Murton WTW (2020)
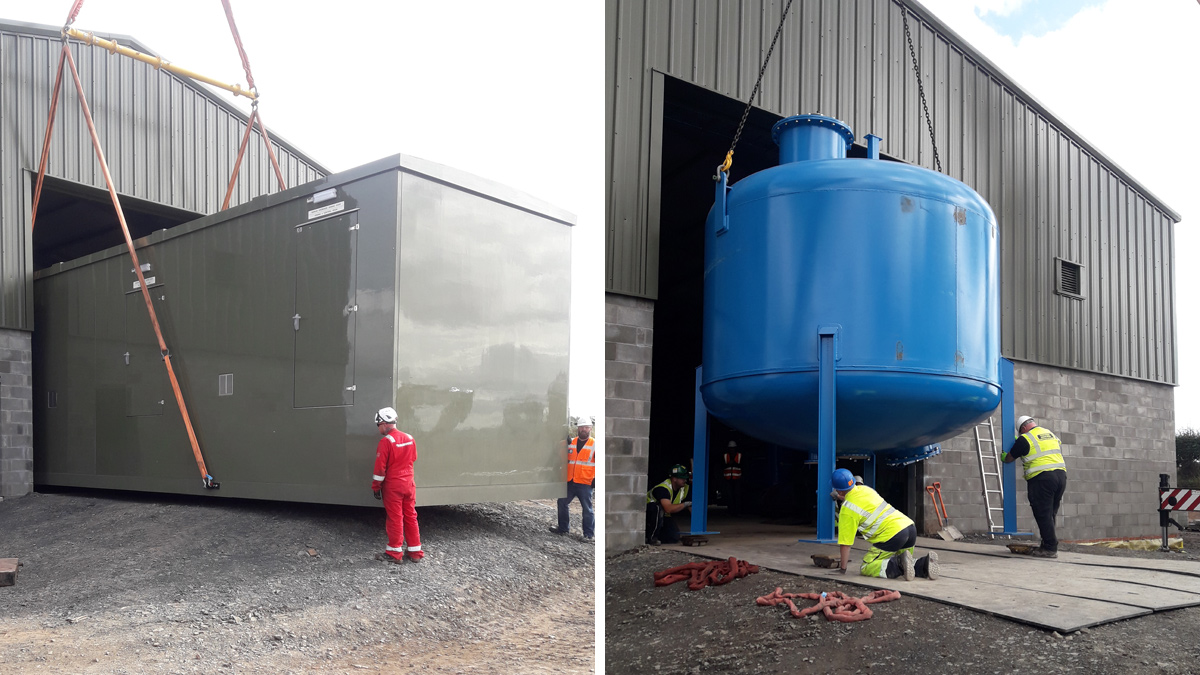
(left) Delivery of a pre-assembled chemical dosing facility and (right) delivery and installation of pressure filters - Courtesy of MMB
Murton WTW is fed by six boreholes and supplies up to 350m3/hour of potable water to Berwick-upon-Tweed and surrounding areas, serving over 7,500 properties. The boreholes which feed the Berwick Water Supply Zone can contain turbidity, particularly when flows are high, interrupted or varied. The existing treatment process was unable to remove the turbidity, causing flows to run to waste. Frequent power outages and varied seasonal populations led to regular manual operator intervention and a growing reliance on tankering from other sites to ensure the supply zone remained primed. In 2016 Northumbrian Water (NWG) awarded Mott MacDonald Bentley (MMB) an Investigate and Define (I&D) contract to review potential solutions to improve treatment at Murton WTW. Following this, in April 2018, NWG issued MMB with a design and construct contract to deliver the design, construction, testing and commissioning of the new treatment facilities.
Background/drivers
The existing treatment facility at Murton was approaching the end of its asset life and did not have the treatment stages available to remove elevated levels of turbidity. As a result, NWG were becoming more reliant on tankering operations to supplement supply during periods of peak demand and/or operational problems. Furthermore, a number of properties are served directly from the outlet main of Murton WTW, meaning that their water supply was disrupted during planned and unplanned shutdowns.
