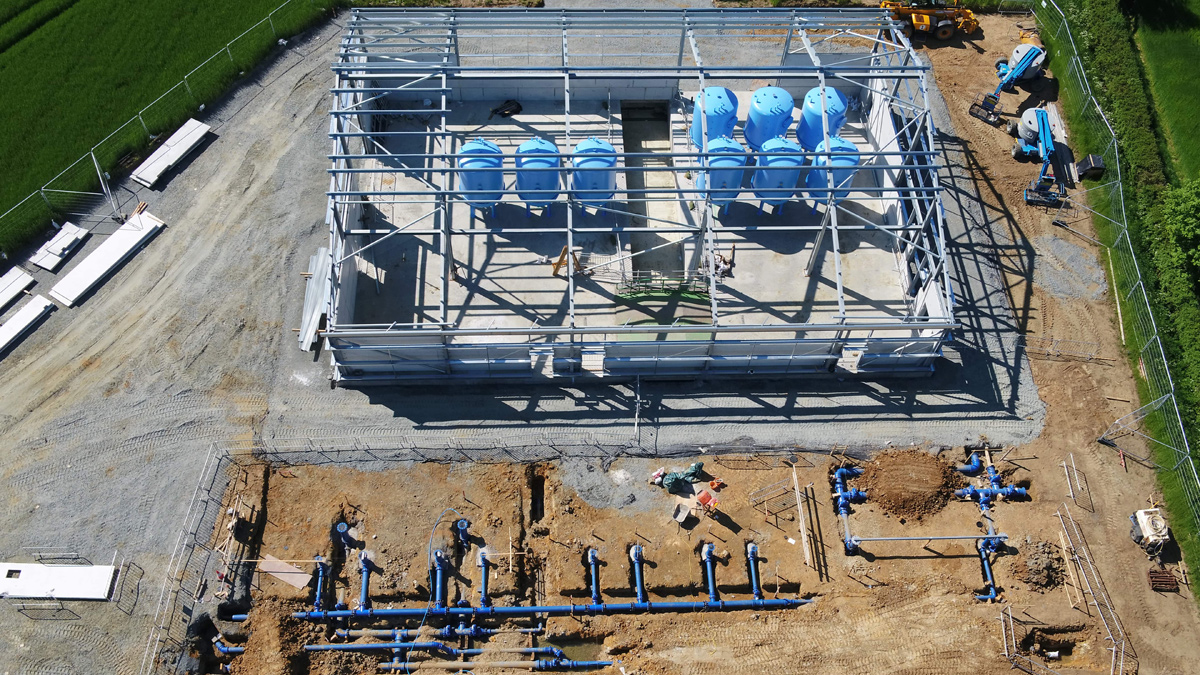
The new building and below, the area for the aerators, backwash tanks and chlorine reaction vessel – Courtesy of Essex & Suffolk Water
Syleham WTW: Supply chain – key participants
- Client: Essex & Suffolk Water
- Principal contractor: Integrated Water Services
- Civil engineering contractor: Claret Engineering Ltd
- Chemical dosing specialist: Sheers Ltd
- Architectural/building services design: Robert Stone Associates
- ECCPM & cost consultant: Turner and Townsend
- Software integrator: OCE
- Process pumps: SPP Pumps Ltd
- MCC: TES Ltd
- Filter vessels: Wefco Ltd
- External building shell: Balsham Buildings Ltd
- Aeration and backwash tanks: Hayes GFS Ltd
- Backwash settlement tank and pumps: Aquardia Ltd
- Pressure filter vessels: AWE Ltd
- Above ground pipework: Leyfos Ltd
- Valves and actuators: CSG Valves Ltd
- Access walkways and platforms: Steelway
Approach
Delivering a new treatment works in 18 months (the time it would normally take to get enough information to go to the business for a full project budget), on arable land that Essex & Suffolk Water does not own, was going to be challenging. The key to successful delivery was a focus on collaboration, embracing lean project management techniques, and putting lessons learnt into practice.
