High Frequency Risk Reduction: Moor Road (2022)
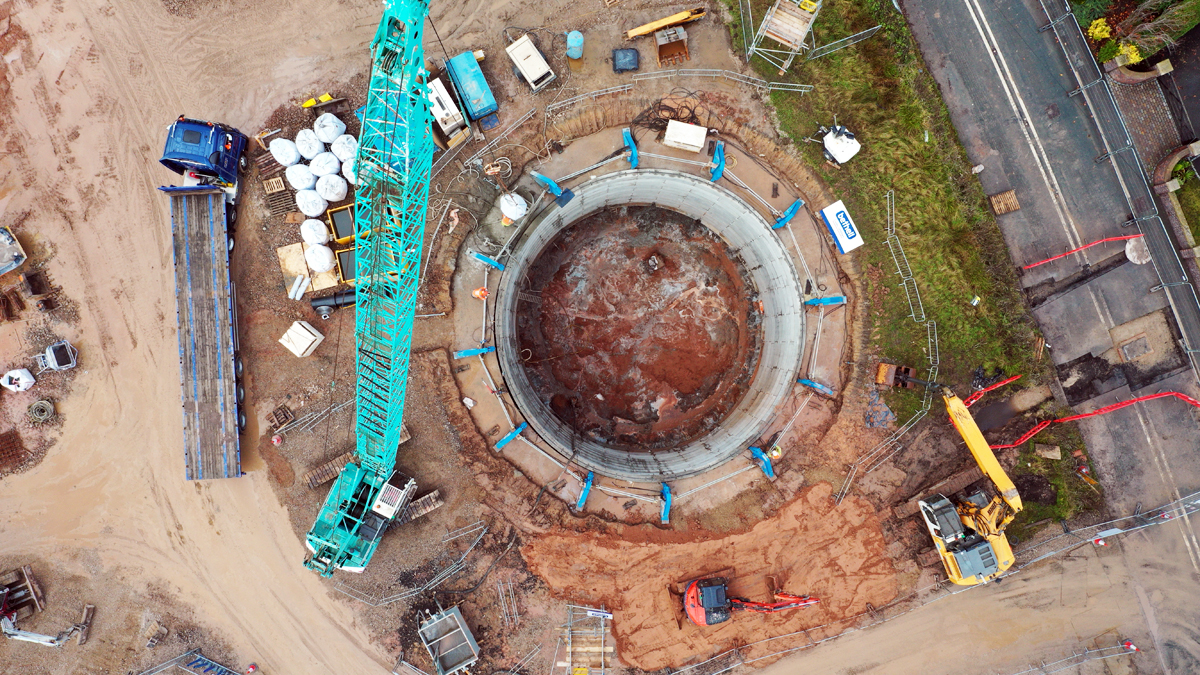
Aerial of detention tank construction - Courtesy of United Utilities
In the PR19 agreement, water companies were encouraged to provide resolution to long-standing flooding problems being experienced by customers – but allowed a less prescriptive approach on the actual projects defined in the Water Company’s Price Review submission. This new process allowed the water companies a degree of discretion on the number and frequency of flooding areas to be addressed in the AMP7 period and provided an incentive in resolving flooded areas based on when in the AMP they were delivered. This article provides a technical and engineering focussed precis of one of United Utilities’ early start ‘High Frequency Risk Reduction’ (HFFR) projects located at Moor Road, Croston, Lancashire, and the factors that were considered in delivering this fast-tracked project.
Background
The overall programme of flood alleviation projects to be delivered by United Utilities during AMP7 is entitled ‘High Frequency Risk Reduction’ (HFFR). The purpose of the programme is to resolve long standing (decades in many cases) issues experienced by residents that previously had been overlooked or not deemed sufficiently high enough priority to be included in previous flooding investment programmes.
The HFRR selection process was based on several factors including frequency of flooding experienced, number of properties affected and whether the flooding was internal or external in nature. It is worthy of note that previous flood impact assessments had often resulted in reduced priority being given to the resolution of external flooding events, whereas the HFFR assessment output generally concluded these events to be almost as traumatic as internal flooding especially when the frequency was high.
