Broadholme WRC (2024)
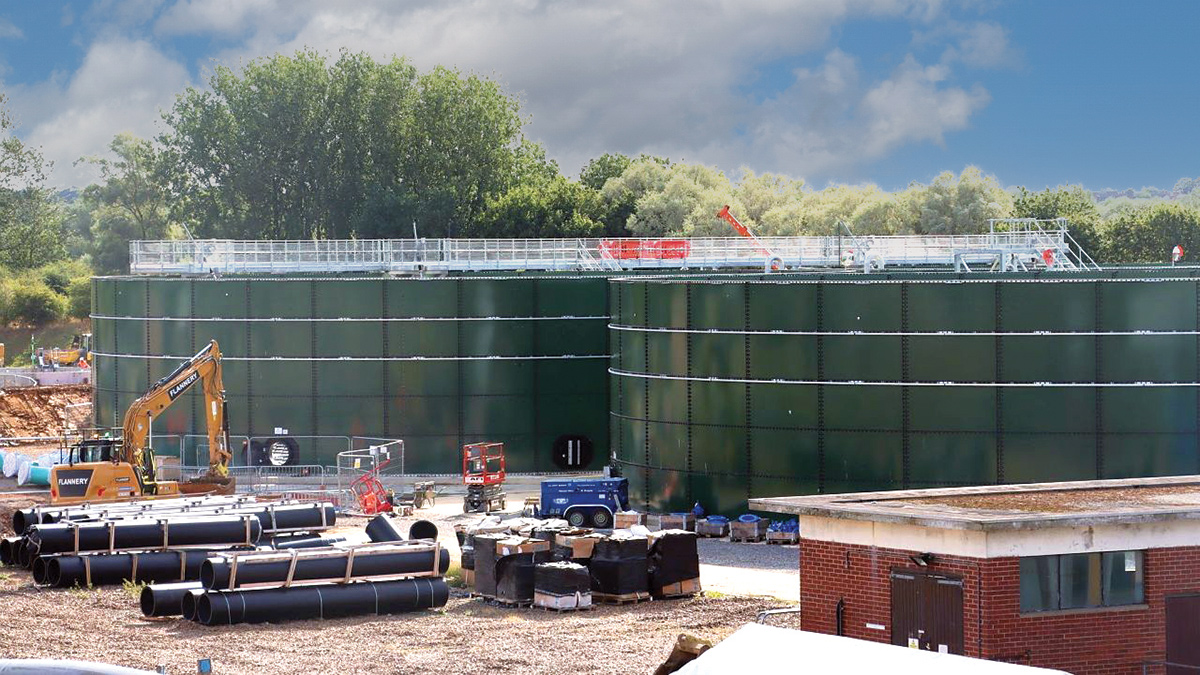
SBR tanks - Courtesy of @one Alliance
Broadholme Water Recycling Centre (WRC) is located off the A45 near the Rushden Lakes Shopping Centre in north Northamptonshire and provides water recycling capability across the Rushden, Wellingborough and Irthlingborough areas. There are multiple large lakes in the area, all fed by the River Nene including the Nene Wetlands Nature Reserve and a Site of Special Scientific Interest (SSSI) Water Reserve in close proximity to the recycling centre. The works was showing signs of beginning to struggle with the increased demand and this was cemented by a change in the Environment Agency (EA) requirements for the site when it came to its full flow to treatment (FFT) and phosphorus removal capacity.
Background
Broadholme WRC is a well-established operational site which treats wastewater from Wellingborough and surrounding catchment areas before returning it safely to the environment. Prior to the project starting, it had a treatment capacity of 233,533 population equivalent (PE). As with all water companies, Anglian Water carries out a range of works across its sites to ensure that it can continue to meet the needs of the local area as it continues to expand and to both improve and protect water quality in line with regulatory requirements as part of the Water Industry National Environment Programme (WINEP).