This new-build WTW facility, on a greenfield site at Murton near Berwick-upon-Tweed, will improve the resilience of the Berwick Water Supply Zone, and has enabled Northumbrian Water (NWG) to achieve ‘food factory’ treatment standards in one of its farthest outposts. The design followed ‘Design for Manufacture and Assembly’ principles and utilised off-site build where possible to minimise personnel numbers on a tight site and to reduce wastage. A strong safety culture within the workforce ensured that there were no lost-time injuries during the construction phase spanning more than 18 months.
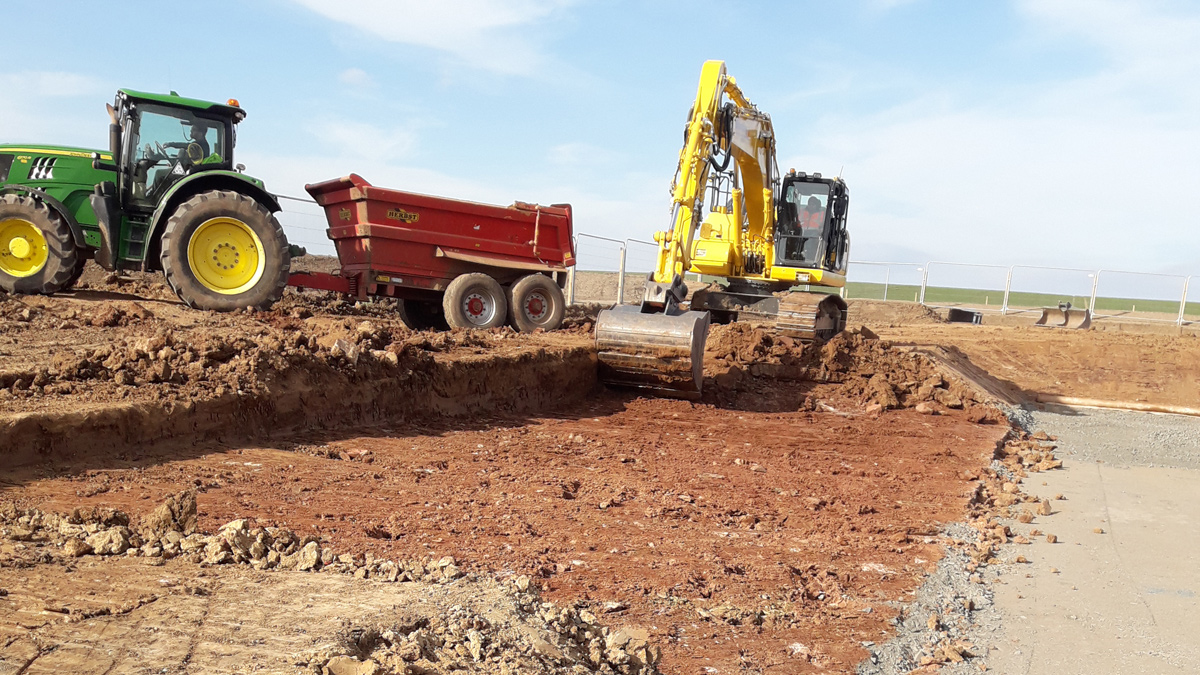
Bulk earthworks were carried out by excavators with GPS control – Courtesy of MMB
Design development
NWG had identified that a new treatment works would be required to replace the current treatment processes, which required treatment at multiple locations due to the varied nature of the individual boreholes. The new Murton WTW was to enable the collective treatment of the incoming supply, including filtration which would allow for continued supply when the boreholes experienced elevated turbidity. The new facility was to meet Northumbrian Water’s goal of achieving ‘Food Factory’ treatment works standards in terms of performance and condition.