Moor Road flooding
Moor Road is located approximately 12 miles south-west of Preston in the small village of Croston, Lancashire. The village has a population of around 3,000 and has developed on the River Yarrow that is also subject to cause flooding in the vicinity during heavy rainfall events. Much of the area is surrounded by farmland. The village is heavily trafficked which causes substantial congestion through the relatively narrow roads and is the subject of much local concern and opposition.
NB: this project was not intended to address any resolution of the river flooding.
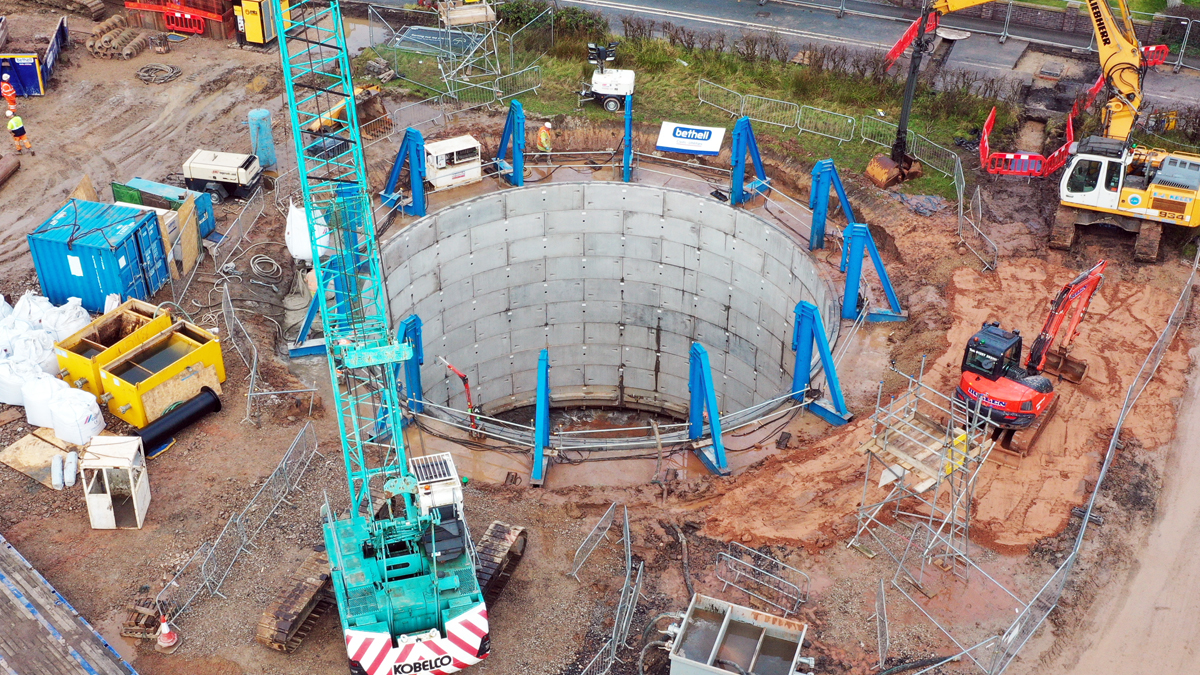
Moor Road detention tank – Courtesy of United Utilities
Project need
Historical flooding has routinely been recorded along Moor Road primarily considered to be due to the topography of the surrounding rural area. Unfortunately, this resulted most notably in three residential properties experiencing both internal and external flooding over many prior years.
The HFFR assessment identified the project need and the urgency of flood alleviation measures required based primarily on the frequency of reported events.
Solution development
Extensive hydraulic modelling was undertaken initially by United Utilities Ltd and its design partners and then by its AMP7 Network Service Provider, Bethell Construction Limited, to understand the root cause of the flooding and subsequently identify and develop potential solutions to resolve the issues. Four basic options were considered at the preliminary optioneering phase, namely:
- Off-line storage with associated spill weir from the existing network and connecting and return pipework/pumping station.
- Isolation assessment to consider whether a ‘cut-and-pump’ on the individual properties could isolate them from the flood surcharge levels.
- Wholescale sewer upsizing to allow greater flows through the network to Croston WwTW, some 1.3km away from the area of the flooding.
- Surface water separation of the largely combined existing network.
