Affinity Water Pesticide Removal (2017)
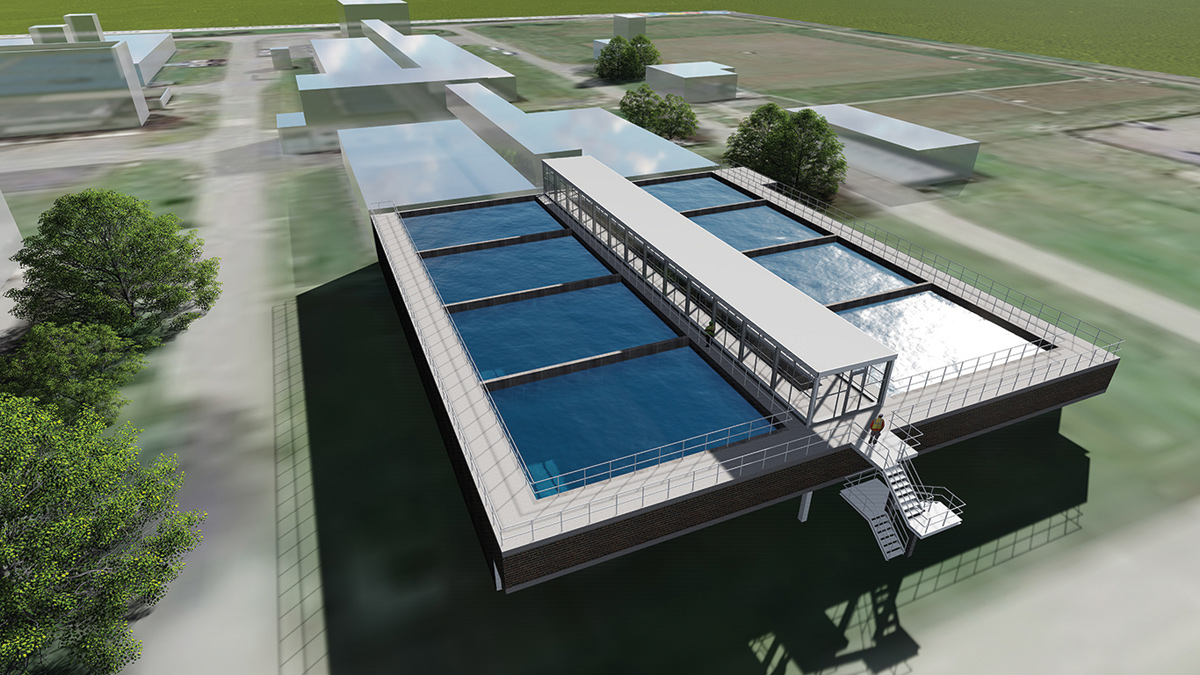
3D model of the new GAC filter bed - Courtesy of AECOM
Affinity Water’s largest water treatment works (WTW) is being upgraded as part of their AMP6 business plan to ensure they continue to provide a robust treatment solution for the removal of pesticides from water abstracted from the River Thames. The scope of the works is to increase the granular activated carbon empty bed contact time (GAC EBCT) to a minimum of 15 minutes to enhance pesticide removal. Trant Engineering has been appointed as principal contractor and has teamed up with AECOM for the provision of 8 (No.) new GAC filters, clean backwash tank and pumping station, high voltage works, increased sludge storage and associated equipment. The (circa) £12m project started construction in January 2017 and is due for completion in July 2018.
Background
Built in 1974, the water treatment works was designed to output 160Ml/d of flow with water abstracted from the River Thames.
Water quality in this abstraction varies depending on weather patterns and land activities in the Upper Thames. This site requires a multistage treatment process to manage the risk from pollutants and produce water that complies with the Water Supply (Water Quality) Regulations 2000. These include the following processes:
- Pre-oxidation.
- Clarification.
- Inter-ozone.
- GAC filtration.
- Disinfection.
Following periods of heavy rainfall and seasonal applications of pesticides to agricultural land, elevated levels of pesticides in the raw water abstractions are detected. Chemicals are used on oil seed rape and wheat predominantly grown in the Thames catchment and are mainly detected in high levels in the abstraction from September to March.
The site currently has 18 (No.) GAC filters split into three streams of six filters each (nominated as streams A, B and C). Streams A and B were built in 1972-1974; Stream C was added in 1992.
Investigations conclude that the existing EBCT should be increased to provide a more robust treatment solution for the times of elevated pesticides levels abstracted from the River Thames.