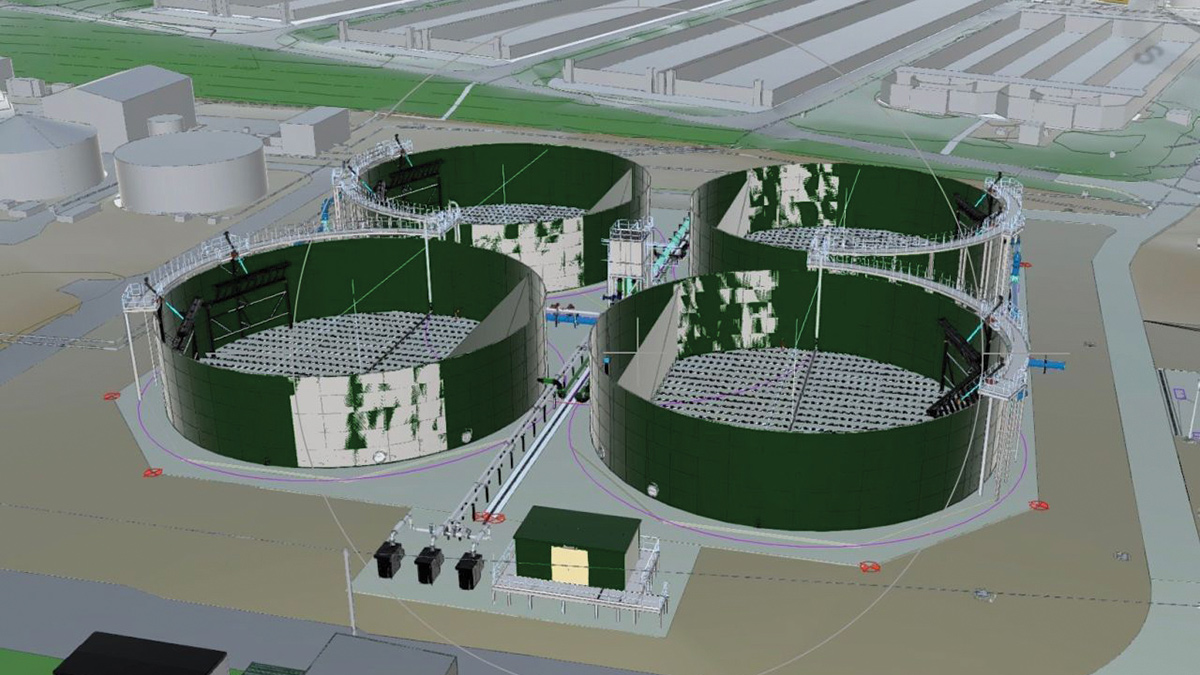
Overview model – Courtesy of @one Alliance
According to the 2021 census data the population the United Kingdom has increased by 6.3% since 2011, however the East of England has seen the highest levels of population growth per region at 8.3%. Both these figures are low in comparison to the level of growth in north Northamptonshire which has seen the population increase by 13.4% since 2011 to now over 400,000 residents.
To meet the new EA requirements in time for the site’s obligation date in March 2025, Anglian Water handed the design and construction of this scheme to its in-house capital delivery vehicle the Anglian Water @one Alliance as part of its AMP7 portfolio.
The Alliance is formed of eight partner organisations including Anglian Water, Balfour Beatty, Barhale, Binnies, Mott MacDonald Bentley, MWH Treatment, Skanska and Sweco. Each partner brings its own specialisation to the Alliance, which allows @one to efficiently deliver large capital delivery projects included in its £1.2bn AMP7 portfolio.
Project delivery
The site team, led by the principal contractor Mott MacDonald Bentley are delivering the Broadholme Water Recyling Centre project which is currently valued at £35m, making it the largest combined scheme that the Anglian Water @one Alliance has delivered in AMP7.
