Horsham New WwTW (2024)
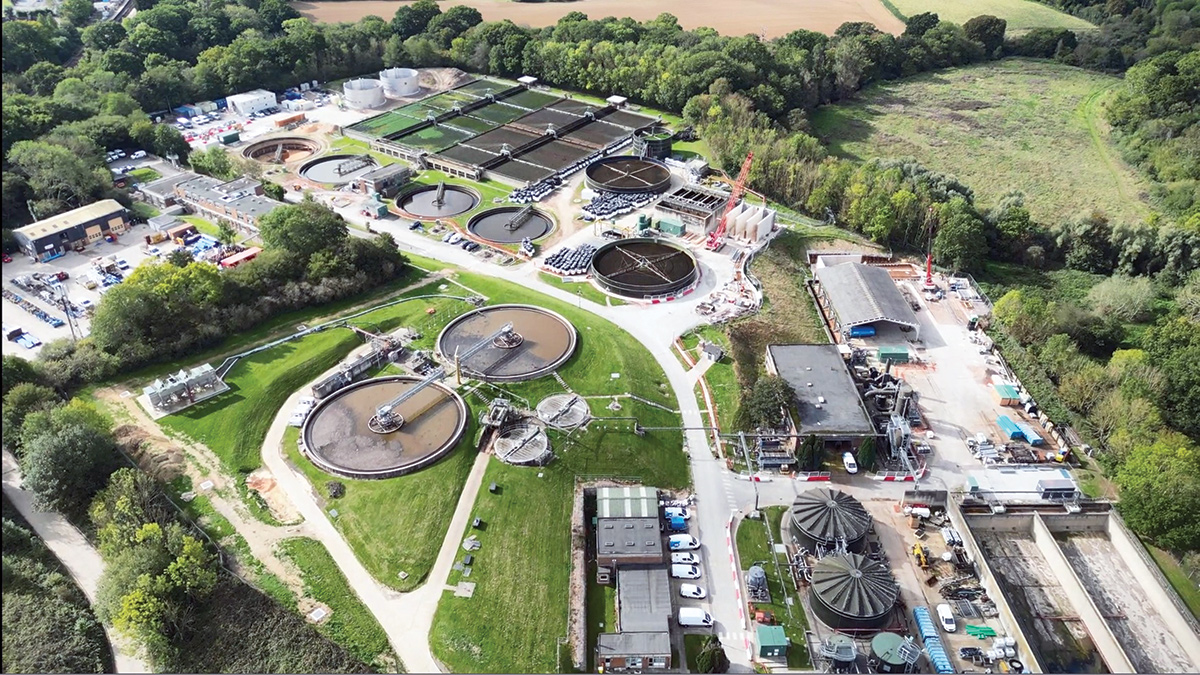
The £31m project to upgrade Horsham New WwTW in West Sussex commenced in September 2022 - Courtesy of CMDP JV
Southern Water are investing £31m to upgrade Horsham New Wastewater Treatment Works (WwTW) in West Sussex, which will improve the site’s treatment processes and capacity, and boost the quality of the final effluent returning to the River Arun, thanks to a range of new hi-tech machinery, control and monitoring systems, as well as the replacement and refurbishment of existing equipment. The major upgrade started on site in September 2022 and is being delivered by CMDP JV, a joint venture between Costain and MWH Treatment. Completion of the works is expected in spring 2025.
Drivers
The capital scheme at Southern Water’s Horsham New WwTW will deliver an upgrade to the treatment facilities at the site to cater for the significant growth forecast within the Horsham catchment and surrounding areas over the next ten years, together with an improvement in the Total Phosphate final effluent emission standard, tightening from 1 mg/l to 0.25 mg/l.
These improvements to the site’s treatment processes have been designed for a 2035 population equivalent of 93,345, representing a 15% increase since 2020. There are no proposed increases to the permitted dry weather flow or permitted flow to full treatment as part of the scheme.
As well as the WFD quality driver, the project also encompasses an element of capital maintenance to be delivered by 31 March 2025, as follows:
- Replacement of two existing band screens with two new fine screens, located within the existing inlet chamber and configured as duty/assist. Each screen is rated at 1,700 l/s.
- Provide duty/standby screenings handling equipment (SHE) and a common launder channel.
- Provide a new centrifugal pump with a duty of 640 l/s to assist the two existing storm screw pumps.
- Replace the screw pumps within the existing works, with two new screw pumps, each rated at 640 l/s.
- Replace the two diesel engines and gearboxes with electric motors.
The third and final project driver, also to be delivered by 31 March 2025, is the need to ensure the upgraded Horsham New WwTW has sufficient hydraulic and process treatment capacity to allow for the 15.5% increase in expected growth in the local population up to 2035.
