United Utilities Filtration System Replacement (2022)
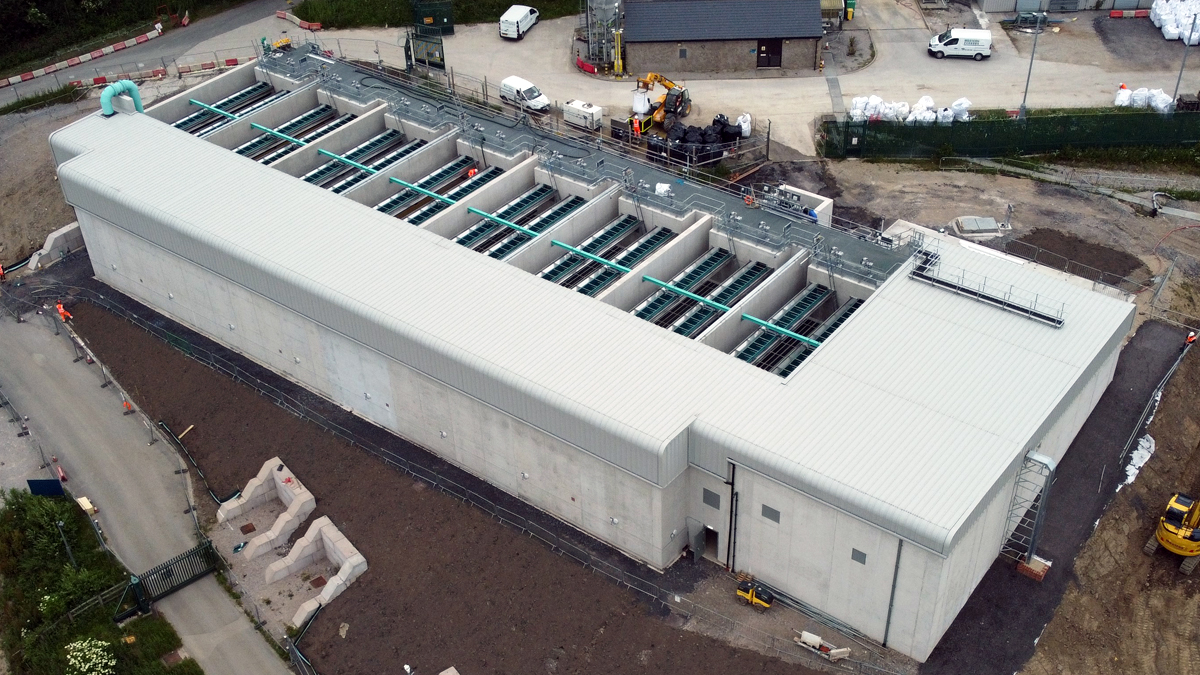
Aerial view of filter gallery - Courtesy of Mott MacDonald Bentley
In May 2018 United Utilities appointed Mott MacDonald Bentley (MMB) to deliver an NEC Option A design and construct project for the upgrade of one of their water treatment works (WTW) in the northwest of England. The project scope comprised upgrade of several key treatment processes to ensure compliance with Badenoch and Bouchier performance recommendations and DWI regulatory requirements. The upgrades would also reduce the average ‘unit cost to treat’ by maximising output from the WTW, making it the most cost-effective water treatment asset in the area. The design and construction were undertaken over a 36-month duration, with contract completion planned for January 2023.
Scope of works
The scope of works for the project, issued within United Utilities’s AMP6 programme, comprised the following:
- New rapid gravity filters, to replace existing bell pressure filters.
- New lamella clarifiers and flocculation tanks.
- An upgraded pH correction system.
