Mill Fleam Pumping Station (2023)
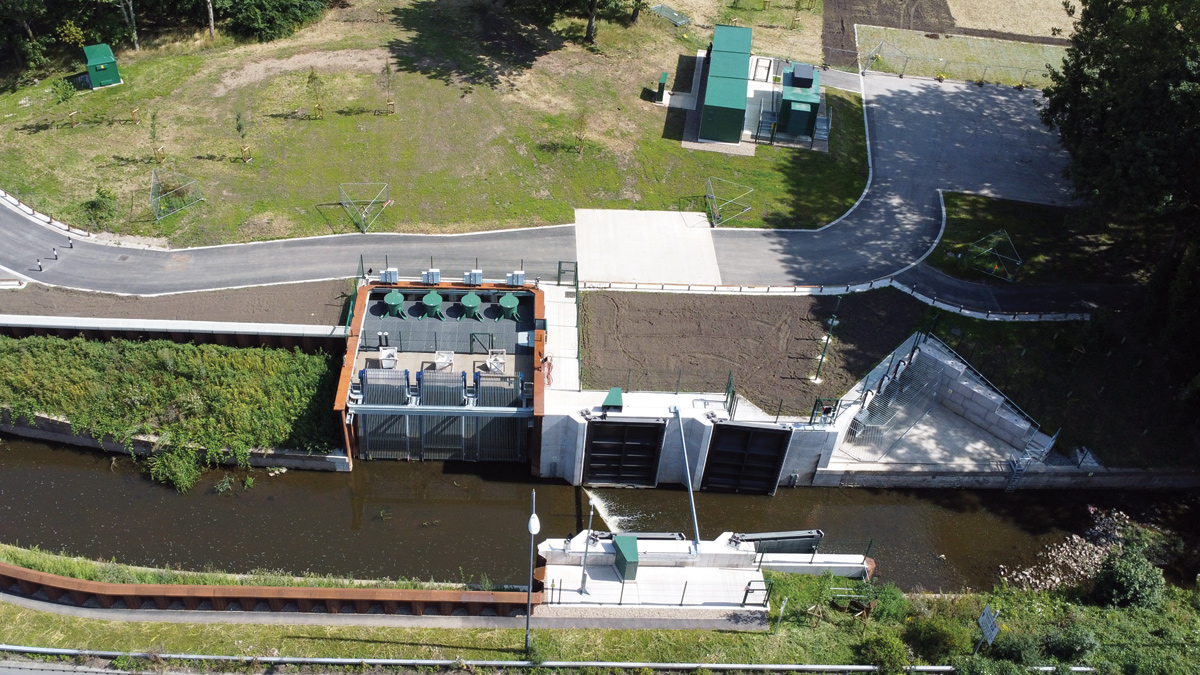
Completed Mill Fleam Pumping Station - Courtesy of JBA-Bentley
Over recent years, Derby’s city centre has suffered historic river and surface water flooding. In partnership with the Environment Agency, Derby City Council sponsored the £8m Mill Fleam Pumping Station project; a key piece of flood defence infrastructure that barriers off and then over-pumps Markeaton Brook when the River Derwent is in flood. In November 2021, JBA-Bentley, a joint venture between JBA Consulting and JN Bentley Ltd, was awarded a contract to design and construct the pumping station, with a completion date set for April 2023; after just 15 months.
Background to the project
The site is within a wooded public park adjacent to the city centre. Bats, birds, aquatic life, third-party infrastructure and high-value trees have all been carefully considered and impacts mitigated during the works. Resilience has been considered in all aspects of operation to ensure the station will remain always ready to operate.
Funding streams required the station to be designed, procured, constructed and commissioned within 15-months, including planning and stakeholder approvals. To meet these challenges several innovations have been implemented:
- 3D and augmented reality improved resource use and safety.
- Off-site and factory manufactured products reduced site-time and enhanced quality.
- Collaborative design, commissioning, construction and client teams ensured the right solution at the right time.