At the completion of the I&D stage, NWG and MMB agreed that the new works must include:
- Filtration by 4 (No.) duty sand pressure filters:
- The filters consist of an anthracite cap, sand and manganese dioxide (MnO2) media. The anthracite and sand are designed to capture larger solids particles during periods of poorer water quality. The MnO2 acts as a catalytic media and further promotes the deposition of manganese and iron onto the filter media. The advantage of removing iron and manganese over a single stage means that a second removal stage is not required, saving on TOTEX, carbon and site footprint.
- Vertical pressure filters were chosen due to the level of robustness provided, high reliability and low operational costs when compared with other technologies.
- New chemical dosing facilities:
- Pre-dosing of raw water with sodium hydroxide and sodium hypochlorite. Raising the pH and adding a chemical oxidant improves the precipitation reactions of iron and manganese onto the downstream filter media.
- Orthophosphoric acid and sodium hypochlorite for plumbosolvency issues and primary disinfection respectively.
- Sodium hydroxide for final pH correction before water is passed to the network.
- Concrete contact tank consisting of 2 baffled cells to provide chlorine contact time prior to distribution.
- Dirty backwash water settlement tanks.
- Run to waste facilities, including dechlorination of treated water.
- New building to house plant.
- Final water pumping station.
- To ensure uninterrupted supply to the properties on the rising main, the design includes clean water storage and a small set of jockey pumps to maintain sufficient pressure in the rising main if the main works is offline.
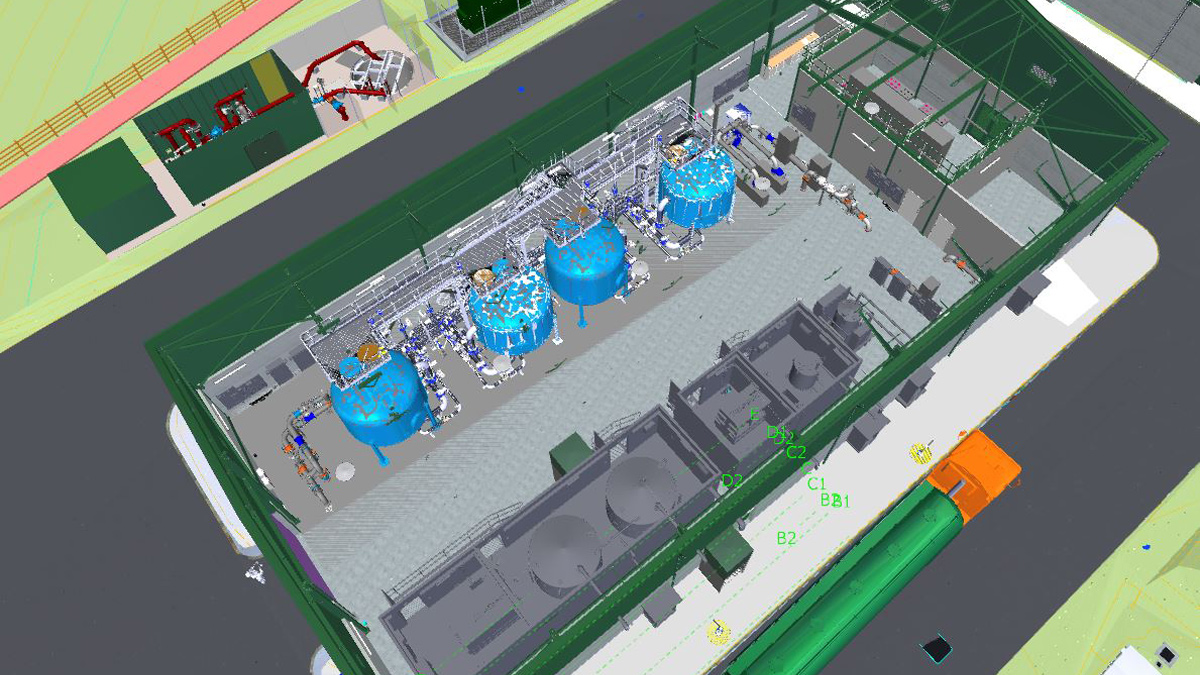
Image from the site model, showing the process units within the treatment building – Courtesy of MMB
Digital delivery
As part of the proposed digital delivery, the greenfield site adjacent to the existing works was GPR and laser scanned to produce an accurate 3D model of the current land and subterranean utility infrastructure. This model was developed further in conjunction with key suppliers and multidisciplinary designers to progress to a full site-wide model of the civil, electrical, mechanical and process elements. The pressure filter, chemical dosing and metalwork suppliers provided models of their discrete works packages which were incorporated into the overall site model, produced in Revit. This enabled the MMB design team to accurately model surrounding structures, interconnecting pipework and services in both Revit and Civil 3D.
