Hanningfield WTW – Washwater System (2023)
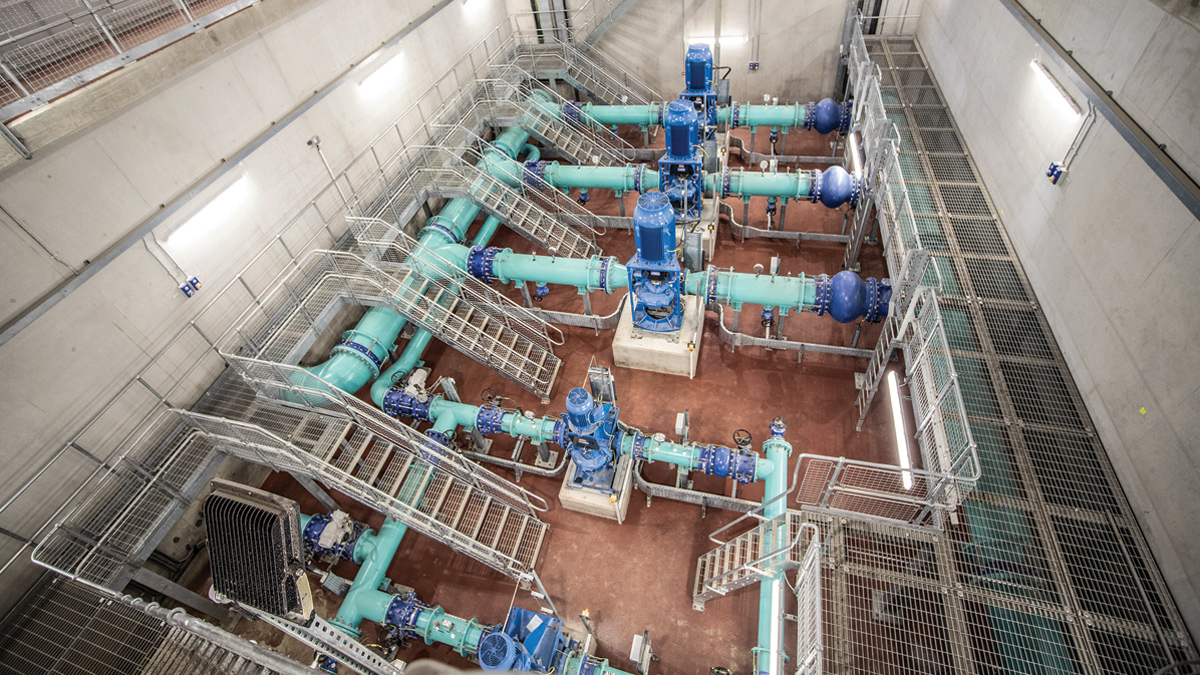
New pumping station layout - Courtesy of Essex & Suffolk Water
Located 5 miles south of Chelmsford, Hanningfield Water Treatment Works (WTW) is the largest works operated by Essex & Suffolk Water (ESW). The WTW, which has a peak output of 220 MLD, draws water from the 26,000 ML Hanningfield Reservoir to supply a large part of south Essex. The washwater system is over 50 years old and required upgrading and refurbishment. This case study follows on from the paper in 2022 and details the progress of the main construction activities through to completion.
Existing works
The treatment process comprises pre-ozone, pulsator clarifiers, rapid gravity filters (RGFs), main ozone, granular activated carbon (GAC) and chlorine disinfection. Dirty backwash water from the RGFs and GAC discharges by gravity to two settlement tanks. Supernatant from the settlement tanks was pumped to Hanningfield Reservoir. Settled material was transferred to sludge tanks for onward pumping to the Whitelillies Reed Beds facility, which provides low energy sludge treatment and supplements the diverse ecosystem that Essex & Suffolk Water has nurtured over many years.
Project need
The original washwater system installed in the early 1970s was at risk of contravening its consented discharge parameters. This was due to increases in treatment works capacity and changing influent water quality to the treatment works, largely due to the algal load from the Hanningfield Reservoir. Operational practices to cope with filter-blinding algal events required increasingly frequent washing to maintain the production capacity of the works.
