Winchburgh WwTW (2023)
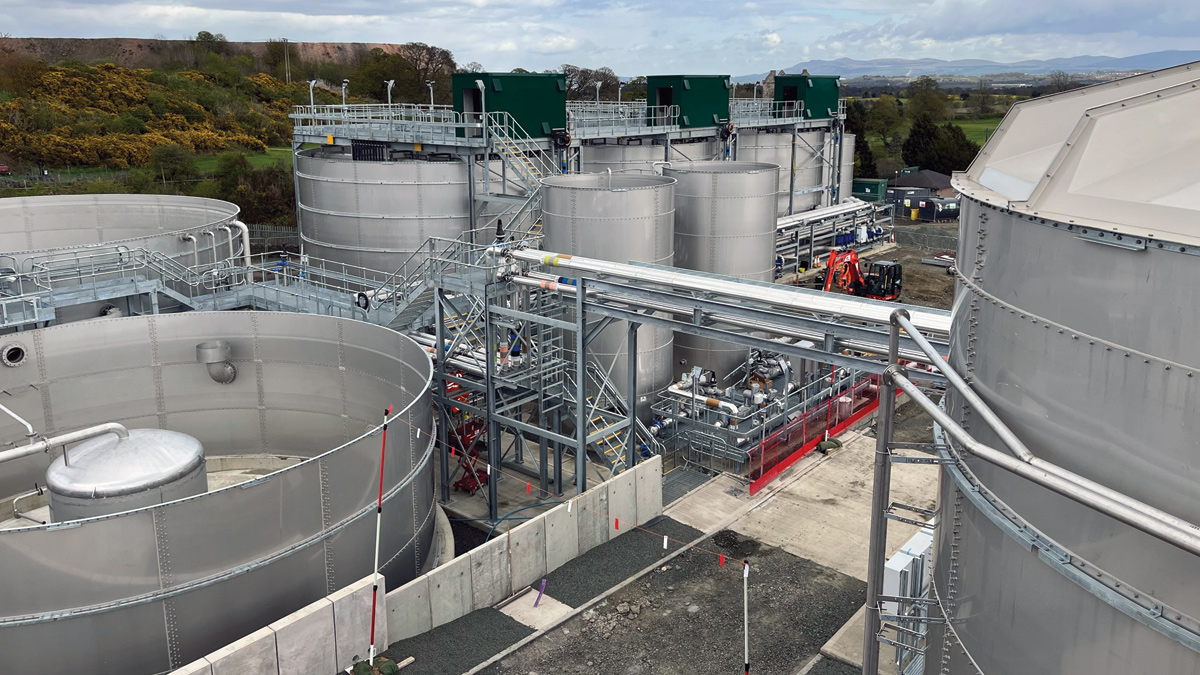
Winchburgh WwTW (May 2023) - Courtesy of ESD
Winchburgh is located five miles west of Edinburgh Airport and the existing wastewater treatment works lies to the south-east of the town, approximately 200m from the nearest residential street. The site access road runs adjacent to the main Glasgow to Edinburgh railway line, the top of the embankment being a couple of metres from the roadside, with the railway line sitting approximately 10m below. The existing works is a traditional biofiltration process, rated for 3,800PE. Due to Winchburgh being designated within the West Lothian Development Plan for significant housing development, there is a projected population increase to 16,389 PE by 2032. To cope with this increase, Scottish Water have started construction of a new £35m Nereda® treatment plant. Scottish Water’s Non-Infrastructure Alliance Partner, ESD, a joint venture of MWH Treatment, Binnies and Galliford Try, commenced construction in July 2021.
Existing works process
The existing works takes combined flows under gravity from upper and lower Winchburgh. The lower Winchburgh flows gravitate into an inlet pumping station and are transferred up to the inlet works, whereas the upper Winchburgh flows gravitate straight into the inlet works. Flows less than 9 DWF pass through screening and grit removal and flows less than 6 DWF (full flow to treatment (FFT)) pass through primary settlement.
Thereafter, secondary treatment of FFT is carried out by biofilters, prior to final settlement and tertiary treatment. Primary sludges are removed to sludge storage prior to tankering off-site and the humus sludges are returned for co-settlement.
