Strongford STW – THP & LTP (2022)
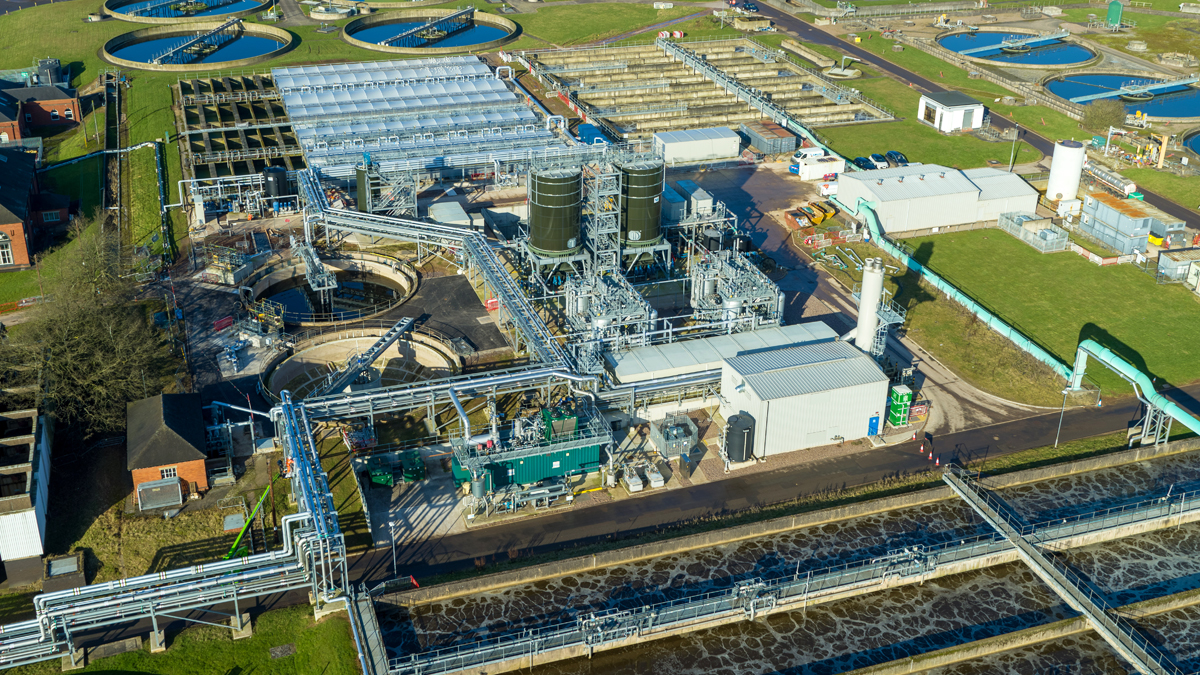
Strongford STW thermal hydrolysis plant and liquor treatment plant - Courtesy of Severn Trent
Strongford STW is a major sewage treatment works serving the population equivalent of circa 350,000 from Newcastle-under-Lyme and Stoke-on-Trent. The site’s sludge treatment facility provides a major centre for regional operations. Based on a forecast increase in population, it was identified that an increase in treatment capacity would be required to accommodate the local growth. To enable this, Strongford STW was identified by Severn Trent as the ideal location for the implementation of a second thermal hydrolysis plant (THP), following the successful THP implementation at Minworth STW.
Project aims
THP implementation aims to transform Strongford STW into a sludge treatment hub, capable of receiving increased volumes of sludge to a total of 94TDS/d, hydrolysing the feedstock, generating and managing additional biogas volumes, producing an enhanced digestate cake product and treating the resultant liquors. The key additional benefits of the THP implementation project are understood as follows:
- Increase in annual revenue.
- Reduction of CAPEX and OPEX costs, through centralisation of digestion capacity to allow closure of digestion facilities on satellite sites.
- Production of Class A sludge cake product.
- Increased energy self-sufficiency, through the ability to produce an additional electrical equivalent of 16.34 GWh gas.
