Hampton Loade WTW – Eel Screens (2022)
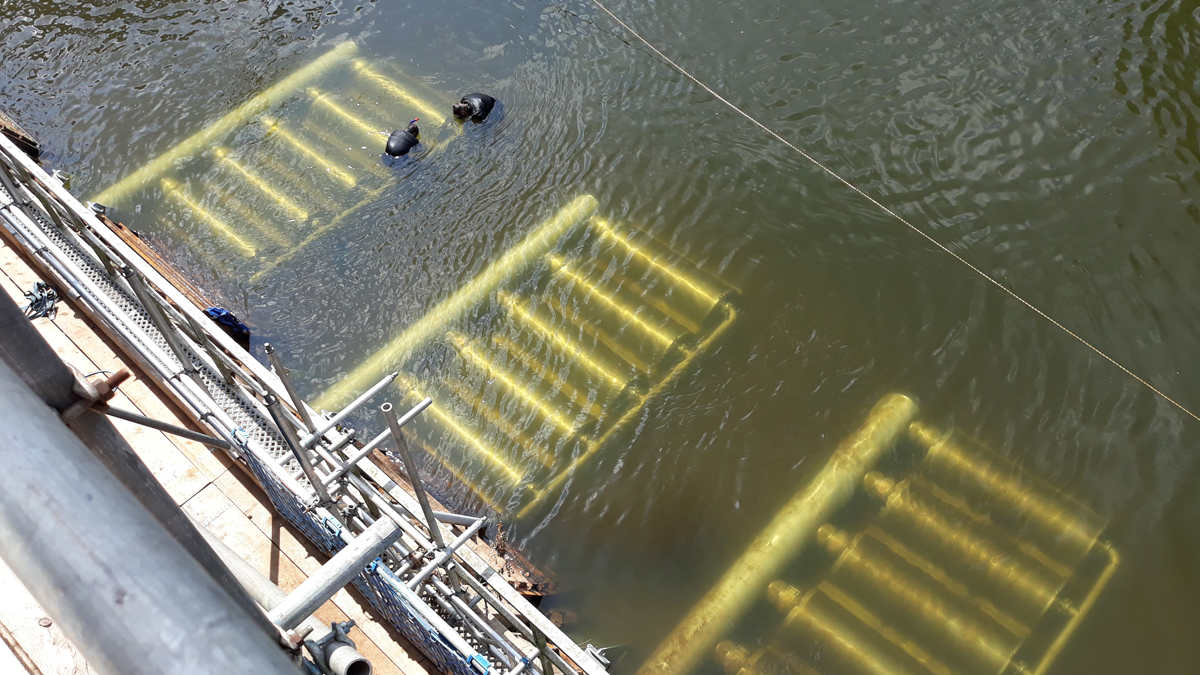
Three of six screen arrays in the River Severn - Courtesy of Integrated Water Services (M&E) Ltd
Operated by South Staffs Water (SSW), Hampton Loade Water Treatment Works is located five miles from Bridgnorth, Shropshire and supplies around 700,000 customers. Constructed in the 1960s, the site comprises the treatment works, an intake on the River Severn and a regulating reservoir at Chelmarsh which stores the abstracted river water. The river intake is a substantial construction about 50m long with a tall façade on the river side, due to the low water to high water differential of 7.62m. The intake has twelve large penstock doors measuring 7’ by 5’. River water flows through the open penstock doors, through coarse and fine screens into three sumps. The water then flows through Ø6.0 mm perforated mesh band screens and is pumped to Chelmarsh Reservoir.
Eels Regulations
Due to abstraction volume, it was necessary to bring the intake into compliance with The Eels (England and Wales) Regulations 2009. SSW engaged leading environmental consultancy, APEM, to investigate screening options and create the scope that was used for the tendering process.
The specification for the screening was for a maximum mesh size of 12.5 mm and a maximum approach velocity of 0.40m/s. Integrated Water Services (M&E) Ltd (IWS) was successful in securing the contract to install a positive exclusion screening system with additional protection for other species with a design proposal for 3.0 mm mesh size and 0.15m/s maximum approach velocity. SSW was particularly interested in implementing the additional protection for other species.
