Brancote Sludge Treatment Centre (2020)
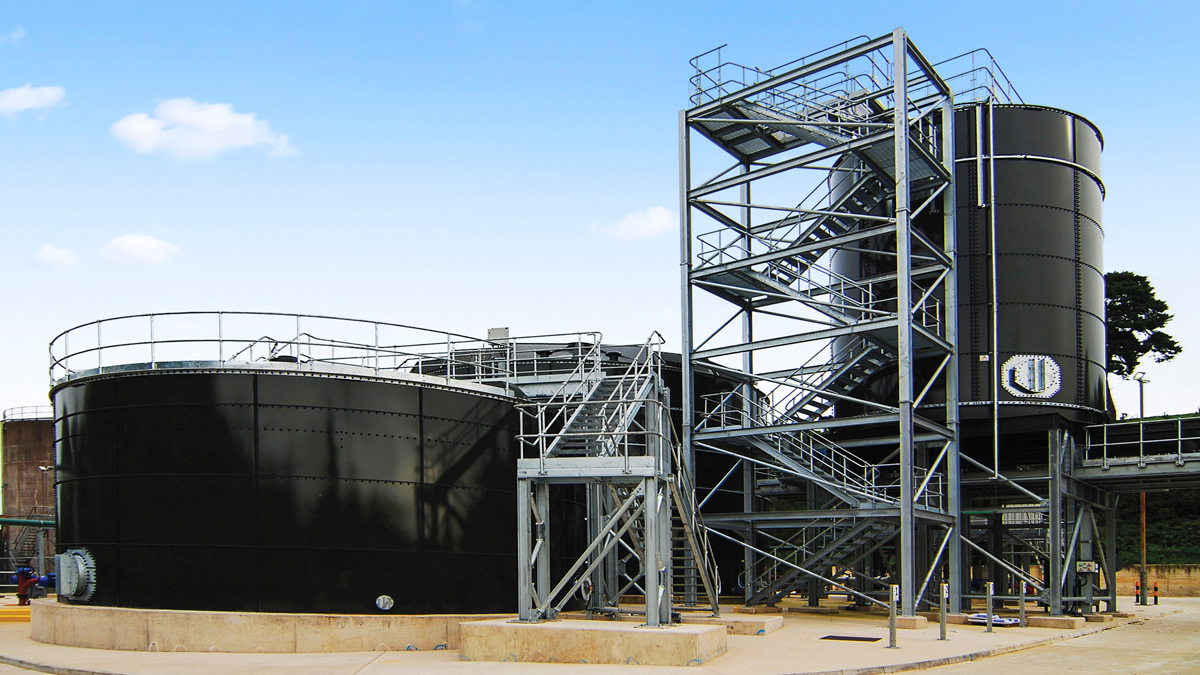
Brancote STC - picket fence thickener corner - Courtesy of Galliford Try
Located to the east of Stafford, Severn Trent’s Brancote Sewage Treatment Works (STW) catchment will see an increase in population from 78,075 current population equivalent (PE) to 85,532 by 2028. The site is split into two distinct areas with the STW processing the sewage flows from within its own catchment and the sludge treatment centre (STC) processing indigenous sludge from the works as well as imported sludge from some nine other smaller rural STWs. Brancote STC has been designated as having rural works status; based on the sludge strategy alignment process carried out in AMP5, the site’s single digester will be shutting down and the works will convert to a strategic raw sludge dewatering site. Brancote STC will be required to dewater raw sludge to 25% dry solids (DS) which will be transported to the thermal hydrolysis plant at Strongford STW for advanced digestion.
AMP6 growth scheme
The Brancote STW catchment is forecast to see an increase of 7457 PE by 2028. The nine satellites sites that currently feed Brancote STC will see an increase in their populations from a total of 75,094 PE to 79,274 PE by 2028; with the vast majority of the imports coming from Rugeley and Penkridge (64,414 PE by 2028).
Cannock STW currently transfers its sludge via an 8km rising main to the Tour Ashes STC. Additional work is being undertaken to now thicken Cannock STW indigenous sludge to 6% and for this to be tankered to Brancote STC for dewatering. This will add an additional sludge population of 65,494 PE by 2028 to Brancote STC.
Therefore, the sludge makeup at Brancote will be made up of 1/3 indigenous sludge, 2/3 imported sludge of which Cannock STW will supply 50% of the imports.