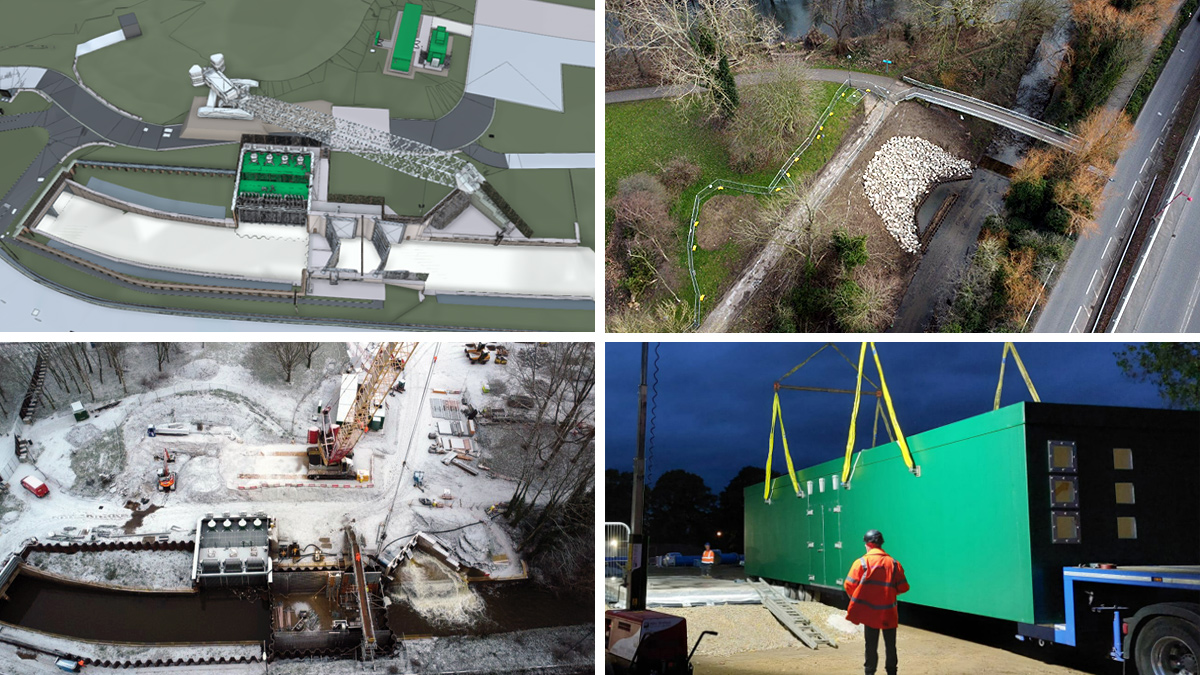
(top left) Modelling of the scheme included the main temporary works required, (top right) a fish refuge was part of habitat improvements implemented, (bottom left) in-channel works continued through the winter, and (bottom right) buildings were prefabricated and delivered to site pre-commissioned – Courtesy of JBA-Bentley
Programme management
As with all construction projects at this time, Brexit, COVID-19 and the war in Ukraine significantly disrupted the global supply chains and created huge uncertainly.
Timely supply of equipment and inflationary uncertainty were significant risks to the project. The team’s procurement strategy centred around early, continued and proactive engagement with the supply chain to minimise impacts.
Weekly coordination and update meetings were held with key suppliers. Miro visual planning software was used with each supplier to understand key risk areas, available float and interfaces between activities/disciplines. Potential blockers to progress were identified and owners assigned to manage and mitigate the impact; for example when PLC component lead-time was unacceptably fluctuating an alternative product was specified and then procured.
At each key stage of procurement and manufacturing, face-to-face updates and factory visits confirmed status and progress. This resulted in amendments to initial plans and supply chains – however, overall, all critical components were assembled on programme.
Due to funding requirements the programme for design and delivery was restrictive. Programme management was crucial to ensure timely delivery and commissioning. Our three levels of programming approach ensured a realistic plan was always in place, with appropriate resources allocated.
