Riding Mill Raw Water Pumping Station (2022)
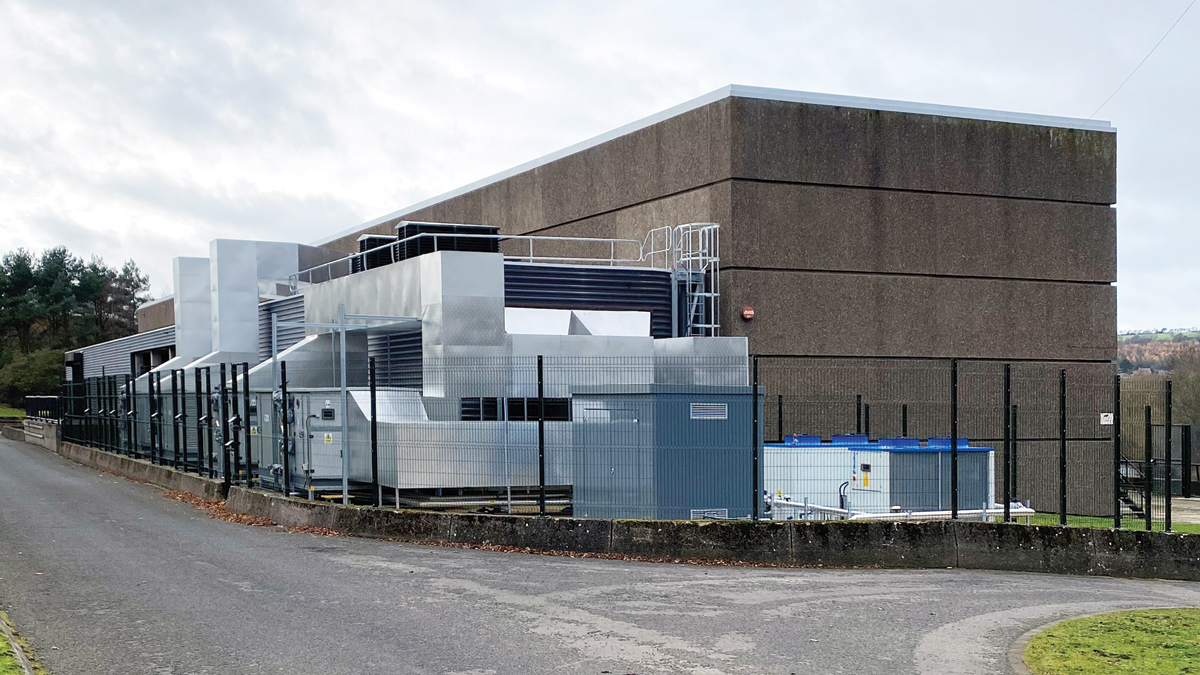
Riding Mill RWPS showing the new HVAC System - Courtesy of Mott MacDonald Bentley
When constructed in 1979, as part of the Kielder Transfer Scheme, Riding Mill Pumping Station was the largest pumping station in Britain. Abstracting flows from the River Tyne, it enables Northumbrian Water (NWG) to transfer water from Kielder Reservoir to the Derwent, Wear and Tees rivers, whilst supporting the operation of Mosswood WTW. The site was initially constructed to safeguard supply against the projected industrial growth and the associated water demands across the north east. Whilst industrial growth slowed below expectations, Riding Mill Pumping Station remains a key asset and will become more critical as the region continues to face the consequences of climate change.
Project drivers
The drivers of the project were to improve the efficiency of the station and protect against failure of assets that were coming towards the end of their design life, with many having been in operation for over 40 years. The site faced the following issues:
- Pump and drive failures were limiting reliability and required reactive maintenance.
- The existing supply agreement with the electrical distribution network operator limited the maximum operation of the site to only three pumps.
- The need to comply with the Eels (England and Wales) Regulations 2009.
- Mechanical and structural assets reaching the end of their design life.
