Durleigh WTC (2021)
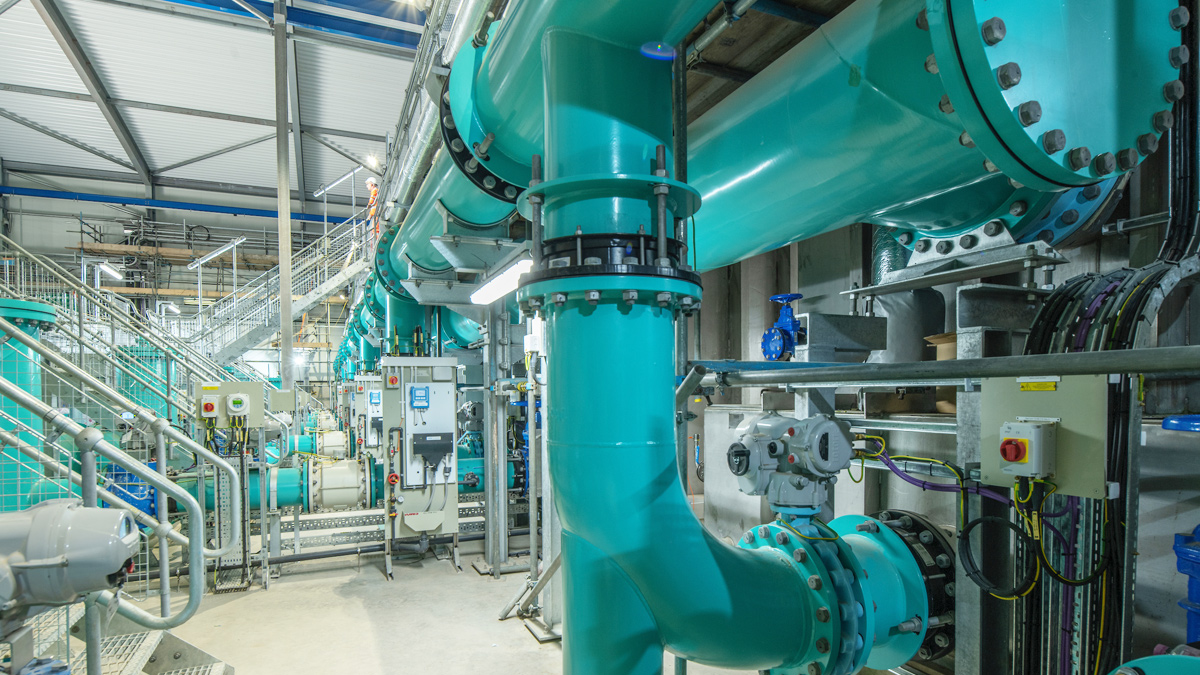
Main treatment building RGF pipework - Courtesy of Wessex Water
Wessex Water’s £50m project to upgrade Durleigh Water Treatment Centre (WTC) in Somerset is progressing on programme and within budget, despite some particular challenges posed by the Covid-19 pandemic. Work at the site near Bridgwater started in 2019. It is the largest single-value scheme delivered by Wessex Water’s Engineering & Sustainable Delivery (ESD) department and forms part of the company’s long-term water supply strategy for Somerset. Drawing from Durleigh Reservoir to the west, the old centre had come to the end of its operational life and extensive reconstruction was needed to maintain delivery of the highest quality drinking water to a population of 44,500.
This paper follows on from an initial case study in 2020 and details the progress of the works at Durleigh WTC.
Digital delivery
The Durleigh project is the first major project to be delivered by ESD, utilising Building Information Modelling (BIM), with AECOM appointed to deliver the digital design using the Autodesk suite of products and Bentley’s ProjectWise software for the common data environment.
The digital delivery processes created at the outset of the project included BIM 3D modelling which has enabled the team to successfully deliver challenging programme commitments throughout this complex and large-scale construction project.
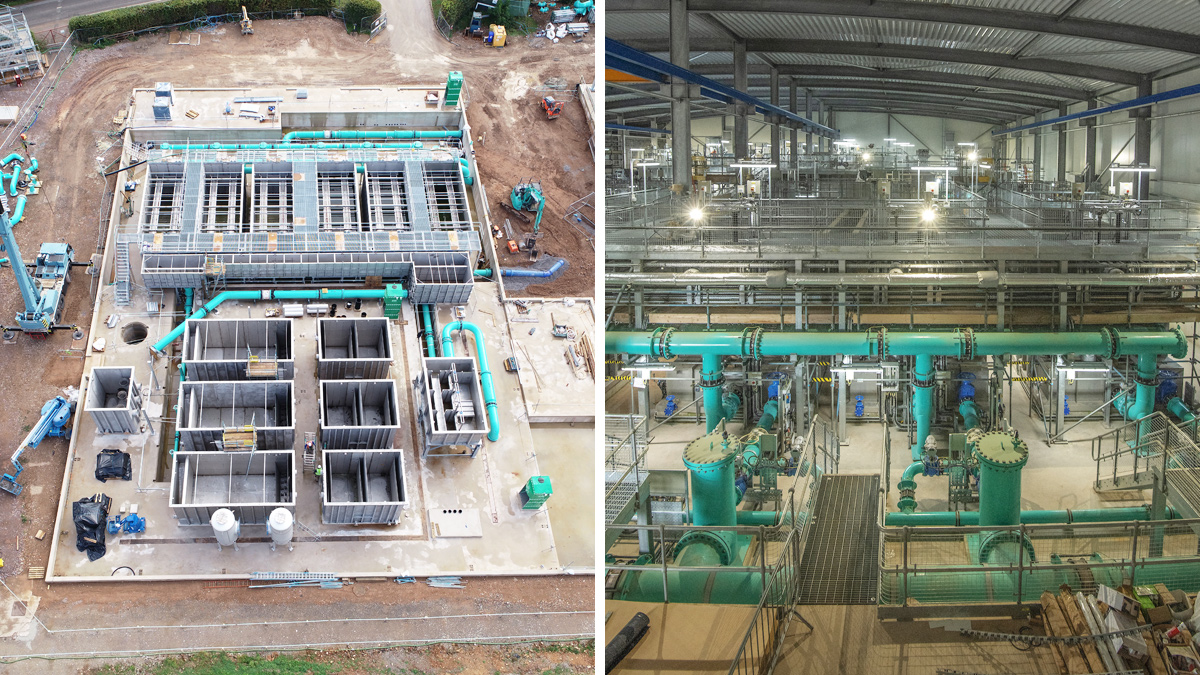
(left) Durleigh WTC in October 2020 and (right) inside the main treatment building – Courtesy of Wessex Water
The benefits experienced from using BIM 3D modelling include:
- Design for manufacture & assembly (DfMA): The model provided certainty during off-site manufacture and modular construction allowing first time installation on site.
