Wolsingham STW (2021)
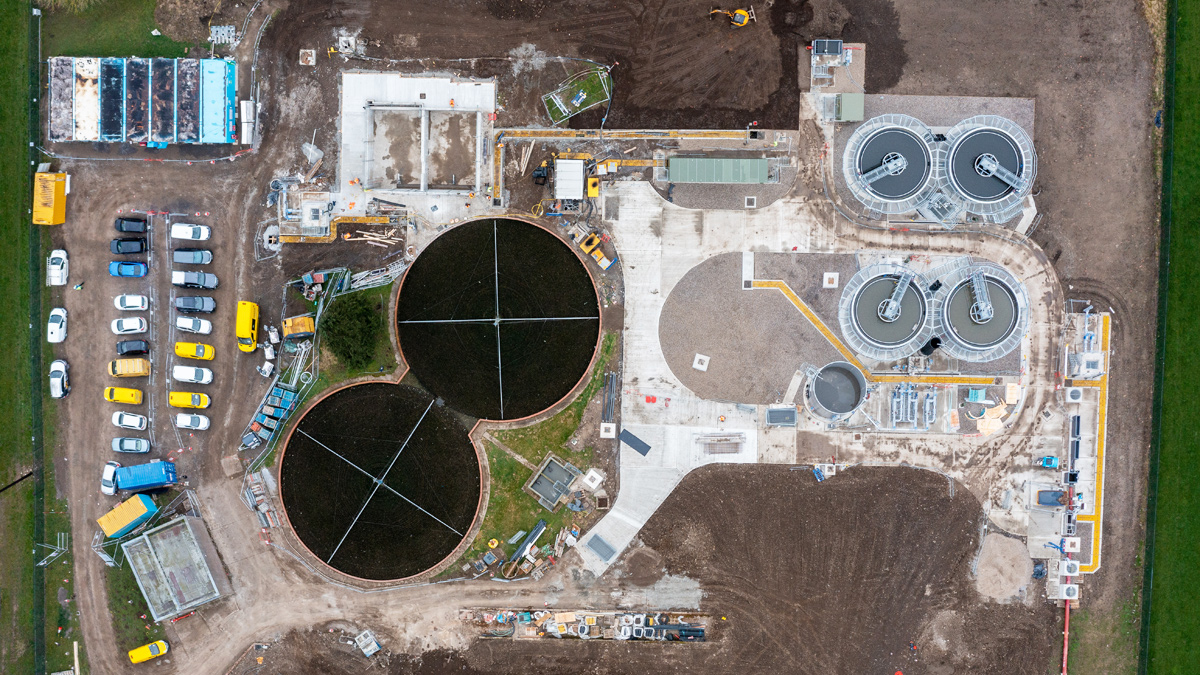
Wolsingham STW nearing completion (April 2021) - Courtesy of Tilbury Douglas
Wolsingham Sewage Treatment Works (STW) required upgrading in order to manage increased demand due to population growth in the catchment. The works, adjacent to the River Wear between Crook and Stanhope in northwest Durham, included a combination of new STW components and the upgrade of existing facilities. Northumbrian Water sanctioned the £5.77m project and Tilbury Douglas (principal contractor) and Wood (designer) began design work in 2018. The project embraced an ‘Off-site by Default’ principle, using innovative design and construction solutions that benefited the project in terms of reduced cost, schedule and environmental impact. Wood’s design and guidance demonstrated the benefits of Design for Manufacture and Assembly (DfMA) and off-site construction.
Main project drivers
The project was launched as a joint feasibility study to identify solutions to the issues at Wolsingham and within the sewerage networks serving the STW. The main driver was increased flows and loads; the original works served a population of 2,902, which was set to rise by 667. Additional works were required on the sewerage network to tackle asset deterioration and repeated pollution incidents linked to combined sewer overflow from surrounding areas. The facility had been suffering from performance-related issues and many of the assets had reached the end of their useful life. Asset deterioration combined with the strain of increased demand meant an upgrade was essential.