Process selection
As a result of the growth in the area there is a need to increase the size of the treatment works. The technology selected by Scottish Water to meet this need is Royal HaskoningDHV’s Nereda® process solution. This decision was based primarily on the following drivers:
- Reduced land take due to the smaller footprint for the Nereda® solution, compared to a conventional solution.
- Carbon reduction due to the power required to run a Nereda® plant being significantly lower than that required for a conventional works.
The Nereda® process technology was developed by Royal HaskoningDHV (RHDHV) and offers sustainable wastewater treatment. The natural sewage treatment process purifies water, using few or no chemicals, through proprietary aerobic granular sludge (AGS) technology.
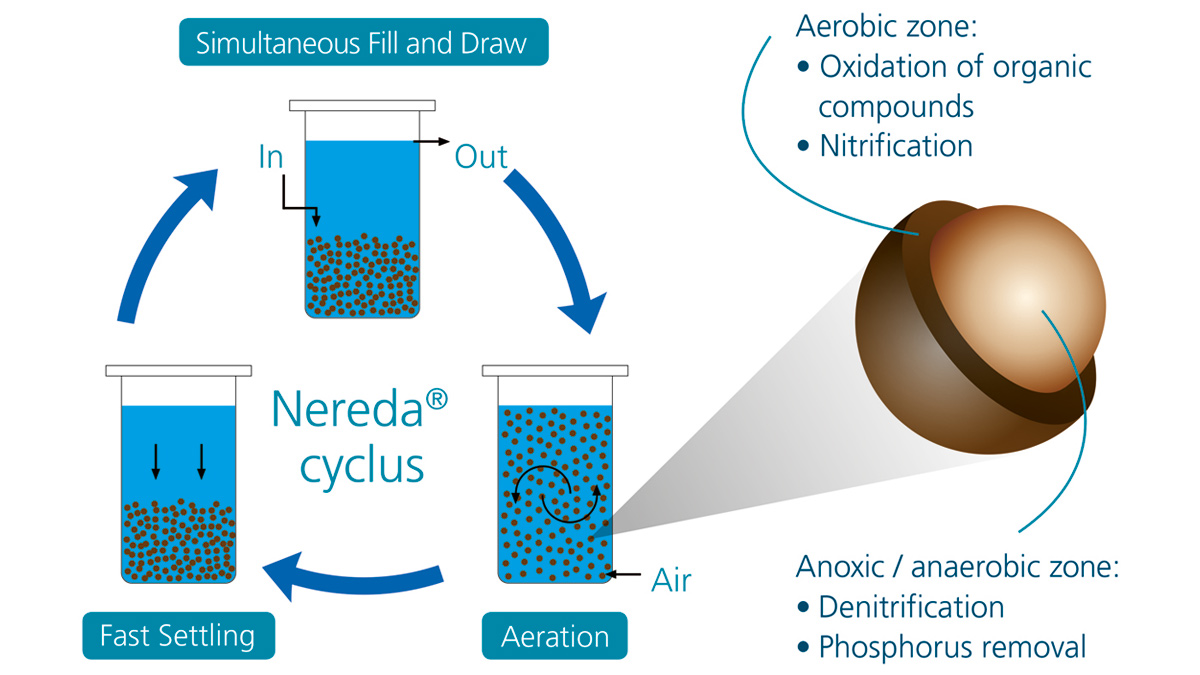
Nereda® process cycle – Courtesy of Royal HaskoningDHV
Within a Nereda® reactor, through a simple three-step cycle, the purifying biomass grows naturally as compact aerobic granular sludge, with superb settling properties. An important feature of granular sludge is that aerobic and anoxic/anaerobic zones co-exist. This enables a large variety of biological processes, including nitrification, denitrification and biological phosphate removal, to happen simultaneously.
The alternating cycle steps are:
- Filling of wastewater at the reactor bottom and simultaneously displacing purified water from the previous cycle at the reactor top.
- Aeration, resulting in extensive simultaneous biological removal of organic, nitrogen and phosphorus components.