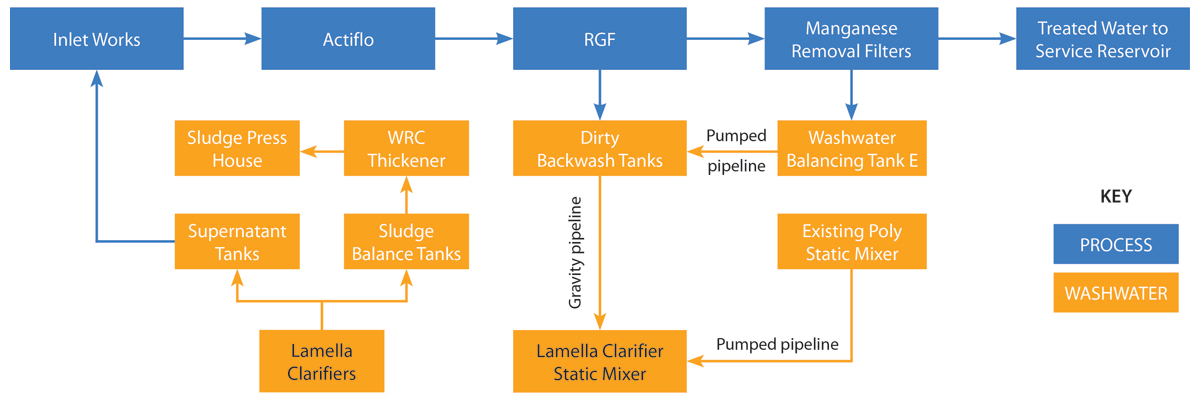
Schematic overview – Courtesy of Mott MacDonald Bentley
New rapid gravity filters
The structure: The existing WTW filtration process comprised of 147 (No.) bell pressure filters, constructed between the 1920s and 1950s. These had exceeded their asset life and were no longer compliant with United Utilities’ asset standards, resulting in inefficient operation and high operational costs with a need for frequent media replacement. The bell pressure filters were replaced with a new rapid gravity filter (RGF) structure comprising 8 open-topped cells with an operational surface area of 83m2 per filter. The structure incorporates an 830m3 clean water backwash tank.
The RGF structure is constructed on a piled foundation comprising 83 (No.) precast concrete piles with 49 (No.) circular steel tube piles installed at depths up to 5m, bearing on shallow bedrock. The structure construction comprises approximately 2,070m3 in situ reinforced concrete slabs and walls with a steel-framed portal frame roof structure with composite cladding over the filter gallery and mechanical control room. The walls on the northeast elevations incorporate a natural stone effect cladding to comply with planning requirements.
Autodesk ‘Robot’ finite element analysis of the RGF was used to aid optimisation of design structural elements.
A 3D geotechnical ground model was developed in Leapfrog for the RGF construction area using new and existing site information to inform ground risks and determine design criteria.
The rapid gravity filter cell design comprises a dual lateral block floor with an 800mm sand and 400mm anthracite media bed and each backwash operation generates 415m3 of water which is collected, cleaned and recycled via recirculation back to the head of the works.
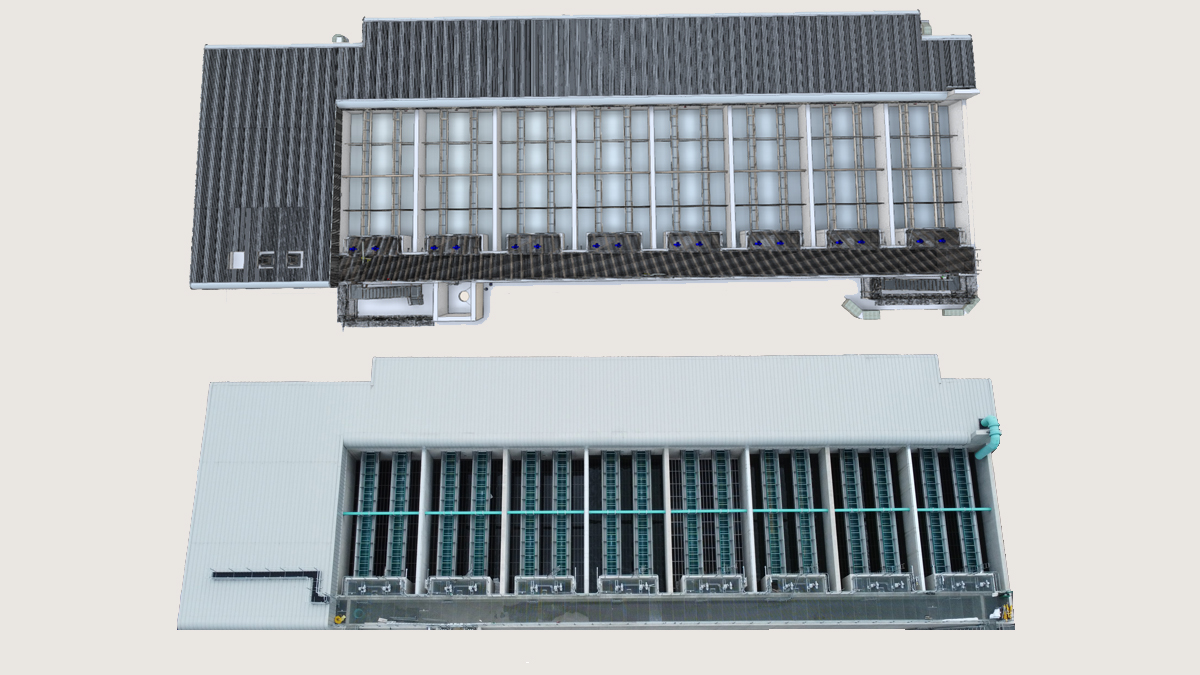
(top) Rapid gravity filter structure 3D model and (below) rapid gravity filter structure – Courtesy of Mott MacDonald Bentley
