Arklow Long Sea Outfall (2023)
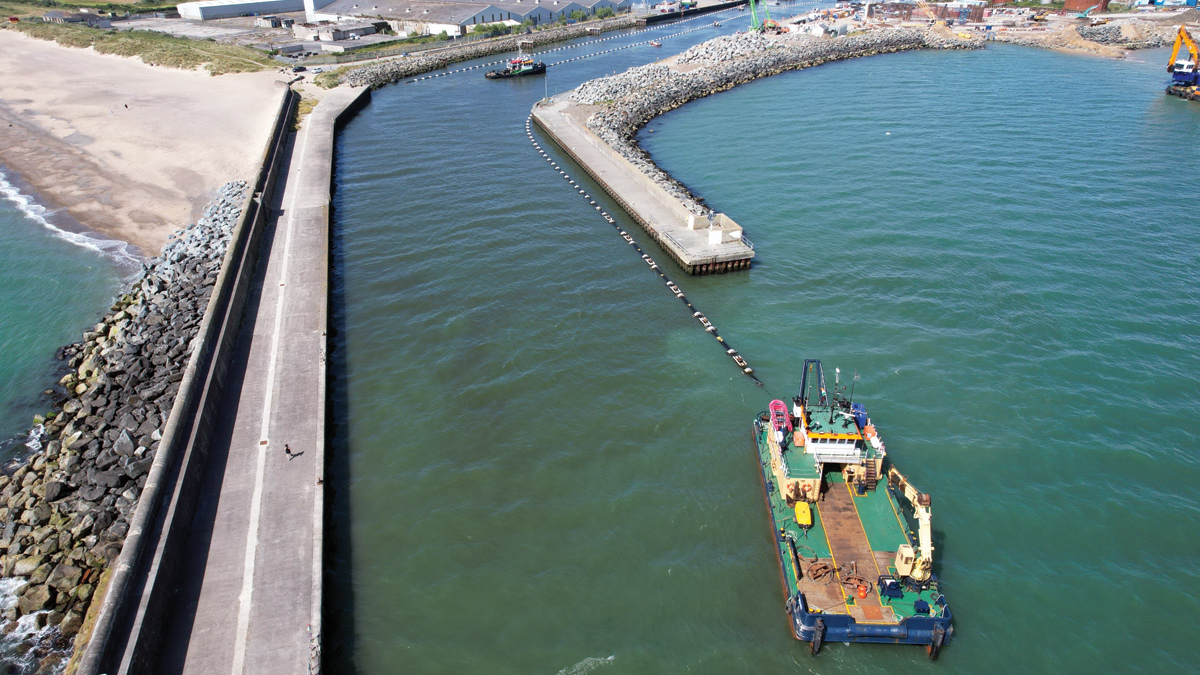
Final outfall pipe sections being manoeuvred out of the port - Courtesy of Van Oord Ireland Ltd
September 2022 saw the successful completion of a new kilometre outfall pipeline in Arklow, Ireland. The lack of wastewater treatment facilities in Arklow resulted in untreated wastewater being discharged directly to the Avoca River. The design and construction of a new wastewater treatment plant and long sea outfall was required to improve the water quality of the Avoca River and bring benefits in terms of health, environmental integrity and facilitate economic and social development for Arklow town and its surrounds, which has been constrained by the lack of adequate wastewater treatment capacity. This paper focuses solely on the marine design/construction elements of the project as construction of the new treatment works and other associated structures are still ongoing.
Background
Arklow is a town in County Wicklow on the southeast coast of Ireland. There were no wastewater treatment facilities in Arklow town and as a result, untreated wastewater was being discharged directly into the Avoca River. This was not compliant with obligations under the European Union Urban Wastewater Treatment Directive.
Uisce Éireann, therefore proposed a development to provide an effective wastewater collection network, treatment capacity and treated effluent outfall that would improve water quality in the Avoca River.
Ward & Burke was appointed as the main contractor for delivering the Arklow Wastewater Treatment Plant (WwTP) project, with the design and construction of the associated long sea outfall sub-contracted to Van Oord Ireland Ltd. Royal HaskoningDHV was appointed by Van Oord as designer for the long sea outfall (LSO).