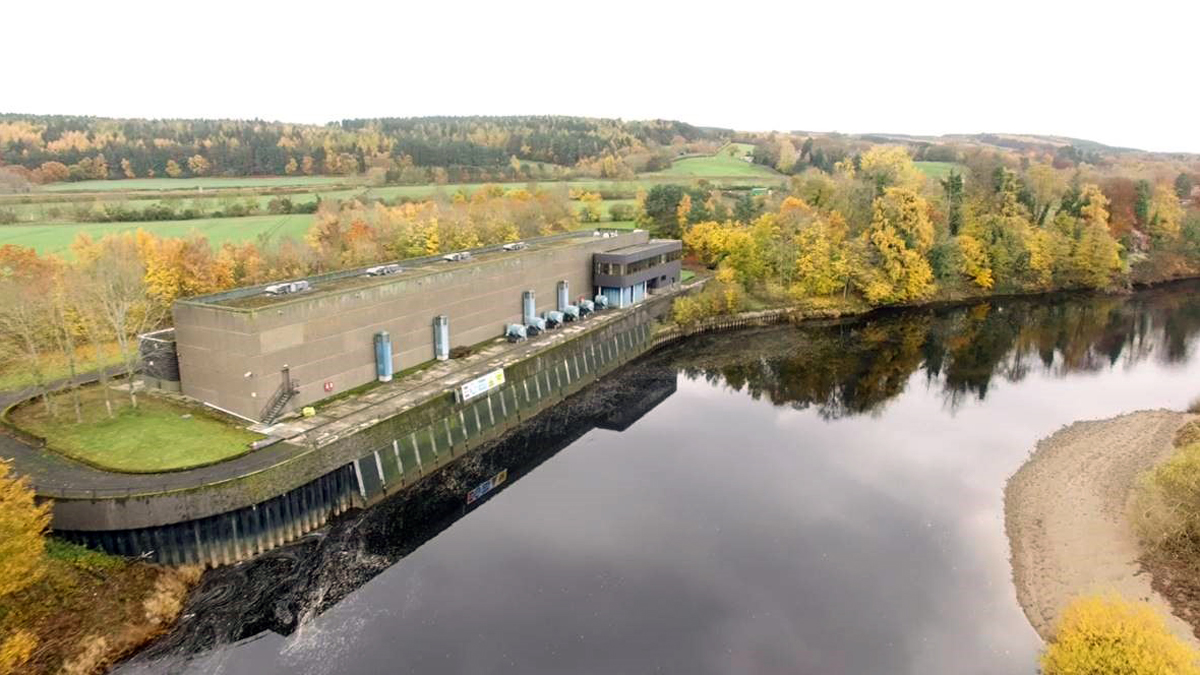
View on site, prior to upgrade works – Courtesy of MMB
Project summary
NWG awarded Mott MacDonald Bentley (MMB) an Investigate and Define (I&D) contract to review potential solutions, followed by a Design and Construction (D&C) contract valued at £12m.
Works completed included:
- Removal of 6 (No.) 90 Ml/d pumps.
- Installation of 4 (No.) refurbished 90 Ml/d pumps and a new 20 Ml/d charging pump.
- Installation of high efficiency motors, variable speed drives and HVAC system.
- Additional valving to improve safety and flexibility of the pumping station.
- Removal of existing band screens.
- Installation of 4 (No.) Hydrolox eel and fish friendly screens.
- Electrical refurbishment requiring the replacment of the 11kV switchboard, the transformers, the 400V/230V distribution system and modernisation of the control system.
- Multiple structural upgrades.
- Replacement of the full roof cover.
- Interior refurbishment throughout.
Throughout the project, Mott MacDonald Bentley worked with Northumbrian Water to find solutions that would benefit the project, through realising CAPEX, OPEX and carbon savings. The upgrade of existing assets over replacement was a key theme throughout the project.
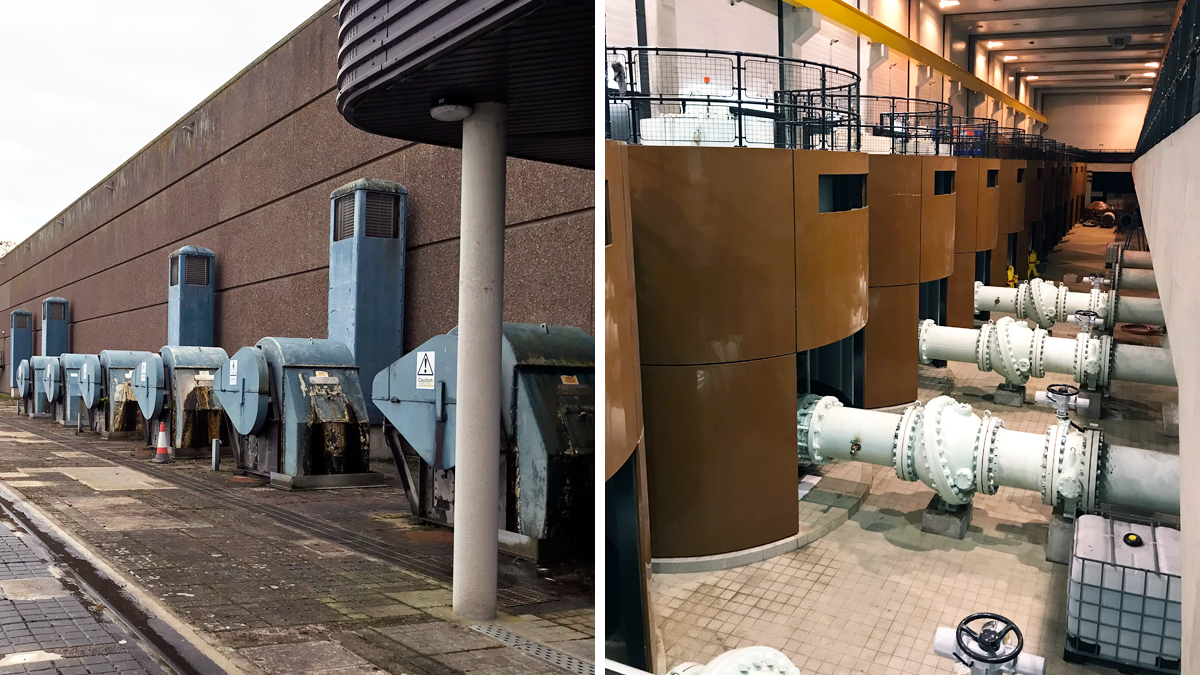
(left) Existing band screens and (right) Existing pump manifold prior to upgrade – Courtesy of Mott MacDonald Bentley
Extending the design life of the pumps
The original project brief required installation of 8 (No.) new pumps at the site, however, this would have required major civils remodelling within the intake bay and within the building structure, plus removal and replacement of the large diameter manifold pipework immediately downstream of the pumps. The team approached the initial manufacturer who built the pumps in 1978 to refurbish instead of purchasing new. The pumps were removed in pairs and sent back to the original factory in Glasgow for strip down, inspection, refurbishment, reassembly and testing before returning to site. This approach vastly saved on costs and carbon and decreased risk to programme through avoiding shipping new pumps from overseas.