- Reduction in operational carbon of 3.0 ktCO2e/year, contributing towards carbon reduction targets.
To deliver this project, Doosan Enpure Ltd was appointed through a competitive tender process, to complete the detailed design, procurement, construction, commissioning and performance testing of the thermal hydrolysis and liquor treatment plant.
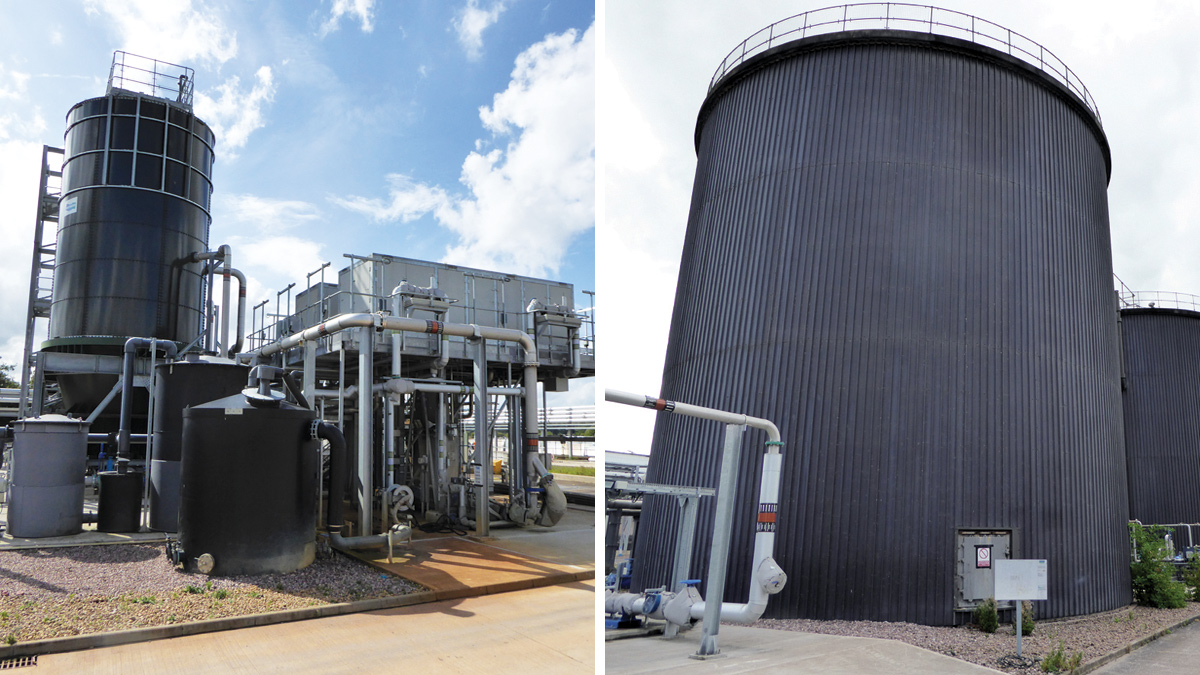
(left) Centrifuges and sludge cake silos and (right) digester bank – Courtesy of Severn Trent
Project scope
The project scope includes the following deliverables to achieve the THP implementation:
- Introduction of a cake reception facility.
- Introduction of a pre-THP dewatering process.
- Introduction of a THP process.
- Modification of existing digesters.
- Expansion of the gas management system.
- Modification of the digested sludge storage tanks.
- Introduction of a liquors treatment plant.
- Modification of electrical, instrumentation, control and automation (EICA) systems.
Detailed information for each project deliverable is provided below.
Cake reception facility implementation
Sludge cake is received from satellite sites a new cake reception facility at between 18-24% dry solids (DS) via road transport with product volumes up to 30m3. Cake is transferred using two duty Mono progressive cavity pumps from NOV Process & Flow Technologies with the assistance of boundary layer injection using site-final effluent to two CTM Systems Ltd pre-THP storage silos with capacity for approximately 2 days average sludge cake production.