The overall project required the design, construct and implementation of the following:
- A new, state of the art, wastewater treatment plant that has been designed to provide an ultimate treatment capacity for a population equivalent of up to 36,000 at the Old Wallboard Factory, North Quay, Ferrybank.
- Sewer pipelines (along the North and South Quays) to bring the untreated wastewater to the WwTP.
- A marine outfall pipeline to safely discharge the treated wastewater to the Irish Sea.
- Upgrade of the existing rock armour revetment adjoining the site.
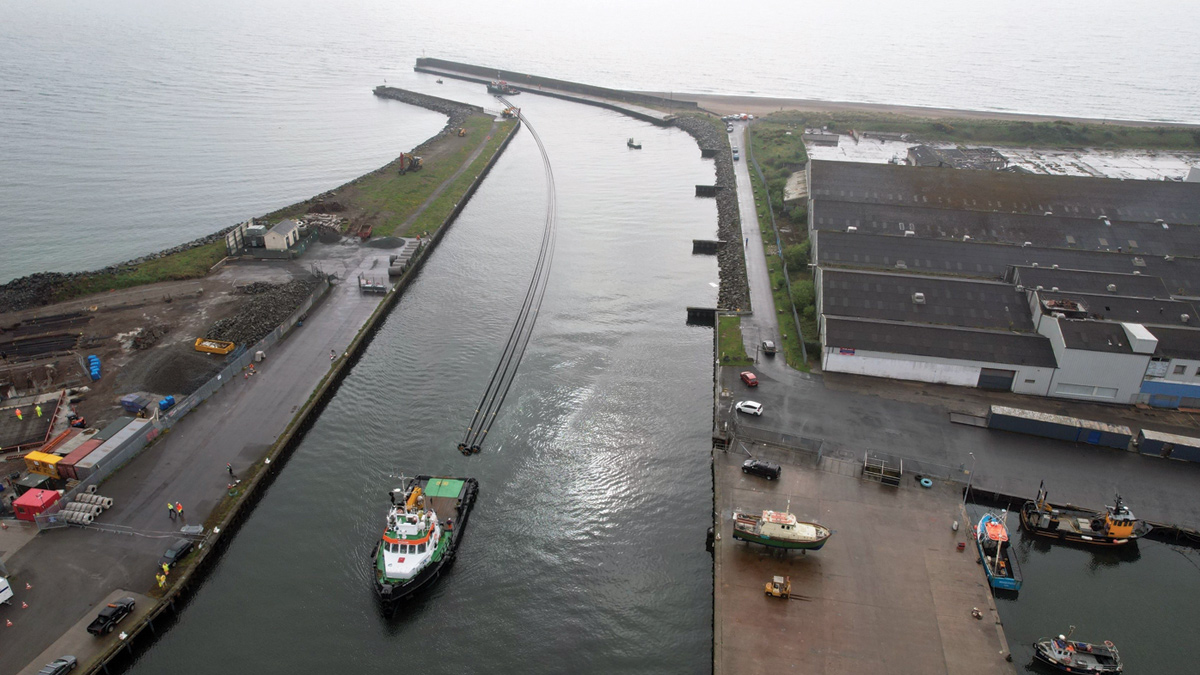
Outfall pipe arrival from Norway by sea to the dock in Arklow for preparation and assembly – Courtesy of Van Oord Ireland
The proposed outfall pipeline was required to discharge the treated effluent from the wastewater treatment plant to receiving waters. Both marine and river outfall options were initially considered for the proposed development.
However, hydrodynamic and water quality modelling demonstrated that the wastewater discharge standards required for a river outfall would be much more onerous than that of a marine outfall. For that reason, the river outfall was not considered further.
Solution
The detailed design of the new outfall system for the Arklow Wastewater Treatment Plant Project considered and finalised the new outfall pipe route, hydraulic design, preferred material and construction methodology, pipe weighting, backfill and diffuser arrangement. The outfall system comprised of a 630mm outer diameter pipeline (630mm OD SDR 17 PE100 pipe) and started at a connection point onshore, behind the revetment and extended offshore for approximately CH927m to the discharge location.
