Melton Mowbray STW (2024)
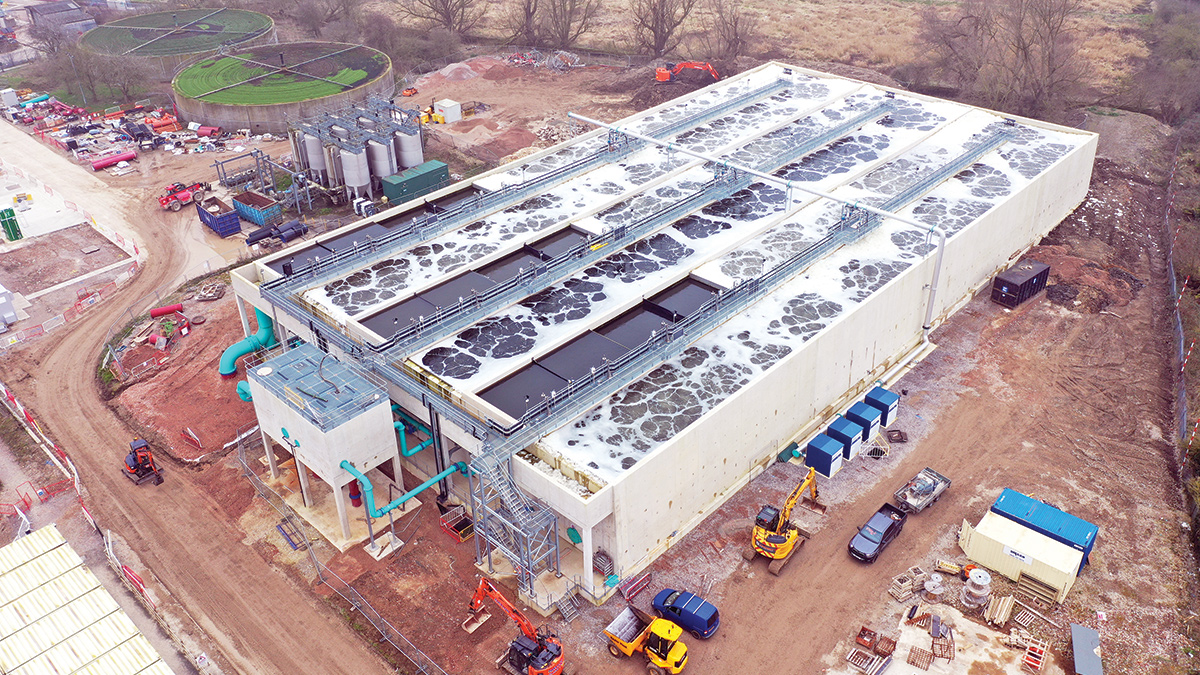
The new EBPR ASP at Melton Mowbray STW - Courtesy of MWH Treatment
Melton Mobray STW is a medium sized activated sludge works, treating a population equivalent of approximately 68,000. The original treatment comprised an inlet works, three primary settlement tanks (PSTs), an activated sludge plant (ASP), four final settlement tanks (FSTs), four biofilters for tertiary ammonia removal, chemical dosing, tertiary solids removal (TSR), four storm tanks and sludge treatment. The works treats a combination of both domestic and trade effluents. As part of the National Environmental Programme (NEP) commitments to meet the obligations of the Water Framework Directive in AMP7, new permit limits will be in place on 22 December 2024.
The new works
The new Melton Mowbray STW is designed to cater for increased treatment flows equating to a design horizon population equivalent of 123,328 (82% growth), a tightening of the Phosphorus permit from 2mg/l to 0.2mg/l and a tightening of ammonia permit of 5/10mg/l to 4mg/l. A significant proportion of the influent is from trade waste.
The new works design comprises:
- A new Enhanced Biological Phosphate Removal (EBPR) Activated Sludge Plant (ASP) with a University of Cape Town (UCT) configuration.
- Two FSTs to work alongside the existing works FSTs.
- Ferric sulphate chemical top up dosing.
- RAS/SAS pumping station.
- ASP feed pumping station.
- COMAG tertiary solids removal plant from Evoqua Water Technologies.
- Gravity belt thickening.
- Conversion of the existing redundant sludge tank back to a fourth PST configuration (complete with new RAM pump adaptive control de-sludge for thickening PST sludges to circa 4%).
- Re-purposing path-kill tanks to sludge storage tanks.