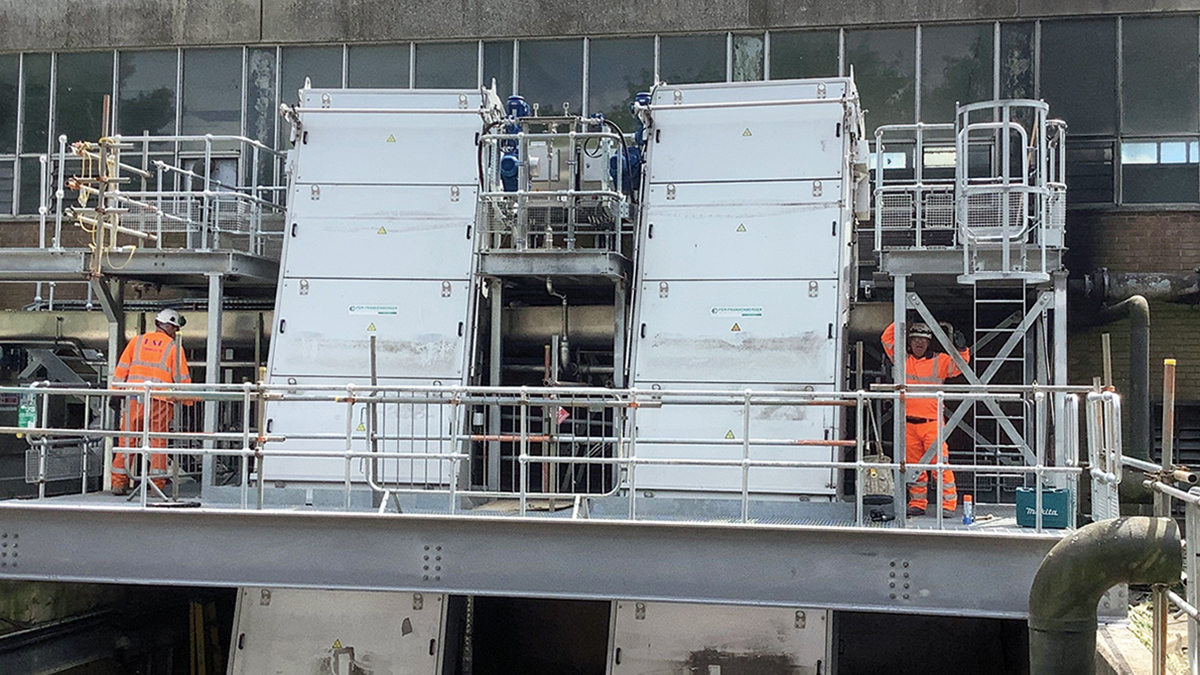
New inlet screens supplied by Hydro International UK Wastewater Services division – Courtesy of CMDP JV
Project scope for the Quality Driver
Ferric dosing
- 80m3 bulk storage facility comprising two 40m3 tanks in common bund.
- 3-point dosing facility.
- POA1Fe downstream of inlet flume.
- POA2Fe at two humus tank distribution chambers.
- POA3Fe at sand filter feed pumping station.
Alkalinity dosing
- 80m3 bulk storage facility comprising two 40m3 tanks in common bund.
- 2-point dosing facility.
- POA1alk filter distribution chamber.
- POA2alk humus tank outlet.
Tertiary Treatment
- Extend deep-bed sand filters by provision of additional three cells.
- Media top up of existing five cells.
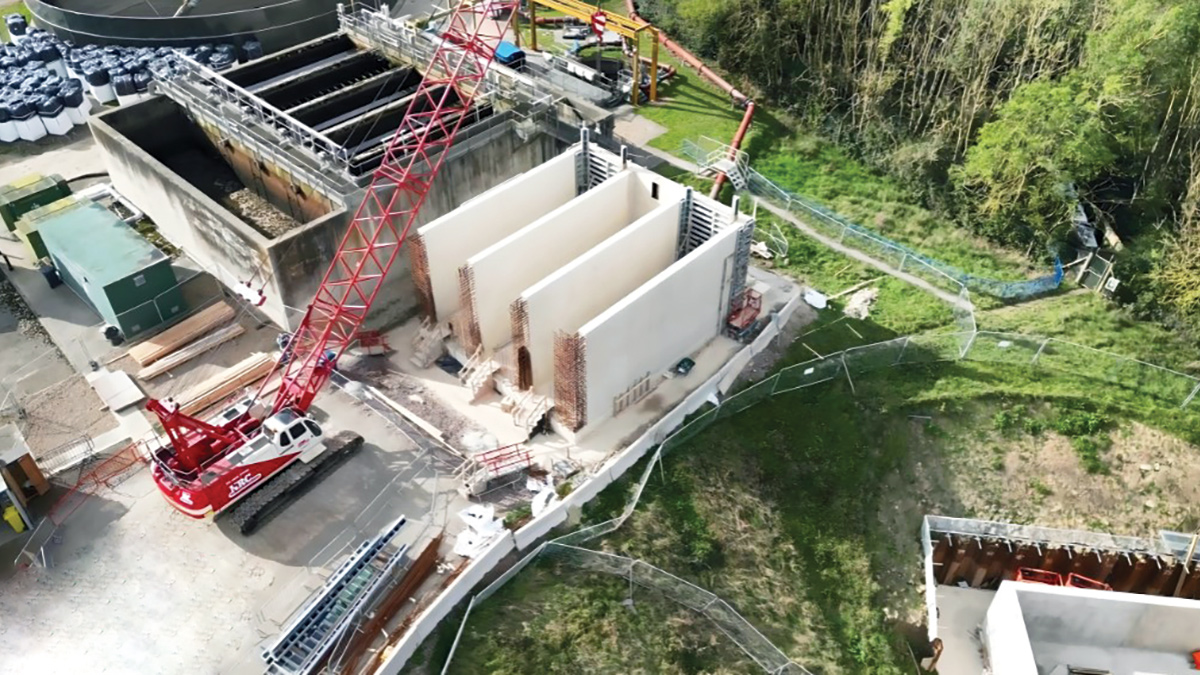
The existing deep bed sand filter is being extended with three additional cells to enhance the tertiary treatment process – Courtesy of CMDP JV
Project scope for the Capital Maintenance Driver
Inlet screens
- Replace inlet screens and screenings handling plant with larger capacity plant.
- Remove need for screenings conveyors by discharging directly to launder channel to feed screenings handling plant.
