Faringdon to Blunsdon Trunk Main Phase 2 (2023)
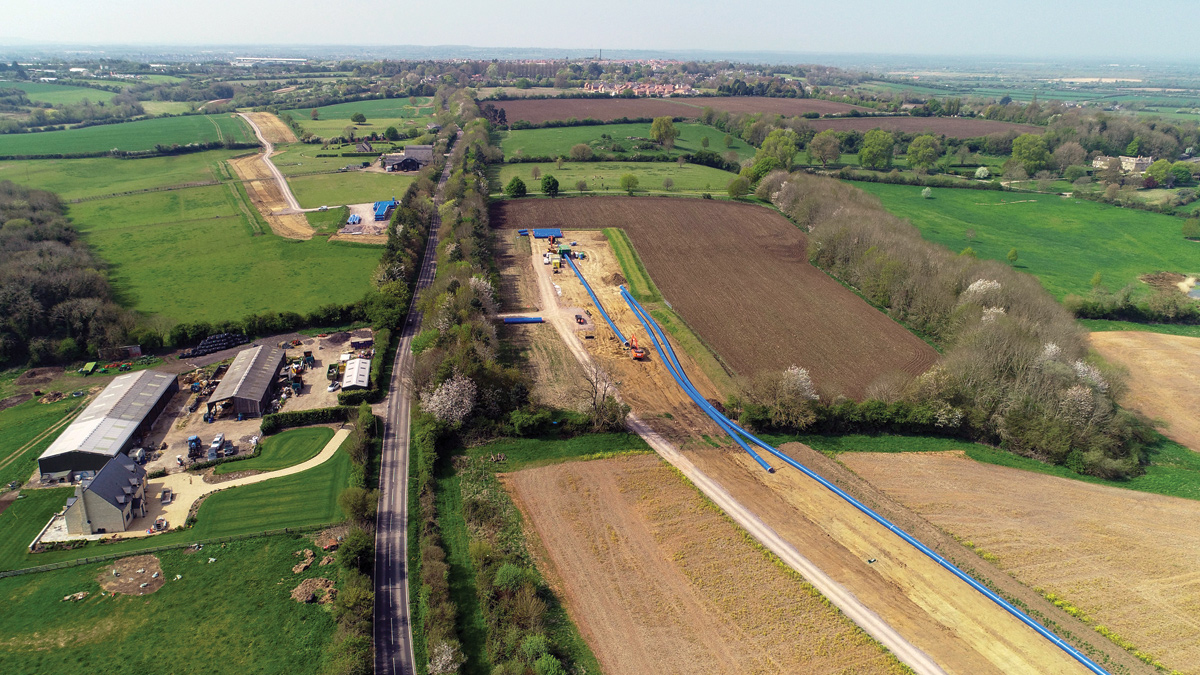
Aerial photograph of the pipeline route - Courtesy of Kier Infrastructure and Overseas Ltd
The water network in the western end of the Thames Valley Supply Area is dominated by local borehole water sources. Over time, population growth coupled with general environmental drivers to reduce reliance on groundwater sources in sensitive chalk stream areas, Thames Water has sought to improve supply resilience and deployable output by linking local sources via trunk mains. This allows movement of water from one area to another as well as to reliably supply the intermediary supply zones. Typically, water from Oxford that is produced at Farmoor Water Treatment Works is transferred via a series of trunk mains to maintain resilient customer supplies to approximately 90,000 people in Swindon and the surrounding supply areas.
Background
The existing Faringdon Water Booster Station (WBS) to Blunsdon Reservoir transmission system comprises a 700mm diameter asbestos cement pipe and a 900mm diameter glass reinforced plastic (GRP) pipe built in 1987 and 2001 respectively. This transmission system is approximately 15.8km long and has various interconnections between the pipes to provide resilience in service.
The Faringdon WBS to Blunsdon Reservoir 900mm GRP main represents one leg of this network. Due to the high frequency of failures, which had a significant impact on Thames Water’s ability to transfer treated water into the Swindon area, work began in AMP6 to replace the highest risk section in the Highworth area and 2.8km was completed, including a crossing of the River Cole. Following the successful replacement in AMP6, and an increased deterioration of the existing 900mm GRP main, the remaining balance of scope (13.7km) was approved for delivery in AMP7.