- Increased storm capacity.
- Inlet works refurbishment replacing the two existing 6mm screens with three 6mm screens.
- A network controlled MCC, HV network and telemetry/eSCADA system.
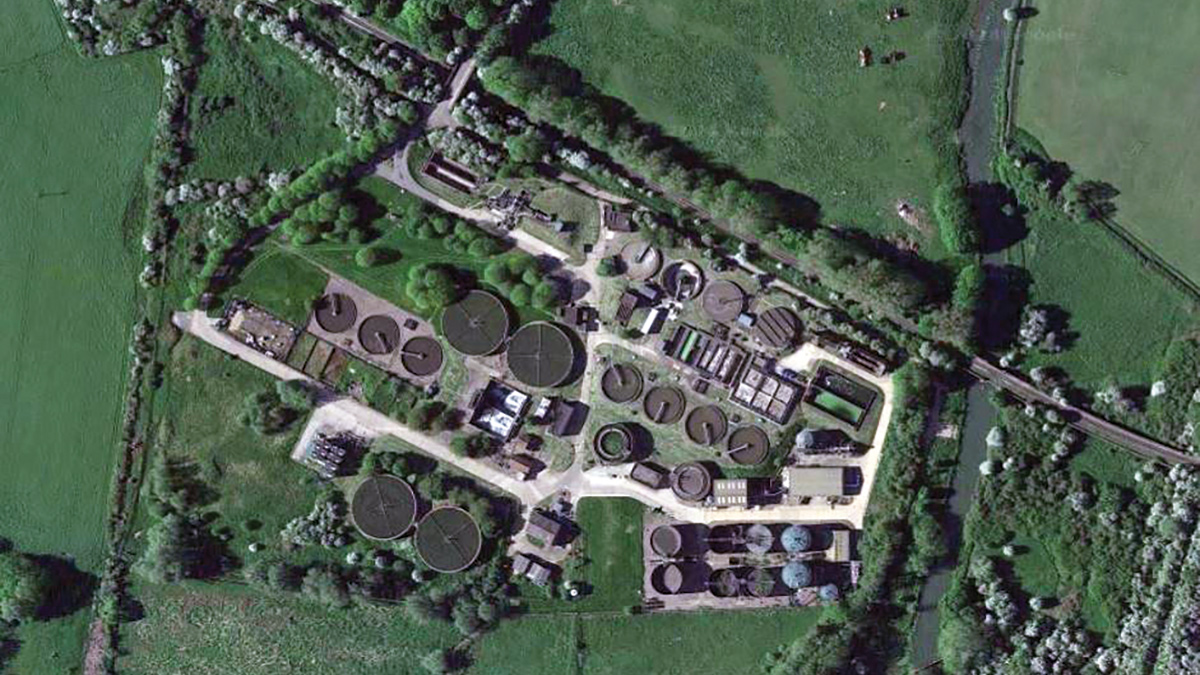
Melton Mowbray STW before the start of works – Google Earth image
Scope of works
MWH Treatment Ltd was appointed as the main designer and contractor by Severn Trent. The scope of works for the project included the investigation, assessment, design, procurement, construction and commissioning of existing and new treatment facilities, thus providing capacity to treat increased volumes of sewage to meet discharge permit standards agreed with the Environment Agency (EA).
Innovative solution selection
A collaborative solution efficiency process was followed to develop the most effective and affordable solution, Severn Trent and MWH Treatment workshopping scenarios and risk that reduced the initial optioneered solution through an Outline Design Early Contractor Involvement order.
A schedule of innovative solutions included:
- The re-use of the existing inlet structure in lieu of a new structure.
- The re-use of the previously abandoned ASP lanes to form a new ASP feed pumping station in lieu of a new structure.
- Re-purposing path kill tanks for sludge storage.
- Procurement of second-hand temporary site offices rather than long term hiring.
- 7m deep ASP (not the standard 6m deep) with tapered walls. Saving on plan footprint, concrete, and reinforcement.
- Re-purposing of existing humus tanks as additional storm capacity.
- Deletion of odour control system.
Project initiation and whole supply chain early engagement
To create a vision of how best to design and build the new plant, the positive step to involve all key stakeholders at the earliest point in delivery was taken. Engaging with the supply chain early in the process gave an opportunity to challenge, augment and create an innovative design and delivery strategy incorporating the supply chain’s input to optimise construction safety of the build e.g. during workshops and collaborative planning sessions, every new asset was evaluated for off-site build potential, access and maintenance challenges with the plant design and construction in the already tight working environment.