The increased washwater production during the algal bloom period further exacerbated plant reliability by affecting the articulating floating arm draw-offs and pump performance of the system. Essex & Suffolk Water commissioned Stantec UK to carry out concept and definition studies, details of which were presented in a case study in the 2022 edition of UK Water Projects and on WaterProjectsOnline. A summary of the solution which was described in detail in the previous article are included in the following synopsis.
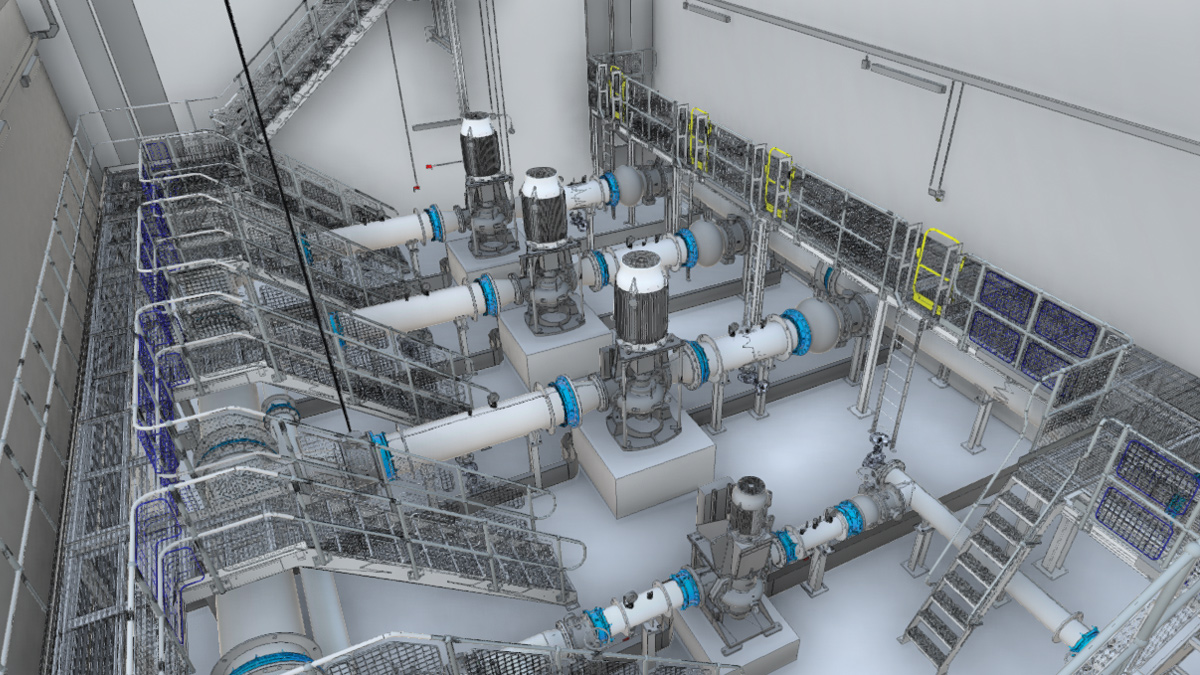
New pumping station layout 3D model – Courtesy of TES Group
The solution
The existing washwater tanks operate with continuous inlet flow and draw-off by periods of supernatant pumping (via floating arm draw-offs) and subsequent periods of settled material pumping. New consent parameters of 50 mg/l suspended solids and 30 mg/l Fe now apply, including the caveat that no chemicals will be added to aid settlement.
To achieve these new consent requirements, extensive lab and full scale in situ tests using the existing washwater settlement tanks were undertaken to ensure a good understanding of the existing washwater production and the time needed for natural settlement to occur. The concept design also considered the storage of GAC-conditioning water following a GAC delivery, where the fine particles would not generally be suitable for return directly to the reservoir. This led to the solution identified being a total of an additional two settlement tanks (three is the minimum number required to deal with the peak flow from filter backwash). While concept design identified that a new pumping station will be required to house the supernatant pumps serving all four tanks, detail hydraulic analysis carried out as part of the detailed definition identified that the separate settled washwater pumps would be installed in the new and the existing pumping stations to keep suction line as short as possible.
