Lynemouth Mine Water Treatment Scheme (MWTS) Phase 2 (2020)
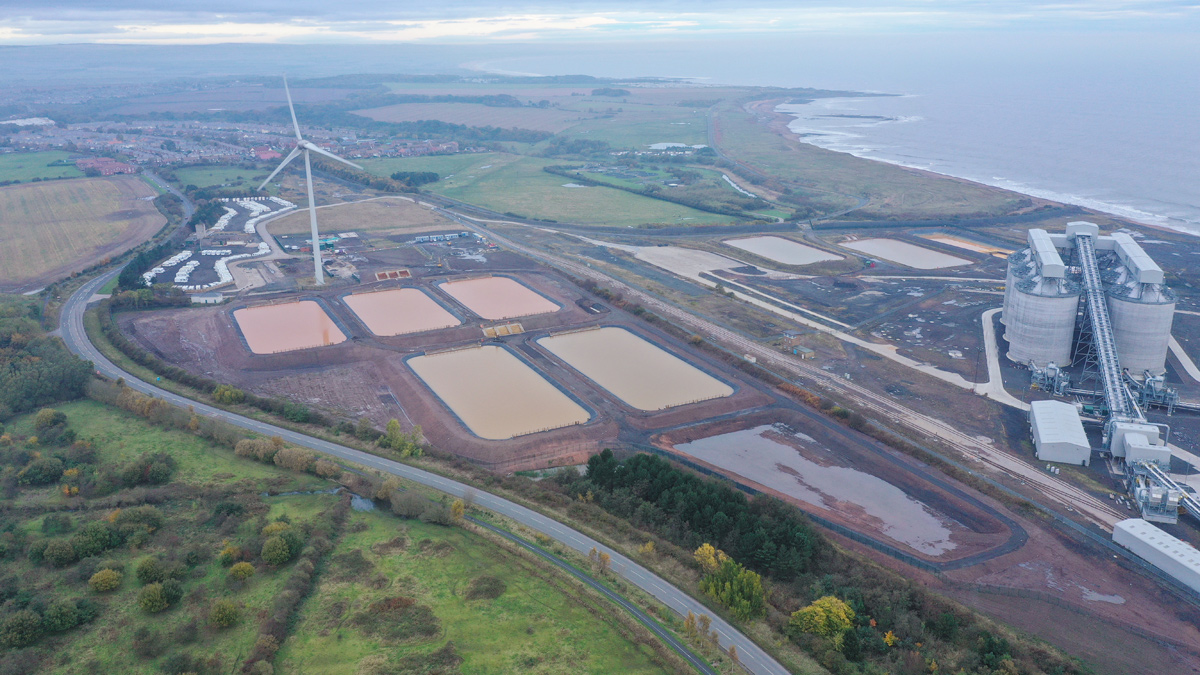
Lynemouth Mine Water Treatment Scheme: Phase 1 on right, Phase 2 on the left - Courtesy of Skylark Aerial for JN Bentley and the Coal Authority
The Lynemouth Colliery was part of a larger mining block linked to Ellington Colliery (Ellington Combine) that worked reserves under the North Sea; the mining block extended inland close to Morpeth. Groundwater lies above the rocks forming the coal measures. If mine water was to rise unchecked, it could pollute a source of water for drinking and industrial uses. If this groundwater was polluted, the effects could be irreversible. There was also a longer-term risk of uncontrolled discharges into the rivers or sea if mine water was to be allowed to rise above sea level. Although not harmful to people, the elevated levels of iron in the water could have a detrimental impact on local habitats and wildlife. The Coal Authority employed JN Bentley as framework partner to design and build the second phase of the Lynemouth Mine Water Treatment Scheme on the site of the former Lynemouth Colliery in Northumberland.
Background and planning
Historically water levels were controlled at several pumping stations in the area, however, pumping ceased in 1994, with the colliery finally closing in 2005. Since mining stopped, water levels have been rising across the block. The first phase of the scheme was constructed by JN Bentley/Coal Authority in 2014. This comprised pumping infrastructure and two 5,000m2 settlement lagoons capable of treating up to 100l/s of mine water. This slowed the rise of mine water and provided information to determine the longer-term pumping and treatment strategy within the mining block.