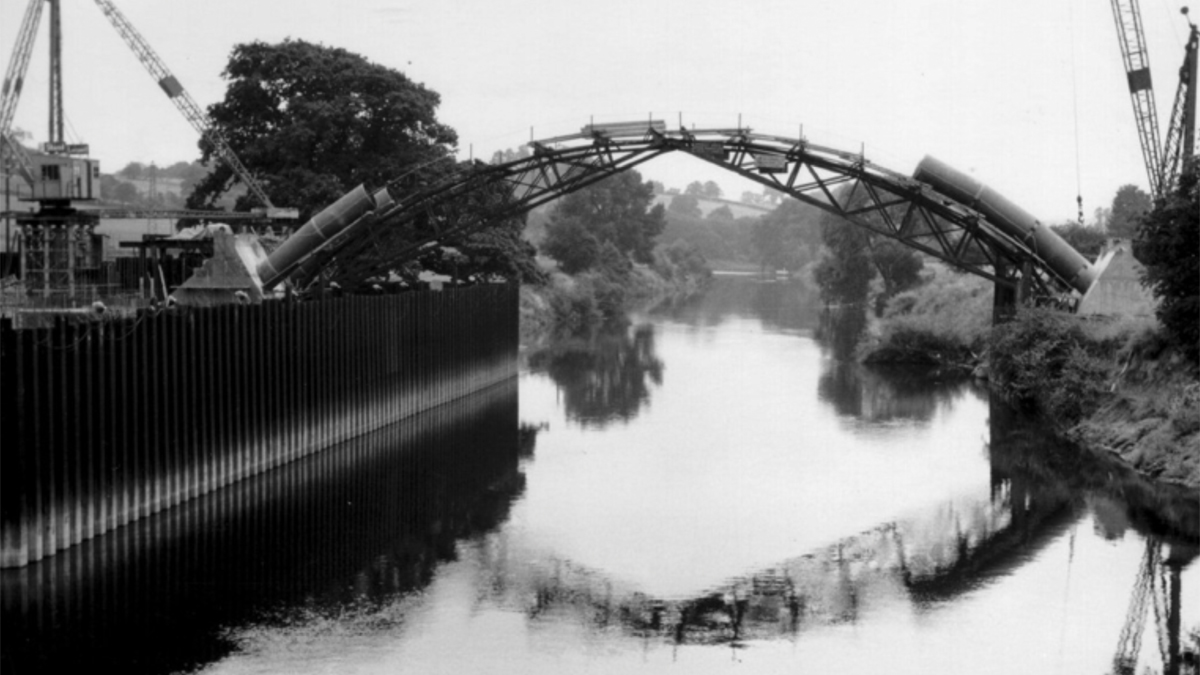
Hampton Loade intake & pipe bridge construction in 1966 – Courtesy of South Staffs Water Archives
Hampton Loade Eel Screens
- Main contractor: Integrated Water Services (M&E) Ltd
- Environmental consultants: APEM
- Ecological survey: SLR Consulting
- Underwater surveys: Specialised Diving Services
- Eel screen system, package plant supplier: Eliquo Hydrok Ltd
- Underwater screen installation: Edwards Diving Services
- Scaffolding & access: JFE Attridge Scaffolding
- Pontoon contractors: ScaffFloat
- Craneage: ABA Crane Hire
- Debris booms: Bolina Booms
- Valve release: Hydrosave
- Pipework: Integrated Water Services (M&E) Ltd
- Compressed air pipework: Enco Ltd
- Gaskets: Delta Rubber Ltd
- Straub couplings: MV Fluids Handling
- Core drilling: Crossland Construction
- Structural capacity assessment for crane loads: Rogers Clarke Lander Ltd
- Systems integration: HBX Ltd
- Recertification of restraint anchors: Holtite Ltd
- Project documentation: 3rd Light Media Ltd
Design & enabling works
Integrated Water Services (M&E) Ltd design proposal was a passive wedge wire cylinder (PWWC) screening system. The selection of this type of screen was due to the relatively low available water height above the concrete apron, so getting the screen apertures as low as possible was crucial. The screen profile used was a half-cylinder with a flat base and wedge wire screen looping over the top. As designed the total functional screen surface area exceeded 75m2.
