Waverley Growth (2021)
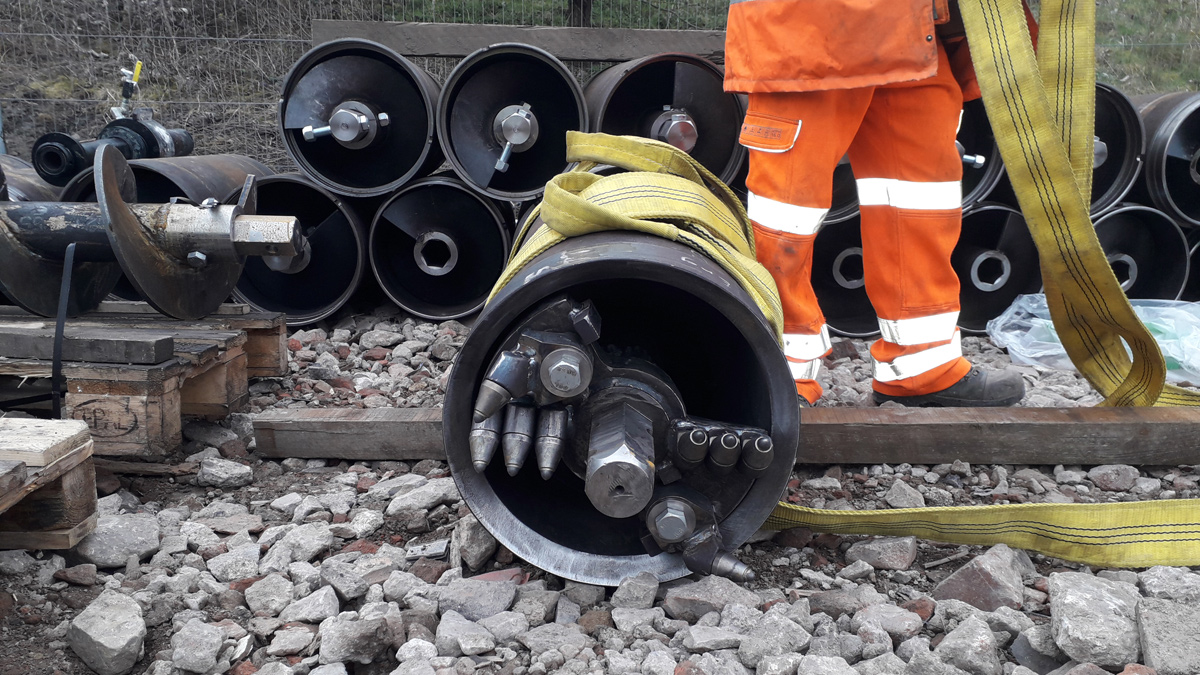
Lead auger and casing with the pigs showing prior to first installation - Courtesy of Barhale
To accommodate new housing and commercial growth in the Waverley/Catcliffe area of Sheffield, Yorkshire Water required the design and construction of a new pipeline to transfer the flows from a housing development of 4000 homes to the main Blackburn Meadows WwTW. The pipeline route crossed main dual carriageways, other roads, roundabouts, railway lines and passed through a significant volume of made ground from Sheffield’s historic heavy steel industry. Barhale was engaged by Yorkshire Water as principal contractor for the delivery of infrastructure works.
Working differently
Traditionally, Yorkshire Water projects are divided into two sequential elements: an investigation stage and then a delivery stage. At the Waverley project initiation, it was quickly established that a new way of working would be required to ensure the project was delivered on programme. The project team decided to split the scheme into two overlapping parts: the pressurised mains (phase 1) and the gravity sewer (phase 2) in order to accelerate the project delivery.
By creating the two distinct elements, it became possible to complete the investigation and design for each faster. It also helped to speed-up project delivery.
A collaborative design sprint workshop to develop the most efficient solution was held by the project team with Yorkshire Water and designers GHD. Its output resulted in a reduction of the length of the pipeline by 1km, resulting in a 3.1km pipe installation. This provided a saving of over £1.5m and reduced the potential for huge disruption to Sheffield’s highways.
The agreement to divide the project into two phases also allowed the construction works to start more than six months earlier than would otherwise have been the case.
Ultimately, the complex project would entail the installation of 3.1km of new twin and triple rising mains laid in 225mm and 250mm polyethylene (SDR 17) pipe from Poplar Way to Europa Link.
Waverley Growth Scheme: Supply chain – key participants
- Principal contractor/tunelling: Barhale
- Ground investigation: Geotechnics
- Designers: GHD
- Tunnelling: Barhale
- Phase 1 contractor: Ken Rodney Construction
- Phase 2 contractor: Indepth Civils
- Shoring/temporary works: MGF
- Surveying & tankering: Quest
- Auger boring & microtunnelling equipment: BCS
- GRP jacking pipe: Amiblu Norway AS
- PE pipe : Westwoods
- Precast pipes & shaft rings: Tracey Concrete
- Directional drilling rig: Ken Rodney Construction
Phase 1
The phase 1 works’ scope was to extend the twin pressurised pipelines to the topographic high point along the route. This involved crossing two major highways, including the Rotherham Gateway/Sheffield Parkway (a busy route into Sheffield city centre).
