Foss Barrier (2020)
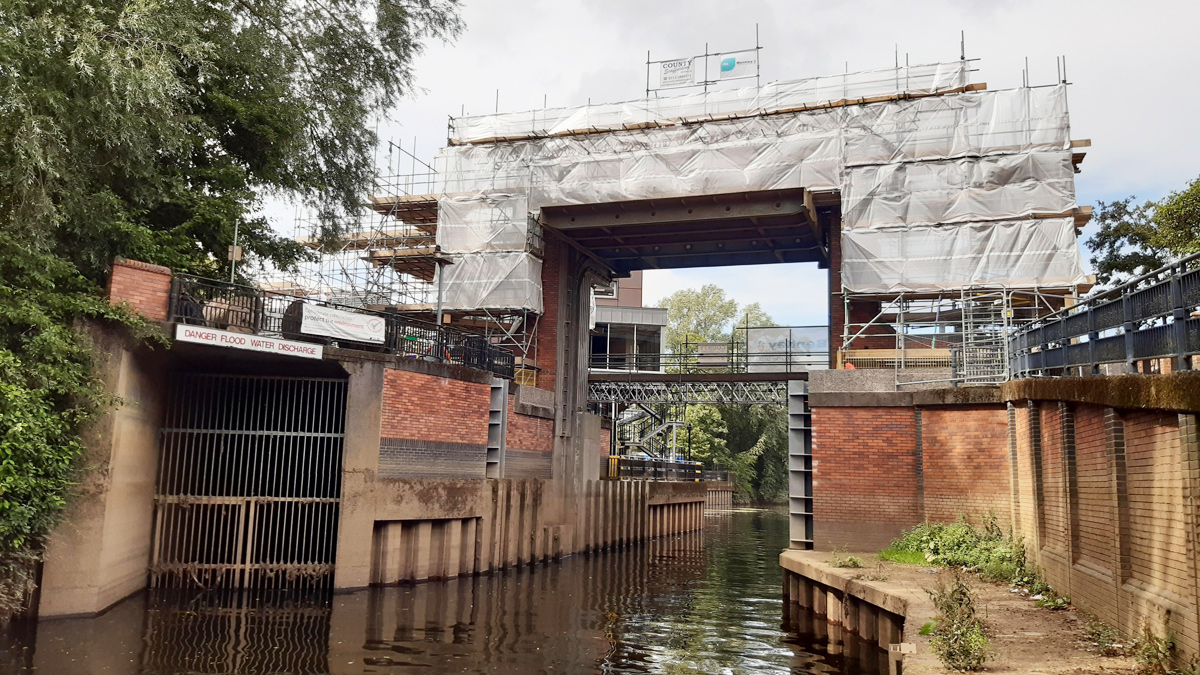
Scaffolding has been erected around the Foss Barrier to enable decommissioning - Courtesy of JBA Bentley
The Foss Barrier and associated pumping station is a vital asset in the City of York’s flood defences and was constructed in the 1980s in response to severe flooding five years earlier. In flood conditions, a mechanical gate can be lowered to stop rising waters in the River Ouse from flowing back up into the River Foss, preventing flooding to large sections of the city. When the barrier is down, the facility relies on up to eight pumps to transfer flows from the River Foss around the barrier into the River Ouse. During December 2015, the most severe floods in a generation hit the city. Water levels on the River Foss rose to the highest recorded level and entered the main control building at the Foss Barrier rendering the facility inoperable.
Contract award
After significant involvement in the initial emergency flood response, JBA Bentley (a joint venture between JN Bentley and Jeremy Benn Associates) was instructed to carry out the high-profile upgrade to the pumping station, gate and ancillaries. The key objective of these works was to enhance the overall resilience and capacity of the site, whilst critically ensuring the pump station remained operational throughout.
Previously… the temporary solution – Phase 1
Temporary works installation: Within three months of the 2015 event, construction works began on an innovative 3m high temporary platform to raise all MEICA equipment above the highest flood level using 596 precast Legato interlocking concrete blocks from Elite Precast Concrete Ltd to quickly construct the temporary platform. Using this method meant:
- Greater resilience to the existing asset: Critical equipment was quickly raised above the highest flood level, providing protection above a 1:1000 year flood event.
