Hawkchurch STW (2024)
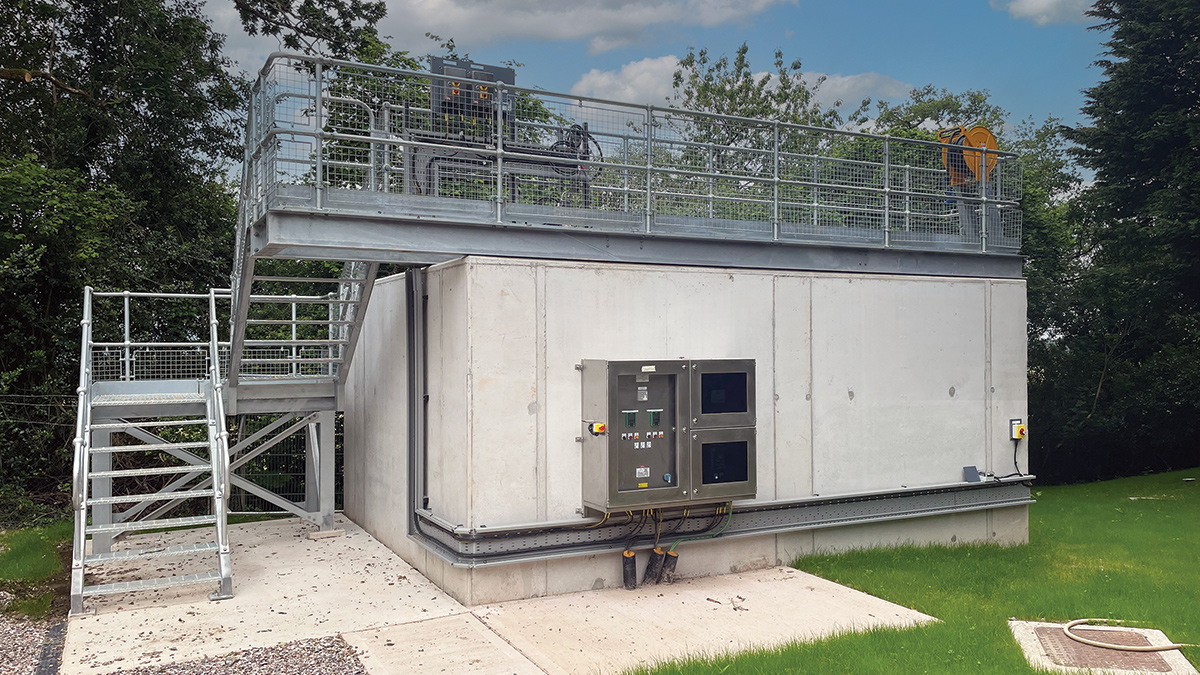
New storm tank with control panel and access staircase - Courtesy of Galliford Try
Hawkchurch is a small village on the Devon/Dorset border, 3 miles north-east of Axminster and 4 miles north of the fishing town of Lyme Regis. The existing sewage treatment works was constructed in the 1980s and serves a population of around 500. It was typical of the era, with an old style Dortmund tank with percolating filter and humus tank off the back end. Final effluent is pumped from the site to an outfall into the Blackwater River. The project driver was to reduce the number of unconsented spills to the environment by providing a capacity of 45m3 storm storage and inlet works screening to remove solids and enhance the operation of the works.
Project scope
At the scoping stage, Galliford Try worked closely with South West Water to establish the most cost-efficient solution when considering both operational expenditure (OPEX) and capital expenditure (CAPEX) to ensure South West Water achieved the best whole life costs. From this exercise it was established that the scope outlined below was to be included for construction on site:
- A new above-ground concrete storm tank with capacity of 45m3 (exceeding the EA’s required storage volume of 40m3).
- New access platform to span the storm tank for washing down of the storm tank.
- New LCP for the control of duty/standby pump for return of effluent within the storm tank.
- One Jacopa wave screen to be installed on the overflow from the storm tank.