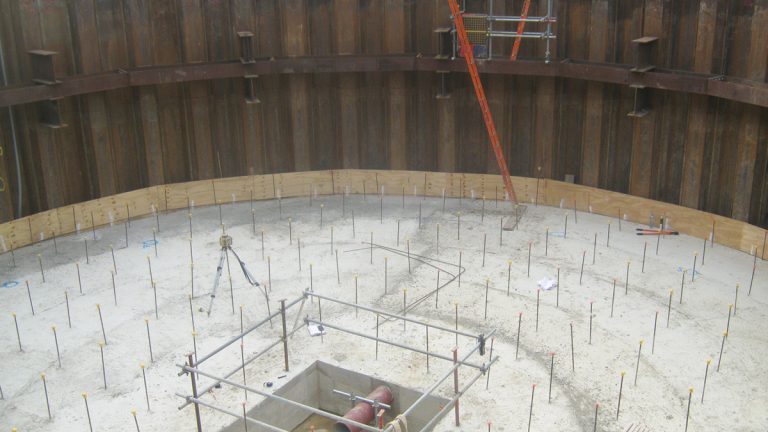
New sludge tank under construction – Courtesy of Trant Engineering
Project scope
Construction and commissioning of sufficient additional GAC filters to increase the EBCT to 15 minutes, to enhance pesticide removal, which requires the installation of additional GAC filters, while one filter is out of service for regeneration and one filter out of service for backwashing. In addition, the GAC filters must lower turbidity, aluminium and iron levels.
Pesticide Removal Project – Key Participants
- Main D&B Contractor: Trant Engineering
- Design Consultant: AECOM
- RC Works: NJ Doyne
- Media Supplier: Jacobi Carbons
- Piling Works: Fussey Piling
- Monolithic Floor: Cadar Ltd
- HV Installation: Morrison Utility Services
- MCC/LVSB: Trant – Control, Automation & Technology
- Diamond Drilling: QST Construction Services
- Backwash Pumps: SPP Pumps Ltd
- Pipework (ductile):Saint Gobain PAM UK
- Epoxy Coated Steel pipe: Freeflow Pipesystems
- System integration: Riverside Automation
- Technical Documentation: 3rd Light Media
- Valves (Butterfly): Glenfield Invicta
- Transformers: Schneider Electric
- Actuators: Rotork Controls
GAC filters – proposed GAC filters (Stream D)
The installation of 8 (No.) combined filter adsorbers in reinforced concrete, constant level – outlet controlled with a monolithic plenum floor manufactured by Cadar Ltd.
- Normal flow rate: 63.5ML/d.
- Normal peak flow rate: 95.2ML/d.
- Emergency peak flow rate: 120ML/d.
- GAC media specification: AquaSorb CS 10 x 20 mesh in all filters. The media size was selected because the GACs are not only acting as adsorbers but also filters.
- Media EBCT: 15 minutes based on maximum design flow and with one filter out of service for regeneration and one filter out of service for backwashing.
- Sweetening flow of 5% of maximum filter flow to be provided to filter out of service to prevent anaerobic conditions developing within the GAC.
Each filter is 9.4m wide, 12.8m long, giving a total filter area of 120m2 and a volume of 138m3. The 8 (No.) have a total filter area of 960m2 and the total filter volume is 1,104m3.
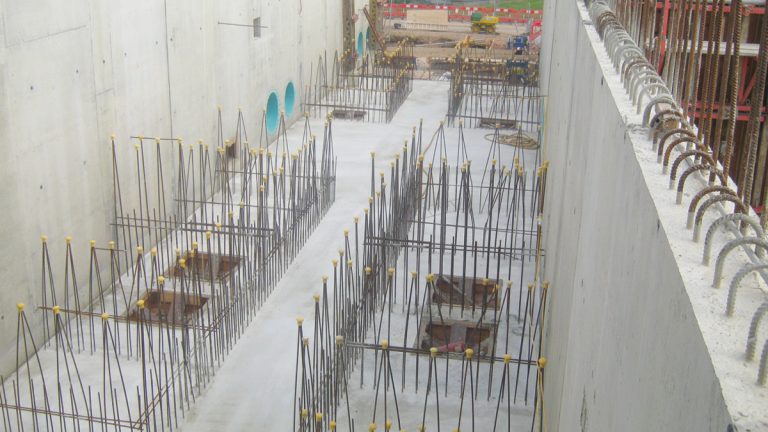
Construction of 8 (No.) GAC filters – 4 (No.) filters either side of a central gallery – Courtesy of Trant Engineering
New backwash system
The backwash system used for the existing GAC filters did not have sufficient capacity for the new GAC filters. Therefore, as part of this project, it was necessary to construct a new backwash system including clean backwash water storage tank, backwash pumps, air blowers and associated equipment.
Backwash philosophy: Each filter operates for a minimum of 24 hours between backwashes, under all inlet turbidity conditions, and 36 hours between backwashes in normal operation (when inlet turbidity post ozone is <1 NTU and algae <4350 cells/mL) without any deterioration on the turbidity, aluminium and iron removal performance. The design is such that the capacity exists for one new filter and one existing filter to convey waste backwash water up to and including the thickened sludge tanks simultaneously.
The new stream backwash system operates independently of the existing backwash system and has sufficient capacity in the new backwash water tank to allow for two successive backwashes without recharge.
- The system is capable of achieving filter bed expansion of 25% for granular activated carbon media densities within the range of 220-550kg/m2.