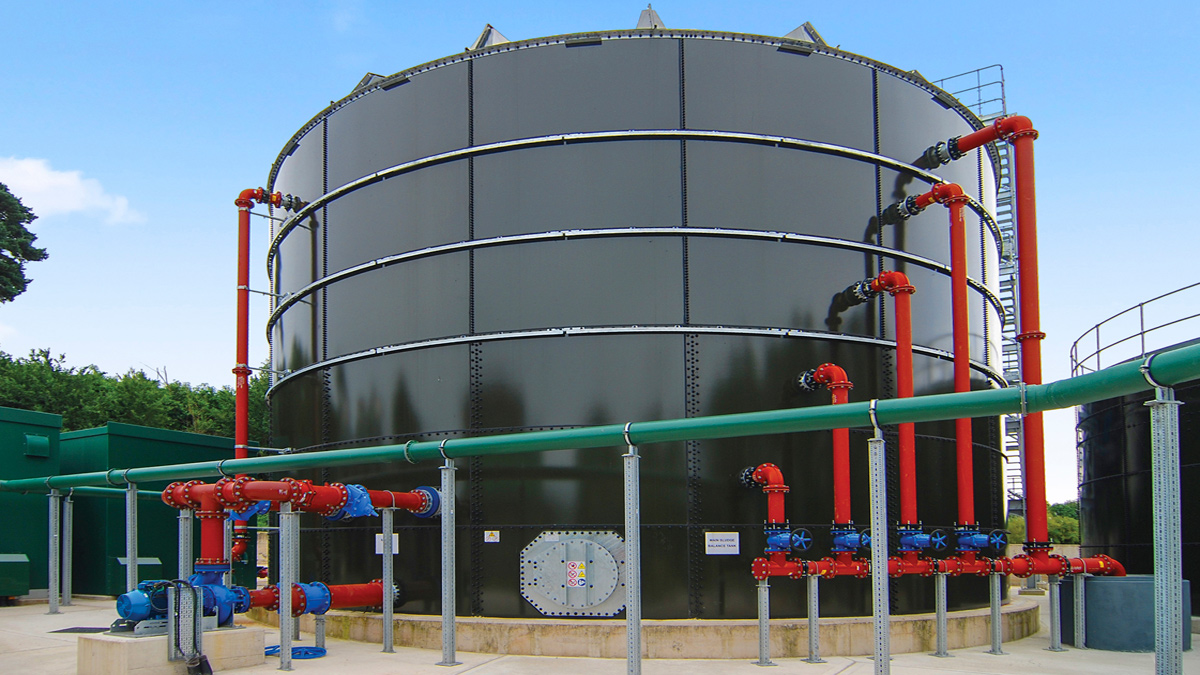
1018m3 thickened sludge storage tank – Courtesy of Galliford Try
Existing works
The Brancote STW is split into two streams; the old works treating 65% of the sewage flows and the new works treating the remaining 35%. The settled primary sludge from the old works gravitates through the existing Huber Rotamat indigenous sludge screens and is then pumped into the existing 37m2 picket fence thickener (PFT). The settled primary sludge from the new works is valved to gravitate through the Huber Rotamat import screens and is then pumped into a 390m3 blending tank. Imported sludge is pumped through the Huber Rotamat import screens and is then further pumped to the blending tank combining with the sludge from the new works. The existing PFT is undersized against design manual criteria, 9.1 m2/TDS (tonnes dry solids) versus 15 m2/TDS hence why the indigenous settled sludge is split for processing.
The PFT flows are then combined prior to the digestion plant in a blending tank with the imported sludges. The single digestion plant has an effective volume of 2544m3 (assuming 80% working capacity). Digested sludge is buffered in 3 (No.) holding tanks with the effective volume of 3000m3 which provide buffering for the 2 (No.) centrifuges. The centrifuges do not have capacity to treat sludge up to 2028 design horizon. Once dewatered the digested sludge cake is transferred to 4 (No.) cake storage bays for a period prior to been tankered off site.
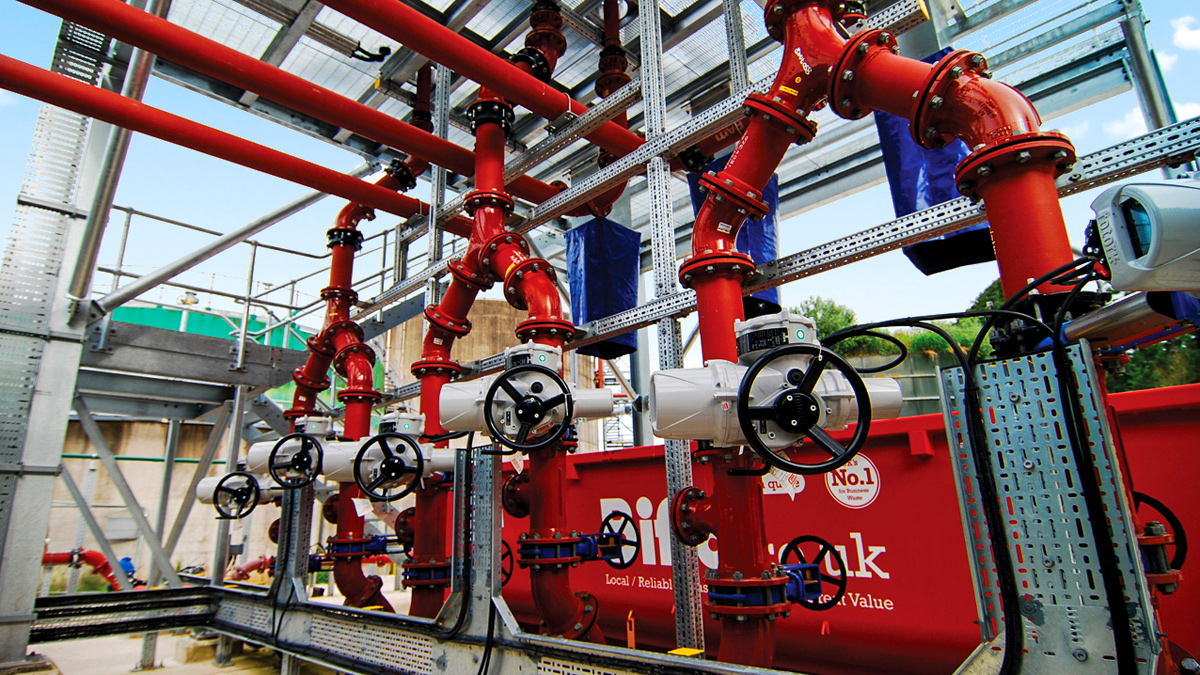
Automated Strainpress feed installation – Courtesy of Galliford Try
Technical solution
The proposed technical solution was to build a new facility that is capable of receiving the indigenous sludge and processing this through a new correctly sized PFT before being transferred to a liquid thickened sludge balance tank (TSBT). A new template sludge import facility was to be constructed which could accept 2 (No.) sludge tanker discharges simultaneously prior to being transferred to TSBT.