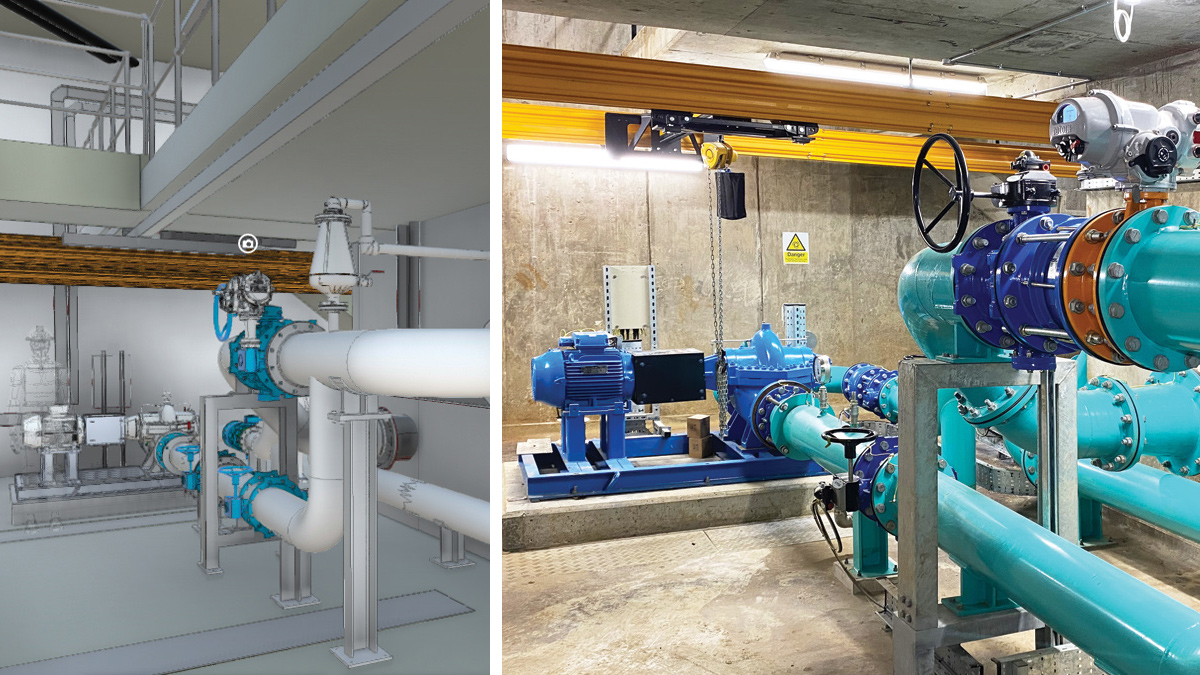
Refurbished pumping station: (left) 3D model – Courtesy of TES Group and (right) pumping station layout – Courtesy of Essex & Suffolk Water
Contracts awarded
For operational and hydraulic reasons, the new works needs to be located close to the existing washwater tanks. The only land that was available was on a small hillock. An enabling works contract was awarded in 2017 to prepare the working platform for the new works. The enabling works involved earthworks, haul road, service protection bridges and exploratory investigations of the buried services in the area.
Following the completion of the enabling works, the competitive tender for the main works was won by a bid submitted jointly by Farrans Construction and TES Group. Both companies have a good track record in the UK water industry and have relevant experience in delivery of Essex & Suffolk capital projects, Farrans with their civil engineering expertise and TES on the MEICA works.