- Time savings: A common data environment enabled an easier way of working and quicker information exchange.
- Cost savings: Fewer changes, better clash detection, potential improvements in future facilities management and maintenance.
- Material savings: Material savings in the amount or type of materials used and corresponding environmental benefits from using fewer materials.
- Risk reduction: The 3D model gave improved project and asset information accuracy and subsequent associated costs, delivery timeline and risk management.
- Health & safety Improvements: The 3D model provided a visual basis for:
- Improved access lifting and maintenance reviews during the design stage.
- Optimising the sequencing of construction and installation activities.
- Improved staff briefings and training.
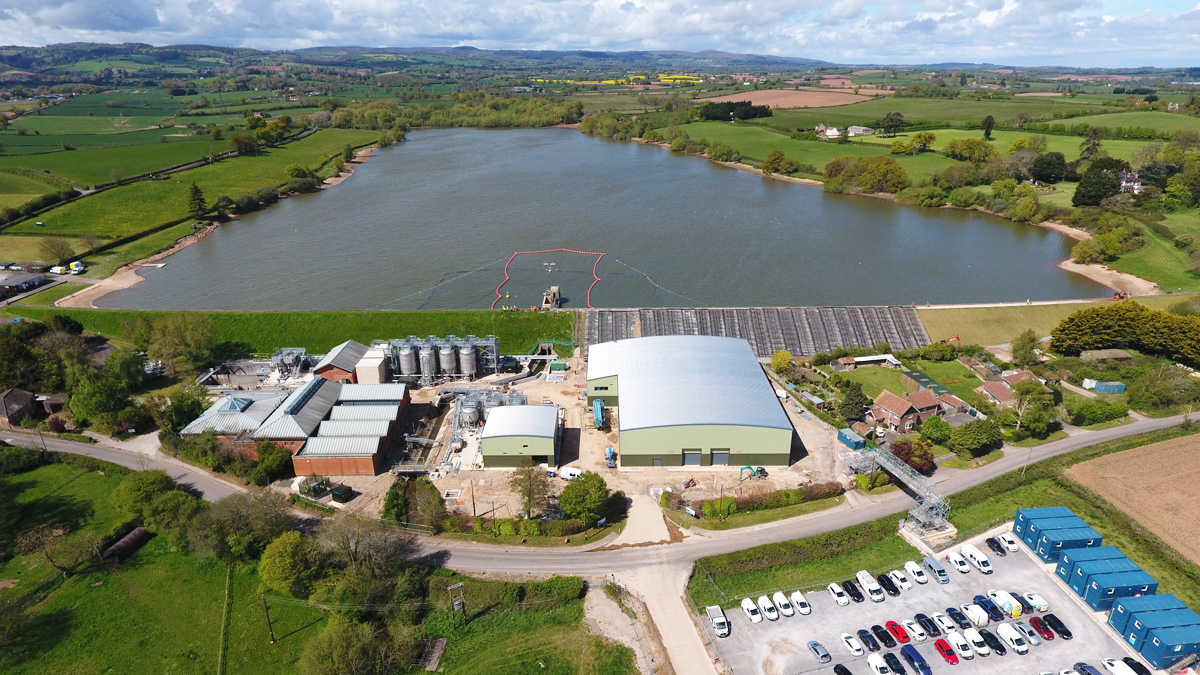
Durleigh WTC and reservoir – Courtesy of Wessex Water
Stakeholder engagement
A collaborative approach by all key stakeholders, both internally and externally, has ensured the goals and aspirations of all parties are aligned. A number of facilitated workshops took place where key members of each team came together to understand individual drivers and how these key team members can influence the strategy and philosophy for delivery.
ESD seconded a number of staff into the project team from other Wessex Water departments to ensure the project meets its required outputs. The project team have liaised closely with all departments throughout the development of the design, construction and early commissioning activities, with further meetings and discussions scheduled to take place through commissioning to takeover and closedown of the project.
ESD construction update
The project delivery has been led by an entirely internal team from Wessex Water ESD, with the Capital Project Delivery team working closely with ESD’s various in-house teams including design and construction divisions including civils, mechanical & electrical, commissioning and automation. Having all the key partners as internal departments resulted in inherent close coordination throughout, with all parties working towards a common goal and driving genuine collaborative behaviours both on and off site.
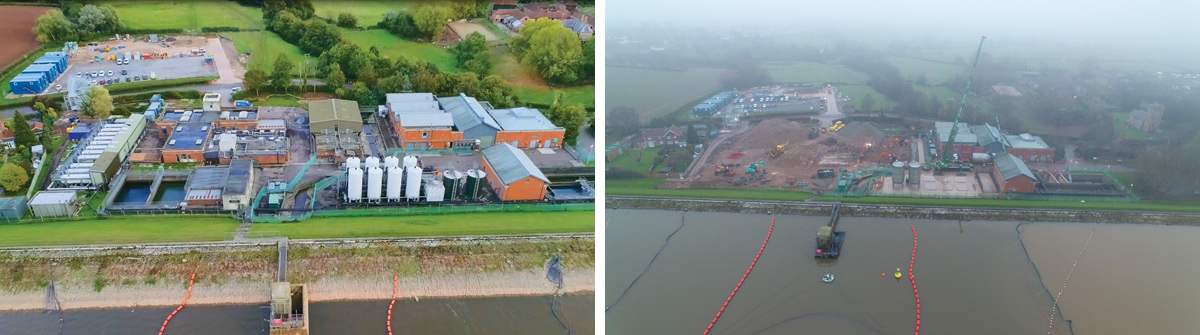
Durleigh WTC (left) original works pre-construction, September 2019 and (right) demolition of the original works underway, January 2020 – Courtesy of Wessex Water
ESD’s new off-site build facility has manufactured and delivered many fabricated items for the Durleigh project that would previously have been constructed on site. Items such as pump skids, motor stands and junction boxes have all been manufactured remotely in ESD’s factory in Salisbury and delivered to site, bringing with them many benefits in terms of health and safety, quality, programme and cost.