- The permanent solution could be built off-line: Making for a more efficient and safer build, eliminating plant, people and construction interfaces on site.
- A fully functional pumping station was maintained throughout construction of the permanent works: A pre-requisite of the solution and critical for the client and public alike.
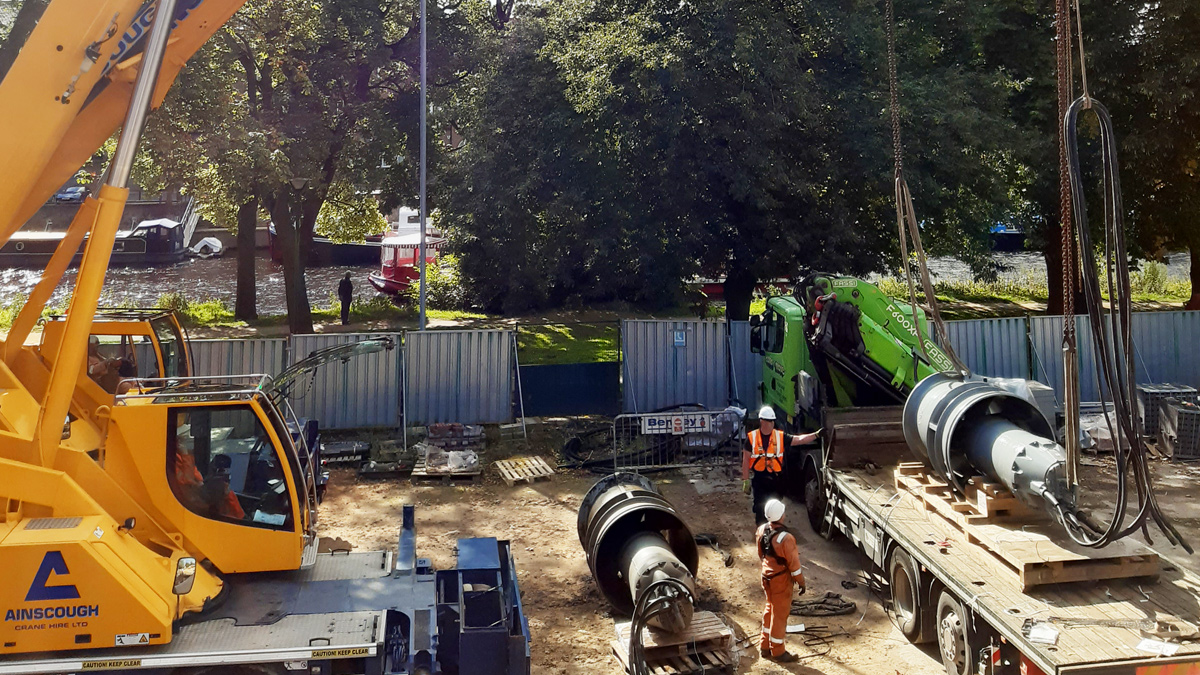
The swapping of pump one to start the 7-yearly maintenance cycle – Courtesy of JBA Bentley
Early permanent pump installation: Preventing another significant flood event at the earliest opportunity was paramount to all involved. In order to do this the pump capacity was increased ahead of the winter of 2016. The rapid construction of the temporary platform meant that new long-lead pumps and drives could be procured and installed early without any building modifications. The eight new pumps and pump drives, capable of increasing the pumping capacity from 30 to 40m3/s, were installed within the existing pump wells in September 2016.
Full pumping capacity achieved: Whilst the permanent works continue towards a fully integrated site, full pumping capacity was achieved in February 2018. The maximum capacity with all eight pumps running simultaneously is 50m3/s (50,000 l/s). This has the equivalent flow output as having 250,000 standard household taps running at any one time. This pumping capacity is an increase of 20m3/s and provides enhanced flood protection to the residents and businesses of York.
Since then… the permanent works – the main build – Phase 2
In early 2019, completion of a single-storey extension and new generator platform, meant that the installation of the five independent generators, fuel store and all the new MEICA equipment, could be installed into their final permanent locations. With the majority of the pumping station operational in Q3 of 2019, the works focus then turned to the mechanical gate, surrounding structure and ancillaries.