- One new HAIGH 590 series, 6mm 2D mechanically cleaned screen and 10mm 1D hand raked bypass screen from Haigh Engineering to be installed within existing inlet channel.
The site
Access to site was challenging, as the site was only accessible via one narrow road with infrequent passing places for the larger vehicles required to get construction equipment and materials to site. Additionally, the footprint of the site was only 880m2 of which only 180m2 was usable for the construction activities.
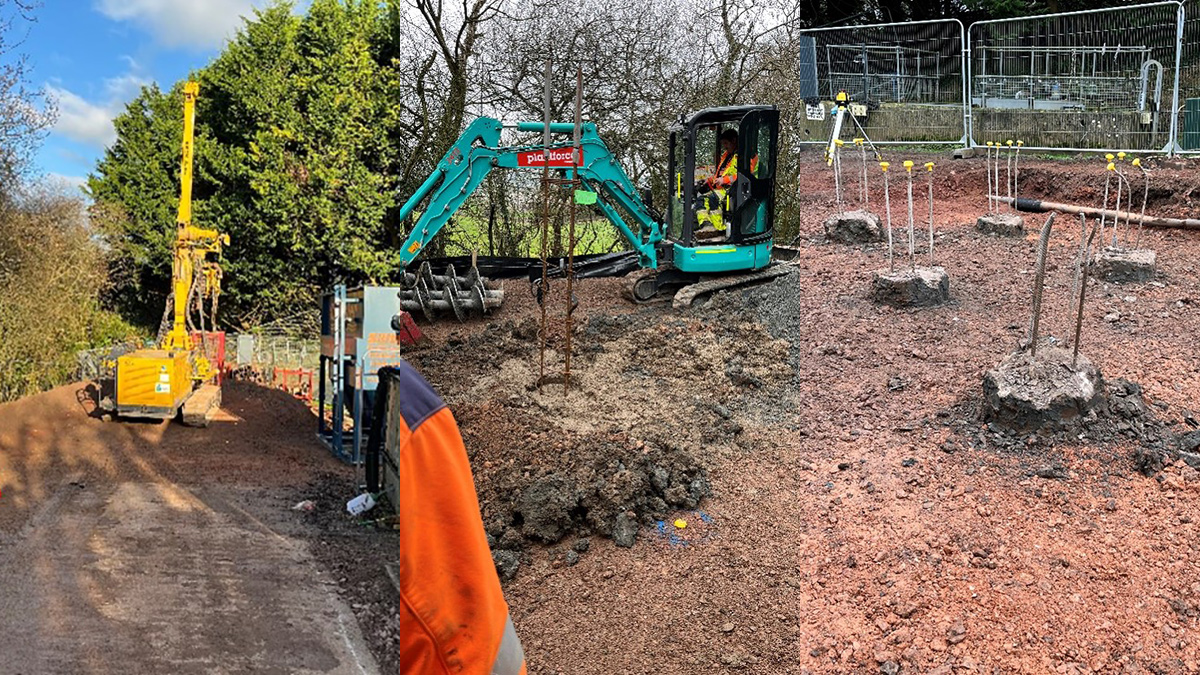
(left) Piling rig set up, (middle) piling reinforcement, and (right) piles cropped – Courtesy of Galliford Try
The stormwater storage tank
Prior to construction it was identified that there was contaminated water within the ground. After the initial sampling, Galliford Try requested further sampling to take place to identify if this was a one-off fuel spill or not. After the second survey, it was identified that contaminated water was still present and was an issue that required managing.
Galliford Try’s environmental team looked into the best practice options to manage this, and then engaged AGS Ground Solutions Ltd to undertake a Tier 2 survey of the site, as it was considered possible that a new fissure could be created during the piling stage which could expose the contaminated water to the environment.
Through further studies and multiple discussions around this topic, to mitigate the risk, Galliford Try utililised contaminated water handling plant and pumps from Siltbuster Ltd to manage flows. Along with this, Reconomy was engaged for the removal of any contaminated arisings.