The MWH Treatment team undertook a collaborative approach aligning the Client Operations team, the in-house design skill set with the construction team specialism to ensure the plant was both functional and constructible, overcoming access, maintenance and operability challenges and elected to take as much construction off-site and to modularise, wherever possible, thus overcoming conventional construction mind-sets.
Reference to previous schemes was also taken and the use of repeat proven design solutions adapted as widely as possible to mitigate re-engineering.
Sustainable and efficient design and construction
Ground conditions at the ASP location presented an early challenge for the construction of the new ASP being both very poor and highly contaminated.
Excavation and removal of this material, together with the importation of suitable virgin stone to create a piling mat, was expected to incur a significant carbon footprint and many vehicle movements along the shared access drive with local residents.

(top left) Groundworks underway, (right) SMR UK ASP area soil stabilisation, and (bottom left) stabilised ASP area with piling and ASP base construction ongoing – Courtesy of MWH Treatment
The team developed a comprehensive Material Management Plan including innovative solutions such as SMR UK’s cementitious binder to stabilise the piling and crane mat in lieu of excavation of contaminated materials and imported Type 1 stone mats, which resulted in project carbon reductions, together with costs savings in excess of £2m. The reduction in materials being exported to landfill together with imports of suitable replacement materials saved over 1300 vehicle movements combining for a carbon reduction of 1272.64 tCO2e.
To facilitate the stabilisation of the ASP formation, crane mat and piling mat, known buried structures that would have prevented piling were removed and crushed on site to form material suitable for reuse as hardstanding.
Additional carbon reduction activities included altering the design of the ASP straight wall to a tapered wall, reduced the quantity of materials used. Reduction in concrete of 368m3 (or 61 wagons) and reduction in 52 tonnes of reinforcement and adopting a process design to include an ASP structure with 13% reduction in area also reduced the materials used.
The design details developed at Melton Mowbray STW were also shared and utilised on the Hartshill STW project which shared similarities in design. This provided efficiencies in the detailed design of the Hartshill project which is running approximately 6 months behind the Melton Mowbray STW programme.