Hanningfield WTW: Washwater Tanks Phase 2: Supply chain – key participants
- Designer/main contractor: Farrans TES JV
- Process design: Stantec UK
- MEICA design: TES Group
- Cost management: Turner & Townsend
- Civil design: Pell Frischmann
- Earthworks/groundworks: RB McGeary Contracts Ltd
- CFA & sheet piling: Murphy Group
- Reinforced concrete/formwork: Murform Ltd
- Superstructure steelwork: AC Bacon Engineering
- Washwater pumps: SPP Pumps Ltd
- Flow Control: Hydro International
- Penstocks: Ham Baker Group
- Valves: Glenfield Invicta
- Pipework & access platforms: Franklyn Yates Engineering
- MCCs: TES Power
- System integration: OCE Systems
- Transformer/RMU: Schneider Electric
- Flow meters/instruments: Siemens
- Pressure instruments: IFM Electronic
- Cranes & lifting: ABUS Crane Systems Ltd
- Photovoltaic system: Solar UK Ltd
- Fire alarms/security: Openview Security Solutions Ltd
- Lightning protection: Bacon Group
- Flow controls: Auma Actuators Ltd
COVID-19
Shortly after contract award in early 2020, COVID-19 was declared a global pandemic. The construction industry was then given government guidance to carry on operating, and Site Operating Procedures (SOP) were issued by the Construction Leadership Council. Additional welfare facilities and safe working practices based on the SOP were put in place to protect the workforce and to minimise the risk of spread of infection. The original works programme was extended to allow for an initial postponement of the works start date, and for reduced productivity caused by the social distancing requirement.
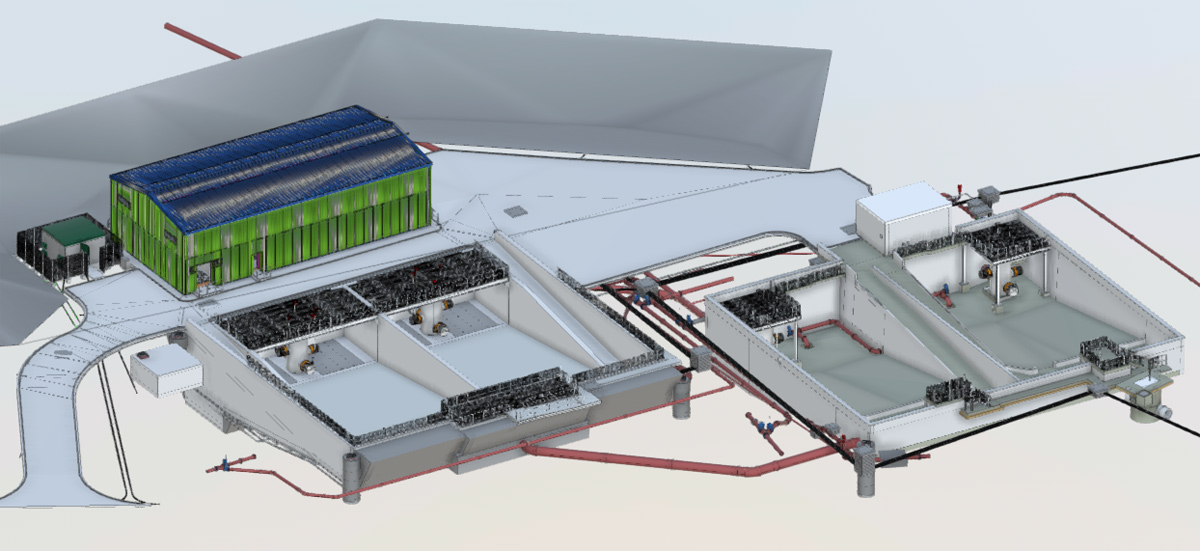
3D model of the whole works – Courtesy of TES Group
Civil construction
The main civil works involved constructing a new pumping station and two new settlement tanks, both requiring deep excavations to create the formation of their reinforced concrete bases.
Given that most of the excavation would be in the London Clay formation it was decided that the use of battered excavations across the site would provide the most cost-effective solution. But due to the proximity of several critical assets; (i) the existing washwater tanks and pumping station (ii) the existing haul road and (iii) live site services (11kV ring main, fibre optic cable, sludge pipeline, and the supernatant pipeline), it was necessary to use sheet piles in the space available to ensure the workings were safe and retained.
Ground piles were used to ensure the tanks did not settle or have any impact on ground heave. This was followed by large reinforced concrete bases and walls to form the washwater tanks. The pumping station foundation and surrounding walls were all reinforced concrete and installed to a depth below ground of approximately 5m. The new pumping station is approximately 27m long by 12m and 8m tall and has a steel superstructure construction with metal cladding.