One of the key factors behind the success of the project to date has been the implementation of an off site secure M&E storage warehouse local to the construction site. This has enabled equipment to be ordered and delivered in advance, thus ensuring availability on site when needed and removing reliance on third party delivery coordination. This was particularly evident during the long-lasting effects of Covid-19 and other external influences on the wider market, ensuring the project was much more resilient throughout.
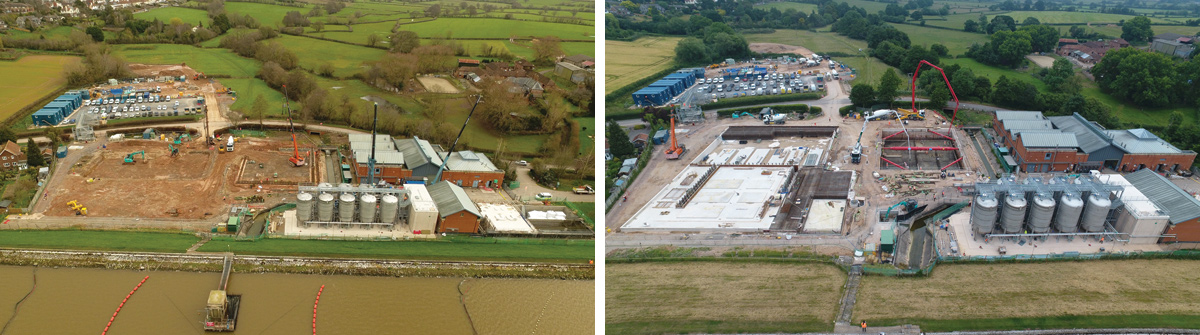
Progress at Durleigh WTC (left) March 2020 and (right) June 2020 – Courtesy of Wessex Water
Demolition, refurbishment and restructuring
Extensive surveys of the old water treatment centre were conducted to establish which structures could be repurposed, refurbished, or recycled. 70% of the old WTC has been demolished and recycled, outdated equipment decommissioned and removed with 30% of structures repurposed and/or refurbished.
Demolition was complete and all was going according to plan when Covid-19 emerged in March 2020, forcing a change in working practices.
The site was closed for a week at the start of the pandemic and the project team conducted a site impact assessment, with new rules drawn up on social distancing and reduction of the maximum number of people able to attend site safely.
The pandemic has certainly impacted the project’s opportunities for early completion, but the whole team deserve great credit for the way they have adapted and taken it all in their stride.
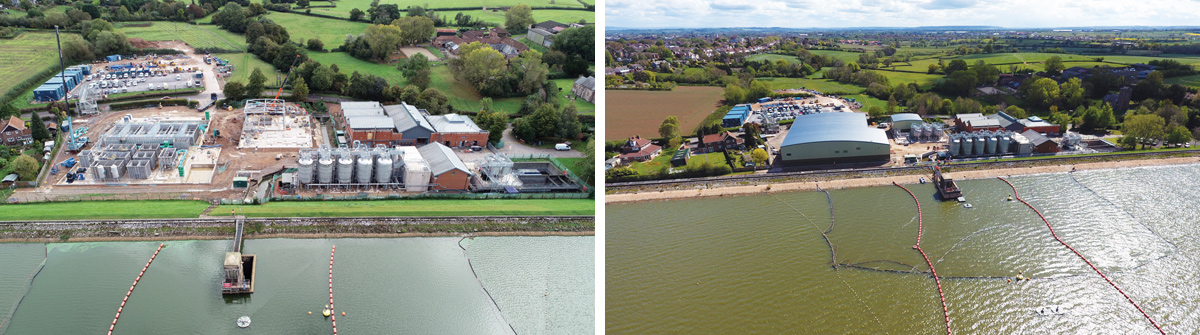
Progress at Durleigh WTC (left) October 2020 and (right) September 2021 – Courtesy of Wessex Water
Chemical building
Refurbishment of the existing chemical treatment building is ongoing and forms a crucial phase of the project. The building has now been restructured, housing refurbished contact tanks, refurbished chemical storage tanks and bunds, installation of new chlorine and sulphur dioxide storage and dosing, high lift network distribution pumps, UV treatment, additional chemical storage and dosing, emergency power generation along with a new power distribution board, several motor control centres, programable logic controllers, a secondary supervisory control and data acquisition (SCADA) system together with full building ventilation systems.
Power distribution
A secure compound has been constructed adjacent to the building, housing a new transformer, switchgear and ring main unit required as part of an upgrade to the 11kV power supply. The transformer supplies the main distribution board (MDB) and motor control centres (MCCs).
Wastewater area
Existing wastewater tanks and an existing workshop to the west of the site have also been retained, re-configured, and re-purposed to meet the new process design requirements. Construction of a new reinforced concrete slab over the existing re-configured wastewater tanks is complete and forms the base for the newly installed sludge thickening lamellas.
The mechanical and electrical works were completed inhouse by the Wessex Water ESD MEICA team and commissioning commenced in June 2021.
