Ashford WwTW (2014)
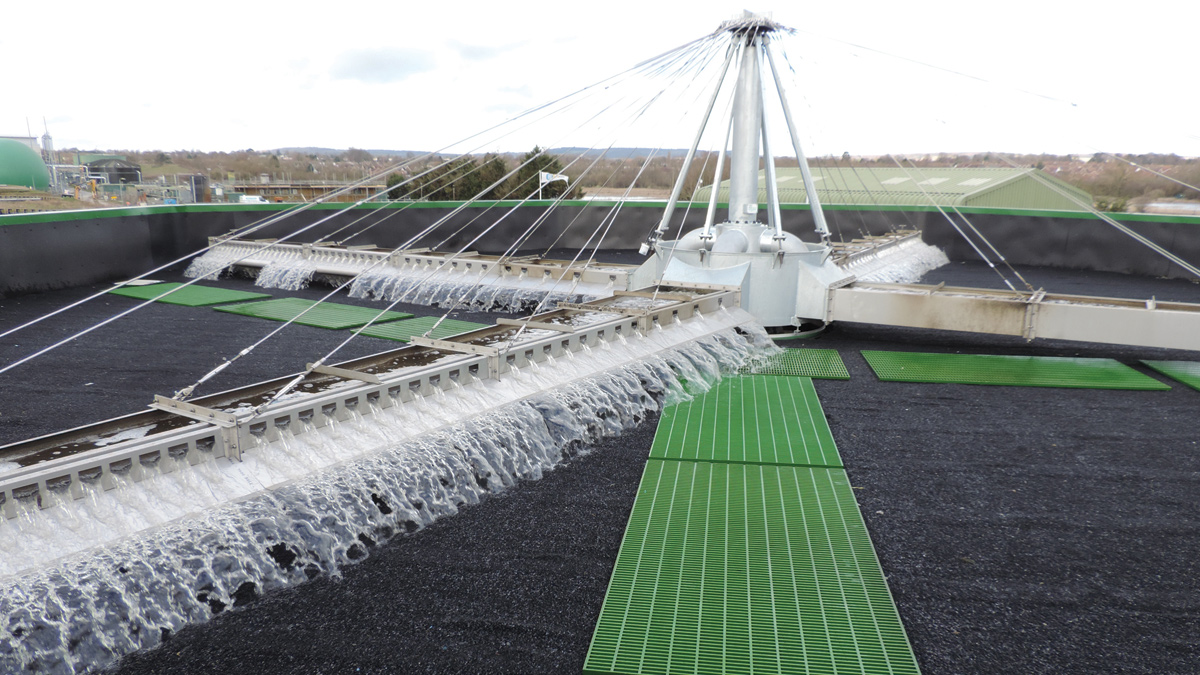
The New NTF starts to seed - Courtesy of Southern Water
Ashford WwTW is located approximately 15 miles north-west of Folkestone in Kent. Prior to Southern Water’s £12.6m expansion, the works served a population equivalent of 100,000 people. Starting in June 2012, this extensive project will ensure that the site continues to serve the growing population of this busy catchment, which is forecast to rise to 130,000 by 2020. To cater for this increase in demand, Southern Water has invested heavily in upgrading and modifying the process units at the site. When complete in March 2014, there will be an increase of 30% in the Full Flow to Treatment (FFT) from 547 to 694 litres/second. As well as providing extra capacity, the new equipment also had to help meet tightening environmental permit limits. Under the National Environmental Programme, the new consents are 20mg/l Suspended Solids, BOD 10mg/l, NH3 2mg/l, Fe 4mg/l and P 1mg/l.
Works requirements
The following works were identified for the extension in order to meet the consent standards and forecast rise in the PE:
- Upgrading of the inlet works.
- Refurbishment of the 16 (No.) biological filters.
- Construction of a new humus desludging pumping station and MCC kiosk for pump sets.
- Construction of 2 (No.) 27-metre diameter humus tanks.
- Construction of a new nitrifying trickling filter (NTF) to join the three already on the site and an elevated walkway to link the four together.