Focusing on re-use, Mott MacDonald Bentlry designed out a further pump from the scheme, reducing the initial requirement for 2 (No.) 20 Ml/d charging pumps to 1 (No.) by upgrading the motor on an existing pump to provide sufficient capacity. The requirement for a 7 bar washwater booster set was designed out by taking a feed from the live, pressurised side of the rising main and controlling the operational pressure. In both cases, there was a tangible CAPEX saving to the project, but also a large OPEX reduction.
With the pumping station remaining in operation, it was crucial to ensure effective isolation when working on the large diameter pipework throughout the building. The initial programme required the rising main to be fully drained down prior to the removal and installation of each set of pumps, taking the station out of service for weeks at a time on five separate occasions. Due to the age of the station, effective isolation measures were not in existence. Through specification and installation of new valving on each pump leg MMB reduced the interruption to one single 7-day shut down, as the individual legs could be isolated and worked on whilst water continued to be pumped through the main. The total cost of the new valves was approx. £250k but prevented over 12-months of delays, greatly reduced programme durations and improved the safety of both construction and future maintenance works.
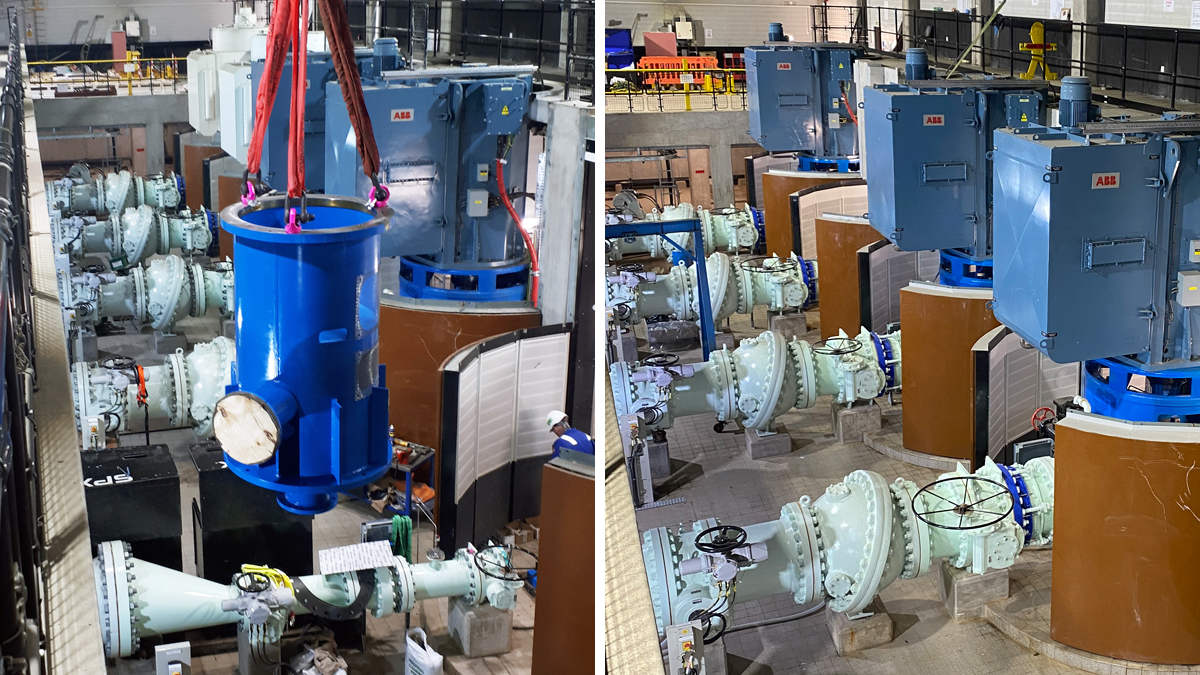
(left) Installation of new 20 MLD pump and (right) refurbished 90 MLD pumps with new motors – Courtesy of MMB
Riding Mill Pumping Station: Supply chain – key participants
- Designer & contractor: MMB
- Pump refurbishment: Celeros Flow Technology
- LV cabling, ICA & electrical refurbishment: Intelect (UK)
- Systems integration: Peak Technology Solutions
- HVAC supply and installation: Air Technology Systems
- HV transformer & cabling: Integrated Utility Services
- HV panel & LV switching panel: Siemens
- LV panel: Blackburn Starling Ltd
- HV variable speed drives: ABB Ltd