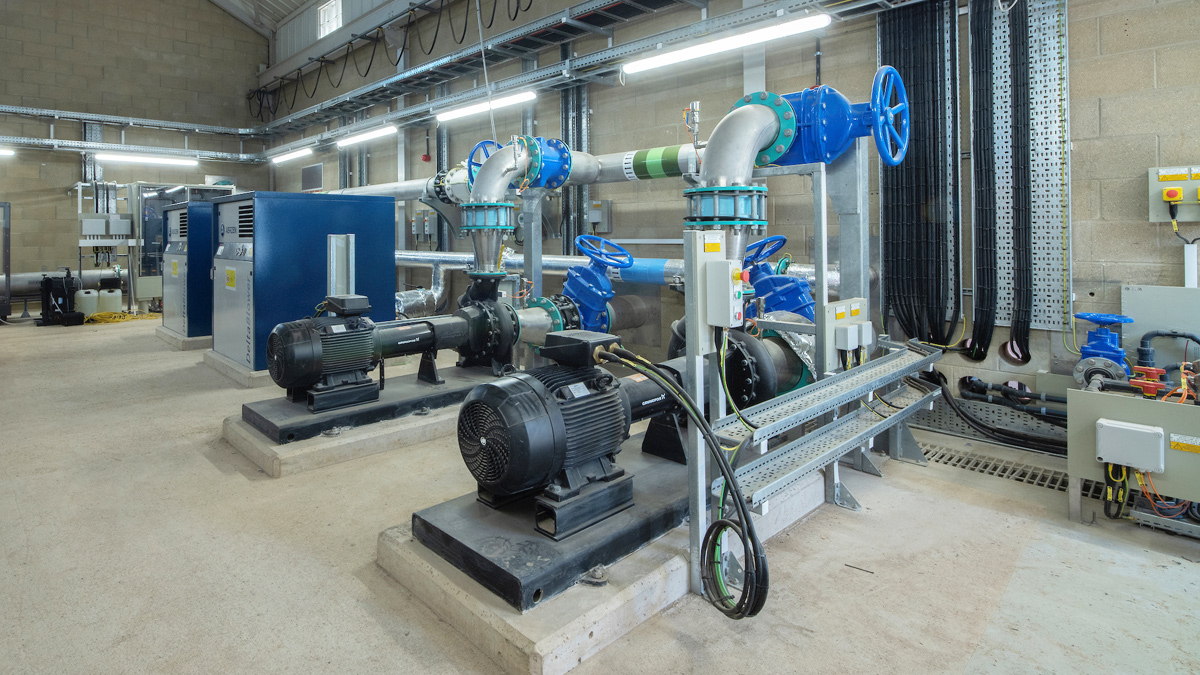
Waste building – Courtesy of Wessex Water
Durleigh Reservoir
The existing reservoir tower equipment has been refurbished with a new bridge, inlet valves, inlet screens and reservoir monitoring equipment installed. ESD Civils have protected the reservoir bank against overtopping in extreme weather events by provision of a geomat, comprising an asphaltic membrane geomesh, installed over the downstream slope of the dam.
Durleigh WTC Reconstruction: Supply chain – key participants
- Principal contractor: Wessex Water ESD
- Principal designer: AECOM
- Temporary works design: Pell Frischmann
- Process design: Stantec UK
- Piling: DAWSON-WAM Ltd
- Formwork & reinforced concrete: Carney Construction
- CFD modelling: The Fluid Group
- Temporary works & shoring: MGF Ltd
- Building cladding: Cover Structure
- Building structural steelwork: Steel Fabrications
- Geomesh: Hesselberg Hydro
- Tank & vessel manufacturing: Vessco Engineering
- Vessel manufacturing & access steelwork: Berry & Escott Engineering
- Access steelwork: Dan’s Engineering
- Pumps: Xylem Water Solutions
- Valves: AVK UK Ltd
- MTB electrical installation: Field Systems Design
- Large bore pipework: Powerrun Pipe-Mech
- Chemical dosing & sampling systems: MBH Engineering
- Chemical dosing & sampling systems: DMS Engineering
- MDB/MCCs: GPS Group
- Ventilation: M&R Airflow
- Project & O&M documentation: Project Support Systems
- Water quality monitors: SWAN Analytical UK Ltd
- Water quality monitors: Malvern Panalytical
- Water quality monitors: Yokogawa UK Ltd
- Water quality monitors: ATi UK
- Water quality monitors: Metrohm
New build
GAC area
Whilst demolition of the existing structures was being completed, ESD took the opportunity to progress the design and construction of the GAC area early in the programme. This area is now complete, consisting of nine 4.3m diameter GAC vessels, each loaded with 57m3 of GAC media, with 1362m of large bore stainless steel pipework and 70 tonnes of metalwork installed around the GAC vessels. The construction, installation and dry tests are now complete along with pre-use safety inspections, meaning the GAC system is fully ready for process commissioning.