Inlet feed and outlet pipework to the RGFs comprise DN1000 restrained ductile iron sections connected to the live flow line via existing tee pieces, installed in 2003 as part of the original Actiflo plant construction. Design of the connections included a need for extensive thrust restraint in particularly constricted working areas between multiple process-critical pipelines. A non-conventional thrust block arrangement was developed with a reduced excavation requirement, allowing protection of the adjacent assets.
The RGF structure was constructed offline and is located at high level within the site to facilitate gravity outlet flow to the downstream treatment processes. The live 3D models were shared with MMB’s sub-contractors to ensure efficient and safe coordination of parallel design and installation works, minimising the risk of service clashes and resulting re-work.
An extensive and detailed hydraulic design was required to integrate the new assets into the existing treatment process over a wide range of flows and conditions, and this was supplemented by on-site pressure and flow logging to assess against real life data and iteratively fine tune the solution.
In particular, the assessment of RGF top water level at maximum flow was particularly sensitive to system friction and fitting losses. The data provided a clear understanding of the risk and provided confidence for both MMB and United Utilities in the suitability of the developed solution.
Throughout the design and installation period there was a sharp focus on the identification and development of innovative design and construction ideas, to improve efficiency and safety, and reduce capital and operational costs. Failure mode, effects and criticality analysis (FMECA) analysis was used to assess performance and resilience of valves and penstocks, and the delivery team were able to identify opportunities to provide valves that are lighter and easier to remove and replace than standard larger alternatives.
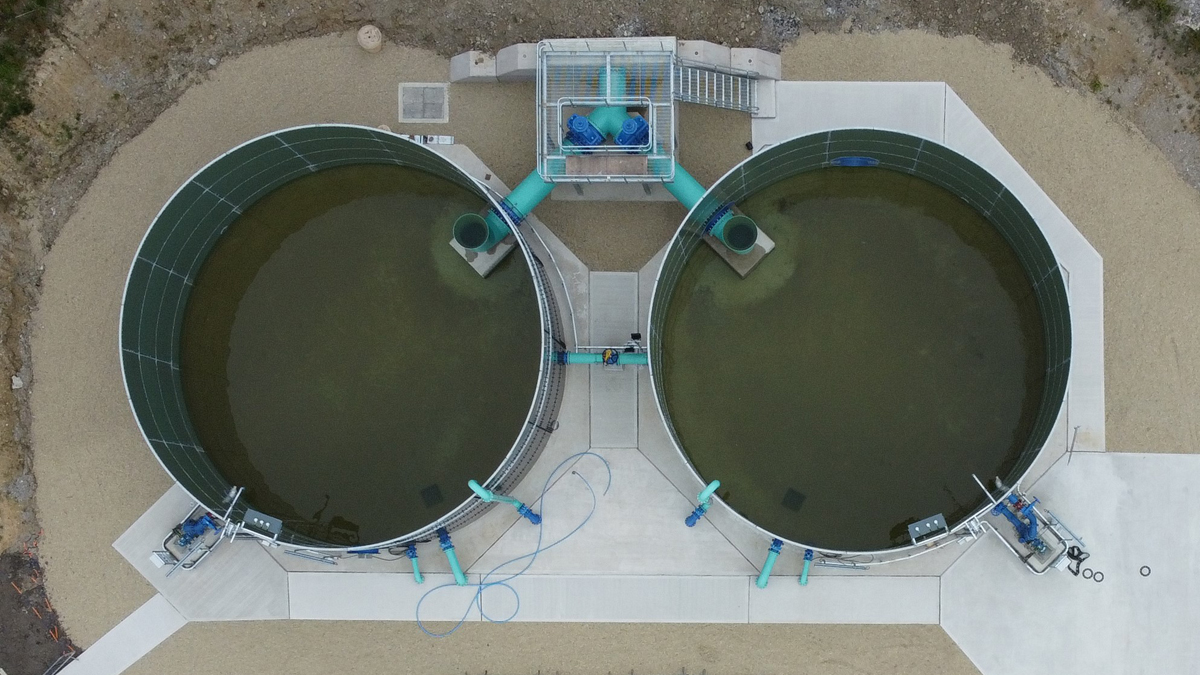
Dirty backwash water tanks – Courtesy of Mott MacDonald Bentley