- Major valves: Glenfield Invicta
- Structural steelwork: JHT Fabrications Ltd
- Eel screens: Hydrolox
- Diving works: Northern Divers
- Roof repairs: John Flowers Ltd
- Crane refurbishment: Kone Crane
- Building refurbishment: Gowland & Dawson
- Fencing: Burn Fencing
Electrical upgrades to maximise efficiency
The principle of refurbishment over replacement was also utilised with the 11kV switchboard, allowing the site to be migrated in a modular fashion. The electrical systems were maintained for demand periods during the refurbishment, with minor shutdowns when the station was offline, meaning that the plant could be upgraded without disturbance to supply to customers.
Upgrades included the installation of ultra-high efficiency low harmonic drives and an associated HVAC system to vastly improve the efficiency and flexibility of the running of the works and to reduce surge. Along with several other electrical upgrades, the site now requires substantially less power to operate, and can be largely operated remotely for the first time since its construction, reducing visits to the site.
For a station of this magnitude, the variable speed drive (VSD) units required to provide the high efficiency desired were large units: each of the 4 (No.) 3MW cabinets had a footprint of 3m2 and weighed over 6 tonnes. Due to space constraints the initially identified location within the pumping hall would have required construction of a mezzanine floor area to protect against flooding. This would have severely constrained the works to replace the existing pumps and would have prevented potential future expansion of the station. MMB identified an opportunity to reduce the size of the 11kV switchboard and partition the existing HV room to create additional space within the existing second floor of the building. Despite the supporting floor being designed for much lower loads, MMB developed a design for temporary and permanent strengthening to the floor, which not only kept the pump hall clear, but improved future accessibility to the VSD units whilst reducing time and cost.
