Jackson’s Edge Service Reservoir – Compartment 1 (2016)
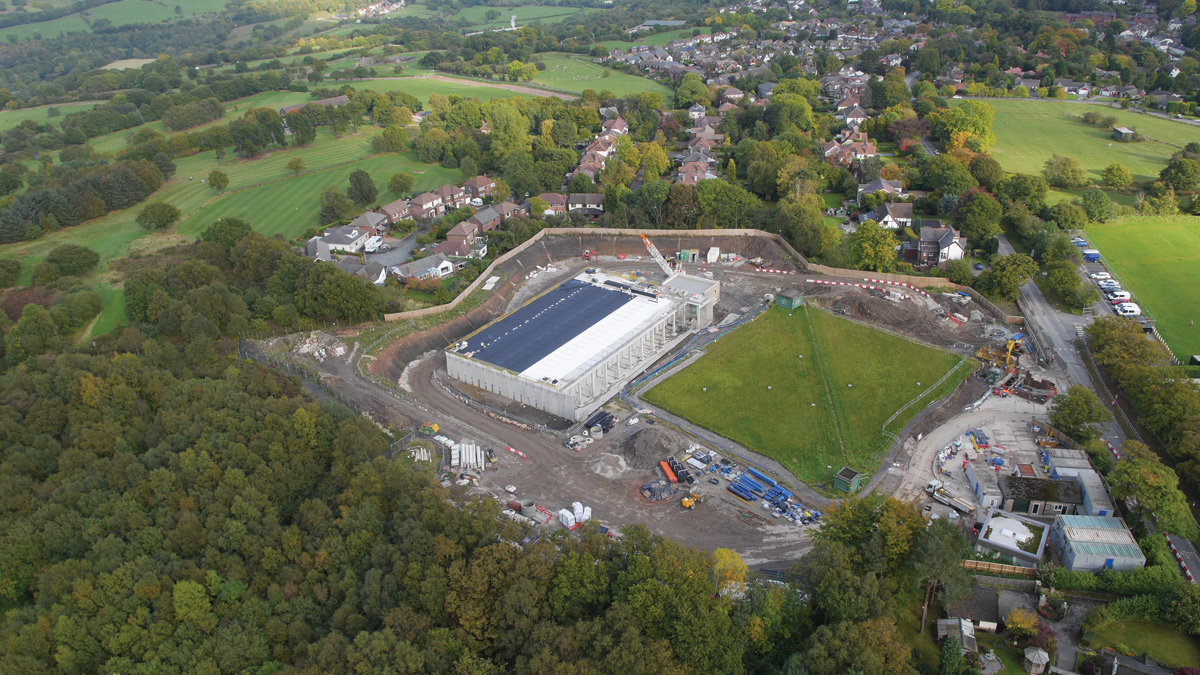
Aerial view of the new Jackson’s Edge SR under construction - Courtesy of JN Bentley Ltd
Jackson’s Edge Service Reservoir (SR) is a water supply scheme that will provide increased security to the network through the provision of a new 18Ml capacity, twin compartment SR on the site of the existing 103 year old SR. The £7.5m project has adopted a Design for Manufacture and Assembly (DfMA) approach, saving approximately £2m on the original budget estimate for the scheme. Principal designer Mott MacDonald and principal contractor JN Bentley who mobilised in June 2014, completed compartment one and the valve house of the service reservoir in October 2015, and they were commissioned in December 2015. Compartment two is forecast for completion in September 2016, which will be located on the site of the existing service reservoir which is to be taken out of service and demolished following the successful commissioning and in to service of compartment 1 of the new structure.
Purpose, design approach & rational for construction methods
Client United Utilities’ Engineering team prepared the design strategy for the project based on the client’s requirements and the many constraints that the site presented, including working in a highly residential area and in very close proximity to the existing live service reservoir. Therefore the DfMA solution was chosen after a comprehensive study of both the design and construction methodologies. Clear benefits were identified using this approach in terms of programme, cost and health and safety. The adoption of this methodology was ideally suited to a site with a very restricted construction and working area, and would significantly reduce disruption for the local residents of Disley and surrounding areas in Stockport.
