Melbourne WTW – High Lift Pump Sump Bypass (2018)
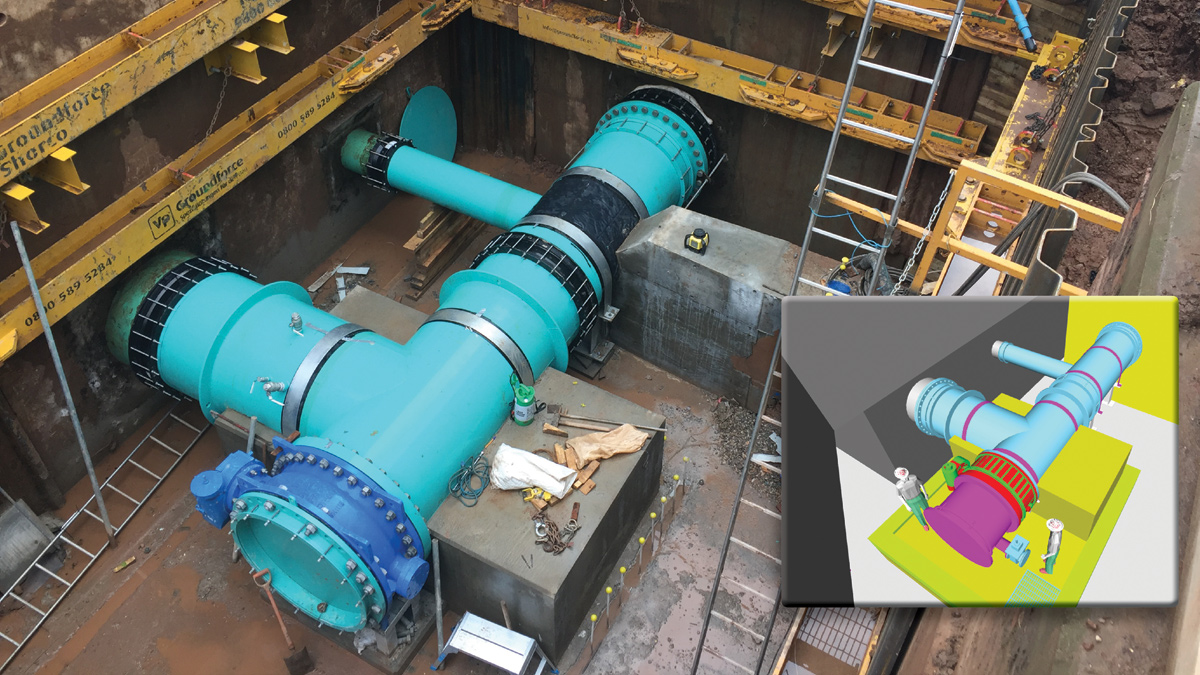
Manifold connection under construction - Courtesy of Severn Trent Water and (inset) 3D model of new manifold - Courtesy of Stantec Treatment
Melbourne Water Treatment Works (WTW) is situated in the eastern region of Severn Trent Water Ltd. It is the primary feed to 750,000 customers in the Leicestershire area. The original works was constructed in the 1960s and this was totally rebuilt in the 1990s and is capable of supplying up to 220MLD. In early 2016, Severn Trent Water had undertaken a detailed review of all their major treatment works and, as part of that study, identified that the high lift sump at Melbourne was a single point of failure. There were also internal inspections of the tank which indicated that it was in urgent need of structural repairs. In late 2016, Stantec Treatment (now MWH Treatment) was approached by Severn Trent Water to design and build a bypass around the high lift pump sump.
Working on a live site
The key problem that Severn Trent Water faced was that the treatment works could not be shut down for more than 16 hours without putting customer supplies at risk. A solution was needed whereby the sump could be taken out of service for a number of weeks and the works kept in supply. The high lift sump is located downstream of the chlorine contact tank and prior to the high lift pumping station and operates as a balancing tank for the pumping station.