Following this review, the treatment capacity at Lynemouth needed increasing to treat 206 l/s. The £4m second phase involved the construction of an additional five settlement lagoons with a combined treatment area of 23,000m2 capable of holding 56,800m3 of mine water. Additional pumping capacity was installed within the existing shaft, together with distribution pipelines, inlet and outlet structures, fencing, landscaping, protection works to the existing wash channel discharging treated mine water to the North Sea and a sludge drying bed.
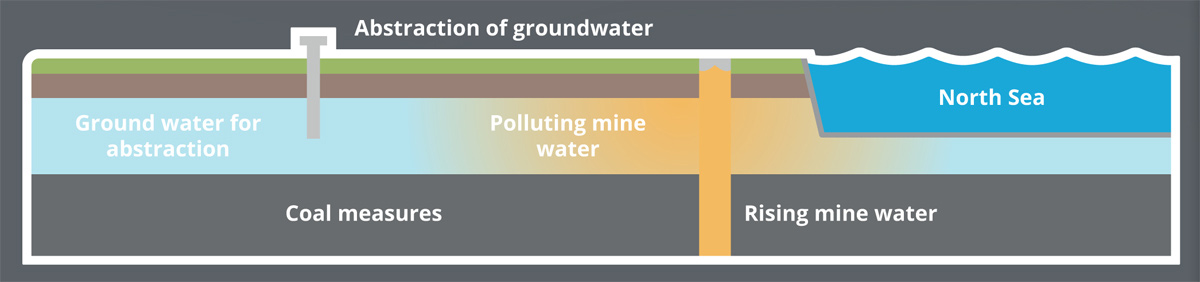
Schematic showing potential pollution from rising mine water – Courtesy of the Coal Authority
How it works
1. Water is pumped from the colliery’s old mine shaft.
2. Air mixes with the mine water as it falls down the cascade steps, which causes the iron to oxidise and form particles.
3. The water moves slowly through the lagoons. Large iron oxide particles fall out of solution and settle in the bottom of the lagoon.
4. Air is added again, by passing water over a second cascade, to repeat the process and remove even more iron.
5. Periodically the iron sludge is removed from the lagoons and taken to the drying bed, to remove excess water so it is easier to store or move.
6. Water is discharged into the sea.

Mine Water Treatment Scheme – Courtesy of the Coal Authority
Lynemouth MWTS: Supply chain – key participants
- Client and principal designer including process treatment sizing requirements: The Coal Authority
- Principal contractor & construction: JN Bentley
- Detailed design of MEICA infrastructure & environmental and ecological support: JBA Consulting
- Detailed design of earthworks, cascades, lagoons and pipework: Mott MacDonald
- NEC project manager and Supervisor: Turner and Townsend
- Support and funding: Department for Business, Energy & Industrial Strategy (BEIS)
- Motor control centre: Labtec (Services) Ltd
- Asbestos monitoring: Wood Group
- Tree/vegetation clearance: Premier Tree Services
- Fencing: Peart Fencing Ltd
- Geomembrane lining: Celtic Lining
- Precast manufacture: Carlow Tanks
- Mechanical installation: Powerrun Pipe-Mech Ltd
- Electrical installation: Dimewest Installation
- FRC and confined space survey: ARM Pipetek Ltd
- Kiosk: Morgan Marine
- Aerial photography: Skylark Aerial Photography
- Submersible pump: Wilo UK
Ochre
The iron sludge (hydro ferric oxide) collected in the settlement ponds as part of the mine water treatment process is known as ochre. To maintain the performance of the scheme, this ochre is periodically transferred to a drying bed and then a polytunnel, where excess water is removed to significantly reduce its volume. The Coal Authority’s innovations team are researching new ways of reusing the ochre to minimise waste and cost. Possible uses found to date include ground remediation projects, within water treatment systems and as a pigment in paints.