Broadholme WRC: Supply chain – key participants
- Principal contractor & designer: @one Alliance
- In situ soil stabilisation: SMR (UK) Ltd
- Sequential batch reactor: Xylem Water Solutions
- Pile cloth filter: FLI Water Ltd
- Power upgrade: Power Testing Limited
- Glass-coated steel tanks: Hayes GFS Ltd
- MEICA package: TES Group Ltd
- Chemical storage & dosing: Lintott Control Systems Ltd
- Access walkways: Steelway
- Lifting equipment: Cadman Cranes Ltd
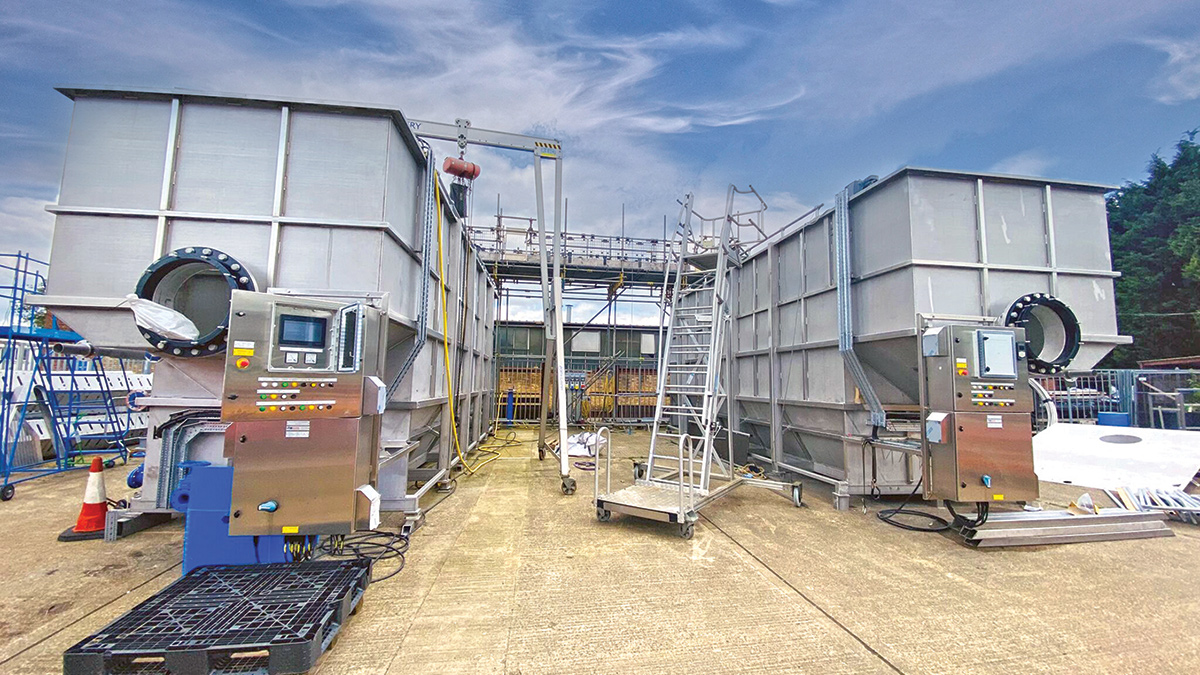
Phosphorous removal scheme – Courtesy of @one Alliance
Solution
With the site facing new EA requirements for growth, full flow to treatment (FFT) and phosphorus removal, the @one design team was required to create a solution that would work together to achieve all of these obligations and come up with a cohesive solution that could increase the sites dry weather flow (DWF) by increasing the FFT capacity to a level that would ensure the WRC does not spill to storm in dry weather and that the contents of the storm tank are able to be returned for treatment as soon as is reasonably possible.
Failure to meet the new FFT and phosphorus consent could create a significant pollution risk for the scheme under significant inclement weather conditions.
Utilising modern design principles, the team made use of 3D modelling software to create a virtual 3D map of the site and the planned works which could be viewed in virtual reality (VR). This was to allow the designers and engineering teams to virtually view the scheme together, as it was being designed to ensure the required additions to the WRC could be transplanted in as easily as possible given the limited amount of space available on the existing site.
The final design for the scheme was to install four new sequential batch reactor (SBR) tanks from Xylem Water Solutions to allow for the increase in FFT capable of providing 413 l/s of additional capacity alongside a 60m3 ferrous dosing package to provide additional phosphorus removal.
