Management of Groundwater Risks to the Water Industry (2016)
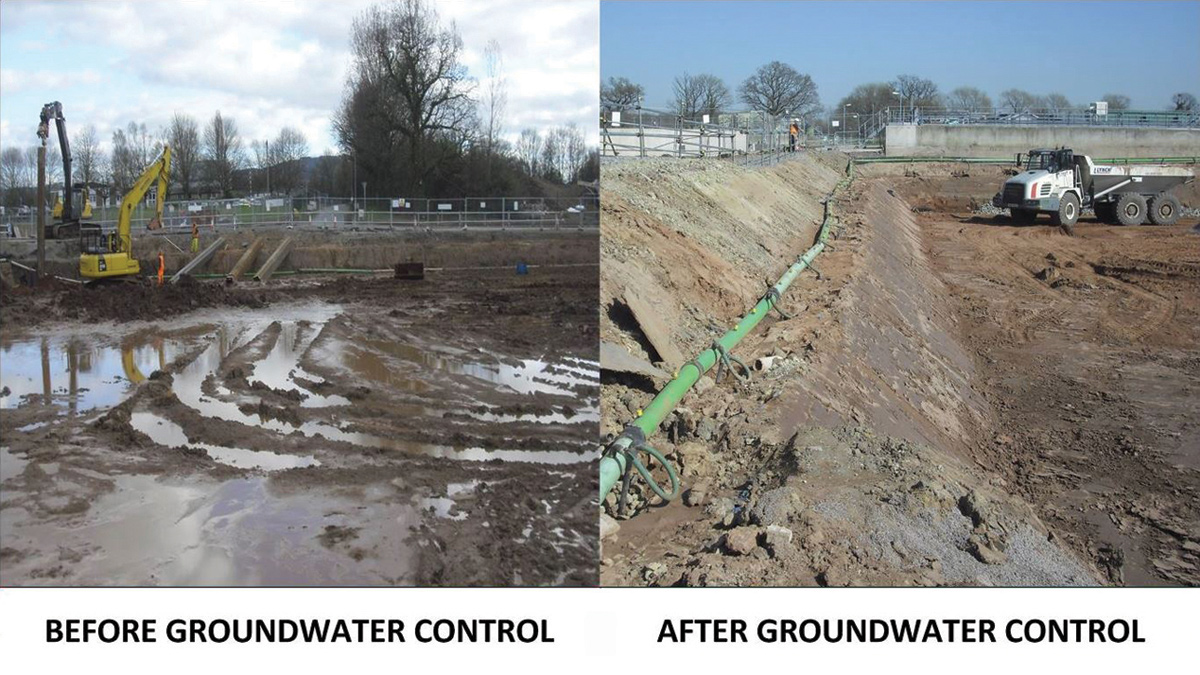
(left) Before control and (right) after groundwater control
When it comes to designing underground structures such as shafts, tanks and pipework infrastructure, it is essential that permanent works designers understand groundwater related issues. Their design typically includes measures to counteract buoyancy, to deal with lateral and vertical stresses imposed by groundwater, to provide waterproofing etc. However, the many risks caused by the presence of groundwater during the temporary works phase (i.e. the enabling works required for construction to take place), are typically not so well understood. As a consequence, the potential impact of groundwater risks to the project can go unrecognised.
Groundwater risks
The way groundwater is managed can make or break construction projects involving below ground excavation. Temporary works groundwater risks may include:
- Damage to plant and equipment.
- Environmental contamination.
- Failure of natural and battered slopes.
- Heave failure of the excavation base or base slab.
- Flotation of structures prior to the application of permanent loads.
- Increased lateral pressures on retaining walls.
- Running sand and ground liquefaction.
- Mobilisation of weak ground layers causing ground instability.
- Weak ground that cannot support structures and site traffic.
- Weak ground that is churned up by site vehicles.
- Slow, difficult and potentially unsafe excavation.
- Costly disposal of saturated soil slurry.
- Delays and failure to keep up with programme.
This list is by no means exhaustive and highlights the importance of recognising and controlling groundwater risks within the design stages of a project – not only in the permanent works condition, but in the temporary works condition also.
