Tynywaun WTW (2017)
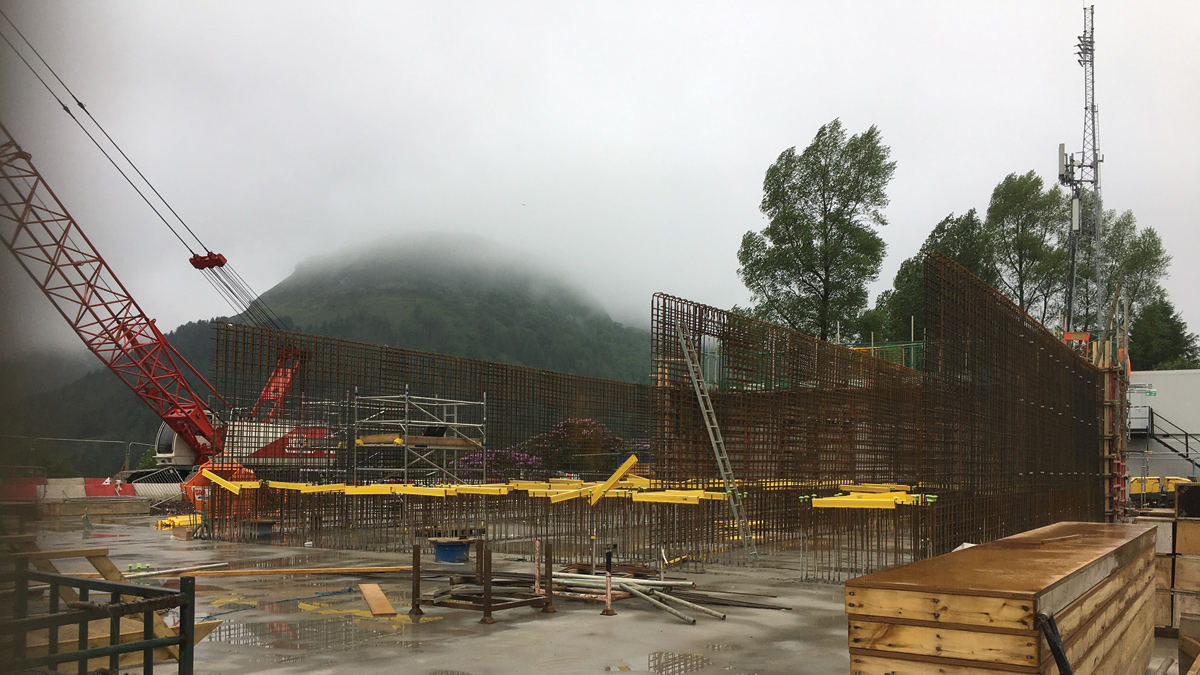
Flocculation tank and DAF cell walls (May 2017) - Courtesy of Skanska
Tynywaun WTW is located at the north end of the Rhondda Fawr Valley, at the base of the Rhigos Mountain, in the village of Tynewydd at an elevation of 1,000 feet. Water treatment works have operated at the Tynywaun site since 1906 and the existing works was last refurbished during the 1990s, with new filters to replace the original pressure filters. The plant serves a population of approximately 30,000 people. The Tynywaun Raw Water Reservoir (approximately 24,200m3) is supplied to by three separate sources; Llyn Faw/Nant Garreg, Mountain Spring and Ystrad Fernol respectively. Over recent years the Nant Garreg source has deteriorated and is subsequently isolated during periods of heavy rainfall. The existing works require refurbishment and modification to ensure enhanced treatment during periods of high rainfall and turbidity and to allow utilisation of Nant Garreg and increase the capacity from 10MLD to 12MLD.
Existing works
Tynywaun WTW comprises two stages of rapid gravity filtration. The first stage is external and of concrete construction, the second stage is internal and of stainless steel construction. Raw water is dosed with aluminium sulphate for coagulation and gravitates to the first stage rapid gravity filters.
The partially treated water is then pumped to the second stage filter house, and dosed prior to filtration with chlorine for disinfection and manganese precipitation, lime for pH correction, and orthophosphoric acid to inhibit plumbosolvency. The second stage filters remove manganese from the water. Treated water is chlorinated and pumped to the final water service reservoir. The final water is then stored for a contact time within the 4ML capacity final water service reservoir before entering the supply and distribution network.
Design
The design of Tynywaun WTW is being carried out by Arcadis (previously Hyder). The value of the design package is £800k and includes the design of all aspects of the project.
Pilot trials: Jar tests were conducted in summer 2015 to determine treatment issues and offer potential process solutions. Process testing was conducted on raw water samples from the Nant Garreg source reservoir to compare coagulant dosing chemicals, the two of which were the existing aluminium sulphate and an alternative ferric sulphate. Raw water samples were taken during a period of significant rainfall, which resulted in a high turbidity sample.
The established aluminium sulphate chemical coagulant at Tynywaun was maintained, as the process tests indicated that the aluminium sulphate produced a better clarified water quality over the ferric sulphate coagulant. It was also determined that the raw water pH reduction anticipated by the aluminium sulphate dose should be corrected with a new lime dosing point upstream, to ensure alkalinity and aluminium precipitation for optimal clarification and residual metal concentrations.
Primary flocculation and DAF clarification was subsequently proposed following these findings, strengthened by its proven ability in treating low turbidity and moderate to high colour upland waters.