Pre-THP dewatering process introduction
Thickened indigenous and liquid imported sludges at approximately 4-6% are processed through duty/standby Huber Technology Strainpresses and feed into a pump-mixed storage tanks before being dewatered to approx. 22%DS by two Alfa Laval duty centrifuges. Ancillary polymer storage, make up and dosing was included for the pre-THP centrifuges. Dewatered cake is also transferred to the pre-THP cake storage silos.
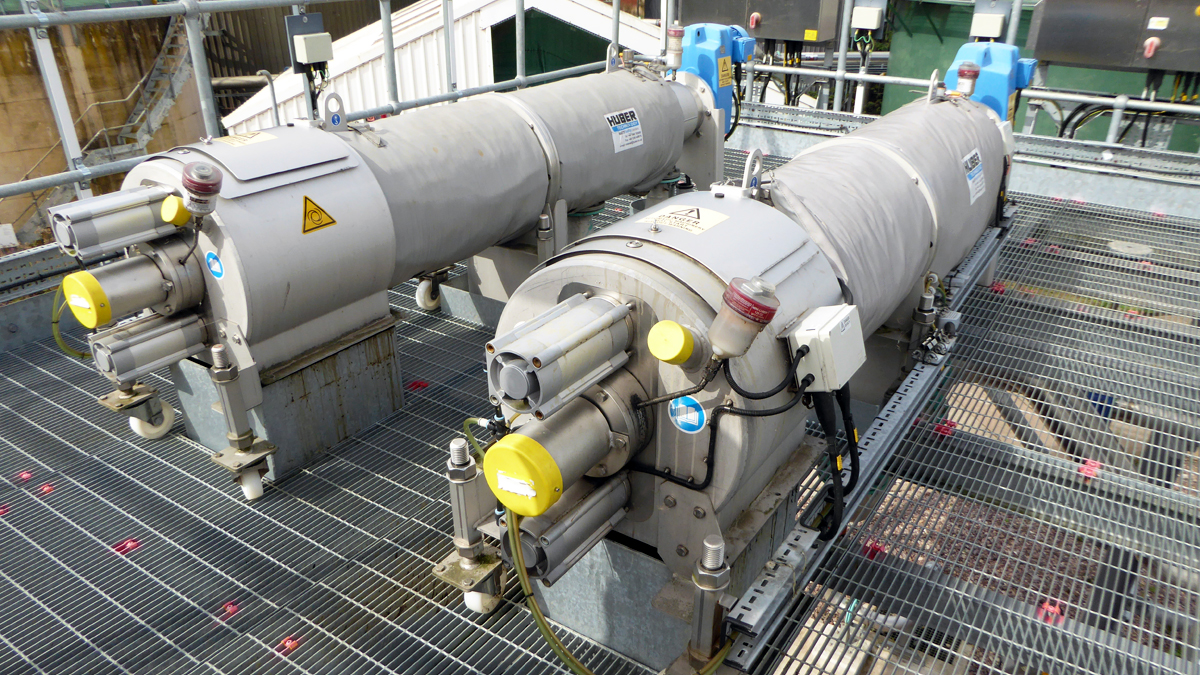
Huber Technology Strainpresses – Courtesy of Severn Trent
Cambi THP process
Two new duty/duty B4-4 Cambi THP streams are used to hydrolyse sludges prior to anaerobic digestion. Cake sludge is rewatered using final effluent to approx 16%DS before entering the process. Each stream is comprised of a pulper, four reactors and a flash tank, plus ancillary units. The pulper receives recycled steam from the flash tank, raises the temperature to 100°C and feeds homogeneous sludge forward into the reactors. Once filled in batch sequencing with sludge and steam, elevating the temperature to 160°C and 6 barg, each reactor is sealed for 20 to 30 minutes to allow for pathogen kill before flashing into an atmospheric pressure tank. The result is a hydrolysed sludge at approx 14%DS.
In order to avoid bacterial contamination of sludge following pasteurisation, a Xylem Water Solution duty/assist/standby ultraviolet (UV) treated FE system with a minimum six-log reduction compared to pre-UV samples provides dilution water for the THP and other service water, such as downstream centrifuge wash water.