To mitigate the frequency of bursts and the impact of the deteriorating asset on customer supplies, temporary emergency abstraction licences at Baunton WTW and Latton WTW were secured with the Environment Agency to allow the existing GRP main to be operated at a lower duty.
Project summary
The principal drivers for the project are:
- To reduce the supply interruption risk to customers in Swindon and the Cotswold area. In a reasonable worst-case scenario, without the current mitigations it could equate to over 14 million minutes.
- To minimise the risk of customer complaints associated with low pressure and/or no supply. In a reasonable worst-case scenario, without the current mitigations this could equate to over 90,000 properties.
- To eliminate reliance on groundwater sources under emergency licences to cover the loss of flow during a burst.
- To reduce reliance on groundwater sources that draw from chalk streams and the River Kennet during high demand and drought conditions.
- To increase trunk main capacity and transfer rates to accommodate increasing flows for future population growth (principally in the immediate Swindon area).
- To eliminate the frequent and expensive repair costs of the existing GRP main sections.
- To restore Thames Water’s trunk main network resilience and bulk transfer capability in this area, which is fundamentally impaired when the Faringdon to Blunsdon main is operating at a reduced duty rating.
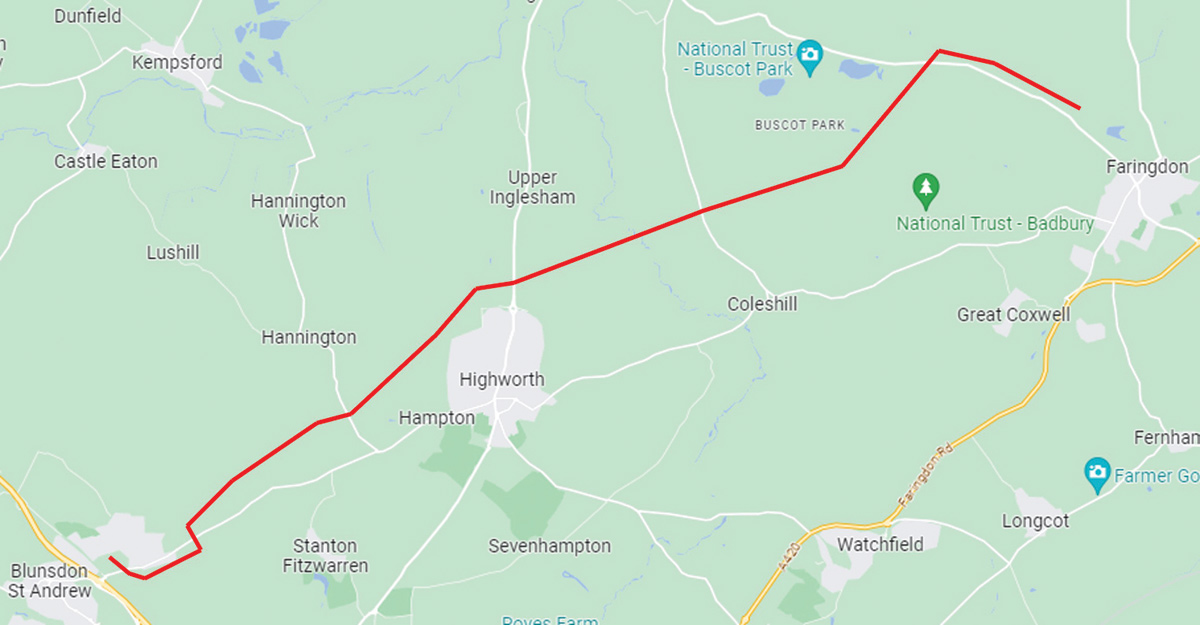
Google Maps image showing pipeline route
Planning and design
Pipeline route: Initial design work was completed during AMP6 by Stantec UK as part of the Phase 1 delivery. The proposed route closely follows the existing 700mm asbestos cement and 900mm GRP mains, and there are several advantages to following this existing route:
- This represents the most direct route between Faringdon WBS and Blunsdon Reservoir thus minimising the overall length of pipework required.
