Maerdy WTW (2021)
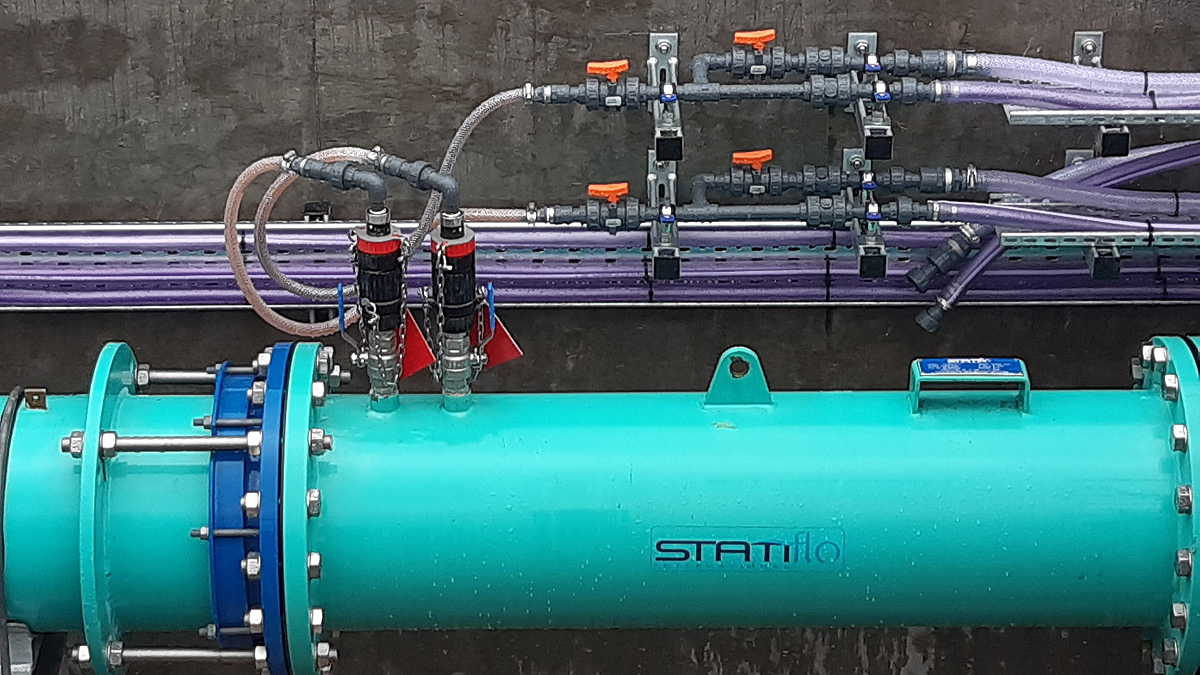
Ferric dosing plant - Courtesy of MMB
Maerdy Water Treatment Works (WTW) is located 35km north of Cardiff, supplying up to 16Ml/d potable water to customers in Ferndale and the surrounding area. Raw water is gravity fed from Castell Nos and Lluest-Wen Reservoirs and the quality can be highly variable, particularly following heavy rainfall resulting in a challenge to WTW performance. In addition, raw water quality varies between the two sources which supply the WTW. Planned maintenance on one of the impounding reservoirs feeding the WTW has necessitated a process review to ensure works performance remains robust during the planned reservoir safety works.
Project scope
MMB have undertaken the following process improvements at Maerdy WTW:
- Resilience project: Source blending and improvements to lime and ferric dosing and mixing to improve the effectiveness and stability of the coagulation process.
- Chlorination project: Replacement of the on-site electrolytic chlorination (OSEC) production, storage, and dosing system with bulk sodium hypochlorite storage and dosing following dilution with service water.
Resilience project
The existing inlet works consisted of raw water from both Castell Nos and Lluest Wen reservoirs freely discharging into the first stage flash mixer via dedicated mains. Lime and ferric sulphate were dosed using a sparge pipe into the top of the tank and A mechanical mixer provided mixing energy before distribution to 2 (No.) flocculation streams.