- Construction of 2 (No.) deep bed sand filters (DBSF) to join the six already on the site.
- Refurbishment and upgrade of the works return PS.
- Refurbishment and upgrade of the NTF feed PS.
- Refurbishment and upgrade of the DBSF feed PS.
- Refurbishment and upgrade of wash water pump set.
- Associated chambers, manholes, pipelines and ducts.
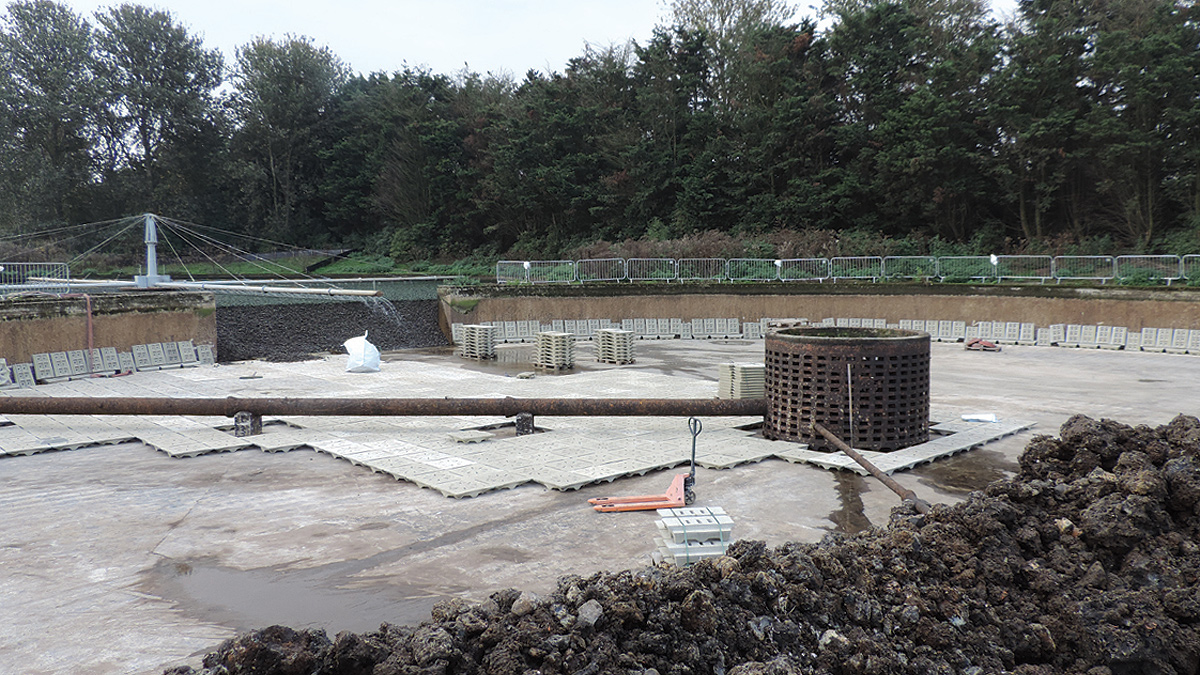
The second of a conjoined set of filters gets refurbished -Courtesy of Southern Water
Inlet works
The new inlet works was required to accept an uplift in flows up to a predicted peak flow to works of 2000l/s. The existing screens were replaced with 4 (No.) Longwood Escalator fine screens 6mm 2d that were placed into the existing inlet works structure with the minimum of structural modifications. A means of by-pass in the event of more than one screen being unavailable was also built into the design by installing a new manually raked screen in a dedicated channel with its own actuated penstock.
The existing penstocks had to be refurbished and new penstocks installed where required upstream of the inlet to allow progressive operation of the screens and screen rotation. The bypass screen penstock was fitted with an actuator with battery back-up. Manual penstocks were installed at the rear of each screen for isolation purposes.