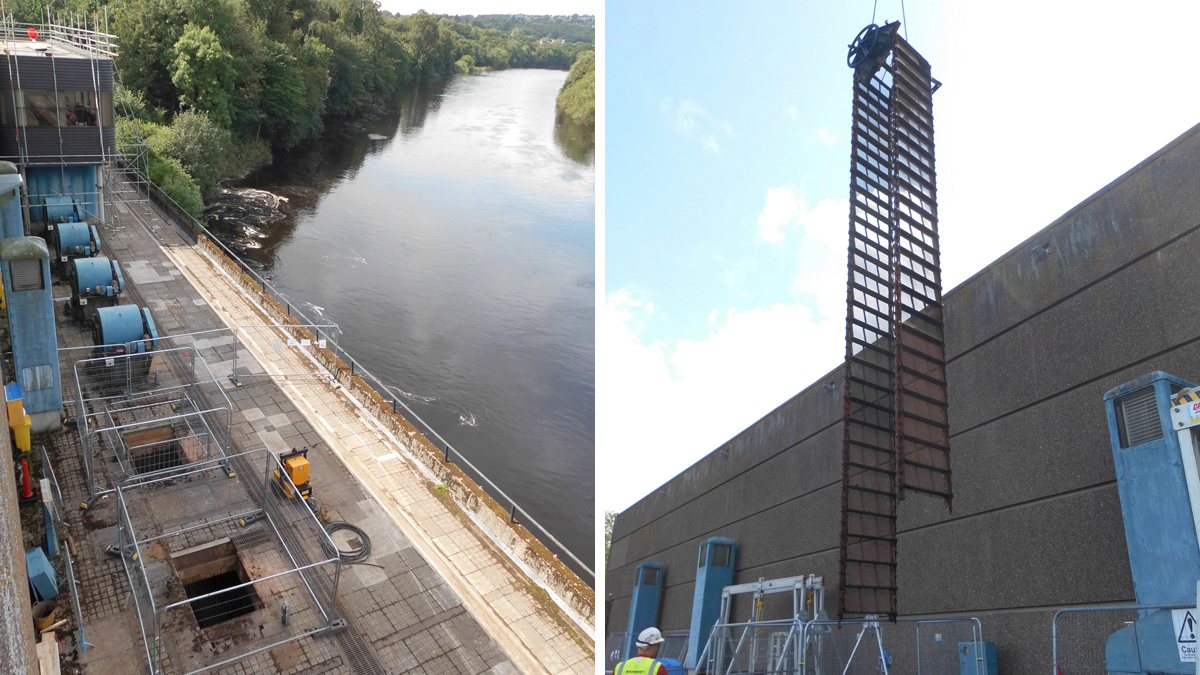
(left) removal of band screens had to be sequenced to enable continued operation of the site and (right) removal of existing screen components – Courtesy of MMB
New screening technology
A major part of the project scope was installation of new eel and fish friendly screens on the works intake. The Tyne Rivers Trust notes that the River Tyne is the best river system for salmon and sea trout in England and Wales, with both species journeying annually from the North Sea beyond Riding Mill Pumping Station to spawning grounds upstream.
MMB and Northumbrian Water worked with the Environment Agency, local landowners, and the angling association from feasibility through to implementation to agree the correct screening solution which would act in conjunction with ongoing upgrades at the nearby weir to significantly improve aquatic biodiversity within the river, particularly at higher reaches and minimise disruption to the public who use the river for fishing and walks.
The previous screening regime utilised screens with a 6mm screening width to prevent debris entering the station and damaging the mechanical equipment within. The existing screens were of ‘fish recovery and return’ style, meaning that fish impinged against the screen due to high abstraction rates would be mechanically lifted out of the flow and deposited into a launder channel to return to the river. During periods of low abstraction, eels and fish could be expected to seek refuge from the river flow in the inlet works after expending energy traversing the weir.
Once the pumps were turned on, fish of all ages would be impinged against the screens and deposited downstream of the weir again. However younger, smaller eels and fish could be entrained through the screens and into the pumps.
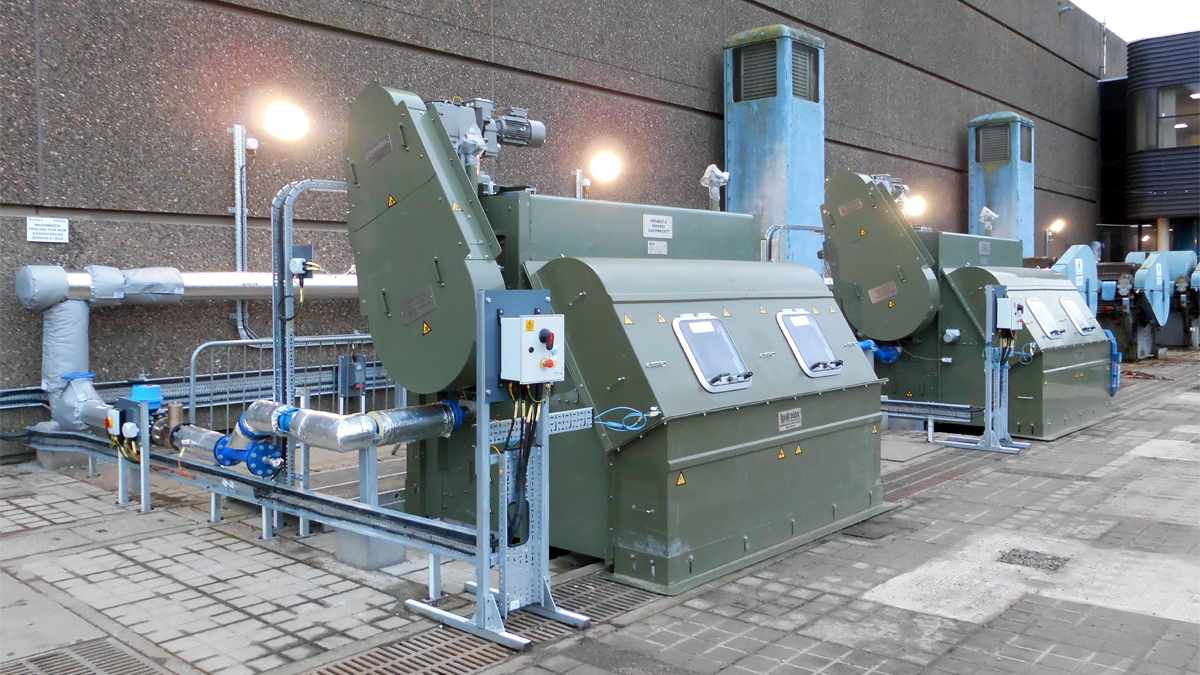
New Hydrolox band screens installed within existing intake bays – Courtesy of Mott MacDonald Bentley
In agreement with the EA, MMB were able to present a case which enabled the use of more slimline fish exclusion (EFE) screens over fish recovery screens. This eliminated the need for over 400m of launder channel and meant the screens could fit into the existing screen bays. The installation of launder channels would have required the purchase and clearance of 3rd party land. Further, being able to fit the screens in the existing bays removed the need for intrusive river work that could be harmful to the aquatic life the screens are designed to protect.