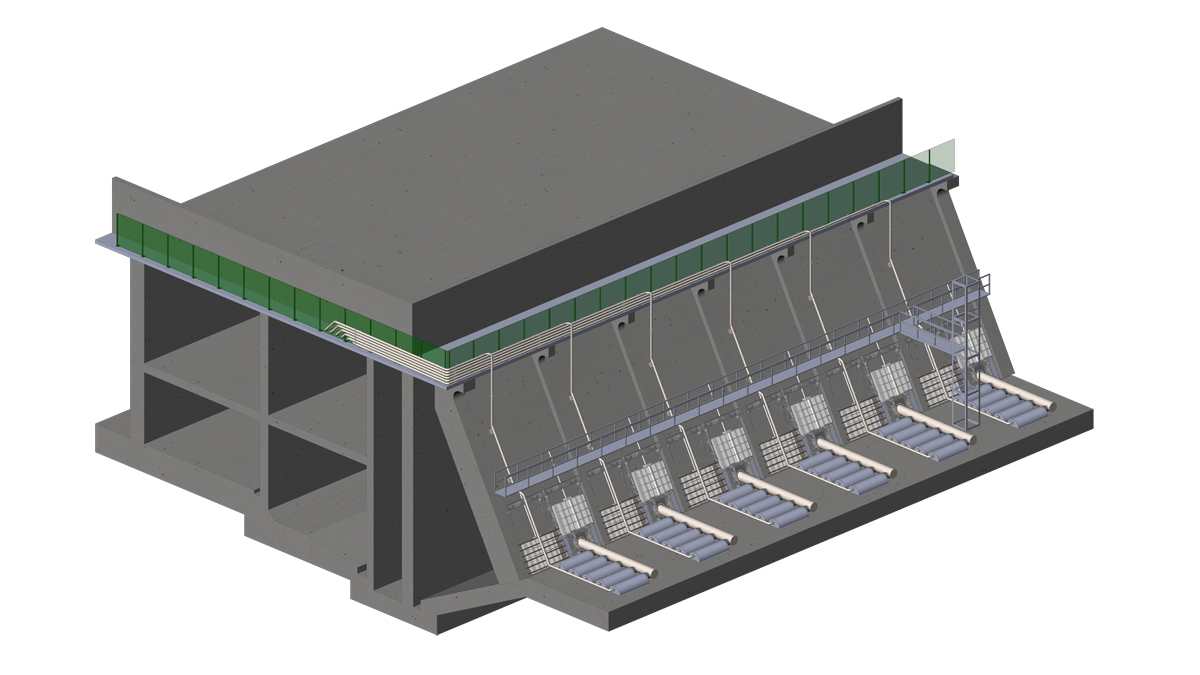
IWS design showing intake screen arrangement – Courtesy of Integrated Water Services (M&E) Ltd
In a PWWC system, compressed air is used to clean the screens. The air is released from a storage vessel and water within the screen is displaced; forcing debris away from the apertures, with the air escaping to the river surface. Due to the size of Hampton Loade Intake and multiple manifolds, it was necessary to design the screen cleaning procedure to be operated in phases from upstream to downstream.
The screens, air purge system and local control panel package plant was supplied by Eliquo Hydrok Ltd for installation by IWS. Each group of screens was to be connected to a compressed air manifold; with manifolds connected by compressed air pipework to storage vessels in the intake building.
Specialised Diving Services was engaged to perform underwater surveys of the intake. IWS was able to talk directly with the diver to request detailed information as the survey progressed. The information was essential for IWS to produce a buildable screen manifold that would be installed right first time.