MMB worked in collaboration with Welsh Water and suppliers to identify the disadvantages of the existing dosing system and identify and develop options for improvement.
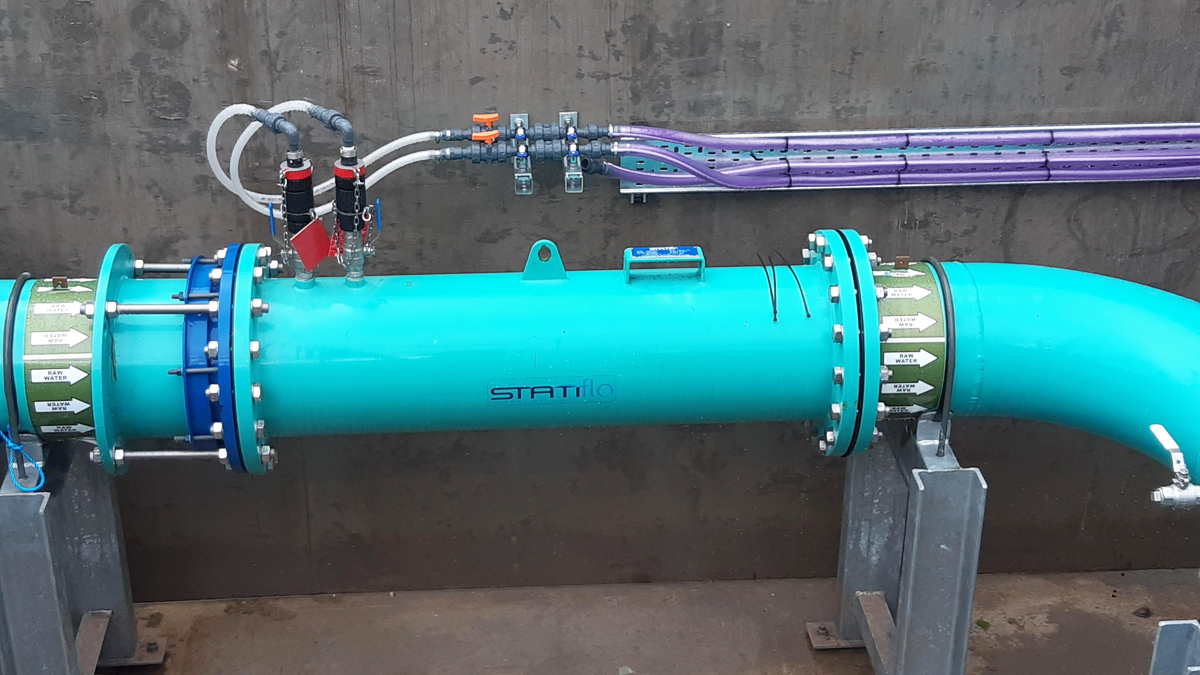
Lime dosing plant – Courtesy of MMB
The key findings were as follows:
- The existing chemical dosing and mixing arrangement was not compliant with Welsh Water design specification requirements resulting in sub-optimal coagulation and flocculation conditions.
- The existing flash mixer was inefficient, requiring constant power input and creating very high shear conditions that can have a detrimental impact on floc formation.
- Flocculation conditions were visibly different in each treatment stream strongly suggesting that front-end mixing conditions were not providing a homogenous mix upstream of the flow split. This difference was resulting in variable plant performance which was particularly noticeable during periods of poor raw water quality.
- Replacing the existing mixing arrangement with dedicated static mixers for both lime and ferric sulphate was identified as the best course of action as it would eliminate energy consumption and provide efficient, effective, and compliant mixing, leading to reduced chemical costs and improved plant performance. Reducing the chemical dose would also result in a reduced sludge volume requiring off-site disposal.