The new storm tank was built upon twelve piles due to the strata within this area a mixture of Charmouth mudstone formed some 190 million years ago and poorly stratified angular rock with clayey hillwash. To undertake the piling, a piling mat and temporary works were required, which allowed Aarsleff Ground Engineeing to mobilise to site and install the twelve CFA piles at 450mm nominal diameter.
Throughout the piling exercise, contaminated water was managed through the Siltbuster Ltd plant, and the piling activity was successfully completed with zero impact to the local water courses.
With the piling compete, steel for the base was installed and tied into the piling reinforcement, shuttered and poured in two sections due to the need for a sump to install the return pumps. Wall steelwork was then installed up to 3m above ground and shutter pans used for the concrete pour.
Overflows from the new tank will spill into an existing chamber on the site and to screen these flows further, Jacopa Ltd fitted a new 2D wave screen to screen all flows to 6mm within the storm tank.
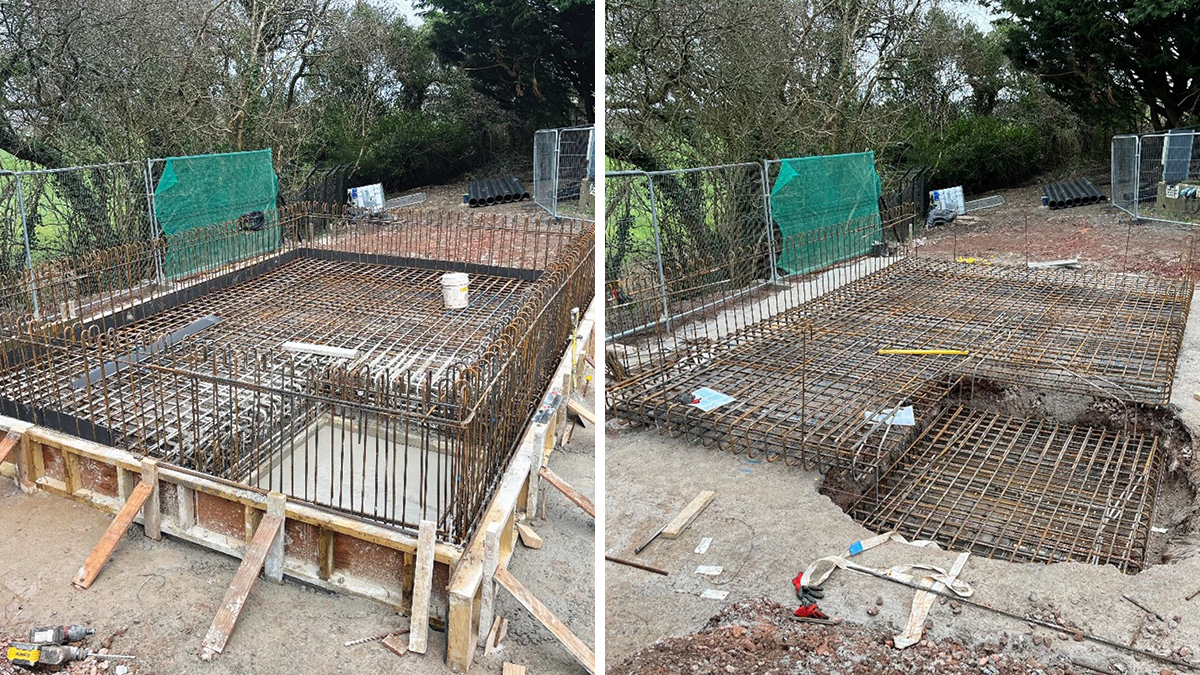
(left) Base shuttered and wall starters, and (right) steelwork for base slab – Courtesy of Galliford Try
Inlet works screening
One of South West Water’s aims is for everyone to feel confident about the water at their favourite beach, river, or lake. Galliford Try have installed a number of inlet works enhancement screens on multiple sites throughout Devon as part of SWW’s WaterFit Programme, and through this have gained useful experience in installing screens whilst managing flows through to the works.