Steam for the THP is generated using two duty/duty boilers, a dual fuel boiler (biogas and natural gas), and a heat recovery steam generation (HRSG) boiler which recovers heat from the exhaust of a new 1MW biogas CHP. Each boiler is capable of producing three tonnes of steam per hour into a common header, sufficient for one THP stream at 54TDS/d.
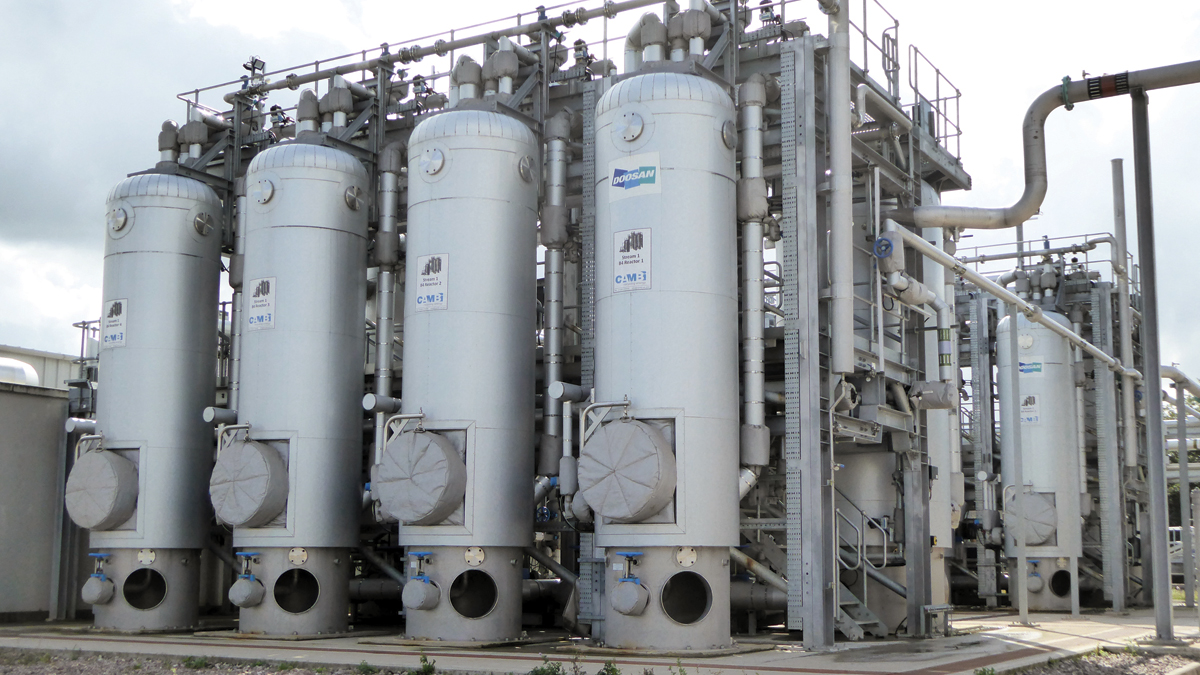
Cambi thermal hydrolysis plant – Courtesy of Severn Trent
Digester modifications
Hydrolysed sludge fed from the THPs is split in two streams, each stream feeds three digesters with a common recirculation line cooled using an HRS Group tube-in-tube heat exchanger using site final effluent as a cooling medium.
Digester spill chambers and pipework has been modified to minimise the effect of THP sludge density change events, an existing Utile Engineering continuous unconfined gas mixing systems has also been modified and refurbished, and digester instrumentation replaced.
Gas management system expansion
Two existing floating roof gas holders were replaced with a new Utile Engineering gas bag which receives biogas and buffers peaks in gas production to maintain a consistent feed composition for the equipment using biogas.
The site biogas system include the existing biogas to grid system, a new Thorne International Boiler Services (TIBS) dual fuel steam boiler, new Clarke Energy CHP engines and a new Uniflare Ltd waste gas burner and emergency vent.
