Christchurch STW Inlet Rising Main Renovation (2018)
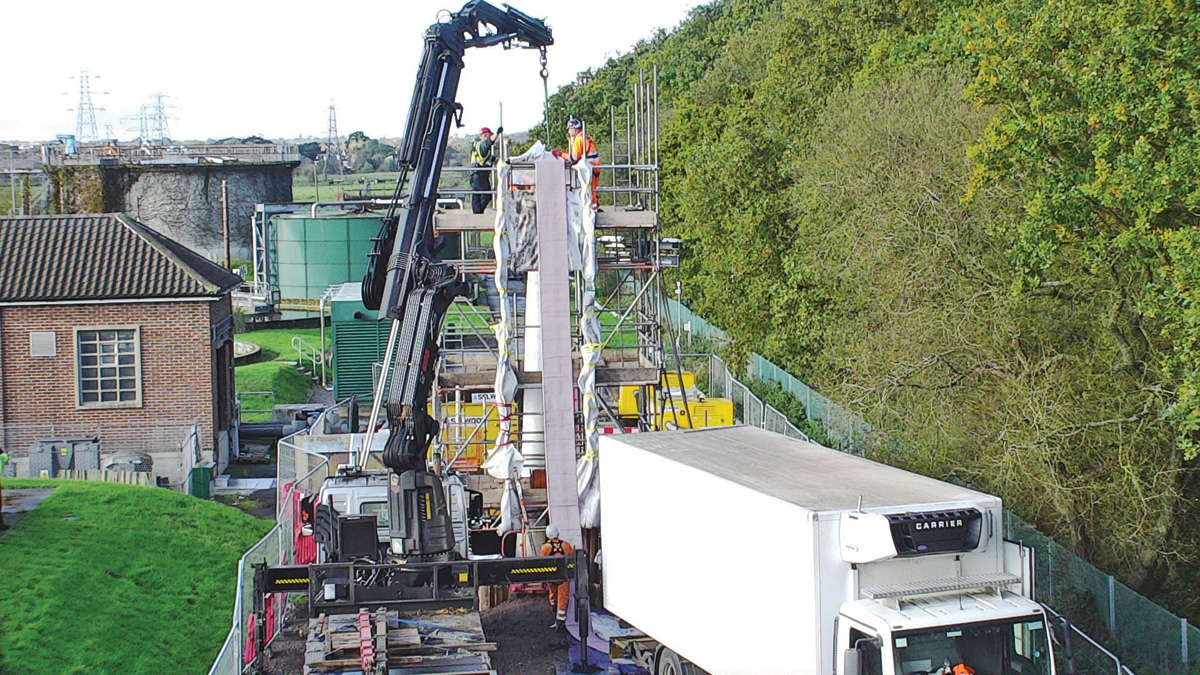
Staged lifting of the CIPP liner - Courtesy of Wessex Water
A burst occurred in a section of 400mm DI rising main within the curtilage of Wessex Water’s Christchurch sewage recovery works in Dorset. The works serve a population in the adjacent catchment of 59,000. The location of the burst was close to a bend in the main, beneath a large diameter primary sedimentation tank, and in a position, which excluded excavation as a means of repair. The failure was found to represent a radial split in the invert of the rising main, and when drained, a plume of groundwater was observed entering the pipe.
Failure of the rising main
The cause of the failure remains unknown, but it is assumed that differential settlement due to changes in effective stress of the local geology resulted in the defect.
Fortunately, there was sufficient land adjacent to the existing rising main to establish an over pumping system, with a tee on the lower end some 120m from the discharge point into the header tank. This allowed an excavation some 4m deep to cut into the rising main. A CCTV survey demonstrated that the main appeared to be in reasonable condition, but access to the damaged area precluded any internally deployed ‘spot repair’, which could resist operating pressures and velocities in the long term. The decision was made to line the sewer with a mixed glass and synthetic fibre cured-in-place pipe (CIPP) pressure liner, otherwise known as glass reinforced fibre (GRF) CIPP as named by Louisiana Tech University (USA), capable of transit through the single long radius 45° bend close to the works.