A total length of 832m of pressurised main was installed along with:
- 4 (No.) valve chambers with 8 (No.) valves.
- 3 (No.) hatchbox chambers.
- 1 (No.) air valve chamber with 2 (No.) air valves.
- 1 (No.) wash out chamber with 2 (No.) wash outs.
The main was laid using a combination of open cut and trenchless techniques. Open cut was used when installing the pipe through fields. Directional drilling was utilised in locations where open cut would have caused disruption.
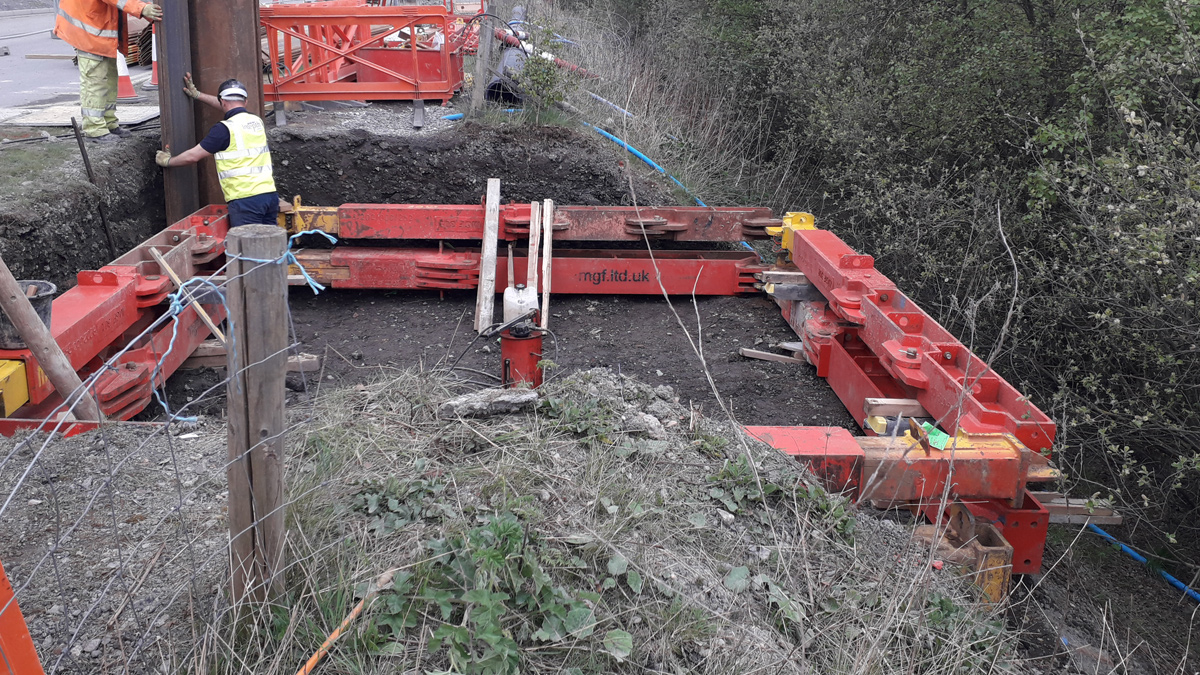
Pitching the 1st sheet piles into the MGF manhole frame to allow excavation of 1 of the shafts – Courtesy of Barhale
Twinned pipework was installed throughout to connect to the existing network. However, this was increased to three pipes under the A630, along with valves and access points to future-proof the installation.
Throughout the project there was a risk of striking existing services, so trials were carried out to identify their location. The project was planned to cross an intermediate pressure gas main and, as part of a trial, it was exposed. A qualified representative was present to observe both the trial and crossing. The crossing was made two metres below the gas pipe to ensure no disruption.
A security bund was installed to prevent unauthorised access to the developer’s land after completion at the site. Existing self-seeded vegetation had provided a natural barrier but was removed during the course of the project.
Phase 2
For the phase 2 works, the project team identified three main route options:
- The Europa Link route.
- Sheffield airport route.
- The steel yard route.
At the design sprint workshop, the project team evaluated each of the options and selected the steel yard as the optimum. The decisions at the workshop allowed the team to focus on the preferred route reducing the investigation stage cycle time.
The second phase of the works comprised 2.1km of pipe installation. This section passed through land owned by local businesses and involved crossing a rail line servicing the steel yard and various associated gas transfer pipes. This section was constructed utilising both trenchless and open cut techniques.
