Isle of Man Central Telemetry System (2014)
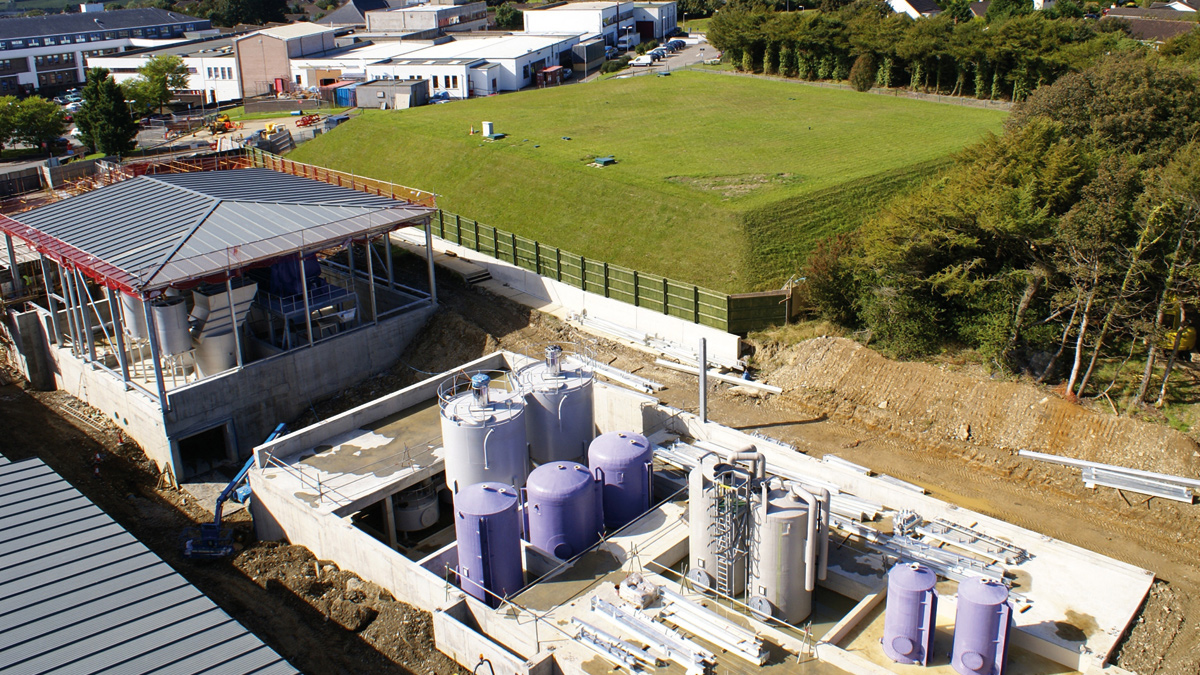
The Isle of Man is a self governing Crown Dependency which, through its ancient parliament Tynwald, enjoys a high degree of domestic legislative and political autonomy. Manx Utilities is a statutory board, charged with ensuring the economic, efficient and effective provision of the services and infrastructure necessary to meet the Island’s needs in terms of a wholesome supply of electricity, drinking water and the treatment and disposal of sewage. The Isle of Man Water Authority is now contained as part of Manx Utilities and has had a program of refurbishing and investing in the assets associated with the production and distribution of water across the entire Isle of Man. The strategic business plan, which will undoubtedly improve the reliability of the water supply right across the Island has been in place for many years and the continued investment in the automated control systems behind the physical assets has given the Manx Utilities company a comprehensive and advanced information and telemetry system.
Background
The beginning of this massive investment in automation came with the renewal and upgrade of the pumping stations. Those that have been refurbished are equipped with pump motor control centers (MCCs) that include the programmable logic controllers (PLCs) that enable the end user to monitor reservoir levels, water pressure and flow rates.
The system can also immediately identify any pump failures and automatically switch operations to the second pump on standby as and when required. This provided the basis of what is now calledthe Central Telemetry System (CTS). To achieve the ambition of centralised monitoring the pumping stations represented the first step in a program of upgrading and development that has spanned many years.
Second Phase
The second phase consisted of establishing an infrastructure using the existing water treatment facilities and installing a number of data gathering outstation control panels (DGOs). These DGO control panels had their own PLC system to allow the collation of data from the outlying pumping stations and reservoir status’and levels via a Modbus connection to a radio system. The 6 (No.) strategically located DGO control panels each connected via PSTN to a central master system located at headquarters at Tromode Road in Douglas. There a SCADA was used for alarming and graphical representation of the control and water distribution system.