- It is mainly through farmland and minimises the need to work in residential areas.
- It minimises impact on landowners.
- Ease of access for Thames Water through use of existing way leaves
- Existing information from previous investigations can be utilised.
The AMP7 project was awarded to Kier Infrastructure and Overseas Ltd when detailed design of the pipeline route was reviewed and refined, taking account of ecological constraints, requirements from landowners and planned developments along the route.
Archaeological mitigation: A programme of archaeological mitigation was undertaken by Wessex Archaeology following consultation with the relevant county archaeological advisors. A mitigation strategy comprised excavation, recording and the strip, map, and sampling. The archaeological excavations formed part of a staged approach consisting of an archaeological desk-based assessment, geophysical surveys, and archaeological evaluations.
Through collaboration with the approving authorities, Thames Water adopted targeted route changes to avoid known areas of high archaeological interest. Generally, a small number of finds were found with possibly the most significant being a crouched burial in the Blunsdon section of the pipeline.
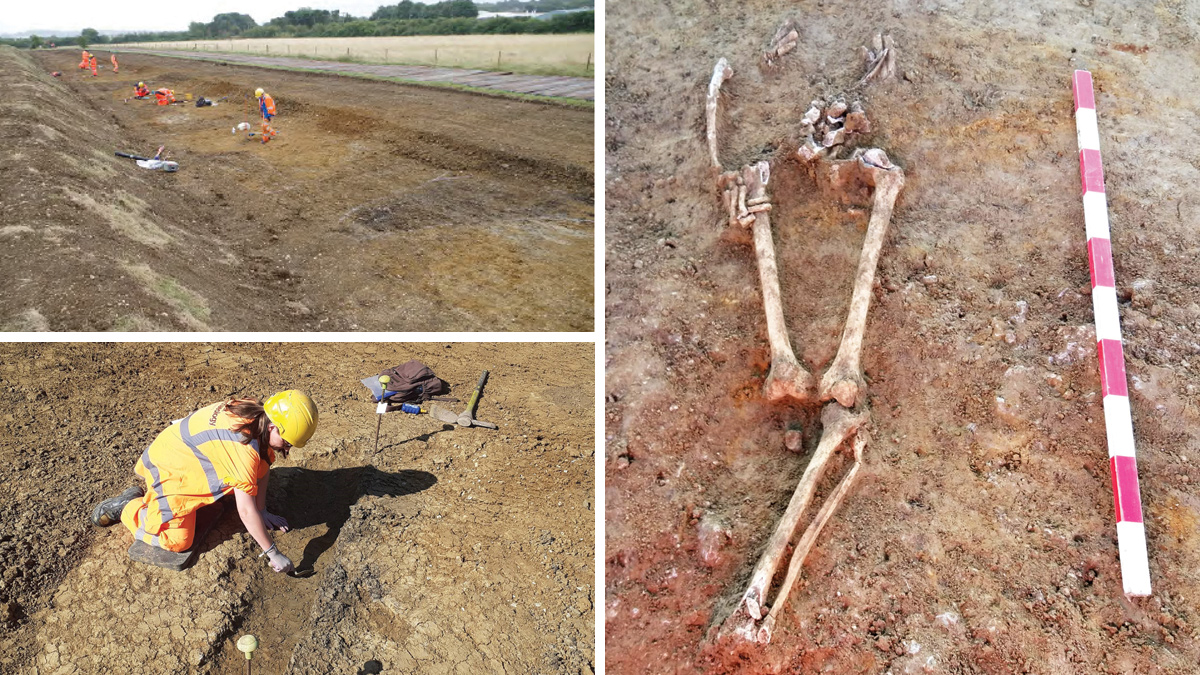
Archaeological investigations and (right) crouched burial – Courtesy of Kier Infrastructure and Overseas Ltd
Pipe material: As part of the design deliverables a technical note was prepared comparing ductile iron, carbon steel and HDPE as the three commercially feasible materials for this diameter range.
