Southern Water Maintenance Transformation (2024)
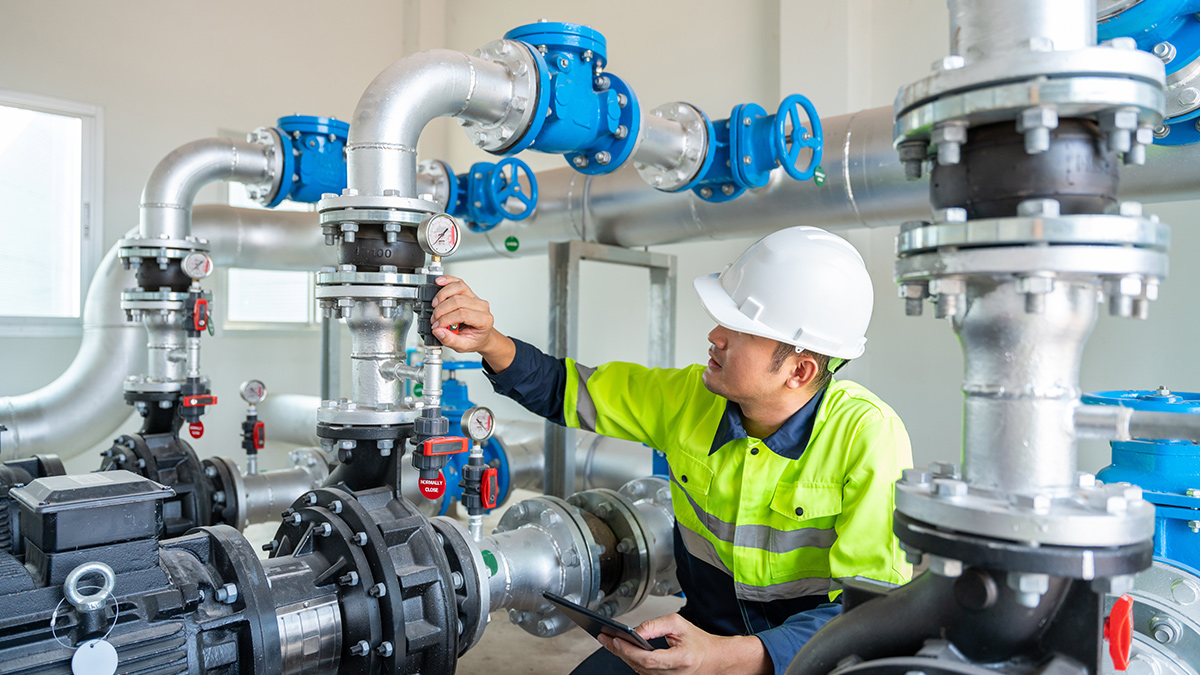
Understanding asset health issues is key to improving environmental performance
The challenge to improve environmental performance is common and topical across the industry, and Southern Water are no different; with considerable effort and headway being made to reduce said impact. A major transformational project is underway business-wide, which sees them moving from a reactive state to one that is more planned and proactive through the adoption of maintenance and reliability best practices. This case study sets out their challenges and how they have been tackled, including how they, in collaboration with consulting partners Binnies, embraced technology to provide an immersive and engaging training course to help embed the new ways of working with their field teams.
Problem statement
Southern Water historically relied on reactive responses to maintenance issues, with day-to-day operations being driven by asset failure – approximately 70% of maintenance activities were reactive. Naturally, working this way impacts an organisations resilience for dealing with asset failures, meaning the impact is greater as an urgent response is required. Uncontrolled breakdowns often result in unconsented pollution events, water quality breaches, and loss of supply events, all of which attract financial penalties, and increased pressure from regulators and their customers for improved performance.
Some of the challenges which Southern Water wanted to resolve included a lack of accurate asset data, low completion rates of preventative maintenance activities, and the suitability of those tasks, combined with an overall concern about the approach to asset health.
Project overview
The Planned Maintenance Project was developed to address maintenance challenges, focussed on improving asset health and reliability, and shifting the organisational culture. The project was designed to provide a refreshed operational maintenance strategy based on outputs from Failure Modes Effects & Criticality Analysis (FMECA), which would then be used to develop Standard Operating Procedures (SOPs) to provide a clear methodology for operators to follow. Additionally, operational staff needed to be trained on the new ways of working, so everyone impacted understood what was changing, why it was changing, and what it meant for them. Asset Management professionals will be aware of the P-F curve; the aim of the project was to get Southern Water on the journey to moving further up the curve, equipping them to easily identify asset health issues, and generate the required corrective actions to avoid a failure. The project was designed to ensure it was paced appropriately. Too many change initiatives become too big too quickly, and ultimately fail. The first step of this process wasn’t to get the teams working with predictive technology, CBM, or Machine Learning. Instead, the aim was to equip them to start utilising human senses, carrying out standardised and consistent inspections to recognise the early signs of asset deterioration and act appropriately in a planned manner.