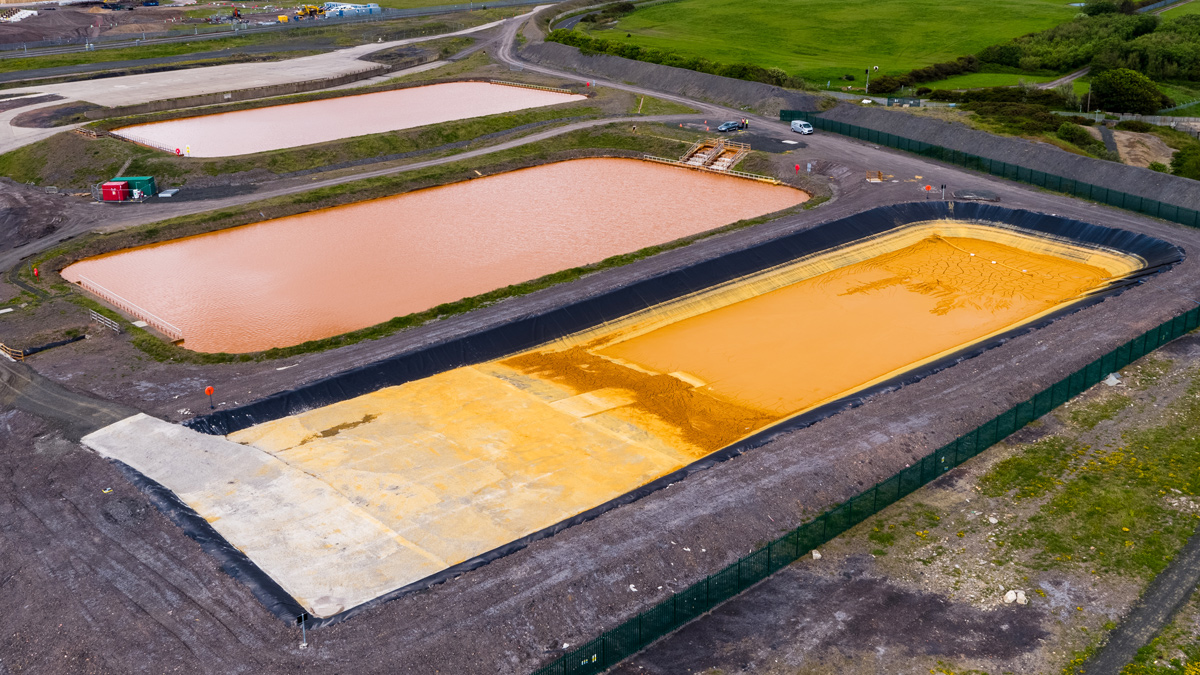
Hydro ferric oxide collected in the sludge drying bed – Courtesy of the Coal Authority
Reuse of materials
One of the key criteria for the scheme was the reuse of site-won material. As the site was located on a former colliery, there was a significant risk of ground contamination from past land use. During the design an extensive suite of ground investigations was carried out and the material tested and assessed to determine the risk of reusing it. The CL:AIRE Definition of Waste Code of Practice (DoWCoP) was used to ensure the material was properly managed on site and enabled 50,000m3 of material to be reused on site without harming the environment. During the earthworks, asbestos, hydrocarbons and old infrastructure was encountered. This required segregation and analysis before being reused in construction or disposed of off-site.
A hotspot of contamination was identified during the earthworks. In line with the remediation strategy for the site, this was stockpiled and segregated while further lab analysis was undertaken. This confirmed suspicions that the material was contaminated with hydrocarbons; at 12 times the hazardous waste limit. Instead of sending this material to landfill, a local company was sourced that undertook soil remediation to treat the material so it could be utilised for landfill capping instead of becoming part of the landfill. This saved 1,800 tonnes of material entering landfill.
De-sludging
Throughout the design and construction stage, the final operability of the scheme was continually reviewed, and standard construction details modified to suit. When in operation the lagoons need to be regularly de-sludged, which has historically been undertaken with extensive pumping and with considerable resource. This scheme’s levels were designed to facilitate a permanent gravity piped solution from the lagoons to a new sludge drying bed. This will both reduce operational costs and aid operation during the scheme life.