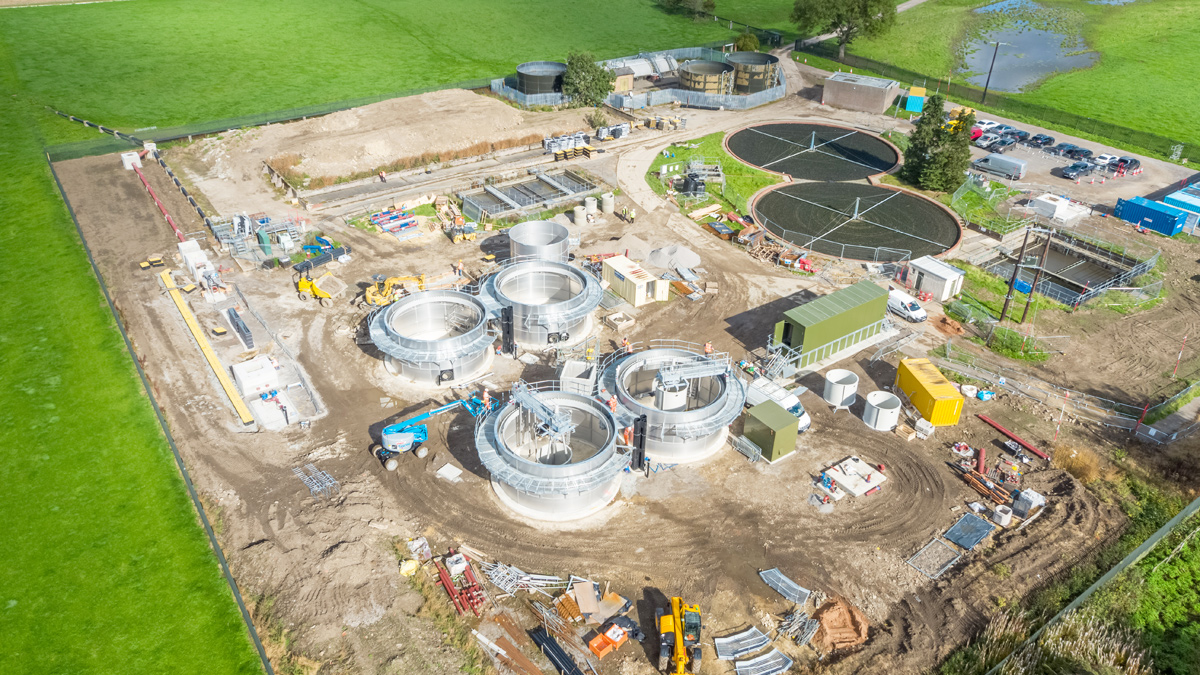
Aerial view of the site during construction – Courtesy of Tilbury Douglas
Scope of works
The scope of works included:
- New inlet works
- New connection into existing pipeline.
- Inlet screens replaced with new combined screen/screening handling units.
- New flow to full treatment overflow and associated pipework.
- New GRP primary influent pumping station.
- New primary settlement
- New automatic scum and de-sludge pumping station to discharge to a new sludge storage tank.
- New flow distribution chamber.
- 2 (No.) new above-ground primary settlement tanks.
- New humus settlement
- New GRP secondary interstage pumping station and rising main.
- New flow distribution chamber.
- 2 (No.) new above-ground humus settlement tanks.
- Conversion of existing HSTs to new storm tanks
- Existing work’s pumping station converted to storm return pumping station.
- New final effluent washwater booster set
- New intelligent MCC and kiosk
- Associated MEICA.
- Demolition and abandonment of redundant assets
- Existing primary settlement was backfilled.
- Abandonment and demolition of sludge storage tanks.
- Sludge drying beds backfilled and abandoned.