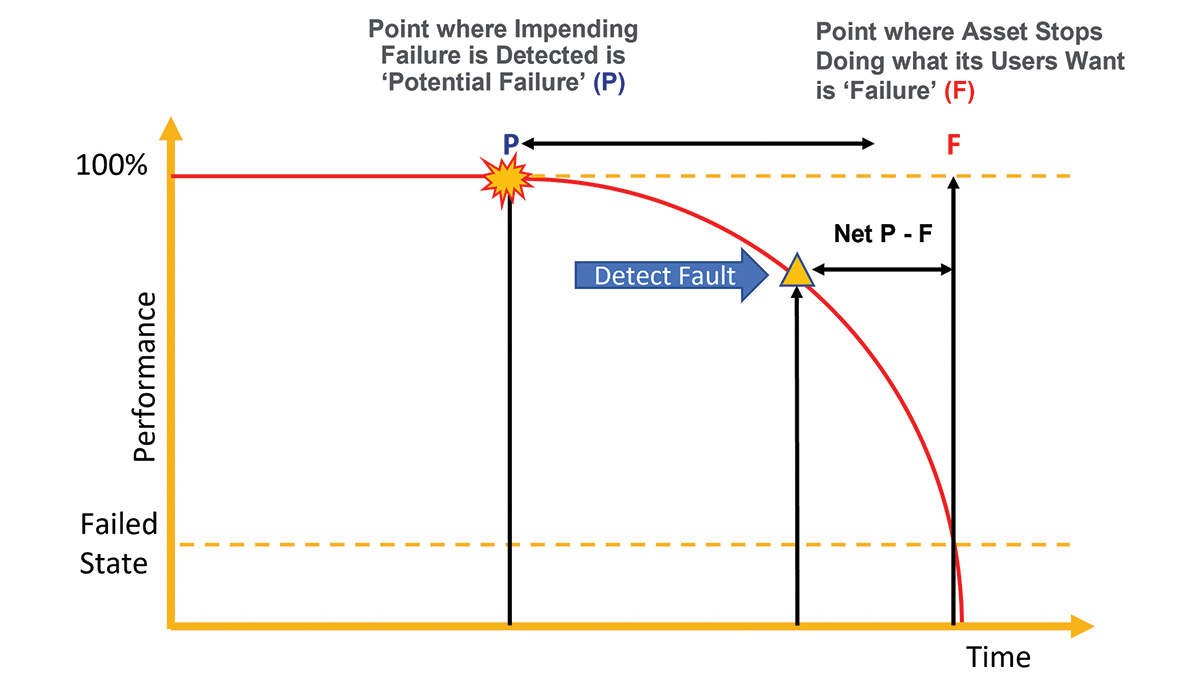
Image showing P-F failure curve – Courtesy of Binnies
The original scope was focused on addressing the root cause of some of their largest financial penalties. This included 100 of the most critical wastewater pumping stations in the business, where sites had a history of pollution events or posed a significant risk to the environment or local community should there be a spill event. During the early stages of the project, Southern Water reviewed the business case and realised that expanding the scope was the right thing to do. This drove business-wide improvements and a consistent way of working, resulting in the scope being extended to cover the entirety of the Southern Water Operational estate.
Project deliverables
Asset register review: An effective maintenance programme requires an accurate asset register. Before any follow-on activities could be completed, Binnies were tasked with completing asset data capture surveys of the original 100 in-scope sites. The surveys captured all required asset attributes, plus a baseline condition report. Additionally, 3D photogrammetry was completed to create a digital twin model of the sites. The project led to 100,000 assets being surveyed, where the teams identified an additional 25% uplift in unregistered assets and corrected a 40% error margin in the data. This exercise put Southern Water in the best possible position for the next stages of the project. Companies struggle to accurately operate and maintain their equipment if they don’t know it exists, or the information held for it is incorrect.
Failure modes effects & criticality analysis: With the asset surveys complete, the next stage was to create network maps of the processes, which are used by field teams to support new starters and improve site familiarity. Within Binnies, the maps were used as part of the FMECA process as a guide to ensure all asset types within a process or site are captured within the analysis. The maps and FMECA were done on either a generic basis where common configurations had been identified, or site-specific/bespoke for higher criticality sites or those with a unique configuration.