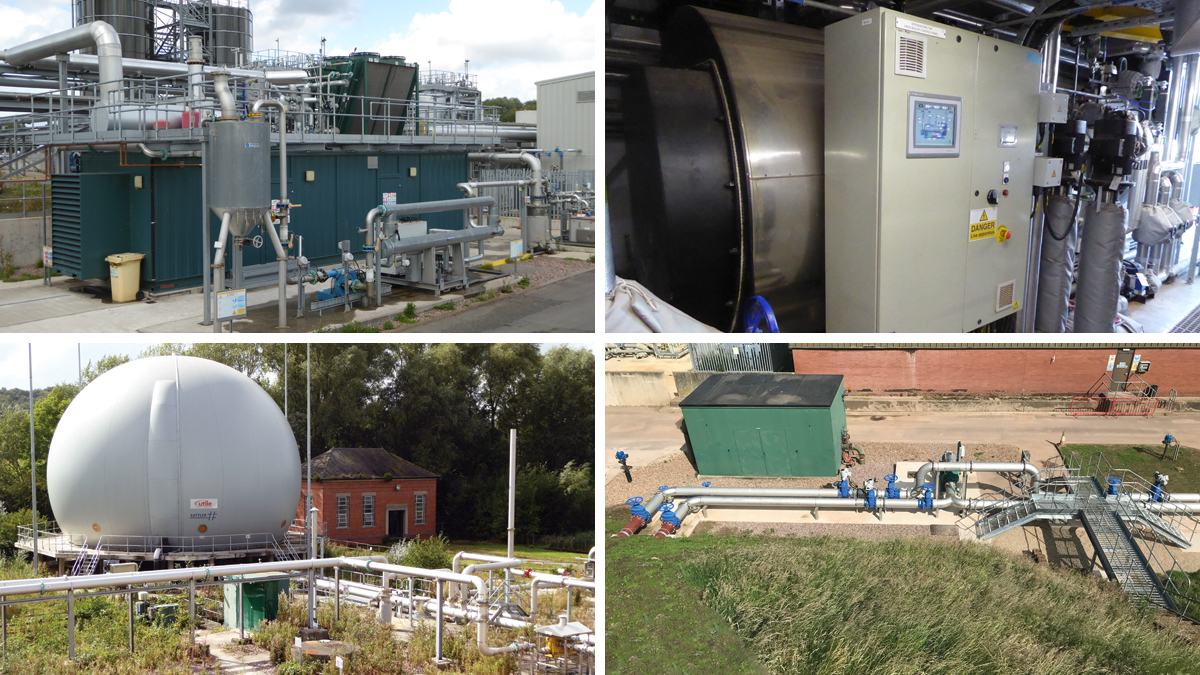
(top left) Biogas CHP unit, (top right) HRSG boiler, (bottom left) Utile Engineering gas bag and (bottom right) digested sludge pump mixing system – Courtesy of Severn Trent
Digested sludge storage tank (DSST) modification
Two existing 3,500m3 pathogen kill tanks were emptied, refurbished and fitted with a shared duty P&M Pumps pumped mixing system designed to minimise settlement, surface crust formation and provide a consistent %DS feed to the final dewatering plant.
This scope of works was managed directly by Severn Trent who undertook principal contractor and designer CDM responsibilities. During tank emptying, digestate was process using a shaking screen and silt removal unit to separate the high grit and rag content, and dewatered using a containerised centrifuge.
Amtreat® liquor treatment plant (LTP)
A detailed model of the treatment process was developed by Primodal and identified opportunities for improvement in the existing works’ operation and defined the existing liquors treatment capacity of the site.
To treat the higher ammonia concentration liquors consequent of the THP process and ensure that the load returned to the head of the works was not increased, a new ACWA Services Amtreat® liquor treatment plant was installed. Seven redundant ASP lanes and an associated final settlement tank were refurbished for use as the LTP by Severn Trent. Doosan re-purposed another FST as a balance tank upstream of the LTP. Heat is required to maintain the design lane temperatures between 26-34°C. An existing hot water loop connected to CHPs, was no longer required to heat digesters. This was modified and extended to service an HRS Group tube-in-tube heat exchanger at the LTP, which provides heat to the process by means of an internal recycle. Insulated roof covers were also installed over the lanes to prevent crosswind heat losses, additional detail described in engineering challenges.