Dirty backwash water tanks: Dirty water from the RGF process is transferred to two new glass-coated steel dirty backwash tanks. Each tank has a 500m3 capacity, combining the first and second stage washwater for one filter backwash plus a full filter capacity transfer. Inflow is via gravity transfer from the RGF and outflow gravitates to a new lamella clarifier washwater system. The tanks were provided without overflows, with control supported by level instruments.
New lamella clarifiers
A review of the existing water treatment works washwater process identified a shortfall in required capacity to cater for the proposed increase in treatment flow. To provide the required capacity, a series of four steel bolted and welded lamella clarifier units with a flow distribution chamber and individual 165m3 flocculator tanks were installed, based on the United Utilities signature design. These receive flow from the new RGFs and existing second stage filters.
The existing site footprint is particularly congested, with both buried and above ground structures and services. To reduce the construction footprint, make best use of available space, and comply with best hydraulic design, the new lamella structure sits above ground on a reinforced concrete slab.
Combined washwater from the dirty backwash tanks is collected and evenly distributed to flocculator tanks before passing into the lamella clarifiers. The supernatant from each clarifier is combined via a manifold and fed to the existing supernatant tanks where it is then returned to the head of the works.
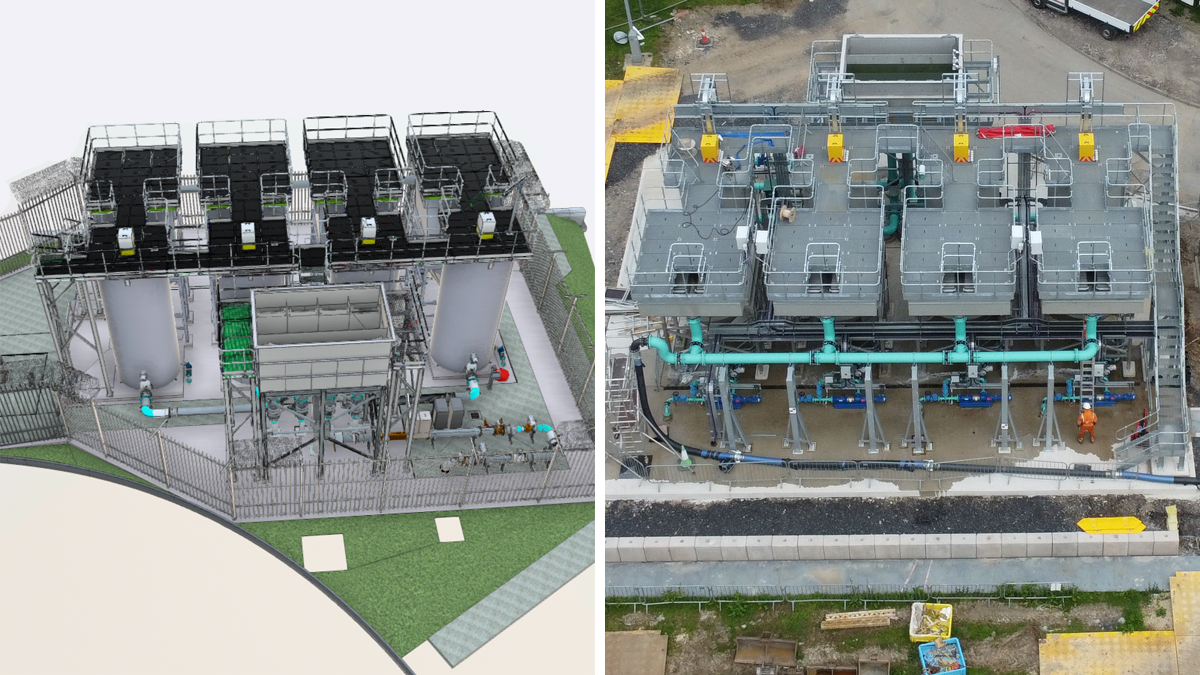
(left) 3D model of the lamella clarifiers and (right) as built lamella clarifiers – Courtesy of Mott MacDonald Bentley
A deviation to the United Utilities sludge handling specification was agreed which allowed improved control of sludge draw-off using progressive cavity pumps. The sludge from each individual lamella clarifier is transferred via a combined manifold and discharges into the existing sludge thickener balancing tank.