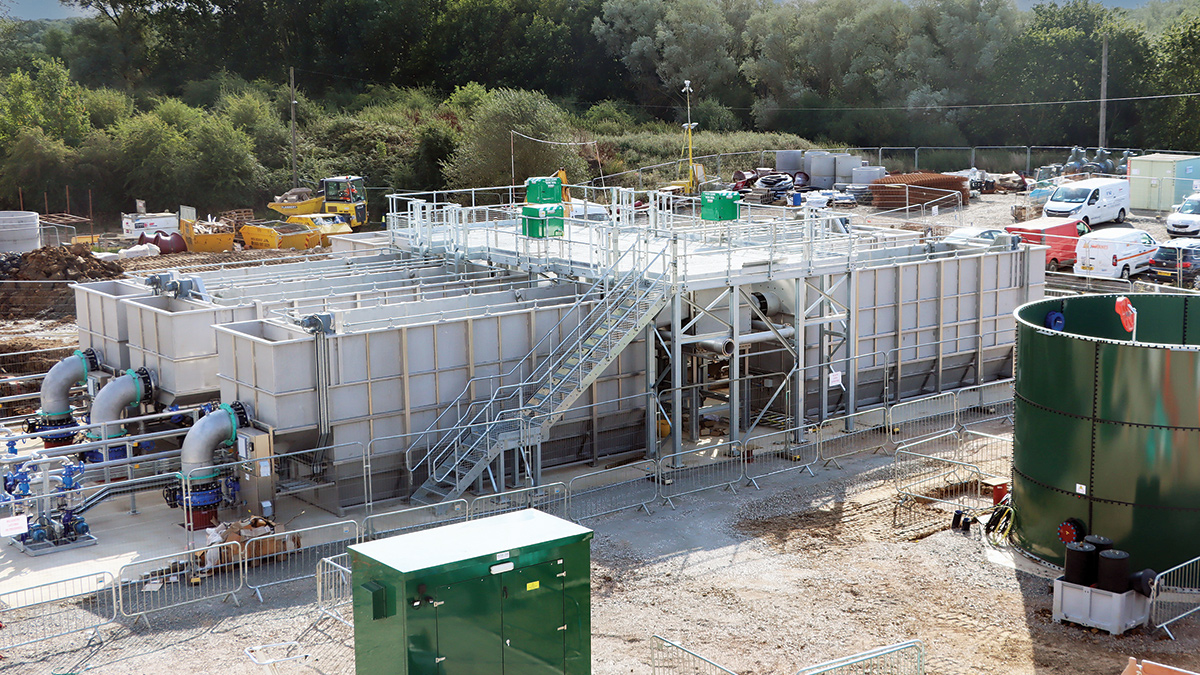
Phosphorous removal scheme – Courtesy of @one Alliance
To accommodate the power needs of the new assets, the existing power supply was upgraded, and a new transformer was provided on-site. A standby generator and fuel tank has also been added to run critical plant in event of a power outage.
The team then began work on the concrete base for the SBR tanks creating a 75m x 75m base slab which included drainage channels, before laying another four raised 35m diameter concrete plinths for the tanks to sit on; based on the redundant space our team had dug up of the old beds. These concrete pours created a logistical challenge for the team as each of the four plinths needed over 570m3 of concrete which required over 75 mixers worth of concrete coming back and forward into the site per plinth along a narrow access road.
Alongside the SBR plinths, the team also built a new motor control center (MCC) plinth, blower plinth and ferrous dosing plinth, alongside steelwork for the new MCC, blower platform and pipework.
The tanks were each built by Hayes GFS Ltd from the top down by creating each ring at ground level before using hydraulic jacks to lift the ring into the air creating space underneath for the next ring to begin its installation.
This method created a safer working environment for the installation team by removing any requirement to work from height. Once constructed each SBR tank will be five rings high reaching 7m in height with a 35m diameter.
During the installation of the tanks the team also had supplier Steelway on site building walkways around the outlet side of the tanks to allow for site access.
In order to feed the new SBR tanks the team had to lay a new 310m, 710mm diameter high-density polyethylene (HDPE) crude sewage pipe which runs alongside an existing inclined access road frequently used by Anglian Water tankers. This new pipe, once fusion welded into place, connects the existing Inlet Works Number 2 to the new SBR tanks via the new common distribution chamber.