The outfall discharge arrangement/diffuser configuration was located in approximately 13m of water depth from the Extreme Water Level (EWL) and consists of six risers (355mm O.D. SDR 17 PE100 pipe), four diffuser ports (160mm O.D. SDR 17 PE100 pipe) each with 24 return duckbill valves that horizontally discharge the treated effluent at a height of approximately 1m above the seabed level.
The detailed design trench detail was developed to provide a minimum cover depth to the outfall pipeline of 1.5m following installation. This cover depth allowed for both seasonal and long-term fluctuations on the seabed levels and protection from potential damage due to dragging anchors. The trench was backfilled with selected as dug material, typically medium dense sands and gravels, that were side-cast during the trench excavation. Where the outfall crossed beneath the existing and proposed coastal revetment, the pipe wall structural thickness was checked and verified to prevent any high point loads from the revetment rock armour.
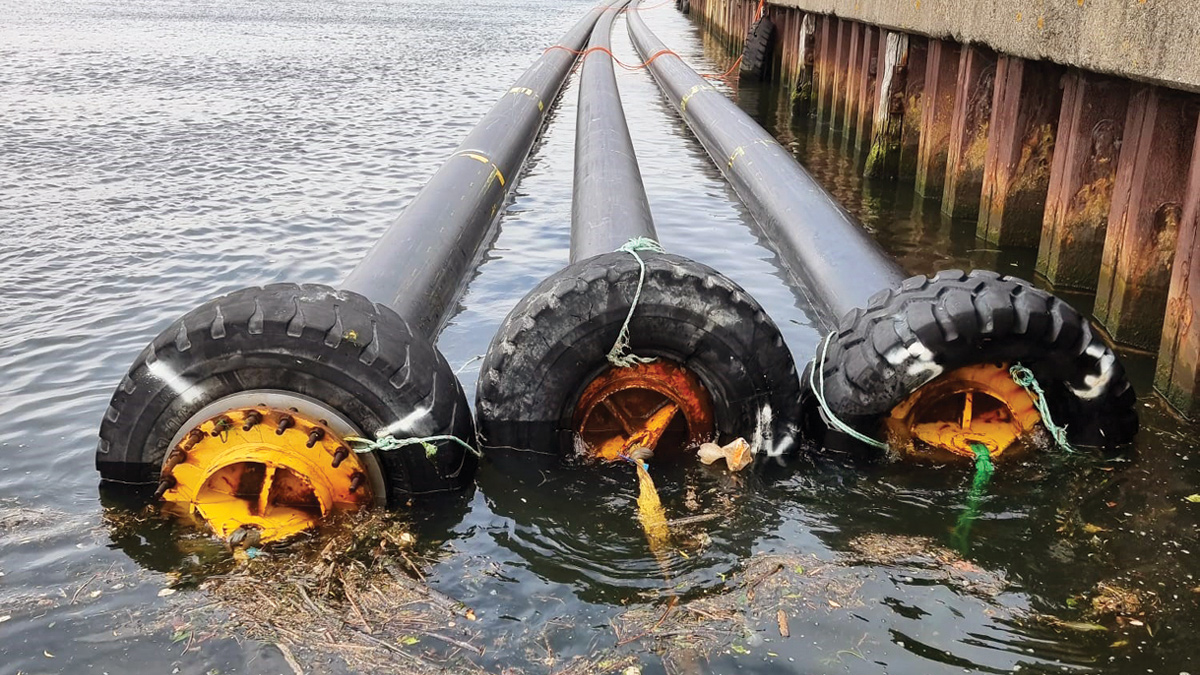
Outfall pipe floated along the quay wall in Arklow prior to preparation and assembly works – Courtesy of Pipelife Norge AS
The marine outfall was also designed to be stable in the ‘worst case’ design loads for current and wave loading conditions provided. It was therefore necessary to weight the pipeline with concrete collars and subsequently concrete kennels after installation (float and flood method), to provide a specific gravity of not less than 1.35 that could be achieved without any reliance on backfill material.
This installation weight was provided with 1015kg (290kg/m) (in air) fixed weight concrete collars at 3.5m centres and to satisfy the permanent on bottom stability, 2292kg (654.86kg/m) (in air) concrete kennels were provided at 3.5m centres in between the fixed weight concrete collars. The collars and kennels were provided by Tracey Concrete.