All this data was pulled together and made available to the client and site team through Navisworks. Utilising the Navisworks model allowed all stakeholders to visualise the final product in a way not possible with traditional 2D drawings. During the design stage, the model allowed for greater clash detection prior to construction allowing designs to be tweaked at low cost in the office, reducing standing time on site. The model was made available to the client during the development phasing to assist with design acceptances and operational reviews of the proposed site processes.
A pair of chlorine contact tanks and balance tanks were required to ensure effective disinfection and adequate clean water storage respectively. The footprint of this structure was optimised geometrically and its disinfection capability was hydraulically verified for a full range of flow rates using a computational fluid dynamics (CFD) model. The associated pumping station was integrated into the contact and balance tank structure, using the balance tank water for network supply. A significant driving head into the pumping station was also guaranteed by utilising the varying existing site topography and by combining the two elements into a single structure, the site team were able to construct both as part of a single package, minimising temporary works and material use.
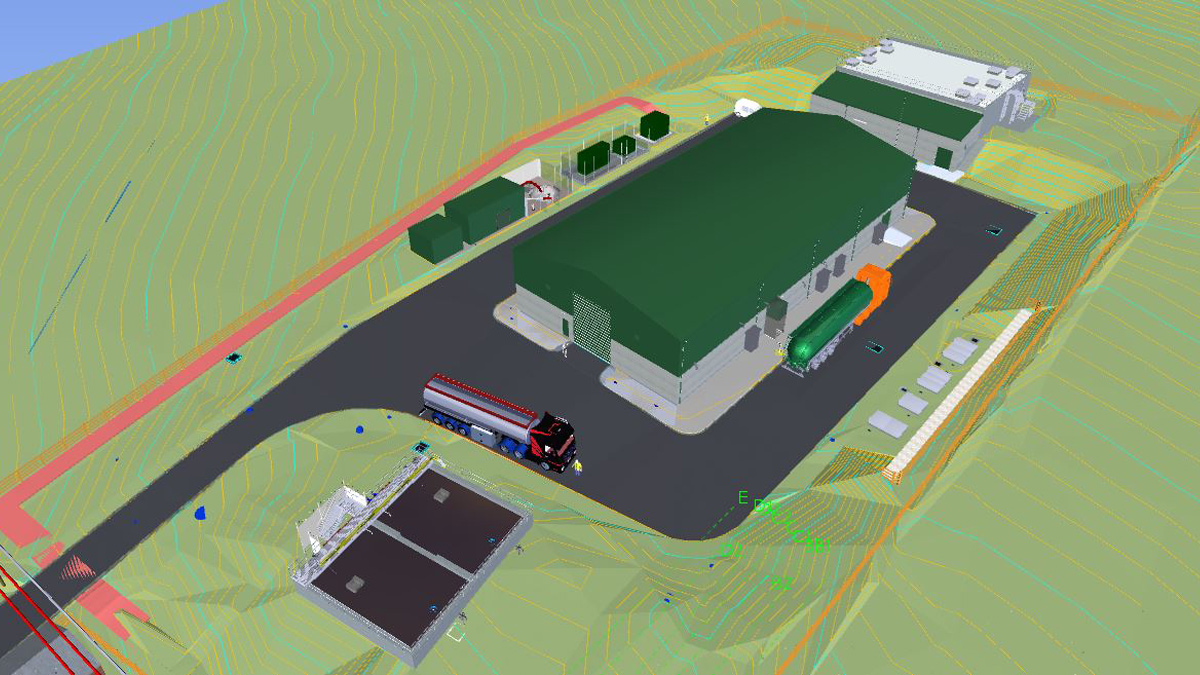
The Revit and Civils 3D models were combined to enable the landscaping, structural details and pipework to be accurately modelled – Courtesy of MMB
Murton WTW: Supply chain – key participants
- Client: Northumbrian Water Group
- Design & Build: MMB
- Feasibility & detailed design: MMB
- Hydraulic modelling: Mott MacDonald
- Structural steelwork design & erection: LH Sleightholme Ltd
- Chemical dosing design, equipment & kiosks: Sheers Ltd
- Reinforcement & concrete installation: Crestfix Ltd
- Pressure filters & manifold pipework: ACWA Services Ltd
- Electrical & cabling installation: Intelect (UK) Ltd
- MCC supply & install: CEMA Ltd
- Systems Integration: IDEC Technical Services Ltd
- Major valves: AVK UK Ltd