The 7’ by 5’ penstock door mechanisms were tested under a valve assessment by Hydrosave and found to be seized. Hydrosave then provided their seized valve release services to free up all twelve penstocks and provided a report for each one including a torque/turns profile. Two universal joints required replacement and safe access was supplied by JFE Attridge Scaffolding.
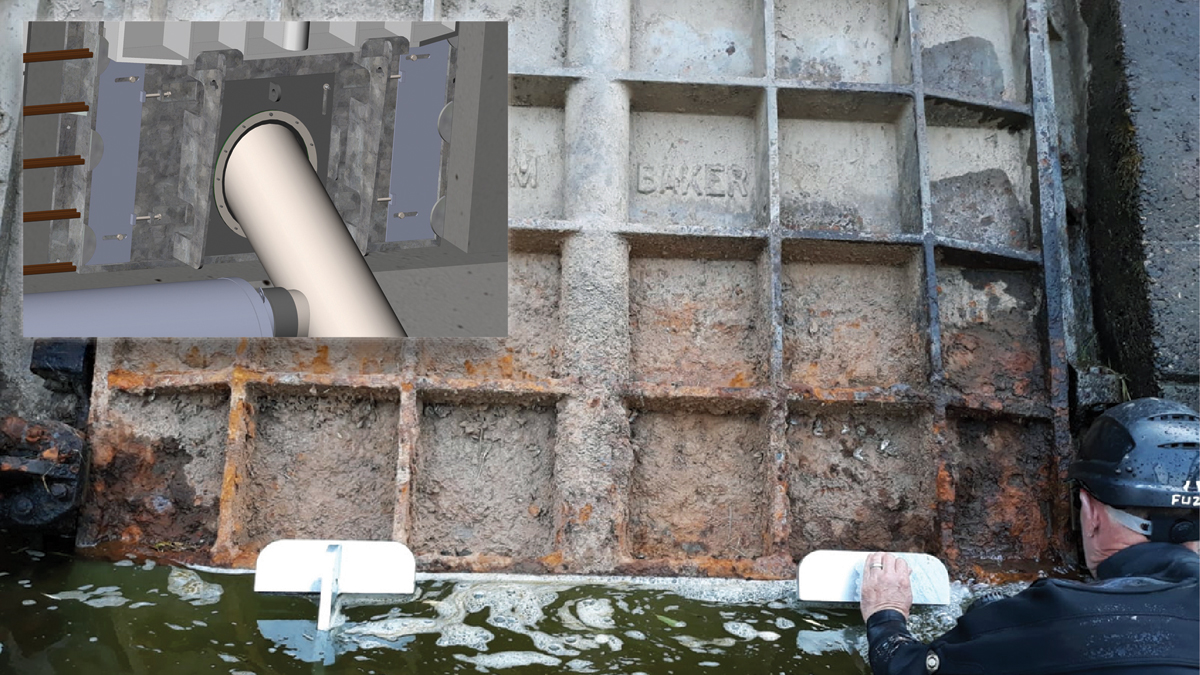
Penstock interface is secured using penstock door and (inset) penstock interface plate design – Courtesy of Integrated Water Services (M&E) Ltd
IWS produced an innovative design utilising the existing penstock doors to secure raw water manifolds using an interface plate. Each manifold was designed to have five screens attached, with six manifolds resulting in a total of thirty PWWC screens.
The penstock interface plate lifting beam was designed with consideration to the centre of mass so that when lifted into position the plates would hang at the correct 60° angle to aid installation. The interface plates were fabricated in-house by IWS in Altham. The plates had an oval hole into which the screened water manifold would be inserted, sealed using a bespoke gasket designed by IWS and supplied by Delta Rubber Ltd.
An advantage of the proposal to use the penstock doors to secure the water manifolds was that the other doors could be kept wide open so that the intake could remain in operation during installation and commissioning. When functional commissioning was complete the six doors could be closed and the intake would be compliant with the regulations.