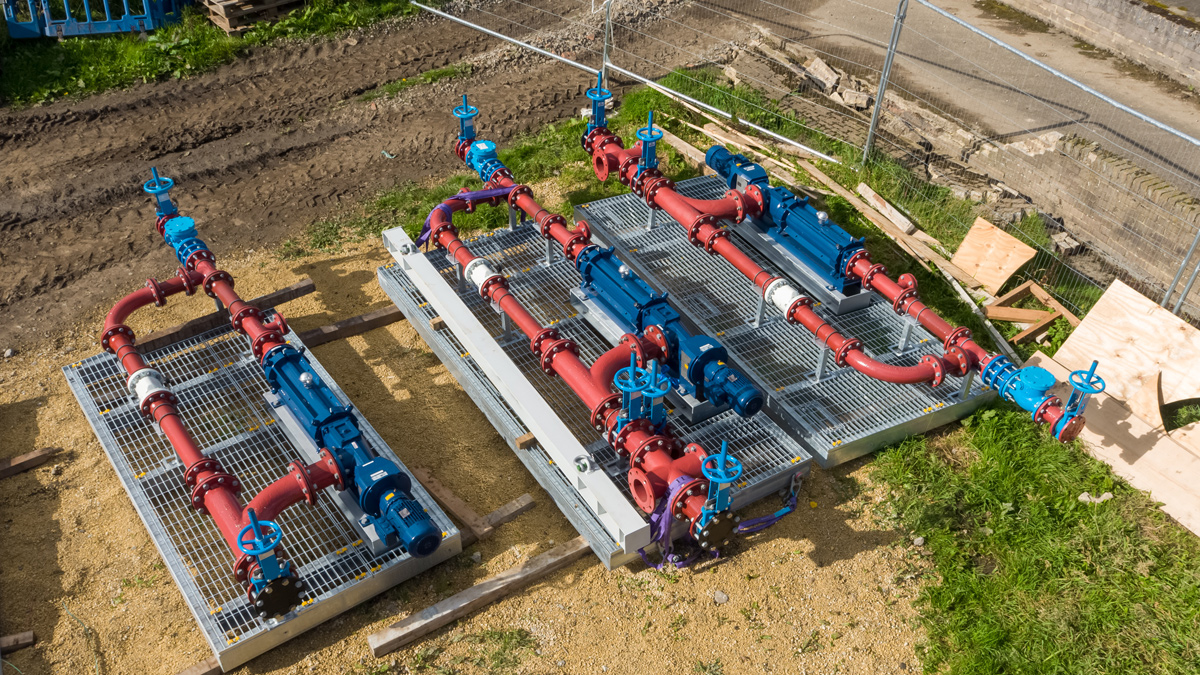
De-sludge pumping skids prior to installation – Courtesy of Seepex UK Ltd
Design: Challenging the scope
As population growth within the catchment area was a key driver, the original scope of works included work to upsize the Wolsingham sewer to handle increased demand. However, after reviewing the predicted growth figures, Wood and Tilbury Douglas challenged the scope based on the revised figures. These figures showed the increase in growth presented no requirement to upsize the sewer. This removed a large construction element of the project, reduced disruption to the public and eliminated the need for connections into live sewers, reducing the target cost.
Settlement tanks design
Material choice: The initial concept for the settlement tanks was for a conventional design approach involving concrete tanks poured in situ. Following the initial ground investigation, water-bearing gravel was discovered where the settlement tanks were to be sited. Also, the ground has a high water table, which changed the original design approach.
After early discussions with a dewatering specialist, it was agreed that an above-ground tank would be the most suitable option for the primary and humus treatment tanks (PSTs and HSTs). This would provide a safer and quicker alternative to working in saturated conditions below ground level.
During the detailed design process, an array of different materials was explored to see which would be most appropriate, whilst adhering to appropriate design guidelines and performance specification. One option involved part of the design being manufactured from bespoke precast concrete, completed by pouring concrete between the shuttering and precast sections at ground level.
The final material choice for the settlement tanks was stainless steel. The walls were to be bolted together to form the chosen diameter and it would be situated on a reinforced concrete base.