- Fast settling, to separate biomass from the purified effluent after which the Nereda® plant is ready for a new cycle.
Overview of scope and process
The annotated model below shows the site layout and highlights each of the key structures and process units.
The new wastewater treatment works has an upper and lower catchment pumping station that will intercept the two existing sewers and pump a maximum of formula A flows to the new packaged inlet works. In the event that the incoming flows defeat the inlet pumps, each pumping station includes a CSO that provides screening prior to the flows gravitating to the watercourse.
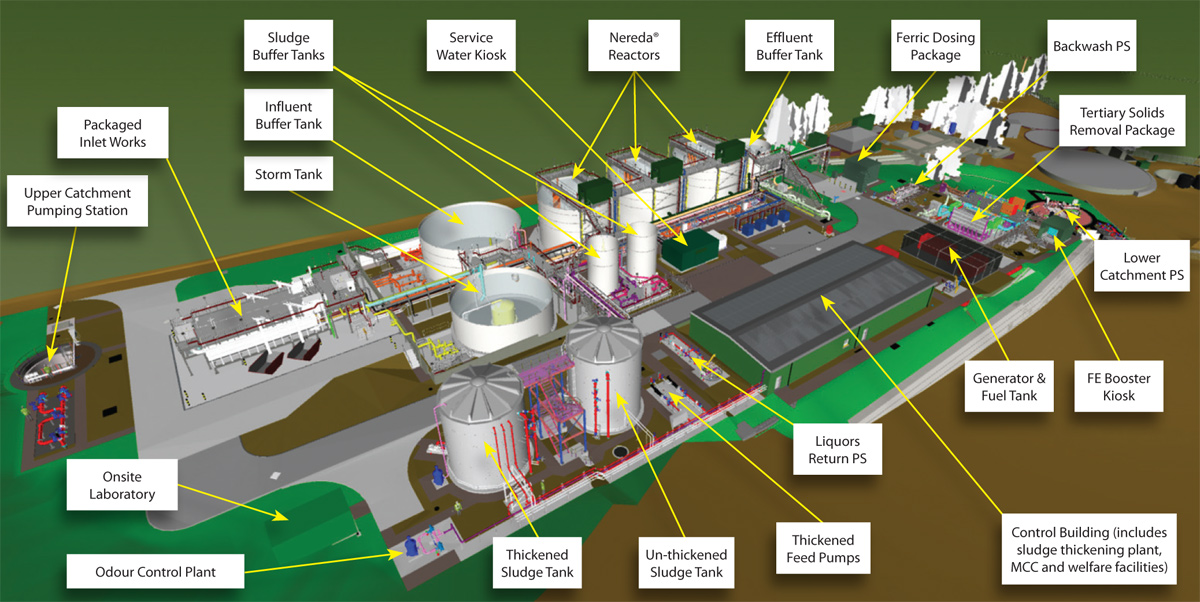
Winchburgh site layout model – Courtesy of ESD JV
The pumped flows from the upper and lower inlet pumping station are combined within the inlet collection chamber at the head of the above ground inlet works and screened via two screens operating in a duty/standby configuration. Grit and FOG removal are also included within the packaged inlet works and the screenings and grit discharged into dedicated skips, positioned adjacent to the units.
Full flow to treatment (FFT) gravitates to the Nereda® influent buffer tank and flows greater than FFT will spill over a weir, within the packaged inlet works, and gravitate to a storm tank.
The storm tanks are automatically emptied after each storm event, and the storm water returned to the inlet works outlet chamber via storm return pumps. At the end of each individual storm tank return cycle, a cleaning system flushes any residual solids back to the inlet works outlet channel.
From the influent buffer tank, the FFT is split between the three Nereda® reactors. Excess sludge from the Nereda® plant will gravitate to the sludge buffer tanks, the contents of which, after further settlement and supernatant return, will be transferred to the unthickened sludge tank before being pumped to two disc thickeners. Thereafter, the sludge is transferred to the thickened sludge tank. Liquors from the thickening process are pumped from the liquors return pumping station back to the influent buffer tank.