The recommendation was to adopt HDPE PE100 as the preferred pipe material, using 1200mm OD SDR17 from Aliaxis UK. Pipework used in cross connections, existing utility crossovers, shafts and other special cases was designed using ductile iron supplied by Saint Gobain PAM UK, with mechanically restrained VE joints as required.
Furthermore, for the tunnel sections, steel pipework with the E-Joint system was utilised supplied by Noksel España. To ensure asset design life, steel pipework was maximised for the critical tunnel sections with pipe wall thickness specified at 10mm, which was greater than Thames Water’s asset standard of 6mm. Based on the pH levels of the water the pipe would be conveying, a far superior asset design life of 100+ years could be theoretically achieved.
Environmental impact assessment (EIA): During the initial stages of the project, several desktop and detailed environment, archaeological and third-party assessments and reports were compiled. This highlighted areas where further surveys and investigations were later completed ahead of an Environmental Impact Assessment Screening Opinion being submitted to the relevant councils for review.
A full EIA was requested but this was, however, successfully challenged with the Secretary of State who did not consider the environmental impact would be of a magnitude necessary to suggest a scheme of this scale would result in significant environmental effects, which would exceptionally necessitate an environmental statement. This successful challenge still obligated Thames Water to work closely with the local approving authorities to deliver a comprehensive programme of environment and archaeological mitigation works for the route.
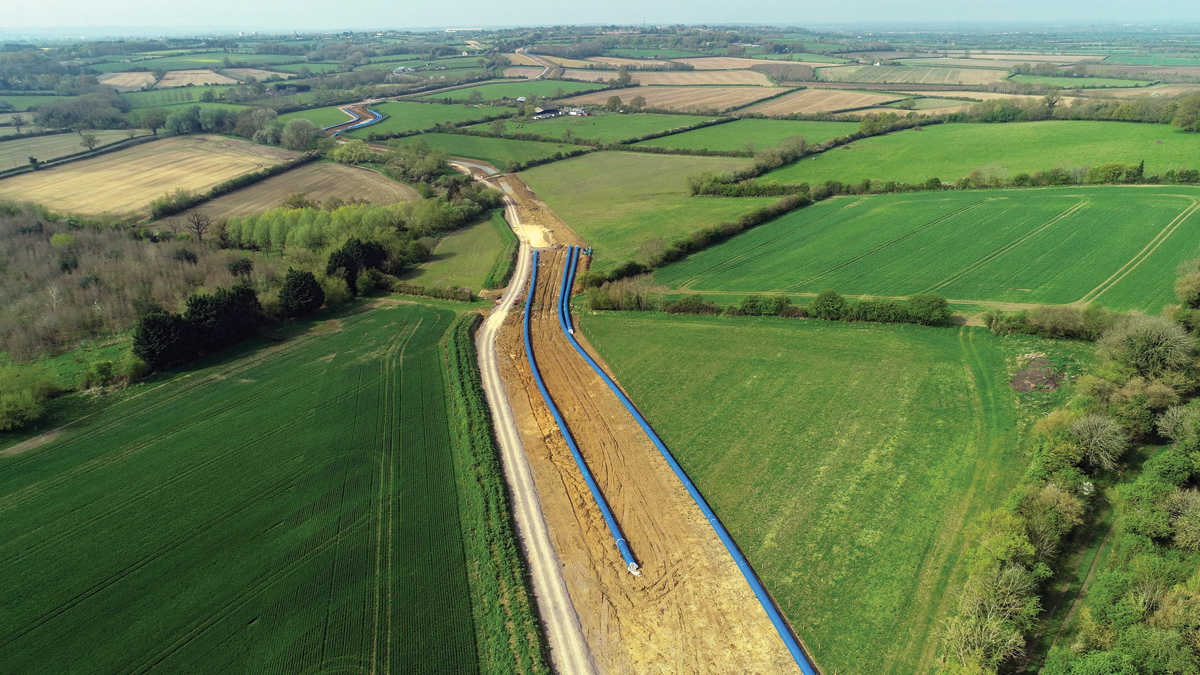
Pipes laid along route – Courtesy of Kier Infrastructure and Overseas Ltd
Faringdon to Blunsdon Trunk Main Phase 2: Supply chain – key participants
- Project delivery: Kier Infrastructure and Overseas Ltd
- Designers & specialist consultants: WSP
- Sahara survey: Water Research Centre Ltd
- Archaeological investigations: Wessex Archaeology