This pumping arrangement allows a greater control of the sludge discharge rate when the lamella is operating over the designed range of top water levels. Sludge is discharged to the existing WRC thickener and press house for processing and disposal.
Upgraded pH correction system
The existing pH correction system comprised lime dosing and was in a very poor condition, with the pumped dosing regularly failing. This required upgrade to reduce the incidence of bursts and blockages and to protect the performance of the water treatment works.
The implemented solution consisted of pipework modifications and the installation of new actuated 3-way valves and 2-way pump bypass valves which facilitate an automated water flush of each individual pump and dosing stream.
The works were required to be undertaken during a scheduled shutdown of the treatment process and careful planning of activities was required to complete the installation within a fixed timeframe.
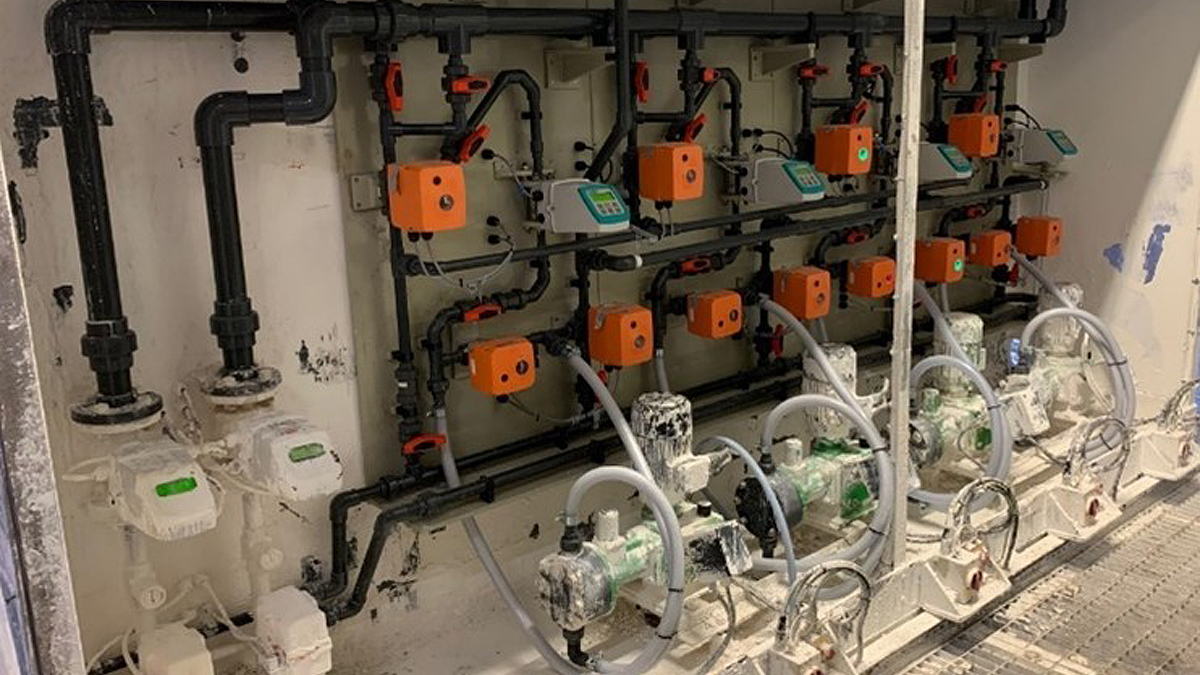
Lime dosing installation – Courtesy of Mott MacDonald Bentley
Pipework modifications
Extensive pipework modifications were required across the site in order to facilitate the new works and connect the new assets into the existing treatment processes. The use of GPR laser surveys and point cloud data was essential to ensuring an accurate understanding for both the design and construction teams in the positioning and installation across a number of areas:
- RGF inlet and outlet pipework.