The assessment of the isolation option showed that while the three properties that suffer flooding would be protected, the resulting increase in hydraulic head elsewhere showed that flooding would be transferred to other areas. Hence this option was not progressed.
Upsizing the main sewer would have involved replacing sewers that were in very restricted areas through the village, e.g., between old houses and along the very narrow main highway. Additionally, the WwTW would have needed extensive expansion to cater for the increased flows. Whilst the option was not priced up in any detail, it was dismissed on grounds of constructability and costs.
As far as the surface water separation option was concerned, the modelling showed that even if 100% of modelled impermeable area was removed from the network for the 30-year design event, the flooding volumes would be substantially reduced, but would not remove all occurrences. This together with the fact that surface water/river flooding is a significant issue also within Croston and adding more flow to the rivers and streams would only exacerbate the problem, it was concluded that this option was not feasible.
The hydraulic modelling indicated that wide-scale upsizing of the sewerage network would be difficult to implement and would also have an adverse impact on Croston WwTW. The significant disruption to construct the larger sized sewers and enhancements/expansion to the WwTW resulted in this option also being dismissed.
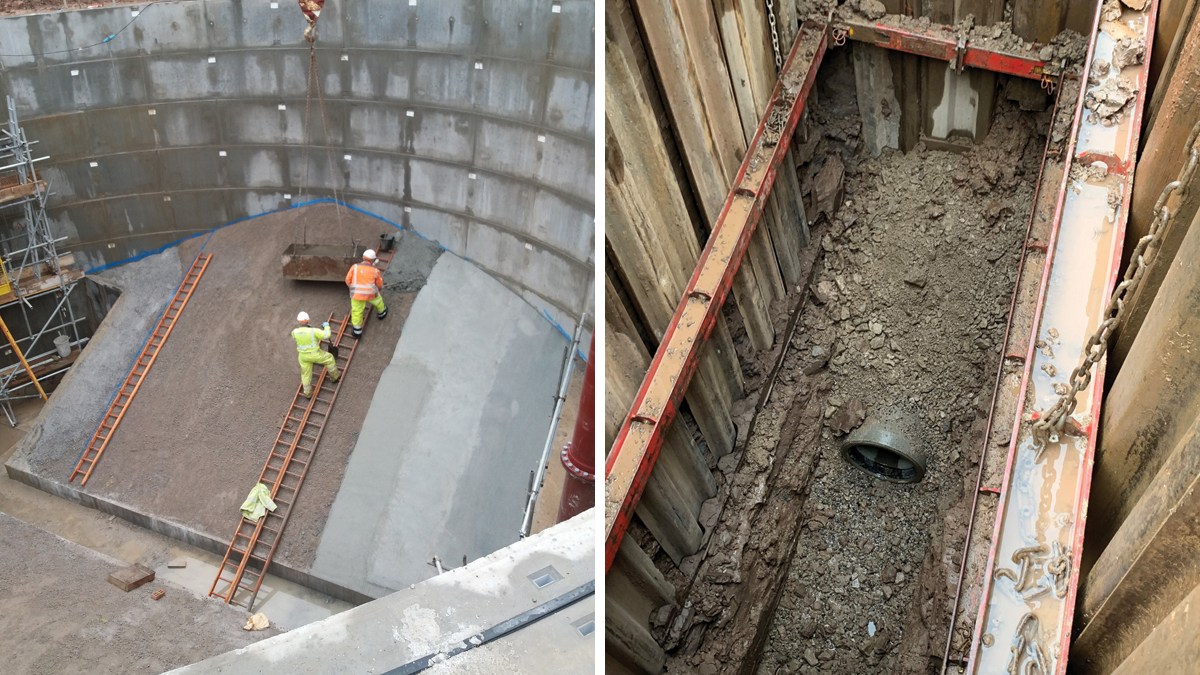
(left) Moor Rd benching installation and (right) Moor Road sewer construction in highway – Courtesy of United Utilities
Recommended option
The most appropriate solution was to provide storage within the catchment to capture the excess flows during storm events and then release this back into the network once capacity was available after the storm had subsided.