There was an array of on-site pipeline work within Farrans’ scope. The first phase of pipework was to divert a number of live mains which were one of first construction activities on site prior to the earthworks. The detailed services information collected by ESW under the enabling works contract proved to be extremely useful for planning these diversions. Farrans had to install line valves and trust blocks to isolate the sections, and the work was staged to keep the duration and number of planned outages down to the minimum. A detailed method statement was submitted to ESW for review during the planning of these diversion works.
The bulk of the new pipework constructed was laid to connect the new and existing structures at significant depth, up to 7m below ground. Due to the limited space availability, open dig was often not an option, so trench boxes had to be used. In addition, the planning of the excavation work had to take account of the many existing buried services, particularly in the area adjacent to the existing structures, to ensure that they are not impacted upon.
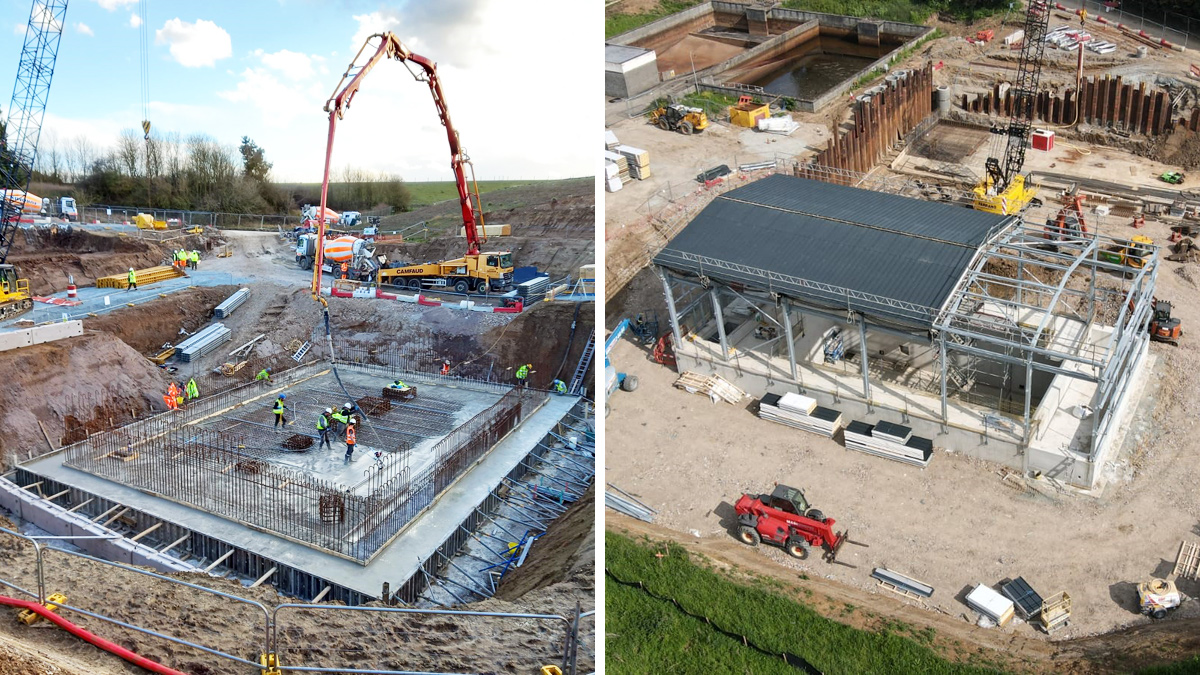
(left) Concrete pour for pumping station base and (right) the pumping station superstructure and tank bases construction – Courtesy of Farrans Construction
MEICA design & installation
TES used Autodesk Revit to undertake the detailed 3D design for the project, utilising point cloud laser scans of the existing plant and tanks enabling the development of a detailed and accurate model of the future completed works. The new structures and associated mechanical and electrical equipment for both pumping stations were modelled and coordinated with various discipline models using the BIM360 Design Collaboration and Revit. This therefore ensured all teams were working with the latest data and model throughout the project, thus producing a true 3D vision of the planned completed works.