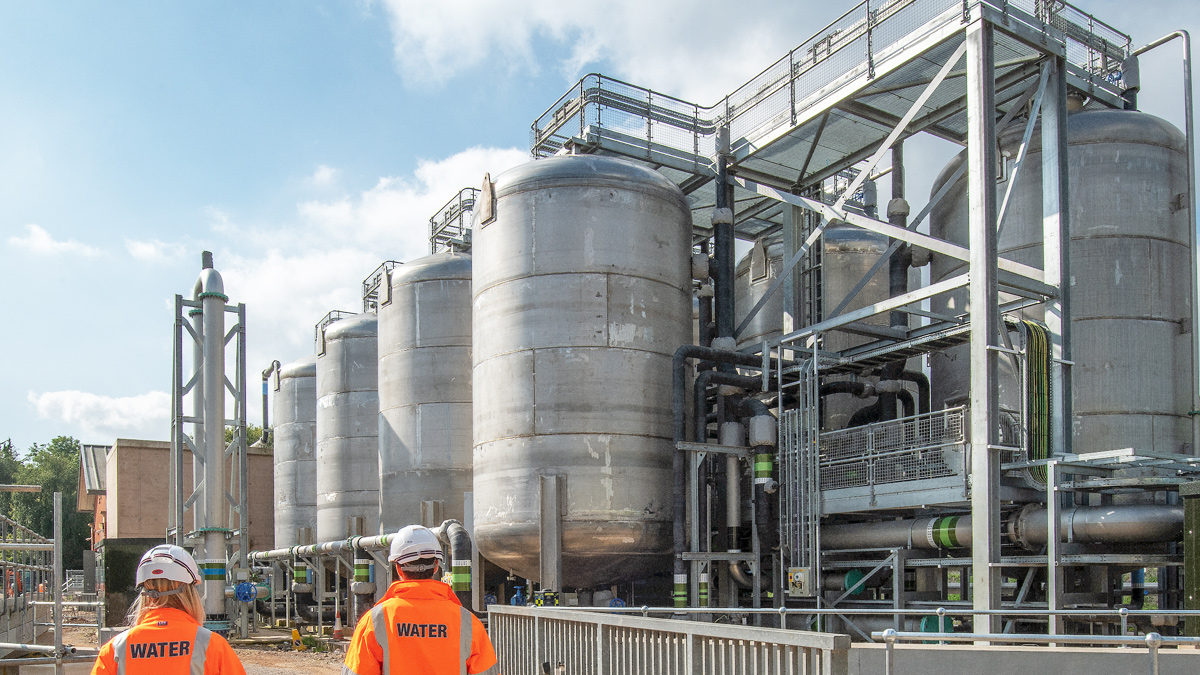
GAC area – Courtesy of Wessex Water
Main treatment building
Construction of the new main treatment building (MTB) is complete, including piled foundations, split level reinforced concrete bases (1583m3 tied to 250 continuous flight auger piles each 16m deep) together with security cladded steel frame building. Installation of all process tanks is complete, with mechanical, electrical, control and automation works nearing completion and mechanical and electrical dry testing commenced.
Collaboration between ESD Civils and M&E teams resulted in a reduced construction programme sequence, whereby the main foundation structure was constructed, then all large tanks, pipework and walkways were lifted into position, prior to the building structural steelwork being erected. In total 14 stainless steel tanks have been installed in the main treatment building, all of which were manufactured and tested off-site. Close coordination ensured each tank was placed into position within two of hours of being delivered to site.
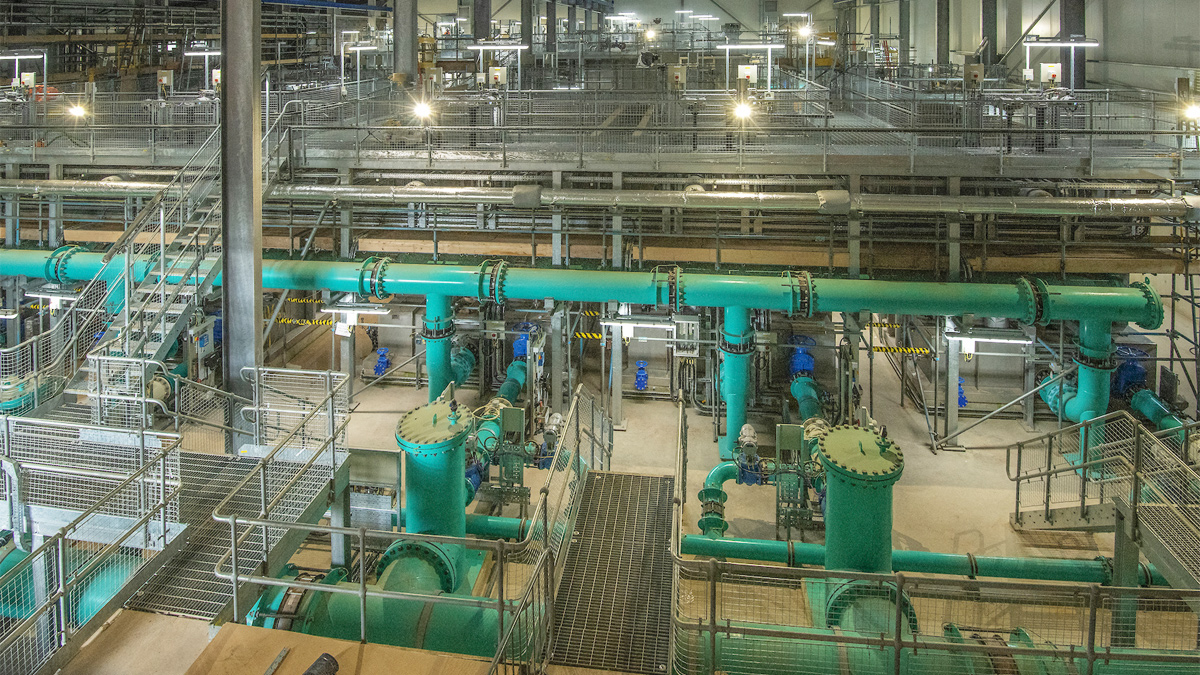
Inside the main treatment building – Courtesy of Wessex Water
The large-bore pipework and metalwork was installed over a period of three months before the building was erected. The installation of the remaining small-bore pipework, access metalwork, process equipment and water quality monitors was completed using the two 2-tonne overhead cranes where necessary.
In total 632m of pipework and 58 tonnes of metalwork were installed within the main treatment building.
Process electrical works started in January 2021 and were completed in June 2021, with 34,000m of cabling installed and tested. MCC 4 (the main hub for all power and control in the building) was delivered in February 2021 and powered up in June, allowing commissioning to commence.
The main treatment building also houses a new administration block containing the water treatment centre reception area, welfare facilities, motor control centre, laboratory, main control room and the primary SCADA system.
Low lift pump area and manganese process
The new low lift pump area (LPA) including backwash, forward flow and waste transfer pump stations, motor control centre, manganese pressure filters and associated interconnecting pipework and cabling is also nearing completion.