Essex & Suffolk Water initially looked to the successful process upgrade at Walpole WTW which was to be used as the benchmark. A great deal of design information was taken from Walpole to use at Syleham; which saved time and reduced risks as this was a proven process to the business. A design envelope was produced by the process design engineer that would steer the design team to key parameters needed to be achieved which included:
- Raw water quantity – abstraction licence conditions.
- Raw water quality – iron 98%ile, manganese 95%ile and ammonia 95%ile. Any results within the dataset of greater than three standard deviations from the mean value have been discounted and removed.
- Raw water quality – pH, DO, temperature and turbidity.
- Final water quality targets.
- Aeration (to provide sufficient dissolved oxygen for the subsequent process, and pH adjustment).
- Primary filtration designed for the biological removal of iron and ammonia.
- Disinfection dosing for catalytic manganese removal.
- Chemical reaction vessel. This is not a contact tank, but a vessel to allow complete reaction of the disinfectant with ammonia should any pass through the primary filters, the theory being that we will minimise any potential ammonia spike allow the disinfection system a chance to adjust accordingly to the new demand the ammonia level has caused.
- Secondary filtration (catalytic manganese removal).Disinfection.
- Wash water and sludge handling.
- Chemical dosing (wash water settlement aid).
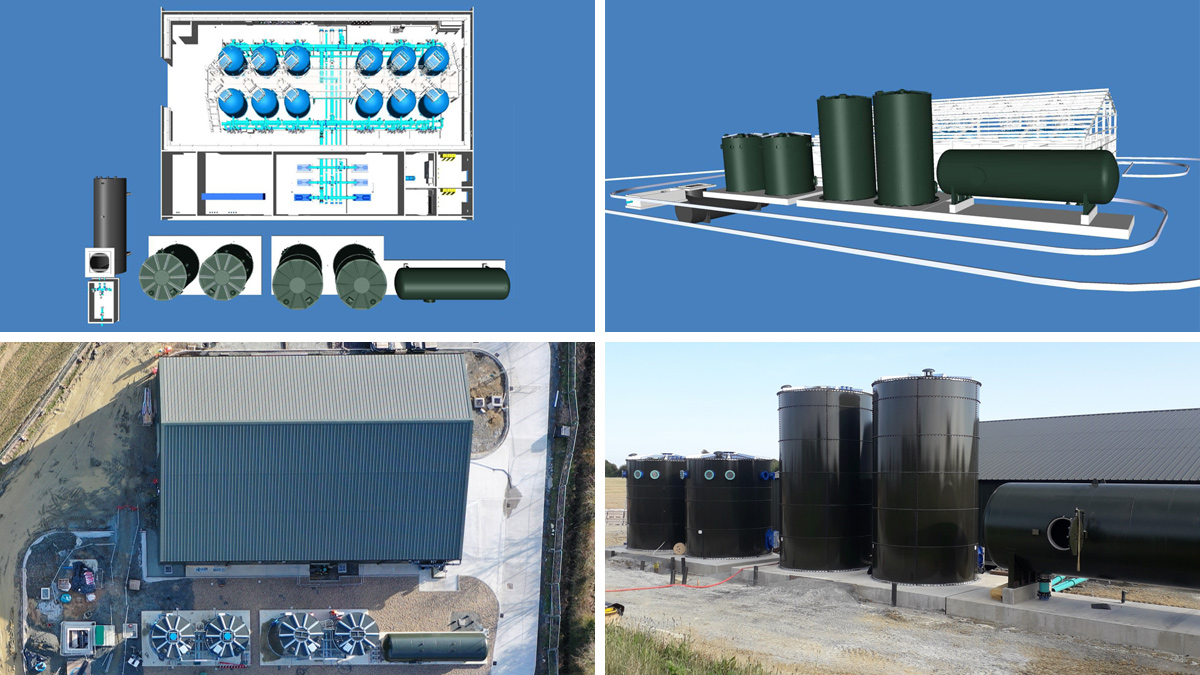
4D model and as built (left) the plan view and (right) from left to right the two aeration tanks, the primary and secondary filter backwash tanks, and the chlorine reaction vessel – Courtesy of Essex & Suffolk Water
Moving forward
With sufficient data for the design team to work from, effective techniques could be considered to drive the project forward.