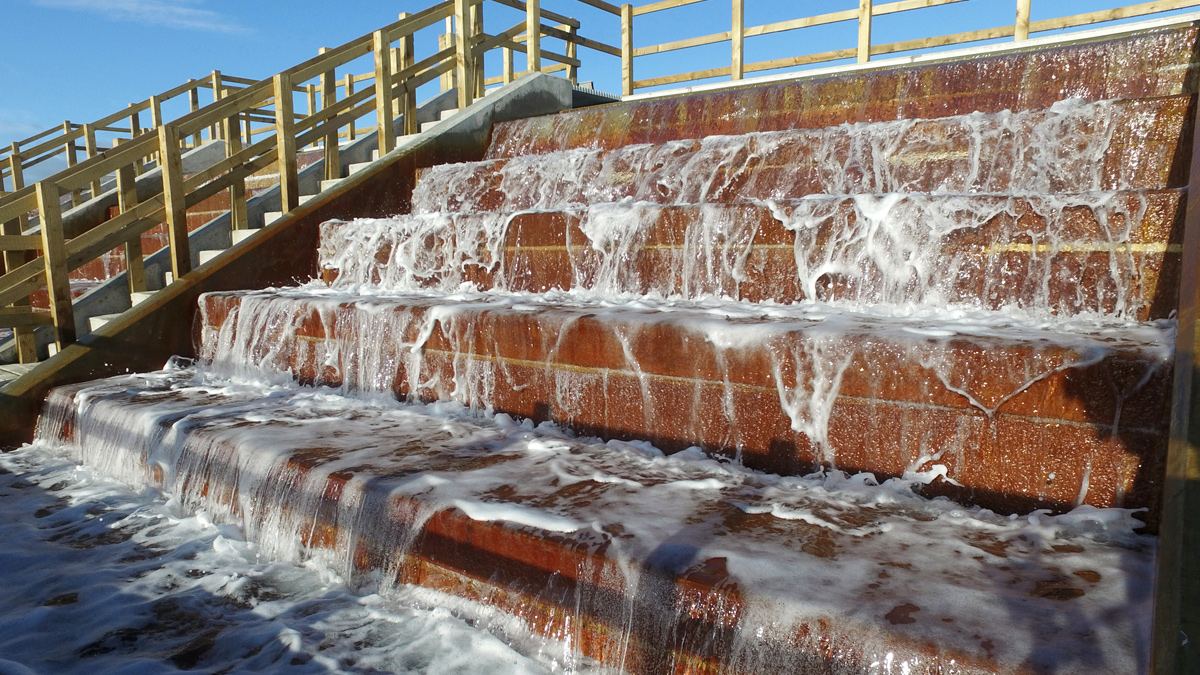
Cascade in use – Courtesy of JN Bentley
Cascades
The cascades site requires periodic maintenance to prevent the build up of ochre on the steps. Therefore, the cascades were split into three sections with access steps between each section to facilitate maintenance. The standard precast solution was modified to extend the width of the cascade. This posed several construction challenges due to the weight of units to be installed, which were exacerbated by the lifting restrictions from the adjacent wind turbine. Working collaboratively with the designers, construction team and the precast supplier (Carlow Tanks), the units were designed to be thinner than standard and divided into sections with a maximum weight of 4.5t, so each one could be lifted and installed with an excavator.
Treated flows
Exiting the lagoons, the treated minewater had to flow under an existing railway siding supplying the adjacent power station. These flows would then meet the discharge from the existing Phase 1 lagoons and flow to the North Sea. In the outline design a new directionally drilled pipe was to be installed. However, investigation identified an existing tunnel system on site. Following survey and remedial works, this was reused, eliminating the need for a new crossing under the railway.
Once under the railway, the increase in discharge flow from the new lagoons meant that there was a need to increase the overall capacity of the existing outlet channel to the North Sea and provide erosion control to the existing slopes above the discharge channel. The channel measured 195m long, with side slopes 2.5 to 8m wide.