The removal of the existing screens was a logistical challenge, requiring a 300-tonne crane blind lifting each 6.5t unit over the pumping station. After installation of the first screen a full structural review minimised lift weights by dismantling the screens in situ, using an excavator and a much smaller crane to remove the screens in a much safer, cost-effective manner and which mitigated against possible weather delays.
The new exclusion system prevents fish and eels from being entrained, with velocities through the screens reduced to less than 0.25m/s even in worst-case conditions – lowest river level, maximum abstraction. Using Hydrolox EFE screens ensures no requirement to capture and release entrained fish and eels, reducing trauma. The screens were chosen to meet current and anticipated regulations for other fish species, ensuring ongoing compliance in the ever-changing environmental landscape. The environmental impact of construction was considered throughout design. By modifying the design to remove the need for a cofferdam within the river, there were no significant works below the waterline and as such, the EA permitted the works to proceed without any formal silt control methods.
Collaboration and proactive management
The project was a complex multidisciplinary upgrade and required adaptable and proactive management of work-faces to maintain the programme. To achieve this MMB employed Construction Lean Improvement Programme (CLIP) throughout.
The CLIPs brought all parties together to highlight opportunities, identify blockers and agree a collaborative plan to complete. Held every 3 months, or ahead of key deliverables, and coupled with buildability reviews on the practicality of the developing methodology, MMB enabled a clear plan to be developed which was bought into by everyone. When NWG experienced periods of abnormal water scarcity due to low reservoir stocks, following record dry spells, the project faced over 12 months of delay.