Originality of concept
This project is the first rectangular precast concrete (PCC) service reservoir that United Utilities has ever built. The client was aware that other water companies were using this system and worked closely with them and their construction partners to fully appraise the system and assess its suitability for the Jackson’s Edge SR.
The constraints of the site required a small footprint for the new service reservoir resulting in a relatively deep structure. The PCC wall unit sizes required were therefore larger than any previously manufactured by the PCC supplier, Carlow Precast (now FLI Precast Solutions), with whom JN Bentley has a strong relationship through delivery of many PCC structures within the water sector for various clients.
The reservoir roof also employs a PCC construction, with roof slabs supported by columns prior to being covered with a roof screed. The water tightness of the roof is provided by an intelligent leak alarm membrane which sits on top of the roof screed but below the backfilling material, and is at the forefront of leakage monitoring and control.
The design system is being adopted as best practice within United Utilities organisation and is being used on many new AMP6 projects.
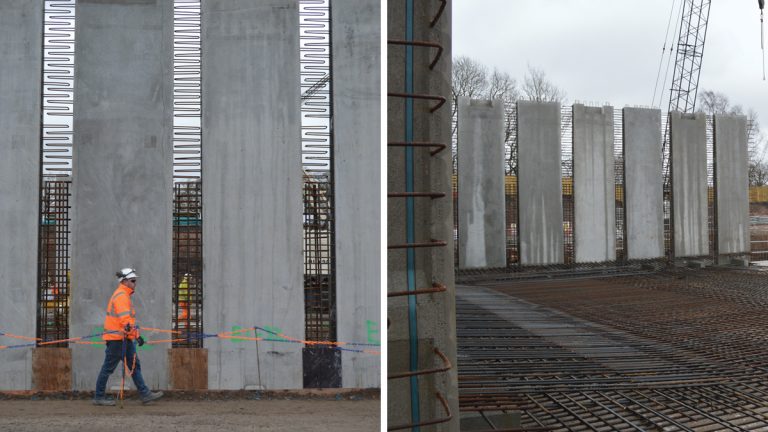
(left) PCC wall units and (right) Rebar placement for base slab – Courtesy of JN Bentley Ltd
Innovation in design
During the design development phase the client’s engineers visited other UK water company sites that were using DfMA systems. Cooperation between engineers and their contractors was excellent and lessons learned were freely exchanged.
Design and construction details that were improved for the Jackson’s Edge Service Reservoir included:
- Increasing the size of the Carlow wall units while optimising weight for transport/delivery.
- Improving joint details between wall unit and roof slab beams.
- Improving the construction joints with the in situ concrete pours.
The intelligent membrane system on the roof has been refined over several SR refurbishment projects and is a client requirement for large PCC service reservoir roofs. The thermoplastic polyolefin membrane combined with electro-conductive fleece and sensors ensures the client of integrity of membrane following backfilling. Its advantages include:
- Proactive monitoring of the roof against leakage.
- Increased security for the reservoir.
- The ability to locate leaks in the membrane to within +/- 50mm and reduce repair costs.
Tank construction
A mass excavation of a depth ranging from 8m to 4m was undertaken to facilitate the construction of the new reservoir adjacent to the existing 103 year old reservoir. The original reservoir at 18Ml capacity was one cell, therefore it was not possible to demolish this prior to building the new reservoir in its entirety.
As such, only one cell of the new twin cell reservoir could be constructed in the available working room. This was then brought into service with the adjoining valve house. Demolition of the old reservoir commenced following the proving period and then the second cell was constructed over the old base and brought on line.
