Macallan WwTW (2016)
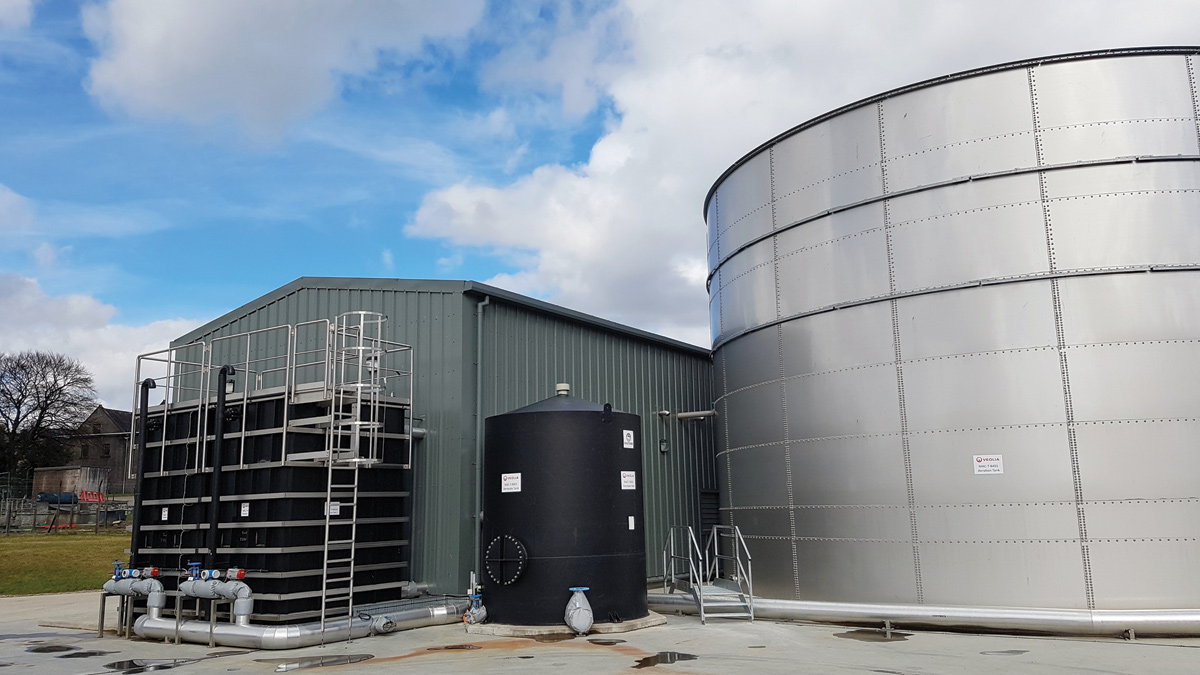
Aeration tank, UF permeate backwash tank and external ultra filtration (UF) tanks - Courtesy of Veolia Water Technologies
The Macallan owners, Edrington, have commissioned an iconic new distillery and visitor centre which will see the distillery transformed into a beautifully designed architectural building that embodies The Macallan’s uncompromising approach to quality and luxury. Over time the distillery will also deliver additional capacity to meet the growing global demand for the world famous Macallan single malt whisky. As part of this ambitious project Veolia Water Technologies was engaged to provide a new wastewater treatment plant on site to handle the future increase in capacity and meet the SEPA regulations for discharge into the environmentally sensitive River Spey. Key to the success of the project was valuable experience acquired while working on The Macallan’s previous wastewater treatment plant, plus a wastewater characterisation study prior to the design of the new plant. The knowledge gained and a close working relationship with engineers from The Macallan enabled the Veolia team to forge ahead with a high degree of confidence that they had the right solution.
Process selection
An initial process review by Veolia of the original waste water treatment plant operation allowed Veolia to better understand the technical requirements of the project and provide support in operating the original plant until the new facility was available. This close cooperation between designers and operators was key to understanding the particular challenges faced by the process and instrumental in the development of the design and selection of key technologies.