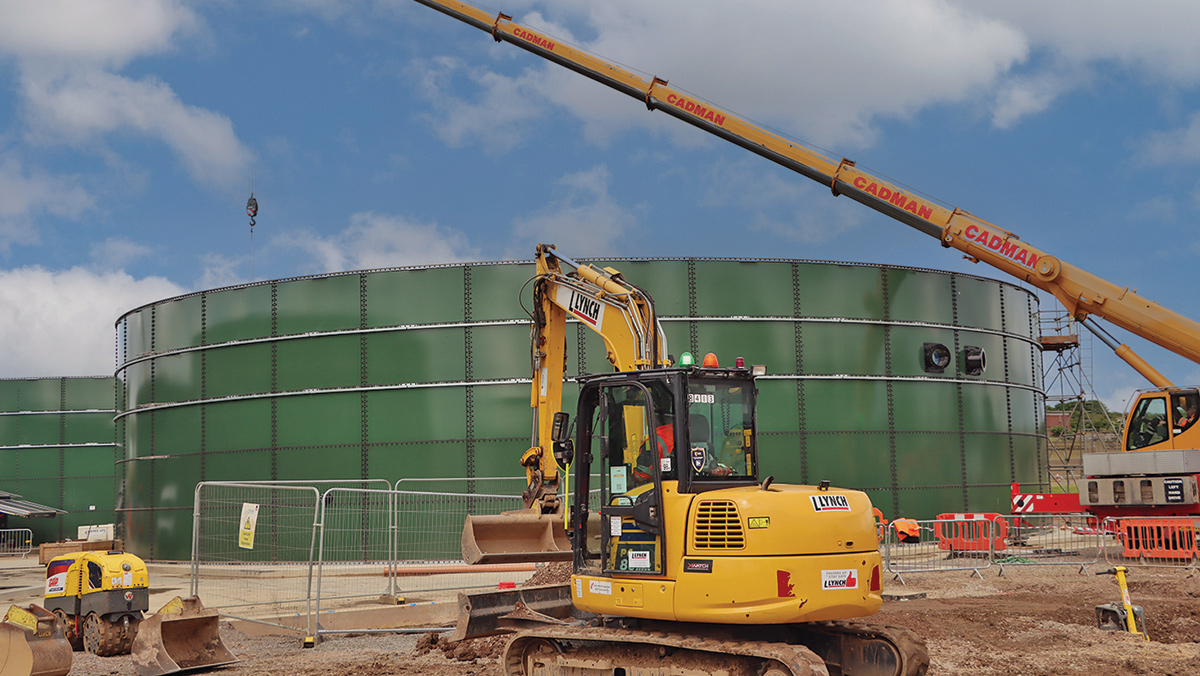
One of the new SBR tanks – Courtesy of @one Alliance
Challenges
With the scheme being the largest scheme in terms of financial investment of Anglian Water’s AMP7 programme, it comes with its own challenges.
Broadholme WRC sits within/adjacent several designations (eg Ramsar, SPA) resulting in the need for screening opinion, and possibility of EIA, for the whole scheme. Extensive surveys and assessments were needed as part of the screening process taking over ten months. This in turn affected start on site reducing the construction window ahead of the obligation date.
During construction, we also encountered some challenges. With several components of the phosphorus cloth filter and SBR tanks coming from overseas, shipping coincided with the start of issues in the Red Sea, so re-routing of components added some delays to the expected programme of work.
Also, during the installation of this scheme, the project team have had to deal with extremely poor weather conditions due to extensive rainfall during the Winter of 2023 and much of 2024, which impacted the delivery of the civils works. Due to increased demand for resources across the country, lead times at pre-commencement have been increased which therefore hindered our programme dates; particularly affecting the MCCs and large diameter valves and pipes.