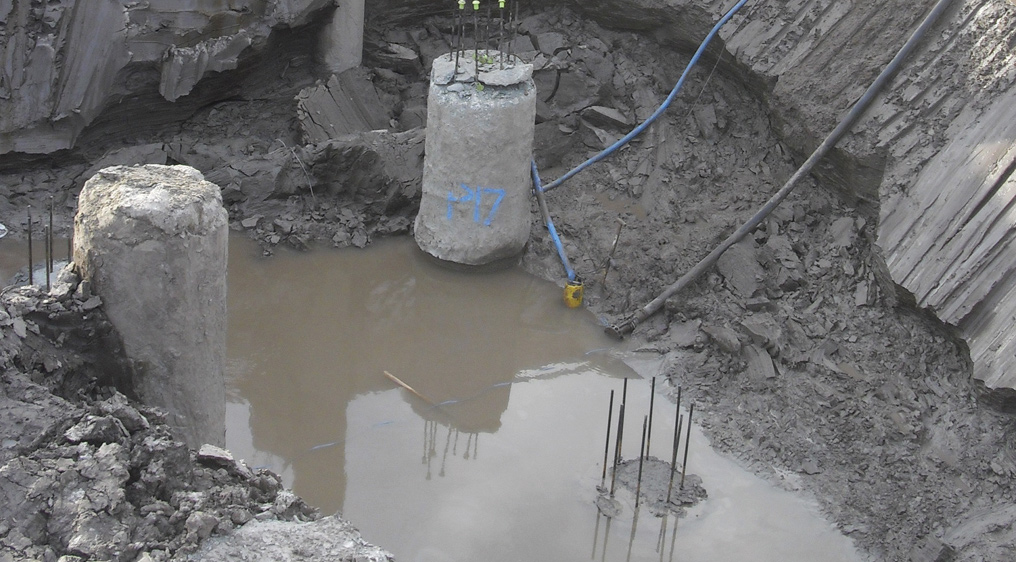
Weak ground prior to collapse – a consequence of no groundwater control) – Courtesy of OGI Groundwater Specialists Ltd
In the commercial world
When a new structure is to be built, the designer of the permanent works will typically provide a preliminary design which is put out to competitive tender.
The tendering documents will occasionally identify that dewatering may be needed, but in general do not normally spell out any detailed requirements or indeed recognise the risks associated.
Instead the tendering documents will typically include any available site investigation reports and groundwater monitoring data. Consequently, it is left to the tendering main contractor to identify the groundwater risks and cover the costs of any mitigation in their tender.
Whilst many contractors may recognise that some level of groundwater control is required, they would not typically possess the in-house knowledge to assess detailed requirements without going out to an independent groundwater specialist.
In reality, the contractor may not always allocate sufficient monies for groundwater control in their tender document. The temptation is always to keep any allocated sum to a minimum, in order to make their bid as competitive as possible, unless they are able to make a strong technical argument that the groundwater control measures proposed are essential and will provide good value to the client.
Once the contract has been awarded, if no sum has been allocated, the main contractor will try to get by with minimal groundwater control. Sometimes, with luck on their side, this approach may work. However, when things go wrong, in addition to being potentially dangerous to personnel, it can cause major delays to the project and be very damaging and costly, not only to the main contractor but also to the client.
The main contractor will often then attempt to make a claim against the client for ‘unforeseen conditions’. Arguments then ensue as to whether the claim was or was not foreseeable. This is not an ideal scenario for either party and one that consumes time and resources!
- Groundwater causes numerous risks to the successful construction and operation of underground structures.
- Within the timescale normally available at tender stage, main contractors are not always the best placed to assess the seriousness and complexity of groundwater issues and how they might affect specific projects.
- Early stage identification of risks provides more options for successful and cost effective mitigation solutions.
- Early stage identification helps to prevent claims made against the client for unforeseen ground conditions.
- Combining mitigation of groundwater risks for temporary and permanent works can result in a more efficient and innovative design, which can bring about considerable project cost savings.
The solution
If groundwater risks are identified much earlier in the project at the pre-tender stage, a safer and more cost effective solution to the risks posed by groundwater can be identified. Such risks can then be designed out of the project or mitigated against in the form of specifications or guidance notes which can be issued to the tendering main contractors.
Benefits
Identification of groundwater risks at an early stage in the project enables the project to progress in a safer, risk reduced, more predictable manner. Main contractors can then tender with an awareness of the groundwater risks that the project faces and an understanding of the type and scale of ground control measures required. They also know that their tendering competitors will all be required to compete on an equal playing field by including the costs for the groundwater control operation.
Opportunities
Significant cost savings can also be made by combining the temporary and permanent works groundwater solutions, thus avoiding duplication of effort and resources.
This opens the door to safe and innovative approaches to groundwater control. In OGI’s experience, this is where real efficiency and cost savings can be made.
Case study: Sewage treatment works in Staffordshire
This case study provides an example of a project where the client recognised at an early stage that both temporary and permanent works groundwater control were required.
Early stage assessment of the groundwater risks at site was carried out by OGI, enabling a combined approach to groundwater control. This meant that some of the most pressing groundwater risks could be designed out of the project and others mitigated against by good design. OGI was then engaged to work with the permanent works design team, to develop a system to resist groundwater uplift pressure beneath an activated sludge plant (ASP) and 5 (No.) final settlement tanks (FSTs).
