Chorley WwTW (2018)
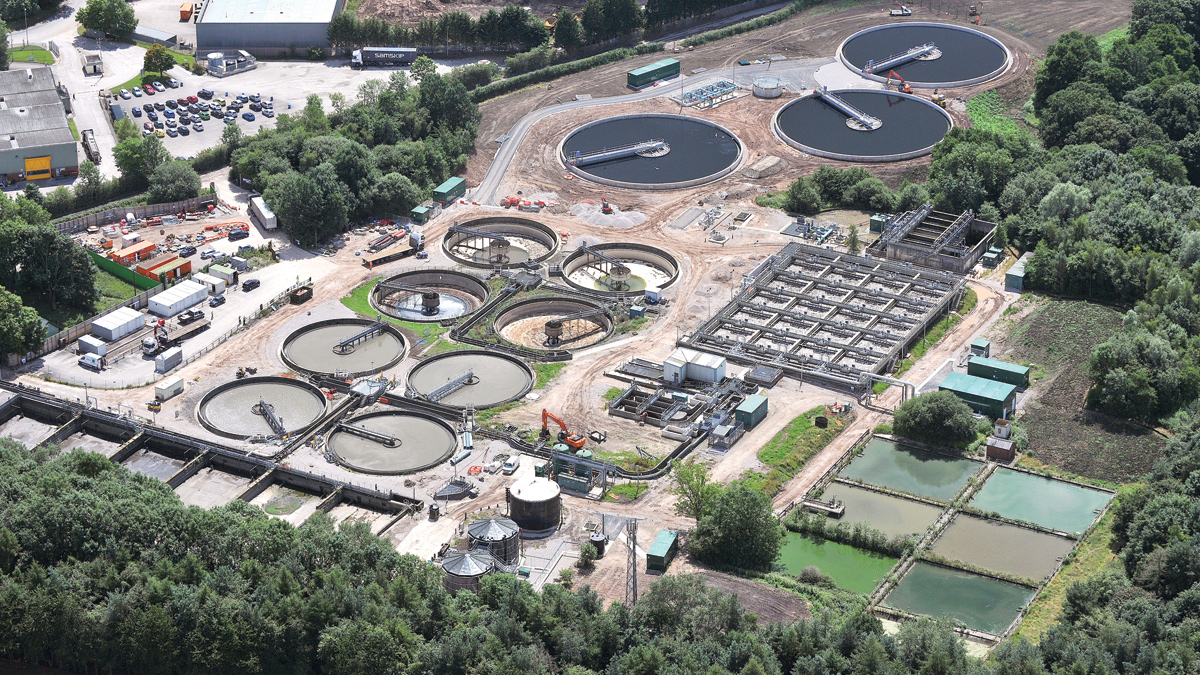
Chorley WwTW - Completed project - Courtesy of C2V+
The town of Chorley, in Lancashire, is mainly residential and much of the surrounding land is dedicated to agriculture and heritage buildings. Chorley Wastewater Treatment Works (WwTW) is located close to a small number of residential houses with a shared access road. C2V+, a joint venture between CH2M (now Jacobs) and VolkerStevin, was awarded a £14.5m design and build contract by United Utilities in September 2015 to upgrade the existing treatment works and comply with Environment Agency standards. This investment was driven by the requirements in the Bathing Waters Directive and Shellfish Waters to enable the operation of the storm tanks overflow to meet the discharge frequency limits. The proposed solution comprised an upgrade to the existing treatment works to address quality and growth drivers, enabling the treatment of flow to the works to be increased from 40Ml/day to 80Ml/day on completion, with a consented FTFT of 1500 l/s.
Project scope
The Environment Agency identified that the overflowing storm tanks needed upgrading to comply with the requirements of both the Shellfish Waters and Bathing Waters Directives. Spills permitted via the directives from the storm tanks into the River Yarrow (via the River Chor diversion) are limited to a maximum of 10 spills in a one-year period and no more than three spills per bathing season (May to September) – figures averaged over a rolling 10-year period.