- Fabricated pipework: JB Fabrication (Wrexham) Ltd
- Geocellular attenuation tank: Hydro International
- Static mixers: Statiflo
- Metalwork: JHT Fabrications Ltd
- Disinfection & swabbing: Panton McLeod Ltd
- Fire protection system: FIDA Systems Ltd
- Security systems: 20:20 Vision Systems Ltd
- Blockwork: Pringle Building Services Ltd
Construction phase
The use of the digital models also brought benefits during the construction phase. The Navisworks model was used as a communication tool during handover and within morning briefings. The model was handed over to the construction team for their use and was utilised to aide in setting out and to communicate progress, sequencing and methodology to technical and non-technical subcontractors and visitors.
As part of the modelling, the initial cut and fill volumes were imbalanced, and so the design team worked with the construction team to identify opportunities to minimise over-dig and to re-use excavated spoil across the site dynamically to reduce temporary stockpiling. A digital terrain model (DTM) was produced in design using AutoCAD Civil 3D and was successfully utilised by the construction team. The DTM facilitated the efficient excavation works using a Komatsu excavator with inbuilt GPS and intelligent machine control. This methodology was a first for MMB and allowed a much greater accuracy to traditional excavation methods. In comparison to the use of profile boards and a traveller, this intelligent method worked to a 6mm accuracy and has had significant health and safety benefits, mitigating the risk of injury caused by personnel working in close proximity to the excavator bucket. The efficiencies brought about from this methodology also resulted in the three-week earthworks programme reducing to two weeks.
The site team sought to seek alternative uses for the remaining excess spoil. The clays excavated were of excellent quality and were transferred under permit for use in other construction projects in nearby Wooler, including as a capping layer for a new housing development and as fill in a sewage works refurbishment project.