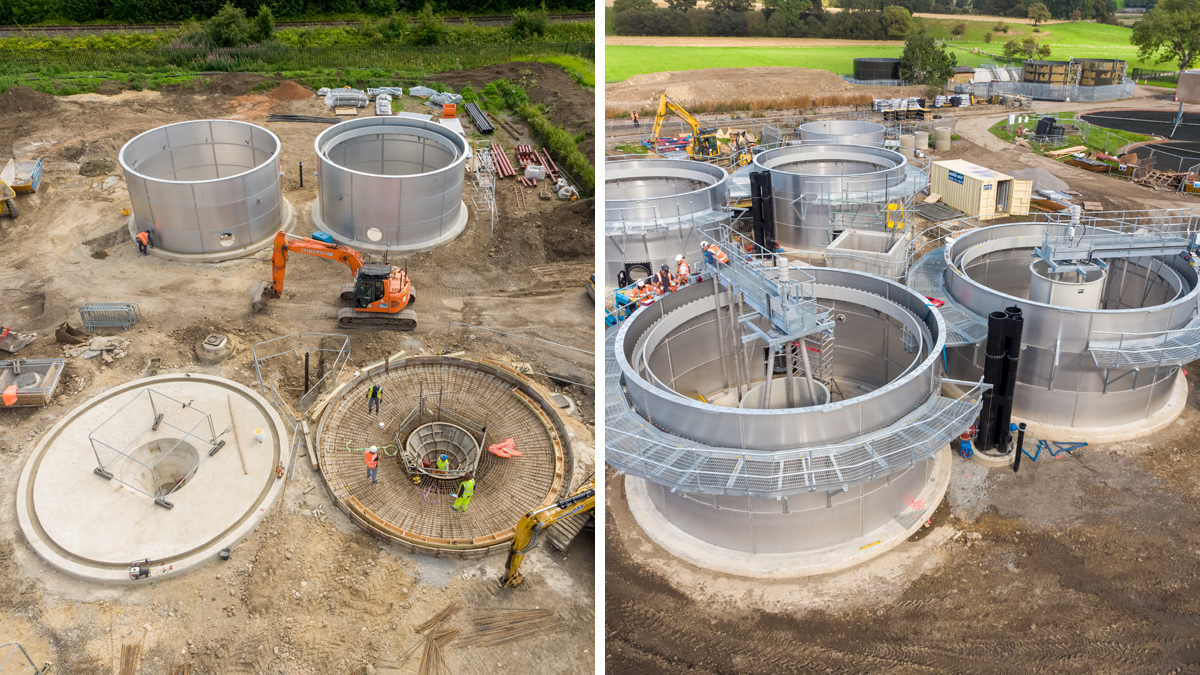
The stainless steel PSTs and HSTs under construction – Courtesy of Tilbury Douglas
Process: The preliminary treatment process has been upgraded with a new inlet screen, housed within a stainless-steel container with integral bypass overflow weir and channel, complete with a hand-raked inlet screen. The new inlet screen was accompanied with a new washwater package, which was part of the off-site build. Downstream of the inlet screens, a new Monitoring Certification Scheme (MCERTS) flowmeter was installed to measure incoming flows into the process.
Flows of up to 26.2 l/s are pumped from the new package primary influent pumping station to two new stainless steel radial flow primary settlement tanks via a new integrated distribution chamber. The co-settled sludge is then withdrawn on a regular basis from the tanks via the new automatic primary de-sludge pumps and sent to the new sludge holding tank for gravity thickening.
The primary effluent will be gravity-fed into the existing biological filters, which were retained as part of the project scope, facilitating removal of ammonia. The secondary effluent is pumped from the new package secondary interstage pumping station and distributed to two new stainless steel, radial flow HSTs for final settlement, where the humus sludge will be withdrawn regularly via actuated bellmouths. As the effluent is pumped to the PSTs and HSTs, the levels for the tanks were less critical in comparison to a gravity system, which allowed more flexibility in design to enable a more efficient construction.