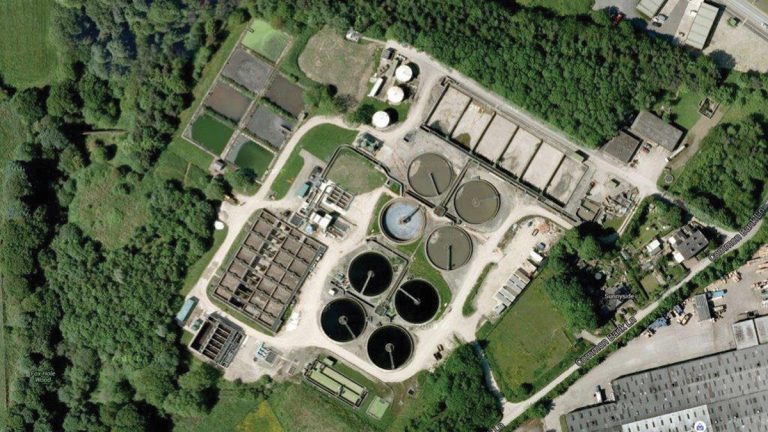
Original works – Courtesy of C2V+
The population is predicted to grow from 53,641 in 2013 to 65,459 at the 2036 design horizon, which causes the emission limit for ammoniacal nitrogen (NH3-N) in the environmental permit to be reduced from 6mg/l to 1mg/l on a 95-percentile basis.
The existing Chorley Wastewater Treatment Works was not capable of achieving this emission level and an upgrade was required to ensure that the new emission limit would be achieved. In addition to meeting the quality and growth drivers of the project, the work required the replacement of two glass lined steel sludge storage tanks.
The new works will be fully automated, including:
- Incorporation of existing assets in to the automation.
- Instrumentation.
- Control.
- Automation and monitoring of the site.
This will be achieved through an upgraded, site-wide communication network and SCADA (supervisory control and data acquisition) system, located within the existing control room at Chorley WwTW and used to communicate with the central control room at Blackburn WwTW.
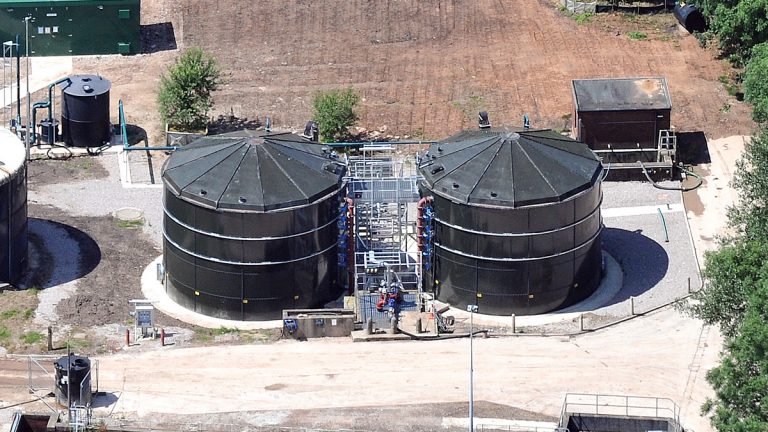
New sludge tanks – Courtesy of C2V+
Key elements of the project
To achieve the required outcomes, the project included hydraulic and network modelling to verify flows to works and size the new units, whilst also verifying the existing design, construction, M&E installation and commissioning of:
- A single lane extension and bypass of the existing inlet works.
- An online replacement of the existing screening and compaction units.
- A new primary settlement tank auto-desludging system.
- Replacement of two of the three existing sludge tanks.
- Increase flow to the anoxic selector process.
- Refurbishment and change of system for the existing surface aeration plant converting into a fine bubble aeration system.
- Removal of the existing sand filter (redundant asset).
- 3 (No.) 43.5m diameter final settlement tanks (FST).
- 5 (No.) motor control centres (MCC), 2 (No.) HV transformers and 3 (No.) ring main units (RMU).
- Interconnecting pipework.
- The installation of a new power and control system cabling site-wide.
C2V+ carried out the design for the main elements in-house. This included the process design development, as well as the normal range of multi-disciplinary design activity associated with WwTW civil, structural, geotechnical and MEICA (mechanical, electrical, instrumentation, controls, automation). The solution incorporated some elements of design provided by the supply chain.