Construction on these three elements has progressed unimpeded. This is due to the fact that these elements have minimal relationship to the existing pumping station on site, and vast amounts of the work can be carried out off-site. Working off-line has demonstrated the successes that can be achieved through a flexible, innovative approach.
The barrier: Due to the increasing threat of flooding it was agreed that the existing mechanical gate needed replacing. Qualter Hall & Co. Ltd were chosen to manufacture the mechanical gate, accompanying bridge deck and gate ancillaries, such as winches, motors and drive shafts. Discussions had been undertaken regarding retrofitting additional plates to the top flange of the existing barrier, in order to minimise waste, reduce lead times and reduce costs. However, the final quality of the weld could not be verified and so it was agreed with the client that a new gate would be manufactured and installed.
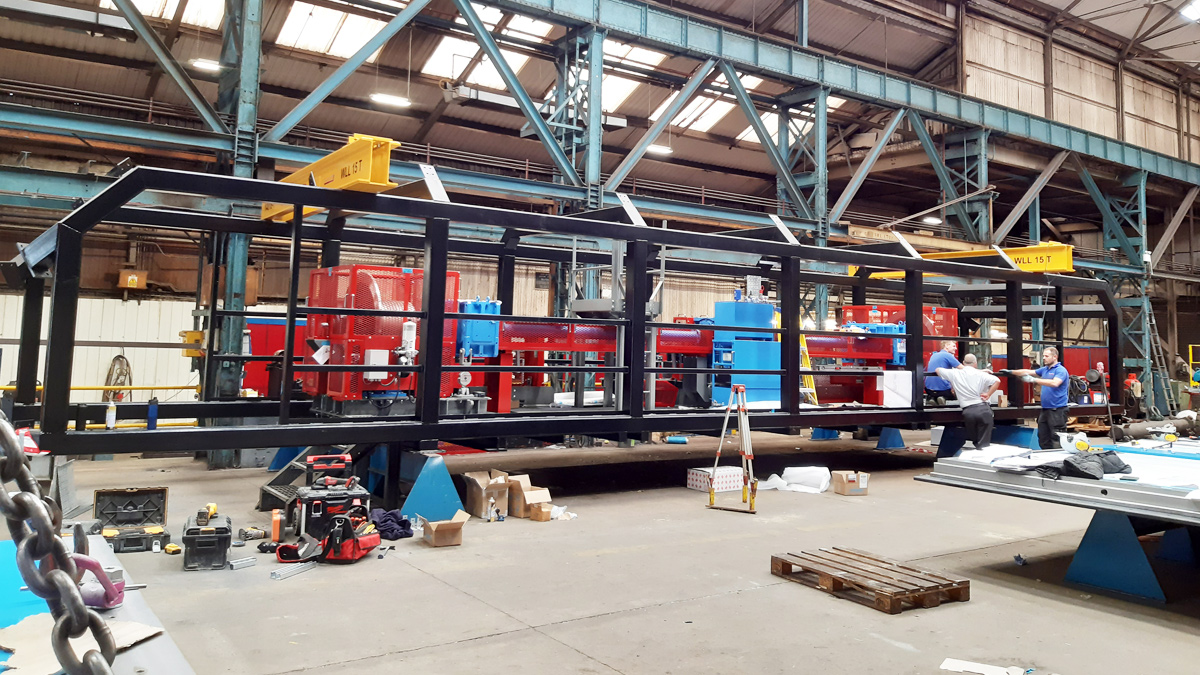
The barrier has been manufactured off site to enable greater quality control- Courtesy of JBA Bentley
The installation of the mechanical gate is programmed for Q4 of 2020. Once the new gate has been installed it will raise the defence level in line with the other elements of the project.
The bridge and gate structure: Qualter Halls & Co. Ltd began manufacturing the bridge in October 2019. Working off-line allowed for tighter quality control measures to be put in place. This was vital as the exact location of the new components had to be identical to the locations of the elements on the existing gate and bridge, working to ±1.5mm.
The floodwall: As global warming becomes more prominent, increasing the overall flood resilience of the City of York has always been a key driver of the scheme. Ensuring the reliability of the Foss Barrier and gate was one element; the other was to increase the height of the surrounding flood defences to ensure protection against greater events.