A new 500kVa 11000/415v transformer and RMU connected to the existing site-wide HV ring main network was required to power the new pumping station. The site management team, HV specialist subcontractors and senior authorised persons worked closely to ensure the safety of personnel and reduce risk or damage to the existing power network. RAMS for identification, cable isolation, spiking procedures, and jointing work were reviewed in line with all relevant safety procedures and regulations before transfer of control was approved and works could commence.
A detailed complete electrical design was developed in-house using various electrical packages to include AutoCAD, EPLAN, Amtech & Relux, which proved invaluable at time of installation and testing.
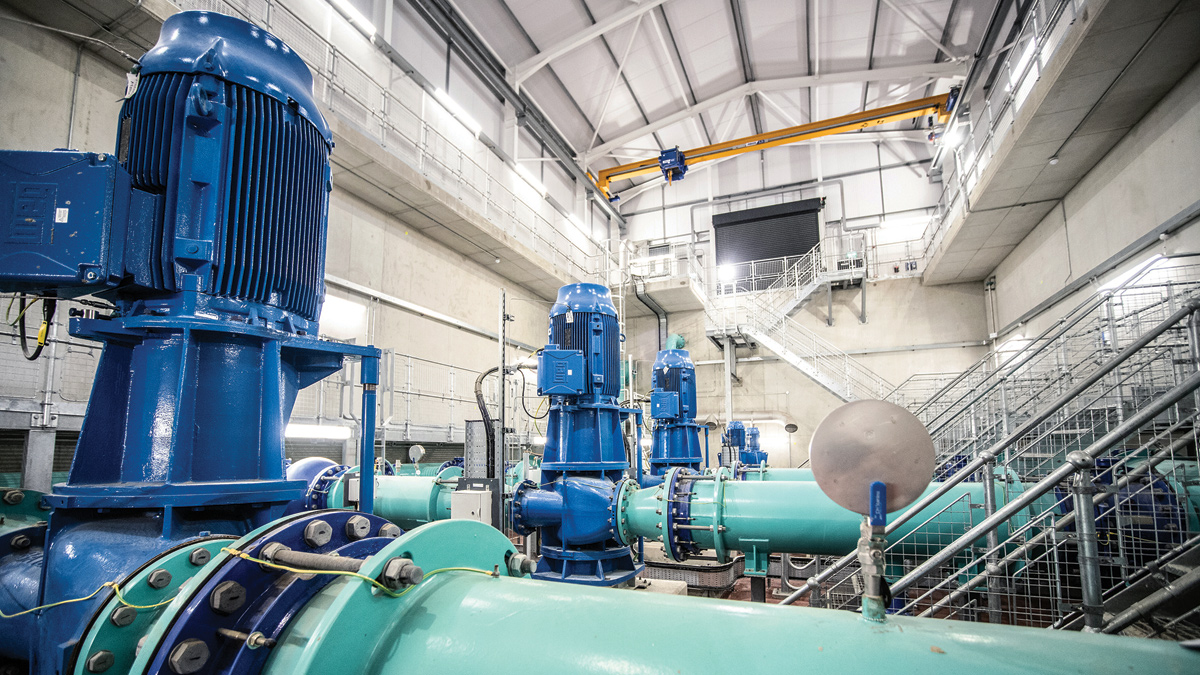
Installed new pumps and gantry crane – Courtesy of Essex & Suffok Water
Refurbishment of existing assets
Upon the completion, commissioning and 28-day trial of the new pumping station and new tanks, the dirty washwater from the treatment works was diverted to the new pumping station and tanks. This allowed the second phase of the work programme to proceed which was to refurbish the existing washwater pumping station and two settlement tanks.
All the existing pumps and pipework were removed from the pumping station and new settled washwater pumps and pipework installed. The new arrangement has significantly improved the access for operational staff because it is less congested now that the supernatant pumps are re-located to the new pumping station.
The two existing concrete settlement tanks, which have been in service for around 50 years, are still structurally sound but required surface cracking and joint repairs. The contractor detected asbestos containing materials in the existing joint filler, so the repair was changed to using over-banding in preference to be disturbing the existing joint fillers.