Design and procurement
Although GRF CIPP or their predecessors, have been available since the 1970s, there remains no internationally published design procedure for pressure liners, and our adoption of this type of lining intervention, at this time, was due to the impending release of ISO 11297 : 2018. This ISO is a manufacture and installation standard, and we undertook a bespoke design with Dr John Gumbel of JG Pipeline Consultancy Ltd.
Compared to mainland Europe, there have been relatively few GRF CIPP installed in the UK and Dr Downey, of Trenchless Opportunities Ltd, records show that Eric Wood the inventor of CIPP, along with his colleagues undertook, just over 100 schemes in the 1970s under license to Edmund Nuttall, who set up their Permaline Division in 1973 based in Ossett. The vast majority of which were for industry and not the municipal water undertakers. These included half dozen projects for Steetley Minerals abstracting seawater for magnesia processing, and a number of cooling lines for the CEGB.
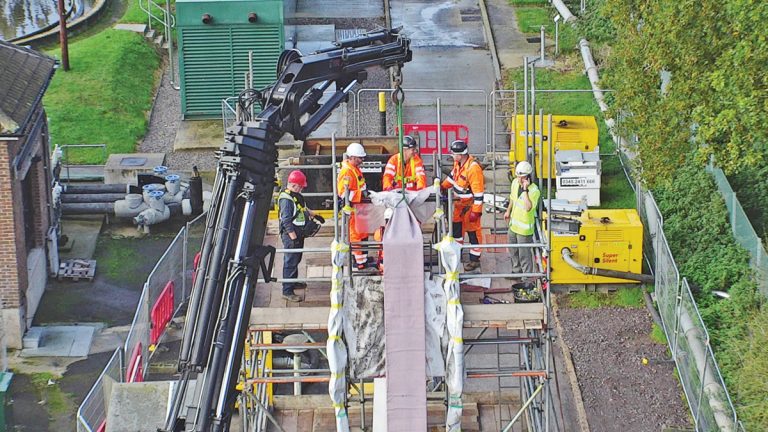
Staged lifting of the CIPP liner – Courtesy of Wessex Water
Also notable were a number of kaolin process lines for ECLP pumping clay and sand in suspension lined in 1977-1978.
From an International perspective, E.W. Avent of the UK acquired the licence from ‘Phoenix AG’ to install the Japanese hose lining system they acquired from Osaka Bosui; ‘Phoenix AG’ was used extensively in Europe for water and gas lines. It is therefore evident that a great deal of experience has been generated in the Far East and mainland Europe, and the chosen lining on this occasion was procured from NordiTube Technologies, who has worked worldwide.
The chosen system constituted the ‘NordiPipe WPP’ in a 6mm final thickness and was installed by framework contractor Onsite Central Ltd. The design offered by the supplier was based on the American standard to ASTM F1216-16, and three design cases were considered:
- Resistance to sustained groundwater head (Hw), assuming rising main left empty for a lengthy period and hence applying long-term (50-year) liner stiffness characteristics.
- So-called ‘fully deteriorated’ case of full soil, traffic and groundwater acting directly on the liner pipe as if buried.
- Short-term resistance to a full 1.0 bar negative pressure surge, as specified.
Case 2 was not considered relevant, as the pipe was in relatively good condition, when cut-outs were examined. Case 3 rather than case 1 proved the critical determinant of minimum wall thickness.
For the case of internal loads, ASTM F1216 considers liner resistance to burst under circumferential tensile stress, but neglects to consider longitudinal forces induced in the liner either directly by pressurisation, and/or as a result of joint movement or thermal shrinkage of the liner from its curing temperature. These forces were however analysed in detail by Dr Gumbel, along with the estimated reduction in liner longitudinal tensile strength associated with folds expected to form on the inside of the bend, and found to be the critical design limit state for resistance to positive surge pressures.
Christchurch STW inlet rising main renovation by GRF CIPP lining: Supply chain
- Client, design and civils: Wessex Water YLT E&C
- Consultant for lining design: J G Pipeline Consultancy Ltd
- Consultant for lining procurement and installation: Trenchless Opportunities Ltd
- Main contractor: Onsite Central Ltd
- Suppliers of lining: NordiTube Technologies
- Safety showers & eyebaths: Aqua Safety Showers International Ltd
Liner preparation and insertion by scaffold eversion
Liner resin impregnation can be challenging. The liner is effectively a polyester and glass felt tube with an exterior polypropylene coating a few millimetres thick, which encapsulates the resin and prevents leakage from the liner until the liner is everted into the rising main. To enable successful liner compilation the resin has to be vacuum impregnated at a temperature between 10-15°C, to allow reduced resin viscosity. Immediately upon impregnation, the epoxy two-part resin mix has to be cooled to extend the ‘pot life’, and the liner transferred to a refrigerated delivery vehicle.