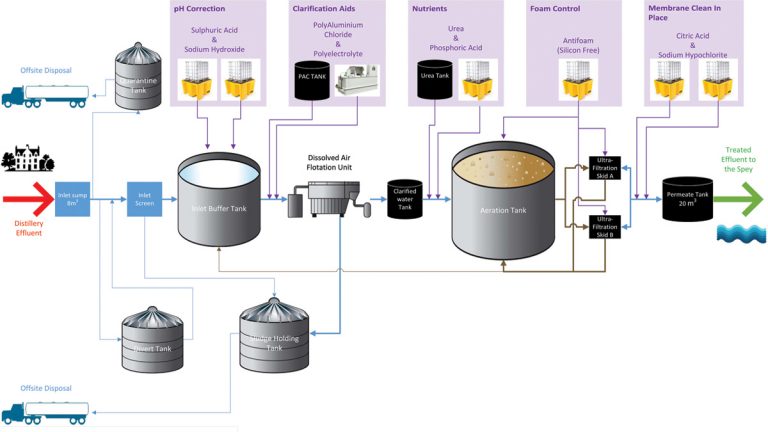
Process diagram – Courtesy of Veolia Water Technologies
A review of the historical operating results of the original plant as well as a twelve week characterization study of the influent, carried out by Veolia, allowed for a high degree of confidence in plant sizing. Based on this initial work, Veolia was able to develop a number of different process options to meet Macallan’s requirements of improving the waste water treatment quality, maintaining the stringent river discharge consent and increasing the treatment capacity to allow for the increased flow and loads from the distillery expansion.
This characterisation report was used as a basis to compare treatment process in order to determine the optimum technology for The Macallan Distillery. The technologies under consideration included:
- Anaerobic UASB/EGSB.
- Anaerobic MBR.
- Aerobic CAS.
- Aerobic MBBR.
- Aerobic MBR.
Following consideration of the influent wastewater characteristics, treatment quality requirements, operational security and site environmental targets, it was jointly decided to design the treatment solution around the Veolia Biosep® MBR technology.
The Biosep® MBR process uses an ultra filtration (UF) membrane barrier to ensure a high treated wastewater discharge quality. The small footprint and modular nature of the UF membranes allows for simple future upgrading, should The Macallan decide to increase spirit production in the future.
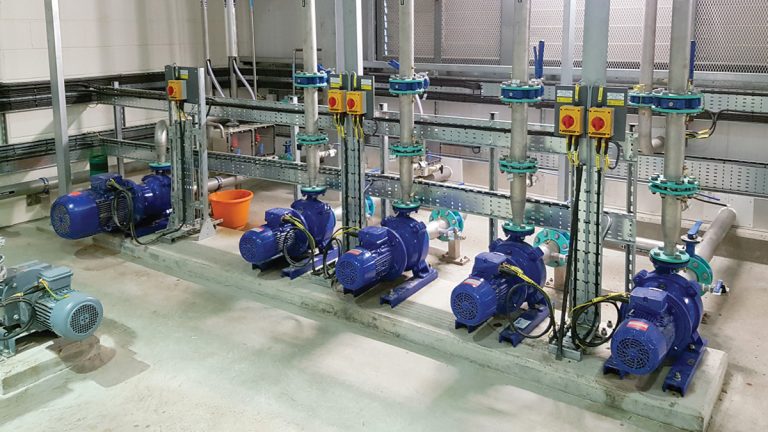
Main process pumps arranged internally within process building – Courtesy of Veolia Water Technologies
Process overview
The installation is based on two proprietary Veolia technologies; the IdraflotTM dissolved air flotation (DAF) unit followed by a Biosep® membrane bioreactor (MBR).
Effluent from the distillery (excluding draff and pot ale) gravitates into an initial collection sump where in normal operation it is pumped through a 2mm punched hole brushed screen to discharge into the inlet buffer tank. The effluent is automatically routed to the quarantine tank if its temperature is measured above 40oC or to the divert tank if its pH is above pH 9. In this way the downstream process is protected from gross solids, pH and temperature spikes and hydraulic fluctuations.
The balance tank will even out fluctuations of flow and load, allowing a more consistent feed to the DAF and MBR treatment stages leading to better operation and reliable wastewater quality.
The high pH contents of the divert tank are automatically returned via the screen to the inlet buffer tank to reduce the requirement for pH correction chemicals.
The contents of the inlet buffer tank are pH corrected to above pH 7.3 to precipitate copper from the Spent Lees; they are then pumped forward to the IdraflotTM dissolved air flotation (DAF) unit to remove suspended solids including precipitated copper solids. A coagulant and a flocculant are dosed upstream of the DAF unit to assist in the removal of suspended solids.