- Civil Engineering Contractor: CPC Civils
- Civil Engineering Contractor: OCC Services Ltd
- Trenchless crossings: HB Tunnelling Limited
- Shoring/temporary works: GroundShore Ltd
- Tunnel boring machine: Herrenknecht
- Precast jacking pipes: FP McCann
- HDPE PE100 pipe: Aliaxis UK
- Ductile iron pipes: Saint Gobain PAM UK
- Steel pipework: Noksel España
- Tunnel roller spacers: FT Pipeline Systems
- Pipe fittings, bends, tees & collars: George Green (Keighley) Ltd
- Pipe fittings: Wolseley
- Pipe fittings: Electrosteel Castings (UK) Ltd
- Pipe fittings: PTS (SA) Limited
- Valves: AVK UK Ltd
- Welding: Fabricon Ltd
- Welding: PTS Group
- Butt fusion welding machine: McElroy Manufacturing
- Independent weld inspector: Technical Innovation Servis Ltd
- Temporary fencing & gates: RF Gardiners Ltd
Construction
The project was classified as a ‘high consequence project’ requiring an enhanced level of quality assurance. To achieve this, several measures were implemented. As part of this strategy, the delivery contractor Kier Infrastructure and Overseas Ltd was briefed to deliver the project in phases to tactically reduce Thames Water’s operational risk until the project was fully commissioned.
The project brief also included decommissioning of the existing fragile 900mm GRP which will be safely decommissioned following commissioning of the new DN1200 pipeline. The contractor will make allowances to ensure that the existing 900mm GRP main can be slip-lined in the future for additional resilience.
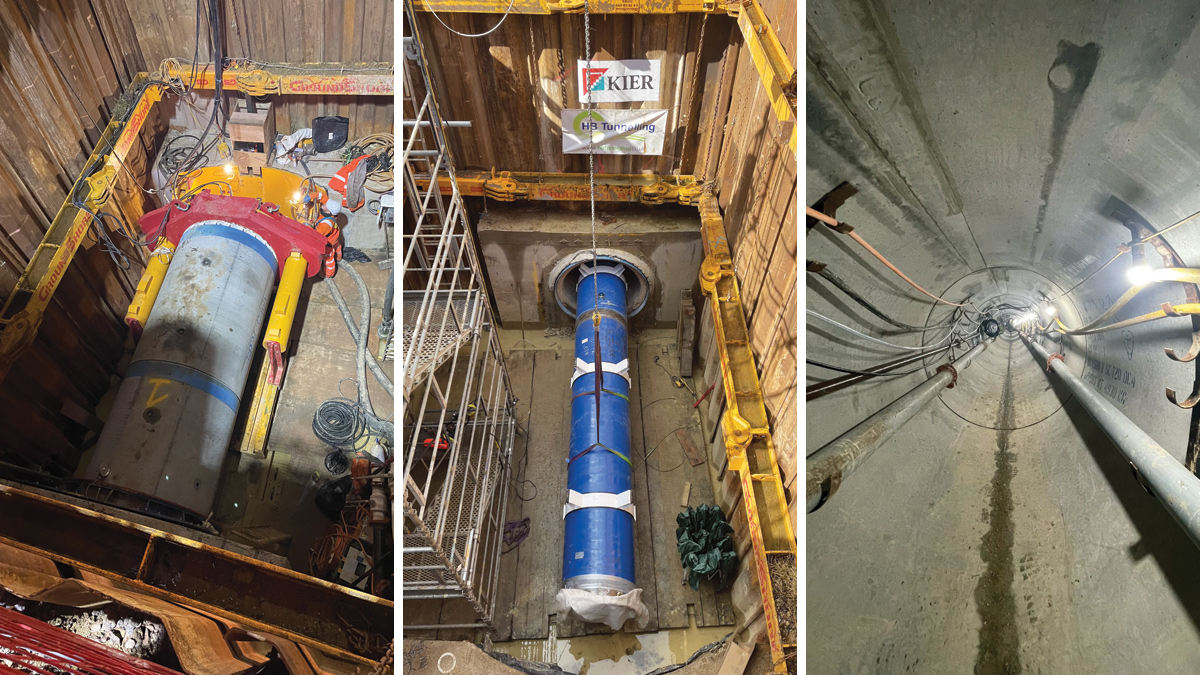
(left) Drive shaft, (middle) tunnel pipe insertion and (right) the completed tunnel – Courtesy of Kier Infrastructure and Overseas Ltd
Tunnelling: Open cut techniques were the predominant pipe installation methodologies and were undertaken by CPC Civils and OCC Services Ltd. However, several trenchless crossings were required for the major roads and rivers crossed by the pipeline route. The relatively straight forward digger shield tunnel boring machine was the predominant method used for trenchless crossings, including Bydemill Brook and the A361.
