Ardsbeg WTW (2020)
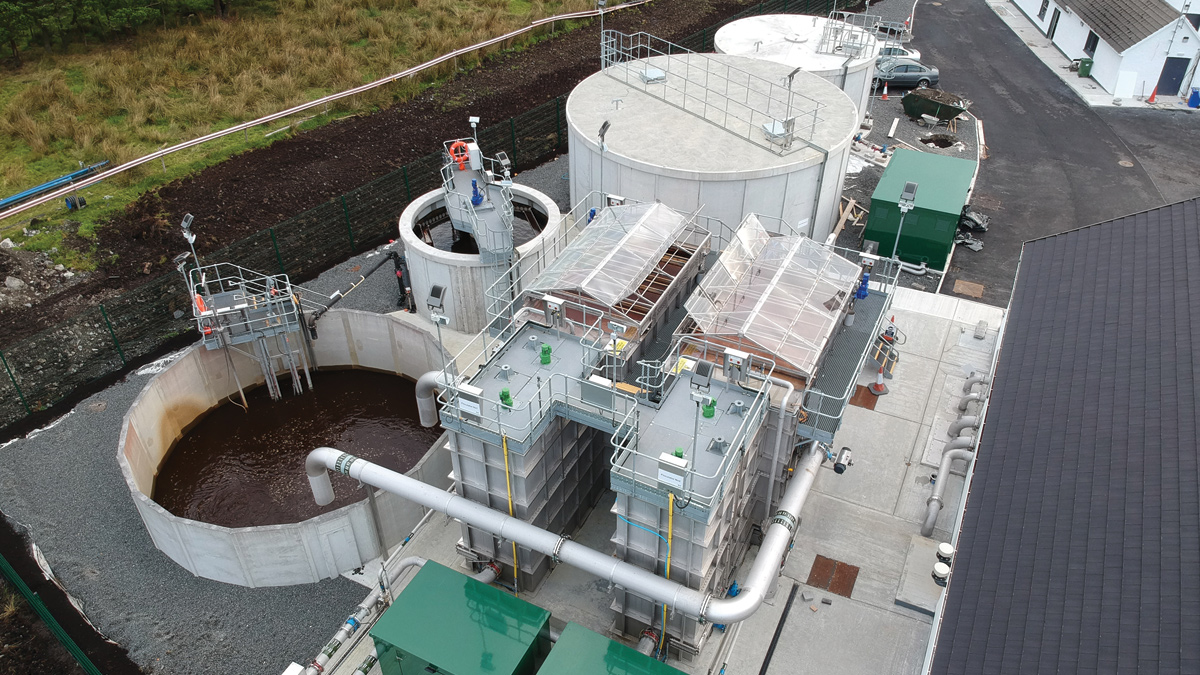
View of the completed Ardsbeg WTW upgrade - Courtesy of EPS Group
Ardsbeg Water Treatment Works (WTW) is located in a remote area in the north of Co. Donegal in Ireland and treats water from a lake source to serve local villages of Gortahork and Falcarragh as well as rural farms and dwellings. The WTW was originally built in the 1960s and was modified in 2003. However, due to operational challenges, compliance concerns and to secure long-term resilience, Irish Water elected to procure a major upgrade to serve the current and future needs of the plant and the customers it serves under a Design-Build-Operate (DBO) contract. The plant upgrade was to be constructed within the footprint of lands on and adjacent to the existing Ardsbeg WTW site with a production capacity of 1,800m3/day. The challenges presented by the site led to the use of digital design and off-site construction techniques to manage risk and achieve the required project outcomes.
Project need and undertakings
The objective of the project was to fully replace the existing process with a modern automated plant, providing futureproof capacity and giving a robust source of supply. The existing plant had to continue in full service – including operation by the DBO contractor – while construction and commissioning of the upgrade took place. Following a comprehensive procurement process, EPS Group was selected by Irish Water to deliver the Ardsbeg upgrade. EPS led the project as main contractor, with support from a range of subcontractors and suppliers including P.J. Tobin Consulting Engineers as civil designer and Ward & Burke as civil subcontractor.