All sludges prior to entering the TSBT are to be screened using Strainpress equipment to 2mm in 2 dimensions. The TSBT had to be designed for 3-days storage, require a mixing arrangement to ensure a homogenous mix between the indigenous and imported sludges and required additional standard decant valve tree for removing the top waters (if required).
A duty/duty centrifuge system along with a polymer chemical dosing system would process the liquid sludge from the TSBT dewater to 25% DS and transfer these to a 5-day capacity cake storage silo complete with a cake dispensing system for the cake transport vehicles.
An auxiliary centrate balance tank (CBT) and pump transfer system was required to handle the PFT and centrifuge centrate liquors as they are required to be transferred back to the head of the STW over a 24-hour period.
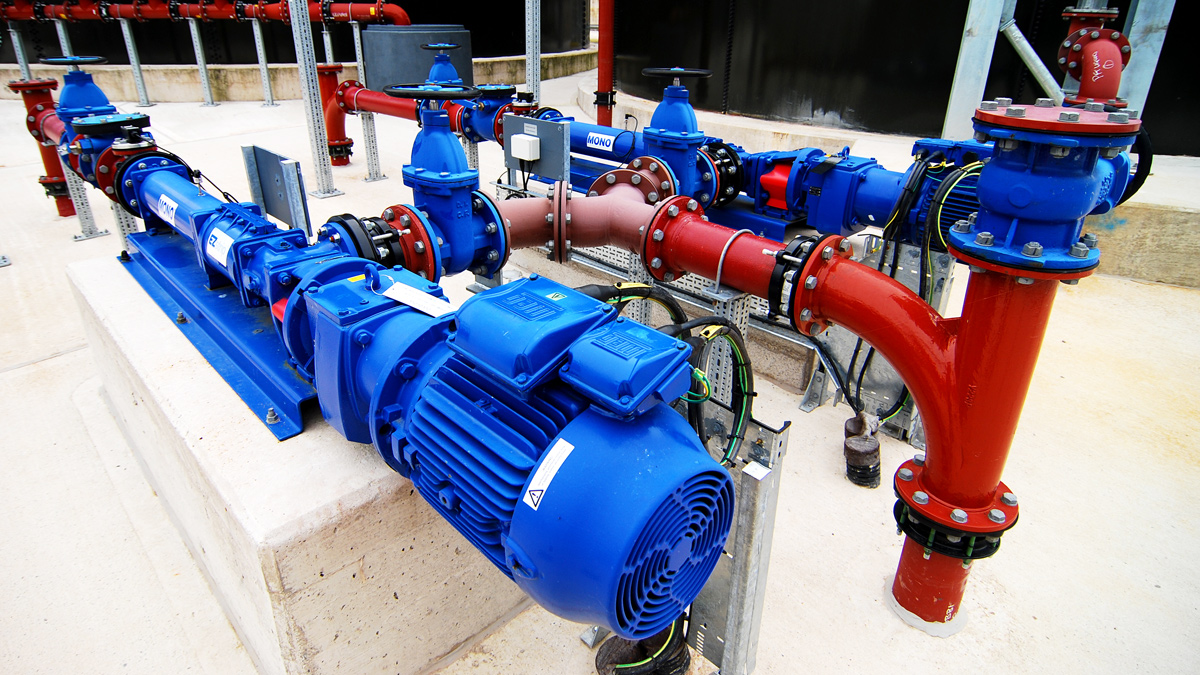
Thickened sludge transfer pumps – Courtesy of Galliford Try
Design phase
Ultimately the single largest difficulty to overcome on this project was space. The whole of the new STC works required to fit into an area 60m x 40m. To ensure this succeeded additional discussions and solutioning work were undertaken between the client and Galliford Try and is discussed later in the article. Adding to the complexity, the build area was centred between the existing STC plant and the cake storage bays, meaning that the construction works had to ensure continued normal operation of the existing sludge digestion process.