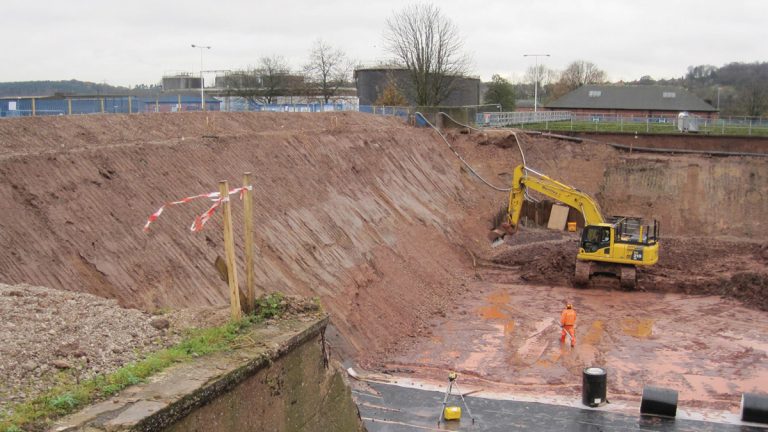
ASP steep batter construction and installation of drainage membrane – Courtesy of OGI Groundwater Specialists Ltd
The geology at the site was very weak, and consisted of clay with interbedded silts and sands. High piezometric pressure meant that the design of the new structures needed to overcome the risk of uplift forces from groundwater beneath the ASP and FST structures. This presented challenges for both temporary and permanent works.
At the start of the project, the following approach was envisaged by the permanent works designers.
- Weak ground strength meant that the ASP would need to be constructed within a secant pile wall.
- To overcome high groundwater uplift pressures below the ASP structure would require an active permanent depressurisation system.
- To overcome high groundwater uplift pressures below the FST tanks would require ground anchors to prevent flotation in the permanent works design.
For the ASP temporary works, OGI identified that the pore water pressure in the ground around the excavation could be lowered to bring about an increase in effective stress within the soil.
This would strengthen the soil such that it could support a 1:1 batter slope, replacing the requirement for secant pile walls. OGI modelled, then designed 1:1 batter slopes which were fully certificated to the design requirements of Eurocode 7.
The design to remove uplift pressure beneath the ASP slab required a structural drainage layer. A composite drainage layer of Deckdrain 1200S (incorporating non-woven general purpose membrane: NW8), was chosen for this purpose, so eliminating the need for large quantities of expensive type 3 stone. Furthermore, the Deckdrain was quick and easy to install and significantly reduced the volume of material required to be excavated.
In the permanent condition, and with the tanks full of water, there is no risk from uplift pressure beneath the ASP slab. However, when the tanks are emptied during maintenance, this situation changes. For this reason, the drainage layer beneath the ASP was connected to the FST drainage system to provide passive permanent condition, groundwater pressure reduction.

FST and ASP combined drainage system – Courtesy of OGI Groundwater Specialists Ltd
The FST permanent works design was required to counter uplift forces from groundwater under normal rainfall conditions, heavy rainfall and 1 in 100 year flood conditions.
This was achieved by designing a passive pressure relief system that intercepts groundwater beneath all five tanks. This system was integrated to accommodate groundwater drained from the neighbouring ASP tank.
To increase the resistance against uplift pressure an extended toe was added to the base of the FST structure, together with the inclusion of pressure relief valves, to protect against groundwater uplift pressures brought about by a 1 in 100 rainfall flooding events.
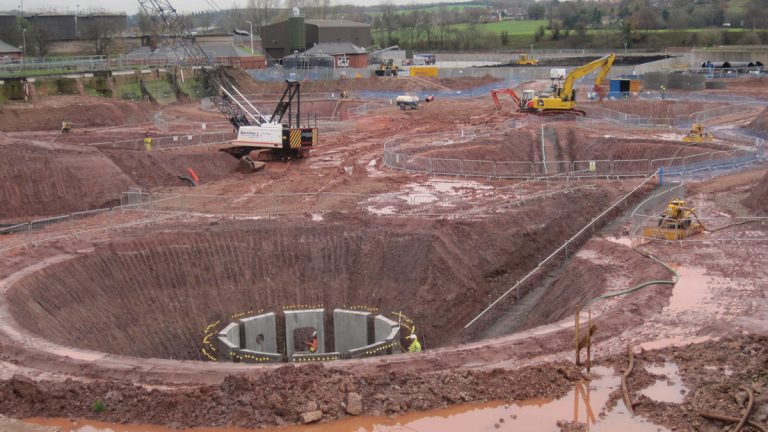
Construction of FSTs underway – Courtesy of OGI Groundwater Specialists Ltd
Benefits to the project
- Considerable cost savings were realised by replacing a secant pile wall around the ASP excavation with 1:1 safe dewatered battered slopes.
- Application of Deckdrain as a structural drainage layer beneath the ASP and FSTs resulted in a major cost saving over the alternative approach requiring deeper excavation and backfilling with a Type 3 stone drainage layer.
- The passive drainage system to lower groundwater uplift pressures removed the requirement for ground anchors.
- The combined drainage system enabled both the ASP and the FSTs to be constructed without risk from uplift pressures during temporary works.
- The installed system provides a permanent, passive solution to resist groundwater uplift of the structures.