Turners Road Penstock Chambers Upgrade (2016)
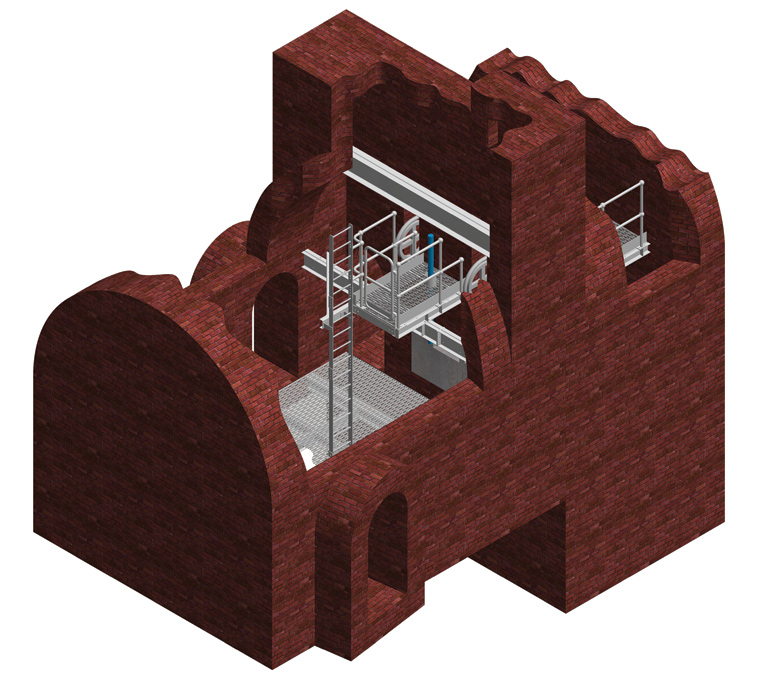
Chamber 1 high level platform, detailed design model (penstock mechanism not shown) - Courtesy of Optimise
As part of the Thames Water (TW) AMP5 programme of works, it was necessary to remove and upgrade condemned platforms within two interlinked penstock chambers on the Low Level No. 1 (LL1) and Low Level No. 2 (LL2) sewers, which are two of the largest and most important in London. The chambers sit beneath a busy, signal-controlled junction in east London and each sewer is approximately 3m in diameter and 14m deep to invert level. The structures were constructed around 1905 and contain 3 (No.) five tonne penstocks designed to be operated by hand with the assistance of counterweights. The counterweights are suspended above pits within separate rooms and are connected to the penstocks by chains, which pass over high level wheel mechanisms. The location of the counterweight rooms in relation to their respective penstocks is different in each chamber. Working in tandem with other penstocks upstream in the network, the Turners Road penstocks allows sections of either sewer to be isolated for inspection and maintenance. Access into the chambers is via an 8m deep main access shaft from road level and along a narrow side entry corridor. Operation and maintenance of the penstocks was carried out from a platform in each chamber suspended 6m above invert level.
Structural survey
Following a structural survey condemning the existing platforms, Optimise was awarded a contract to carry out their demolition and to design and install a new fit for purpose platform arrangement. Condemning the platforms meant that access into the chambers was prohibited, including access for any form of survey or investigation. The existing flooring for demolition consisted of 4” thick Yorkstone floor slabs supported by steel beams, which were built into the masonry walls. Optimise was faced with the immediate challenge of trying to plan, design and coordinate the demolition and replacement of a structure buried 8m underground, which could not be safely accessed.
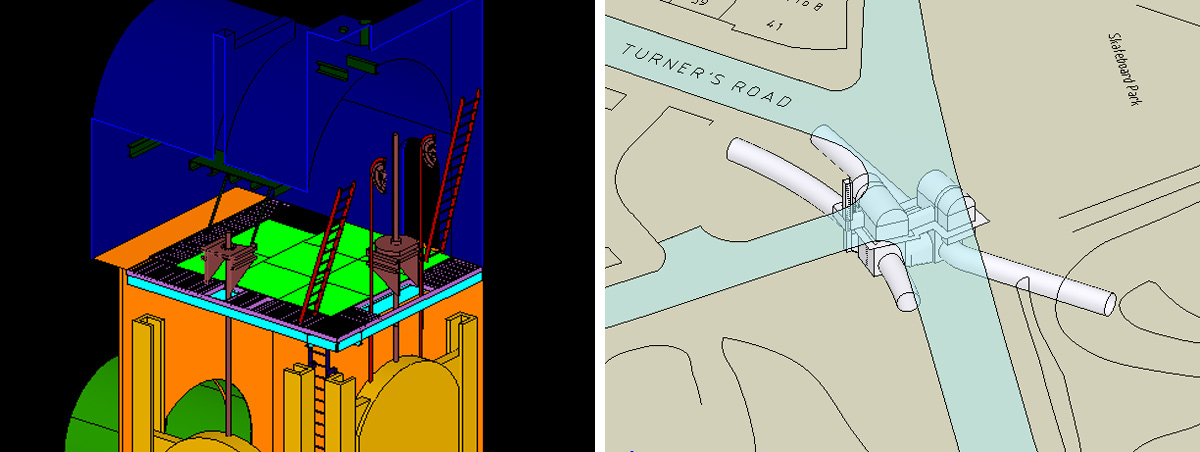
(left) The existing platform arrangement in Chamber 1 (counterweight room not shown) and (right) 3D model showing the position of the penstock chambers under the junction – Courtesy of Optimise
The problem
The contractor’s initial outline methodology was to excavate onto the chambers, remove their roofs and demolish the platforms from above. Scaffolding would then be installed and the new platforms constructed.
