Woolston WwT Scheme (2015)
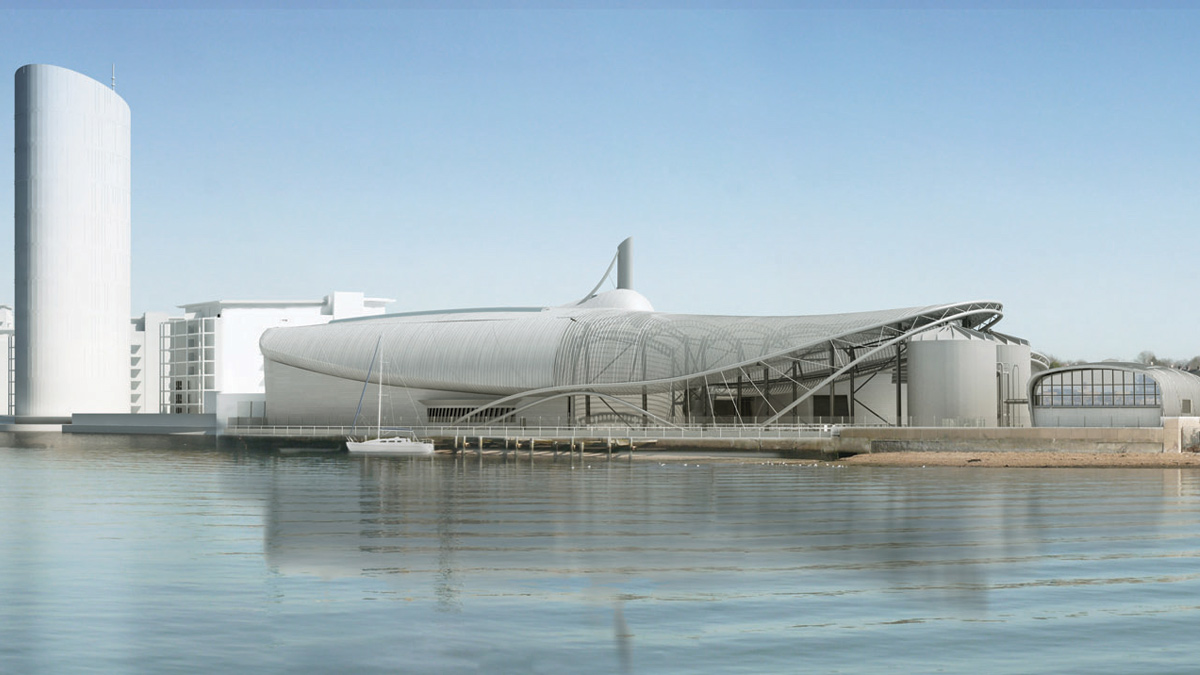
Primary building visualisation - Courtesy of 4Delivery
Work has started on a £63m environmental improvement scheme to redevelop and completely modernise Woolston WwTW. The existing works uses a conventional activated sludge plant (ASP), built in 1966, treating sewage flows from part of the Southampton conurbation, serving a population of approximately 62,000 people. The site occupies an area of 1.26 hectares. The existing sewerage system which feeds into the WwTW collects both wastewater and stormwater from the Woolston Catchment area. At present wastewater is continuously treated and the treated sewage effluent discharged into the River Itchen Estuary near the western end of the jetty through the final effluent outfall. Existing storm and final effluent discharge points will remain unchanged during the works.
Improvement drivers
The Woolston WwTW discharges into the River Itchen Estuary within the Solent and Southampton water Special Protection Area (SPA) which has been designated as a nitrate sensitive zone by the Environment Agency.
Southern Water is required to provide nitrogen removal for the Woolston catchment to comply with the European Urban Wastewater Treatment Directive (91/271/EEC) and associated Urban Waste Water Treatment (England and Wales) Regulations 1994 as well as nitrogen removal requirements under the habitats directive.
A new effluent discharge permit requirement of 15 mg/l total nitrogen (TN) has been imposed as part of a coordinated strategy involving changes at other wastewater treatment works.
Dispersion modelling predicts that the impact due to odour from the existing wastewater treatment works at Woolston is substantial and extensive. Once the installation is completed, with a stack on the primary building (shown above) for the central odour control facility, all ground level impact remains below the target value of 1.5 ouE/m3 at all locations.