The crossing of the B4019 proved more challenging however, when hard rock was discovered. This was because of a last-minute change in the location of the micro-tunnel shaft to avoid a new attenuation pond being built by a developer in the immediate area.
Following a review of the new geotechnical investigation completed, it was agreed that the previous digger shield tunnel boring machine was not suitable to overcome the hard rock. Instead, the more robust variable density tunnel boring machine was employed with a specialist drill head brought in from Herrenknecht in Germany to cope with the density of the rock. Although the deployment of this complex machine took four weeks to set-up, the 180m long, 1.5m diameter tunnel was constructed in no time at all and was successfully completed in just over eight weeks. The trenchless crossings were undertaken by HB Tunnelling Limited.
Pipe welding: An automatic butt fusion welding machine was utilised on the project to enable the joints to be made in what was an industry first. The machine from McElroy Manufacturing was shipped from the United States for the project, and enabled butt fusion joints to made up to 1200mm in diameter; a first of its kind in Europe. The automatic nature of the machine enabled far higher quality welds to be made and on a consistent basis as the human element of checking temperatures, raising of the welding plates etc. was eliminated.
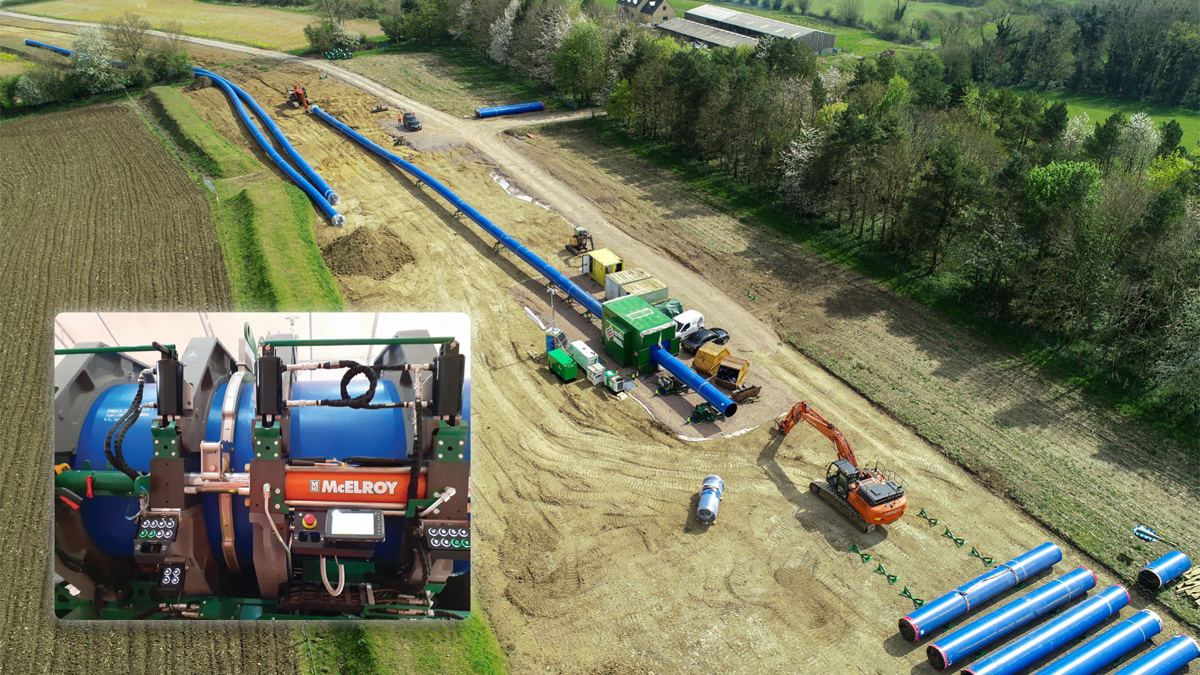
Pipe welding operation and (inset) McElroy Manufacturing welding machine – Courtesy of Kier Infrastructure and Overseas Ltd
Welding work was undertaken by Fabricon Ltd and PTS Group with Technical Innovation Servis Ltd employed as an independent weld inspector to provide an additional level of assurance on the quality of the butt fusion joints made on the 1200mm OD PE100 SDR17 pipework.