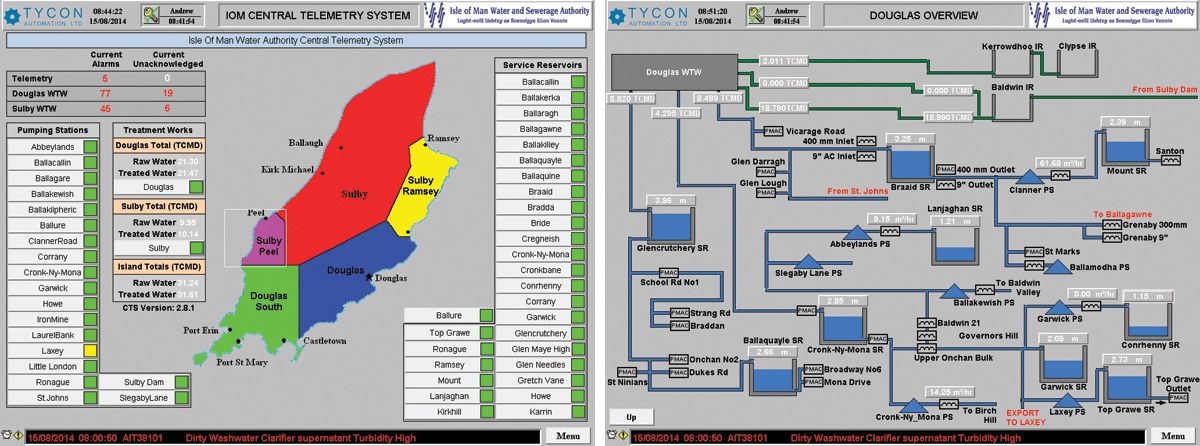
(left) Island CTS overview and (right) Douglas water distribution network – Courtesy of Tycon Automation
Major Assets
The strategic upgrade program that started with the newly built or refurbished pumping stations soon progressed to more substantial planned capital investment. 2003 saw the construction of a new water treatment production facility at Sulby. This new multi-stage water treatment works is capable of producing 21ML/day to the highest standards. It will see the Island forward for many decades.
The idea of a two works strategy for the whole Island is not new. It was first mooted by the late Howard Simcocks MHK, who was Chairman of the Water Authority from 1972 to 1982.
It came in response to a Tynwald question back on 19 October 1982 and indicated that there should be two major new water treatment works – one located at Sulby and the other at Douglas – adjacent to the major sources of water in the two large impounding reservoirs – Sulby and West Baldwin. This is the overall strategy, which has been developed through the 1990s and has now come to fruition.
The Authority has for many years recognised that the small works at Glen Maye, Ballure and Ballagawne did not have substantial sources of water at the back of them to meet modern day demands. During drought years, just when the water is needed, the catchment areas have dried out and supplies have had to be supplemented from other more robust resources. Coupled with that the fact that they are now over 50 years old, and although well built to high standards at the time, are at the end of their useful life.
These works are all single stage works and the problems of discoloured water, due to the manganese deposits in the mains, have continued to this day because these single stage works are not capable of removing the manganese in the treatment process. The new Sulby WTW, with its 2nd stage filters and better chemical dosing and control facilities will remove the source of that problem.
PLC systems were introduced at Sulby WTW for resilience and the Profibus communication protocol for increased levels of information and diagnostics. During this contract the introduction of a site specific dual redundant SCADA system for the water production facility was introduced under the capital contract.
Following the required testing, acceptance and hand over periods this stand-alone SCADA project was integrated into the main CTS SCADA. This not only provided another point of access for operators for the CTS but added value by giving the operations personnel the visibility of being able to monitor and control the whole water distribution system from water treatment facility.
Shortly after the capital expenditure was approved for the de-commissioning of the aging Glencrutery WTW (built in 1933), there followed a major £26.5m capital investment in a new water treatment works at Douglas. Work began on site in June 2005 to construct the facility, which is designed to treat up to 37ML/ day. Construction was completed on time and within budget in October 2007 and the new works went into supply in January 2008.