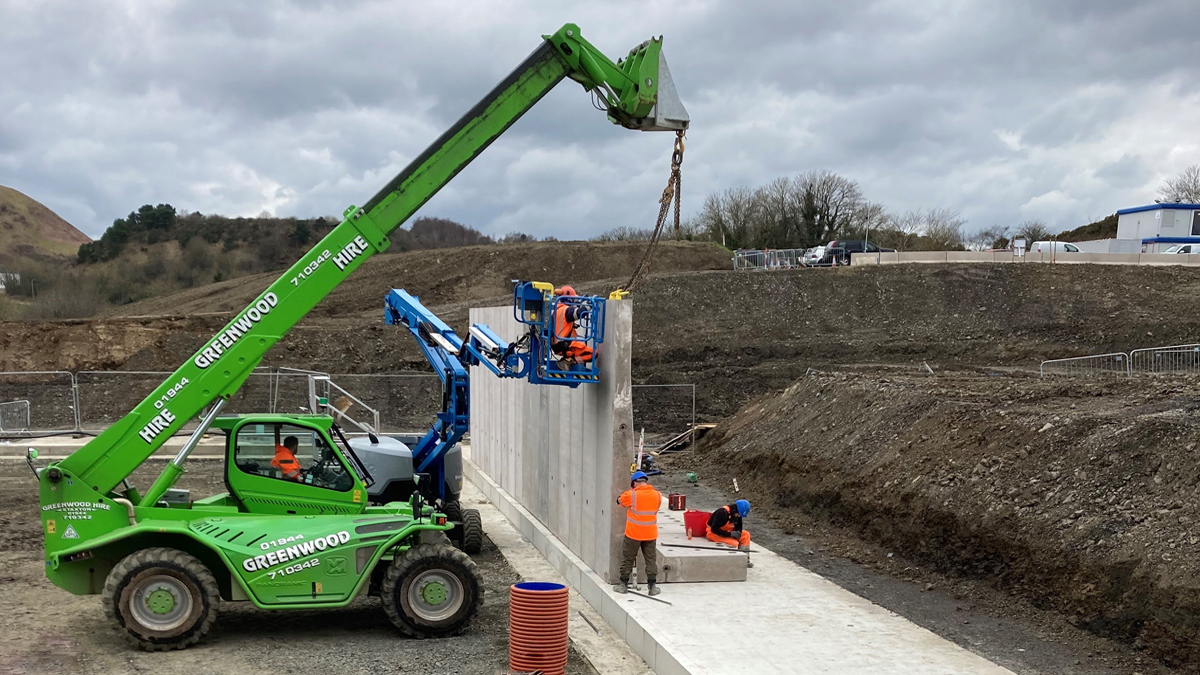
Precast retaining wall installation – Courtesy of ESD JV
Treated effluent from the Nereda® reactors gravitates to an effluent balance tank, which is required to attenuate the flows, prior to being passed to the tertiary solids removal plant, which is the final treatment prior to discharge to the water course.
Also included within the scope is a ferric dosing plant. This was included within the scope of supply on the Winchburgh project as a result of the lessons learned on the Inverurie WwTW project, the only other operational Nereda® plant in Scotland. The limited dosing of ferric will better facilitate P removal to a lower concentration, if required.
Winchburgh WwTW: Supply chain – key participants
- Client: Scottish Water
- Principal designer & contractor: ESD JV
- Nereda® process: Royal HaskoningDHV
- Design/fabrication/installation of inlet works & Nereda® plant: EPS Water
- MCC/systems integration: MCS Control Systems Ltd
- Mechanical installation: Dustacco Engineering
- Electrical installation: Field Systems Design Ltd
- Steelwork, cladding & access metalwork: Archibald McAulay & Son Ltd
- Tertiary solids removal plant & CSOs: Eliquo Hydrok
- Sludge thickening plant: Huber Technology
- Building designer: Allen Gordon LLP
- Building fit out: B2 Projects Ltd
- Service water & FE booster sets: KGN Pillinger
- Pumps: Hidrostal
- Pumps: Xylem Water Solutions
- Pumps: Mono Pumps – (NOV Process & Flow Technologies)
- Air mixer: Landia UK Ltd
- Standby generator: DTGen
- Odour control plant: ERG (Air Pollution Control) Ltd
- Sludge tanks: Goodwin Tanks Ltd
- Chemical dosing: Lintott Control Systems Ltd
- Precast concrete: FP McCann Ltd
- Gabion walls: Maccaferri Ltd
- Shaft sinking: Fineturret Ltd

Extract from 4D Synchro animation – Courtesy of EPS Water
DfMA and collaborative design
The strategy from the outset of the project was to maximise the use of Design for Manufacturing & Assembly (DfMA) and the use of the available digital delivery tools, with the primary aims being:
- Reduced programme: Most of the M&E construction can be completed off-site, reducing the amount of manpower required on-site and enabling fabrication and mechanical assembly to be completed in parallel with civil construction.