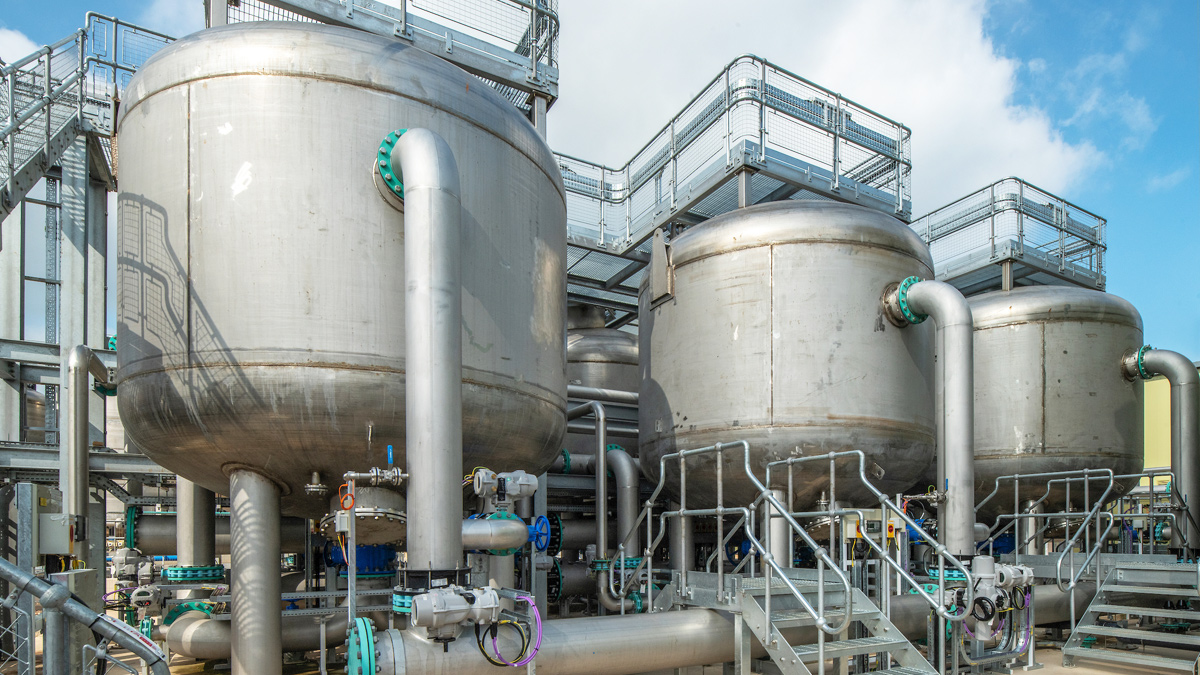
Manganese pressure vessels – Courtesy of Wessex Water
Underground tanks were constructed using 600mm diameter secant piles forming the temporary and permanent works. The base of the tanks was poured in one day (858m3 of concrete), with the main soffit taking two days. Six stainless steel manganese pressure filter vessels were then sited directly on top of the storage tanks.
The manganese pressure filter vessels were manufactured and tested off-site, delivered in two banks of three with two months between each delivery, close coordination again allowed installation within a few hours of arriving at site. The pipework and metalwork installation followed delivery of the first bank of three vessels.
In total 554m of large bore stainless steel pipework and 18 tonnes of metalwork were installed around the six new manganese pressure filter vessels. The pipework was built off-site on supporting frames and assembled in situ to reduce overall site installation time.
Following the LPA building erection, installation commenced for the end suction manganese forward flow pumps, rapid gravity filter (RGF) and manganese backwash pumps, waste tank mixers and transfer pumps, manganese blowers, water quality monitors and the MCC. This allowed electrical works to commence in February 2021, completing testing in June and enabling MCC 3 to be powered up in July, triggering the start of commissioning in this area.
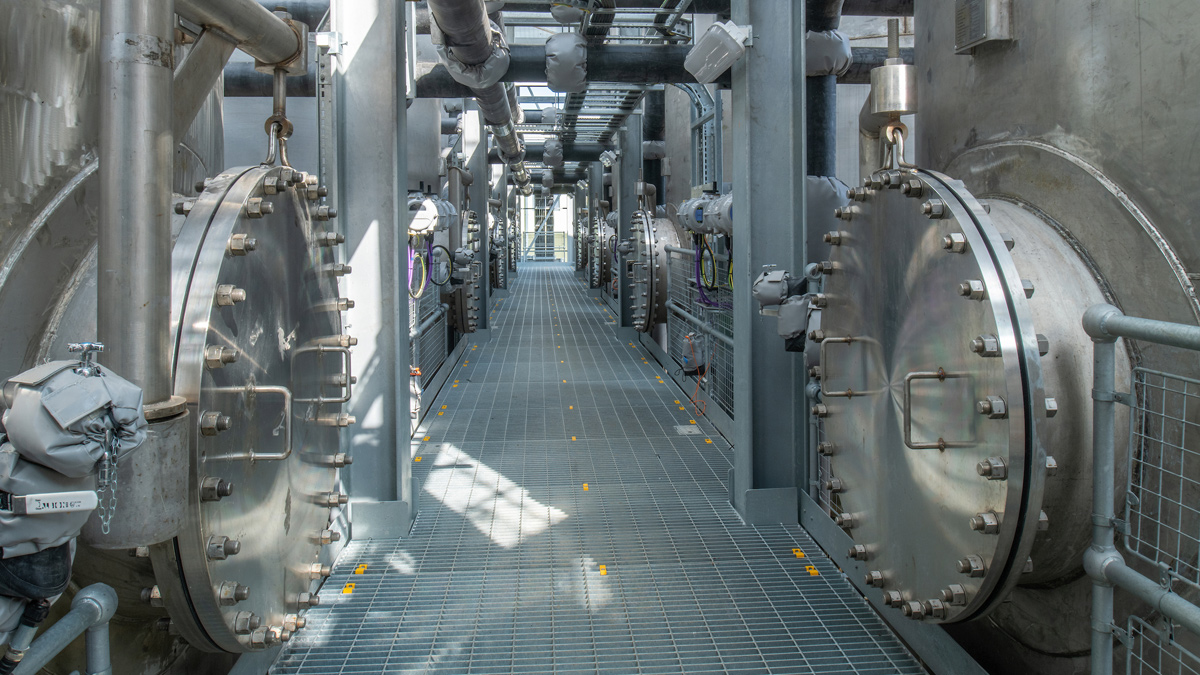
GAC vessel platform – Courtesy of Wessex Water
Automation
The site control and monitoring system consists of six high performance Siemens programmable logic controllers (PLCs) housed in four intelligent Profibus MCCs. The local monitoring system comprises dual redundant SCADA servers with a combination of distributed desktop and panel mounted IPC clients.