All sites are scanned using a Faro3D laser scanner to generate a point cloud of the existing site from which a 3D model was created in 3D building information modelling (BIM) software, Autodesk Revit. Other surveys were imported such as topographical and underground surveys to provide pertinent and complete information to develop the site arrangements.
Each subcontractor submitted their designs in compatible 3D models which were then imported to the master model. These models included the largest tanks down to simple pumps and lifting equipment.
The design team extensively use Autodesk360 cloud-based viewing platform for review and comments by the client and other parties. By converting the model to virtual reality (VR) we were able to use the VR headset to undertake design reviews and hazard and operability (HazOp) studies with the client prior to construction at key stages throughout the project.
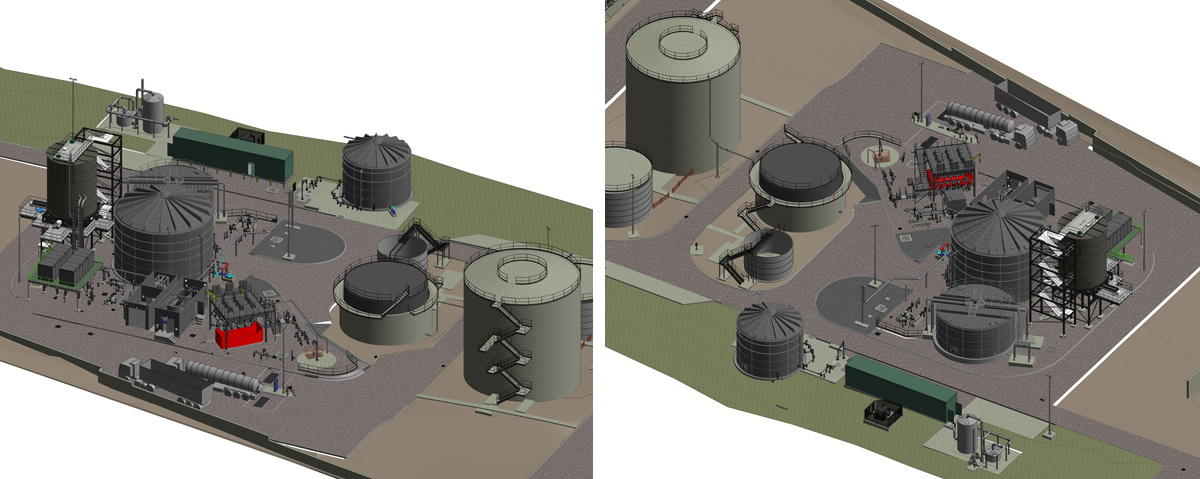
Digital twin of the installed assets – Courtesy of Galliford Try
Brancote STC: Supply chain – key participants
- Principal contractor: Galliford Try
- Ecology/environmental consultants: RammSanderson Ecology
- Motor control centre & ICA: MCS Control Systems
- Electrical installation contractor: Mealey Electrical Contractors Ltd
- Mechanical installation contractor: De Havilland Engineering
- GRP enclosures: Pro-tech GRP Enclosures Ltd
- Ram pumps: EMS Industries Ltd
- Cake silo system: CTM Systems Ltd
- Submersible pumps: Grundfos Pumps Ltd
- Mono cake pumps: NOV Process & Flow Technologies
- Lifting equipment: T Allen Engineering Services Ltd
- Glass fused to steel tanks & PFT mechanical fittings: Stortec Engineering Ltd
- Trace heating and lagging: Jade Insulation Ltd
- Screening equipment: Huber Technology
- Shaft tank: HB Tunnelling Ltd
- Chemical dosing equipment: Northern Pump supplies
- Demolition and groundworks: Collins Earthworks
- Odour control systems: Odour services International
- Prefabricated plastic tanks: Moor Fabrications Plastics Ltd
- Centrifuge plant: Alfa Laval Corporate AB
- Pumps and mixers: Hidrostal Ltd
- Telemetry services: JR Pridham Sevices Ltd
- HV power systems: Central Power Ltd
Processing plant
Sludge imports: The new sludge import facility required a 60m3 below-ground wet well; however due to the close proximity of the existing water sealed gas holder and the high water table mixed with running sand, this made normal excavation activities non-viable. Galliford Try engaged with HB Tunnelling Ltd to install a shaft tank with concrete plug running to a depth of approximately 8m. The pumping station was then capped off with a prefabricated concrete biscuit lid delivered and installed in 2 sections. The sludge pumping is facilitated by duty/standby Hidrostal Ltd open impeller type pump arrangement to deliver 60m3/hr at a pressure of 1.2bar.