- RGF overflow pipework.
- RGF dirty backwash pipework.
- Second stage filtration feed pipework to first stage dirty backwash water tanks.
- Dirty backwash water tank pipework to lamella clarifiers.
- Washwater supernatant return pipework.
- Washwater sludge return pipework.
- Existing Bells filter pipework bypass for new 1st stage filtration to existing 2nd stage filtration.
MMB were able to incorporate new pipeline routes in working areas which were heavily congested with existing services and, where feasible, the pipework was installed above ground, utilising existing support structures. This allowed a reduction in construction risk as well as improving access to pipework and flow meters for the client operational team in the future.
As part of the pipework modifications, a new point of application (POA) was provided for the existing site polymer chemical dosing system. This was designed to connect to the existing polymer dosing plant and did not require any changes to batching volumes, pump capacities or dosing rates. The design solution included the use of Molecor material in place of the originally selected ductile iron for the below-ground pipework connections between the RGF and the washwater system. This material has good strength properties, however is easier than alternatives to manoeuvre and lift due to its relatively light weight.
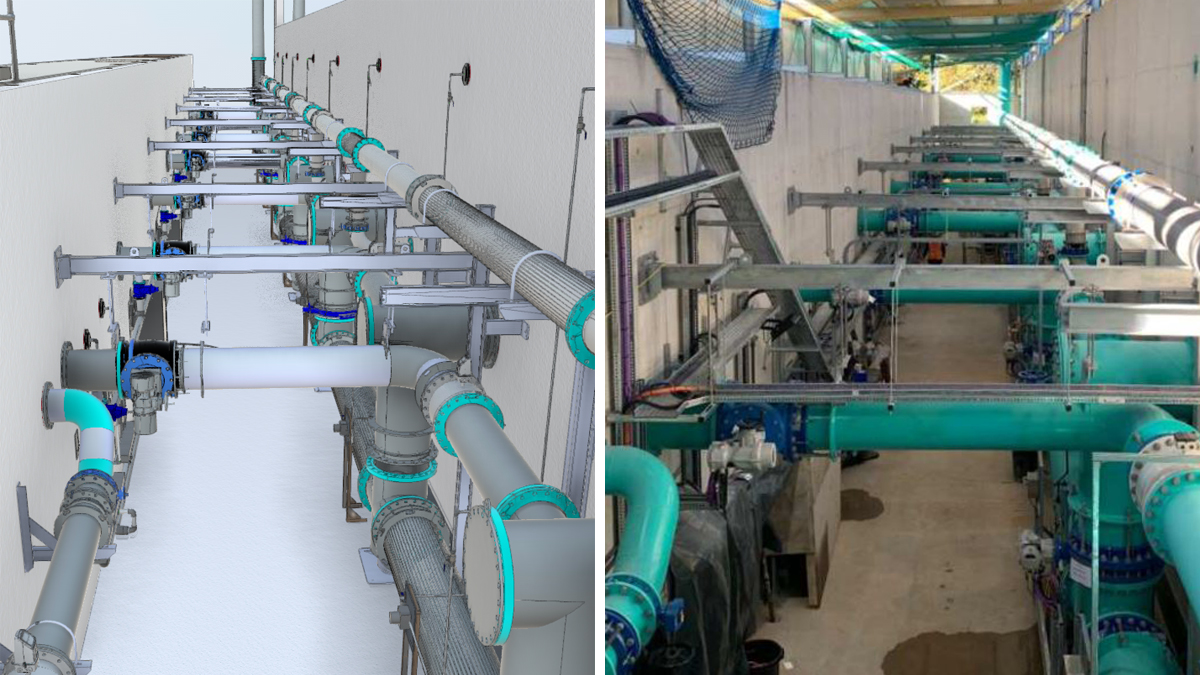
(left) RGF pipework gallery 3D model and (right) RGF pipework gallery – Courtesy of Mott MacDonald Bentley
Digital tools and delivery
Throughout the construction and testing stages the MMB BIM team worked closely with the design and site teams, as well as all sub-contractors to maintain up to date document and model control. This enabled the project team to consider as-constructed elements of the project as part of any on site design modifications, reducing the risk of errors, clashes, and associated delays during construction.