Longwood Combi wash screenings handling units were also installed. The size of these units was calculated based upon the predicted screenings load from a population of 250,000 based on all flows being pumped. The screenings are washed via launder channels into the 4 (No.) Longwood units situated at ground level adjacent to the inlet works. Suitable skip handling/covers were also supplied. The wash water requirements for the new equipment has also been upgraded.
In addition, a new MCC and standby generator were installed to control the new equipment and ensure its resilience in the event of power outages.
All of the above works was carried out and commissioned with the existing inlet works live and flows uninterrupted. This was achieved by carrying out the work in two phases, with half of the new equipment being installed in each phase.
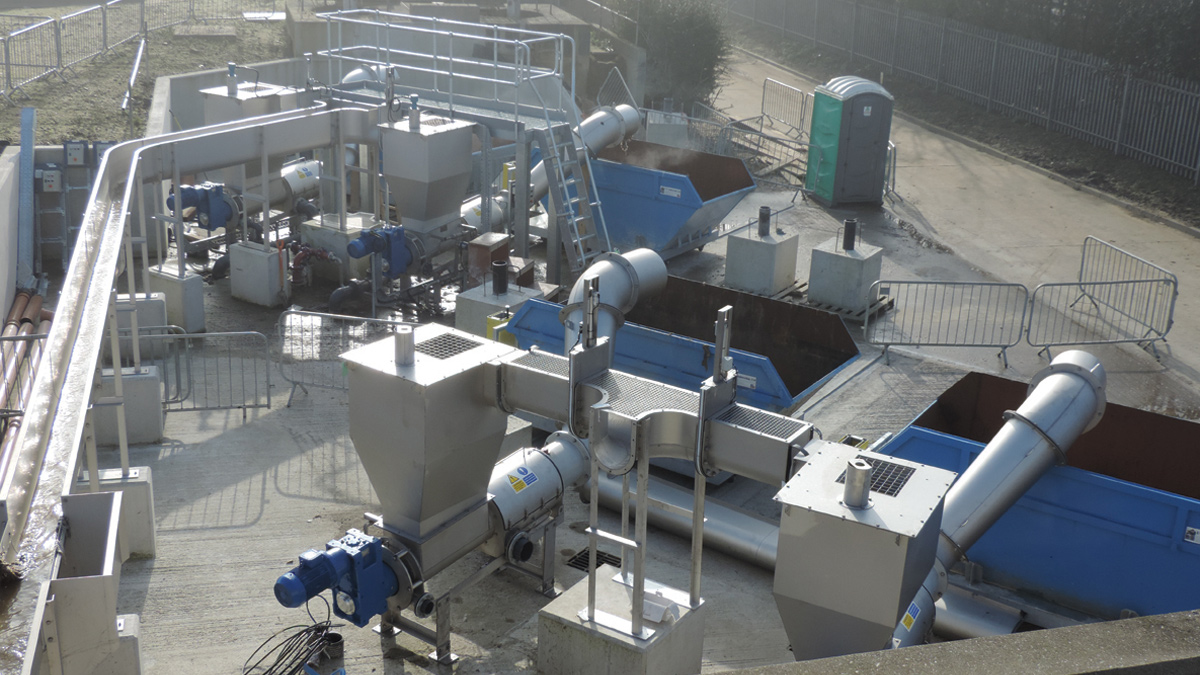
The new screenings handling area nears completion – Courtesy of Southern Water
Biological filters
There were 16 (No.) filters in all to refurbish. 6 (No.) filters contained blast furnace slag (BFS) media which was washed and reused in the filters. The remaining 10 (No.) filters contained clinker media that was washed on site and then taken away to be recycled.
New BFS media was supplied and installed into these 10 (No.) filters. Replacement of all underdrain tiles took place and pipework and valves were also refurbished.
New motorised drive arms and columns were fitted to the existing 16 (No.) filter bed distributors which were designed to accept a combined flow rate of 874l/s. Only 2 (No.) filters at any one time could be taken out of service for refurbishment. So the critical path for the project went through this part of the works.
A new flow distribution chamber was also constructed between the primary sedimentation tanks and the existing filters, with the flows distributed via four new actuated penstocks and magflow meters to the existing syphon chambers.