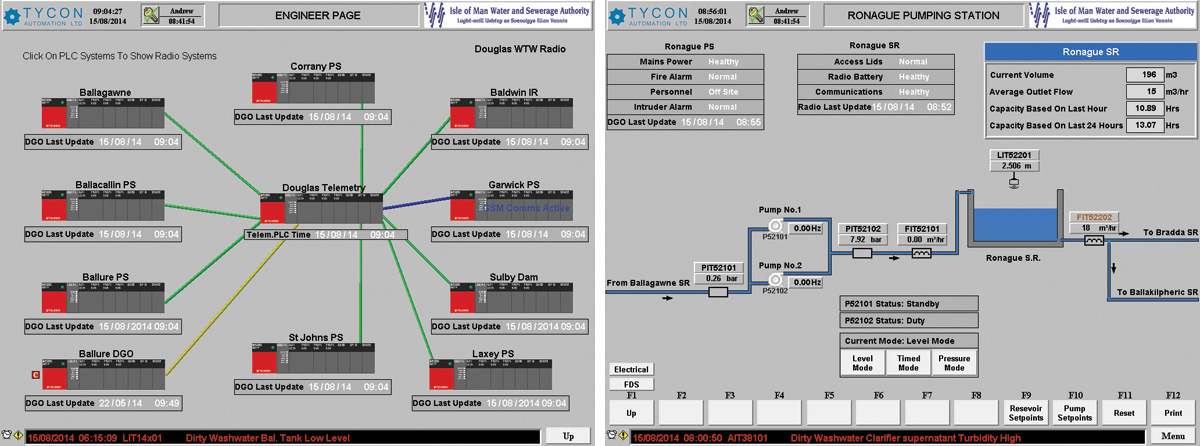
(left) 3G remote link status and (right) pumping station status – Courtesy of Tycon Automation
PLC & SCADA technology
With all of the major water treatment and distribution assets in place the Isle of Man government had provided a strategic foundation to build on. Both of the water treatment facilities at Douglas and Sulby used the latest PLC and SCADA technology from Mitsubishi incorporating intelligent network architectures to retrieve data from devices and communicate and control the statuses of the plant to the operator.
Each of the water treatment facilities on the island operates dual redundant SCADA technology that allows the instant duty changeover of the server SCADA should any hardware issues arise.
In the main Douglas WTW the redundancy is taken a step further to the PLC level incorporating the Mitsubishi QnPRH range of redundant CPUs.
A crucial aspect to the control system was the use of a full dual redundant PLC system. Complete with its own CPU, the secondary system is fully wired-in and tested, increasing the system reliability by mirroring the primary CPU so that in the unlikely event of a failure of the main CPU, power supply or base unit, the secondary system can take over within 21 milliseconds from the same control point.
The requirement from the outset was for a fully redundant system. The Mitsubishi QnPRH PLCs are designed to work in a redundant set-up and therefore met the specification precisely. The system was designed with two processor racks and two I/O racks in each of the main process MCCs, of which there are three for process redundancy. Within each of the MCCs is a industrial touch screen PC running the SCADA client software so that all of the plant is available for control and monitoring at all of the locations.
The pump motors across the site are mostly controlled by Mitsubishi variable speed drives (VSDs) which communicate to the PLC using a Profibus DP network. Mitsubishi Slice I/O with Profibus DP interfaces were employed to manage the I/O locally in the field, which reduces cabling and installation costs and works well with the Mitsubishi PLC that will accept most fieldbus network protocols with a plug-in communications module.
Due to the amount of digital and 4-20mA I/O (over a thousand I/O points) including flow meters, level instruments and quality instruments we segmented the Profibus DP networks to provide maximum redundancy and system resilience. The response time of the PLC however is far beyond what would be needed for this application. PID control loops for flow control valves etc are well within the processing capability of the CPU, with the control loops for the chemical dosing system being the most critical. For this application we are talking seconds, rather than milliseconds, which we often work with in other more dynamic higher-speed applications.
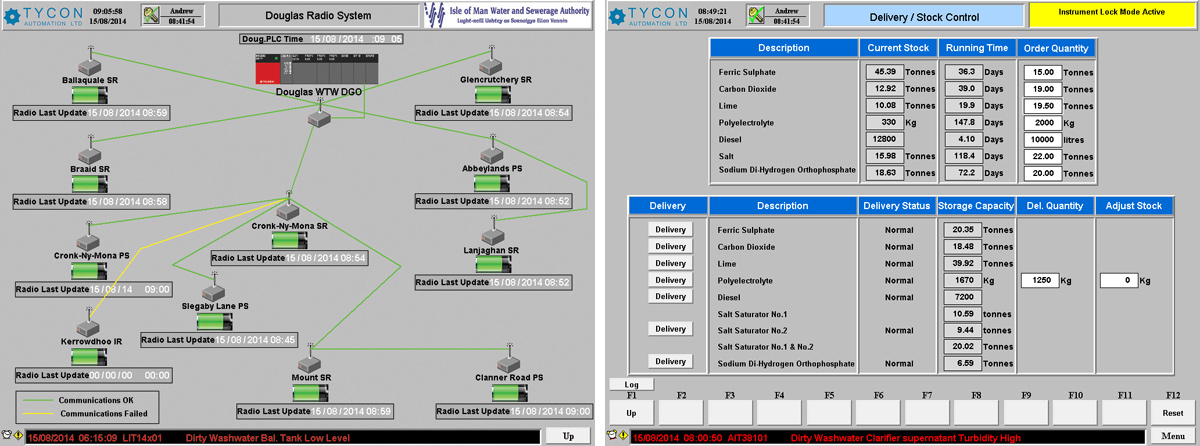
(left) Radio telemetry system status and (right) automated delivery and stock control status – Courtesy Tycon Automation
Evolving the system architecture
Following the completion of the Douglas WTW the CTS has continued to evolve its system architecture to keep in line with the advances of modern remote communication technologies. In the original form the Data Gathering Outstations (DGO) for the collation of the Island wide data numbered only six and relied on the PSTN telecommunication technologies for this activity.