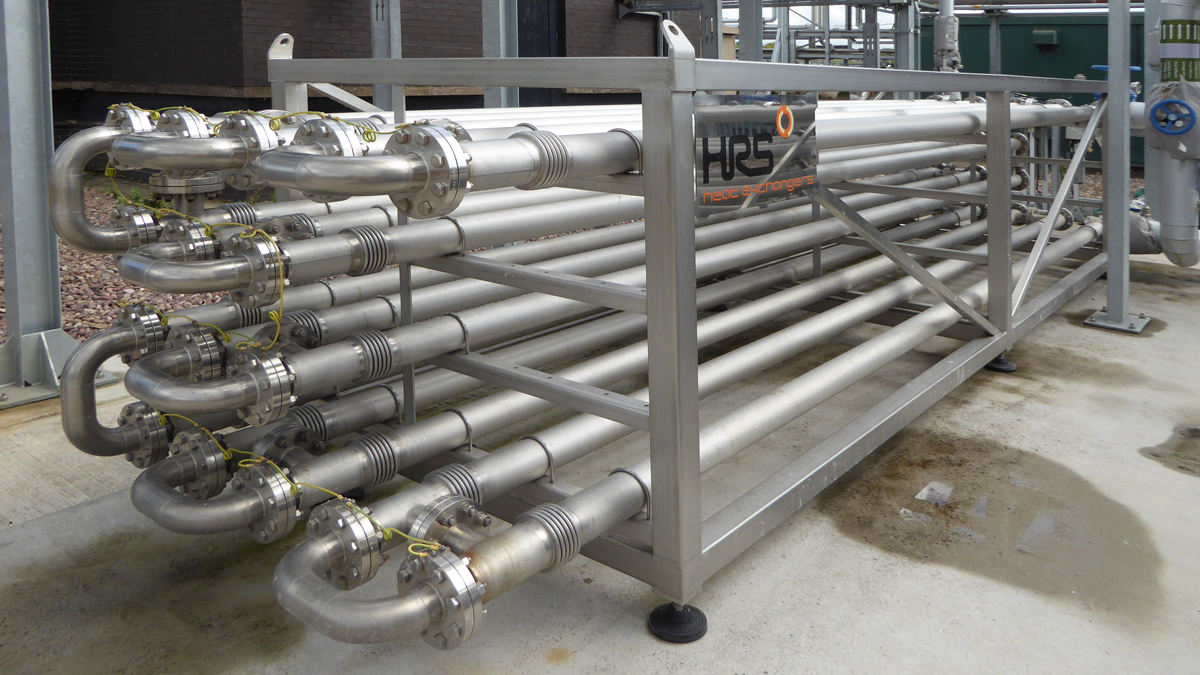
HRS Group heat exchangers – Courtesy of Severn Trent
Strongford THP & LTP: Supply chain – key participants
CONTRACTED DIRECTLY WITH SEVERN TRENT
- Digester emptying & cleaning/DSST mixing systems: GTS Maintenance
- Main designer/contractor: Doosan Enpure Ltd
- CHP engines: Clarke Energy
- Civils refurbishments: Makers Construction
- Boiler & THP operational support/training: PBJ Engineering Services Ltd
CONTRACTED DIRECTLY WITH DOOSAN ENPURE
- Thermal hydrolysis plant: Cambi Ltd
- Civil engineering: Barhale
- Civil engineering: MAST
- Civils design: GHD
- Imported sludge reception & sludge silos: CTM Systems Ltd
- Software integration & MCCs: BGEN Ltd
- Sludge screen Stainpresses: Huber Technology
- Stainless steel pipework: ABC Stainless Ltd
- Polymer systems: Richard Alan Engineering
- Odour control system: Air-Water Treatment Ltd
- Electrical installation: Main Electrical Ltd
- UV disinfection system: Xylem Water Solutions