Storm pumping
- Replace two storm screw pumps (duty/assist).
- Convert pumps from diesel drives to electric drives.
- Provide an additional centrifugal storm pump to supplement screw pumps. Pumps to be configured duty/assist/assist.
Project scope for the Growth Driver
Re-configurate secondary treatment stage
- Convert the 2-stage biological filter process to single pass carbonaceous process.
New Moving Bed Biofilm Reactor (MBBR) nitrification process stage
- MBBR nitrification process stage comprising two GCS reactors, process media, process air system and associated infrastructure.
- Upgrade the ADF pumping station to intermediate/MBBR feed pumping station.
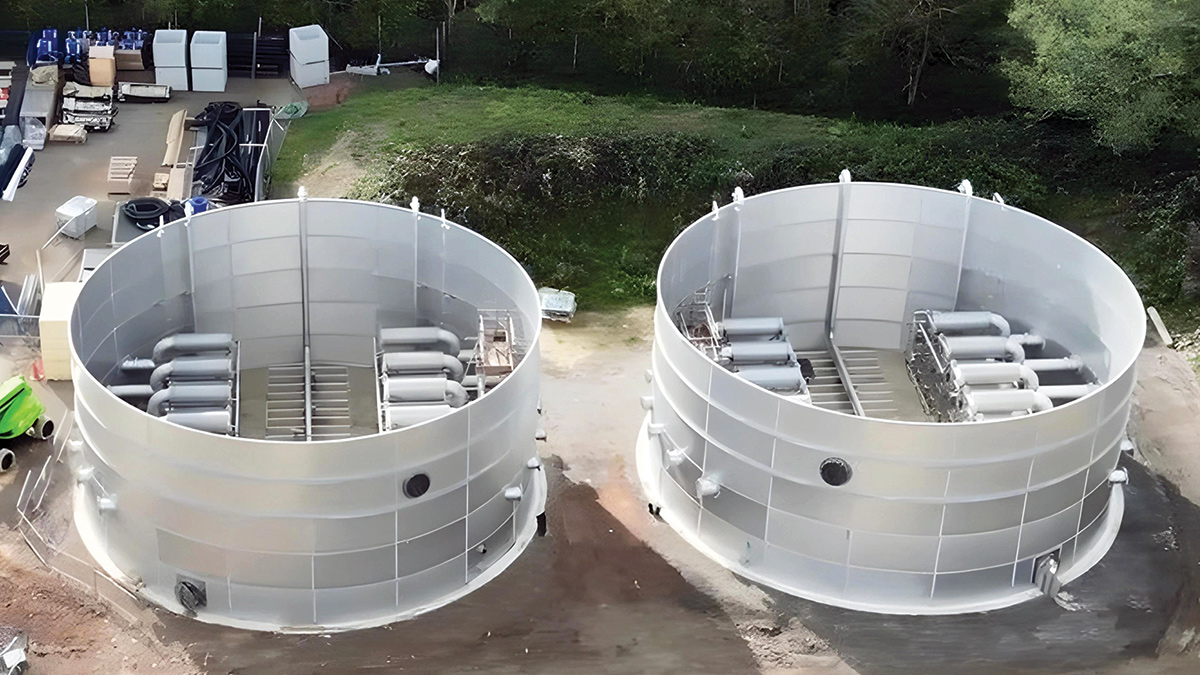
The two new Moving Bed Biofilm Reactors (MBBR) to remove ammonia from the final effluent returning to the River Arun – Courtesy of CMDP JV
Upgrade site HV infrastructure
- New DNO incoming supply including two RMUs.
- New high voltage assemblies (HVA1 & HVA2).
- New transformers (TX1 & TX2) and replace HV cable from mains incomer to TX2.
Upgrade site standby power infrastructure
- New 1250KVA standby generator to serve the inlet works and sludge treatment areas.
- New 500KVA standby generator to serve the MBBR and tertiary treatment areas.
Site SCADA & telemetry upgrade
Sludge treatment
- New dry solids sludge centrifuges and associated infrastructure.
- New ‘big bag’ polymer storage, make-up and dosing plant to serve centrifuges.
- Partial demolition of cake-bay building.
- Retain existing cake pump and sealed container facilities.
- Replace the odour control unit’s (OCU) motor control centre (MCC) with new combined LVA to facilitate location of new centrifuges.
- Make existing dewatering plant with sludge building redundant and make safe.