Innovation
3D-printed concrete: Modern methods of construction and off-site manufacture were implemented where feasible throughout. 3D-printed concrete was used for semi-structural applications including ground bearing access stairs and sheet pile cladding/capping panels.
The scheme has been a 3D-printed concrete pathfinder project, where learning and development for future construction applications of the technology has been captured.
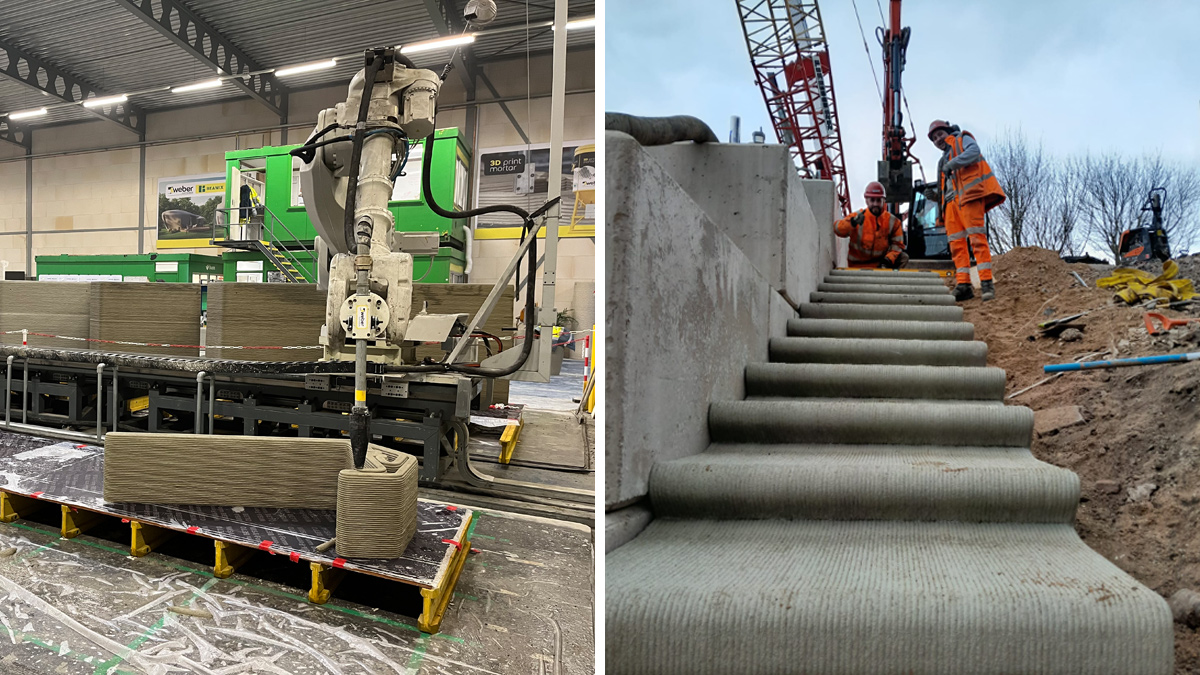
(left) 3D concrete printing and (right) installation of steps – Courtesy of JBA-Bentley
The profile, mix design and finishing of each element was chosen to suit each product location and optimise production. Should additional or duplicate components be required, all printing files and software programming is available. Working with specialist suppliers, the elements were printed and cured in a factory-controlled environment (humidity, temperature etc), and delivered to site ready for immediate installation – saving time, reducing waste, ensuring quality and reducing embodied carbon over baseline solutions.
Augmented reality (AR): AR software is cutting-edge in construction, taking gaming-based software to provide enhanced visualisation of site and otherwise unseen features (i.e. below-ground assets). The site is crossed by numerous below-ground services and the works interact with several existing below-ground structures. Generally, the works were designed and methodologies developed to not affect the existing equipment. However, the location of apparatus and intrusive nature of the works presented potential risk to delivery teams.
AR was trialled and then used to assist with planning site operations and communicating buried service risks to site teams. The software geolocates and then provides an enhanced view of the existing site in photographic quality with below-ground services and new structures overlaid to essentially make the ground transparent on screen. AR minimised risk to delivery personnel and third-party assets, contributing to the excellent safety record.