Across the site there is over 150m of concrete-stem, brick-clad floodwalls. To further reinforce the resilience of the city, all the surrounding floodwalls are being raised, thus providing protection against future flood events.
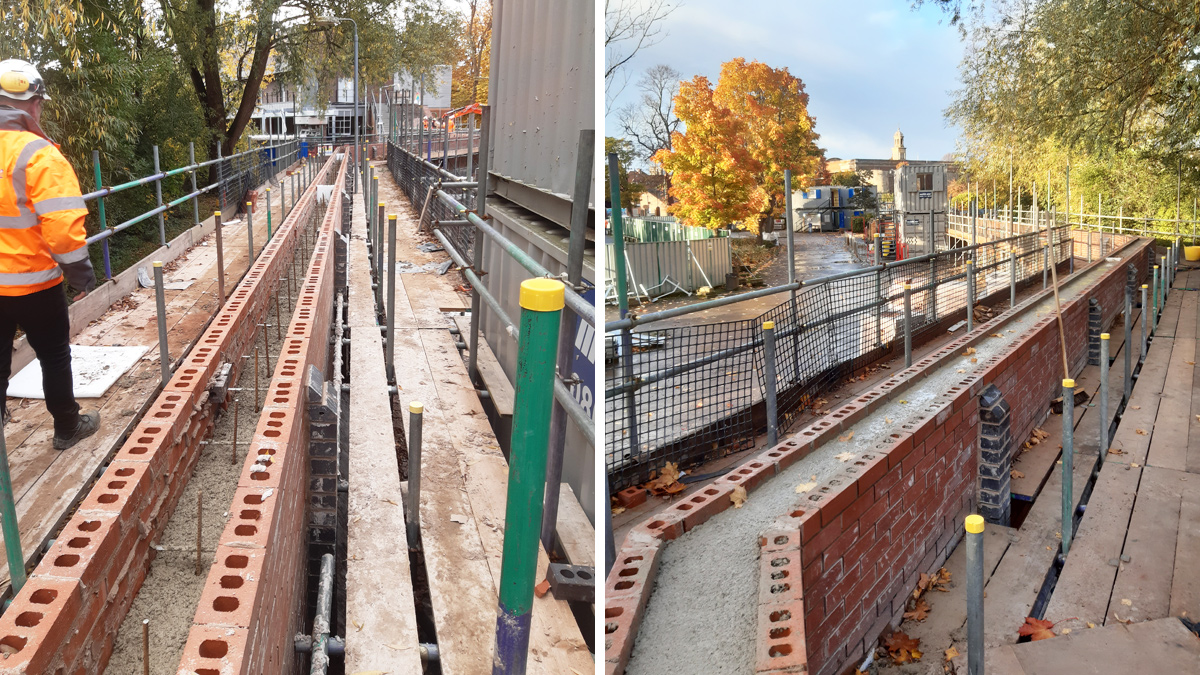
Works to the base of the floodwall included thickening the concrete stem to more than 500mm – Courtesy of JBA Bentley
Client commitment
Due to the ever-changing nature of the scheme, collaboration between designer, contractor and client has been key. It is paramount to have key decision makers on site working together. Co-locating key parties, such as client, design, contractor and MEICA specialists, from day one has been crucial to the success of the project. Working together to successfully deliver a scheme of this value and complexity has been challenging, but we are proud to have done so safely, on budget, and to a high standard.
As the defined scope of the project has developed over time, multiple project cost control measures have been supplemented by regular risk control meetings. These meetings would include members from JBA Bentley, the Environment Agency, Jacobs, and other key subcontractors. Regularly working through any issues from site, with all parties involved allowed for more comprehensive programming and forecasting. Each month forecasts were submitted and discussed. This better understanding of cash flow, risks and challenge, has helped increase confidence in the overall project costs.
The recent flooding that occurred in York, and the devastation that it caused, has reiterated how visible the scheme is to public, and it is now considered one of the Environment Agency’s most high-profile sites. With the site situated in the centre of York, there are many different stakeholders. This has meant that the solution has had to deliver benefits to varying groups. Customer and stakeholder satisfaction have been a key consideration throughout the project, with communication being broadcasted on different social media platforms by JBA Bentley and The EA’s communications team.