Design sprint: Not a five-day sprint, but a slimmed-down one day event. Key to this was still adopting the principles of the five-day version and getting good stakeholder participation in the exercises.Design sprint outputs: A day where the project team presented their vision to the wider stakeholder audience, with a clear mandate of achieving stakeholder buy-in before closing the day.Scope freeze: Another critical meeting to present the revised design solution with all the various stakeholders, and once all feedback and amendments were captured, this was then the solution frozen at this point.
New innovation to the project came by the use of a 4D model, not only allowing the team to look at the finished building, but link this to a programme to easily see how construction is progressing against a tight programme.
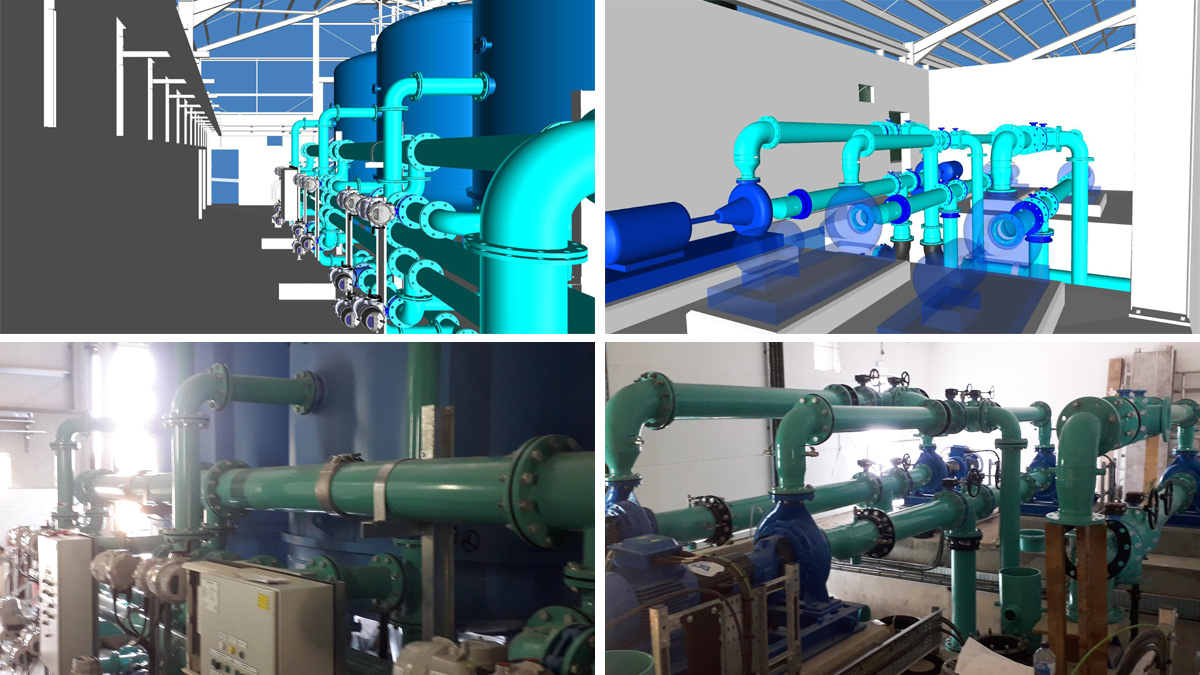
4D models and as built (left) primary filters and pipework and (right) the plant room with six VSD pumps and two positive displacement air blowers – Courtesy of Essex & Suffolk Water
In order to achieve this programme, the team had to think creatively about construction and embracing off-site build; some examples are:
- Use of concrete slabs for the internal wall of the building instead of conventional brick or block.Filters pre-loaded with nozzles ready for the sand and media.