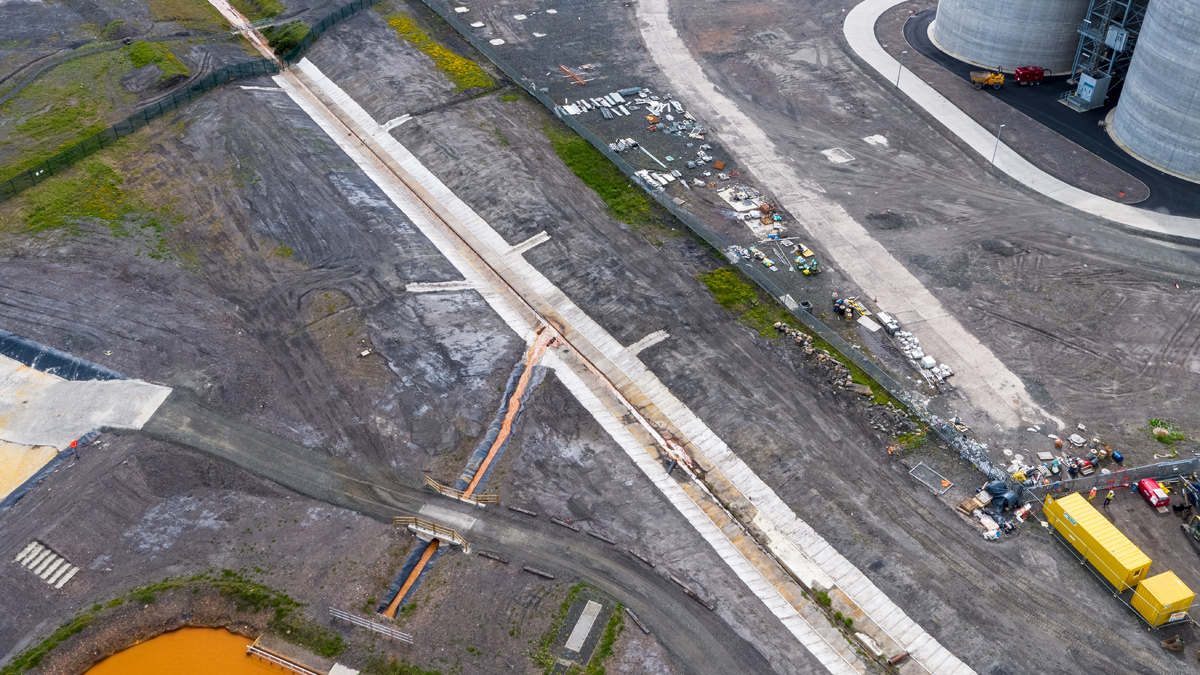
Concrete canvas lined discharge channel – Courtesy of the Coal Authority
Concrete canvas
Initially, it was considered to use a geotextile or in situ concrete to provide the erosion protection to the slopes. Concrete Canvas was ultimately chosen due to its puncture resistance, durability and UV resistance compared to an exposed geotextile, and for efficiency and reduced carbon over in situ concrete.
This was anchored within an anchor trench cut within the existing slide slope and fixed to the existing channel with a stainless-steel bar and masonry bolts. Along the length of the channel there were several small channels that were suffering from the washing out of the substrate when heavy rain occurred and these were formalised as part of the works to help with the overall management of water on the site.
The new Wilo K10.310 borehole pumps, being used for the first time in the UK, offer a 10% efficiency gain against their next best alternative, with the permanent magnet motors giving added efficiencies. The calculated cost saving of the pump in energy alone equates to £4k per year.
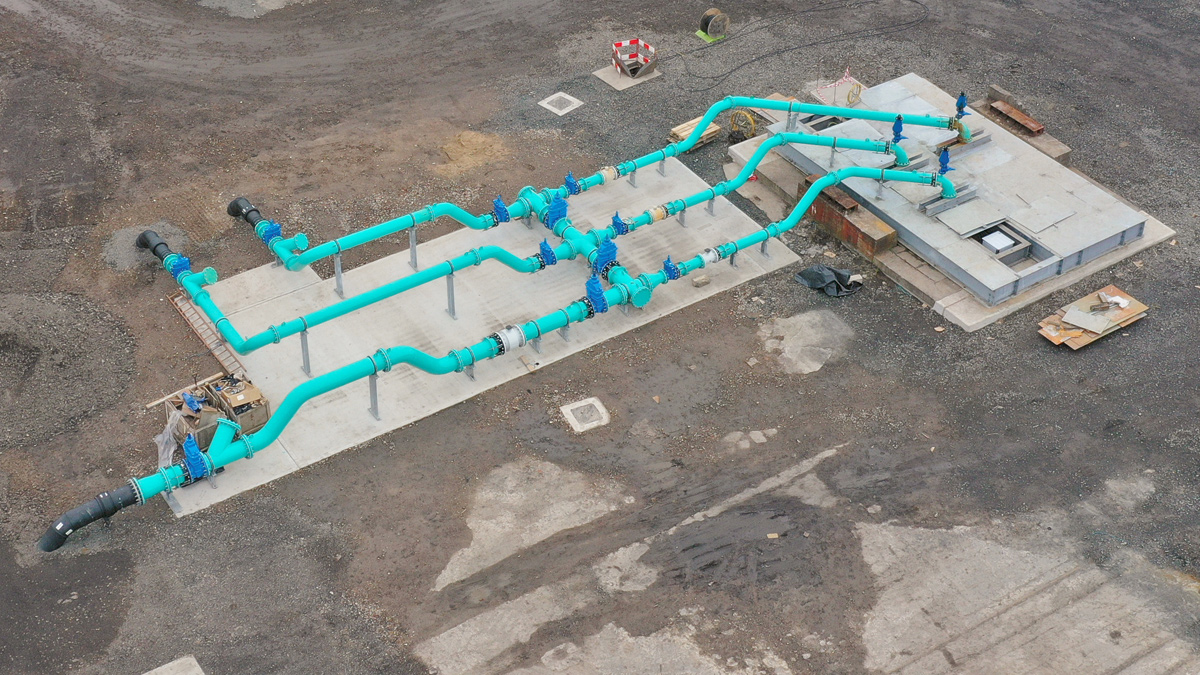
Mine shaft with new pumping arrangement – Courtesy of JN Bentley
Summary
The biggest benefit to the community that the project has brought about is the scheme prevents untreated mine water entering groundwater resources and the North Sea. Based on the current situation of mine water levels and pumping requirements, at full capacity the scheme can annually treat more than 6 billion litres of mine water, the equivalent of 2,400 Olympic swimming pools, removing 300 tonnes of iron in the process. It is estimated that the scheme will protect approximately 1.6 million cubic metres of usable groundwater.