Commissioning
Due to the large volume of water involved in commissioning each section of the new pipeline and significant flow rates required to achieve water quality standards, flushing lagoons were constructed to allow the safe and controlled disposal of the flushing water.
Working in the community/customer communications
Following disruption to landowners over many years due to frequent bursts on the existing GRP pipe, all contractors have been fully focused on maintaining and improving relationships with all landowners. At the time of writing (May 2023), Kier Infrastructure and Overseas Ltd and CPC Civils have worked very successfully with all landowners along the new pipeline route developing great working relationships. This has been demonstrated on a few occasions particular during the funeral of one landowner who CPC Civils had developed a great relationship with, when works were stopped so all workers could pay their respects.
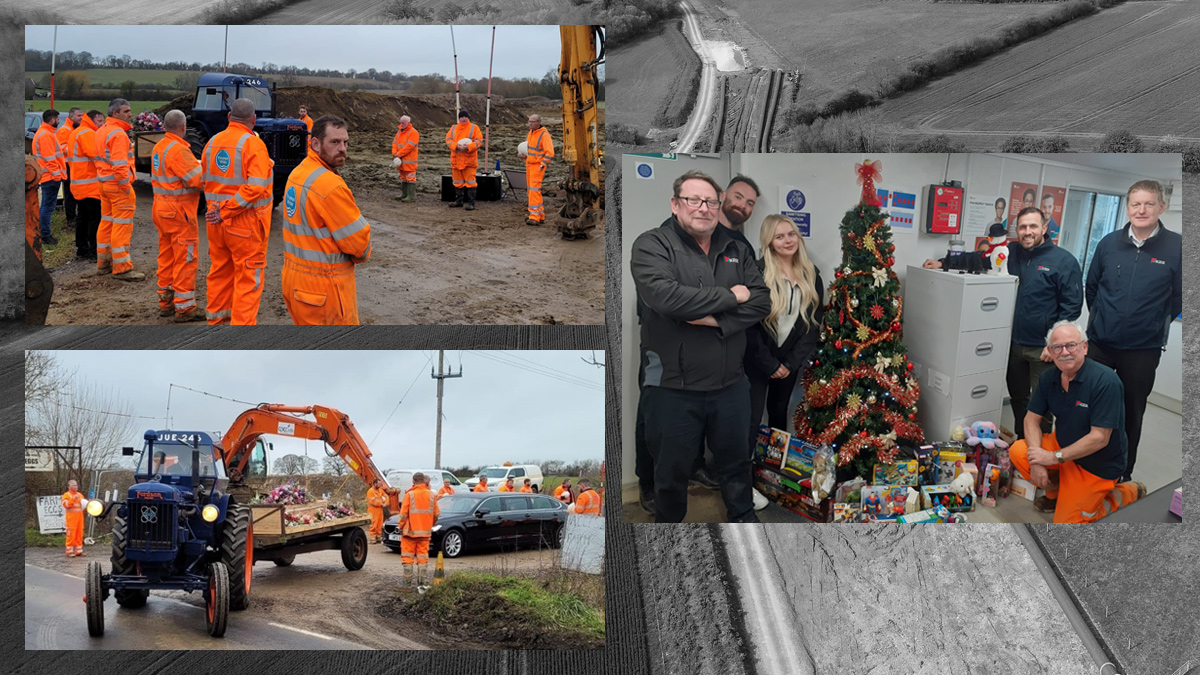
(left) Funeral cortege – Courtesy of CPC Civils, and (right) Salvation Army Christmas present appeal 2022 – Courtesy of Kier Infrastructure and Overseas Ltd
Kier have also worked well with local councils donating materials for community initiatives, with CPC Civils also donating two portable defibrillators to support local campaigns, as well as supporting a Salvation Army present appeal on the run into Christmas 2022 to support families who would otherwise be unable to afford gifts for their children.