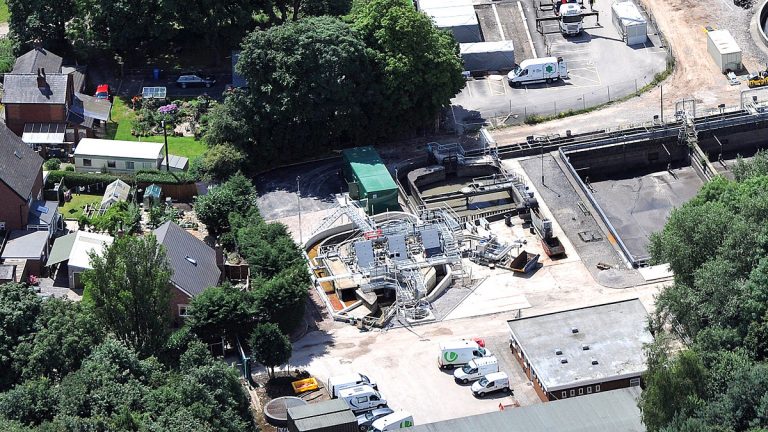
Inlet works – Courtesy of C2V+
Inlet works
Construction at the inlet works included a new in situ concrete bypass channel and screen channel to enable the increased flow, including storm flows, to be screened. It was also necessary to remove two existing Longwood escalator screens and install 3 (No.) new Longwood escalator screens and dewatering compactors. New flow control penstocks and the ability to isolate for maintenance using stop logs were also incorporated into the works. The new arrangement required extensive modification to the existing flooring and access arrangements to ensure the screens area could be maintained in a safe manner upon completion.
A new kiosk, supplied and installed by MCL Ltd, and an MCC, from Lloyd Morris Electrical Ltd, were installed along with power and control cabling that fed back to the existing process control building and to the upgraded SCADA system. A new flow measurement was also installed which required the installation of temporary over pumping and hydro-demolition of the existing flume concrete. The temporary over pumping was sized to enable full consented flow of 40ML/day on a fully automated system included telemetry supplied by Pump Supplies.
Use of high pressure water jetting (hydro-demolition) to break out concrete sections in a precise controlled manner was used on-site to avoid the risk of damage to the main structure, which was required to be retained. The work was completed in one and a half days, compared to a week or more if conventional techniques were employed.
Primary settlement tanks
New automated de-sludge pumps, pipework and controls were installed to enable the existing PST to be utilised. The solution chosen in this case was ram pumps supplied by EMS.
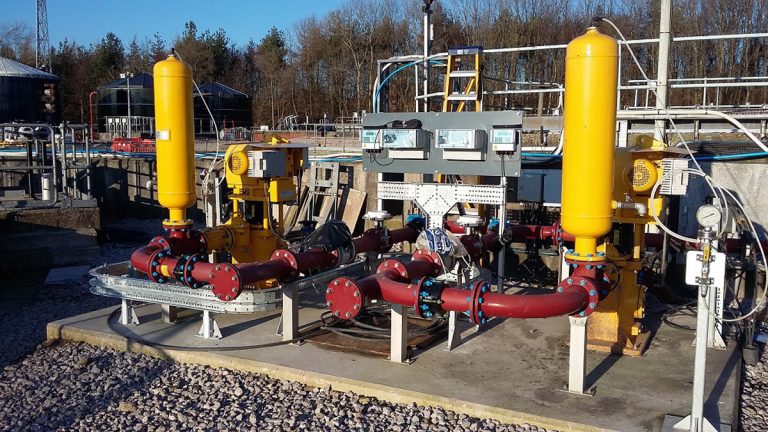
De-sludge pumps – Courtesy of C2V+
Sludge tanks
Two of the existing glass coated steel tanks had reached the end of their usable life and were replaced, one at a time, by two new 9.3m diameter steel tanks. A new access staircase was also added to allow for the maintenance of the probes installed into the roof of the tank. The tanks had an air mixing system (supplied and installed by Monsal) for sludge agitation and odour control (supplied and installed by Air Water Treatments) to ensure that there was no increase in odour at the site boundary. A new control kiosk, system and MCC were also installed as part of the works.
Activated sludge plant
A major process driver for the scheme was the application of an ammoniacal nitrogen consent limit of 1mg/l. Several potential options had been reviewed with United Utilities to up-rate/develop the activated sludge plant (ASP) system.