Multiple digital tools aided the safe design and construction, including Autodesk Civil3D for the pipework layouts and BIM360 for both the design and construction coordination, assessment, and as-built markups. The generated outputs were again shared as live information with the MMB sub-contractors to coordinate their design and installation requirements. 3D laser scans along with GPS and GPR surveys were used extensively throughout the project and the 3D site models were also used to consider the construction phasing and temporary installation requirements of elements such as crane pad locations and pipe connection requirements.
Testing, commissioning and completion
In Spring 2022, MMB began commissioning the RGF and lamella clarifiers, starting with dry and wet testing of each individual system. In June 2022 the pattern testing of the RGFs was completed and filter media installation commenced. The pH correction upgrade was also completed to be brought into service in the same timeframe.
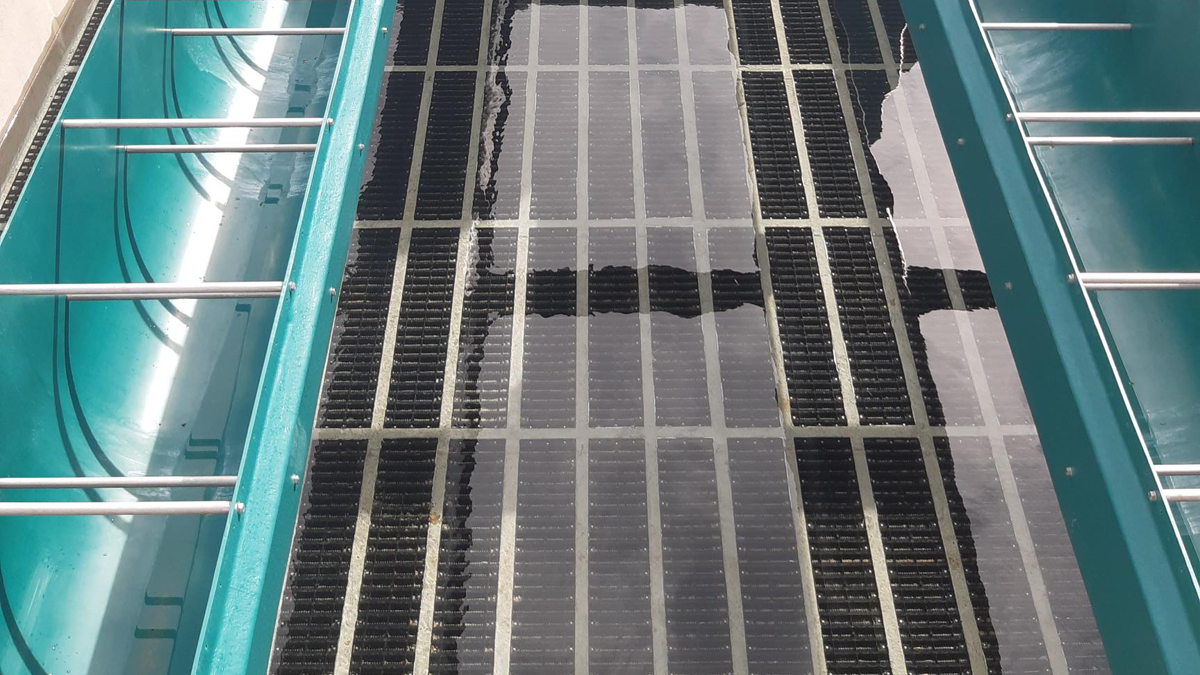
RGF during testing – Courtesy of Mott MacDonald Bentley
Numerous existing process shutdowns and isolations were required to undertake connection and testing works and these were coordinated with the United Utilities operational teams, with notice, around the day-to-day functional requirements of the treatment works.
As of August 2022, and despite the COVID-19 pandemic, MMB are continuing to maintain programme, working closely with the United Utilities project and operational teams to complete all remaining construction and commissioning tasks safely and efficiently to meet the regulatory compliance date.