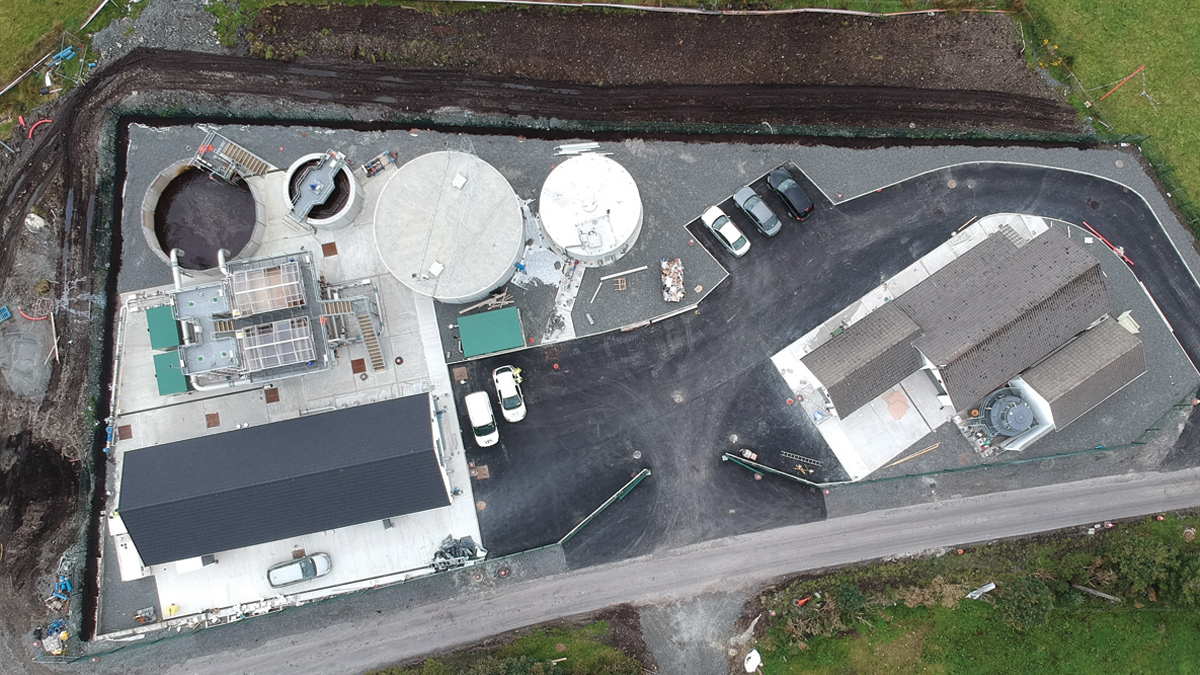
Aerial view illustrates the confined nature of the available construction site – Courtesy of EPS Group
Key project constraints
The design envelope and site conditions presented several significant challenges to the EPS project team:
- Process: Raw water at Ardsbeg WTW is abstracted from the nearby Lough Lagha, the catchment for which is primarily made up of elevated moorland and unforested blanket bog. This presented the process design team with specific challenges around the removal of colour, turbidity, pH and organic compounds.
- Footprint: The Ardsbeg site was extremely constrained, especially as the existing treatment assets had to be kept in operation throughout the construction and commissioning phases. Not only did this impact on the available footprint of new assets but it also severely limited the remaining space for the construction compound and material storage and lay-down areas.
- Location: The site is located on a narrow rural road in a remote and exposed area of north-western County Donegal, over 100 miles from the nearest motorway and almost one hour from the nearest large town; Letterkenny. This increased project risk in terms of access to consumables/materials, availability of local skilled labour, weather impacts and the potential cost of re-work.
- Programme: The programme was constrained from the outset and would have proved challenging in any location using traditional sequential construction methods.
Together, these factors led EPS to consider and ultimately adopt an alternative approach to the design and delivery of the project in order to mitigate the identified risks and help assure delivery on time and within budget.