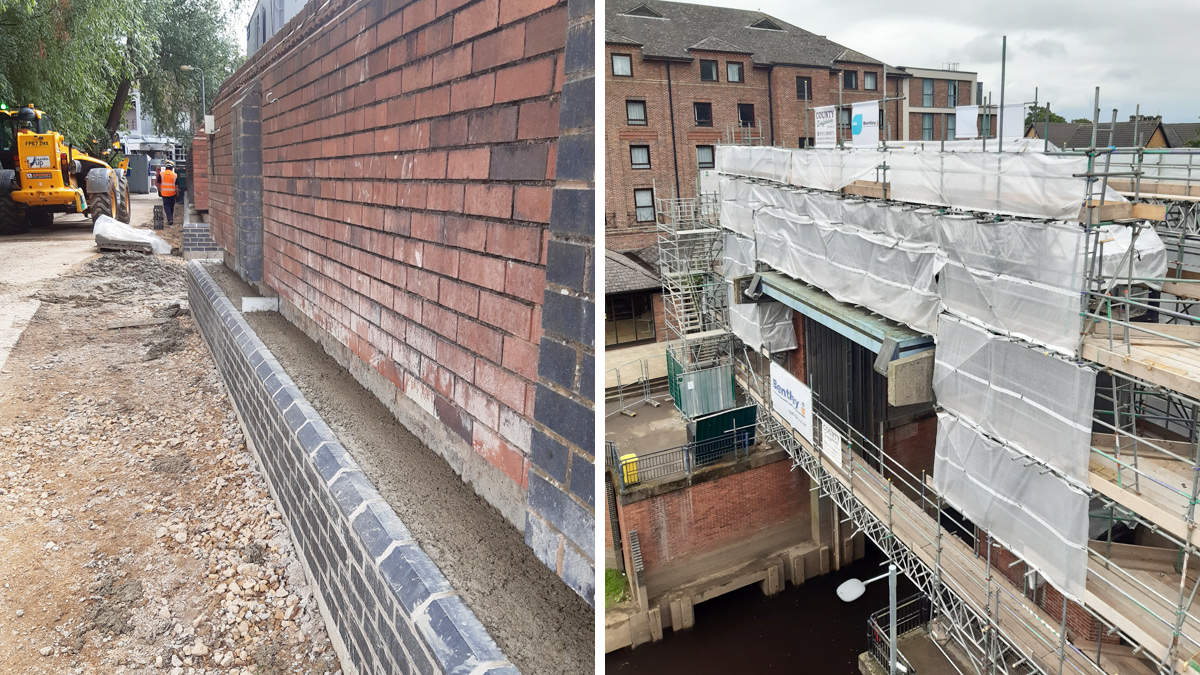
(left) Works to the base of the floodwall included thickening the concrete stem to more than 500mm and (right) scaffolding has been erected around the Foss Barrier to enable decommissioning – Courtesy of JBA Bentley
One of the most significant stakeholder groups have been the residents of York themselves, who endured the destructive flooding in December 2015 and February 2020. Therefore, significant effort was made regarding stakeholder engagement, including site visits from a variety of parties, including The Secretary of State, CIWEM (Chartered Institution of Water & Environmental Management), Rotary Club, Local Councillors and EA Regional Directors.
The team’s open approach has helped facilitate the works, and enabled stakeholders to engage with the scheme and understand the benefits the asset delivers to York and the surrounding areas. The site has also hosted several educational visits for local universities and the wider industry, introducing them to flood risk management, and the specifics of the Foss Barrier solution. For the past four years the scheme has been registered with the Considerate Constructor Scheme and the Foss Barrier Project is widely acknowledged to have been successful by the populous of York.
Foss Barrier Recovery Project: Supply chain – key participants
- Design & build: JBA Bentley
- Design (permanent works): Jacobs
- M&E installation: AMCO Giffen
- Detailed design of gate | Exemplar design of hoist & control system: KGAL Consulting Engineers Ltd
- Commissioning support: LEADA Engineering
- Structural steelwork: ECS Engineering Services
- Piling: Roger Bullivant Piling
- Pumps and VSDs: Xylem Water Solutions
- MCC & systems integration: Blackburn Starling Ltd
- Bridge and flood barrier: Qualter Hall
- HV Switchgear: Schneider Electric Ltd
- HV Transformers: Wilson Power Solutions
- Weedscreen: Ovivo
- Generators and fuel system: Yorpower
- Lifting equipment: AIS Vanguard
- Legato interlocking blocks: Elite Precast Concrete Ltd
Quality, environment & safety
Throughout the whole construction programme, works have been planned so that the temporary pumping station could be operated and maintained without compromise when refurbishing the permanent station. Early on in the programme of works, JBA Bentley released the cost and environmental benefits of using the permanent MEICA equipment as part of the temporary station. This meant minimising temporary or abortive purchases and maximising value to the EA, along with providing earlier enhanced protection to the City of York.