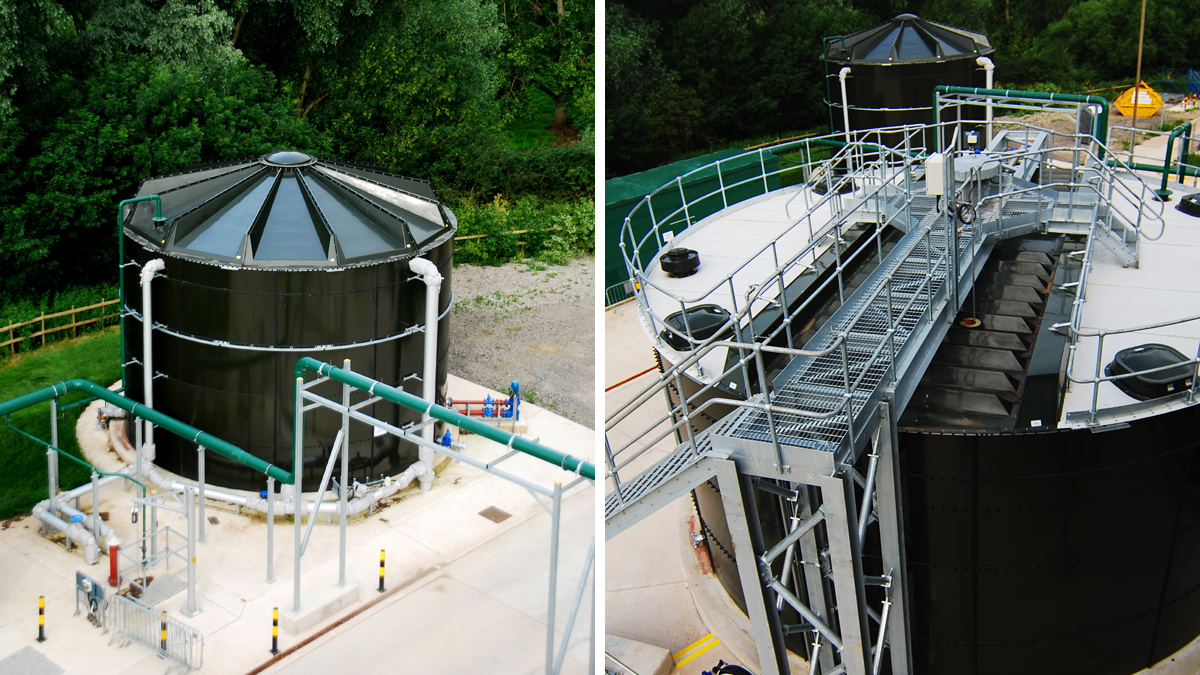
(left) Centrate balancing tank and (right) 94m3 picket fence thickener – Courtesy of Galliford Try
Picket fence thickener (PFT): During solutioning works the team reviewed construction options for all process tanks from below ground to above ground vessels. Materials such as glass fused to steel (GFST) and prefabricated concrete were reviewed; the solution finally settled on above ground GFSTs.
There were 2 original solutions for the PFT, the first retained the existing undersized existing PFT, however upon inspection of its poor condition the risk to the process was deemed too great, additional a TSBT of 1490m3 @ 19mØ would have been required and would severely impact on our available space. The second option included using the existing PFT and providing a further PFT asset of 59m3 to increase the thickening capacity to comply with the client’s design manual criteria. This option allowed for a more manageable 1018m3 @ 13mØ TSBT, however the risk of the existing asset still remained and provided additional complexity with now having to unevenly split the flow between two different sized assets.
Having discussed options with the client the design was changed to provide a new 94m3 PFT which has a throughput of 6.4 TDS/d, 641m3/d @1%DS, thus allowing the retention of the smaller TSBT option. The PFT constructed rise up 4.8m @ 11.5mØ. The concrete base had a slope of 1.5 degrees to the centre. The PFT along with all the GFSTs on the project and PFT mechanical fittings and access steelwork was undertaken as a design and build package by Stortec Engineering Ltd.
Strainpress screening: Both imported and indigenous sludges required screening to 2mm in two dimensions dictated by the downstream THP projects and had a client specified Strainpress process. To ensure that the solution allowed both sludge streams to have a duty/standby screening facility, an automated valved feed system was designed to allow the 3 (No.) Strainpresses to work as a duty/duty/common standby for all process streams.