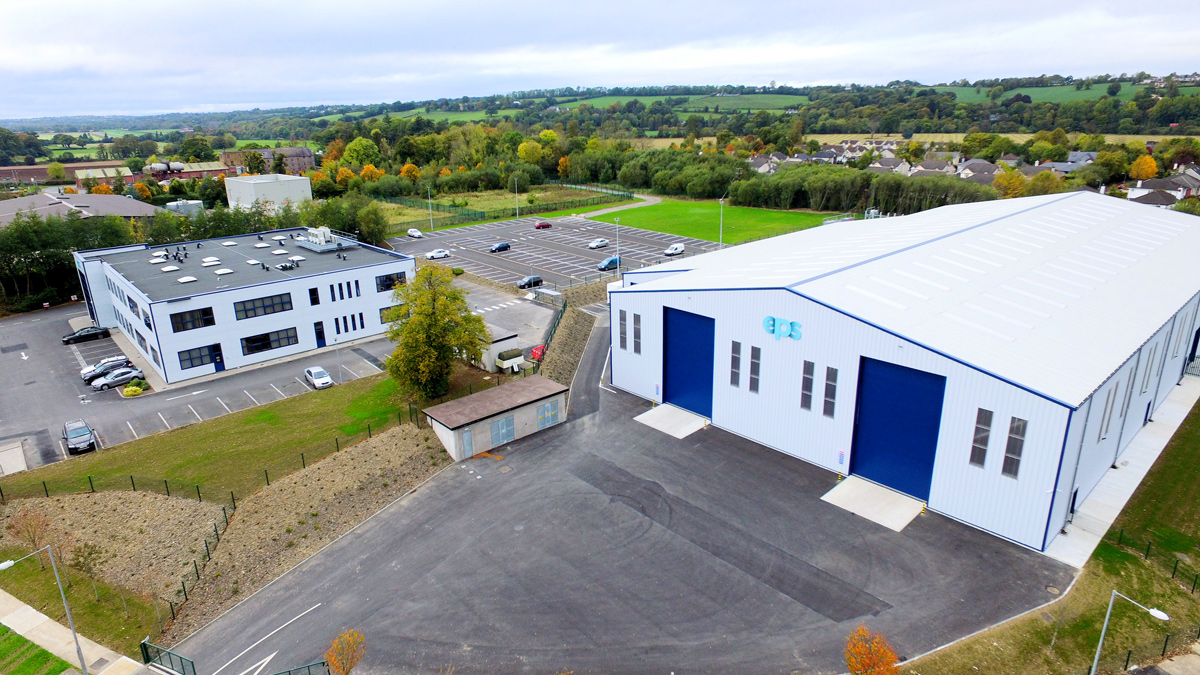
EPS Design & Manufacturing Centre of Excellence – Courtesy of EPS Group
Process selection
Following an extensive programme of raw water characterisation and jar testing, it was determined that the required quality of produced drinking water could be achieved using a three-stage process as follows:
- Dosing of a coagulant, flocculant and pH corrector with contact and mixing with a flocculation tank.
- Combined dissolved air flotation and filtration (DAFF) stage, with DAFF media comprising of a 400mm bed of anthracite and 700m of silica sand sitting over a plenum floor system.
- Two stage UV and liquid chemical disinfection, along with pH correction and plumbsolvency dosing and residence in a contract tank, prior to pumping to the main network reservoirs.
The proposal to use the EPS DAFF technology over the more traditional two-stage DAF and RGF combination was driven by the desire to minimise footprint uptake. The EPS DAFF system has been applied on numerous projects over the past 10 years, delivering effective, efficient and economic capital and OPEX benefits. A decision to apply DAFF Technology was agreed when it was accepted that the benefits could be realised without compromising on the quality of water produced at the plant.
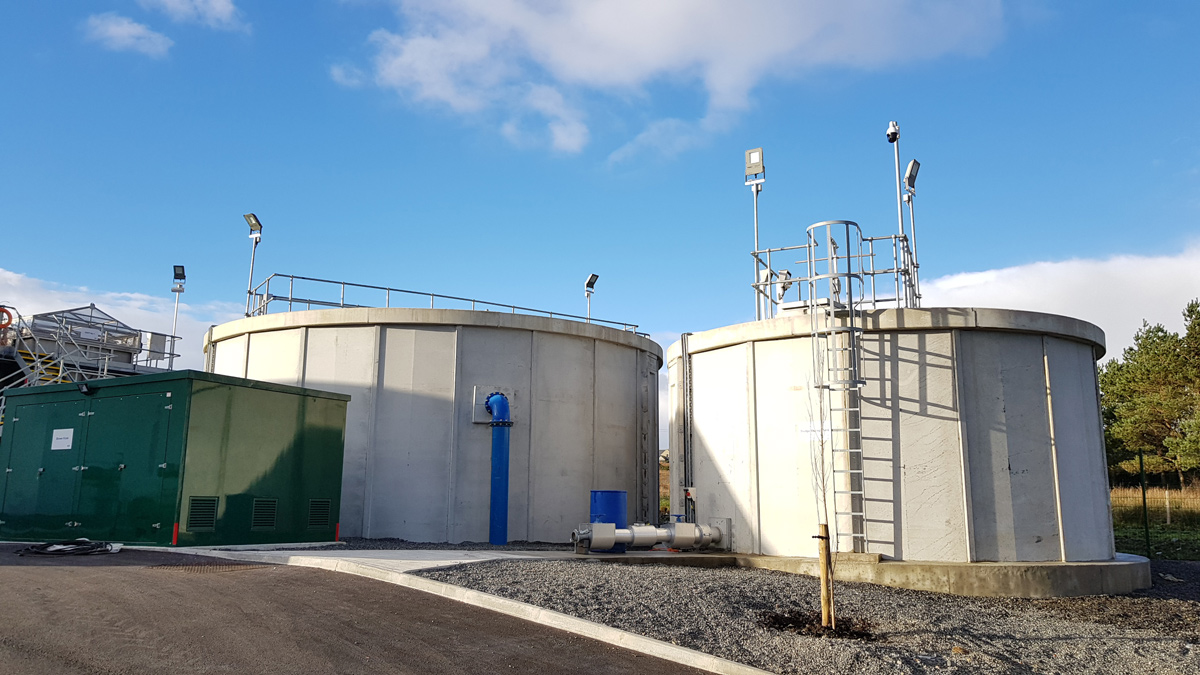
Appropriate use of precast concrete tanks was integral to the off-site delivery strategy – Courtesy of EPS Group
Delivery strategy
An early recognition that even ‘Gold Standard’ level of traditional construction execution and sequencing was unlikely to achieve all the desired client outcomes led EPS to shift to a digital design and off-site construction approach to the Ardsbeg project. EPS engaged with Irish Water and other key stakeholders, with all parties recognising the risks logistical difficulties from the outset. An alternative strategy for the delivery of the project was therefore drawn up and agreed.