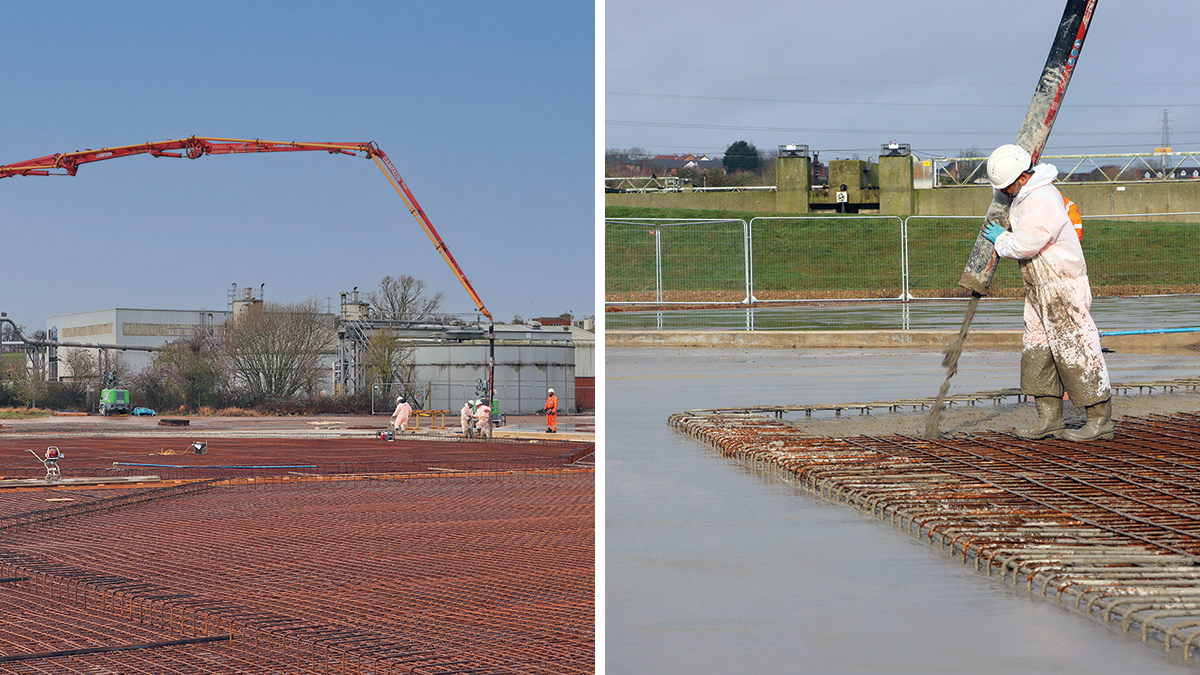
(left) Preparing for concrete pours and (right) concrete pours – Courtesy of @one Alliance
As part of this scheme, the team is completing the renewal of the access road into Broadholme WRC, which includes over 1km, split into tarmac and concreting for Anglian Water personnel. These works are being completed overnight to maintain tanker access as the road does not have enough width to shut half the carriageway while leaving enough space for safe access.