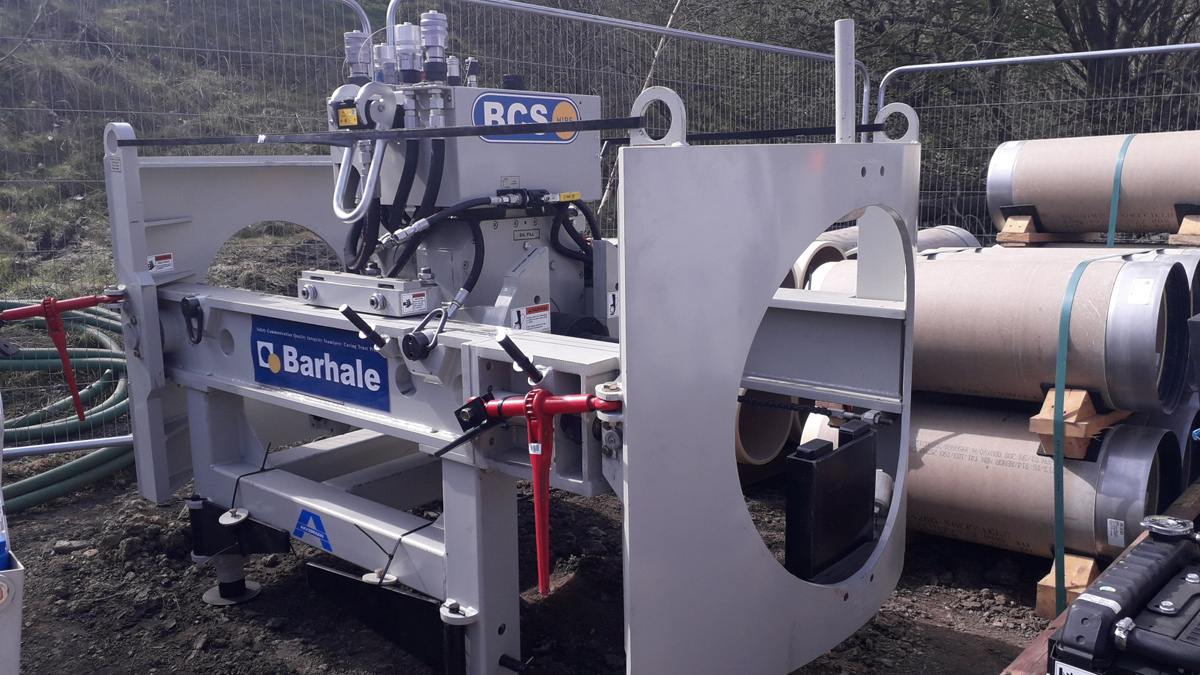
BCS owned Akkerman guided auger rig making its debut at Waverley – Courtesy of Barhale
Tunnelling methods
To run the new pipeline from the development to the treatment works, the route had to overcome a variety of road, rail and industrial challenges – involving the use of different tunnelling methods for each section.
This included 650m of horizontal directional drilling (HDD) below two live busy dual carriageways. The team also needed to accommodate an almost 90° bend in the pipe’s radius in a relatively short distance so the pipe was laid in 250mm and 225 mm polyethylene (SDR 17) using a Ditch Witch JT40.
A significant proportion of the pipeline needed to be laid across made ground on the site of a former steelworks. Ground conditions, concerns about contamination and the required 6m depth meant that auger boring was the preferred approach. Use of 375mm GRP pipe meant less ground needed to be displaced than with clay pipework. One of Barhale’s Akerman GBM 308A augerboring machines was employed. The overall length of the auger bore was around 800m.
Microtunnelling was selected for a distance of 150m where survey bores had indicated a higher proportion of rock. This section of pipe also crossed below two live rail lines so it was necessary to avoid interruption. A 600mm diameter Iseki slurry microtunnelling machine was employed to drive a larger bore tunnel enabling 600mm concrete pipe to be laid.
Open cut excavation was used to lay 375mm diameter concrete pipe to a slightly shallower depth of around 3m, over a total of 875m.
The ControlPoint system was utilised to ensure high quality control and monitoring of the jointing of the pipes. This technology controls welds and cooling times based on the site conditions and provides a coordinate location of each joint.

Perfectly fits into a 2400mm diameter launch shaft with lead driller and assistant driller present – Courtesy of Barhale
Conclusion
Tackling the two key elements as parallel project phases, bringing the business’s extensive tunnelling experience and access to resources to bear, and optimising the tunnelling method deployed for each phase delivered multiple benefits. Most importantly, the Barhale team was able to get on site much earlier, allowing capacity in the timescale to address often difficult ground conditions.
Additionally, the use of clever planning and design meant the total length of pipe laid over the two phases was 3124m – a saving of more than 1000m on the original project specification. It delivered a commensurate saving in costs and carbon footprint and has made future development possible at the Waverley site.