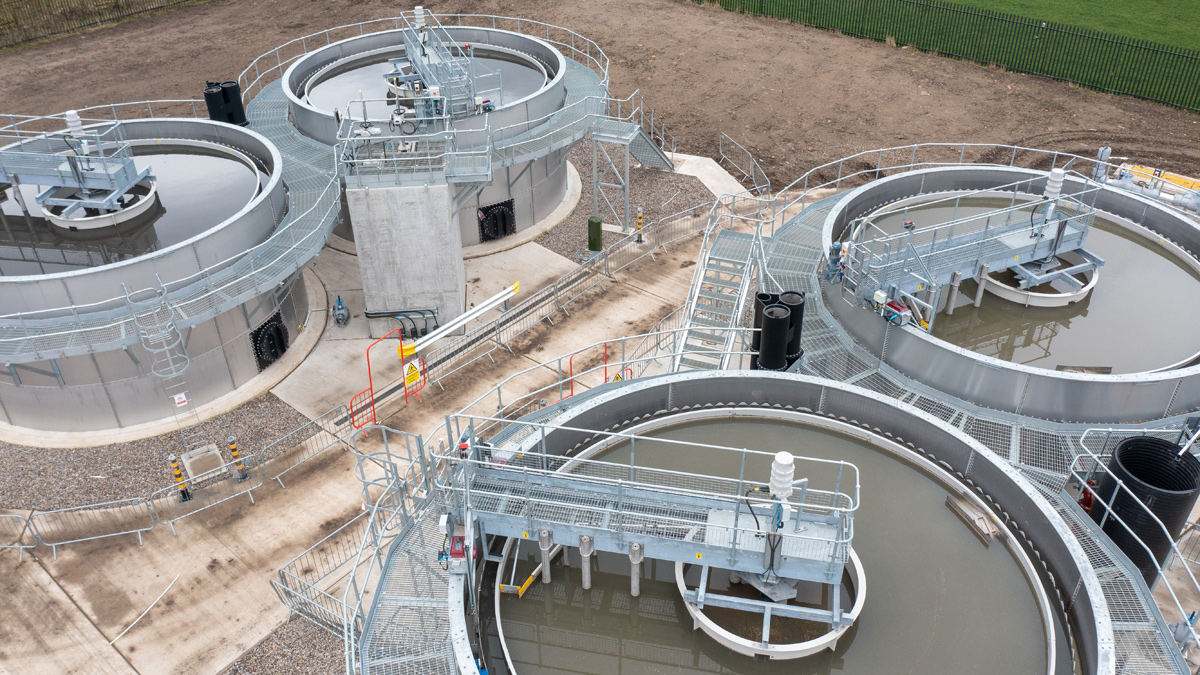
The settlement tanks in operation – Courtesy of Tilbury Douglas
Storm tanks design
Prior to the Wolsingham upgrade, there was no storm storage on site. As part of the design, the existing HSTs have been converted into storm tanks for the retention of flows in excess of 26.2 l/s flow to final treatment. During prolonged storm periods, storm flows will spill to the River Wear once the storm tanks are full.
The contents of the storm tanks will be returned to the head of the works via a storm return pumping station fitted with submersible pumps. This will occur when the storm subsides to ensure that any returning flows to the main process do not result in re-spilling to the storm tanks.
3D modelling
A crucial element of the design work was 3D modelling. The 3D site model, developed in Civil 3D software, was vital for clash detection and allowed to design tie-ins between supplier interfaces with greater accuracy and efficiency. The model incorporated supplier scope, enabling a full walk-through of the model, which provided the client with a feel for the end product.
Wolsingham STW: Supply chain – key participants
- Principal contractor: Tilbury Douglas
- Lead designer/design coordinator: Wood
- Principal designer representative: Wood
- Systems Integration subcontract: IDEC Technical Services
- Structural/civil/drainage/pipelines subcontract: Rainton Construction
- Cabling & cable sizing: Intelect UK
- Design & build of MCC kiosk: JHT Fabrication
- Inlet screen: Huber Technology
- iMCC: CEMA Ltd (Labtec UK)
- Pumping station: Xylem Water Solutions UK
- Primary sludge & scum pump package (Wolsingham): Seepex UK Ltd
- Distribution chambers: Aquardia Process Solutions
- Flow inlet works weirs and flumes: Siris Environmental
- Settlement and sludge storage tank: Stortec Engineering Ltd
Construction of off-site manufactured parts
Inlet works – flume: Wood envisaged a solid, off-site build concept for the inlet of the works, by seeking a prefabricated above-ground approach. Concepts were presented to supplier Siris Environmental, which took Wood’s design concept and produced an inlet flume design. This was fabricated in factory-controlled conditions, using non-standard materials for this type of construction, and so yields finer tolerances and greater accuracy during the build process. These tolerances are particularly important to achieve MCERTS certification.