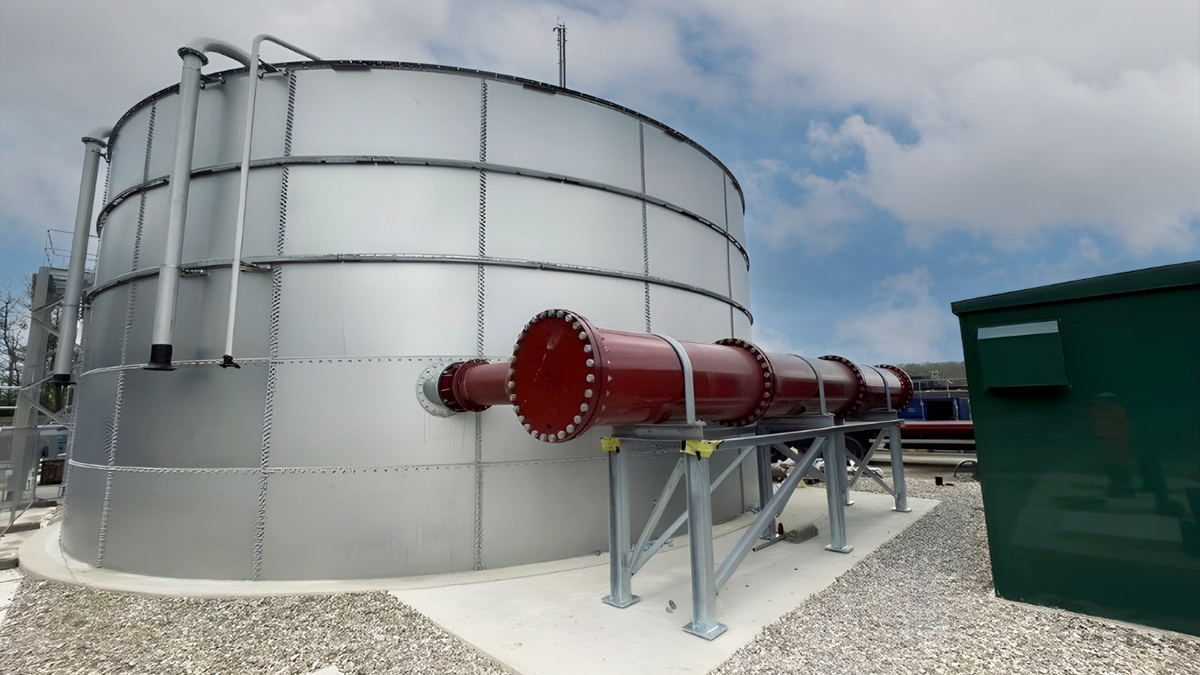
DN900 outlet pipework installed on one of the newly constructed MBBRs – Courtesy of CMDP JV
Horsham New WwTW: Supply chain – key participants
- Client: Southern Water
- Design & main contractor: CMDP JV
- Confined space rescue services: Rescue 2 Utilities Division
- Deep excavation & trench work: Rochester Utilities Ltd
- Formwork, reinforcement & concreting: McHugh Concrete
- Demolition contractor: John F Hunt Group
- Drilling & linestopping: Swan Pipelines
- Electrical installation: Field Systems Design Ltd
- Mechanical installation: R&B Engineering Ltd
- Inlet screens & screenings handling plant: M&N Electrical & Mechanical (Hydro International Ltd’s UK Wastewater Services Division)
- Moving bed biofilm reactors: Veolia Water Technologies
- MBBR blowers: Aerzen Machines
- Tertiary treatment plant: De Nora Water Technologies UK
- Chemical dosing plant: Bridges Electrical Engineers Ltd
- Polymer dosing plant: Richard Alan Engineering
- Centrifuges: GEA
- High voltage engineering works: Powersystems UK Ltd
- LV & HV switchgear services: Max Wright Ltd
- Transformer manufacturer: Wilson Power Solutions Ltd
- Critical power specialists: P&I Generators Ltd
- Progressive cavity pumps: NOV – Mono Pumps
- Submersible pumps: Xylem Water Solutions
- Below-ground DI pipework: Saint Gobain PAM UK
- Construction labour services: Hercules Site Services
- Construction labour services: NBC Group
Replacement inlet screens
The replacement of the existing 40 year old inlet screens was always going to be a significant milestone for the project and a very challenging operation. Before the new screens could be installed, which are needed to remove a vast amount of solid matter from the treatment process, the existing inlet channels were widened in places using a wire saw to provide additional room for the inclined toe of the new screens. The existing screens were electronically isolated and disconnected, along with an existing spiral conveyor, before being mechanically disconnected and removed.
This complex activity required specialist support from supply chain partners John F Hunt, FSD and R&B Engineering, to ensure a safe and successful operation.
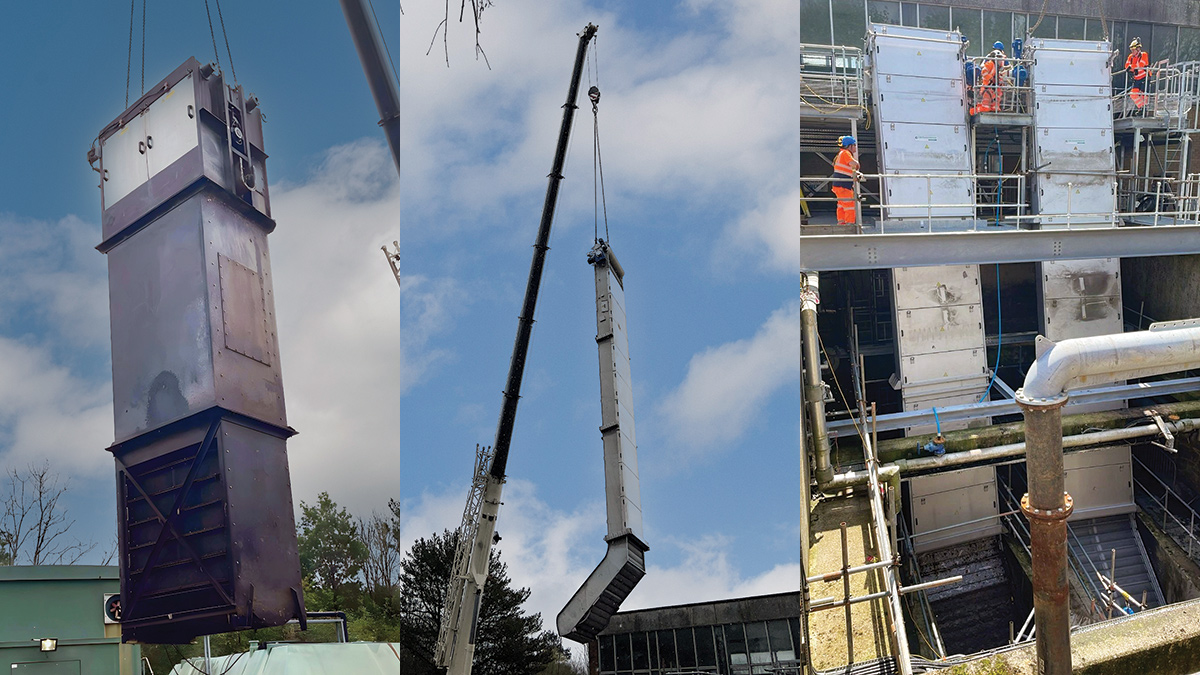
(left) One of the two existing inlet screens being removed, (middle) one of the new 12.8m long Alpha Beta Escalator Screens being lifted carefully into place, and (right) the new inlet screens installed – Courtesy of CMDP JV
Manufactured by FSM Frankenburger in Germany on behalf of M&N Electrical & Mechanical (Hydro International Ltd’s UK Wastewater Services division), the new state of the art inlet screens measure 12.8m in length and are among the largest Alpha Beta Escalator Screens not only in the UK, but in Europe. Accordingly, their installation required close collaboration between CMDP JV, Southern Water and all relevant supply chain partners.