The solution incorporated a fine bubble diffused aeration (FBDA) system. In poor condition and unsuitable to meet the new regulatory requirements, the existing surface aeration system was replaced on a lane by lane basis with a Xylem Water Solutions FBDA system. The works in the lanes focused on the removal of a single lane at a time and installation of temporary ferric dosing.
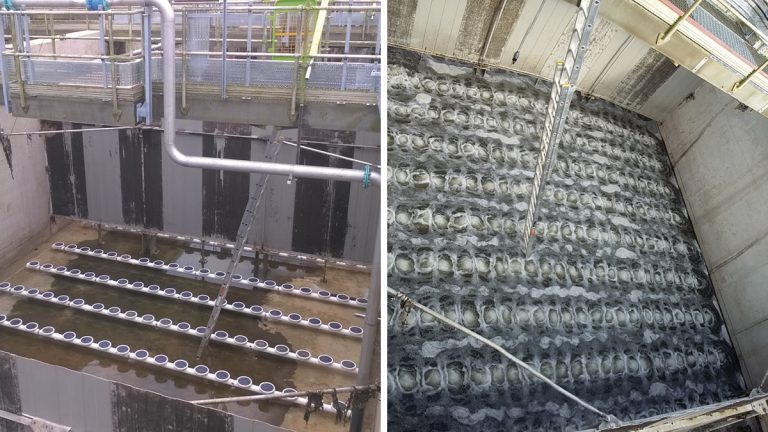
FBDA distribution main – Courtesy of C2V+
The existing PSTs needed to improve their settlement performance and reduce the process load at ASP during the temporary works period. As such, the works required extensive planning and discussions with the client before the first lane was handed over for the new system to be installed.
Once isolated, the lane was drained down and access was provided to each cell to be cleaned out and all existing equipment removed. The feed pipe was also increased in diameter for each lane, which required the coring out of the existing and installation of a new 900mm ductile pipe connection.
The new air pipework and diffuser fittings were then lifted into position via a mobile crane. Following the installation of the fittings in the base of the tank, new instrumentation was then installed and commissioned which was then leak and pattern tested prior to the tank being put back into service. This process was repeated for each lane until complete.
Final settlement tanks
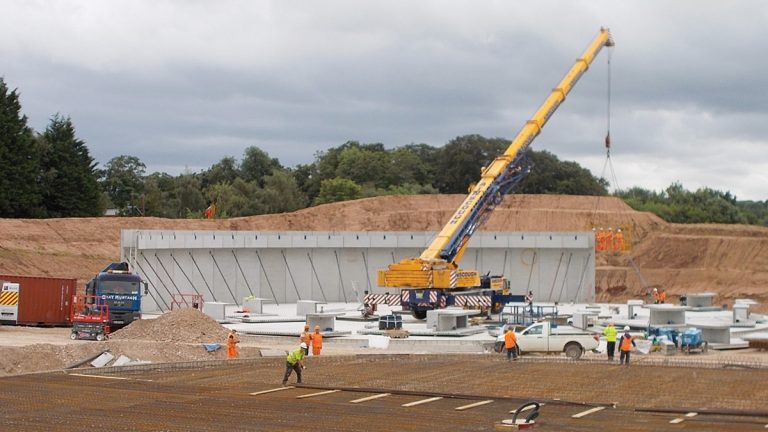
FSTs under construction – Courtesy of C2V+
Another key component of the ASP system upgrade was the construction of 3 (No.) 43.5m diameter, 7m deep, flat-based (with suction scraper) FSTs. A design for manufacturing and assembly (DFMA) approach was adopted, and the integrated design and construction team began engaging with specialist suppliers in the industry. Working with Shay Murtagh Precast, who had successfully constructed a very similar tank in the Thames Water area, C2V+ was able to incorporate features from their proven, more cost-efficient manufacturing process into the design for the Chorley tanks. This meant that the existing moulds could be re-utilised. The bases for each tank were then installed, consisting of around 750m3 of concrete, at a rate of one day per tank.
The DfMA approach ensured that the tanks were constructed quickly and with minimal disruption on a very constrained site. The 57 (No.) 2.4m wide, precast concrete panels were brought to site in phased transport deliveries and installed with a 200t crane located in the middle of the tank base. From start to finish, the assembly of the walls for each tank only took three days. Once each element of the WwTW had been constructed, it was subjected to a water test with a client representative present to confirm each tank met the required specification.