Design details: The proposed refurbishment and modifications required construction of a new building to house the flocculation and DAF plant together with the proposed lime, alum and poly storage and dosing systems, along with the corresponding MCC room and a laboratory for sample analysis.
Having increased the energy requirements with the introduction of a new DAF system, the environment and efficiencies were reviewed and improvement was identified to utilise the site topography by removing the existing interstage pumping between first and second stage RGFs and replacing with a gravity main. The first stage RGF outlet pipework was rerouted to suit the inclined site topography with a gravity main configuration, thus eliminating the current need for pumping.
First stage RGF modifications also include improved filter flow control and backwashing facilities with a new rinse-to-waste facility. The rinse to waste is designed to divert initial flow of water through a filter to waste after a backwash. This rinse water is collected and pumped back to the raw water reservoir. A run to waste facility has also been incorporated to enable the treatment works to be flushed through, should the treated water not meet quality standards.
The existing orthophosphoric acid and chlorine storage dosing systems are approaching the end of their asset life and are therefore being replaced as part of the scheme.
Design challenges: Once the clarification stage had been agreed, the location and layout of the works extension had to be designed to accommodate the limited space available on the treatment works site. It was considered advantageous to locate the DAF plant at an elevation higher than that of the existing 1st stage filters to eliminate the need for any interstage pumping.
The location onsite selected for the new DAF building revealed some unexpected issues during the ground investigations. Several buried tanks were discovered beneath the site which had been part of the earliest treatment works and consisted of slow sand filtration and a water storage tank. Once discovered it became apparent that the tanks were filled with rubble and covered with grass; presenting unsuitable ground conditions to support the new DAF building without ground improvements. Various groundworks solutions were considered, before being narrowed down to two suitable alternatives, ground stabilisation or piling.
Ground stabilisation was potentially the most economical solution, but was ultimately rejected as it would not have been possible to deliver the plant and equipment to site due to the restricted access to the site. Piling was finally chosen, and again the piling design was limited to the size of piling rig that could be delivered to site. These ground conditions also necessitated a review of the proposed plant layout, to position the flocculation and DAF tanks on the best load bearing area of the site.
Washwater from the works (from filter washing and sampling) was designed to be collected in lagoons and discharged to the sewer. A limit of 20m3/hr of the site waste volume can be discharged to the sewer, presenting a limited spare capacity remaining for the additional discharge from the new DAF plant.
To minimise DAF sludge volumes, a sludge scraper was incorporated into the DAF cell design. This scraper pushes sludge over a beach rather than hydraulic desludging; whereby a DAF stream is isolated, allowing the tank level to rise until DAF sludge discharges over a weir. Therefore, surface scraping produces less wastewater than hydraulic desludging, hence maintaining the total wastewater volumes within the permitted flowrate and eliminating the need for an additional wastewater treatment process to reduce the volume of wastewater discharge to sewer.
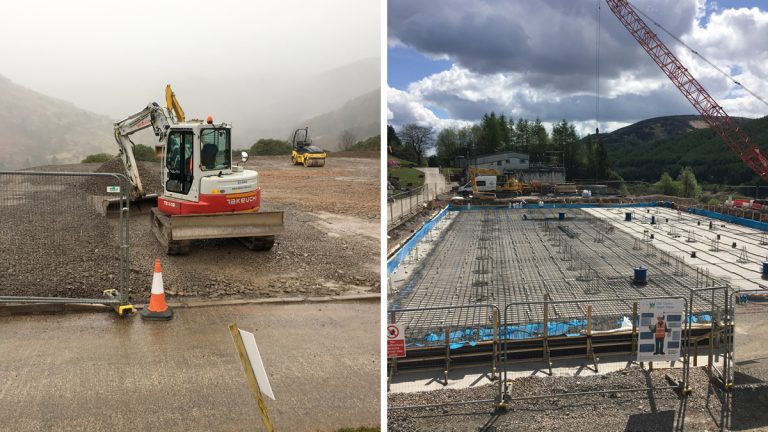
(left) Pile mat nearing completion and (right) piles inserted – Courtesy of Skanska
Construction
Site establishment at Tynywaun was in early November 2016, with the first activities limited to excavation and piling. Many issues presented challenges from a construction point of view. Access to the site is gained through a small village, with pinch points in the road, which restricted the size of vehicle access to Tynywaun.
Any level ground on the topographically inclined site is accommodated with existing works resulting in a scarcity of spare storage space. This restriction meant that any excavated material had to be removed from site in small lorries adding time and cost implications to the construction activity. Deliveries associated with the construction were time managed in line with the local school – scheduled outside of start and finish times – to reduce risks and promote safety.
The site access restrictions have also limited alternative construction techniques for implementation at Tynywaun. The previously mentioned road pinch points ruled out the practicality of factory assembled steel process tanks or precast panels; therefore conventional concrete site construction methods were required, which extended the construction programme.
Environment
Potential environmental impact has been at the forefront of the AMP6 improvement works at Tynywaun WTW. Where process critical introductions have resulted in increased energy consumption, the design team has considerately reconfigured pipework to remove interstage pumping and utilise the site topography for gravity operation. The building for the new DAF plant was put through planning with provision for solar panels to offset the energy usage. The panels are outside of scope but planning was agreed with them installed.
Progress
Initial phases of civil construction began in the DAF plant in early 2017, with the foundations piled, floor slab poured and works starting on the DAF tank walls. Construction in the DAF plant is expected to continue until late 2017. This will run in parallel with the other site modifications, aiming for commissioning and phasing the new plant into service by the end of March 2018.