The following scope items were agreed to improve the front-end process:
- Construction of a common manifold downstream of the existing flow meter chamber to combine water from both Castell Nos and Lluest Wen reservoirs, direct the flow through the new static mixers and discharge water into the existing first stage flash mixer tank. The existing dose points were to be relocated so that chemicals were dosed via injection lances that form part of each static mixer assembly. Each chemical was to have its own static mixer to ensure full ‘in-pipe’ mixing prior to introduction of the next chemical. The chemical dosing sequence was agreed to be lime followed by ferric sulphate. Provision was also made for a carbon dioxide dosing point upstream of lime dosing, for installation at a later date.
- Removal of existing mechanical mixer within the first stage flash mixer.
- Relocation of the carrier water injection point for the coagulant to as close to the point of application as possible to minimize risk of hydrolysis.
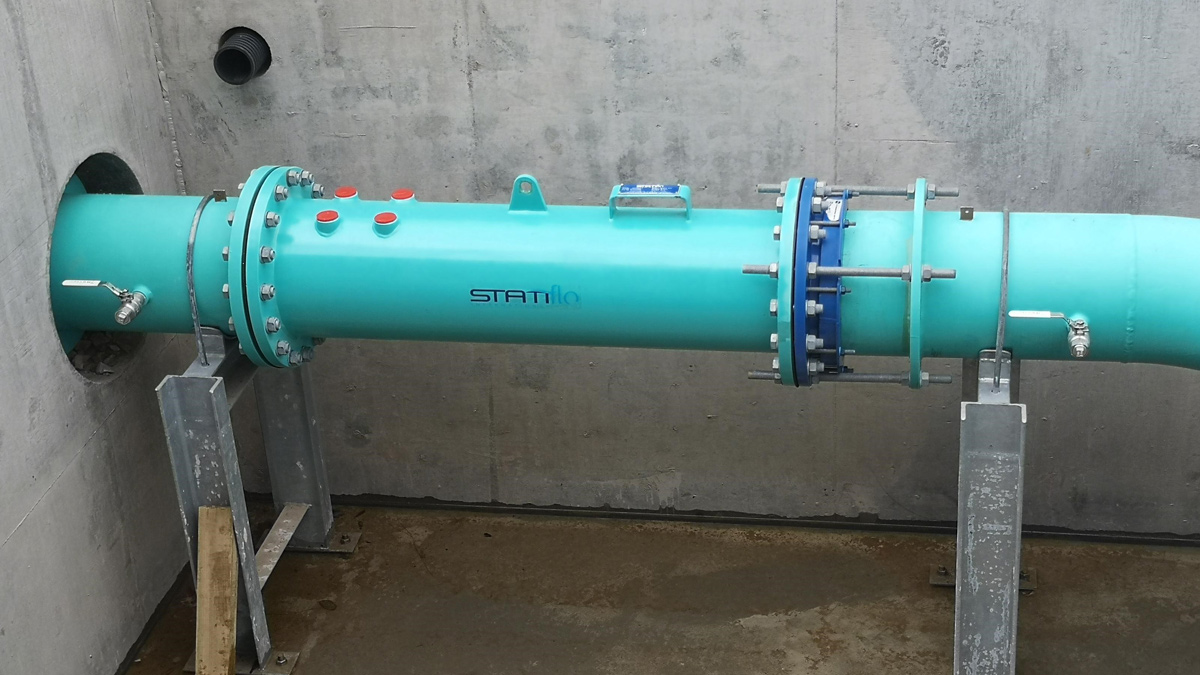
CO2 static mixer – Courtesy of MMB
During the design stage, hydraulic calculations were completed to ensure sufficient hydraulic head was available to deliver the required flow rates (3-16 Ml/D) to the works. Process calculations were completed to confirm the required range of lime and ferric sulphate dose rates to treat all anticipated raw water blends. The range of dose rates was critical to informing specification and procurement of the static mixers.
The design team opted for precast concrete for the chamber construction with dimensions of 5.2m (L) x 4.6m (W) x 2.5m (H). The chamber was delivered to site in sections and the assembly was completed within two days. This minimized the amount of work required on site, therefore reducing the health and safety risks and waste generation. Pipework was prefabricated in flanged steel to aid with installation and eliminate the hazard associated with dissimilar metals.