4D-modelling and programming: The constrained nature of site made detailed and thorough planning of activities and phasing critical. Parts of the works required numerous engineering disciplines to operate in overlapping/interfacing areas.
Early in the project the use of 4D-modelling was identified as essential to ensure safe and efficient delivery.
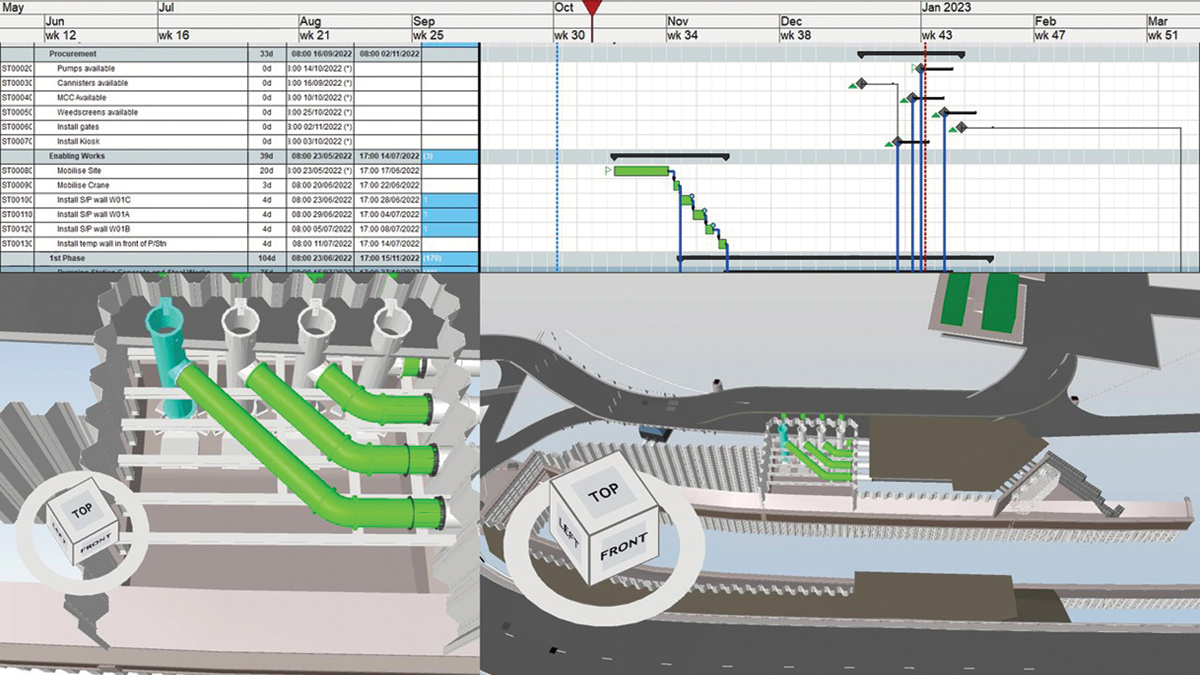
Extract from Synchro 4D planning software – Courtesy of JBA-Bentley
The design and construction team opted for Synchro 4D-planning software, which sees the 3D digital model and works programme integrated into the platform. The software then produces a sequence animation of structures and assets being installed. Including the most significant items of temporary works into the model and software allowed teams to understand potential clashes of working space and access and improve resource planning to maximise efficiency.
Key challenges
Flow presentation: The pumping station will only operate during periods of high flows on the River Derwent (approximately three events per year expected). As the majority of flows under normal rainfall events will pass along the channel, the pumping station is built off the main channel line.
To minimise the overall site footprint, flows will turn into the pumping station and then rising mains turn again to the outlet. Bespoke-formed suction intakes are used to ensure what could be uneven flow presentation to the pumps during high flows will not negatively affect pump capacity or efficiency.