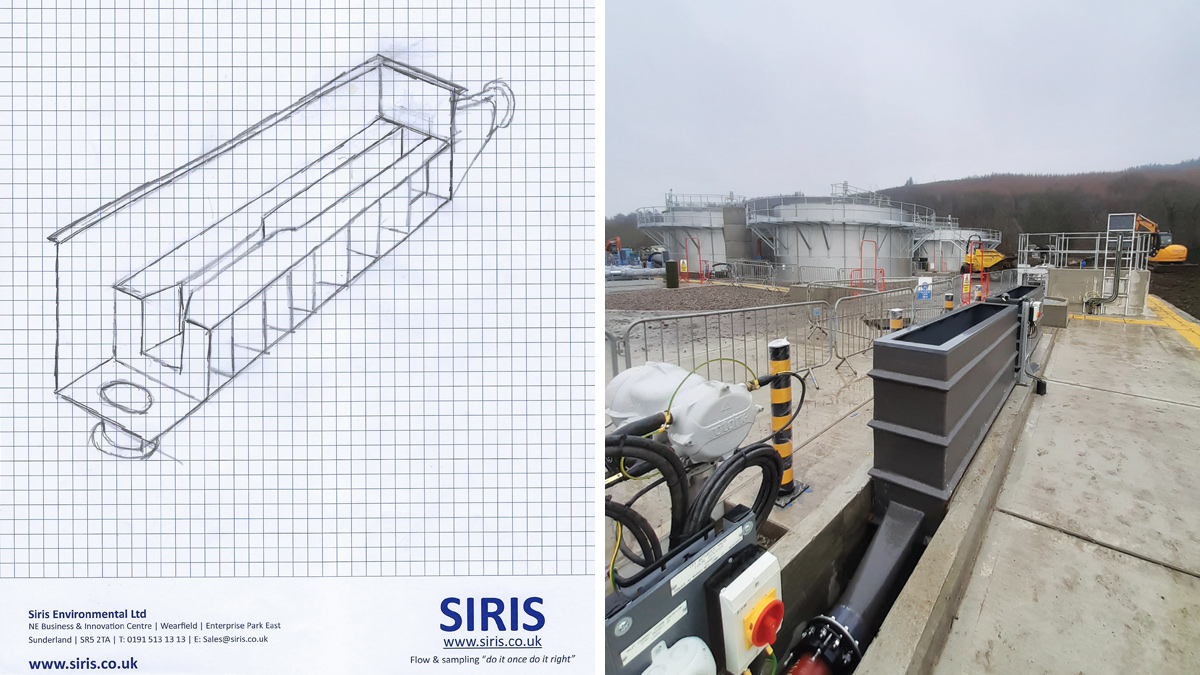
(left) An early stage sketch of the flume design and (right) the off-site manufactured flume fitted into the inlet works – Courtesy of Siris Environmental and Wood
The non-standard material the fume was constructed from was GRP reinforced welded PVC, which can achieve a service life of up to 50 years. The flume was required to be manufactured and transported to site in two sections, which was a change to the initial concept of transporting the flume in one section, however this did not affect the seamless integration of the flume into the works, showing the resilience of the off-site build approach.
The project scope was routinely challenged to reduce environmental impact, achieved through reduced vehicle movements due to significantly less in situ concrete pours for the base slabs and reduced working hours required on-site. These benefits, made possible through off-site construction, are heavily dependent on engagement with suppliers to streamline their construction process and thorough review of all aspects of suppliers’ designs.
Distribution chambers: The standard distribution chamber is traditionally cast from concrete in situ. By assessing the flows into works and modelling the site, alternative construction methods were considered, in line with the off-site by default approach. This approach is an above-ground construction using materials that can be fabricated off-site to yield greater accuracy. Aquardia took the concepts from Wood and produced a design model that was bespoke and had never been manufactured before.