Following installation of the static mixers, Welsh Water reviewed the performance of each aspect of the treatment process and were satisfied that a significant improvement in works stability and resilience had been achieved, with cost savings being achieved for coagulant chemical, a reduction in power and water consumption associated with reduced filter washing activities and reduced sludge production resulting in reduced off-site disposal costs. In addition, the improvements associated with the front-end of the works has resulted in the works becoming less dependent on operator intervention.
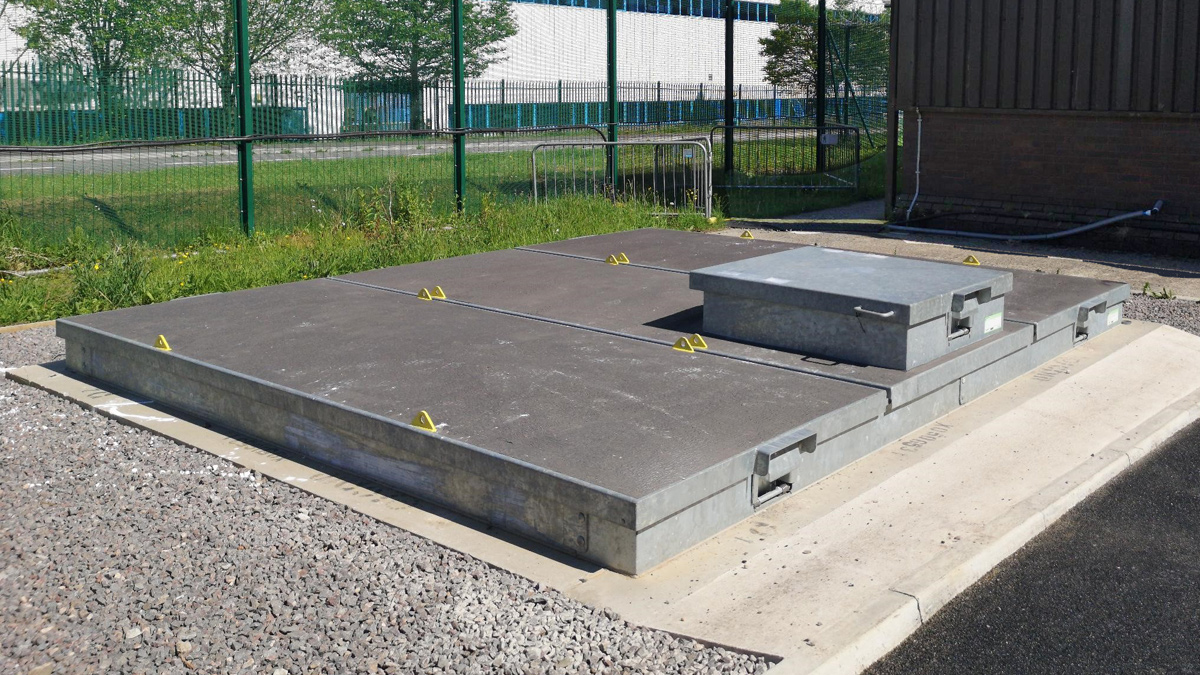
Maerdy dosing chamber – Courtesy of MMB
Maerdy WTW: Supply chain – key participants
- Client: Dŵr Cymru Welsh Water
- Principal designer & contractor: MMB
- Static mixers: Statiflo
- Precast chamber: Marshalls CPM
- Hypochlorite dosing package: WES Ltd
- Electrical installation: Protocol Control Systems (PCS) Ltd
- Systems integration: Oasis Software Solutions
- Bespoke pipework: Industrial Pipework Services (IPS)
- CO2 dosing package: PGM Cryogenics
Chlorination project
The existing on-site electrolysis chlorination (OSEC) plant was at the end of its asset life and was therefore in need of replacement. The use of bulk sodium hypochlorite dosing is preferred by Welsh Water for Maerdy WTW as this removed the inherent risk associated with OSEC and Dangerous Substances and Explosive Atmosphere Regulations (DSEAR) zoning and presented the lowest whole life cost.