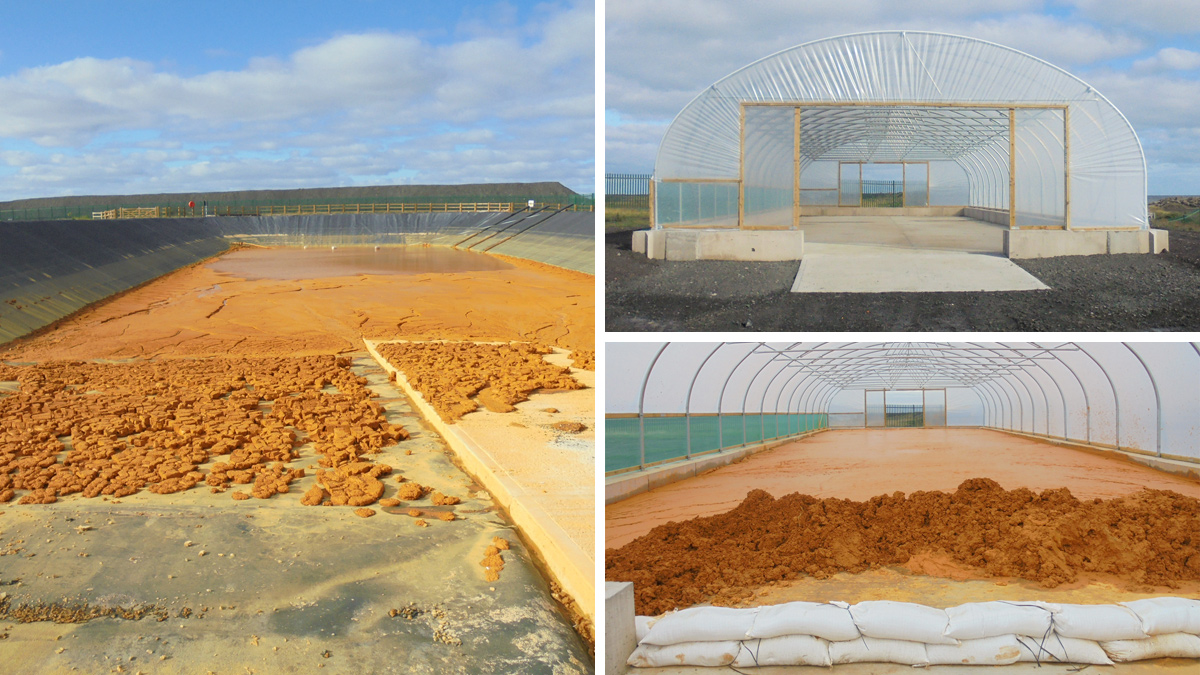
(left) new sludge drying bed following first de-sludge, (top right) polytunnel and (bottom right) polytunnel full of ochre in drying process – Courtesy of JN Bentley
The area on which the MWTS lies is a brownfield site, which was unused and unsuitable for most types of land use. Utilising this area has prevented the project using productive land and provided an environmental benefit. In total 1,240kg of asbestos containing soils/material were removed from site and disposed of at a suitably licenced facility.
The project has been shortlisted for the IEMA Sustainability Impact Awards 2020.