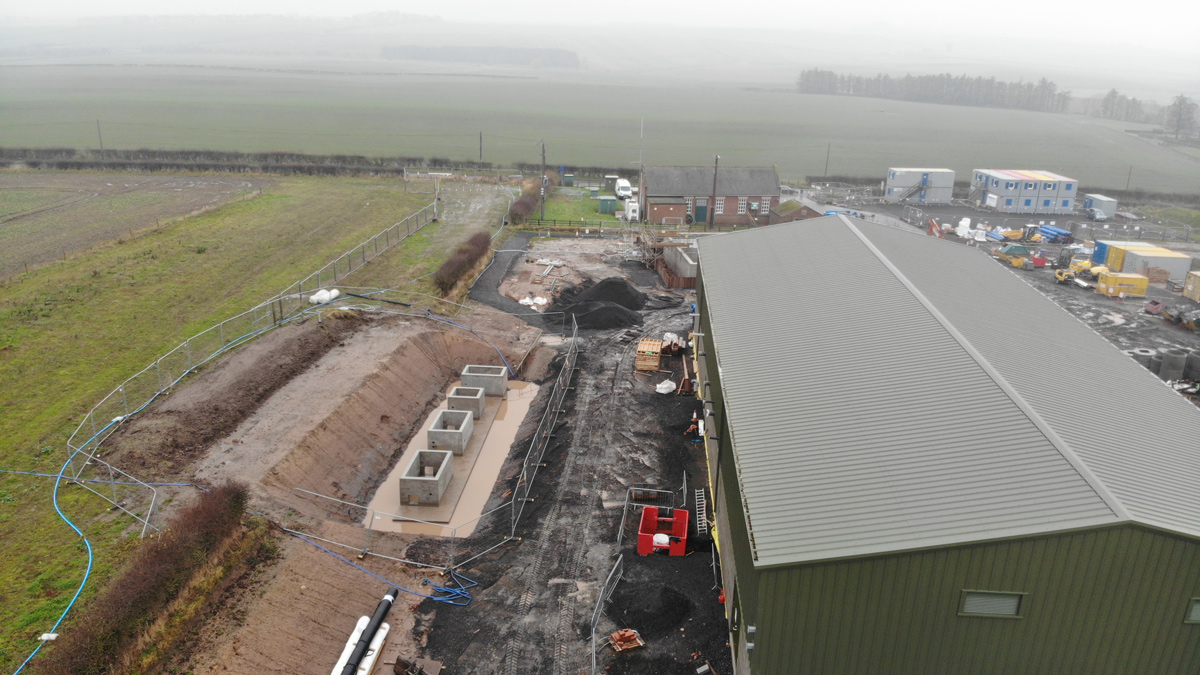
Construction of the final valve complex adjacent to the main treatment building; the existing WTW building can be seen in the background – Courtesy of MMB
The design and construction team also worked together to identify opportunities for offsite manufacture, to minimise the number of personnel operating on a relatively small site. The chemical dosing facilities provided by Sheers Ltd were manufactured and tested within kiosks within their own facility and each was delivered to site as a plug-and-play element of the process, leading to improved quality control through factory testing and commissioning. An early decision was made to house these within kiosk despite being ultimately housed within the main treatment facility, as this maximised the offsite build benefits, as well as forming part of the self-contained secondary bunds for the chemical tanks.
Off-site manufacture was key in the decision to utilise vertical pressure filters. Like the chemical dosing kiosks, the filter units, associated pipework and metalwork access gantry were all pre-assembled and tested within ACWA’s facilities prior to final offload and assembly on site. This approach was also taken for most of the complicated manifold pipework weaving between and connecting the site process plant. The 3D model was utilised by stainless steel pipework fabricators to design and detail the pipework for accurate off-site manufacture meaning that site material.
Working in a design and build environment, constructability is considered at every stage. To formalise this process, Murton’s construction team were identified in the early stages of the project, with regular reviews held to discuss the design, its buildability and associated temporary works requirements. These reviews, along with similar client meetings, were held to invite challenge and give the whole project team an opportunity to influence the design. This brings a wealth of experience which assists in developing a carefully considered design, reducing and controlling risk when total mitigation is not possible.
MMB’s positive safety culture was evidenced throughout the construction phase, where in over 100,000 hours worked, almost 2,000 proactive health and safety incidents were reported, and no lost-time or reportable injuries occurred. An added complication to this project has been the COVID-19 pandemic, during which the site remained operational and avoided closure. Procedures were put in place and method statements were altered to ensure as much work as possible could be completed whilst maintaining strict social distancing. This achievement is of great testament to the whole health and safety conscious project team, given the complex nature of the project and unusual circumstances in which it has been completed.