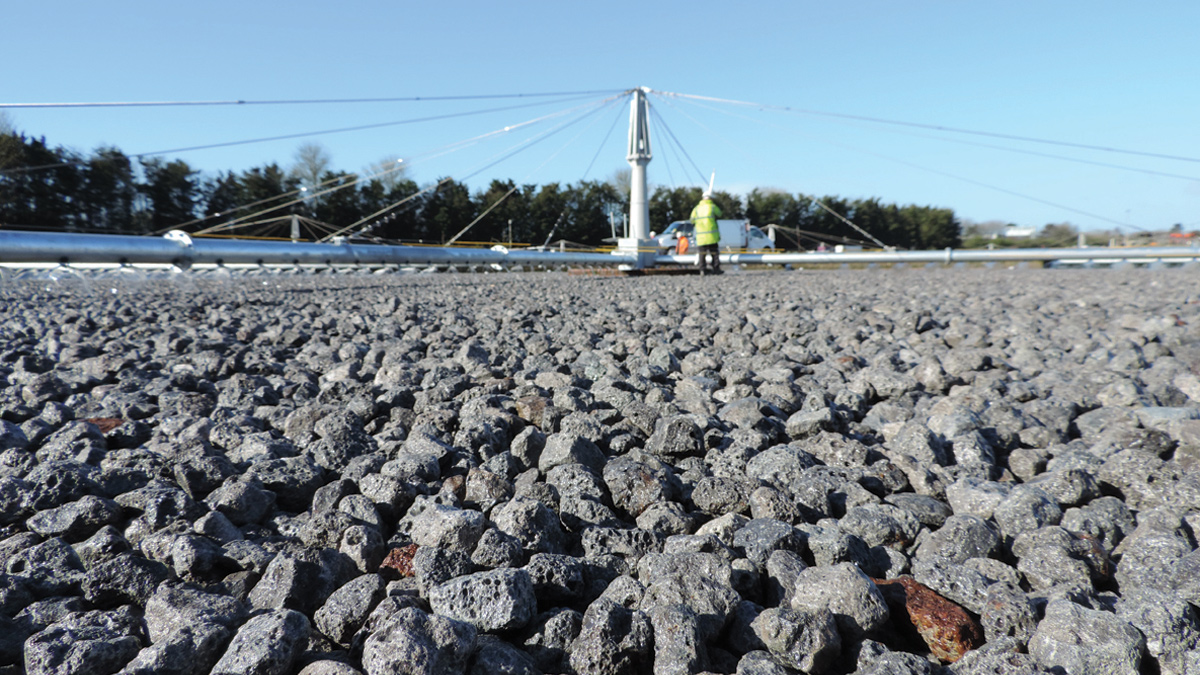
All 16 (No.) of the biological filter beds were refurbished. The final filter bed was officially switched on by Damian Green MP on 28 March 2014 – Courtesy of Southern Water
Humus tanks
FFT of 694l/s and a new distribution chamber on the effluent pipeline from the set of 16 (No.) filter beds was also constructed to distribute flows through two pipelines to the two existing banks of 4 (No.) humus tanks and a new gravity pipeline to flow split chamber feeding the new humus tanks 9 and 10. Again this chamber was built over live pipes that had to be kept in service throughout construction and commissioning while also putting in new magflow meters and actuated penstocks within the existing as well as the new works.
Two new radial flow humus tanks 27m diameter x 2.5m wall depth were also constructed complete with new scraper bridges and duty/standby humus tank desludging pumps (rated at 5l/s each), scum removal boxes connected to works drainage lines. The new desludging pumps discharge into an existing works return gravity line and were integrated into the existing humus desludging regime to ensure only one tank was desludged at any point in time. The installation of new gravity pipe work to take humus tank effluent from these new tanks to the existing NTF lift pumping station was also part of the scope.
The supply and installation of a new MCC panel in its own kiosk adjacent to the new tanks was also included.