Following discussions on how to manage flows at Hawkchurch STW, a new 590 Series screen from Haigh Engineering Ltd was installed into the inlet channel. Flows are screened to 6mm, with bypass flows screened to 10mm.
Hawkchurch Storm Tank: Supply chain – key participants
- Project delivery, civils & MEICA: Galliford Try
- Ground surveys: AGS Ground Solutions Ltd
- Civil design: Eastwood & Partners
- Contaminated water handling: Siltbuster Ltd
- Removal of contaminated arisings: Reconomy
- Piling: Aarsleff Ground Engineering
- Tank construction: D Wall Construction Services
- Steelwork: GT Fabrications
- Wave screen: Jacopa
- Inlet screens: Haigh Engineering Ltd
- Pumps: Xylem Water Solutions
- Pipework: Saint Gobain PAM UK
- Flow meter: Siemens
- Instrumentation: Pulsar Instruments
- Kiosk: GR PRO Precision Manufacturing
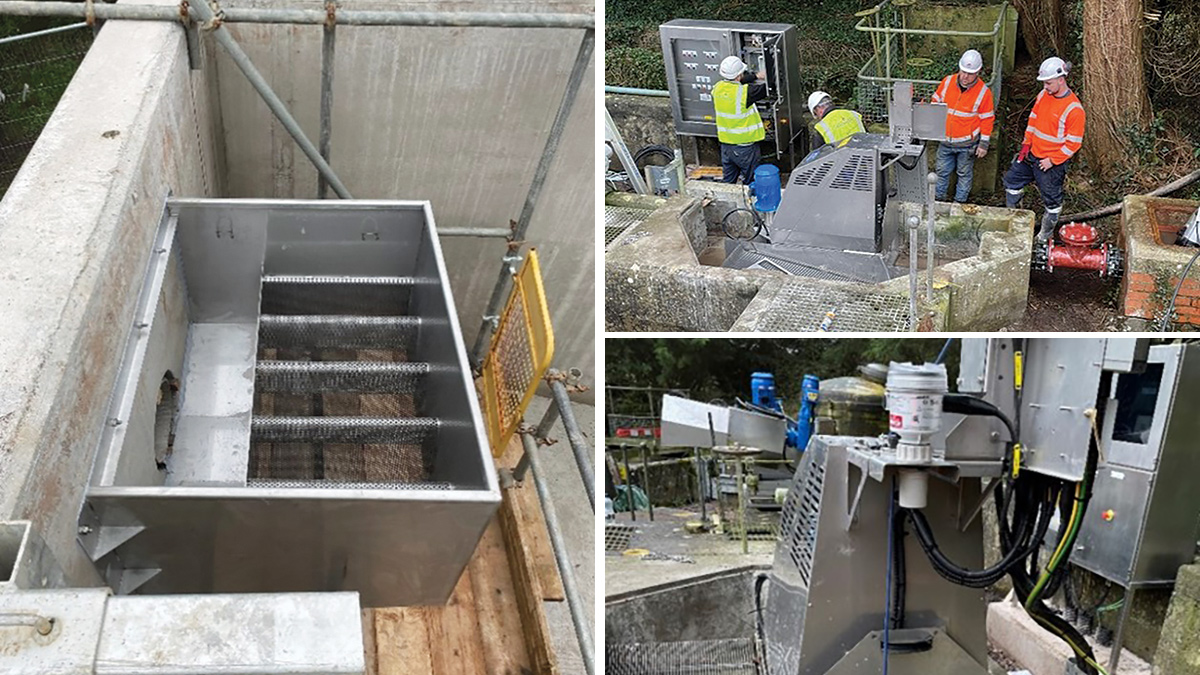
(left) Jacopa wave screen in the storm tank, (top right) Inlet screen installation in the channel, and (bottom right) inlet screen in action – Courtesy of Galliford Try
Carbon savings & in-house capability
Local resources and materials were used where possible including subcontractors, which as a result provided the local economy with a financial boost during the construction phase. Where local suppliers were not available, Galliford Try strived to use off-site build solutions where possible to minimise commuting.