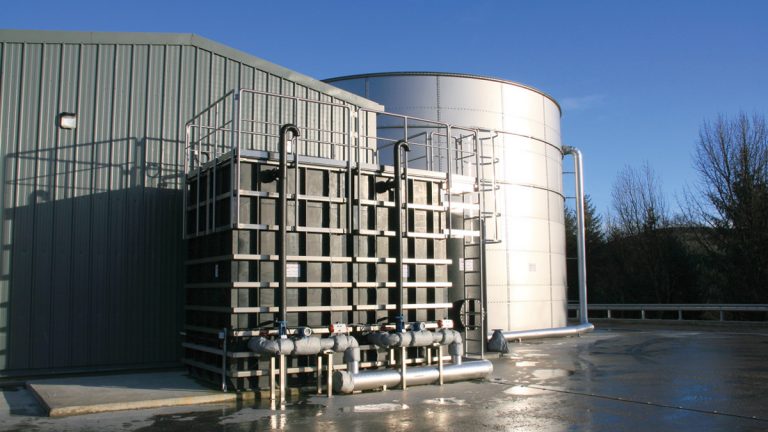
Process building with external ultra filtration (UF) tanks – Courtesy of Veolia Water Technologies
The clarified liquors from the DAF unit are then dosed with two nutrients, urea and phosphoric acid, before being pumped into the aeration tank where the organic substrates (BOD) within the liquors are degraded by the aerobic biology. Air is continuously added to the contents of the aeration tank via a fine bubble air diffuser system to ensure a healthy biological system is maintained.
A mix of biological solids and treated liquors gravitate from the aeration tank to the dual stream ultra-filtration (UF) membranes where the treated liquors are separated from the biological solids and the high quality permeate can now be safely discharged to the River Spey. The biological solids are maintained within the system and returned to the aeration tank to continue to treat the incoming effluent.
Periodically The UF membranes are automatically chemically cleaned in place (CIP) to prevent fouling and maintain hydraulic through-put. Excess biological solids are transferred to the Inlet buffer tank to be thickened and removed from the system by the DAF unit.
The gross solids removed by the screening system and the thickened solids generated by the DAF unit are stored within a sludge buffer tank prior to being taken off site for disposal.
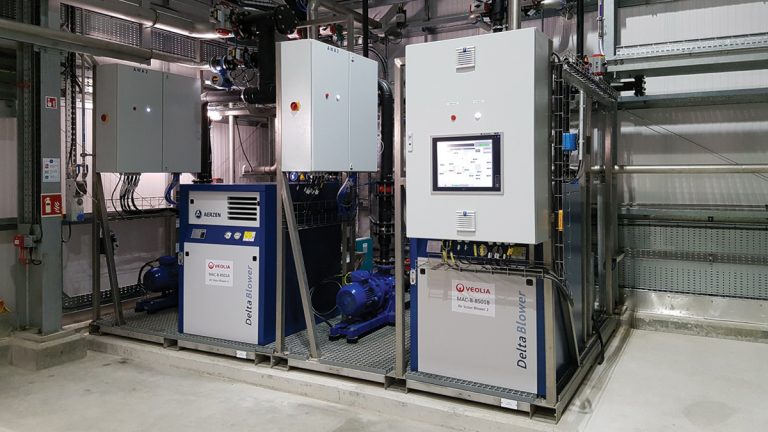
Internal UF membrane pump skids – Courtesy of Veolia Water Technologies
Plant capacity and future proofing
The treatment capacity of the installed plant is capable of treating 390m3/day and 2,691kg/day of COD peak loading. To ensure process reliability and operational flexibility over 1.5 days of buffer storage capacity have been provided at this peak hydraulic flow rate. Similarly over 7 days of sludge storage capacity is provided on site to assist in disposal logistics. Duty/stand-by arrangements of all process and chemical pumps have also been provided to ensure a high degree of reliability and assist in maintenance tasks.
The dissolved air flotation unit has also been specifically selected to allow for greater hydraulic through put and allowances have been made in the placement of equipment for ease of upgrade as demand for whisky increases.
The site layout has also been designed to provide maximum protection against sustained periods of temperatures down to -25oC during the winter months by centralizing the main mechanical equipment within a dedicated process building and minimizing external pipe runs a far as practicable.