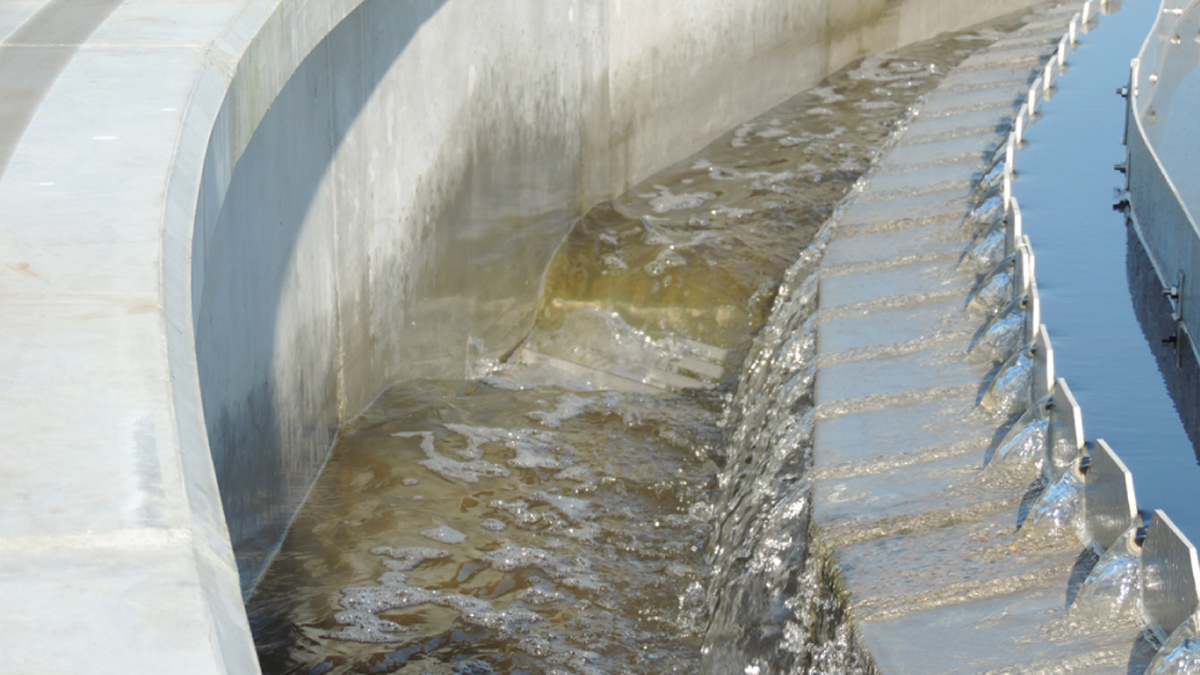
The new humus tanks come on line – Courtesy of Southern Water
Works return
The existing works return pumping station was totally refurbished with new pumps, pipework and MCC to pump the 150l/s peak works return flows back to the PST distribution chamber along a new rising main.
A new auto start/auto changeover generator for the works return station and wash water system at the existing recirculation pumping station was also installed along with the supply and installation of a new washwater pumping station and rising main to feed the new inlet works washwater system.
Tertiary treatment
As part of the tertiary treatment upgrade new gravity pipework to take humus tank effluent from these new tanks to the existing NTF lift pumping station had to be installed as well as providing larger pumps and pipe work within the existing NTF pumping station structure. In addition a new fourth NTF filter bed, 20m diameter x 5m high, to match existing three NTF filters, was constructed.
This filter included a filter distributor the same as that fitted to the existing units and was integrated into the existing filter flushing regime software. A new elevated walkway from existing NTF distribution chamber was supplied and installed which also carried the 600mm feed pipework. A snail trap was built into the effluent line from new NTF to the DBSF pumping station.
Increased size pumps and pipework within the existing DBSF pumping station structure had to be installed along with their associated VSDs. Two new matching Tetra rapid gravity sand filters rated at 27m x 3m were added onto the existing bank of 6 (No.) filters and integrated into their current flow/backwash/dirty backwash return systems and then functionally integrated into the SCADA system.