Optioneering
A number of optioneering workshops were held with Severn Trent Water. From these workshops, it was clear that building a second sump was not a viable option due to the lack of space on site. The only sensible option was to construct a bypass around the tank allowing the sump to be taken out of service and using the volume in the contact tank as the pump balancing tank. A 3D model was produced and it was concluded that there was enough room to install a 1400mm bypass and maintain a flow of 200 MLD.
To construct the bypass, two major connections needed to be made; an upstream connection post the contact tank and a downstream connection onto the existing pump manifold both of which presented some interesting challenges.
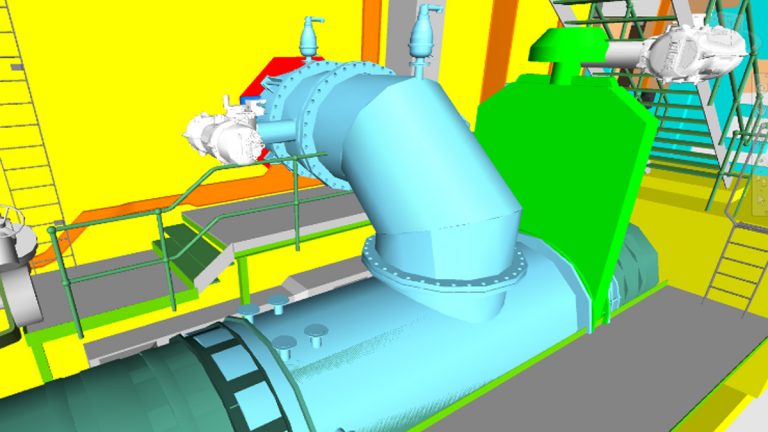
3D model showing the mixer ‘T’ in position, new 1800mm gate valve and 1400mm bypass connection – Courtesy of MWH Treatment
Downstream connection
The downstream connection to the pump manifold was undertaken first. Part of the existing pump manifold needed to be removed to install the new section and valve. This required two of the three pump sets to be isolated for two weeks whilst the construction works took place. By installing a cross connection inside the pump hall, six of the nine pumps were made available to use and the works operated on a reduced output for the two weeks. The existing pipework was 8m below ground level and in between major civil structures making the construction challenging.
The upstream connection
The upstream connection was undertaken second. The major challenge here was determining actually where to connect to the existing 1800mm main. The existing pipework from the contact tank to the high lift sump is contained in a large underground chamber. The 1800mm pipework was made of GRP and had the added complication of also having an in-line static mixer for dosing sulphur dioxide and the existing mixer was located at the ideal point for connecting in the bypass.
Working with Statiflo, the team designed an arrangement that would not only retain the chemical dosing facility but also had the ability to divert the flow through the bypass. The design replaced the existing mixer with a mixer ‘T’ so that chemical dosing could be maintained whether the site was on bypass or not. As there were no means of isolation downstream of the mixer and the area was very tight for space, an 1800mm knife gate valve (from T-T Flow Valves) had to be fabricated and installed in the same space.
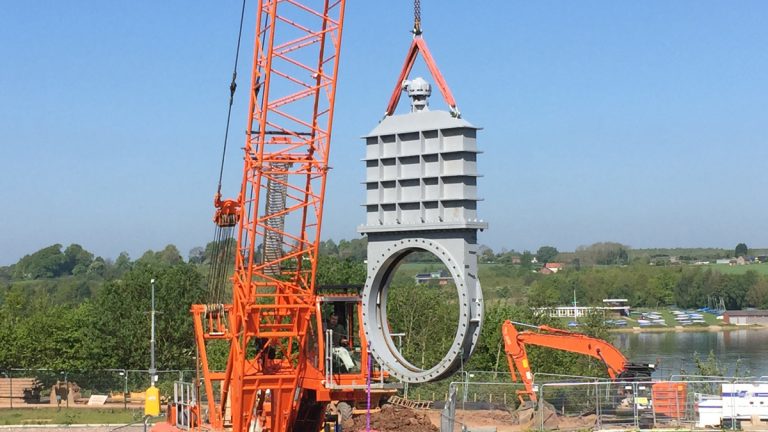
Installation of the 1800mm knife gate valve – Courtesy of Severn Trent Water
Mixer/valve arrangement
The installation of the new mixer/valve arrangement was the biggest challenge and riskiest part of the project. This required the site to be shut down completely. As a result, the team only had a maximum working window of 16 hours. After detailed planning and risk assessment, it was concluded that the whole assembly could not be installed in the shutdown window. The work was split into three separate outages. Additional spool pieces and blanks were made to facilitate the installation.