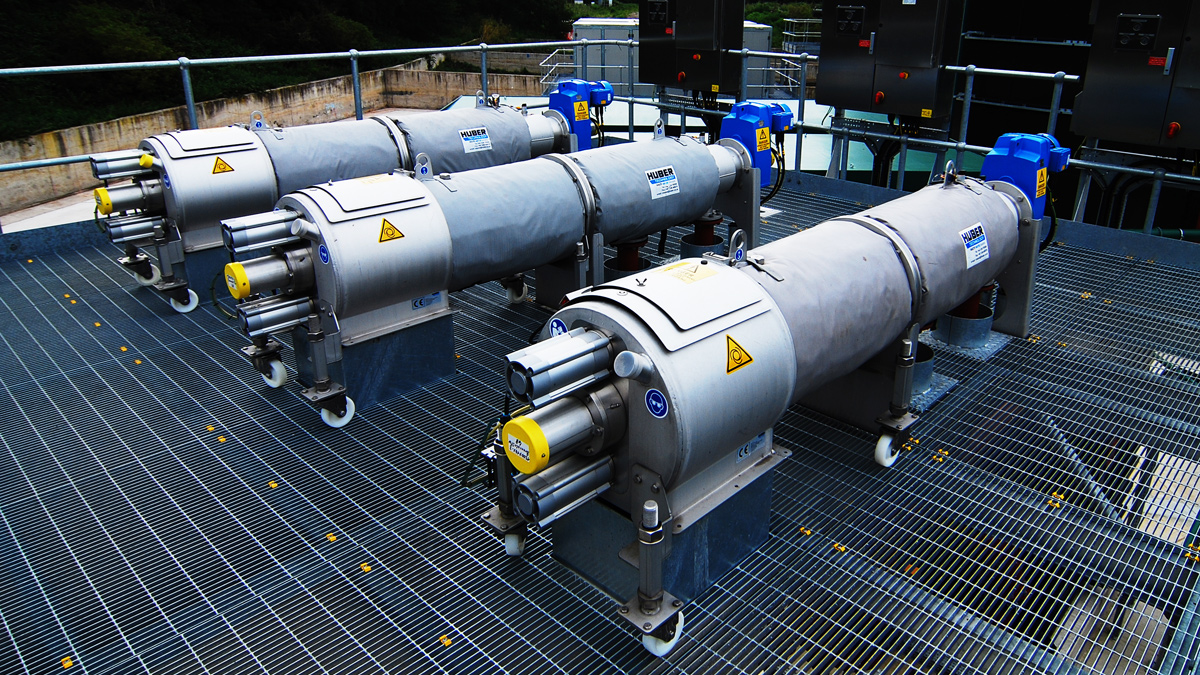
Huber Technologies Strainpress installation – Courtesy of Galliford Try
As the screens work on a pressurised pumped system with a gravity discharge, the screens are required to be mounted on a raised platform 4.7m high to allow discharge of the screenings to the single skip below; the system is capable of processing 60m3/hr of sludge at a thickness of 6%. A complete Strainpress solution including steelwork access platform was designed, manufactured and installed by Huber Technologies.
Thickened sludge balance tank: As previously stated, a 1018m3 (8.4m @ 13mØ) GFST has been installed to provide a 3-day storage capacity for the liquid sludge, and therefore allows the normal running of the centrifuges 5-days per week. An 18.5kw Hidrostal mixer was provided to ensure that the sludges have a homogenous mix. Additional functionality has also been embedded by providing a standard valve decant pipework tree allowing top liquors to be taken off prior to mixing; the decanting tree also allows the ability during commissioning to adjust the thickness of the sludge so that the performance criteria can be tested and verified.
Centrifuge system: A duty/duty centrifuge system (G3-95) installation provided by Alpha Laval gives a process capacity of 18.3m3/h @ 4% sludge per unit running for 80hr/week; but is also capable of meeting the process volume of 26.3m3/h as a duty only centrifuge running for 168hr/week and requiring an output in both scenarios of 23% ±2% DS. Both centrifuges are installed on a combined raised platform designed and manufactured in house by Galliford Try and are housed in full acoustic enclosures provided by Alpha Laval.
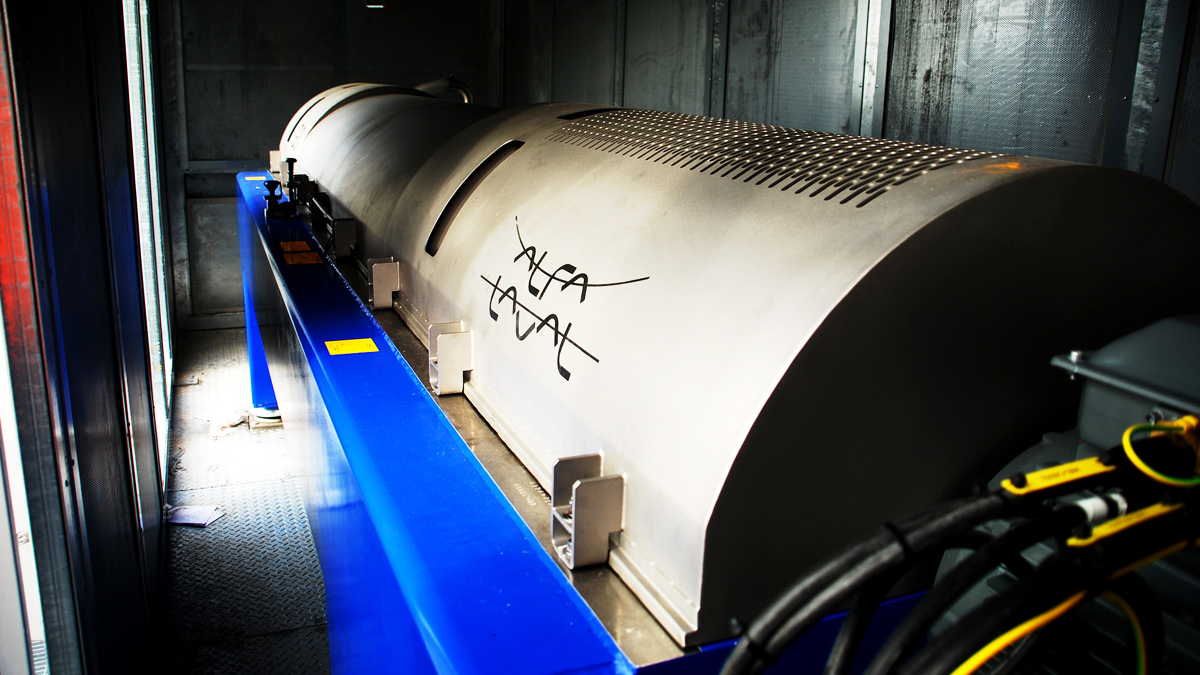
Centrifuge No.1 – Courtesy of Galliford Try