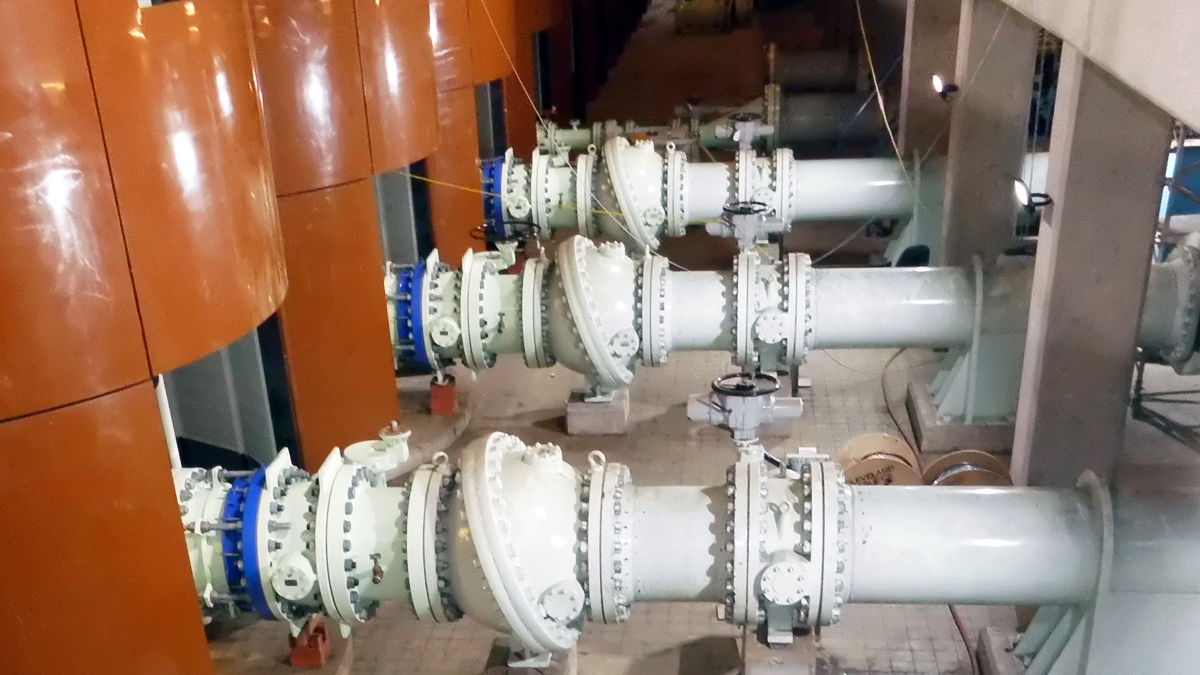
Secondary isolations installed within manifold – Courtesy of MMB
The team met the challenge head on and through identifying the additional valving in the pump manifold, reduced over 150 days of shutdowns to one single 7 day shut down. This enabled the project to continue but has also greatly increased the flexibility of the station, enabling future major upgrades or refurbishment without compromising supply.
Throughout the project the site team worked very closely with site operators to coordinate permits to work and the live CDM areas throughout the station. This ensured efficient and safe handovers of high voltage switchboards, equipment, and large capacity pumps.
The core team also worked closely with an ecologist ensuring that the roof modification and refurbishment works minimised the impact on bat colonies and nesting oystercatchers. The requirement to provide gravel on the new roof structure to preserve the habitats was designed out with the support of the ecologist through reclaiming the temporary gravels utilised on site for material storage and temporary parking to create additional permanent nesting habitats within the site. As a result, a roofing product with longer design life could be selected, no additional gravel import was required, and several tonnes of used gravel were diverted from landfill.
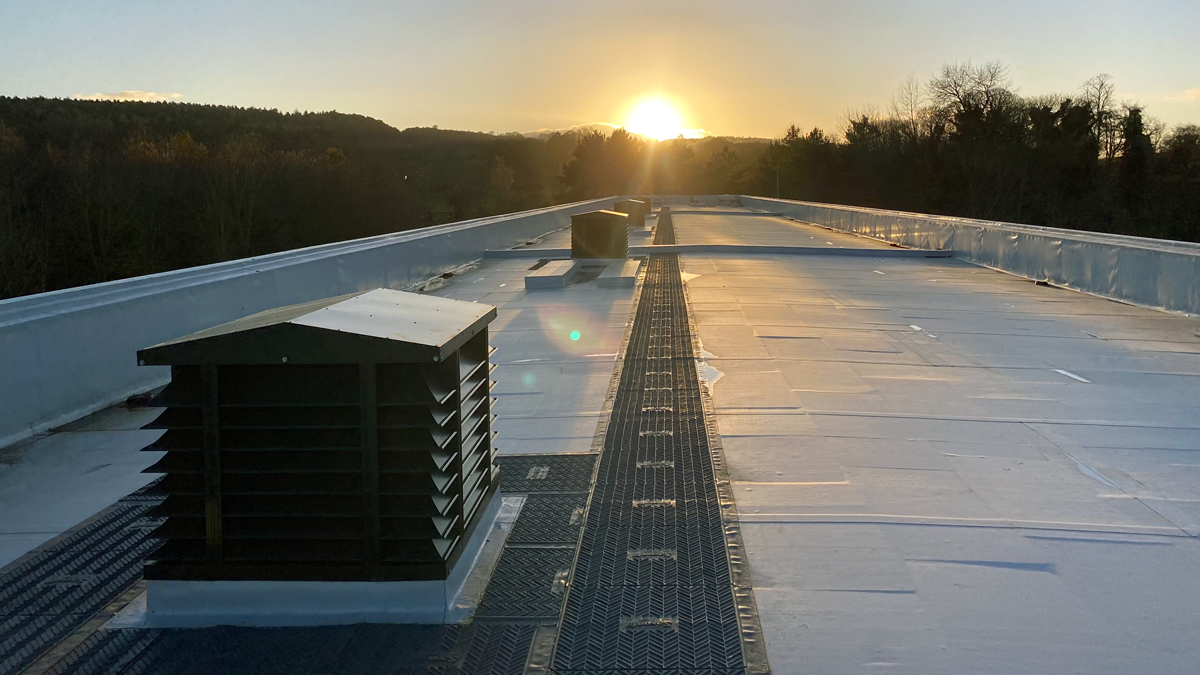
New roof protection – Courtesy of Mott MacDonald Bentley
Conclusions
Riding Mill Pumping Station’s status as a key asset within Northumbrian Water’s portfolio means that the community benefit it currently provides, in terms of safeguarding water supply for major parts of the north east, cannot be understated. After over 40 years of service, the works carried out as part of this project will mean that the station can continue to operate for decades to come, with less demand on power supply due to multiple electrical and mechanical upgrades and is future proofed for further expansion should it be required.