With just over 10mm tolerance on either side, the new screens were successfully slotted into position within their concrete inlet channels. Pipework and cabling were installed before commissioning was completed.
Deep bed sand filter extension
As part of the project scope for the WFD quality driver, the tertiary treatment process has been enhanced by extending the existing deep bed sand filter. This has involved the construction of three extra cells, to complement the four cells already in situ.
Due to the ground conditions in this area of the site, piling was required to ensure the structural validity of the new cells, with a significant amount of temporary works required. At the time of writing (July 2024), the internal pipework has been completed and walkway platforms are in the process of being installed, with external pipework scheduled for completion at a later date.
Moving bed biofilm reactors (MBBR)
The addition of a new moving bed biofilm reactor (MBBR) nitrification process stage to the treatment process is a key element of the project, with the installation of two new reactors undertaken by Veolia Water Technologies. As part of the scope for the project’s growth driver, the new MBBR process introduces fixed film controllable biological treatment to the works’ capabilities.
Prior to the installation of the new MBBR reactors, a substantial amount of piling was required to ensure the stability of the ground in the area where they are now situated. Work is now underway to install the underground feed pipe that will serve the new reactors.
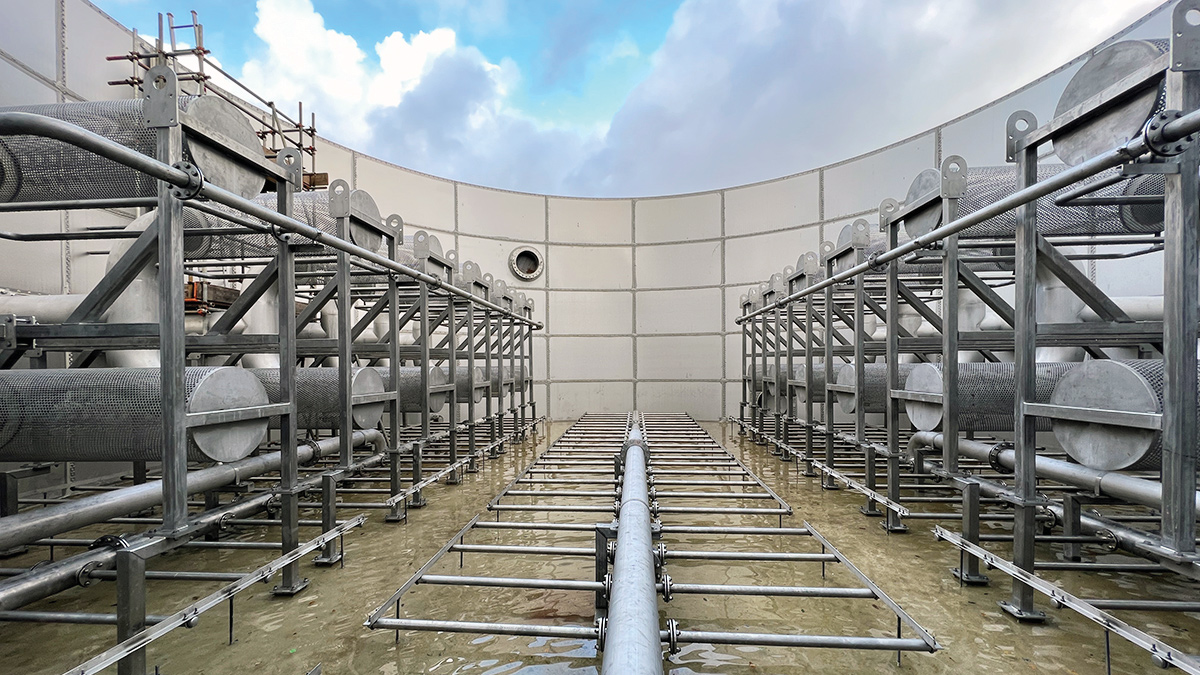
Inside one of the new MBBRs as its installation approached completion – Courtesy of CMDP JV
Alkalinity dosing
The scope for the project’s quality driver includes an enhancement to the works’ alkalinity dosing capability, with a new 80m3 bulk storage facility comprising of two 40m3 tanks in a common bund and two-point dosing facility at the carbonaceous filter’s distribution chamber and the humus tanks effluent chamber. This element of the project was led by MEICA specialist Bridges Ltd.