- Dewatering centrifuges: Alfa Laval Ltd
- Progressive cavity pumps: Mono Pumps – NOV Process & Flow Technologies UK Ltd
- Final effluent filters: Bollfilter UK Ltd
- Pump mixing systems: P&M Pumps
- Service water tanks: Forbes Tanks Ltd
- Digester emptying & cleaning: Thorne International Boiler Services
- Waste gas burner: Uniflare Ltd
- Digester gas mixing & gas bag: Utile Engineering
- Heat exchanger sludge coolers: HRS Group Ltd
- LTP detailed model: Primodal
- Amtreat® liquor treatment plant: ACWA Services
- LTP lane covers: Power Plastics Ltd
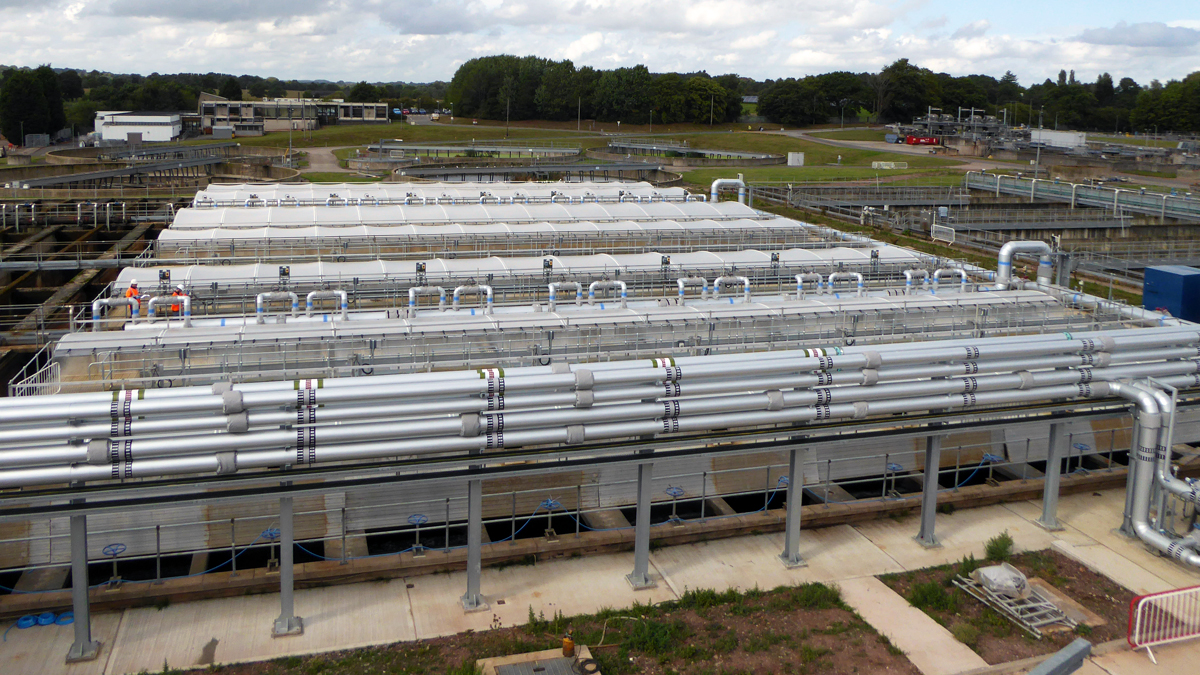
Liquor treatment plant lanes – Courtesy of Severn Trent
EICA works
An EICA enabling project upgraded the SCADA system, replaced PLCs and installed a site-wide fibre communications network to facilitate the integration of the new and existing equipment. BGEN Ltd supplied and installed three new MCCs on site connected to the network, which control the distributed plant and interface with the SCADA system.