The modelling indicated that a storage volume of approximately 800m3 would be required to cater satisfactorily with a storm of return period of 1-in-30 year event (the design horizon requirement for flood alleviation projects). Due to the relatively shallow sewerage network and level topography in the region it was not possible for a gravity-only solution to be developed, hence the final solution was a deep tank with pumped return to the sewer.
Various locations were considered for the tank but there was only really one suitable location; a site approximately 400m east of where the flooded properties were located. The second preferred location would have involved the crossing of a railway line and a primary road traffic route through the village, which was considered to have too much risk attached to it.
To transfer the excess flows to the tank, the existing sewers could not be utilised, hence it was necessary to install a new purpose-built carrier sewer between the flooding location and the tank. This sewer was to be sized at 450mm diameter.
Moor Road HFRR Project: Moor Road: Supply chain – key participants
- Main contractor: Bethell Construction Limited
- Civils designer: Royal Haskoning
- Mechanical & electrical design: FWB Engineering Services Ltd
- Shaft storage & pumping station construction: E J Kelly Construction Ltd
- Geotechnical investigation: Geotechnics Ltd
- Sewer construction: Trenchless Solutions Ltd
- Mechanical & electrical installation: Eric Wright Water Ltd
- Pumps: Xylem Water Solutions
- Sewer pipes: FP McCann
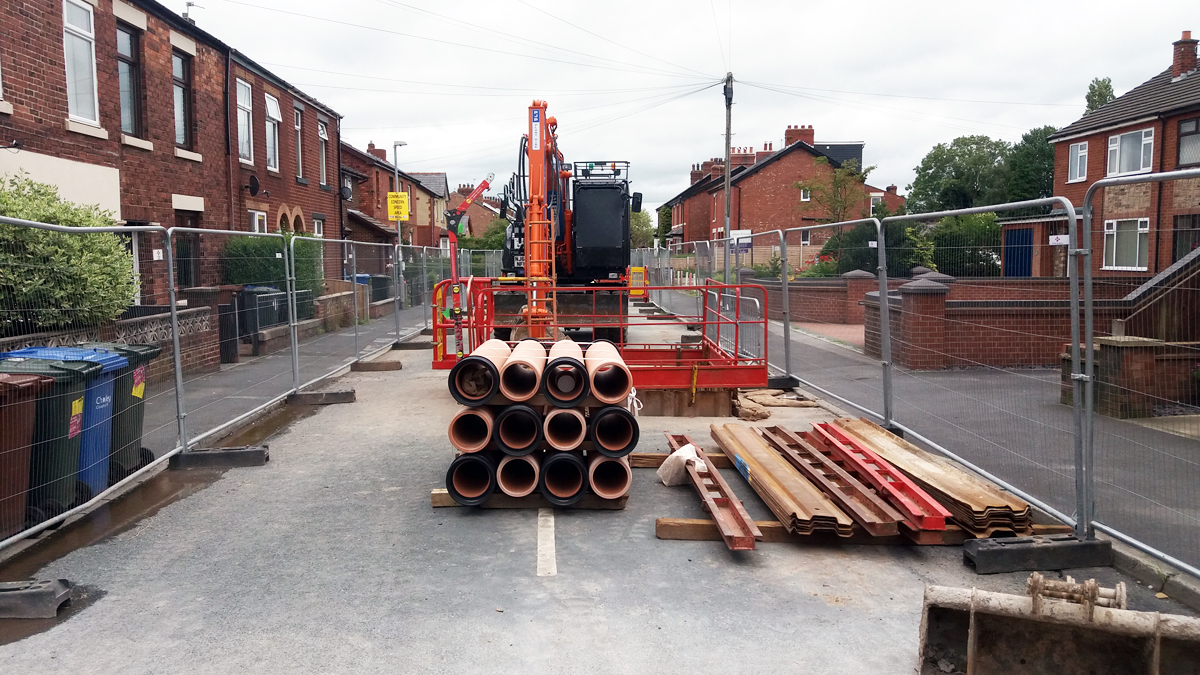
Site working area in Moor Road for sewer installation – Courtesy of United Utilities
Sewer construction
Various methods of installing the sewer along Moor Road were considered but were split between traditional open-cut and some form of no-dig technology. However, as Moor Road is an important traffic corridor through the village both for vehicles and underground utilities it was important that assessment of the duration that the road could be taken out of service had to be made.