IWS designed the pipework between the screen air manifolds and the compressed air purge system. Due to the large size of the intake structure the pipework system was extensive. The decision on pipe routing to avoid restricting existing access points was to fix the pipe around the perimeter of the safety fencing, with a small step over platform where the pipes exited the intake building. Individual pipes to screen air manifolds were designed to drop over the front edge of the structure and be fixed to the façade at multiple points to protect against floating debris. The design included a pipe route over the original penstock framework on its route to the screen air manifolds. Compressed air pipework was fabricated by IWS and Enco Ltd.
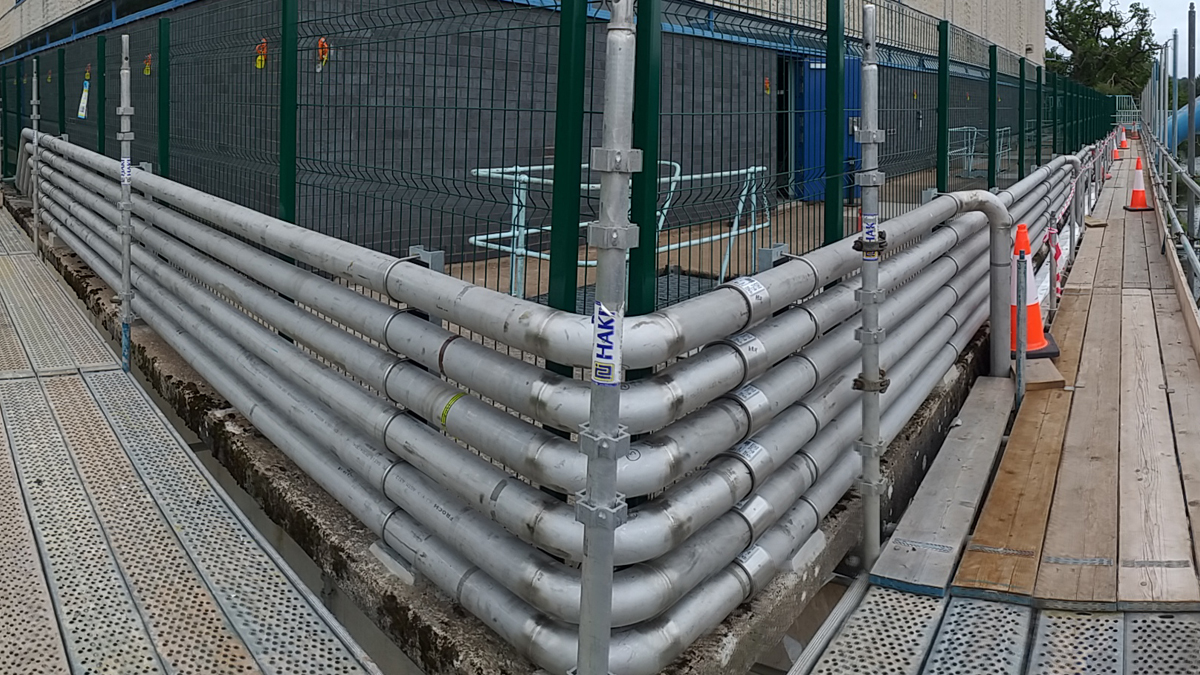
Compressed air pipework installed around perimeter security fencing – Courtesy of Integrated Water Services (M&E) Ltd
Construction
Due to the large size of the intake structure and the nature of the road access from the main site it was not possible to allow for installation using only a crane; the reach was too far. Following discussions with numerous lifting and access suppliers JFE Attridge Scaffolding recommended ScaffFloat for pontoon and lifting hire.
A demonstration event was held at Bartley Sailing Club and the robust pontoon system, decked with boards, was obviously an ideal solution. The proposal from ScaffFloat for Hampton Loade was a two-pontoon system, one that a crane could lower items onto and a main working pontoon with a substantial A-frame for lifting the screens into the installation positions.
Edwards Diving Services (EDS) were engaged to perform installation in the river. The first tasks were to clear vegetation from the intake and remove bar racks from in front of alternate penstocks. EDS then performed light clearance of the concrete apron where the eel screens were going to be installed.