Space on site was limited and hence a temporary dosing installation was required to allow the OSEC area to be re-used to house the new bulk dosing skid. The temporary dosing utilized the existing dosing pumps and storage. Dilution was provided to enable the chemical to be dosed at the same concentration as the existing OSEC product to minimize disruption to works operation. Several works’ shutdowns were utilized to provide new pipework connections and process changeovers.
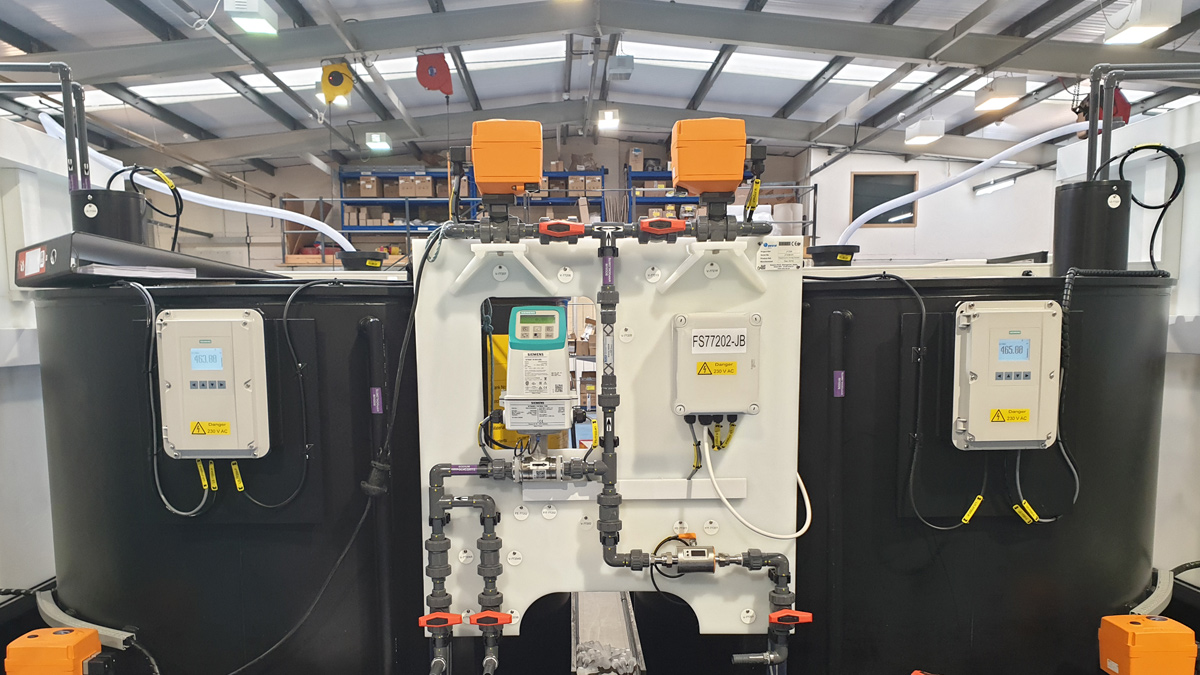
WES package dosing plant during FAT test – Courtesy of MMB
The existing OSEC room was relatively small, and it was therefore important to fully utilize the available space. The team worked collaboratively with WES Ltd to develop a compact solution that achieved this. The solution consisted of a factory-built assembly (FBA) including skid mounted dosing plant, chemical transfer and dilution, day tanks, dosing pumps and ancillaries. The design team engaged with site operatives to ensure they were satisfied with safety, access, lifting and maintenance provisions.
The FBA was Factory Acceptance Tested (FAT) off-site and transported to Maerdy WTW in one piece. The interconnecting pipework was connected, and the skid electrically installed by the appointed electrical subcontractor. The new sodium hypochlorite storage and dosing system was site tested, first with water during February 2021 and fully commissioned and put in service during March 2021.