Polyelectrolyte dosing system: A full design and build package was let to Northern Pump Supplies to provide a big bag polyelectrolyte dosing system. The solution includes 2 (No.) GRP buildings, the first being for the dry storage of 2-weeks requirement of granular polyelectrolyte and contains the powder dispensing hoist and metering equipment. The second GRP building is a fully self-contained bunded structure which houses the batching and running equipment for the chemical along with the duty/standby dosing pumps. The system is designed to deliver a maximum dose of 15kg/TDS at strength of 0.3% and a volume of 7m3/h.
Cake handling: The original solution for the cake handling included a conveyancing system from underneath the centrifuges to the top of the cake silo, but due to the available space and size of silo, it was evident that this would not be feasible. Then during the design stage several contractors were approached to discuss available options which led to placing the contract with CTM Systems Ltd, who were able to show through significant experience that a cake progressive cavity pump system would provide the required solution within the confines of the limited space available. Below each centrifuge sits a dedicated Mono cake pump, each capable of pumping 5.4m3/hr @ 17-30% DS to the cake silo. CTM Systems were able to provide a full cake silo, support and access steelwork, cake pump, and cake dispensing design and build package.
The 326m3 silo (9m high @ 6.8mØ) was raised by 6m to allow the cake transport vehicles to manoeuvre underneath the structure for the cake to be dispensed. The silo GFST was assembled at ground level and the raised in one crane lift onto the structure, removing the difficulty of assembly above ground level.
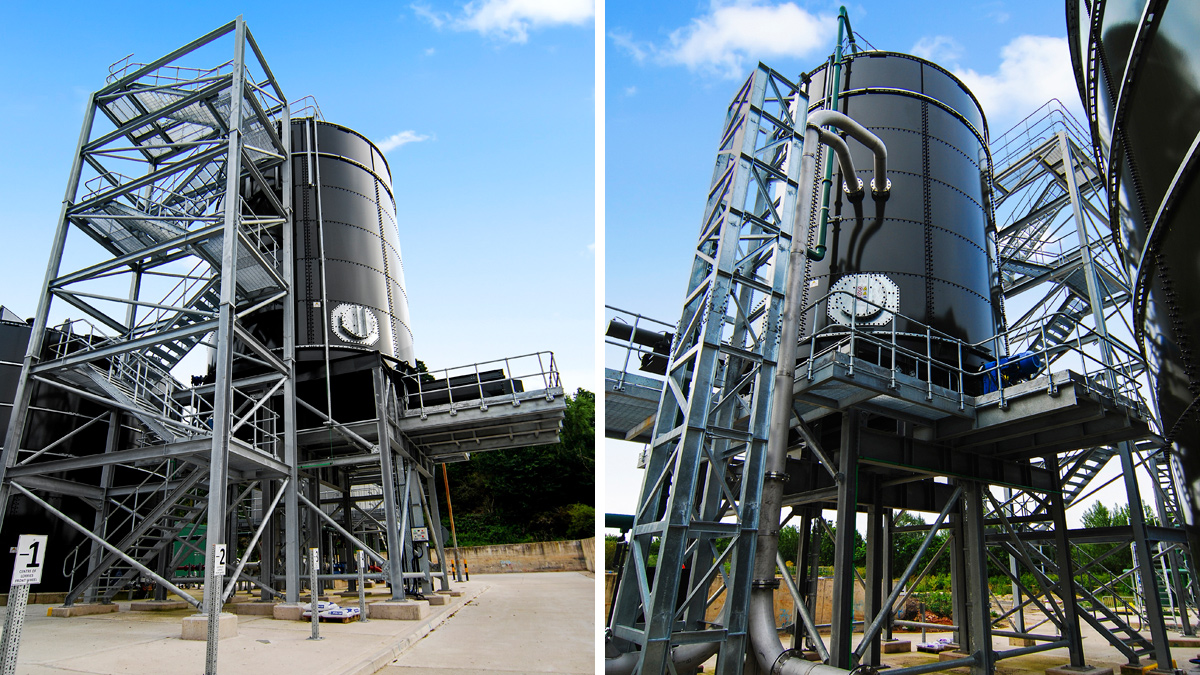
(left) Cake silo and discharge road and (right) cake silo north view – Courtesy of Galliford Try
Liquors: The two sources of liquors (PFT and centrifuges) return back to the STW process. The design assumes that liquors generated from the PFT occur consistently over a 24-hour period and therefore do not require further intermediate balancing. Due to the large volumes of imports and the potential resultant septicity and strength, the liquors are pumped to a 400m3 GFST for balancing over a 24-hour period with an outlet rate of 14.7m3/h.