Initial preparation of the host rising main, included an ultra-high-pressure, 10,000 psi, descaling of the host pipe. To stem the gushing groundwater from the radial fracture of the host pipe, a ‘cured in place repair’ (CIPR) was installed to WIS 4-34-06 : 2010. The silicates in the CIPR were tolerant of fast flowing phreatic groundwater, which would otherwise dilute and compromise the epoxy saturated resins in the primary rising main liner. This groundwater regime was exacerbated by the cyclic recharge of the normally unsaturated sand geology in the vadose zone by the adjacent tidal River Stour, which was a consideration of design case 1. A considerable groundwater flow was removed during the works by ‘well pointing’ with fines migration control from within the trench sheets of the excavations.
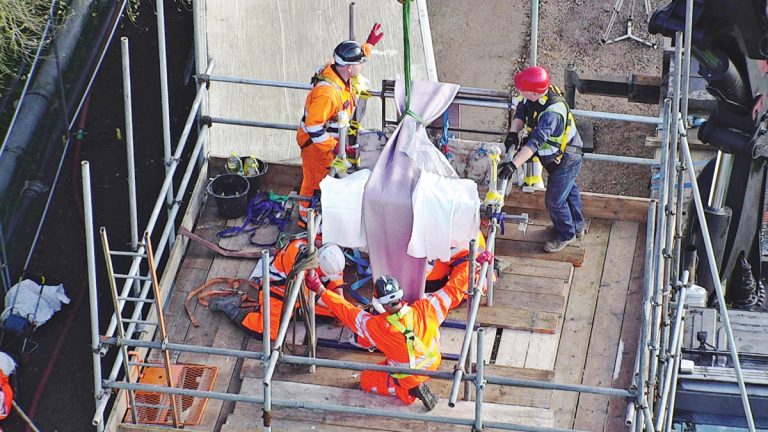
Staged lifting of the CIPP liner – Courtesy of Wessex Water
The primary Norditube WPP liner was everted through the host pipe by water head and hot water cure was considered the best mechanism for initiating the cross polymerisation of the liner. This ensured a more holistic cure, with a greater certainty of control of the liner’s temperature gradient throughout the cure cycle. The installation process required a 10m high eversion scaffold tower to overcome frictional pipeline losses and the viscosity of the geometry of the everted liner.
The liner had no continuous longitudinal axial glass reinforcement and to minimise any potential tensile forces subjected to the liner during elevation onto the scaffold, and reduce any stress of the fibreglass layers, the liner had to be lifted onto staged platforms, pre-built into the scaffold structure. As the liner was everted into the rising main, any sections of liner not supported by the internal periphery of the existing rising main, were provided with reinforcing jackets, to prevent radial over-expansion.
The liner was cured over an 8-hour period to ensure cross polymerisation and left quiescent to cool prior to dressing of the liner ends. To seal the liner ends, WEKO seals were installed to prevent any possibility of flows passing between the liner and the host pipe. These seals have a rubber membrane, with stainless steel retaining bands, installed hydraulically over the liner end.
Post installation, pressure testing saw blanking plates bolted to the stub pipe ends and was applied to the renovated section, all in accordance with current testing standard IGN 4-01-03 (Issue 2).
Conclusion
The lining was one of two viable solutions, the other was to reconstruct the rising main above ground on piers or pillars. This alternative option would have taken some months to design and complete at an estimated cost of £300k. The lining solution ensured the liner was on site ready for insertion within a month of approval, and has been working well since completion, at a fraction of the cost of the former solution.
Wessex Water is establishing a design and procurement protocol for a wider use of GRF CIPP in AMP7 potentially with a matrix of capabilities of various lining systems from around the world, suited and bespoke to the physical characteristics of the rising mains in question and their operational variance.