The reservoir compartments consist of precast wall units 6.65m tall, and in situ base slab and in situ 0.45m wide wall infills. As the beams, columns and roof slabs are all precast concrete, this decreased the time required to construct the roof structure.
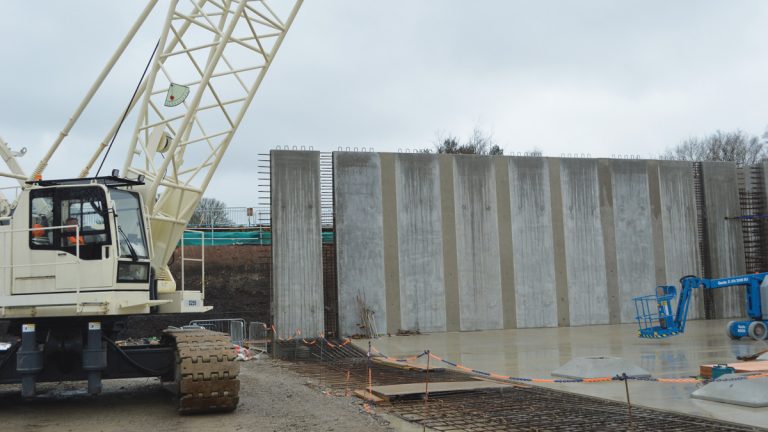
Infill panel construction – Courtesy of JN Bentley Ltd
Valve house construction
The integrated valve house is approximately 10m tall; the construction of the valve house offered two options, fully in situ or part in situ part precast. The option of precast would have required a 4m deep footing for the wall units to be sited. This would have resulted in excessive volumes of concrete to accommodate the precast units. The option of a fully in situ valve house was taken forward. The access metalwork and structural beam for the roof slab was also prefabricated where possible to reduce the installation time on site.
Management approach
The client’s engineers invested time in keeping the client’s asset managers fully informed about the design proposals for the project. There were common goals for all parties associated with project including engagement, KPIs and a rewards system. The management structure for both organisations has included both site and office based employees.
The client’s construction manager and JNB’s site manager are based in same office which facilitates the flow of ideas and discussions to quickly resolve issues etc. Regular project team meetings are also held to discuss progress and design and close out actions.
Lessons learned sessions are convened to feedback information to other AMP6 projects. Quality assurance was a key element for the design, and the manufacture and construction of the project.
Environmental management and sustainability
Environmental issues that have been managed on the project include:
- Protection of waxcap mushroom spores on the scour route.
- Translocation of bluebells.
- Provision of bird boxes to mitigate tree removal.
- Securing a nearby location for the stockpiling the excavated material prior to reuse as backfill to the new service reservoir.
To monitor the sustainability of the project the UU waste management tool ‘Elevate’ was used to monitor factors such as material to landfill and use of recycled materials against the company’s targets.
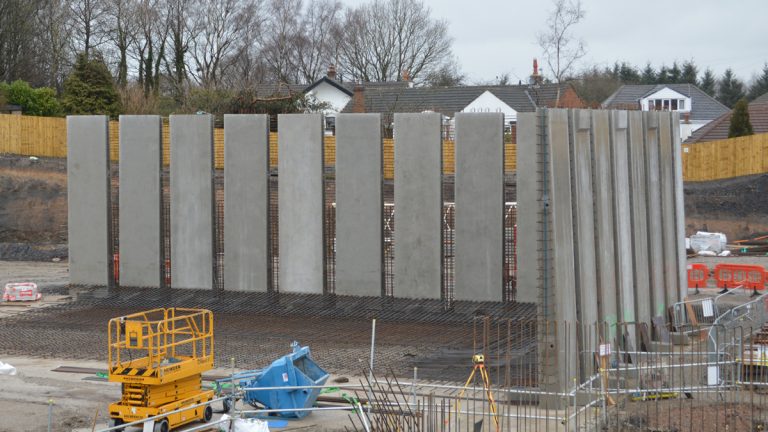
Installation of PCC wall units – Courtesy of JN Bentley Ltd
Health safety and welfare (HS&W)
There was a robust HS&W culture on site. All parties to the contract operated stringent HS&W policies, with stringent systems implemented on site that help to ensure a safe workplace. The DfMA system also had benefits to health and safety. By undertaking manufacture in a controlled factory environment it reduced the requirement for working at height, reduced trades and less man-hours required on site resulting in less exposure to risk. Just-in-time deliveries also resulted in a tidier and more efficient site.