When the new tanks were being installed at the bottom of a sloped area of the site, concerns emerged around the stability of this a bank in the immediate vicinity. As a result, a decision was taken to sheet pile the bank, thus ensuring its stability.
The base of the area housing the new dosing equipment was also piled, prior to a concrete slab being poured. The existing dosing capability will remain in operation until the upgrade goes live, at which point it will be decommissioned.
Self-delivery success
A ‘self-delivery’ approach to construction was adopted, with CMDP JV directly contracting the various specialist sub-contractors required to deliver the project.
Through careful management by the site team, this approach has resulted in significant cost savings, through a reduction in the amount of non-productive time spent on site by the supply chain. This has been particularly beneficial due to the number of unchartered services unearthed on site that would have otherwise resulted in time delays.
A self-delivery approach has also allowed further savings through the avoidance of mark-up of goods and services that would have been imposed had CMDP handed control of management of the wider supply chain to a third party. This has also allowed CMDP to prioritise the use of local suppliers wherever possible.
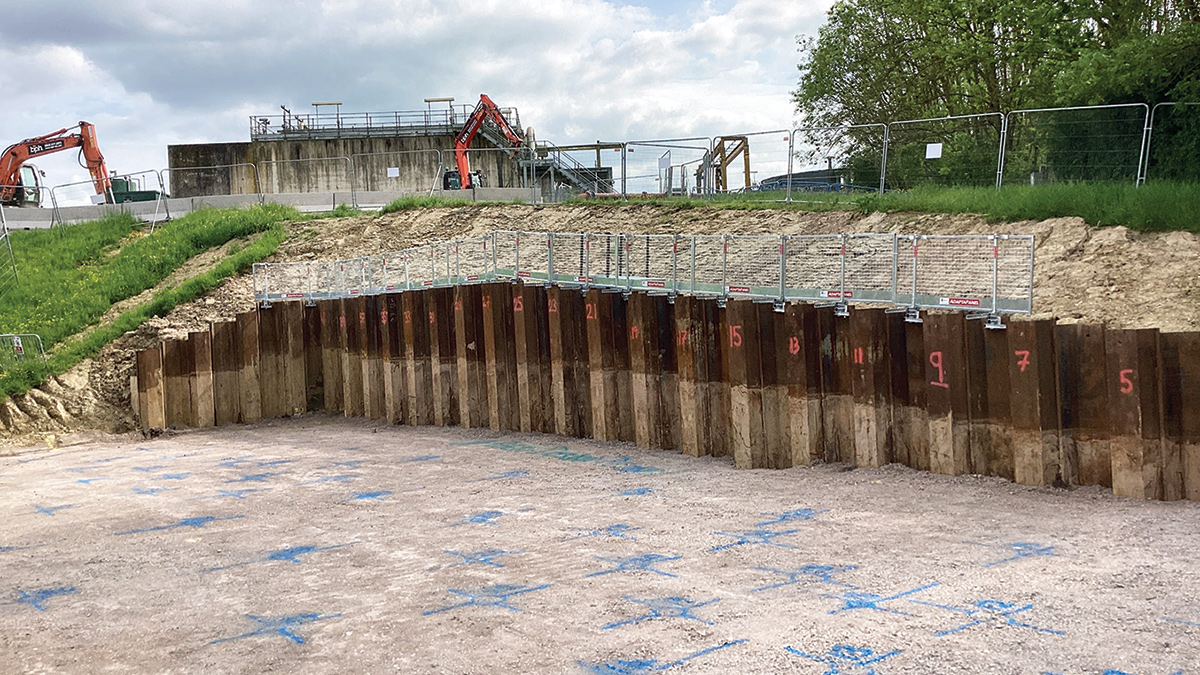
Setting out for piling works in alkalinity dosing area with sheet piling in place for bank stability – Courtesy of CMDP JV
Health & Safety
A significant challenge throughout the lifespan of the project has been the excess of buried and unchartered services on site. To control the high risks of excavation works, since the start of construction CMDP JV has issued a total of 182 “permits to dig”, with no service strikes recorded at the time of writing.
Another significant health and safety challenge faced by the project has been the fact that Horsham New WwTW serves as a Sussex area hub for four other Southern Water “Tier One” suppliers, resulting in a large amount of vehicle traffic on a constrained site.
Recognising that, proactive communication with all internal stakeholders has paid dividends, reducing delays to the project and disruption to other users of the site.
Environment
The project involves a combination of environmental mitigation and improvement, with landscaping and habitat enhancements on-site ensuring an overall 9% gain in biodiversity within the boundaries of the works.
To minimise any detrimental noise impact resulting from the operation of the upgraded works, the three blowers from Aerzen Machines that form part of the new MBBRs will have acoustic barriers installed. These barriers will ensure that any noise from the blowers, which form part of the process air system, will not impact the residential properties located closest to the works.
An opportunity to further minimise the environmental impact of the project has been possible through the use of local suppliers, as detailed further in the ‘Social Value’ section below.