The work was undertaken as follows:
- Shutdown 1: Removal of the existing mixer and installation of the straight element of the mixer ‘T’. A 1400mm blank was fitted to the mixer and an 1800mm spool piece, the same dimension of the 1800mm valve was also fitted.
- Shutdown 2: Removal of the 1400mm blank and installation of the 1400mm section of the mixer and the 1400mm isolation valve.
- Shutdown 3: Removal of the 1800mm spool piece and installation of the 1800mm knife gate valve.
Once all three shutdowns were successfully completed, the 1400mm bypass pipeline was laid around the structures. The depth of the dig and the proximity of the existing tank structures meant that detailed planning and assessment had to be made before the work could start.
Melbourne high lift pump sump bypass: Table of designers, contractors and suppliers
- Client: Severn Trent Water Ltd
- Main design/build contractor: MWH Treatment Ltd
- Civils sub-contractor: Forkers Ltd
- Pipework fabrication/fittings: Freeflow Pipesystems
- Mixer ‘T’: Statiflo
- Supply of fittings: R2M Limited | Teekay Couplings
- Electrical sub-contractor: Southern and Redfern
- ICA sub-contractor: Boulting
- Knife gate valve: T-T Pumps
Automation
As well as the civil and mechanical aspects of the project, new software was required to run the high lifts in automatic mode. Under the bypass arrangement, the existing contact tank needed to act as both a high lift pump balance tank and also maintain its primary purpose as a chlorine contact tank.
To achieve the hydraulic requirement of 200MLD, the contact tank needed to be run at a higher level than under normal operation. Interlocks were also installed to ensure the pumps shut down if the contact tank level dropped too low.
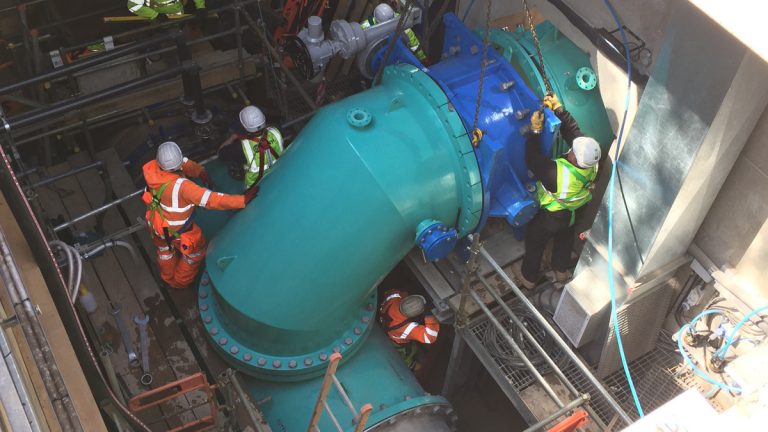
The completed installation of the 1800mm-1400mm custom made ‘T’ static mixer: Courtesy of Severn Trent Water
Handover
A detailed commissioning plan was produced and after a thorough period of testing, the project was handed over to Severn Trent Water. Since handover, Severn Trent Water has successfully removed the high Lift sump from service and completed the necessary repairs to the tank. The new bypass was in use for four weeks during the remedial work. Overall the project value was ~ £3.5m.