Digley IRE Valve Tower Metalwork Replacement (2017)
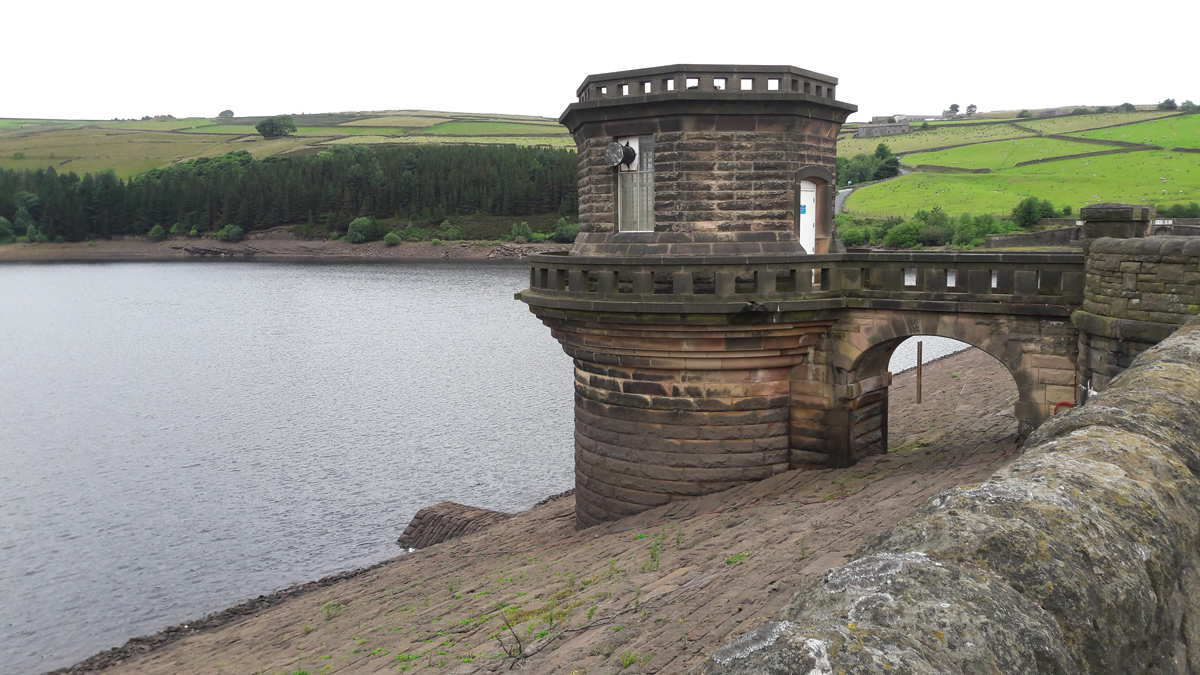
Valve tower at Digley IRE - Courtesy of MMB
Digley Impounding Reservoir (IRE) is located in Holmbridge, Huddersfield. The valve tower associated with the reservoir had corroded access metalwork which did not meet current health and safety standards. The project replaced all the corroded access metalwork within the valve tower with new Yorkshire Water Asset Standard compliant metalwork, improving safe access within the tower. The scheme also included application of a paintwork system to the existing pipework, valve spindles and support beams. A 3D laser scan of the valve tower was undertaken to prevent repeated visits into a confined space and to aid the design process.
Background
Yorkshire Water Services (YWS) has over 130 impounding reservoirs (IREs) which have deep shafts/valve towers that require regular internal inspection. Due to their age, the access arrangements within the valve towers do not meet the modern health and safety standards. Design and build contractor Mott MacDonald Bentley (MMB) was awarded a delivery contract to address access issues within the valve tower at Digley IRE. The valve tower at Digley IRE is approximately 44mm deep and is circular in shape with a diameter of 3.8m. There are eight intermediate levels in addition to the top platform level and scour tunnel invert level. The reservoir, including the valve tower, was built in late 1940s/early 1950s.
Health & Safety
The significant health and safety issues that were addressed at the design stage and during the works included:
- Working at height.
- Working in a confined space.
- Working adjacent to deep water.
- Manual handling.
- Working on steep slopes and uneven ground.
Due to the nature of the work, the entire scheme was about improving the health and safety and access issues within the existing valve tower. To eliminate the need for repeated entries into a confined space, and in the interest of health and safety, MMB employed a specialist subcontractor to use the cutting-edge technology of laser 3D scanning throughout the entire depth of the valve tower. The 3D scan created a point cloud where the distance between any two points could be measured by using 3D-compatible computer software. The accuracy of the scan was +/- 5mm.
All the new metalwork was fabricated utilising the 3D scan which prevented a need for taking manual measurements within a confined space, cutting short the entire process by weeks. This had commercial and health and safety benefits, by increasing efficiencies and reducing design time, whilst maintaining high quality standards. The 3D scan will also add value to any future schemes related to this particular site by visually accessing the inside of the valve tower and taking any required measurements from the scan without having to visit site. A 3D model was generated for the final metalwork design of the valve tower to visualise and discuss the proposed design with YWS project managers and operational team, ensuring real ‘buy-in’ to the project from all parties.