- Improved quality: Stringent quality control in fabrication facilities, coupled with the ability for the client to inspect and snag assemblies prior to delivery.
- Reduced HSE risk: A significant portion of the construction is completed in a controlled factory environment, rather than on site.
- Improved collaboration: The use of common data environments and design within the 3D world to aid communication of latest information.
Design
To help assist in delivering the project strategy, EPS Water was identified early in the project life-cycle as being a key subcontractor. EPS are the Nereda® license partner of RHDHV for Scotland and were a key partner of ESD in delivering the Inverurie STW project. EPS was engaged at the outline design phase to work alongside ESD to collaboratively design the Nereda® works for Winchburgh.
The design was developed using Revit, a 3D modelling package, which was shared in Glue, a cloud-based BIM management and collaboration product. Using these tools allowed regular design reviews between the ESD and EPS design teams throughout the design process. This being of particular benefit as the design could be progressed without restriction during the COVID pandemic.
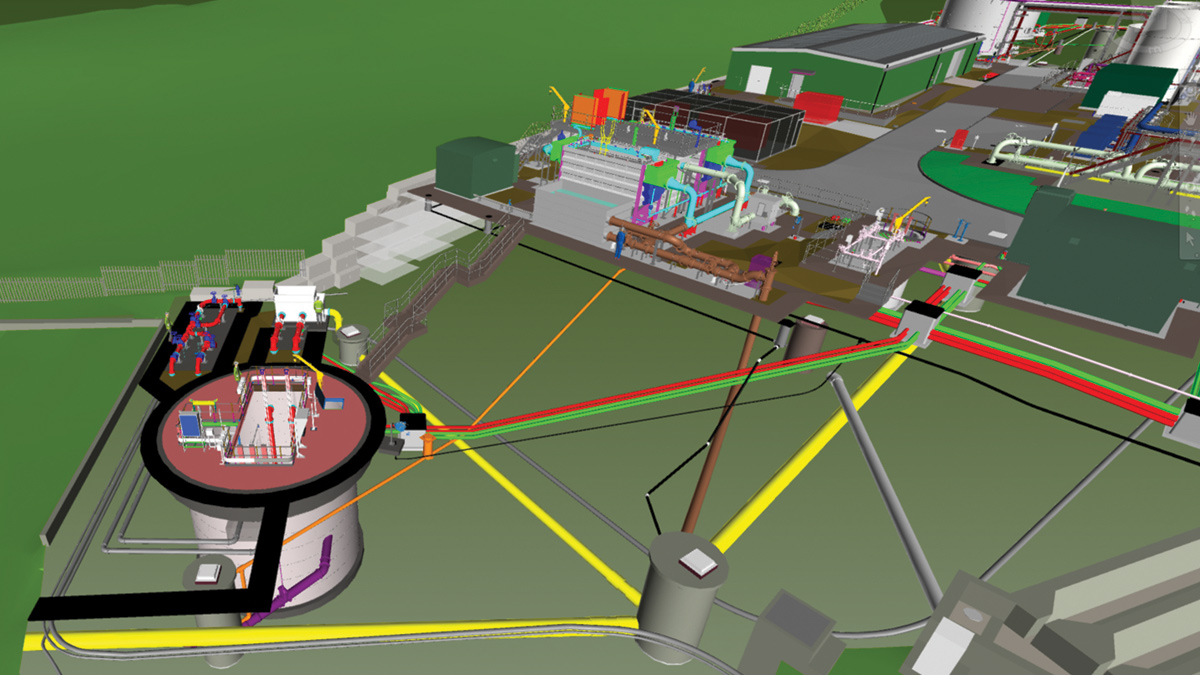
Winchburgh 3D model (lower pumping station area) with below ground services visible – Courtesy of ESD JV
In addition to the experience held within EPS of Nereda® treatment works they also have a strong background in the development of DfMA solutions, which combines in-house advanced digital engineering services with their substantial manufacturing capacity. The Winchburgh project was designed to be a DfMA solution, meaning that the large assemblies were designed to be broken down into modular transportable sections, taking into account the particular site delivery restrictions, that can be reassembled on site.