Commissioning
TES developed a commissioning plan with the purpose to assure that the electrical systems were safe, reliable, perform within manufacturer tolerances, were installed in accordance with the design specifications, and conformed to ESW standards. ESW engineering and operations teams were consulted throughout the various stages of the plan development. Progress, control, and operational commissioning was undertaken using the industry standard level 1,2 & 3 testing documentation, therefore providing client confidence, and fulfilling end user operational requirements and quality. ESW operation and maintenance personal were trained, and specific routine maintenance tasks were demonstrated.
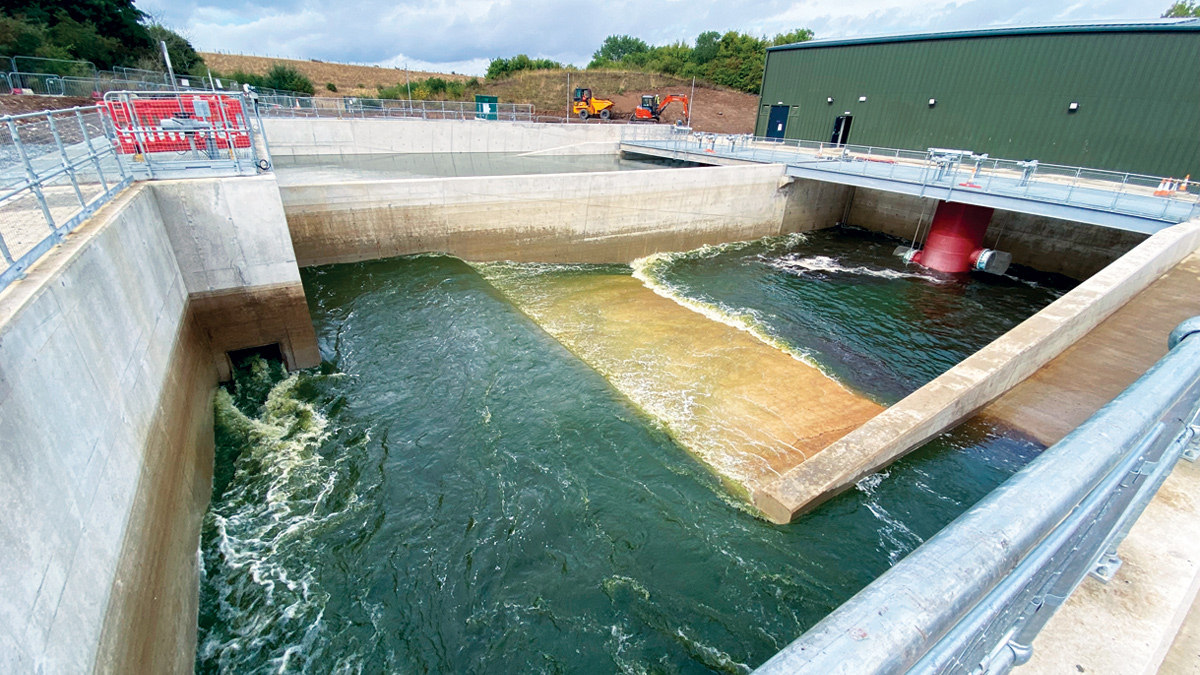
New tanks during commissioning – Courtesy of Essex & Suffolk Water
Environment
Considerations were given to the high ecological sensitivity of the site throughout the project, particularly related to the presence of a large numbers of reptiles. Vegetation management and reptile relocation were part of the enabling works. As areas of the construction site are handed back, these areas have been restored to grassland.
To maximise the potential for biodiversity, suitable seed mixes of native grass and wildflowers have been sown. On sloped areas the diversity of plant species leads to greater soil stability as well as promoting pollinators. Following on from the reptile relocation works, a large hibernaculum site has been constructed within the restored grassland area.
The residents of the nearest villages were kept informed via letter drop on the progress of the project and how traffic and noise are to be mitigated. The final landscape works will involve tree and shrub planting to screen out visual impact on the nearest neighbour.
Summary
At the time of writing (August 2023) the Hanningfield Washwater Project has started final reliability trials. The project team has worked collaboratively to deliver a high-quality product meeting the required standards in a safe manner while protecting the environment having overcome the severe challenge of COVID-19.

Completed works and surroundings - Courtesy of Essex & Suffolk Water