Odour control: One key critical success factor for the project was to have no additional odour production at the site boundary. Therefore, Severn Trent procured a baseline odour survey. A full site-wide odour abstraction system provided by Odour Services International Ltd has been installed to all key assets for the removal and treatment of fouled air. It has a capability of treating 2,048m3/h of air volume utilising both a Lavarok® biofilter (20m3) and a carbon filter for secondary polishing (2.28m3) connected in series, all providing a performance requirement < 1,000 ouE/m3.
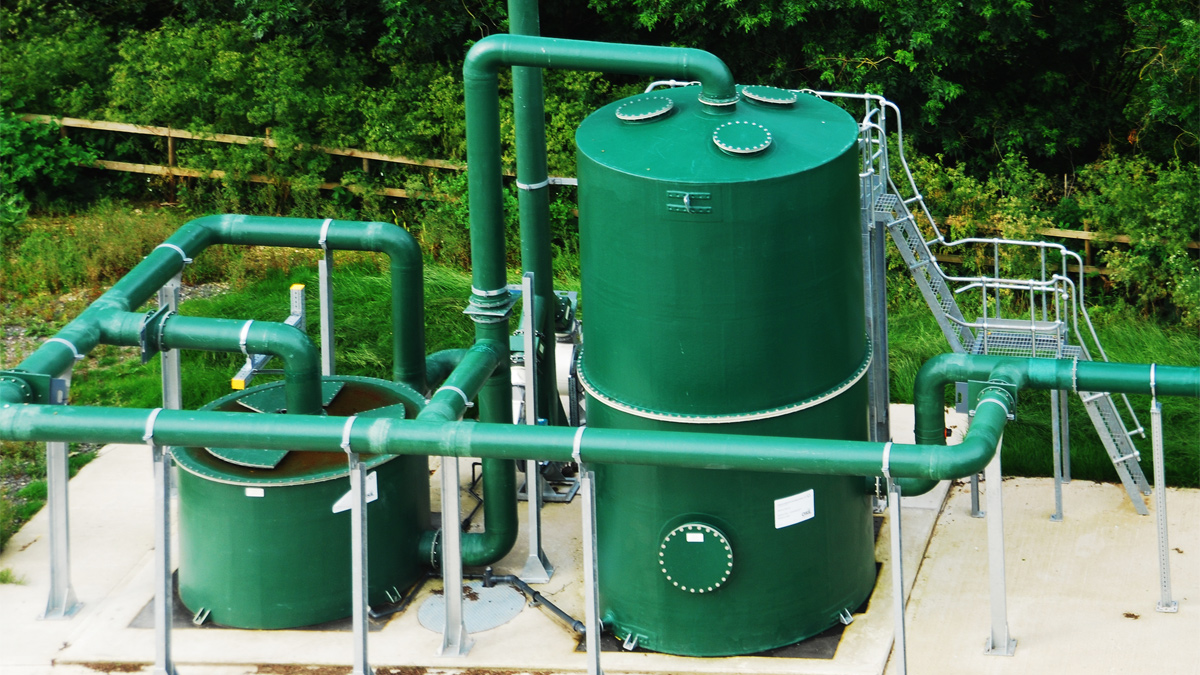
Odour control plant – Courtesy of Galliford Try
Success criteria/commissioning
At the time of writing (June 2020) the project has undergone dry and water commissioning. The programmed sludge commissioning is due to commence mid-August 2020. The project performance criteria is as follows:
- All sludge has been screened to 2mm in two dimensions with Strainpress.
- A homogeneous sludge fed into the centrifuges with a variance of ±0.2%DS/hr (as measured with the online %DS monitor). The feed %DS will vary depending on the volume and source of imports.
- Combined maximum centrifuge throughput of 30 m3/h (1394 kg/h) measured pre-poly dose or 37 m3/h (1415 kg/h) measured post- poly dose.
- Cake dry solids 23 ± 2%.
- Poly dose < 10 kg/TDS on average.
- Poly dose < 15 kg/TDS when dewatering difficult sludge.
- Centrifuge solids capture rate of 97%.
- No increase in odour at the site boundary due to the scheme.
Conclusion
The contract started in March 2018 with the design phase running for 9 months, construction started February 2019 and was due to complete in March 2020 however due to unforeseen difficulties from external factors the completion is planned for August 2020. The project value was £4.25m.