Due to the extensive number of utilities along the road, including water and the existing sewer, the decision was ultimately taken that the most appropriate no-dig approach would be a guided auger bore (GAB) that could be installed beneath all existing services.
Launch and reception shafts were required at maximum intervals of around 50m, which resulted in nine pits being required; it should be noted that all pits were subsequently built up as permanent manhole chambers, apart from one that was required in the junction of Moor Road and The Orchard which was used as a ‘blind’ manhole and ultimately backfilled over the sewer once the GAB had completed the drives on either side.
Work on the sewer section commenced in June 2020 and although the GAB no-dig technique was used to reduce the inconvenience to residents, a significant road closure was needed along Moor Road that would also restrict access to the properties for vehicles.
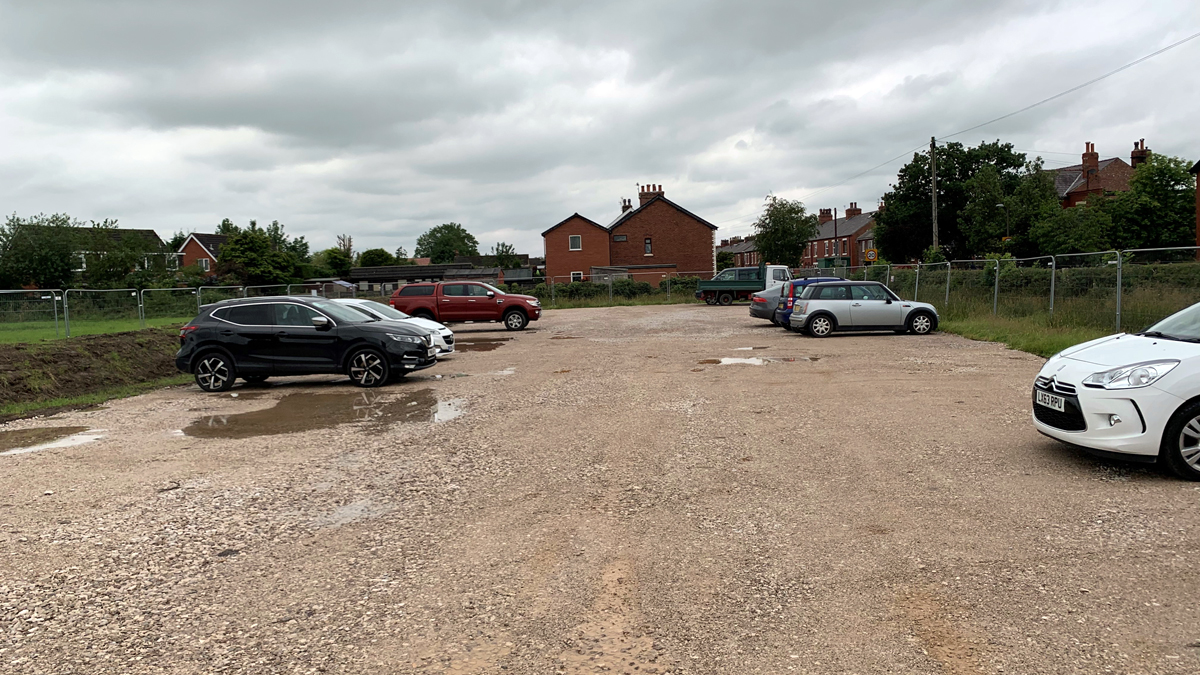
Temporary car park for residents during closure of Moor Road – Courtesy of United Utilities
This was a major stakeholder issue as no existing alternative parking was available nearby. A temporary car park was therefore established at the location of the site compound and proposed storage tank, and it was envisaged that the sewer work would be completed before the detention tank construction would commence, meaning it could be removed once the road was re-opened. The temporary car park was built to accommodate around 120 vehicles.
In total there were eight GAB lengths installed; with construction durations ranging between 5 to 10 days, for the 25m to 50m drives that were necessary. In addition to the GAB drives, other work to create launch & reception pits and then construct the permanent manholes was undertaken as part of this construction sequencing.