Using off line manufacturing techniques and early supply chain engagement, has meant that early procurement could take place. This meant that specific tasks could be carried out off-site in controlled environments, increasing the level of quality control. An example of this is the electrical sub-contractor having access to the bridge manufacturing facility to carry out the first fit of all the electrical components, prior to the bridge arriving to site. Increasing quality, reducing the health and safety risks on site, and reducing the overall project programme.
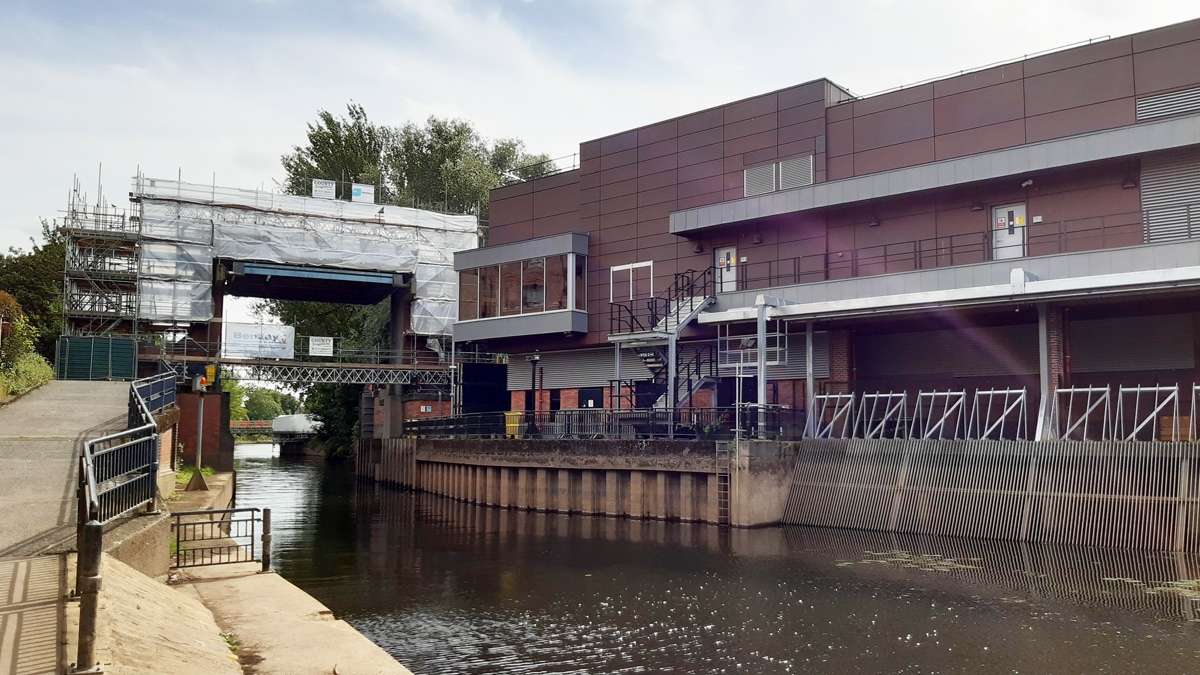
The Foss Barrier – Courtesy of JBA Bentley
Awards and acknowledgements
Due to the high-profile status of the scheme, over the past few years the project has been nominated for various awards and accolades with various results, including:
- Constructing Excellence 2019: Civil Engineering Project of the Year Award – Winner.
- The British Construction Industry Awards (BICA) Temporary Works Initiative 2019 – Winner.
Through innovative solutions, continuous development, and engagement with all stakeholders, the scheme has been able to showcase some the best engineering solutions within the industry.