During the initial scoping and optioneering phase of the project, a number of coordination and hazard review meetings were attended by the whole project team. These meetings were paramount to understanding the issues faced and the project scope.
Some of the issues identified by the project team included:
- The chamber roofs consist of masonry arches surrounded by concrete with their crowns 3m below the highway, making demolition extremely challenging. In addition, a 48” intermediate pressure gas main and a large brick egg sewer cross the junction very close to the roofs of the chambers.
- Both sewers surcharge during storm events, regularly flooding the chambers and inundating the platforms.
- Temporary over-pumping and isolation of the chambers was not be feasible given the high flow rates experienced, even during dry weather conditions. Access into the sewers at invert level was only possible at night time in dry weather for a short period of time with very strict controls in place.
- Due to the platforms being condemned, access underneath the platforms for any type of works was completely prohibited, i.e. no scaffolding or crash deck could be installed. The condemned floor slabs were very heavy and would need to be carefully removed individually to avoid causing a catastrophic collapse.
- The platform could not be broken up and allowed to fall into the inverts of the sewers due to the risk of a catastrophic collapse, of damaging the sewers and of causing blockages.
It became clear to the project team that the initial outline methodology of removing the chamber roof and demolishing from above would not be feasible and a bespoke confined space working methodology would need to be employed by specialist rope access personnel.
Survey
To allow the design of the new platform and to devise a safe methodology for the demolition and construction, it was important that a detailed survey was carried out. The design team worked with a specialist survey company, APR Services, and a rope access sub-contractor, CAN Geotechnical, to devise a feasible survey methodology given the inherent constraints within the chambers.
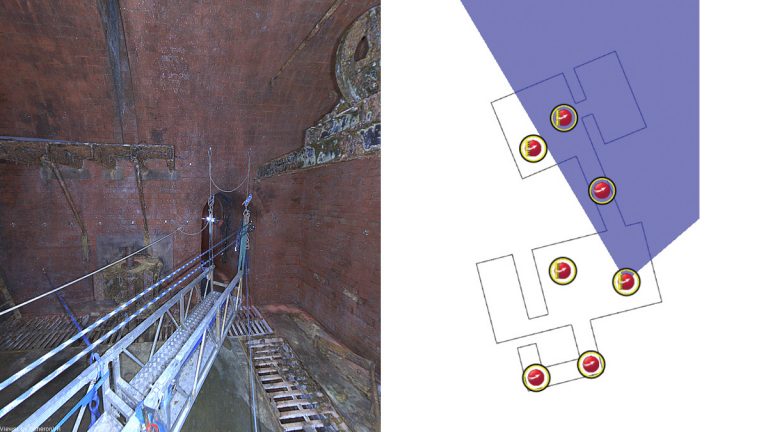
Virtual site tour output showing a temporary walkway – Courtesy Optimise
To obtain the most accurate information possible and to minimise man hours in the confined space, laser scanning was carried out to generate a 3D model along with 360° Spheron Photography. This technology, more commonly used as part of crime scene investigation, was used to create a ‘virtual site tour’, which allowed users to navigate themselves around the chamber viewing high definition imagery. The technology also allows the user to take measurements and zoom in on areas of interest.
Under the supervision of Optimise, CAN used bolt climbing techniques to install temporary safe walkways over the condemned flooring. This then allowed APR Services to set up their equipment safely and carry out the survey. The ‘virtual site tour’ was subsequently used to provide information for design and to enable effective collaboration within the project team by facilitating discussion and risk identification during a number of project team coordination meetings.
For the use of this technology, the project team was awarded ‘Innovation of the Year’ at the 2016 Thames Water Excellence in Health and Safety Awards.
Demolition
Safely removing the condemned flooring in this environment was no mean feat. Due to the issues faced, the safest way to remove the condemned flooring was in small sections by rope access personnel within the confines of the existing chamber. Therefore all demolition material had to be removed via a side entry corridor and up the 8m deep access shaft. To enable this, Optimise worked with CAN and specialist lifting company, Niko Ltd, to manufacture and install a temporary gantry crane inside the chambers.
To ensure everything went smoothly and safely on site, CAN’s operatives attended a training course with Niko where they rehearsed the installation in a safe environment.
Collaborating with Niko Ltd and CAN, Optimise developed a safe method for removing the existing floor slabs by fixing chemical resin anchors and extracting them with a hand operated jack attached to the temporary crane. Working with a specialist cutting contractor, a cutting method suitable for the atmosphere in the chambers was employed to remove the existing steel beams.