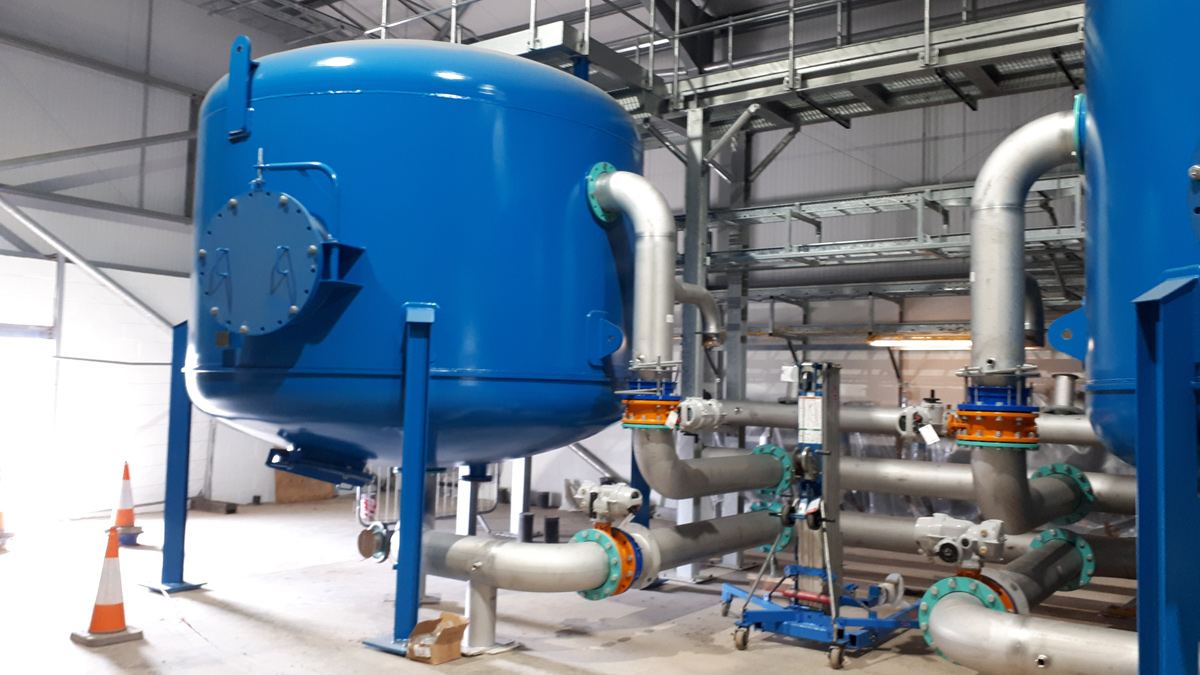
Filter pipework installation – Courtesy of MMB
Sustainability, environmental and community benefits
The previous treatment sites were set to run to waste until the turbidity in the borehole water was suitable to be treated further (not greater than 0.95NTU). NWG were experiencing turbidity spikes on pump start-up, which was exacerbated by frequent start-ups required due to the power outages across rural Northumberland. This resulted in time consuming and costly operator intervention, and wastage of borehole water to the environment. The new WTW incorporates four large pressure filter vessels, which, coupled with upstream chemical dosing, is effective in removing turbidity at higher levels. This will result in significantly fewer run to waste occurrences and therefore provides a more sustainable use of water abstracted from the aquifer as well as improving the security of the water supply to the Berwick area.
Sampling takes place throughout the process to ensure the treatment is effective and the water quality remains within set targets. A by-product of the sampling process is a trickle-waste containing varying levels of chlorine depending on the treatment stage. As mentioned previously, there are also occasions where water must be disposed of where the treatment targets are not met, particularly when the works are restarted following a shutdown. All process wastes from the site are collected and discharged to a local watercourse via an existing swale. In order to safeguard the receiving environment, the process wastes are collected in an on-site wet well and passed through a dechlorination system which circulates the effluent until the correct level of residual chlorine can be determined from the varied discharge. The flows are then dosed with a precise level of sodium bisulphite to remove the free chlorine before discharge.