Existing siphon pipes: The site crossed by a deep sewer. Twin-siphon pipes pass under channel coinciding with the new flood walls. The ground conditions, topography and proximity of the highway determined steel sheet-piles as the most effective structure for the new flood walls.
Design details and installation methodology for the sheet-piled walls were agreed with the outside-party engineer from Severn Trent. Details were set in terms of proximity to assets, vibration limits, monitoring and contingency. The pile line steps-up over the siphon pipes at both crossing locations. A waler beam then distributes loads into the adjacent higher capacity piles to support the wall.
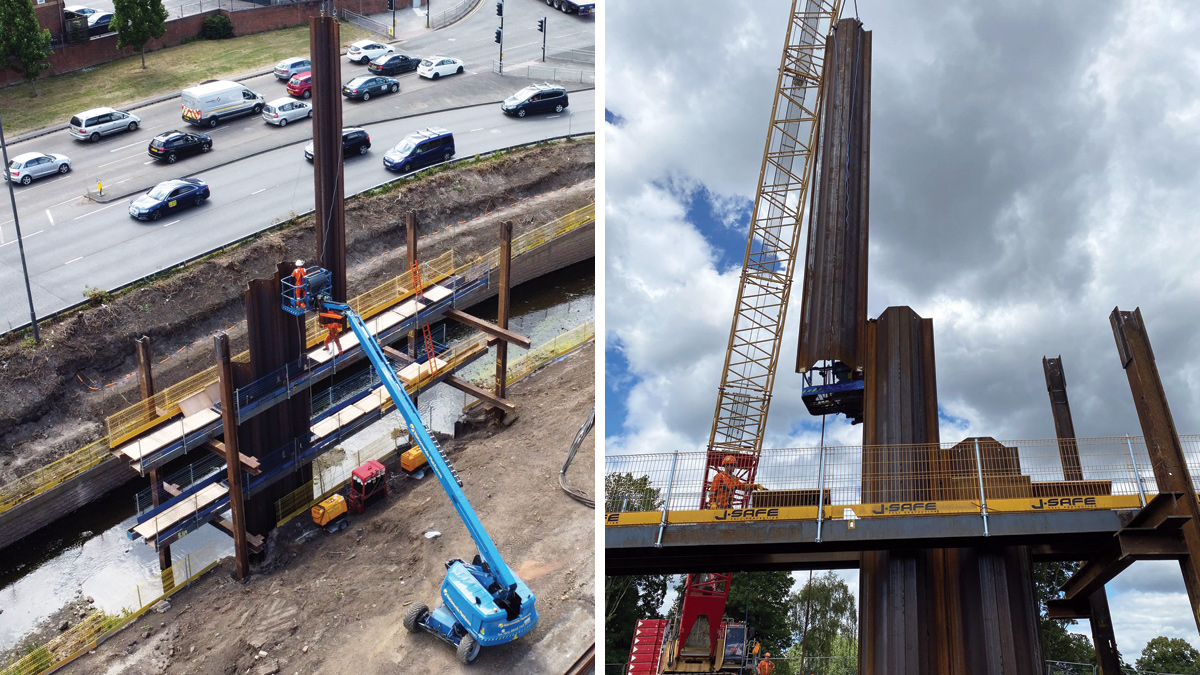
Pile installation methods suit ecology and service locations – Courtesy of JBA-Bentley
Ecology and pile installation: A large colony of Daubenton’s bats is known to live in the upstream culvert, using the downstream watercourse within site for feeding. While the works did not directly affect the colony, all works near the culvert were approved by a licensed bat-worker. The approved methodology included assessment of anticipated noise/vibration limits for pile installation.
Assessment considered proximity to sensitive receptors, ground conditions, equipment used and historic data for similar installations. Generally traditional displacement hammer piling was used; areas closer to the culvert were installed with an excavator-mounted MOVAX attachment. Watching briefs and monitoring confirmed no bat disturbance.
Combining temporary and permanent works: The baseline solution included a full structural concrete wet-well. Typically this would be constructed using a temporary sheet-pile cofferdam and framing arrangement. Use of carbon modelling tools and programme scrutiny identified significant carbon and critical path savings by value engineering this structure.