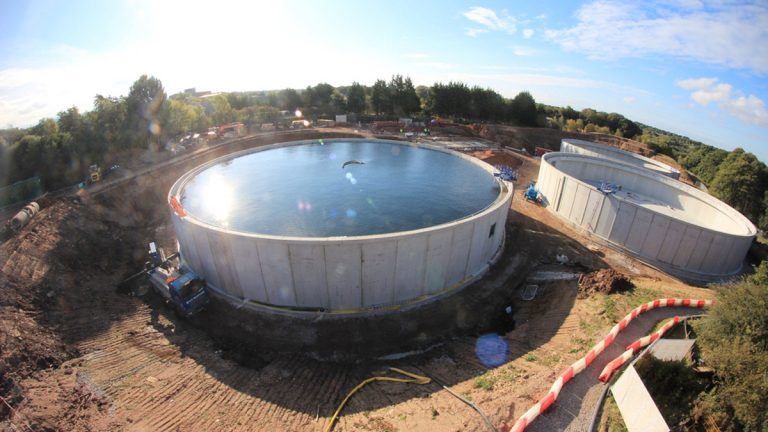
FSTs under test during construction – Courtesy of C2V+
Half bridge suction scrapers bridges
The bridges were brought to site in two sections. They were then lifted into the tank to be placed on a central feed column, prior to the suction equipment being installed. Once complete and power available, the bridges were spun around the tank coping and the scraper set to the optimum position to remove the sludge from the tank.
The specific lift chosen removed the need to have a 300t crane on the outside of the tank during installation of the bridges and equipment, hence improving the safety of the bridge installation operation.
General
The increased flows requiring treatment and the new process required the installation of new pipework. The process included a 1200mm diameter feed pipe, 500mm diameter residual activated sludge and 150mm diameter surplus activated sludge pipe (all in ductile iron supplied by Saint Gobain PAM UK). Three in situ concrete distribution chambers and various flow control systems were also required to be constructed to enable the plant to distribute flows and function efficiently.
The new process required an increase of power supply to the works and the requirement to provide 2 (No.) new HV transformer and RMU units.
Customer experience
The treatment works are located close to a small number of residential properties and share an access road. Prior to the work commencing this was in poor condition.
The project refurbished the road, providing an additional benefit to residents, and then maintained it during construction to reduce the impact of construction traffic for the local residents. Arrangements were also made to acquire additional parking for site staff, eliminating any additional traffic on the access road.
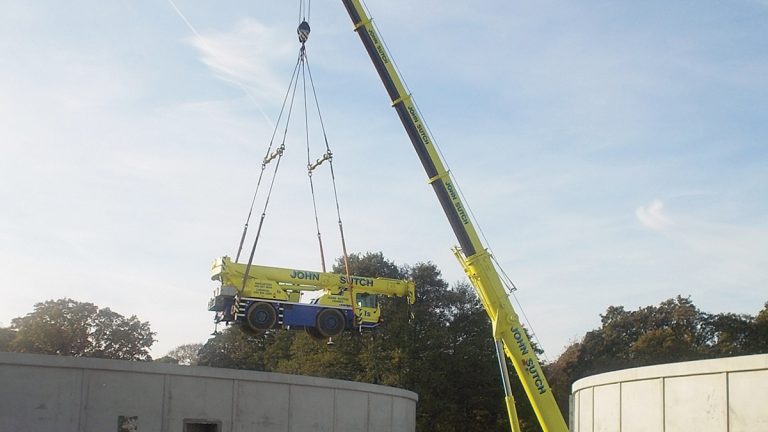
Lifting in a 40t crane to enable the installation of the scraper bridge from inside the FST – Courtesy of C2V+
Summary
The new works was commissioned and are set to allow United Utilities to meet their regulatory output in March 2017. The remaining minor works were then completed to allow formal second stage hand over in December 2017.
The work had been subjected to some prolonged periods of high flow and load since commissioning and has met performance standards throughout. The new plant has reduced the demands upon the operations team which has led to an operational plant that is more cost effective and efficient, reducing the operating costs.