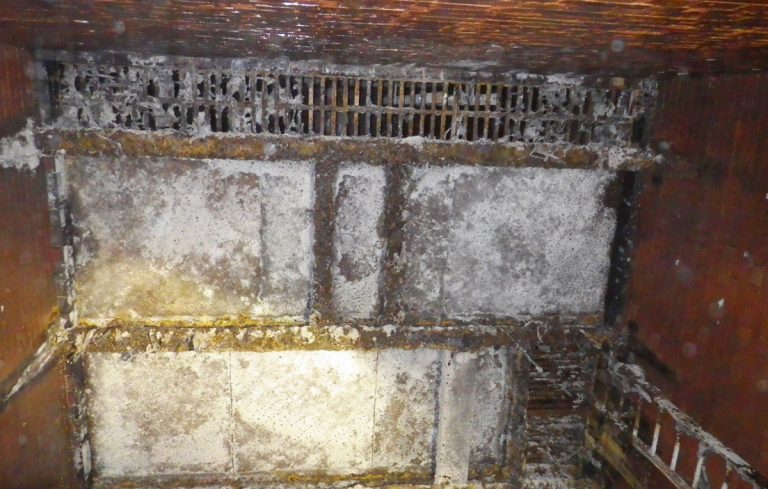
The underside of the condemned flooring in Chamber 2 – Courtesy of Optimise
Design
Using point cloud data from the laser scanning, the Optimise design team generated an accurate 3D model of the chambers. This was used along with the ‘virtual site tour’ to design a new bespoke, fit for purpose three level platform system, which would allow Thames Water operatives to safely operate and maintain the penstocks and their mechanisms.
As with the demolition, the new platform would be installed within the confines of the existing chamber and all required materials would have to be delivered to the installation point down the 8m deep access shaft and along the narrow side entry corridor.
Through a number of coordination meetings, the Optimise design team worked with the Optimise site team, CAN (the rope access contractor) and Steelway Fensecure (the specialist steelwork fabricator) to ensure that the design was buildable given the rope access working methodology and the access routes. A modular design was developed which allowed the new platforms to be delivered into the chambers in sections.
During a workshop, the design team used the 3D model to test and confirm with CAN that structural members could be safely negotiated through the access point and be manoeuvred into position. The design team also engaged with representatives from the Thames Water trunk sewers team to understand their requirements and to ensure that the design met their needs. The 3D model was further developed by Steelway Fensecure during the detailed design phase.
Turners Road Penstock Chambers Upgrade: Project Delivery Team
- Client: Thames Water
- Project delivery: Optimise Joint Venture *
- Designers: MWH (now Stantec UK)
- Main contractor: Clancy Docwra
- Rope access sub-contractor: CAN
- Survey contractor: APR Services
- Specialist lifting company: Niko Ltd
- Steelwork fabricator: Steelway Fensecure
* Optimise is a joint venture formed to deliver AMP5 projects for Thames Water and is made up of four companies: MWH, Murphy, Barhale and Clancy
Construction
The assembly of the platform was carried out with precision by specialist rope access operatives supported by the Optimise site team. During construction, the Optimise site team and CAN worked collaboratively to manage health and safety risks on a day to day basis.
To ensure safe working in the chambers, the project team liaised with TW Operations staff at Abbey Mills SPS to understand the operation of the network and expected levels in the sewers.
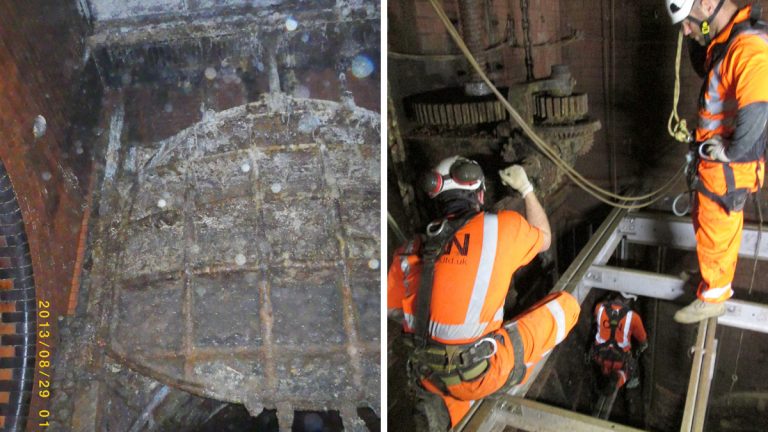
(left) 5 ton penstock from the sewer invert level and (right) Rope access operatives installing the new platform in Chamber 1 – Courtesy of Optimise
Maintaining a constant link between the site team and TW Operations was critical to the safety of the rope access operatives working in the chamber. During the construction phase, the Optimise design team provided effective site support to both the site team and the specialist contractors, liaising with them as required to resolve queries and issues.
Following the completion of construction, the platforms were successfully handed over to TW Operations, allowing them to safely access and carry out essential maintenance to these important assets once again.