With the demands of more sites and more data, the number of DGOs has increased to ten and the requirement for “real time” rather than ‘dial up’ data has been realised. The 10 (No.) DGOs are now connected to the CTS through real time secure VPN links across the Internet and there is no longer any traditional PSTN technology used in the CTS data gathering functions.
From this involved and sophisticated architecture at the plant level both the Sulby and Douglas WTW provided the foundation for the Central Telemetry System to evolve even further. In conjunction with managing the more functional alarming and control aspects of the control system the CTS is now delivering benefits far beyond its original remit.
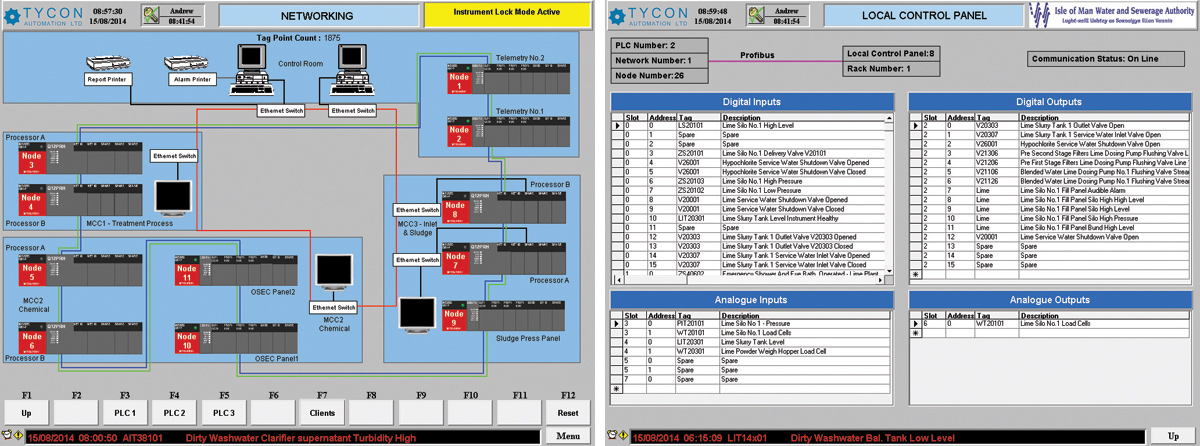
(left) Control system status and (right) works control IO status – Courtesy of Tycon Automation
Strategic features
With the integrated approach adopted by Tycon Automation Ltd the CTS now contains strategic features such as:
- Planned preventative maintenance functionality.
- On call staff management system and on-call out of hours alarming via SMS.
- Embedded documentation help and support for the plant operation.
- Quick help guides for common quality issues.
- Critical alarm and response management.
- Automated delivery monitoring of raw materials.
- Power and chemical usage and reporting.
- Web based reporting packages, including board level reports with financial detail
- Strategic remote access to allow for service support activity by Tycon Automation Ltd.