The collaborative approach between MWH Treatment, their subcontractors and the Severn Trent design teams enabled a focussed, efficient and standardised design sign off process.
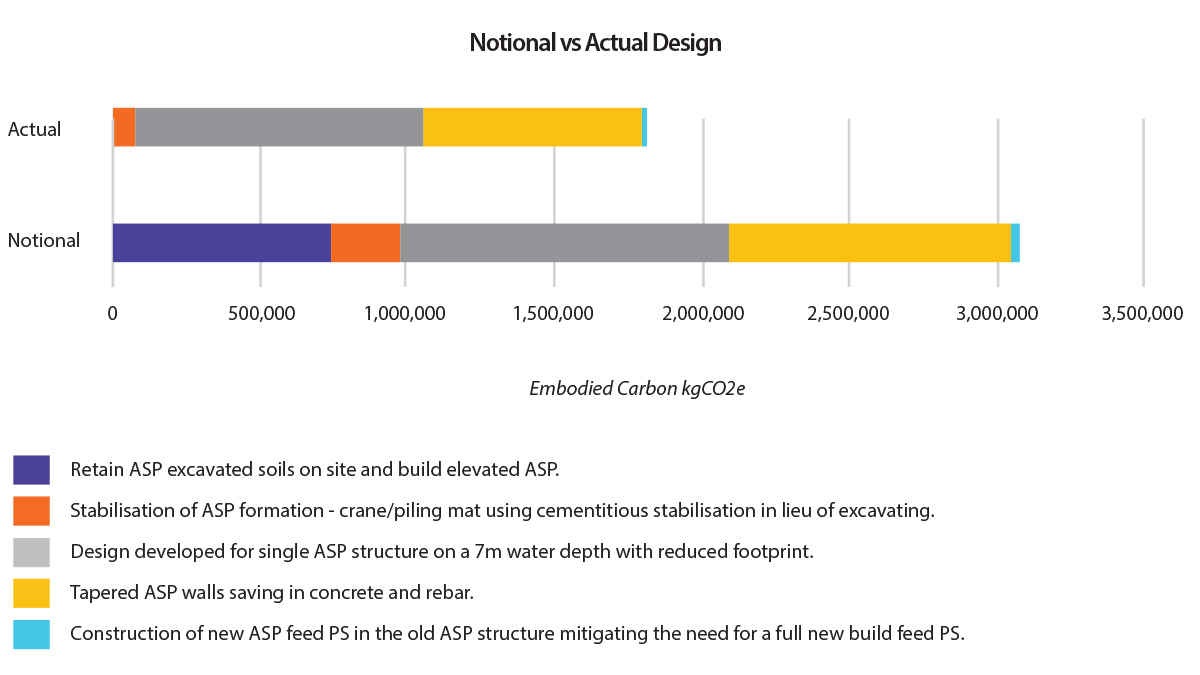
The net carbon reduction profile of these activities
Melton Mowbray STW: Supply chain – key participants
- Client: Severn Trent
- Main designer & contractor: MWH Treatment Ltd
- Environmental consultants: Middlemarch Environmental
- Hydraulic modelling: Hydrotec Consultants Ltd
- Ground stabilisation: SMR UK
- Piling: Balfour Beatty Ground Engineering
- General civil works: Naylor Construction
- FRC works: JS Structures Ltd
- Cross-site pipework: Hollywood Civil Engineering
- Mechanical installation: MWH Direct
- Electrical installation: S&R
- COMAG tertiary solids removal plant: Evoqua Water Technologies
- FST precast tanks: A-Consult Ltd
- FST & PST bridges: EPS Water
- Coated pipework: George Green (Keighley) Ltd
- Chemical dosing rig: Colloide
- Polymer plant: NPS Engineering Group
- MCC & ICA controls: Blackburn Starling Ltd
- Aeration equipment: Suprafilt Ltd
- Pumps & mixers: Sulzer Pumps Wastewater Ltd
- Inlet screens & WAPs: Huber Technology
- Thickener plant: Kent Stainless Ltd
- Clarifiers: Stortec Engineering Ltd
- RAM pumps: EMS Industries Ltd
- Access metalwork: Galliford Try Fabrications
- Access metalwork: Tushingham Steel Fabricators Ltd
Digital delivery
The project team optimised digital delivery, developing innovative digital engineering tools to increase efficiency at initiation, design development, assembly, commissioning and ultimately client operational stages in the project lifecycle.
MWH Treatment undertook a full digital survey of the site. This was used as the basis of the 3D model but additionally this digital information and imagery was also actively used in the induction process to develop visual awareness of both the works layout and the impact on access.
Hydraulic modelling of refurbished inlet works
The existing two-screen installation with centre by-pass channel was designed to be replaced by three new screens and two new wash compactors. This was further complicated as the refurbishment had to fit the existing inlet works structure.
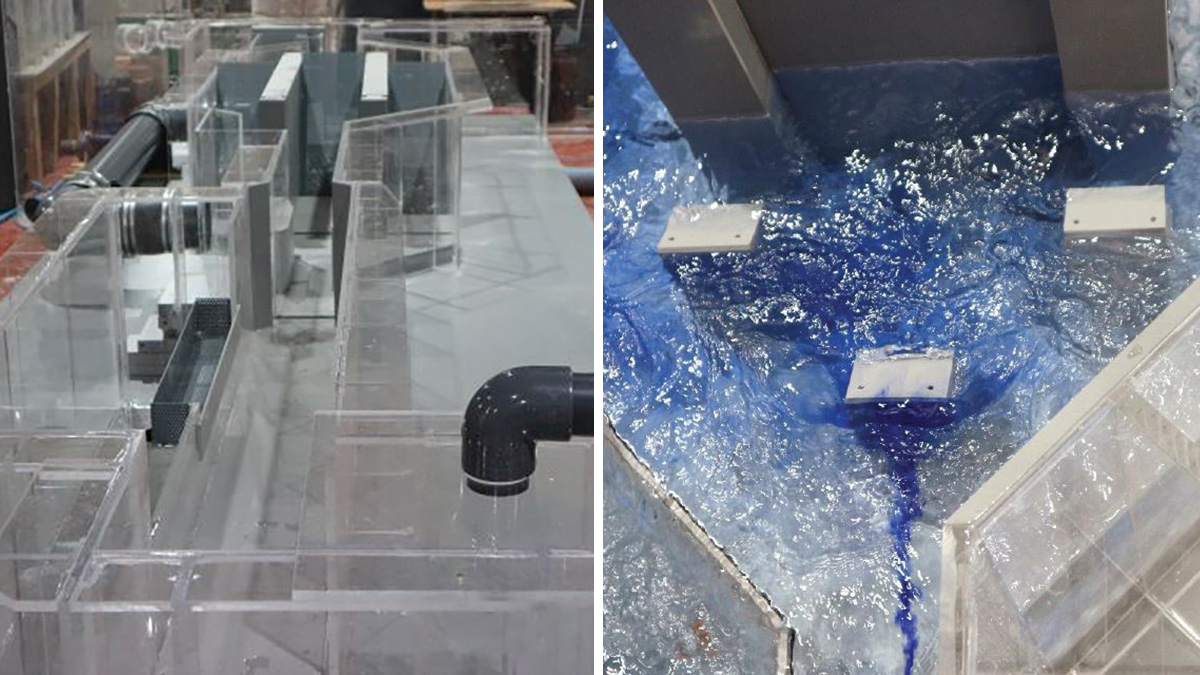
(left) Inlet works physical model at Hydrotec and (right) inlet works screen baffles and dye test – Courtesy of MWH Treatment
This was achieved by the provision of a new bypass pipe outside the inlet works structure and the use of the existing centre bypass channel to house the third screen.