Overall, the sewer installation went extremely well with little incidents and/or noticeable settlement above the sewer line. However, the final sewer work was not completed until early December 2020, some 8-9 weeks later than initially planned, and resulted in having to relocate the temporary car park to another part of the site compound to commence the detention tank in September 2020.
The GAB work was subcontracted to Trenchless Solutions Ltd.
Detention tank construction
The 800m3 detention tank was designed as a circular segmental shaft, 15m in diameter and approximately 10m deep.
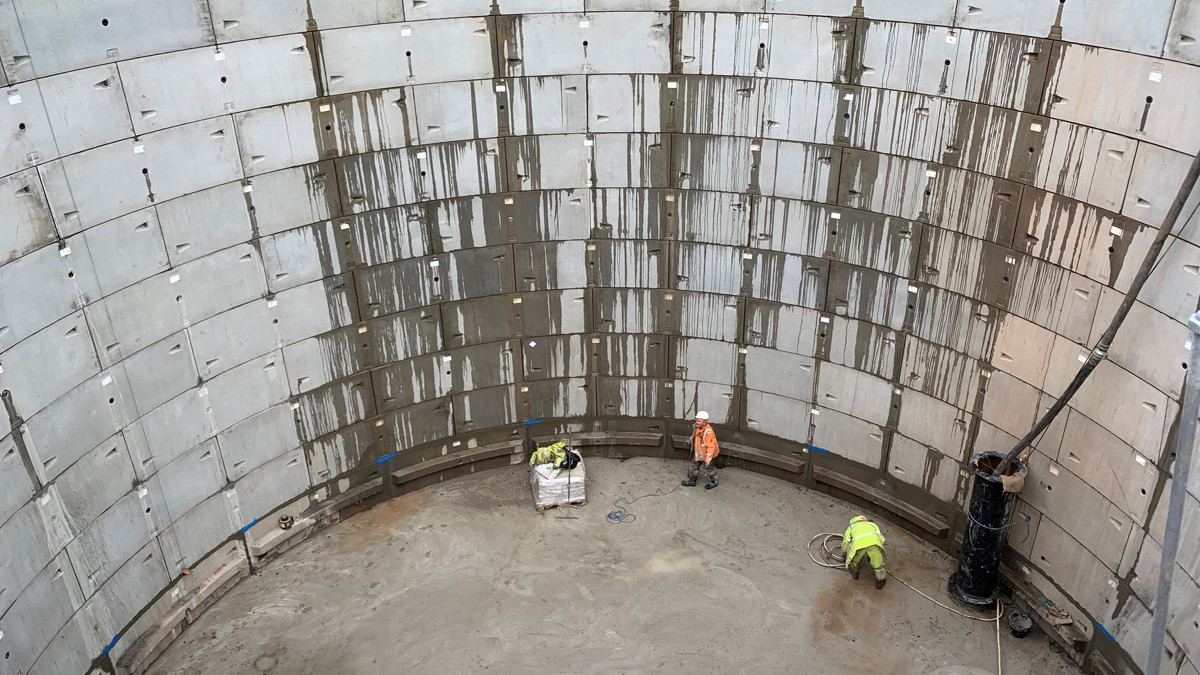
Excavation of detention tank – Courtesy of United Utilities
The construction was relatively straightforward and commenced in September 2020, after the necessary Planning Application was granted to remove the hedgerow on the access perimeter of the site. However preliminary work started prior to the granting of the Planning and had to use the existing farm access until a wider temporary site access could be constructed, this involved careful traffic movements and the lifting of plant and equipment over the hedgerow to get it all on site.
The shaft construction was subcontracted to EJ Kelly Construction.
Stored storm sewage will be returned to the existing sewer once the storm abated, and adequate capacity was again available. This was monitored via ultrasonic levels downstream of the pumping station. The returned flow rate would be approximately 17 l/s, which would commence when the level in the pertinent part of the network dropped to 8.905m AOD with a 4-hour delay in pumping to reduce the risk of recirculation back into the tank.
The mechanical & electrical equipment was designed by FBW Engineering Services Ltd and installed by Eric Wright Water Ltd.