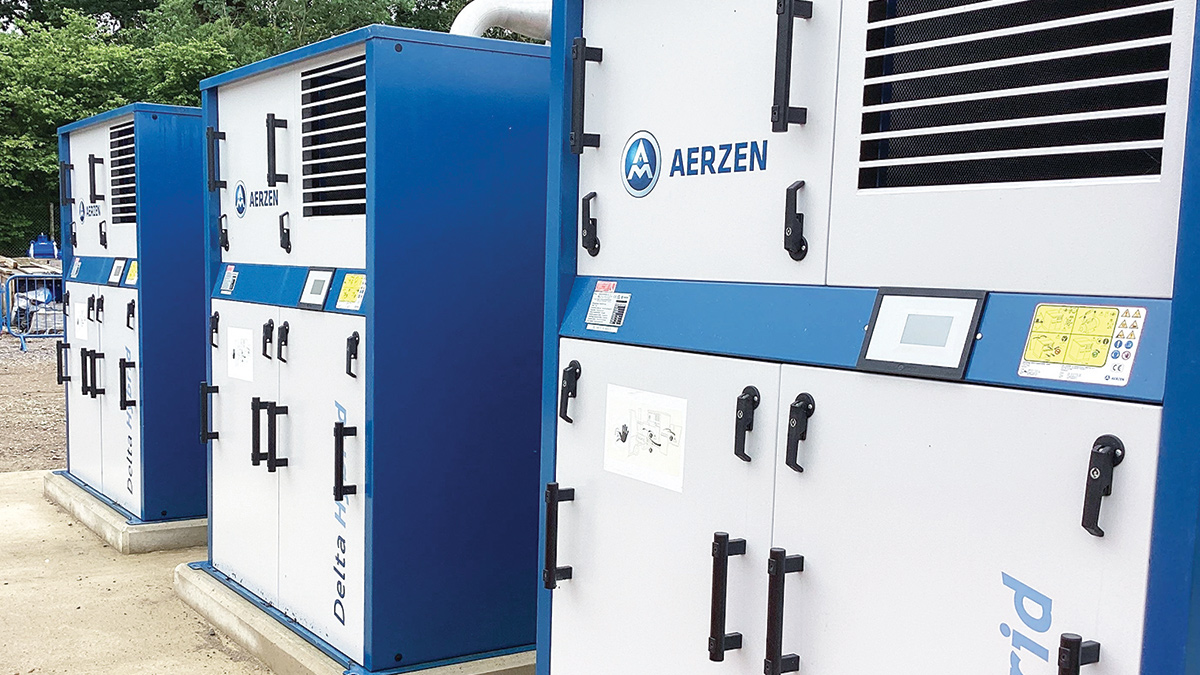
The new MBBR blowers are fitted with acoustic barriers to minimise any possible impact on nearby residential properties – Courtesy of CMDP JV
Award-winning site team
In line with the commitment shared by both Southern Water and CMDP to ensure a positive impact upon the communities they operate within, the efforts of the site team at Horsham New WwTW were recognised with a national award.
The Considerate Constructors Scheme (CCS) National Site Awards are one of the most prestigious accolades in the sector, highlighting those sites that have made the greatest contribution towards improving the image of construction. At a ceremony held in London, CMDP JV Construction Manager Garry Burgess was presented with a Bronze Award to recognise the efforts of the Horsham New team in terms of creating value in the local community and being respectful to the public, the workforce and the environment.
A customer-centric approach and focus on protecting and improving the environment has proved very successful for this project, with the site team achieving a top score of 45/45 (ranked as excellent) for three consecutive assessment visits.
Social value
With very few homes or businesses in the immediate vicinity of the works, the construction phase of the project has had negligible impact on the local community.
However, with the importance of ‘Social Value’ growing rapidly within the water industry, and Southern Water aspiring with the help and support of CMDP JV to improve the communities in which it operates, the project team partnered with Horsham District Council’s voluntary sector support team.
This has led to project staff regularly taking time away from the scheme to support local organisations in need of volunteers to help worthy causes in and around the town; ensuring the project delivers a long-term positive impact on the local community and wider area.
This approach has helped to make the project an exemplar for both companies in terms of the creation of long-term social value and furthers Southern Water goal of being a local company that cares.
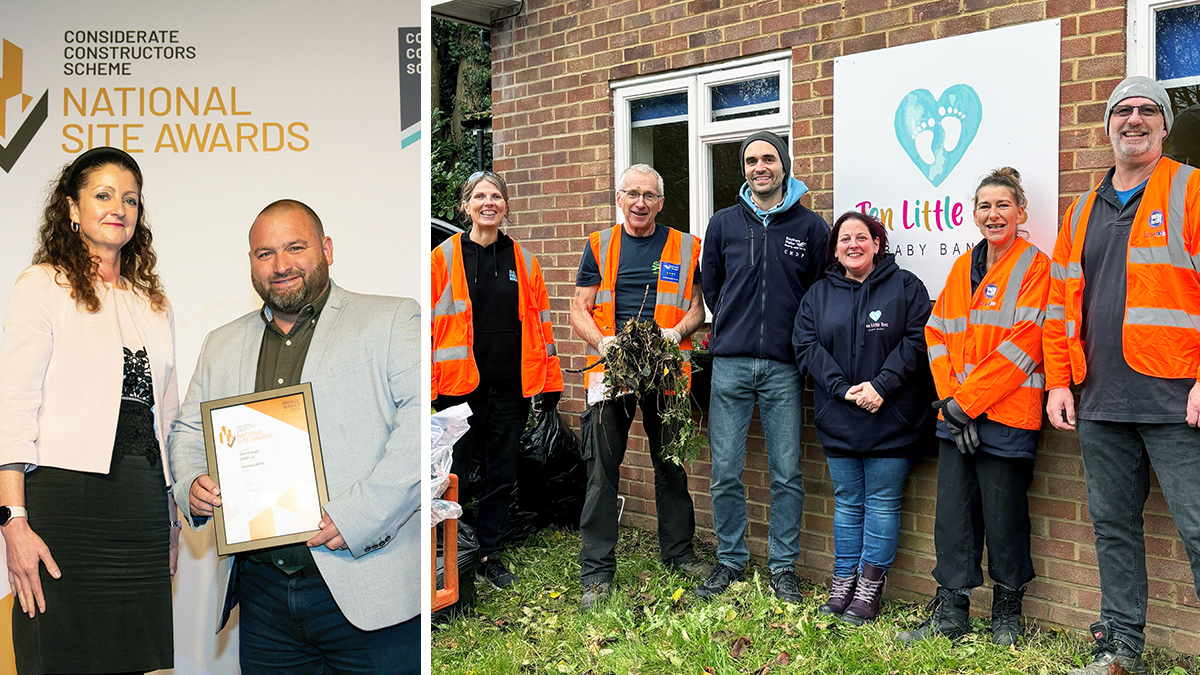
(left) Garry Burgess, CMDP Construction Manager, receiving the award for the efforts of the Horsham New WwTW team and (right) CMDP JV and Southern Water staff pictured volunteering to support local charity, Ten Little Toes – Courtesy of CMDP JV
As well as partnering, efforts have been prioritised in areas where a genuine need exists within the local community, and where the project team could employ their skills most effectively. The Social Value portal’s ‘Themes, Outcomes, Measures (TOM)’ system was used to measure and report the value of the wealth of social value activity undertaken by the project team, which includes:
- £2.4m spent on equipment and services with businesses within a 20-mile radius of the site, including £100,000 spent with businesses located within five miles of the works. This has helped to reduce the project’s carbon footprint and sustain the local economy.