Working across disciplines (hydraulic, geotechnical, structural) and with the client, the temporary works were incorporated into the permanent structure, with the otherwise temporary steel sheet piles made permanent and vertical structural concrete omitted. Corrosion control, flow presentation to the pumps and long-term geotechnical stability were all analysed and engineered to realise the benefit. Over 17-tonnes of carbon were saved, and four-weeks from the critical path.
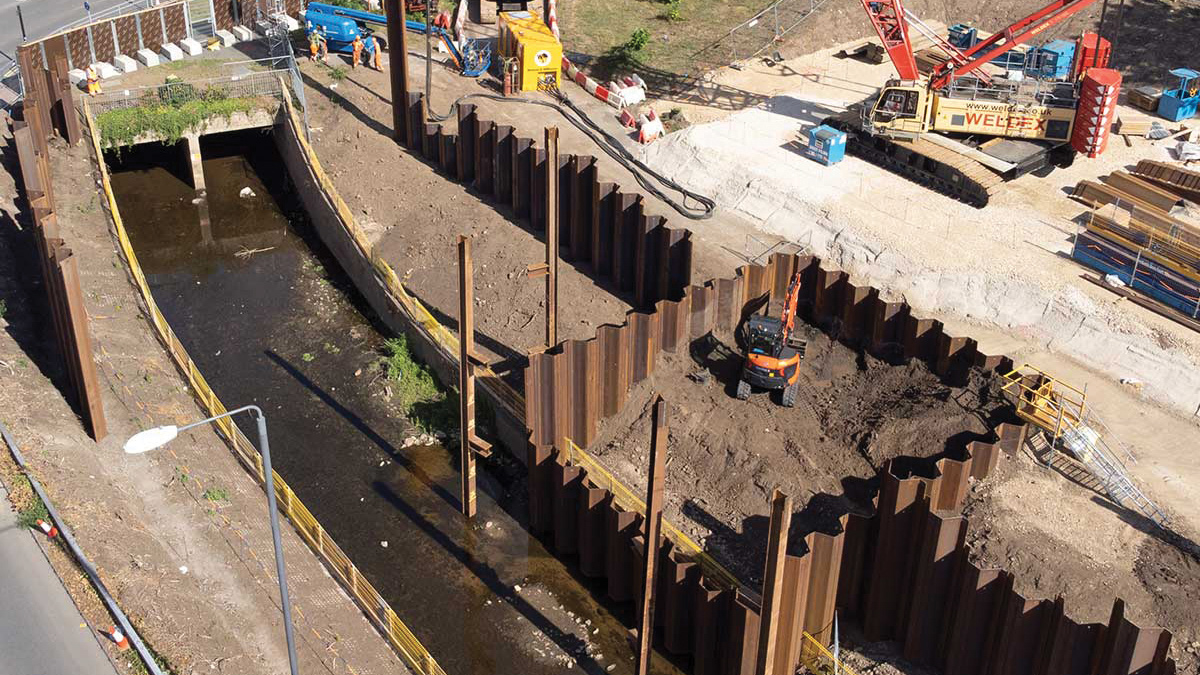
Sheet piling incorporated into the permanent solution – Courtesy of JBA-Bentley
Mill Fleam Pumping Station: Supply chain – key participants
- Designer & delivery contractor: JBA-Bentley JV
- JBA Consulting
- JN Bentley
- Environmental clerk of works: Tetra Tech
- Sheet piling & anchors: Sheet Piling UK
- Concrete installation: Rebar Formworks Solutions
- 3D concrete printing: Weber Beamix
- Mitre gates & actuation system: Hunton Engineering Design
- Weedscreens & non-return valves: Aquatic Control Engineering
- Pumps & canisters: Bedford Pumps
- Control panel & electrical installation: IMAC Ltd
- Containerised generator: A&M Generators
- GRP enclosure: NPS Engineering Group
- Pipework & fittings: Electrosteel Castings (UK) Ltd
- Metalwork: APT Marine Engineering
- Concrete supply: Tarmac
- H&S fall protection: J-Safe Ltd
- Landscaping & fencing: Leveret Contracting
Carbon reduction and environmental management
In operation the pumping station will be the most efficient of its type. High-efficiency pump motors coupled with variable frequency drives and intelligent control will ensure pump operation is optimised for all flow conditions.