- Motive water pump skid.
- Poly dosing packaged plant.
- WQ monitors fully installed on a backboard layout.
- Disinfection install, with all key elements fully installed on back board ready to plug and play.
- B/W settlement tank with internal pumps already installed.
Putting all of these measures in place allowed the team to get from site mobilisation on the 20 February 2019 to having one of the four boreholes into supply on the 17 December 2019.
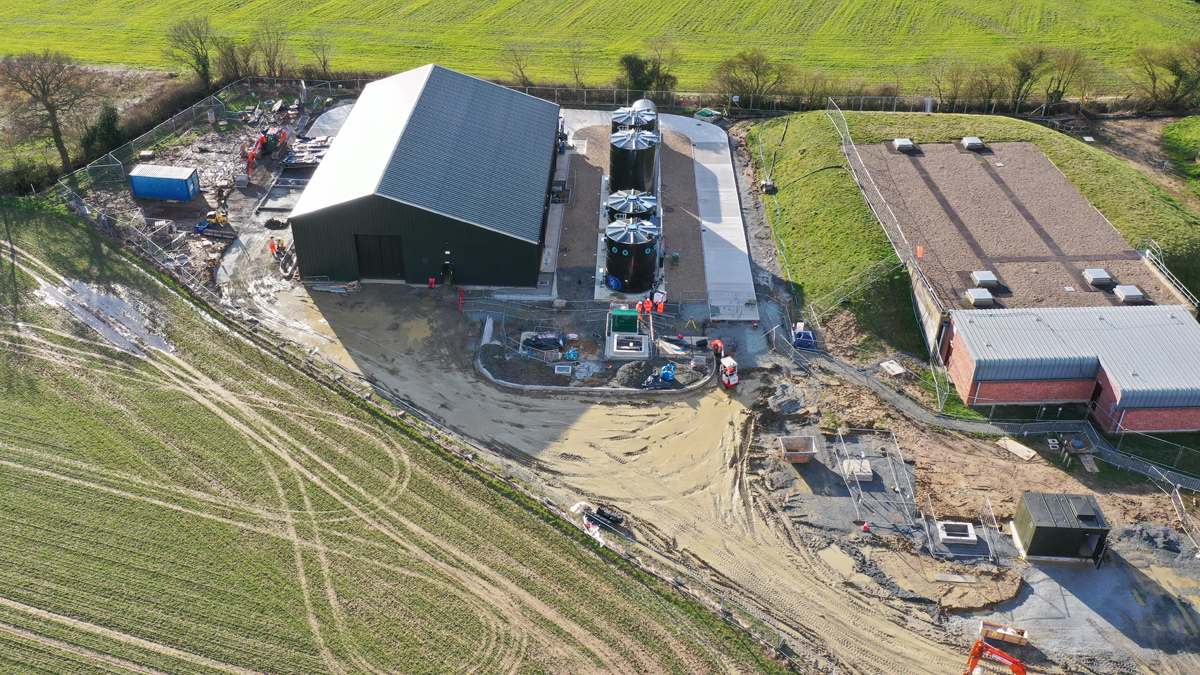
Structurally complete building and all five tanks in place (26 February 2020) circa one year on from starting on site – Courtesy of Essex & Suffolk Water
Programme dates
- Project conception: 17 July 2018.
- Investigate and define budget approved: 5 August 2018.
- Investigate and define contract awarded: 17 August 2018.
- Full project budget approved: 5 November 2018.
- Enabling works: 13 November 2018.
- Main project design and construct option C contract awarded: 3 January 2019.
- Mobilise to site: 20 February 2019.
- Disinfection contract awarded: 8 April 2019.
- Disinfection commissioning: 19 August to 6 September 2019.
- Process commissioning: 23 September to 16 December 2019.
- In supply: 17 December 2019 (only one bore water source was used in the process commissioning).
- Further commissioning on three other bore sources all with varying levels of iron and ammonia: 6 January to 16 March 2020.