The scheme
4Delivery, a joint venture between Veolia Water, Costain and MWH (now Stantec UK), is undertaking the design and construction of the project on behalf of Southern Water.
The permanent works treatment process will fully treat flows up to 36.9MLD, in compliance with the new discharge permit requirements. All future permanent processes will remain within the boundary of the existing site.
The wastewater treatment includes:
- Inlet works comprising:
- Coarse and fine screens and screenings processing.
- Fat, oil, grease and grit removal and processing.
- High rate primary sedimentation Lamella process.
- Membrane bioreactor (MBR) plant comprising:
- Modified Ludzack Ettinger (MLE) activated sludge plant (ASP) for the biological removal of nitrogen.
- Membrane filtration tank, utilizing microfiltration hollow fiber membranes.
- Existing ASP converted into future storm tank.
- Odour control comprising chemical scrubbing and carbon units.
The sludge recycling includes:
- Sludge storage and blending.
- Indigenous sludge dewatering and processing.
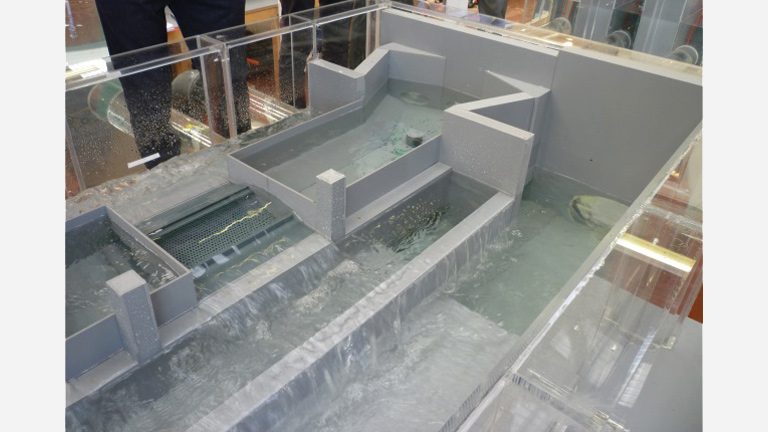
Hydrotec model of CSO operating in 1 in 30 year storm – Courtesy of 4Delivery
Early engagement
Following outline design, 4Delivery approached Hydrotec to carry out physical modelling of key hydraulic structures. A physical model helps to identify unwanted hydraulic features such as vorticity or excessive turbulence and identifies remedies during detailed design. This provides a comprehensive assessment of the hydraulic grade line to be determined through each of the individual elements of the inlet works.
Water level measurements are undertaken with piezometric tapings and comprise the upper limit of the intermittent and top water surface. Confirmation of the hydraulic profile is essential to verify the overall hydraulic concept and ensure effective plant operation.
The first physical model of the CSO and inlet channels/screens confirmed acceptable flow/velocity distribution, and hydraulic and solids transport through to removal stages.
BIM
The use of BIM on Woolston provides a collaborative working environment between all the partners on the project. The federated model gives a greater understanding by all parties of the design.
Processes and techniques developed on the project allow engineers to explore, develop, communicate and refine the design in the 3D environment before producing a final issue of drawings just once; right first time saving the time and cost of multiple revisions of the drawings. The process produces an auditable record for governance and allows improved contextual understanding by designers and ultimately better design with less re-work and consequently significant cost savings. The process creates time to engineer and add value for our clients whilst reducing drawing production costs.

Example of model checking software: Isometric view from 3D BIM model – Courtesy of 4Delivery
Traditional methods of checking a design from a 3D model by production of 2D drawings are both time consuming, counter intuitive and offer the engineer a limited amount of information that is restricted by the number of plans and sections cut from the model. By putting the control back in the hands of the engineers every aspect of the model can be checked and total confidence in the models that are shared with third parties can be achieved. To the left is an example of a check made of the model, but cutting any section and interrogating it for levels, distances, areas, volumes, coordinates etc.
MBR technology
Due to the extremely constrained site MBR technology was selected to allow the treatment process to fit within the existing site footprint. Reinforced hollow fiber ultrafiltration membranes will separate the final effluent from the mixed liquor in an activated sludge plant. Therefore the membranes replace the final settlement tanks (FST) and any tertiary solids removal treatment.