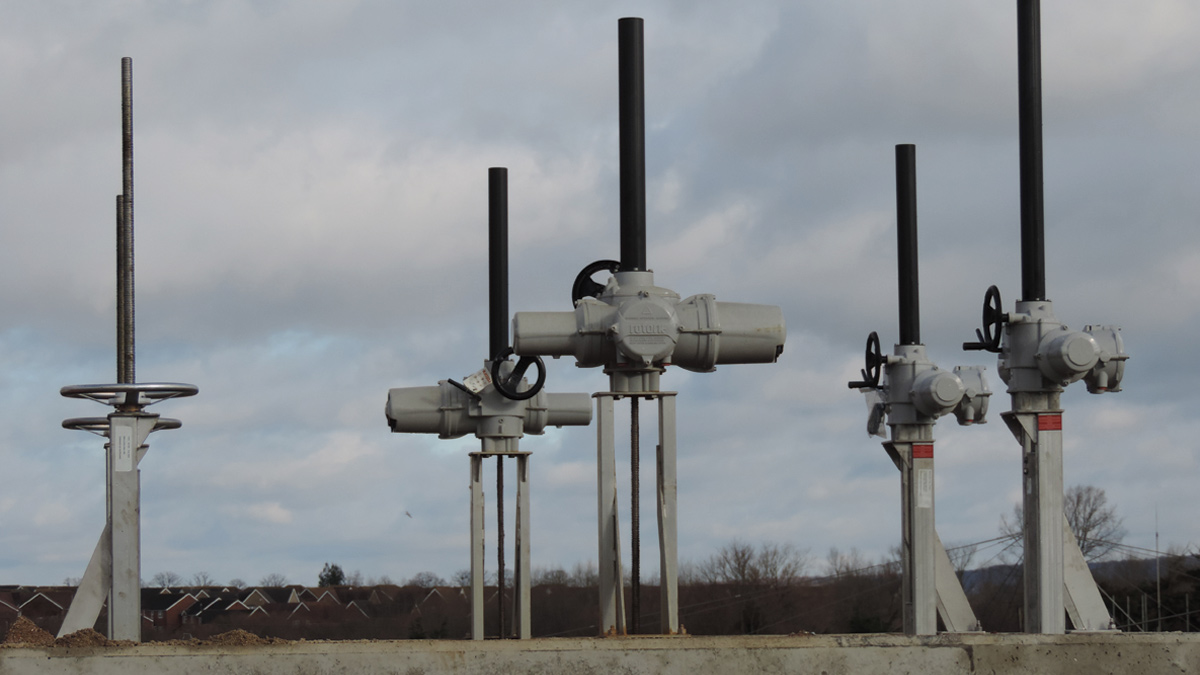
A forest of actuated and manual penstocks on the new filter distribution chamber – Courtesy of Southern Water
Undertakings
In March 2012, Southern Water appointed BTU (a joint venture between Trant Holdings Ltd and Barhale Plc formed solely to service Southern Water on their MSF contract for AMP5) as principal contractor for the extension works of Ashford WwTW. BTU, along with their delivery partner, URS, undertook the design and construction of the project.