Through the use of DfMA (Design for Manufacture & Assembly) techniques, EPS were able to carry out the design, fabricate, pre-assemble and pre-commission the majority of MEICA element off-site, simultaneously with the groundworks and civil construction being completed on site. This freed up valuable ground space at Ardsbeg WTW, which would otherwise have been needed for laydown and storage. It also shortened the delivery programme by creating a far greater overlap between civil and MEICA works; by minimising disruption from multiple disciplines working on site at one time; and by shortening the on-site commissioning period.
The civil works were shortened by making the maximum use of precast tanks and other elements, which again could be produced off-site while groundworks progressed. Post-tensioned systems were selected as these required the least time and resource from erection on site to completion and testing.
The majority of MEICA works were carried out at EPS’s Centre of Excellence for Design & Manufacture, located at its headquarters in Mallow, Co. Cork, 450km from the site. This independent working arrangement was facilitated by Irish Water, who simultaneously monitored progress and inspected activities at both locations.
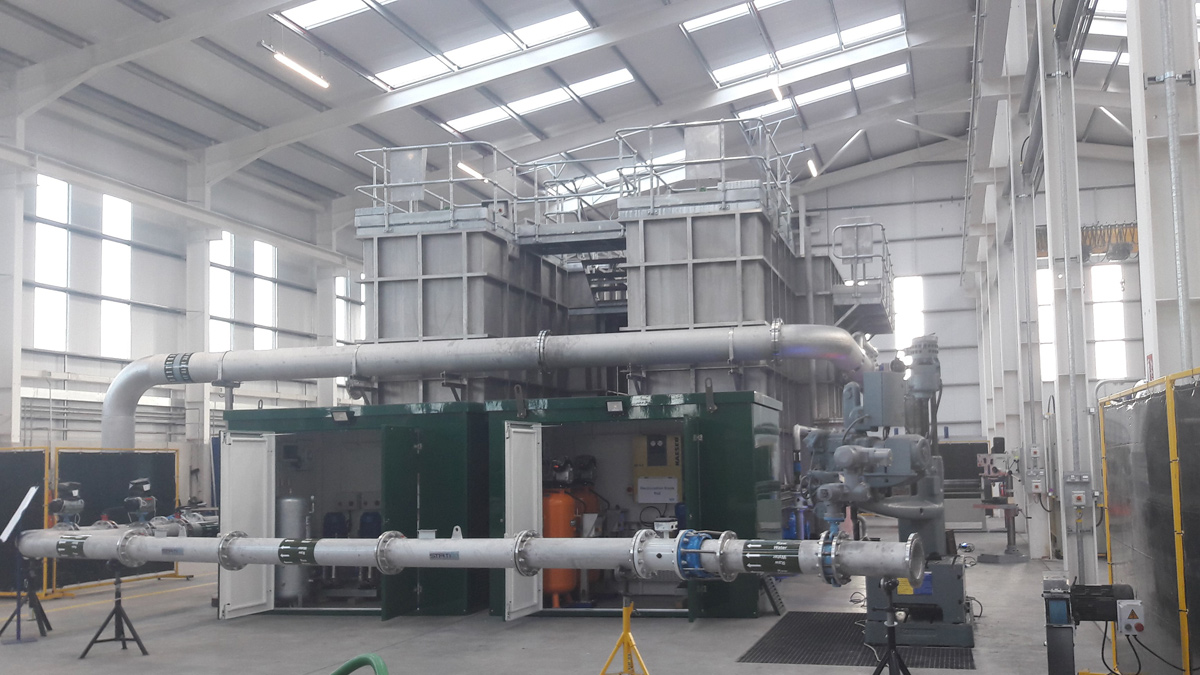
View of the main flocculation tank and DAFF block in the EPS factory – Courtesy of EPS Group
Project execution
EPS worked in collaboration with the Donegal CC operations team based on the site for the duration of the build. EPS took responsibility for operating the plant, allowing Council representatives to monitor discharge and service provision while also seeing at first hand the building and commissioning of the new plant. Irish Water oversaw the design and construction phases, including the provision of community liaison services, with consultation and notification of local residents at every stage and in advance of any activities that may have potentially impacted on them.