Engineering challenges
- Refurbishment of existing structures: A notable challenge was the refurbishment of an abandoned ASP and FST which were selected for use as the structure of the LTP. Due to the age of the structure and concerns identified during a survey, specialist refurbishment contractors were engaged. Makers Construction undertook the required works to repair cracks in the structure and apply a protective coating and installed sacrificial anode to extend the structure’s life. These works could only be completed in low moisture conditions above certain temperatures. As such, weather was a particular impacting factor, with the programme of works disrupted by rain and cold weather. An anti-flotation valve was also installed in one of the FSTs to relieve groundwater pressure on the structure.
- LTP lane covers: A new cover was required for the LTP lanes to reduce heat losses due to surface cross-winds, and thus eliminate unnecessary heat demand, as the LTP design operating temperature range is 26-34°C. Due to the reuse of the structure, a bespoke roof installation was required. Power Plastics Ltd was contracted to design and install the roof covers. The design was based on aluminium extruded main trusses with insulated and removable tensile PVC roof sheets. Additionally, inclusions were made for a number of walkways across the lanes for access to M&E equipment and visibility into different lane cells.
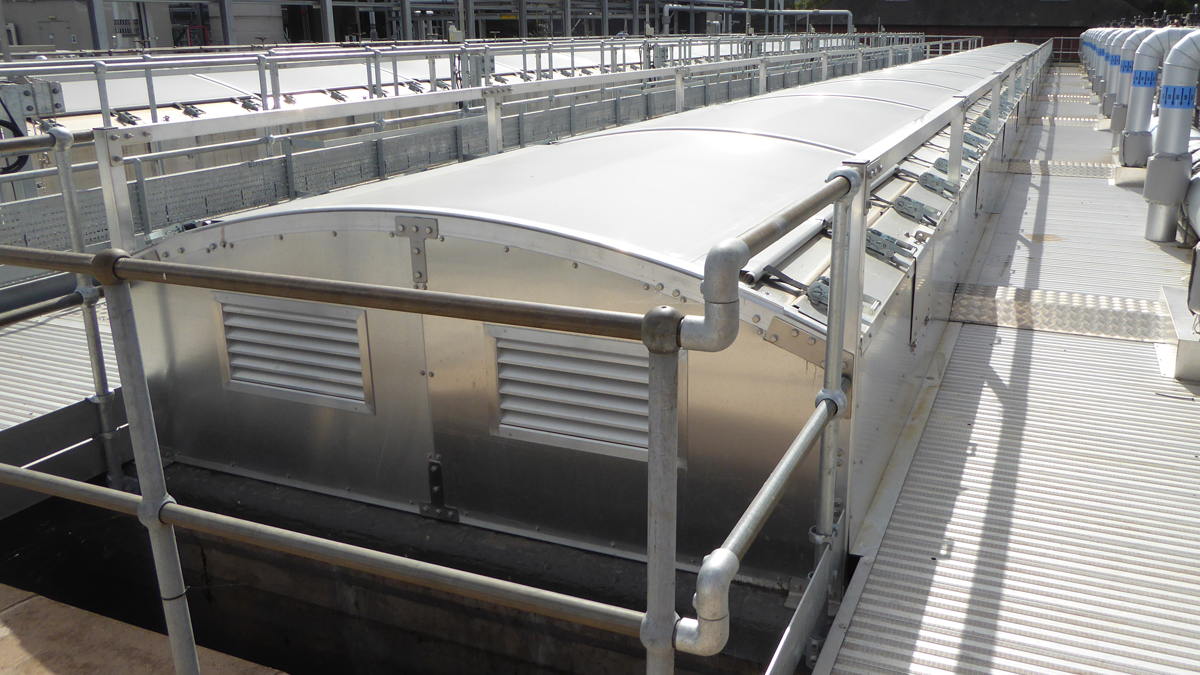
LTP lane covers from Power Plastics Ltd – Courtesy of Severn Trent
Progress
At time of writing (September 2022) the THP and ancillary scope are operational and have been taken over by the Severn Trent following successful performance tests. The LTP is currently in late process commissioning, and when operational, will facilitate the final ramp up and performance tests.