With the preparation works complete the penstock interface plates were installed using the twin pontoons. Plates were lifted to the correct position and then expanding plates both sides were used to seal the penstock aperture. The corresponding penstock door was then closed to securely hold the plate in position.
VIDEO: Hampton Loade eel screens installation on the River Severn – Courtesy of Tony Budd – ScaffFloat
The next task was to install the screens. Due to the unusual lifting arrangements some assembly was required in the river, some of it on the storage pontoon. The water manifold was inserted into the penstock interface plate and then five passive wedge wire screen modules were attached. The air manifold was then fitted, and the screens secured to the concrete apron.
JFE Attridge Scaffolding provided access around the top and across the front of the intake to enable the compressed air pipework to be installed. IWS used Straub couplings supplied by MV Fluids Handling to easily connect the pipework fabrications together. Edwards Diving Services made the final connections of the pipework to the screen air manifold pipes.
Final large installation in the river was an exclusion boom supplied by Bolina Booms. To allow for the range of river levels the boom was secured to long outriggers that enabled vertical articulation through a sufficient swept angle. An alternating colour scheme was selected for the floats and the floating element was secured upstream with a substantial ground anchor and to the downstream intake structure adjacent to the bridge.
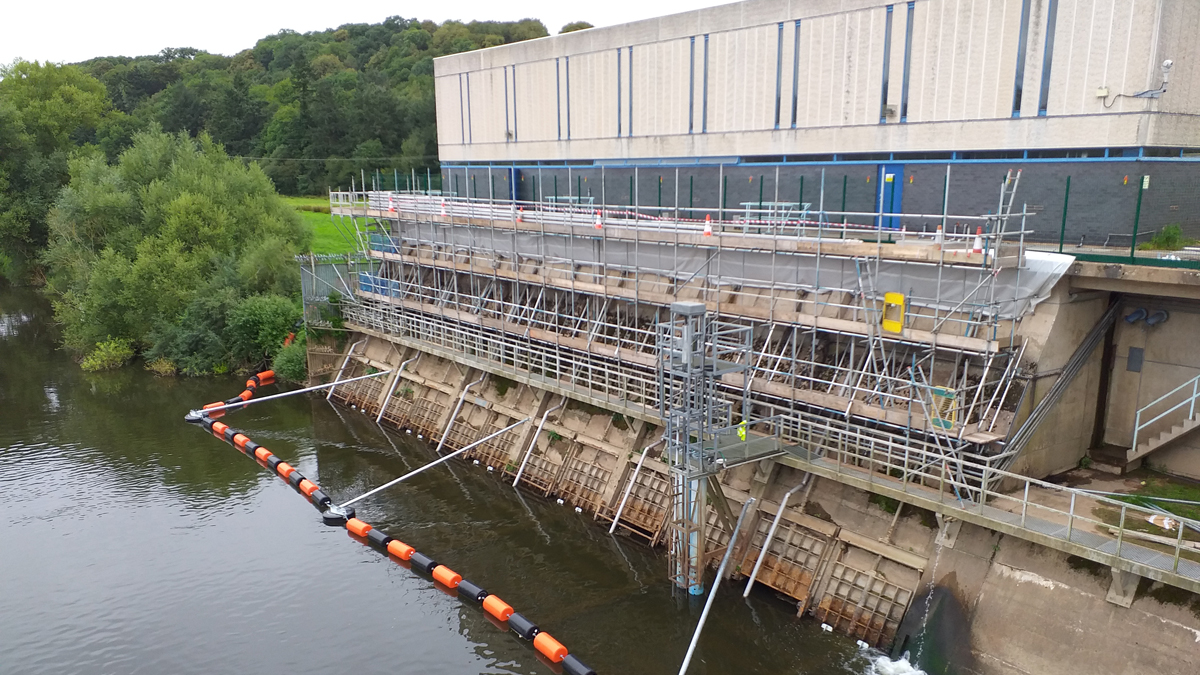
Hampton Loade Intake with Bolina Boom installed to exclude river users from screen area – Courtesy of Integrated Water Services (M&E) Ltd
The air backwash system was installed in the intake building on the top floor. The system comprised the local control panel, two compressors duty/standby, two air storage vessels duty/standby, actuated valves for screen cleaning in stages, and associated items including (food grade) oil/water separator.