Ashford WwTW: Supply chain – key participants
- Main designer: URS
- Temporary works designers, Civils installation and Access and stairs manufacture: Barhale Plc
- Inlet screens, screenings handling plant and launder channels: Longwood Engineering
- Refurbishment of the 16 biological filters – Filter arms: Ashbrook Simon-Hartley
- Refurbishment of biological filters – Media: Day Group
- Construction of humus tanks and DBSF – Shell: Carlow Precast (now FLI Precast Solutions)
- Humus tanks – Scraper bridges: AJ Fab Tech
- Construction of a nitrifying trickling filter: Sewaco Ltd
- New nitrifying trickling filter – Media: Hewitech UK Ltd
- Washwater Pumps and Boosters: KGN Pillinger
- Standby Generators: Broadcrown
- Formwork and Concrete: NBC
- MCC/Systems integration: Max Wright
- MCC/Systems integration: MCS Control Systems
- Piling: Roger Bullivant
- Mechanical Installation: Arnolds Environmental
- SCADA & Telemetry configuration: Multiform Technologies
- Electrical installation: FSD Ltd
- Deep bed sand filters – System: De Nora
- Works Return, NTF & DBSF Pumps: Xylem Water Solutions
- Sludge Pumps: Mono Pumps
- Actuated Penstocks: Invicta Valves
- Dewatering: WJ Groundwater
- MCC Kiosks: Industrial GRP
- Skips & Skip Transfer System: R & B Engineering
- Overall Site Commissioning: MCS
- Overall Site Commissioning: Multiform
- Overall Site Commissioning: Barhale
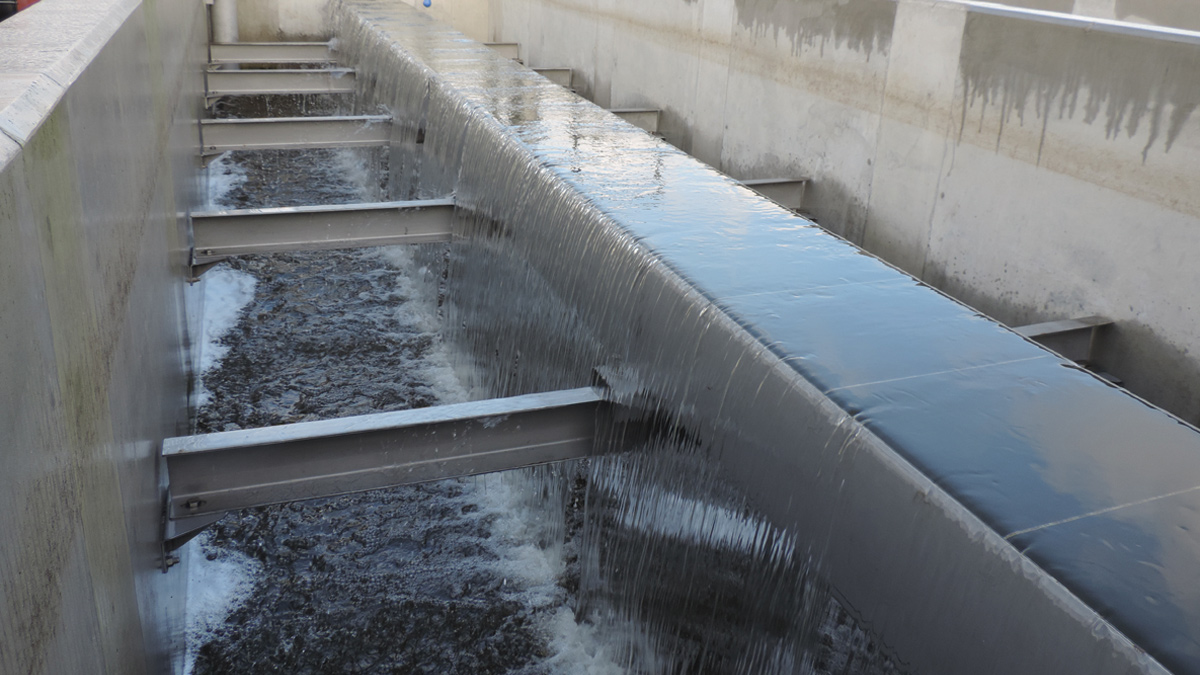
The new DBSFs come on line – Courtesy of Southern Water
Conclusion
The expansion ensures the treatment works continues to provide top quality wastewater treatment to the growing population of Ashford with extra capacity to allow for future population growth in the area. Southern Water’s continued investment in its infrastructure was praised by the town’s MP Damian Green who officially opened the site by switching on the final treatment tank. He said:
“It’s absolutely necessary that, as Ashford grows, our capacity to treat wastewater grows as well so I’m delighted to set in action the final part of a piece of important infrastructure which Southern Water has installed for the town.”
The final filter bed was officially switched on by Damian Green MP on 28 March 2014.