Carbon has been monitored and removed at each stage in the asset lifecycle; the table below summarises the most important embodied carbon savings:
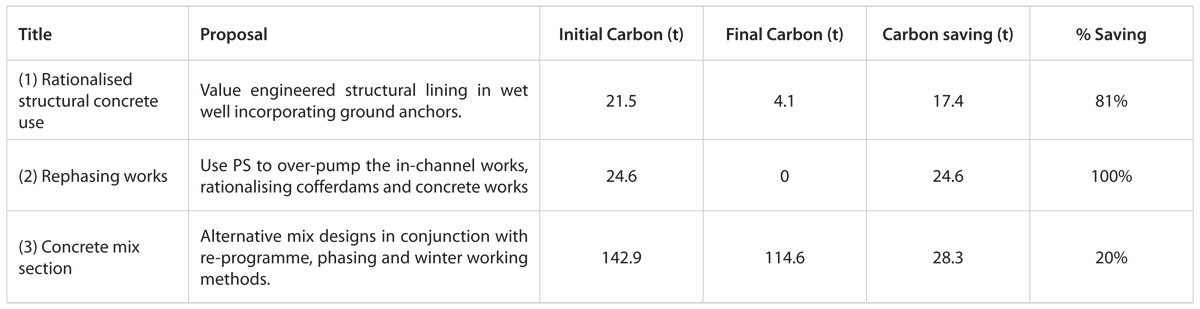
Embodied carbon savings
- As described above, the wet-well structure was reviewed and carbon modelling tools used to remove concrete from structures, and utilised structural steelwork where design life and flow management wouldn’t be adversely affected.
- Scrutiny of programme and early procurement of critical MEICA equipment allowed the phasing of works to be revised, and pumping station commissioned early. Bypassing flows using the pumping station then enabled reduction of the cofferdam arrangement and associated invert slabs.
- Winter working was inevitable; JBA-Bentley worked with specialist suppliers to review and challenge mix designs. A higher proportion of cement replacers were used than standard specified winter mixes in conjunction with site controls to ensure quality nor programme was affected. Concrete installation continued through winter with minimal cost increase while significantly reducing embodied carbon over baseline.
There were a number of environmental enhancements including re-landscaping the surrounding parkland and a fish refuge to provide shelter for aquatic life in low and high-flows; enhancing habitats of the reach. Existing trees, vegetation and access pathways were replaced or improved. Over 75 new trees will be established, with bird and bat habitats improved. During the in-channel construction works, a ‘bubble curtain’ mitigated silt disturbance and managed fish passage. All site plant and equipment utilised hydrogenated vegetable oil (HVO) in place of traditional gas oil. Whilst more expensive, HVO significantly reduces CO2 emissions.
Planning and communication
The design, construction and commissioning Mill Fleam Pumping Station required a wide range of engineering expertise including geotechnical, civil, structural, hydraulic, mechanical, and electrical. Addition specialist consultant advice was required around planning permissions, ecology, fire risk, and landscaping. Effective coordination across these teams and disciplines was crucial to successful project delivery.
The restrictive 15-month design and delivery programme required activities to be delivered simultaneously. Weekly collaborative workshops were held throughout the planning, design and continued into the delivery phases to ensure engineering disciplines effectively communicated design intent and interfaces were fully managed.
Extensive and detailed live 3D digital modelling of the scheme enabled the coordination and clash detection between internal and external teams, always ensured a single point of reference and the latest information available to all. Early in the project common platforms/ software or compatible products were tested to ensure effective integration of modelling from all disciplines.