The air storage vessels were installed perpendicular to one-another resulting in a smaller footprint (considering maintenance access for both receivers in parallel, plus cable containment) and the compressors were sited between them. The local control panel was sited on the external wall as was the air manifold with actuated valves. The pipework went through core drilled holes to the external compressed air pipework array.
The control philosophy was time based with differential level as a secondary trigger. For differential level control there was an ultrasonic head installed in a long stilling tube attached to the external intake tower. The internal ultrasonic level sensor was installed in a stilling tube that was designed to fit through a chamber and lead down to the intake sump.
Operational and alarm data was connected to the existing SCADA communications system IWS.
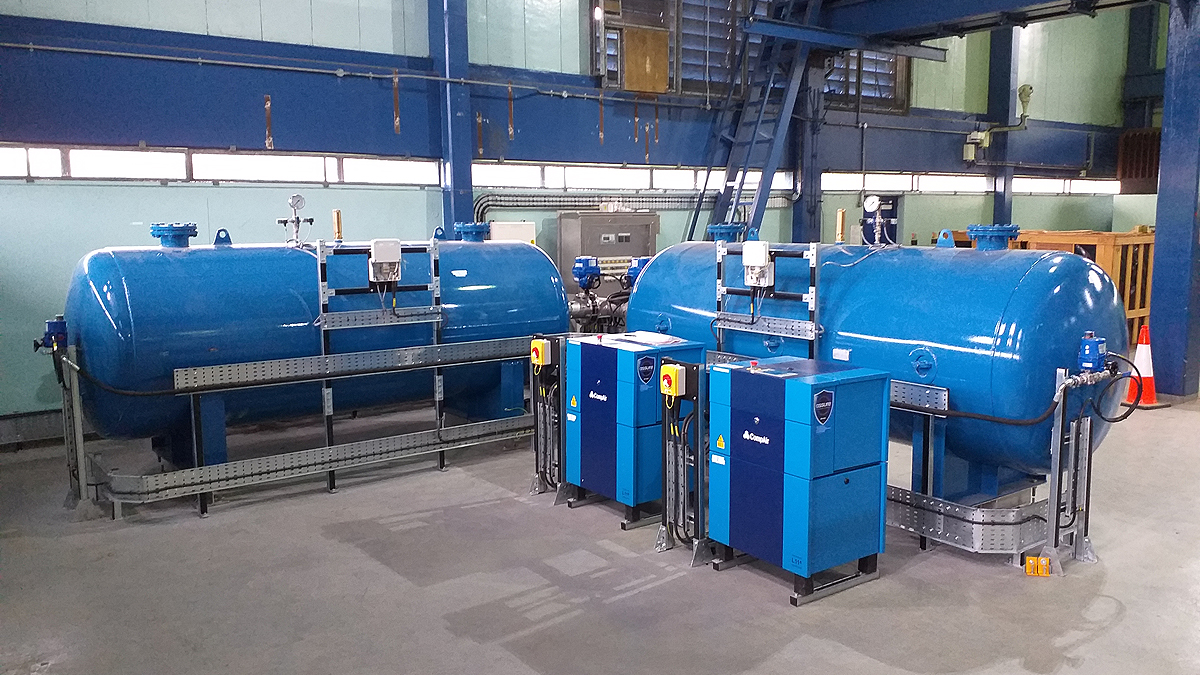
Compressed air backwash system – Courtesy of Integrated Water Services (M&E) Ltd
Completion
Following commissioning in September 2021, and functional testing to SSW satisfaction, the six open penstock doors were closed and from that moment all of the water abstracted at Hampton Loade Intake was flowing through the eel screens. No aquatic life or debris exceeding 3.0 mm was able to flow into the sumps. The screen area was sufficient to guarantee that the approach velocity would not exceed 0.15 m/s under maximum licence abstraction.