The DfMA approach was also utilised within the civil design, where possible. The level differences across the site led to retaining walls in excess of 4m high, most of which were constructed from precast concrete, reducing site installation time from 3-4 weeks to 6 days.
Furthermore, precast segments were used to construct the shafts required for the upper and lower catchment pumping stations, the biggest of which was 8m diameter by 8m deep. This again had programme savings, but crucially reduced the risk associated with an in situ concrete solution for such deep shafts.
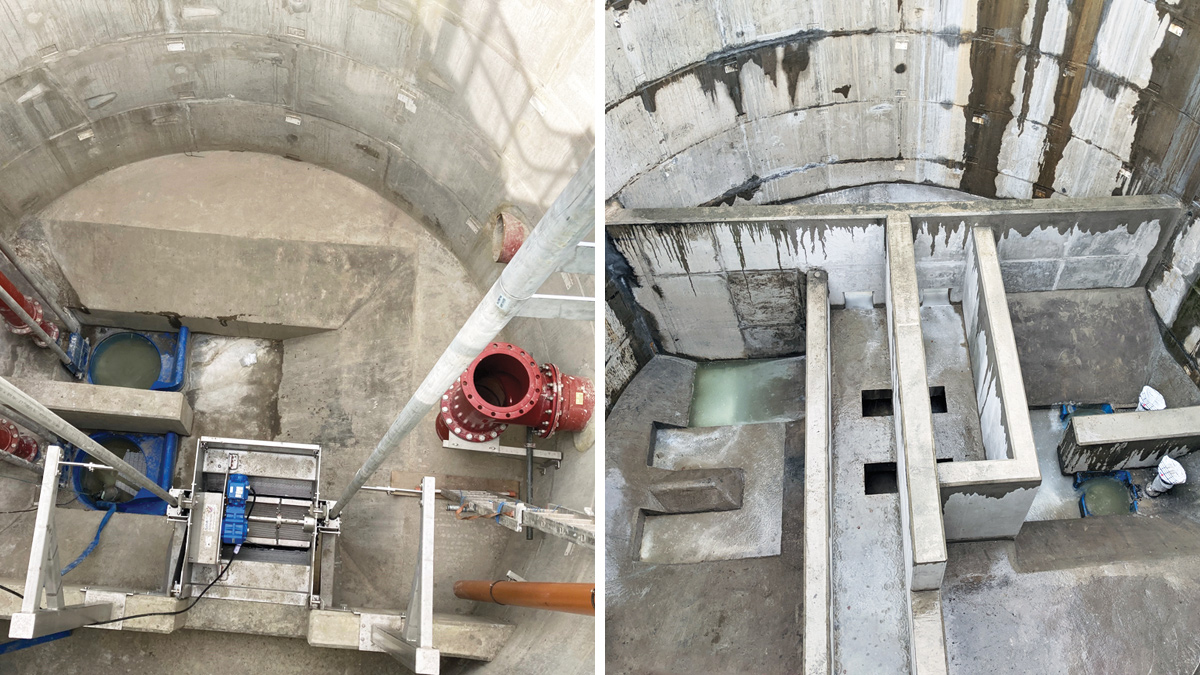
(left) Upper catchment pumping station and (right) lower catchment pumping station – Courtesy of ESD JV
The 3D model has proved invaluable throughout the life-cycle of the project, from the early stages of the project being used to develop the design in conjunction with all stakeholders within Scottish Water, to facilitating discussions between the site team and design team during the construction phase.