The membrane plant will occupy only about 1/5 of the area required for conventional final settlement tanks. In addition due to the presence of the membrane filtration plant the MLE ASP will operate with a mixed liquor suspended solids (MLSS) up to 10,000mg/l.
This allows the size of the ASP to be reduced to approximately 1/3 the size of an ASP with conventional final settlement tanks. MBR technology allows the plant to operate with a high sludge age; this results in consistent nitrification and low sludge yields. The ultrafiltration membranes provides a physical barrier to reduce solids bacteria and viruses leaving the plant to very low levels providing additional water quality benefits to the Itchen estuary.
The project will be the largest membrane plant in the UK when complete.
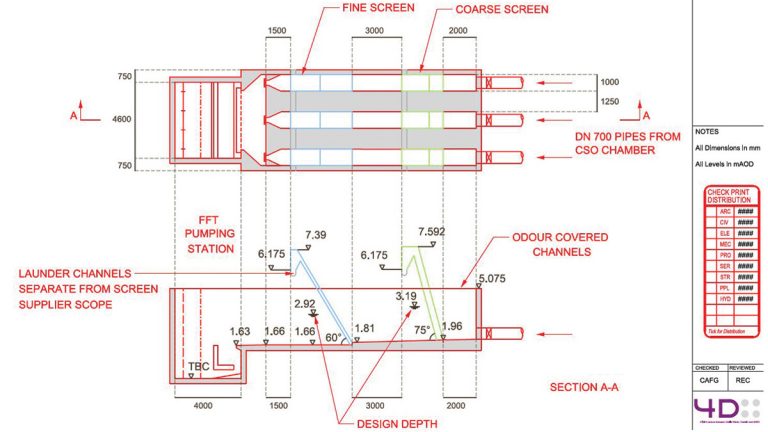
Primary area screen layout sketch – Courtesy of 4Delivery
Current Phase – Enabling works
The Woolston WwTW site is small in size and has a congested layout creating a challenging area in which to construct 3 (No.) large building structures.
In order to provide significant programme savings 4Delivery & Southern Water have leased an area of land from a neighbouring development owned by the Homes & Community Agency (HCA). This area of land is being used to house the enabling works, temporary process units constructed to allow existing structures within Woolston WwTW to be demolished.
Currently under construction, these process units will provide primary treatment of wastewater, stormwater storage and sludge storage to allow Southern Water to continue to meet their environmental permit with the EA whilst construction within the extents of the Woolston WwTW site are completed. Secondary (ASP) and tertiary treatment (FST) in the existing Woolston WwTW site will be used to complete the treatment of wastewater whilst the new primary and secondary buildings are constructed.
Once the new process streams are commissioned, the enabling works PSTs will be utilised as tertiary treatment to allow the existing FSTs to be demolished. This creates the opportunity of constructing the new sludge facilities ahead of the programme providing an additional saving to the client.
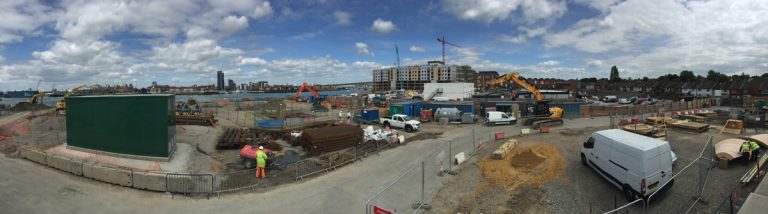
Enabling works – Courtesy of 4Delivery
The Woolston WwTW Programme
- June 2014: Planning permission granted, followed by a six-week standard review period.
- September/October 2014: Mobilisation of welfare units and project offices and construction of temporary treatment works begins on land adjacent to Woolston WwTW.
- Late 2014: Earthworks and piling complete for the temporary treatment works.
- Mid 2015: Temporary works complete, allowing the wastewater to be diverted from the existing site.
- September 2015: Demolition of the existing site begins along with the construction of new site.
- June 2019: All wastewater is diverted into the new site and the temporary plant is removed and leased land reinstated.
- September 2019: Work complete.