One of the key constraints of the project was the requirement to construct, test and commission the works whilst maintaining the water supply to the nearby properties served directly by the adjacent treatment works. MMB’s construction and commissioning teams worked with NWG’s network planning and operation teams to develop a detailed sequencing plan that identified water requirements and key dates. In order to accurately plan key dates, the key stakeholders held regular CLIP planning sessions together on site and worked to identify and remove potential blockers at each key stage of the construction and commissioning process.
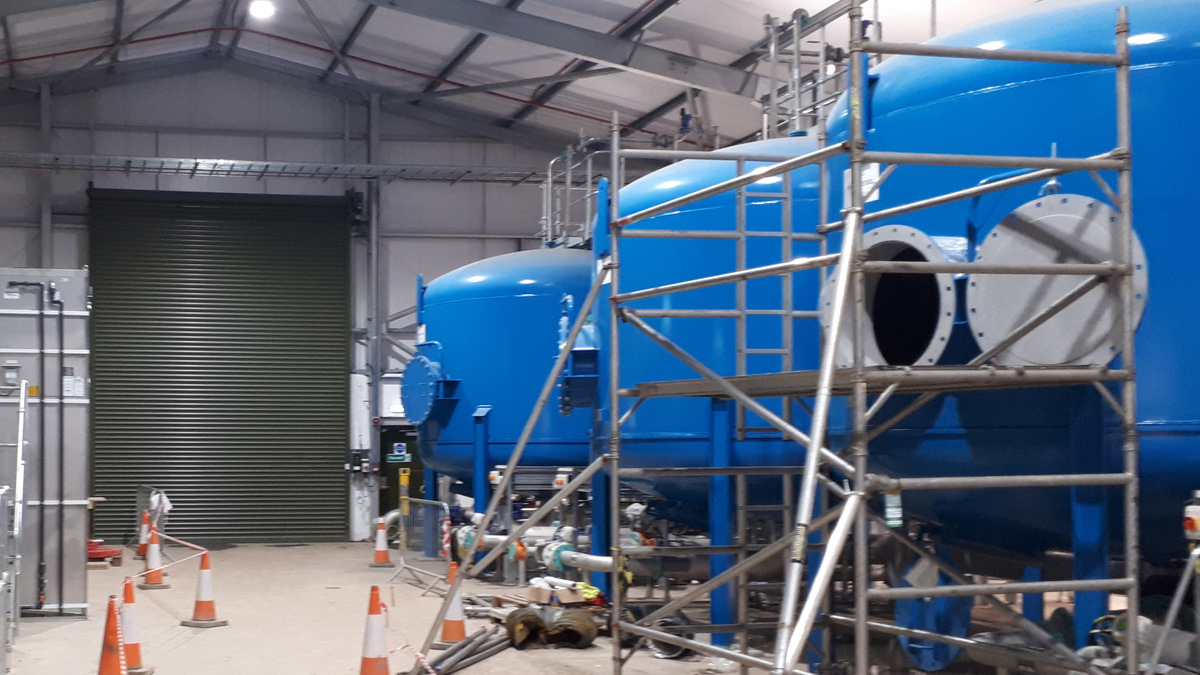
Commissioning works within the treatment building – Courtesy of MMB
Conclusion
Despite inclement weather conditions and disruptions from a global pandemic, Murton WTW has been constructed without any unplanned disruption to the local water supply. Site clearance works commenced in November 2018, with the main site construction works commencing in February 2019. The treatment works construction was substantially completed in summer 2020, with overall completion and handover to NWG expected in autumn 2020. The use of 3D technology, lean planning techniques and off-site manufacture helped to minimise wastage on site, maintain excellent safety standards and find opportunity within a challenging programme.
Key learnings from this process have been fed back into the next scheme in the batch (Wooler WTW) which will utilise the same core team, with construction commencing in June 2020.