Civil works were completed on-site at Ardsbeg concurrently with the fabrication and assembly of the MEICA modules at the EPS Centre of Excellence:
- The flocculation and DAFF tanks were fabricated and fully assembled in the EPS factory, with all connected parts (pipework, pumps, electrical, controls, Robuschi air blowers) assembled and tested. Pattern tests on the filter floors were witnessed by Irish Water and signed off prior to them being transported to Ardsbeg.
- The DAF recycle/whitewater system and the blowers and associated equipment were both completely assembled and fitted out within kiosks at EPS. Each underwent preliminary testing before being packaged and shipped to site where they were unloaded into position and final connections made.
- Areas replicating the future site buildings were created within the EPS facility. All pumps and ancillaries were skid mounted, piped, wired and tested before being assembled into a ‘virtual pump room’ complete with surge vessel etc. Similarly, the chemical dosing skids were manufactured, assembled and laid out into a ‘virtual chemical house’. Both areas were subject to client inspection and pre-commissioning tests, before being partially dis-assembled and transported to site for final installation.
A crucial factor in the successful transfer of assets to the worksite was a comprehensive transportation analysis. This highlighted height, width, weight and turning restrictions for delivery and determined the maximum delivery vehicle size and maximum module dimensions that could be shipped from the factory to site. This information was used in the process design stage including the relevant sizing of the main DAFF tanks. The delivered modular assets were off-loaded, positioned and installed on site at Ardsbeg WTW within a period of only eight days. Four months later, the remaining mechanical, electrical, ICA and landscaping works were substantially complete and the plant was ready for dry and wet PLC testing and full process commissioning.