The project has also given the opportunity to work with the royal agricultural university and bring students to site to understand the ecological and environmental impact and considerations on a project of this scale, as well as visiting their workshops to build owl boxes to be installed along the route of the pipeline.
Summary
Design of the £45m Faringdon to Blunsdon Pipeline Project commenced in November 2020 followed by a construction start in May 2021.
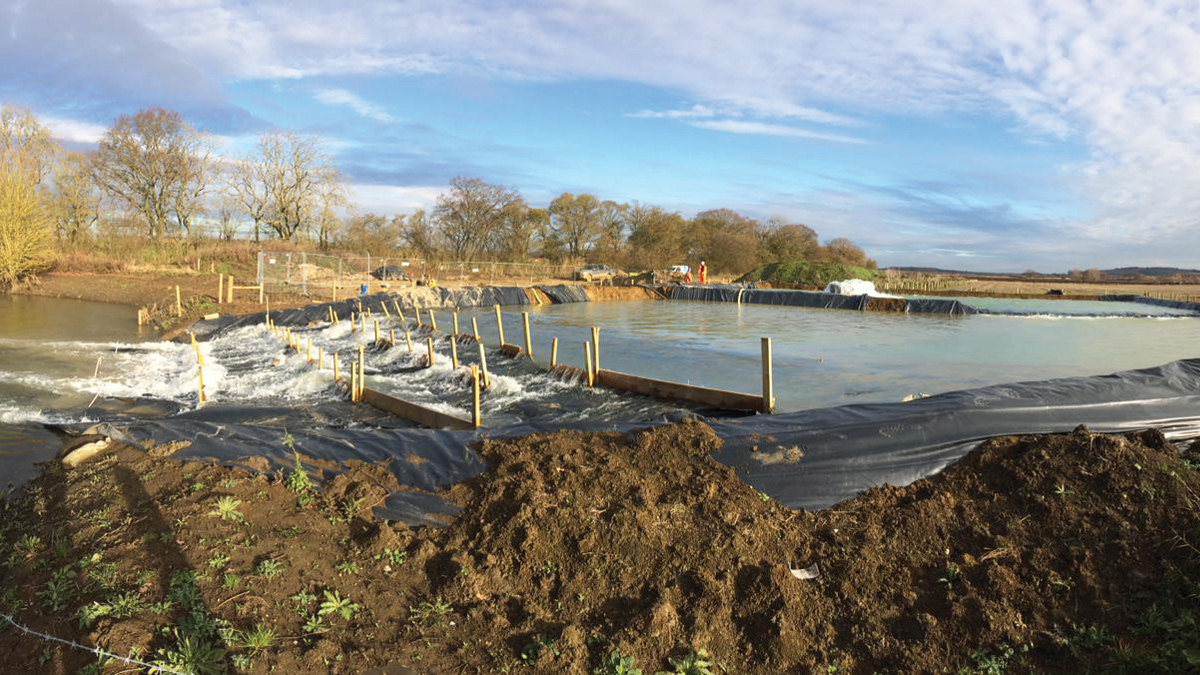
Flushing lagoons – Courtesy of Kier Infrastructure and Overseas Ltd
Commissioning and beneficial use of the pipeline is expected in November 2023 with all site works being completed by August 2024. This will complete replacement of the 15.8km transmission system providing resilience to supplies to help meet future supply and demand requirements.