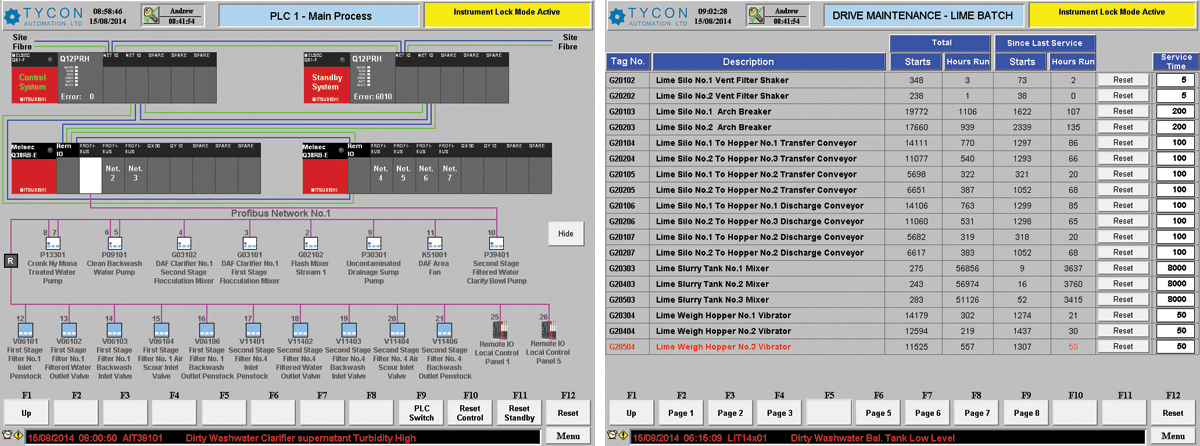
(left) Profibus system status and (right) planned preventative maintenance status – Courtesy of Tycon Automation
The features and benefits of the CTS evolved around the operational, maintenance, quality and business requirements of these plants and the end user. With the recognition of the power that such an architecture provided the water authority had the foresight to continue to invest in the system which has brought about a evolution that has seen the CTS change from a visualisation and alarming tool to an island wide control system.
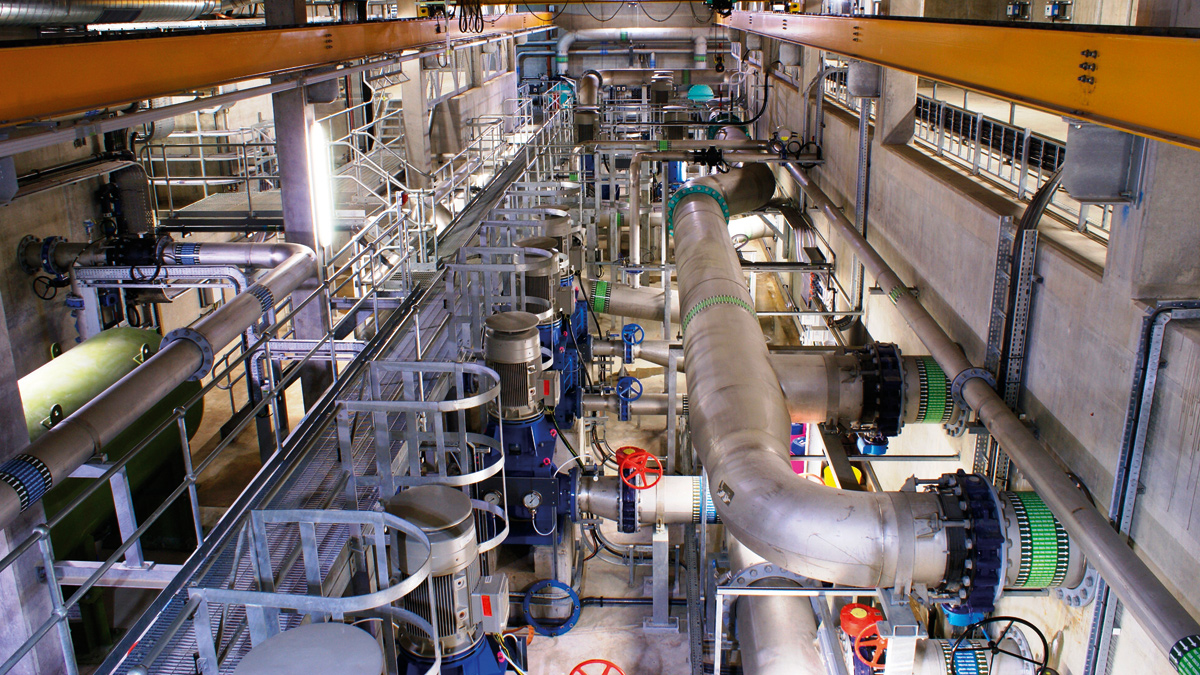
Douglas IOM WTW: Treated water pump gallery (with backwash and interstage pumps in background) – Courtesy of AECOM DB
The CTS has made the transition to a system that now allows the full monitoring control capabilities of the all of assets within the water production and distribution system from either a central or decentralized location. With the further added benefit to the water authority of providing real time strategic and statistical data. This data is collated, formatted and reported for the company executives to make better business decisions helping them increase production and improve efficiencies across their business.