Hydraulic modelling of the inlet works ensured proper flow presentation to the new screen layout through the construction of a scaled model at Hydrotec Consultants, which identified enhancements that ensured flow calming and screen flow presentation.
Electronic induction
The project has used an electronic GDPR compliant induction system for all workers and visitors. This system of completion online prior to arrival allows the site induction to focus purely on the key site-specific dynamic issues enabling people to start work more promptly. Over 1200 people have used this system, typically saving over 1700 hours of site time. The digital induction includes a video of the access routes and access restrictions enabling drivers and delivery persons to clearly understand the access routes and restrictions before setting off for site.
The induction was translated into a number of languages representing the diverse workforce deployed to deliver Melton Mowbray STW ensuring easy understanding of the requirements by the workforce on site.
Ensuring service compliance during works
The complex scheme involves intrusive works across most of the existing work’s operations which required meticulous planning to ensure Severn Trent process operation stability and security risks were minimised as far as practical.
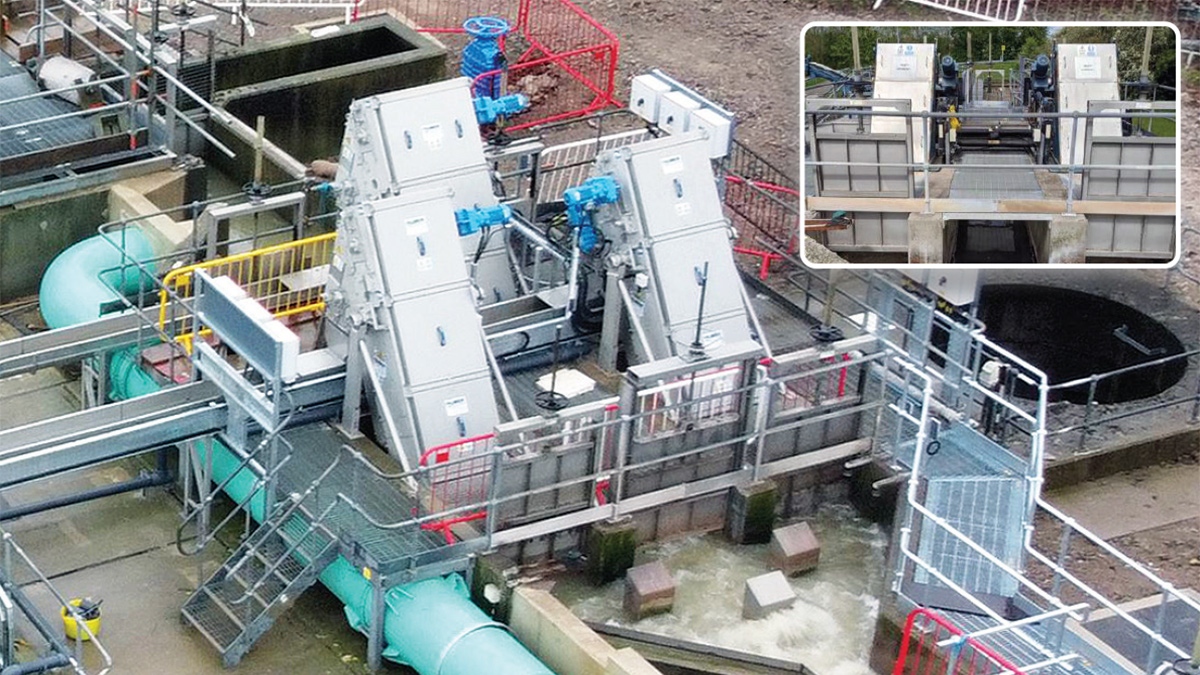
Refurbished inlet works with three screens & bypass pipework and (inset) the inlet works prior to the upgrade with two screens – Courtesy of MWH Treatment
Refurbished inlet works with three screens & bypass pipework and (inset) the inlet works prior to the upgrade with two screens – Courtesy of MWH Treatment
These interfaces included:
- Changing HV transformers and switchgear for the whole site
- Removal of two screens, the provision of a new bypass pipe and the installation of three new screens from Huber Technology on a phased changeover at the inlet.