Achieving the goal
Through collaborative working, hard work, determination and diligence of the entire project team, the project has been able to progress at pace. With the majority of the work being carried out off-line, this has allowed for early procurement of long-lead items, vitally reducing the overall project programme. Throughout the scheme, many challenges had to be overcome, which were faced head-on to drive towards achieving the key objective of enhancing the resilience and capacity of the site, whilst always protecting the people and businesses of York. The project increases pumping capacity by 55% and provides increased protection to over 1,000 properties.
The scheme has been able to progress at such pace due to:
- Early contractor and subcontractor engagement with the design team streamlining design and construction issues.
- Co-location of key stakeholders to allow vital decisions to be made with input from all parties.
- Collaborative review on design, driving safety and efficiency and embedding a ‘right first time’ culture within all parties.
- Agreements between different parties, allowing for additional works to be instructed quickly through PMIs, meaning work on site could begin earlier than traditional contracts.
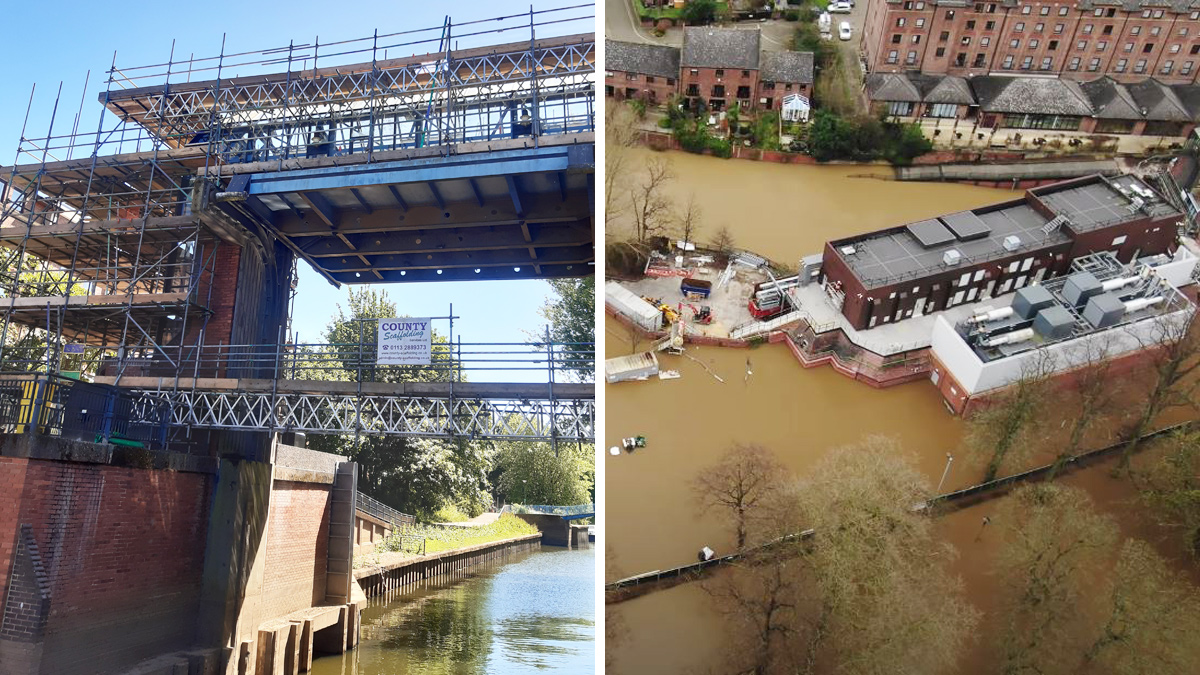
(left) The Foss Barrier and (right) flooding: February 2020 – Courtesy of JBA Bentley
Put to the test
The importance of the scheme was once again noted in early 2020 when the Foss Barrier and Pumping Station had to be utilised for one of the longest periods in its history – 18 consecutive days. To put this into perspective, the barrier had only been utilised for 18 days in total over the previous 24 months.
During this event, the pumping station was working around the clock in order to ensure that the residents of York had peace of mind. At times all eight pumps were working to over half their full capacity, 30m/s. With the majority of the works complete by this point, the pumping station remained running on automatic (with an operative there for any emergency failures).