Whilst carrying out the metalwork installation work on site, MMB employed a specialist subcontractor specialising in emergency rescue in confined spaces, working at height and safety management so that the proposed works were carried out in a safe, controlled manner. Temporary scaffold platforms were used to dismantle the old metalwork, install new metalwork and apply the paintwork system to existing steelwork within the valve tower. All MMB personnel who were involved in site activities were confined space-trained and CSCS qualification holders.
Traffic Management was employed in the form of half lane closure across the crest road for loading and off-loading construction material. Local roads and the crest walkway were kept clear at all times for local public and dog walkers.
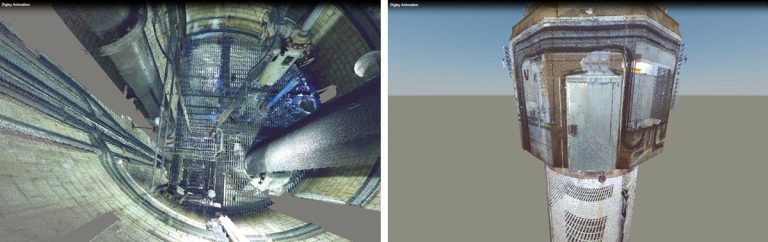
(left) Internal 3D scan of the valve tower and (right) External 3D scan of the existing valve tower – Courtesy of MMB
There were several constraints and challenges that MMB has faced at both the detailed design stage and at the installation stage:
Provision of a bespoke man riding davit
The current YWS operational strategy is such that there is provision for one entrant into the valve tower with one top man – however, going forward YWS wish to facilitate entry for two personnel into the valve tower with a top man. To meet this change, MMB procured a bespoke man riding davit which has provision for two entrants accessing the shaft one after another. The davit is supplied at the top platform level and can be removed when not in use. A flush davit socket is supplied which is fixed to the new metal decking at the top level. There are two winches supplied with the davit which have fall arrest as well as retrieval capabilities in the event of an emergency.
Achieving a straight lift out of the valve tower
The old access arrangement in the valve tower was such that the access ladders were staggered at every platform. This meant that the entrant could not be pulled up to the top platform level in an emergency. The new metalwork design was undertaken in such a way to achieve a straight stretch of ladders all the way down into the shaft to facilitate emergency rescue. The 3D scan proved very helpful to achieve this.
Damp environment due to leaks and water ingress into the valve tower
The lower levels of the tower were excessively damp and it proved very difficult to apply a paintwork system to the existing steelwork at the lower levels when the old metalwork was removed. To overcome this problem, MMB employed heavy duty ventilation equipment to force ventilate the shaft and reduce the moisture level for application of the paintwork system.
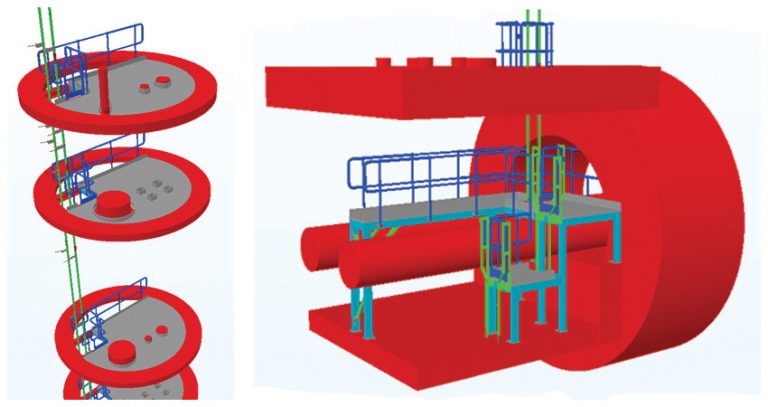
Left) 3D model of the gantry levels within the valve tower (right) 3D model of the base of the valve tower – Courtesy of MMB
In order to reduce the impact on the local residents in close proximity to the reservoir, no work was planned outside of ‘standard’ working hours. There were no noise or vibration issues as all the work was carried out within the valve tower away from local private properties. As part of YWS standard procedure, a customer engagement plan was produced for this scheme, with customers living in the local vicinity of the reservoir contacted prior to the commencement of works to inform them of the proposed project.
The scheme fulfils the YWS sustainability requirements which are actively pursued as part of YWS strategic business objectives and performance commitments for AMP6 projects. All the decommissioned metalwork that was recovered from the valve tower has been collected in skips and will be widely recycled, and a site waste management plan (SWMP) was produced by the principal contractor as part of the project. Where possible, structural elements including support beams associated with the access metalwork were retained and applied with a specialist paintwork system to extend their design life in damp, corrosive environment. The success of the scheme is down to excellent teamwork and collaboration between all parties involved in its delivery.