In-house resources that were utilised included project management, electrical design, LCP design/build, process control, and commissioning. The in-house workforce undertook the site establishment, civil engineering, landscaping, MEICA works, and finally the demobilising the site.
Stakeholder management
At pre-construction phase, all third-party stakeholders were identified and entered onto a management plan. Galliford Try’s Customer Liaison Officer contacted all stakeholders prior to commencement to provide them with the appropriate project contacts should they have questions, queries, or complaints and to establish their requirements and desires throughout the construction phase of the works. As part of the management plan all communications where complaints or agreements are made are formally recorded, resolved, and closed out.
Conclusion
Initial progress on site was good with setting up site and setting the project up for an efficient delivery until delays were encompassed by switching the piling rig out due to the environmental considerations. Once this was managed and piling underway, the remainder of the project ran through a smooth transition and was delivered by the regulation date of 31 March 2024.
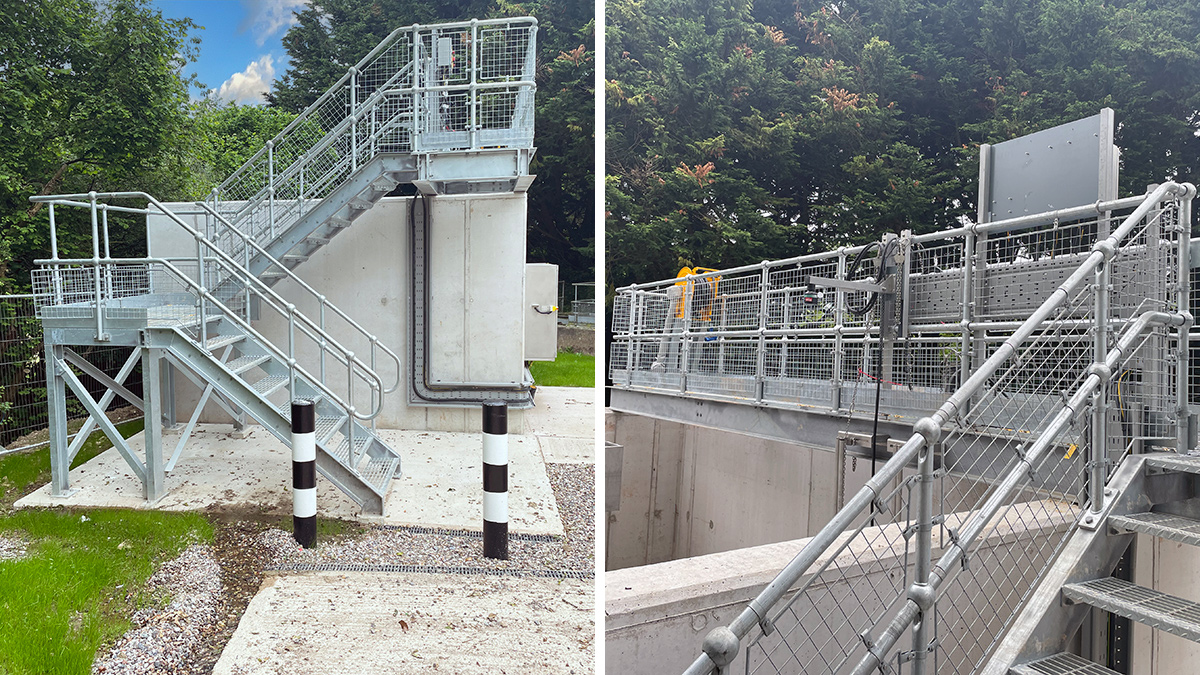
New access steelwork - Courtesy of Galliford Try