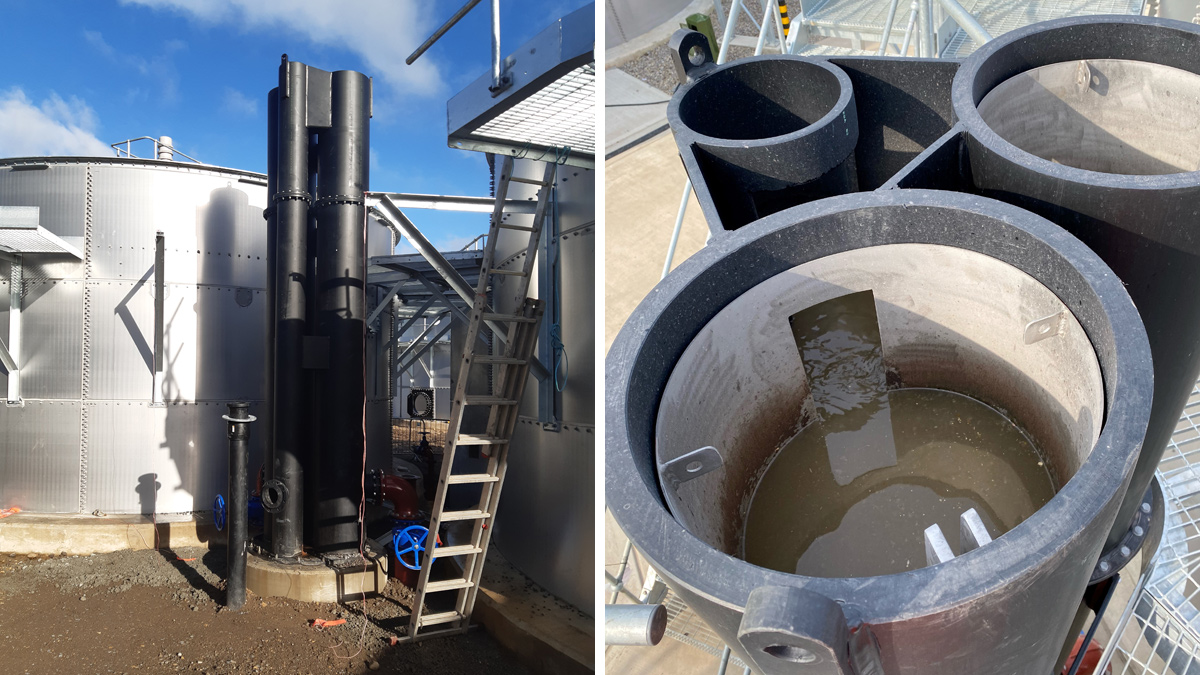
One of the HDPE distribution chambers in operation – Courtesy of Wood
Using versatile high density polyethylene, a scale physical model was produced with fully adjustable weir plates. These ensured minimum, average and maximum flows while providing equal distribution and air clearance on the discharge side. The results from the model’s testing verified the accuracy of the bespoke design and fabrication process.
The prefabricated and above-ground construction had significant construction time savings compared to traditional distribution chamber construction, due to fewer working hours on-site and less vehicle movements. In turn, this resulted in reduced environmental impact and significant cost savings.
Washwater booster set: An off-site build approach was also applied to the final effluent washwater booster set, housed within a walk-in kiosk. The kiosk was fabricated off-site and the booster set was completed with a header tank fitted inside. A constraint of the off-site build was down to transportation restrictions, which limited the size of the kiosk. This caused issues with sizing the header tank and ensuring it was of sufficient capacity to supply the washwater system. This was solved by incorporating a hydraulic link between the header tank and the nearby final effluent sample chamber. This provided the necessary additional capacity, with the washwater booster set able to draw from both the header tank and final effluent chamber.