As with the majority of ESD schemes, the Durleigh PLC software, SCADA and telemetry configuration has been produced entirely in-house by a team of engineers from the ESD automation team. Use of the highly experienced in-house team has improved continuity and flexibility, and assured high quality software using tried and tested function blocks and graphical objects.
The functional design specification (FDS) which details the software requirements, including normal and abnormal operation, setpoints, alarms and interlocks was also produced in-house by staff from the ESD commissioning and automation teams, and by staff from operations.
All PLC software and SCADA configuration has been extensively tested offline using PLC simulation techniques prior to delivery to site. Using the in-house capability has made design changes very easy to implement. Changes are tracked using a SharePoint based ticketing app developed by Wessex Water specifically for the ESD automation team. The app runs on mobile phones, tablets and laptops to make it easy to raise, track and sign off bug fixes and design changes. The app also feeds into the process to produce ‘as built’ documentation.
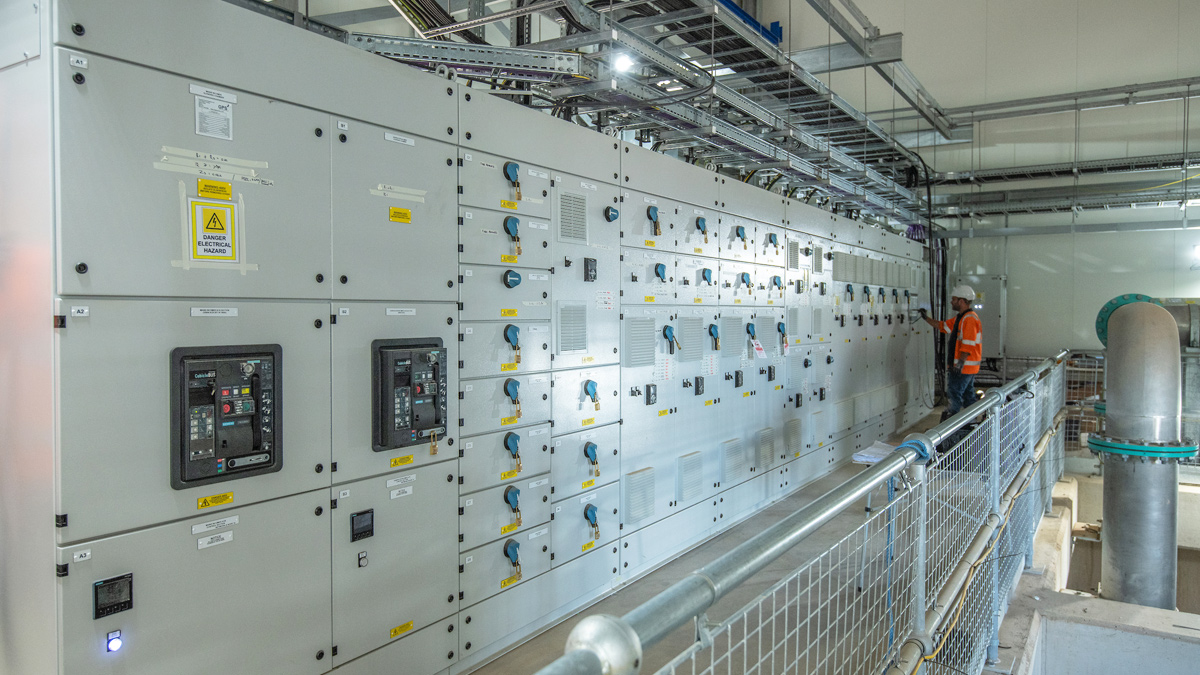
Low lift pump area MCC – Courtesy of Wessex Water
All PLCs are connected using high speed, dual redundant, fault tolerant fibre networks. An isolation network has been provided for inter-PLC communications. Additional networks have been provided for SCADA server to PLC data communications and SCADA server to client communications using VLANs.
Secure remote access and communications with Wessex Water’s telemetry system uses an industrial router, the primary connection of which is DSL with an automatic fail-over to cellular. Remote access has proven invaluable for both automation and commissioning engineers, particularly with a reduced site presence due to Covid-19 restrictions.
Durleigh is the first site in Wessex Water to use DNP3 to provide all telemetry information, without the need for an outstation. Data generated by PLCs is made available directly to telemetry using dedicated DNP3 cards in each of the main PLC racks, removing the need to carry out complicated mapping between PLCs and to a telemetry outstation. The use of IP based DNP3 technology has drastically reduced the time taken to test telemetry signals.