Standard operating procedures: Completion of the FMECA exercise provided the maintenance task lists needed for each asset. The next stage was to use the tasks to populate the Standard Operating Procedures (SOPs) documents. Historically, teams would pass on their knowledge based on what they had been shown by their predecessors, or through their own understanding of a task instruction. Naturally, this brings inconsistencies with task completion, and the risk of misinterpretation. These documents provide operations with a clear set of job instructions to ensure tasks are completed consistently. Like the FMECA process, the SOPs were site-specific where needed, but used the common configurations allowing Binnies to produce templated documents in high volumes.
Through FMECA and the creation of Network Maps and SOPs, Southern Water gained over 20,000 operational documents which provided a standardised way of working and promoted asset health and reliability.
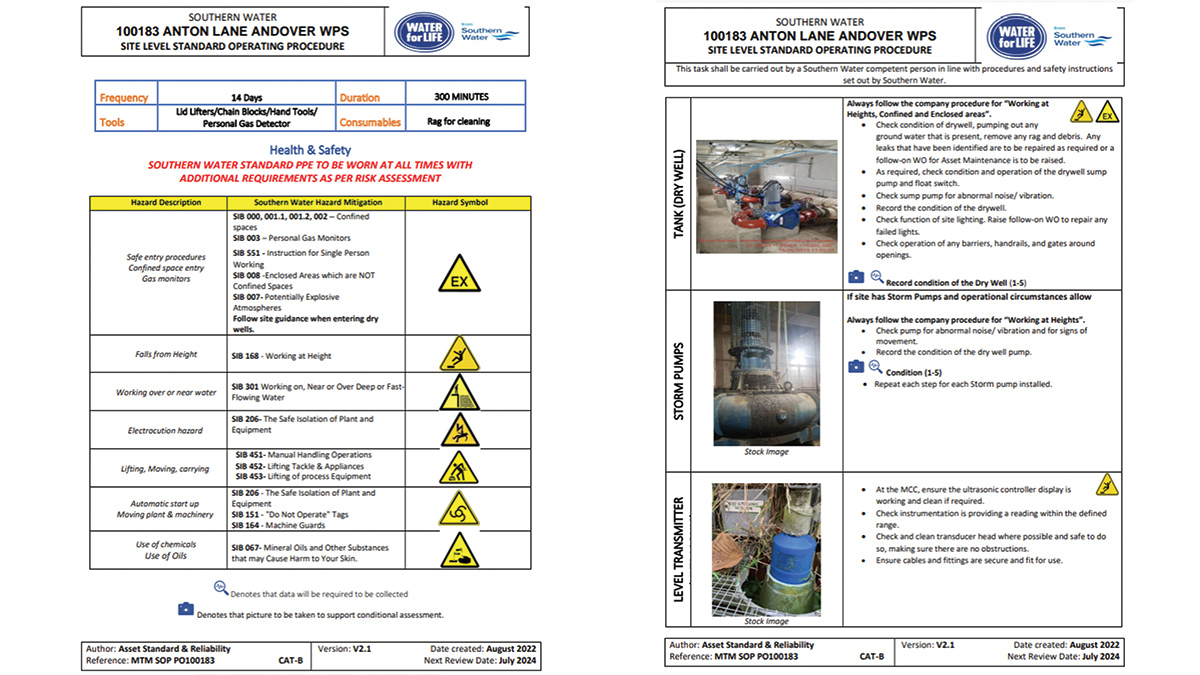
Image showing example of Standard Operating Procedures – Courtesy of Binnies
Dynamic risk model: To help support the internal deployment of effective, executable maintenance tasks, Binnies developed a Dynamic Risk Model for Southern Water. Understanding that risk is dynamic and not fixed, the model was developed to allow Southern Water to manage their assets based on real-time condition, understanding that time-based maintenance is not always the best solution. The model looked at fixed criticality but also took into consideration real time operating characteristics, telemetry data, and the condition data the field teams were submitting. The model was set up to enable Southern Water to schedule the right maintenance to the right assets, at the right time.
Project embedment
The final stages of the project involved training operational staff on the new tools and technology being implemented, and on-site embedment checks with the field teams to ensure the classroom learning could be applied in the operational environment. The course was designed to be interactive and immersive, reducing the passive learning time to promote engagement and interaction to ensure the operational teams were engaged throughout the sessions. The team designed a training programme which focussed around the newly created digital scans of the Southern Water sites. These scans were used to house the training content, in which the delegates were taken on a virtual tour of their sites. The course contained all key business messages along with foundational asset management knowledge to provide delegates with all of the information they need to understand what changes were being implemented, why the changes were needed, and what it meant in terms of new tools, and new ways of working. The second half of the training course was set up so the delegates could experience the practical requirements of the learning through using the 3D technology. Training scenarios were built into the models; these scenarios contained the job instructions from the SOPs, and a description of what was found when completing the inspection. The delegates discussed the consequence of the asset failing, and what the appropriate corrective action should be.