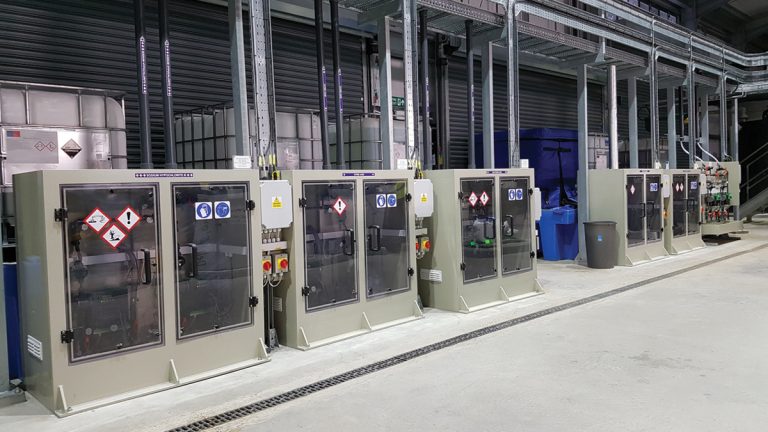
Chemical dosing pump skids – Courtesy of Veolia Water Technologiess
Project delivery
Detailed process design development and equipment procurement began in May 2014 and was carried out by Veolia from its Birmingham office with regular on-site project status meetings held at The Macallan Distillery.
Following initial ground preparation and civil’s works carried out by Blyth and Blyth and Caledonia Property Maintenance including the movement of existing cooling water pipes and ground piling, Veolia took over the role of principle contractor in March 2015 and oversaw the installation and carried out the commissioning of all process plant and equipment.
First acceptance of flows into the new plant began in September 2015 following the planned summer shutdown of the distillery.
Testing and commissioning
The biological process was seeded with biological sludge from the existing on-site treatment works thus ensuring the biological process was as adapted as possible to the incoming influent. This allowed for a rapid phased ramp up of the plant to 100% of available flows and synchronous ramp down of the existing works over the course of 6 weeks.
Following this period chemical dose rates and plant performance were optimized and the plant was ultimately handed over to the client in February 2016. Throughout this period plant performance has remained well within consent parameters and an average discharge quality of:
- 37.1mg/l COD.
- 3.2mg/l BOD5.
- 253 μg/l dissolved copper.
- 2mg/l suspended solids.
- 2.9mg/l orthophosphate.
- 8.5mg/l ammonia & total oxidisable nitrogen (TON).
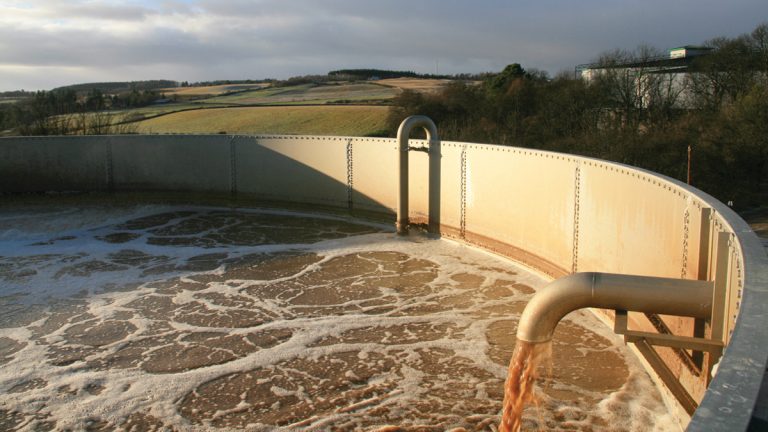
Surface of activated sludge aeration tank – Courtesy of Veolia Water Technologies
Conclusion
The Macallan Distillery Wastewater Treatment Plant has been built with reliability and future proofing in mind and can be easily upgraded as demand for the whisky production increases.
By working closely with the client Veolia have been able to better understand their requirements and schedule installation and commissioning work to synchronize with the existing production and maintenance programme allowing for a rapid and successful start up of the new process plant. Edrington’s UK Engineering Manager, George McKenzie, is delighted.
“Based on Veolia’s experience we expected to achieve a good quality discharge – certainly well within the consent limits – and that we have done”, he says. “In addition the new plant has a much higher level of automation which means reduced operator involvement.”
The new plant is now fully up and running, and has the potential for reducing the distillery’s water footprint and water costs by recycling high quality treated wastewater for use in many areas of the plants operation instead of potable water.