- Over pumping of the full inlet works to install flow baffling to enhance flow presentation to the new screen layout in accordance with the modelled hydraulics.
- Removal of three existing gravity belt thickeners and replacement with two new larger units from Kent Stainless Ltd.
All the above key interfaces were conducted seamlessly with no loss of production.
Programme
The site construction period was optimised using digital design, DfMA and effective site planning including collaborative programme workshops, and bi-weekly planning updates to drive the Melton Mowbray project to a completion date in May 2024, allowing Severn Trent six months of optimisation before the new consent comes into force.
The collaborative effort between MWH Treatment and Severn Trent is driving project success for all parties.
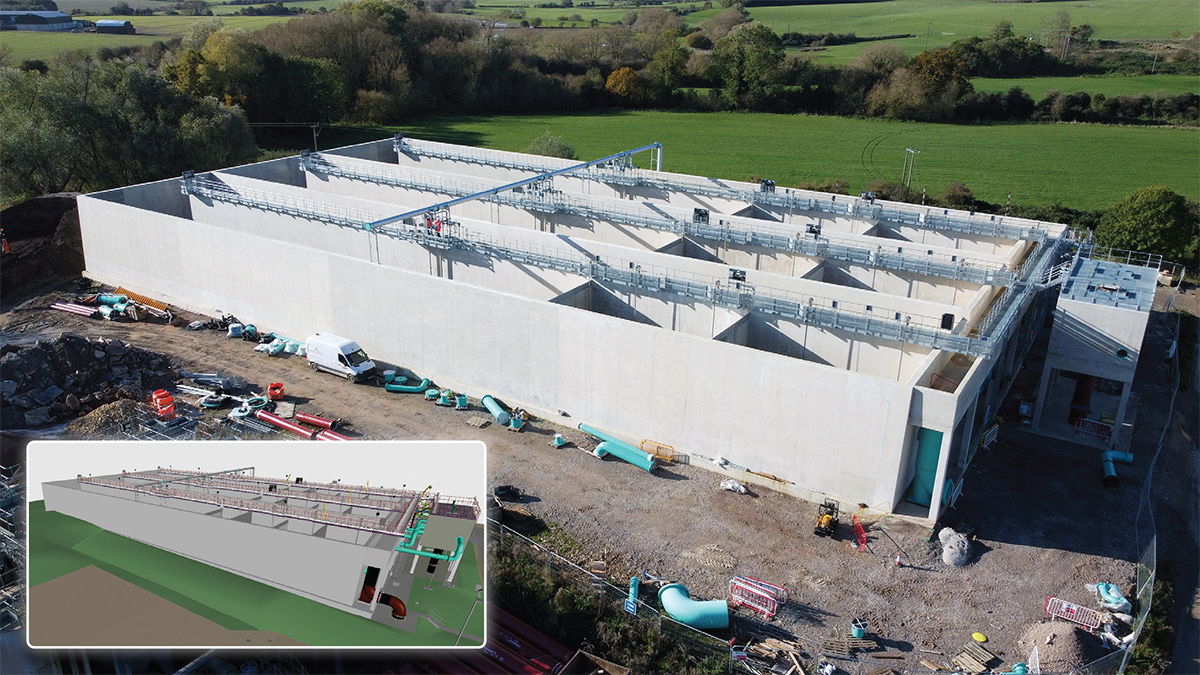
Activated sludge plant under construction and the BIM model (inset) - Courtesy of MWH Treatment