Mill Fleam Pumping Station – Design, construction & innovation
Introductory video to Mill Fleam Pumping Station – Courtesy of JBA-Bentley
Safety management
The project has an excellent safety record, borne out of great engagement from the team. All interventions (preventative, corrective or otherwise) are recorded to monitor for trends. At Mill Fleam Pumping Station, the positive intervention reporting rate was 3,447 per 100,000 hours worked, far in-excess of the minimum expected and organisational average across directly-employed and sub-contractor personnel. This demonstrates an excellent safety culture (company expectation is 1,550 per 100,000 hours).
As well as great engagement, key to safety is planning. The use of off-site manufacture and digital tools reduced site hazards and enabled delivery teams to manage and then communicate risks. The 3D-model provided not only a digital twin of the permanent works but included main items of temporary works and plant. This allowed teams to plan positions of equipment, temporary phasing of installations and access routes/systems. Visualisation of methods and equipment in this way ensured the correct deployment of resource and equipment to deliver the works safely.
Summary
The contract was awarded to JBA-Bentley in November 2021; with design, planning submissions and procurement undertaken in early 2022. Site enabling works were undertaken in February 2022, and the main site works commenced in May. The main station works were completed and the pumps initially commissioned in December 2022. Site works were finalised in April 2023.
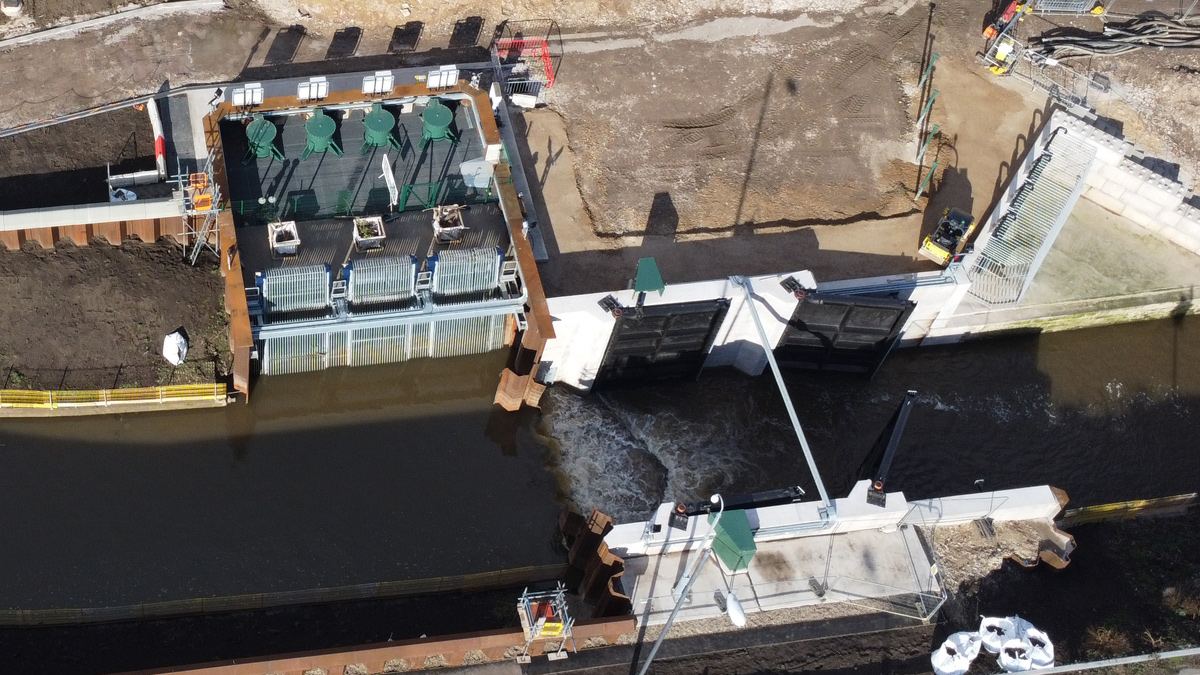
Mill Fleam Pumping Station (March 23) - Courtesy of JBA-Bentley