- Air scour rate: 40m/hr.
- Filter-to-waste duration: 30 minutes or 414m3 based on 3 (No.) bed volumes.
Backwash pumps: Housed in a new RC structure 3 (No.) new 150kW variable speed, end-suction centrifugal variable speed driven pumps have been installed. Working on a duty/assist/standby basis, the total flow rate is between 730l/s to 1330l/s for water temperature range 2 to 25°C. Each backwash duration is in the range of 6-9 minutes, but is typically 8 minutes or 414m3 based on 3 (No.) bed volumes.
Air scour blowers: Housed in the same area as the backwash pumps are 2 (No.) 75kW air blowers. Working on a duty/standby basis, the blowers provide 4800Nm3/h of flow during the air scour process of the backwash cycle. Each cycle duration can range from 3-6 minutes, but is typically 5 minutes.
Clean backwash water storage tank: Construction of a new covered concrete single compartment, clean backwash water tank, with a working capacity of 1328m3. The design is based on two wash volumes on a 9 minutes wash at 25°C without replenishment. The tank has internal dimensions of 22.3m x 12.4m with a tank top water level at 5.3m.
New sludge storage
Prior to the project commencement the existing sludge reception tanks were reported to overflow on a regular basis, indicating that existing hydraulic balancing capacity was insufficient at times. Due to the increase in backwash water flow rates from the new filters, an increase to both hydraulic and compositional balancing was required to minimise overflow events in the future and to provide better control of thickener solids, chemical dosing and solids removal efficiency in downstream processes.
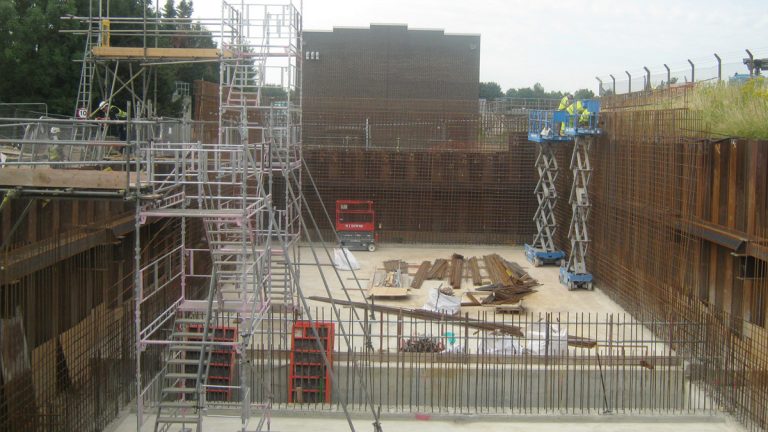
Piling for the new clean backwash water tank and pumping station – Courtesy of Trant Engineering
To control the predicted sludge concentrations within the sludge reception tanks to within a maximum-to-minimum ratio of 2:1, a minimum volume of between 1000-1200m3 is required to be maintained in the tanks at all times.
It was calculated that a minimum operating volume of 2000m3 will be required to minimise the potential for overflow during times peak hydraulic loading. The current combined storage volume is only 1,550m3; therefore to increase capacity a fourth tank, similar in construction to the existing three tanks, was constructed.
MEICA
GAC plant: Using Trant Engineering’s own specialist in-house panel manufacturing division (Trant – Control, Automation & Technology), Trant constructed a new MCC to power the new 2 (No.) 90kW air scour blowers (soft starts) and 3 (No.) 132kW backwash pumps (VSD). The MCC also included power supply and control of the package plant for air compressors, 42 (No.) Rotork actuators for penstocks and valves, 8 (No.) pneumatic flow control valve with closure on power failure and the building services for new plant room and GAC filter gallery.
Trant – Control, Automation & Technology conducted a full harmonic analysis of the site, resulting in the inclusion of a 150A active harmonic filter that was incorporated into the new MCC.
Instrumentation
- 10 (No.) electromagnetic flowmeters.
- 14 (No.) ultrasonic level transmitters.
- 8 (No.) differential pressure transmitters.
- 9 (No.) turbidity analysers.
- 1 (No.) iron analyser.
- 1 (No.) aluminium analyser.
- 2 (No.) pH analyser.
- Full PROFIBUS control system for actuators and instrumentation (PROFIBUS DP and PA).
- Fiber-optic distributed PROFIBUS network, PROFIBUS interface panels, and PROFIBUS pneumatic control for local override systems.
SCADA
- Local operator console and integration with existing SCADA fibre optic network with modification to the SCADA server for the new plant and equipment.
- Modification to existing MCC.
- For the addition of new sludge tank jet mixers and control penstocks.
Conclusion
The (approximately) £12m project started construction in January 2017 and is due for completion in July 2018. Only close collaboration forged with the operations and project teams from Affinity Water, Trant and AECOM has made the achievement to date possible and the entire team are keen to ensure this collaborative approach is maintained in order to also achieve the committed end date of the project.