Following the classroom training, a 6-month Early Life Support (ELS) team was stood up to provide one-to-one coaching and assurance checks with the field teams to confirm they were able to put the classroom learning into action in the operational environment.
The training provided 67 face-to-face sessions, training over 500 of the Southern Water operational workforce. Additionally an eLearning course was created to be added to the Southern Water learning system. This was to be used for new starters and for anyone who needed refresher training following the ELS programme. The training received outstanding feedback from those trained. The trainers fed back to the project team that throughout the entire training deployment delegates remained highly engaged, and the use of 3D models promoted conversation in the room. Many of the delegates were familiar with the sites used to model the training which enabled them to discuss some of the issues they faced providing additional insight for the groups being trained. A temperature check was completed to gauge the delegates’ confidence in the new ways of working landing successfully, this scored 84%.
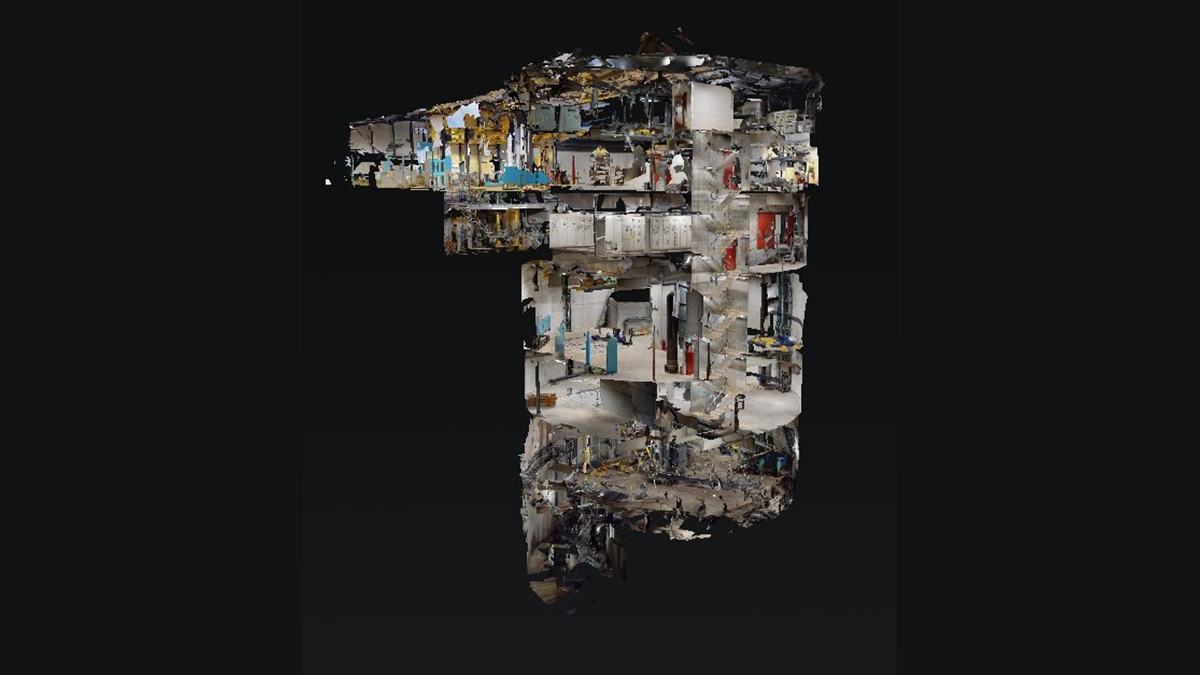
Screen grab of 3D training model – Courtesy of Binnies
Next steps
To further support the embedment of the new ways of working, and to overcome some of the data challenges being faced by Southern Water, the company are currently in the process of implementing a new Enterprise Asset Management System, IBM Maximo.
This platform will provide an integrated solution to data management, ensuring all key information is stored in one system, breaking down some of the barriers they had previously experienced with data management. It will enable the field teams to effectively capture and feedback asset condition data and support central teams in monitoring and trending the information in parallel with the dynamic risk model, to ensure risk management is optimised and corrective actions driven at the right time.
The deployment of the system will be carried out in a phased approach, with the first pilot deployment due to go live on the Isle of Wight in July 2024.
Southern Water and Binnies continue to work closely together, with the asset data capture surveys now being deployed across the entire water supply estate to increase the baseline asset information standard. Additionally, Southern Water are investing further in their staff by increasing their problem-solving capability through the completion of Root Cause Analysis training provided by Binnies specialist trainers.
For Southern Water, proactive maintenance is not the end state, it is very much the start of an exciting journey.