Project efficiencies
It has been estimated that using the PCC system has saved approximately 12 months when compared to an in situ concrete solution.
There have also been economies in the labour/trades required on site due to the construction methodology adopted. There has been material savings through the minimising of waste and potential reduction of re-work. The system has also given greater certainty of programme as it is not weather dependant.
In April 2015, the project delivery team was awarded the United Utilities ‘Quarterly Safety Prize’ in recognition of excellent performance in the field of health and safety whilst delivering a number of projects for United Utilities – and in particular the fine efforts of the team working at Jackson’s Edge.
Response to the client’s brief
The project has met all the client’s requirements and has also delivered on the United Utilities company values of innovation, customer focus and integrity.
The new SR will provide increased security of supply to the water network. The twin compartment tank will enable future inspection and maintenance, and the new bypass pipework and scour pipework will also improve the operability of the new asset.
The innovative DfMA construction approach has provided the lowest whole life cost (WLC) solution for the client. It has also reduced the impact of construction on neighbouring residents, providing a shorter construction schedule, reduced the number of traffic and wagon movements to and from the site, and mitigated other construction factors such as noise, dust, and vibrations. The Intelligent Membrane provided on the PCC roof is in line with the UU’s ‘Future Concept of Operation’ allowing remote monitoring of the integrity of the reservoir roof. Environmental management has ensured no net loss of biodiversity.
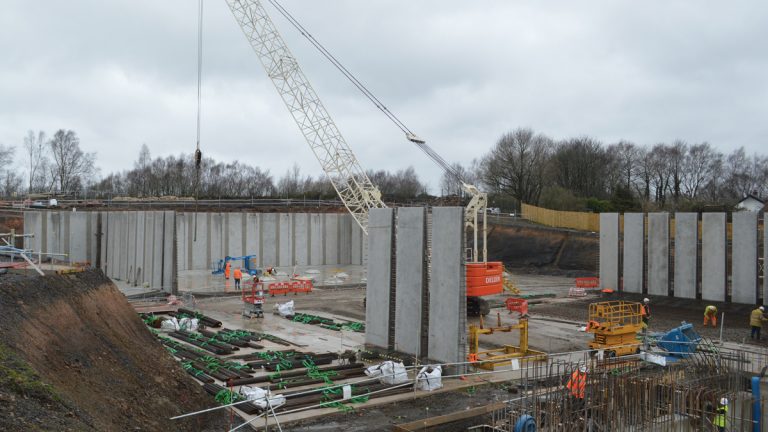
Logistically complex site – Courtesy of JN Bentley Ltd
Conclusion
The construction of compartment one of the new Jackson’s Edge Service Reservoir has seen the implementation of United Utilities’ first ever rectangular precast service reservoir to add to their asset portfolio.
Community liaison has been critical across this logistically challenging project as the site is situated in the middle of a residential area and close to several leisure facilities in Disley, Cheshire. The delivery team hosted a number of community liaison events and the use of off-site manufactured products which reduced the length of time we were on site, minimising our impact on the local residents and business owners.
In total the 126 (No.) wall units, 132 (No.) beams, 120 (No.) columns and 400 (No.) roof slabs that were all precast in factory conditions away from site have been delivered and carefully crane-lifted into position to form compartment one.
Once commissioned and put into service, the old service reservoir can be decommissioned and demolished to make way for construction of compartment two to be constructed ahead of the 2016 completion date.