Outcome
The works were completed and put into operation in June 2021. Since that time, although there have been several significant storms there has been no further reported flooding of properties in the area.
One item that is outstanding is the drainage of the permanent site compound that does not drain away effectively enough and results in standing water flooding the compound after heavy rainfall; this standing water often requires several days or weeks to finally drain away into the ground.
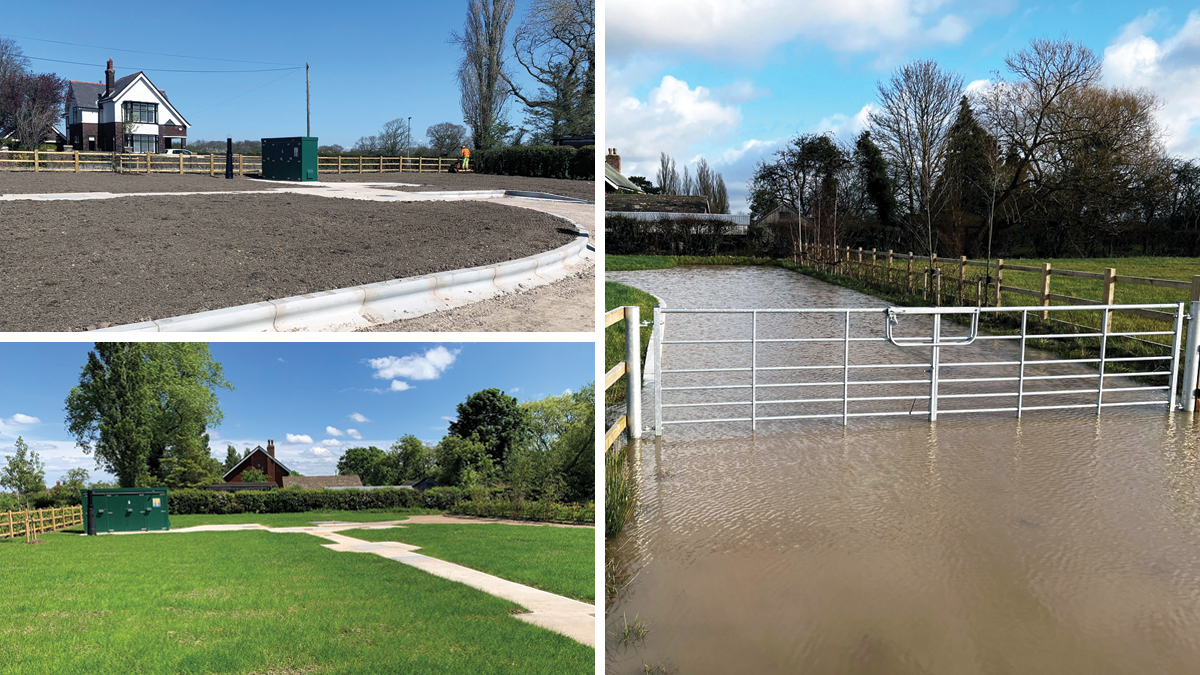
(top left) Detention tank site reinstated pre-seeding, (bottom left) completed works and compound and (right) flooded compound following heavy rain – Courtesy of United Utilities
Several options to drain the site have been considered, the main options were:
- Provide soakaway: the ground is heavy clay and remains waterlogged for many months unless very dry periods exist, hence it was not considered a feasible option.
- Drain the surface water to the detention tank: this would not be non-compliant with United Utilities policy of not accepting surface water into the existing network. Additionally, the tank was not sized to accept extra flows and therefore this could compromise the solution and potentially cause flooding in the areas that needed to be addressed.
- Install positive drain to the adjacent ditch: unfortunately, the nearest ditch did not have an outfall and therefore standing water would have remained in the compound and the ditch.
- Install a positive drain to a nearby watercourse: this was the recommended solution and would require approximately 150m of drain across the adjacent field and connection into the watercourse. Due to potential development of the field, significant negotiation with the landowner had to be undertaken before permission was given to lay the pipe, including a commitment from United Utilities to ‘lift and shift’ the drain if it did not align with the development proposals. These agreements have been finalised but at the time of writing (June 2022) plans were being made to install this drain across the field to resolve.