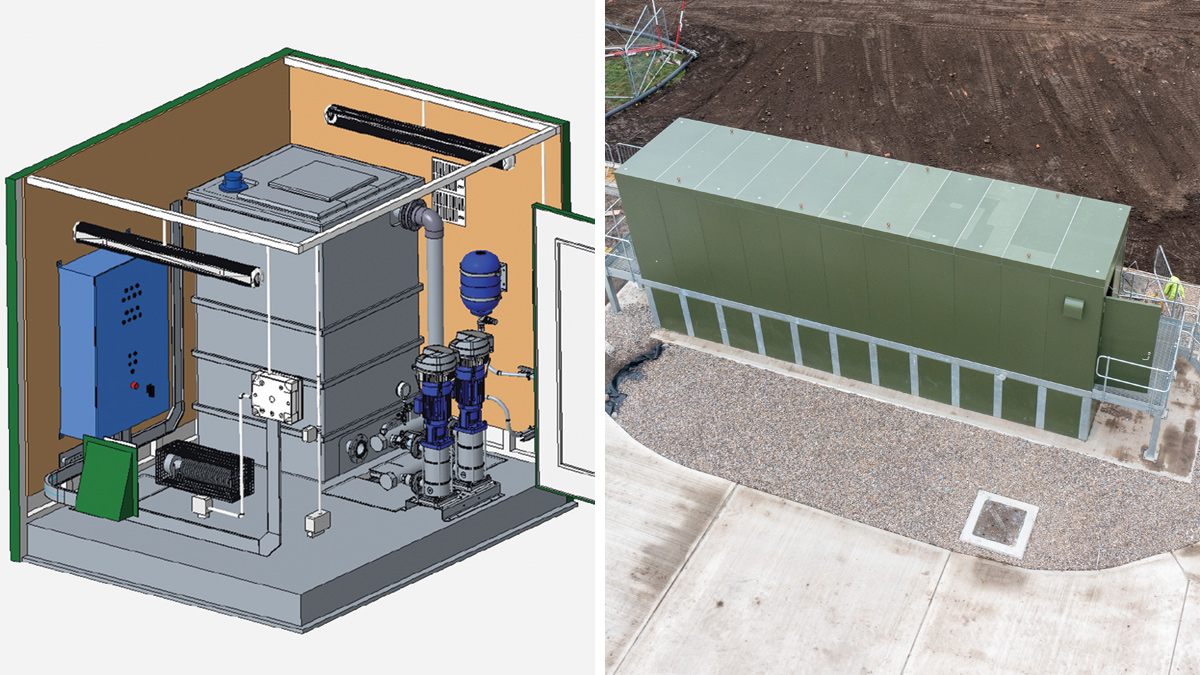
(left) A 3D model render of the washwater booster set – Courtesy of Wood and (right) aerial image of the iMCC kiosk – Courtesy Tilbury Douglas
Intelligent MCC: The electrical installation included provision of an intelligent motor control centre (iMCC). By using intelligent technology throughout design and construction, it provided a future-proof solution. This design uses fewer components and reduces hardwired (programmable logic control) I/O requirements, compartment sizes and interconnecting cabling. The intelligent technology allows a greater number of monitoring signals, providing flexibility in meeting any requirements for post-manufacture system reconfiguration. Having fewer components reduces the number of spares required for maintenance and resulted in a reduction in the size of the iMCC footprint. This allowed for a smaller kiosk and associated civil works, again reducing the environmental impact of the project.
Project success
Wood and Tilbury Douglas, with the backing of Northumbrian Water, were able to use the Wolsingham STW refurbishment to showcase the benefits of Design for Manufacture and Assembly (DfMA) and off-site construction on water industry construction projects. The project was completed on time and within budget, saving 20% on target costs through being able to provide greater predictability in delivery times due to the use of off-site manufacture. Quality overall was improved dramatically compared to traditional methods while time on site was reduced by 20% on contract completion thanks to off-site construction, which also significantly benefited the project’s safety performance. The main takeaway point from the off-site build is the importance of the relationship and communication between suppliers, which was vital for the project’s success.
The Wolsingham STW project was shortlisted for the Water Industry Awards 2020, for Wastewater Innovation Projects of The Year, due to the success of the design and the integration of prefabricated assets.