Progress
At the time of writing in September 2024, the four SBR tanks have been successfully installed and the team are working hard to complete the phosphorus and growth elements prior to the obligation date for the completion of the works.
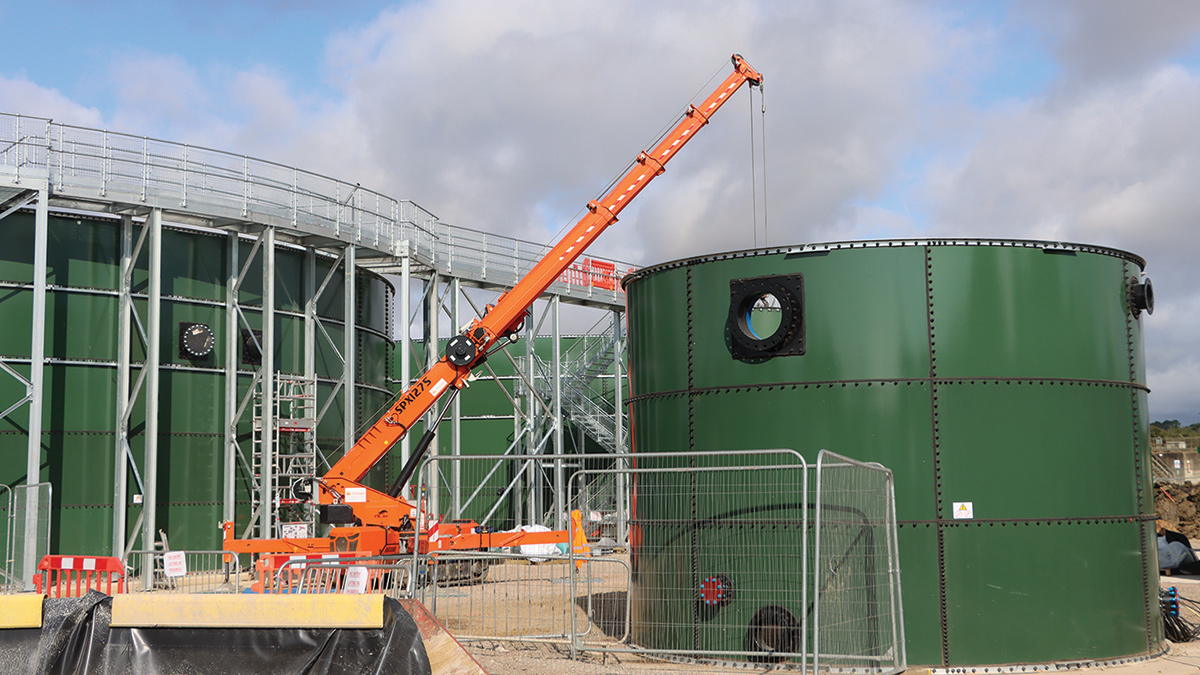
Construction of the SBR tanks - Courtesy of @one Alliance
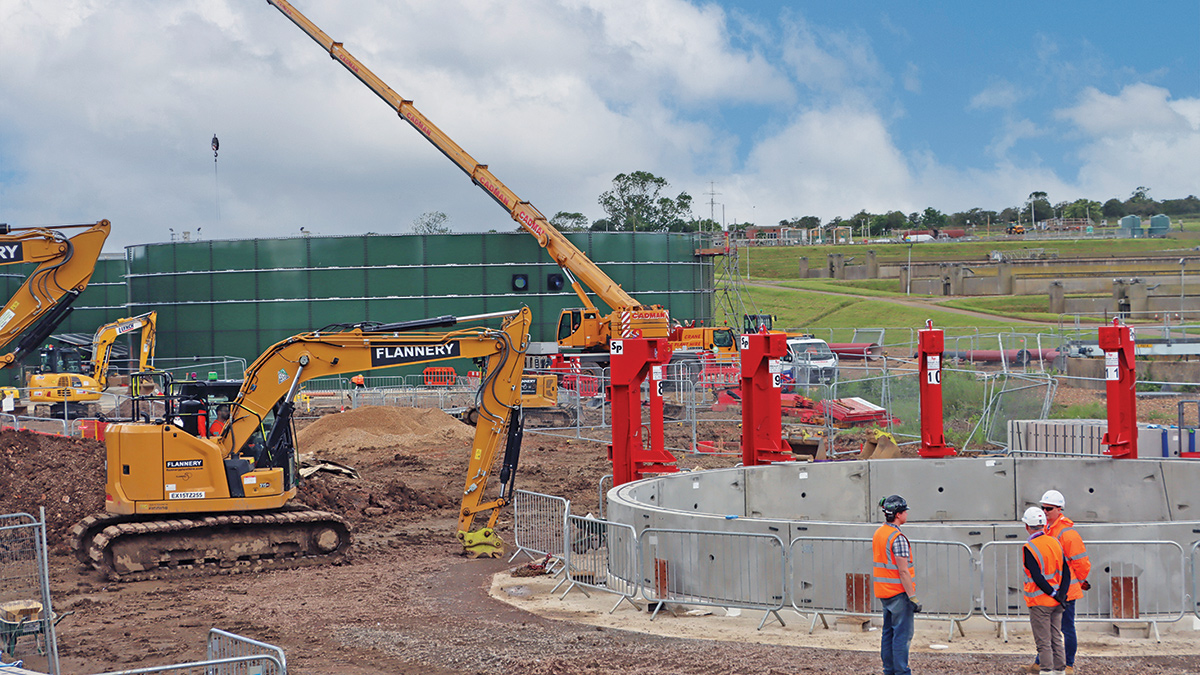
Elements of the growth scheme - Courtesy of @one Alliance