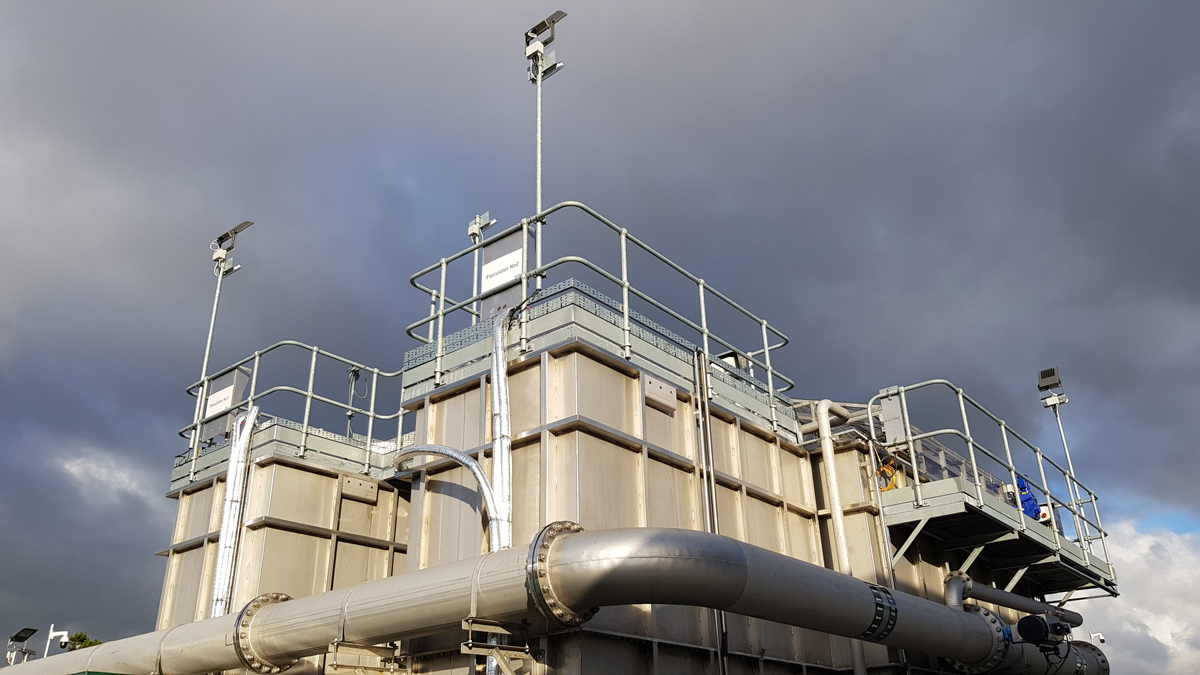
View of the completed flocculation tank and DAFF block on site at Ardsbeg WTW – Courtesy of EPS Group
Ardsbeg WTW: Supply chain – key participants
- Employer: Irish Water
- Employer’s representative: AECOM
- Local authority operator: Donegal County Council
- Main contractor, MEICA design & MEICA manufacture & installation: EPS Group
- Civil & structural designer: PJ Tobin Consulting Engineers
- Civil sub-contractor: Ward & Burke
- Electrical sub-contractor: M&E Services
- Precast concrete tank supplier: Shay Murtagh Precast
- RGF filter floor equipment: Cadar Ltd
- DAF saturators: Alpha Tanks
- Air blowers: Robuschi (a Gardner Denver brand)
- Pumps: DPS Ltd
- Sludge transfer progressive cavity pumps (Ardsbeg): SEEPEX UK Ltd
- Pumps: Zenit Pumps
- Ultraviolet disinfection: Trojan UV
- Motor control centre: Enisca Ltd
- Kiosks: Quinshield
- Chemical storage tanks: SILOTANK
- Chemical dosing pumps: Prominent Fluid Controls
- Polymer make-up unit: Celtic Watercare
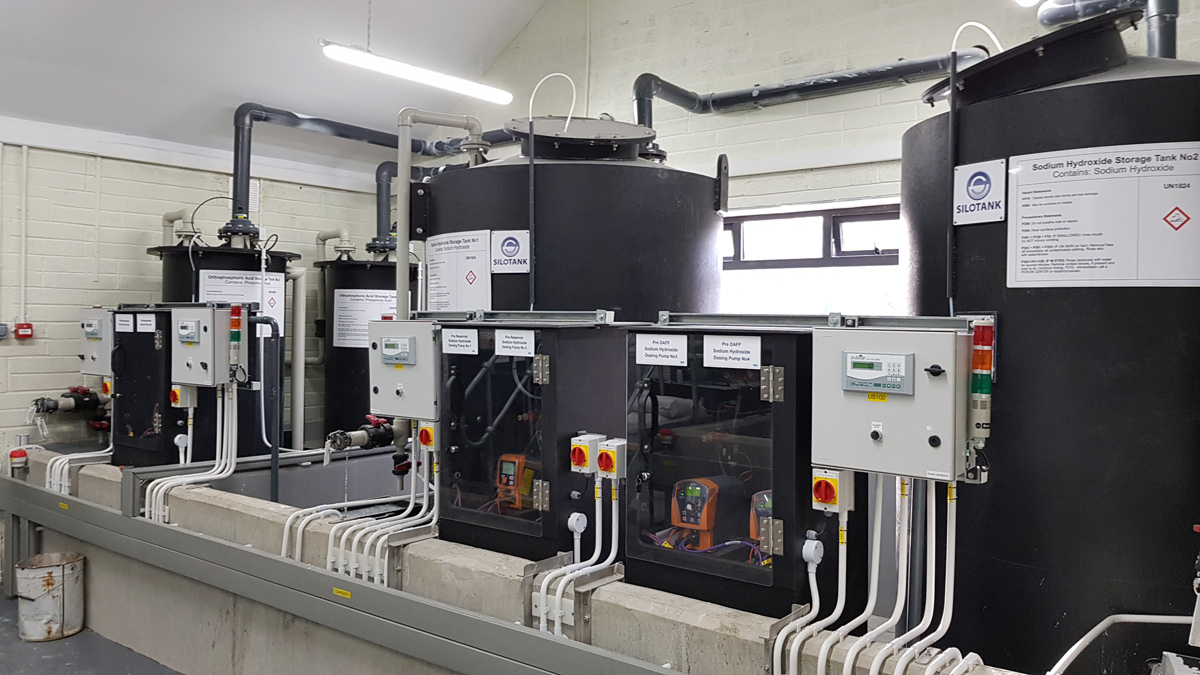
Part-view of the completed chemical house at Ardbeg WTW. All dosing systems were skid-mounted and had been laid out as a ‘virtual chemical house’ in the EPS factory – Courtesy of EPS Group
Successes and benefits
With the support of Irish Water and its subcontractors, EPS successfully delivered a WTW capable of producing up to 1,800m3 of compliant drinking water each day, using off-site construction methods. In terms of the percentage of overall scope, this has been one of the most ambitious and comprehensive off-site construction projects to have taken place