A consequence of the model providing such a clear picture of the design is that meaningful discussions can be held with people of all technical levels and minimises the risk of miscommunication.
The use of digital tools was further extended to develop the programme. The construction programme and 3D model was used in conjunction with a 4D Synchro scheduling tool to develop a simulated programme of works. This assisted the site team in planning the works and identifying any clashes or pinch points in the programme whereby there may be too much activity within certain areas of the site that could lead to inefficient working, or prevent certain operations being completed in parallel.
Status – June 2023
Construction work commenced on site in July 2021 and is due for completion in October 2023 at which point process commissioning will commence.
At time of writing (June 2023), the civil construction works are nearing completion, with key remaining works being the construction of the new outfall and the installation of the deep pipework for the CSO overflow and lower catchment sewer tie in.
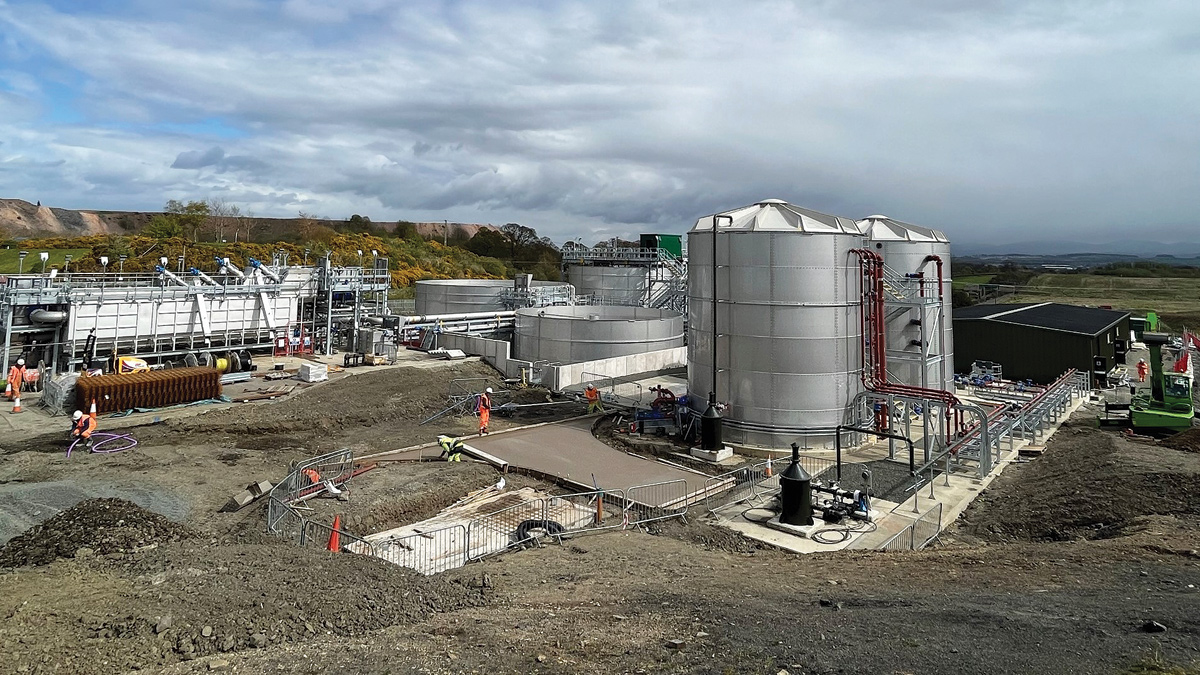
Winchburgh WwTW (May 2023) – Courtesy of ESD JV
The main process units/structures are installed, with the MCC planned for delivery at the end of May 2023, at which point the electrical installation can be completed, allowing dry, then wet commissioning to commence. The target date to start slowly turning the flows from the existing treatment process to the new Nereda® treatment process is October 2023, with handover to Scottish Water planned for June 2024, allowing the intervening time for process commissioning.