- Joint collection for a local charity supporting families and parents in crisis and/or facing difficult circumstances throughout West Sussex.
- 49 staff hours dedicated to local school and college visits.
- 65 weeks of apprenticeships spent on the project.
- Over 100 hours spent by project staff volunteering to support local community projects.
- In total, the project has made over £3,000 worth of donations and in-kind contributions to local community projects.
Use of the ‘Themes, Outcomes, Measures’ system allows the project team to track success and ensure momentum, which in term will help to set a benchmark for the social value element of future projects.
With strong relationships established with a wide range of local organisations and key stakeholders, the figures listed above will continue to grow as the project progresses towards its scheduled completion in 2025.
Conclusion
The complex upgrade of Horsham New WwTW involved the installation of a range of new hi-tech machinery; including two of the largest Alpha Beta Escalator Inlet Screens in Europe.
CMDP JV’s self-delivery approach has provided added flexibility and numerous benefits, and a keen focus on social value will ensure a long-lasting positive impact beyond the scope of the project itself.
Once complete, the upgraded works will be equipped to cater for the significant growth forecast within the Horsham catchment and surrounding areas over the next ten years. It will increase the quality of the treated water being returned to the River Arun and ensure Southern Water fulfils its regulatory requirements.
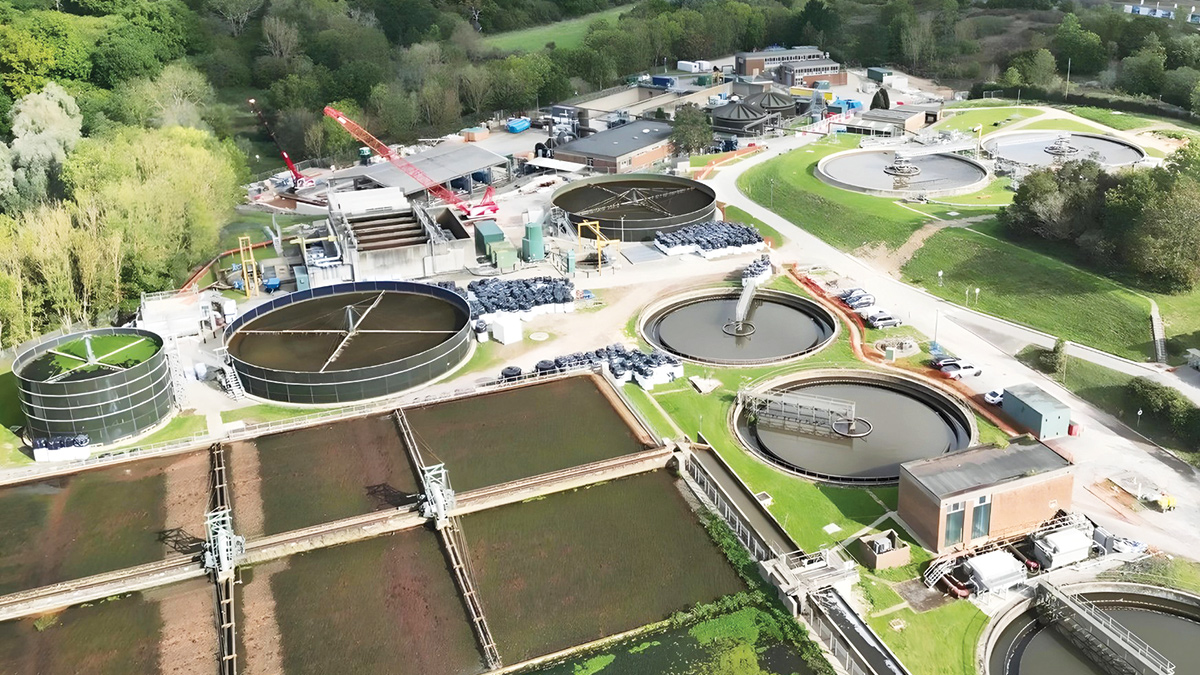
The upgrade of Horsham New WwTW will allow for an expected increase in the local population up to 2035. It also caters for the transfer of flows from three catchment treatment works at Mannings Heath, Warnham and Faygate - Courtesy of CMDP JV