in the UK and Irish water sector to date. The full scope of mechanical and electrical equipment was delivered, offloaded and installed on a remote and logistically challenging site over a period of eight days using just six operatives and a crane crew. Conventional building techniques would have required an uninterrupted period of at least 14 weeks with a far larger installation team used. This approach yielded an overall reduction in site labour of 72%.
The project could never have efficiently accommodated uninterrupted access for civil construction and mechanical installation due to the tight confines of the site, the lack of adequate material lay-down areas and the need to maintain full and uninterrupted water supply to customers. As such, the use of off-site construction unlocked and de-risked the execution of the project. There were zero accidents or injuries on site during the installation. This was largely due to the designing out of nearly all working at height, the use of smaller installation crews on site and the site operatives involved having already carried out the assembly and disassembly work in the factory, thus giving them familiarity with all the processes involved. The number of crane lifts required was more than halved.
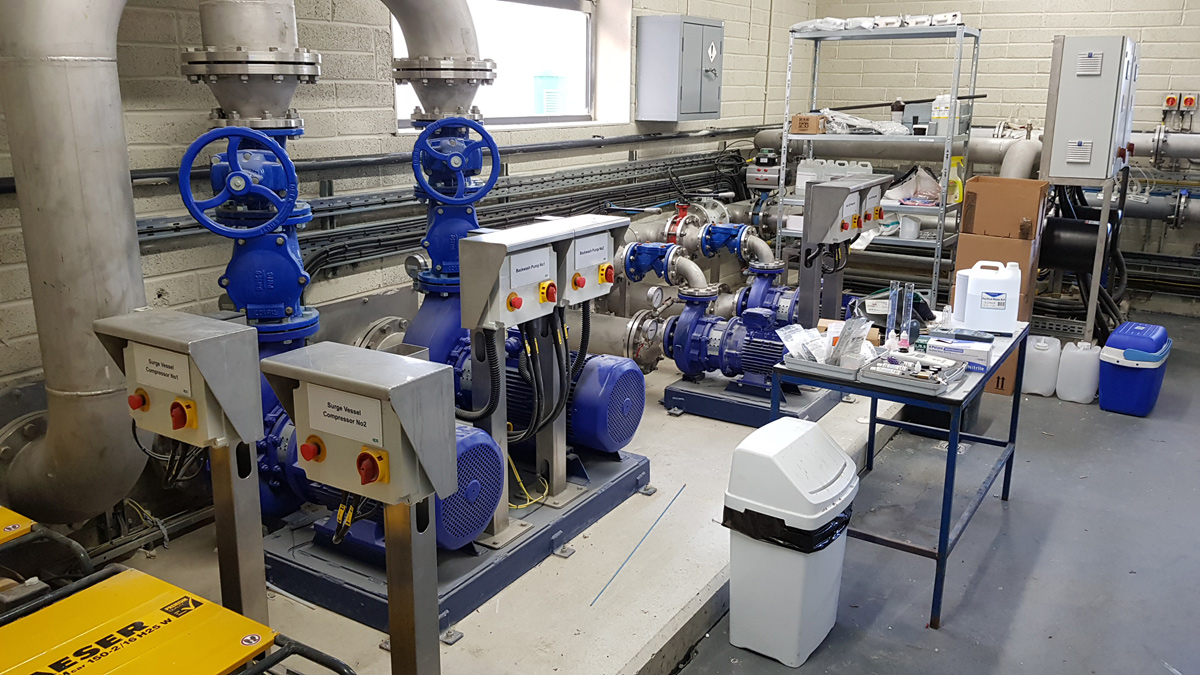
Part-view of the completed pump room at Ardsbeg WTW. All pump sets were skid-mounted and had been laid out as a ‘virtual pump room’ in the EPS factory – Courtesy of EPS Group
Stakeholder engagement was enhanced significantly through the use of digital tools in the design phase, and the ability for the client and operators to inspect and critique all of the MEICA equipment and layouts of the new treatment facility in a factory environment in advance of the permanent installation. This aligned expectations, avoided unexpected surprises and minimised re-work following delivery to site.