Control and monitoring system statistics
Each of the PLCs contribute to the following statistics:
- High performance PLCs: 6
- Speed drives
- Fixed: 70
- Variable: 42
- Profibus valve actuators: 215
- Inputs
- Digital: 1,248
- Analogue: 544
- SCADA data points: 60,000
- Telemetry signals
- Digital: 3,000
- Analogue: 930
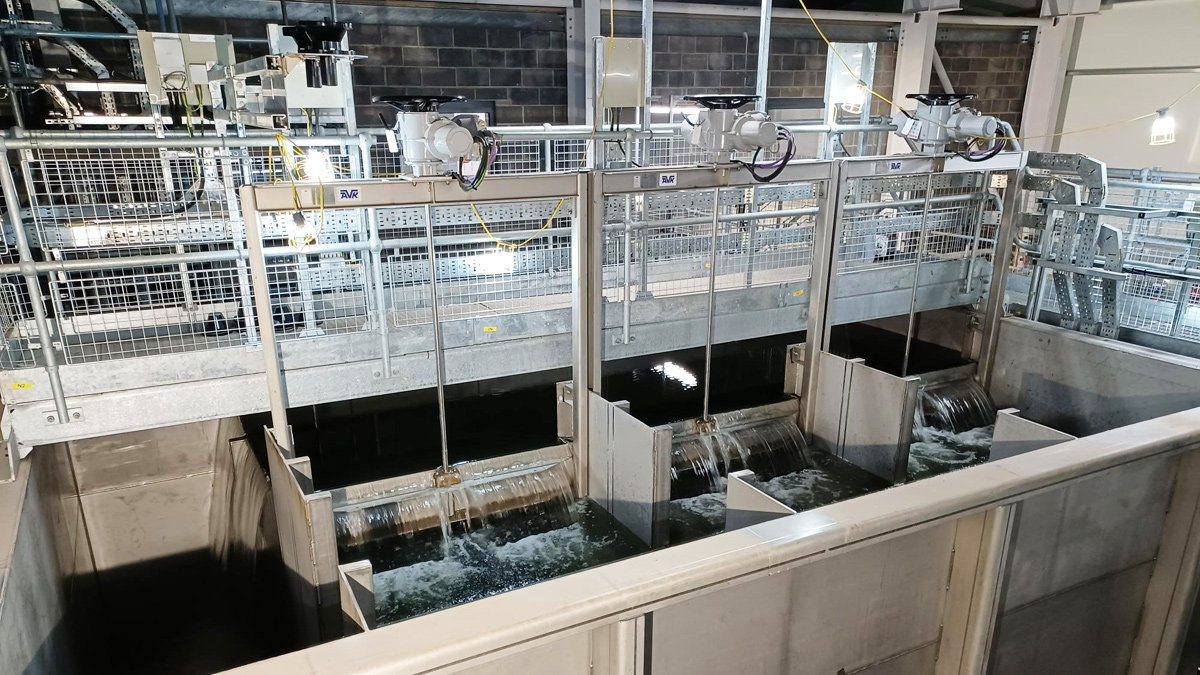
DAF inlet – Courtesy of Wessex Water
Commissioning
Staff from the in-house ESD commissioning team have been embedded in the project throughout the design and construction of Durleigh. Working in collaboration with the design and delivery teams, the commissioning team have developed a systemised, risk-based commissioning plan so that the scheme can be delivered as efficiently as possible.
In order to mitigate the risk of delay on site significant effort has been devoted to factory inspection and testing of complex, major or long lead time equipment to ensure that it delivers to the required specification. Early engagement with the suppliers and continued dialogue has been key to ensuring any issues that have been identified have been resolved in a timely manner.
The scheme is currently two months into the commissioning programme with early works focused on commissioning of the filter backwash and waste treatment systems to facilitate the commissioning of the main physical and chemical treatment processes over the remaining eight months.
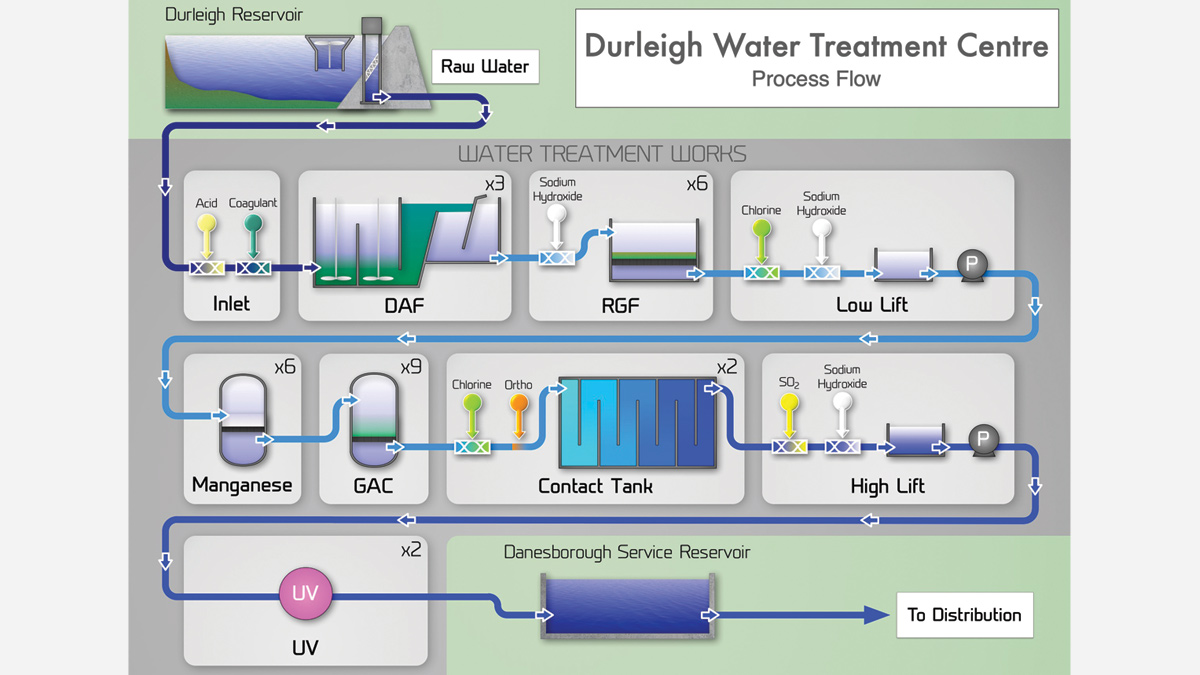
Durleigh WTC: Process flow – Courtesy of Project Support Systems
The next phase
Given the potential impact of Covid-19 on such a complex and large-scale project, it could easily have caused major delays. Everyone in the ESD team, AECOM and the supply chain deserve enormous credit. Whilst early completion targets have been adjusted the project is currently on target to return water back into supply in 2022.
Further case studies covering the remaining construction and commissioning elements of the Durleigh WTC Reconstruction Project will be published on this website and in future editions of UK Water Projects.