Overall use of collaborative planning enabled the site team to stagger trades and work locations to ensure that H&S was uncompromised, even when the project swelled to its peak. This was invaluable when Covid-19 struck, and MMB were able to maintain programme momentum whilst ensuring everyone was safe and operated within the evolving guidance.
In total the project clocked up a total of over 77,000 person hours, at points had over 50 bodies on site and involved 35 different sub-contractor organisations. During the project MMB recorded 956 positive safety interventions and achieved an AFR of 2.93.
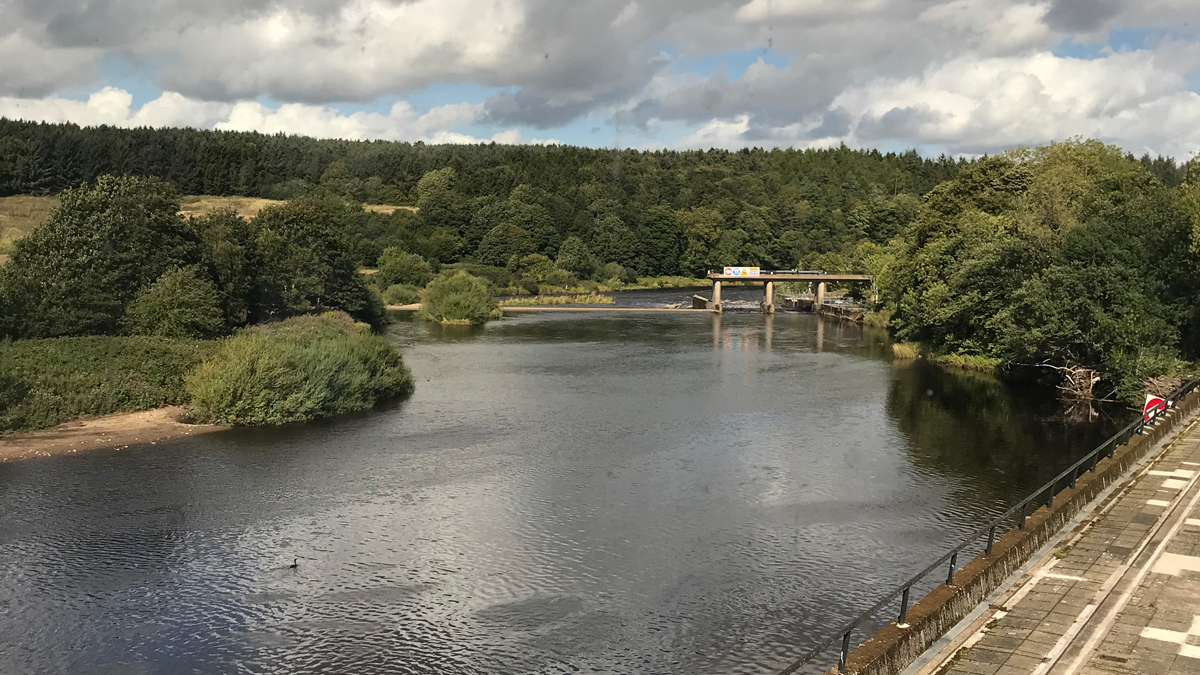
Location on River Tyne – Courtesy of Mott MacDonald Bentley
Over the course of the project, despite additional scope increasing the target cost to £13.5m the project was delivered for £11.7M, within the initial budget. Commencing in November 2018 and programmed to be completed in November 2020, despite water scarcity restrictions, additional scope and Covid-19, this date was maintained through proactive, collaborative programme management.