Carbon reduction performance was substantially enhanced through reduced logistics transportation, fewer worker journeys to site and a reduction in waste through digital planning and lean production methods. And disruption to local customers and communities was minimised by maintaining water production, reducing traffic movements and reducing noise-producing site activities (e.g. cutting, grinding, etc.).
The success of the project was highly dependent on the cooperation of Irish Water and Donegal County Council. Speaking about the project, David McLoone from Irish Water said:
“We are delighted to have completed these works and look forward to celebrating with the local community at the official opening of the plant. This project will ensure a safer, more secure and improved drinking water supply for our customers in that area.”
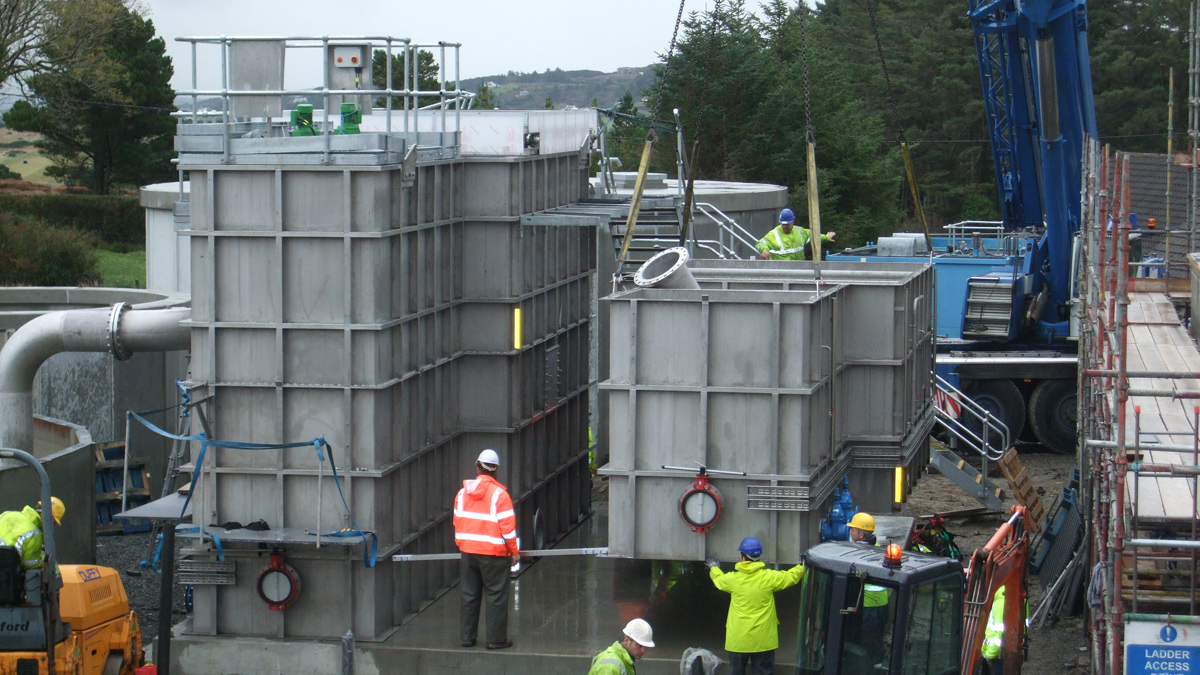
Module crane lift at Ardsbeg – Courtesy of EPS Group
The Ardsbeg project was shortlisted for the WWT Water Industry Awards 2020 in two categories; ‘DfMA Project of the Year’ and ‘Water Innovation Project of the Year’.