Constraints
Arklow is a town with a population of 14,000 people and a small port which generates medium to high traffic within the port. This constituted working and delivery restrictions during the preparations of the offshore section of the outfall pipeline. In addition, the turbulent weather did not allow for preparing the outfall pipeline offshore, outside of the port vicinity.
Additionally, a survey undertaken by Uisce Éireann showed an existing subsea cable in close proximity to the designed LSO route. The cable supplied power to a substation located South of the site location from the offshore Arklow Bank Wind Farm. The survey undertaken by Uisce Éireann confirmed the location of the power cable and showed that the cable route was outside the redline boundary for the works. However, the owner/operator of the subsea power cable was consulted to ensure that the new LSO route and location was compliant with the applicable exclusion zones/constraints for the subsea power cable.
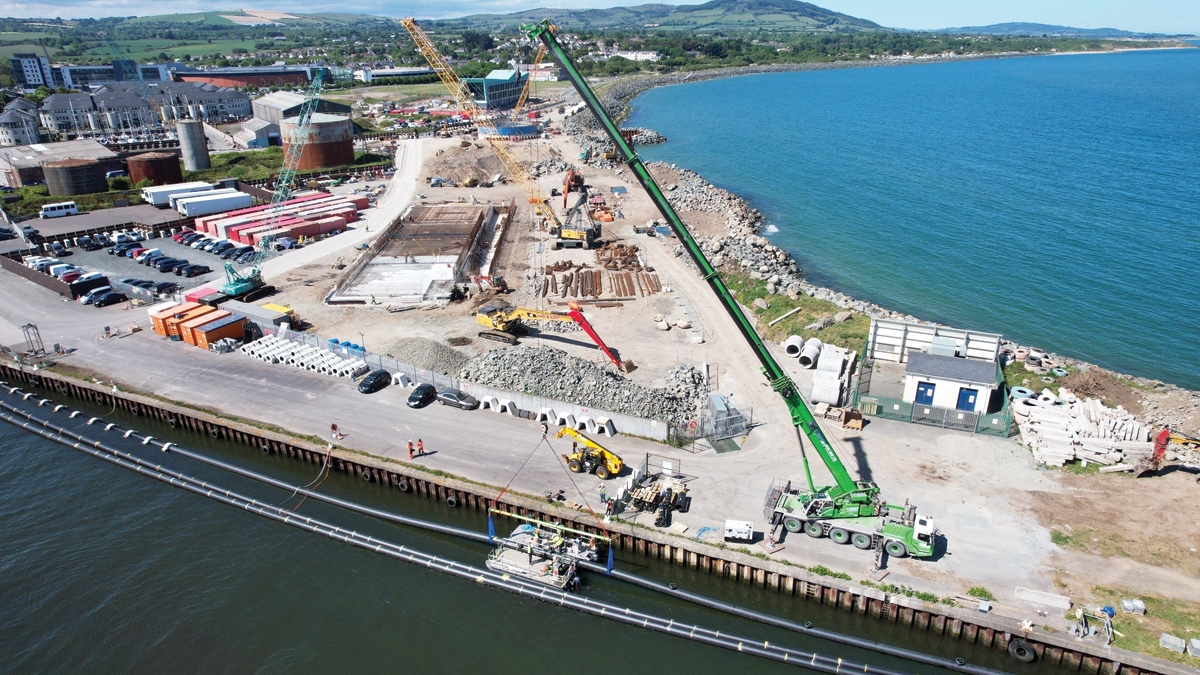
Welding of risers for diffuser section of outfall pipe – Courtesy of Van Oord Ireland
Site investigation
Site information was provided by Uisce Éireann from a ground investigation undertaken in 2017 at the proposed site location, as well as information from the Geological Survey Ireland (GSI) website borehole archive that included relevant land-based and overwater boreholes. The ground investigation indicated that the ground conditions generally comprised of a variable sequence of medium dense to coarse soils and gravel.
The offshore investigation data indicated that there is a significant variation in the ground conditions between the boreholes which were spaced at approximately 150m intervals e.g., buried valleys, rock outcrops etc. Large boulders of metamorphic rock were also encountered in the boreholes. Whilst the depth of the boulders generally exceeded 3m below bed level, the presence of boulders at shallower depths could not be discounted and posed a risk for the construction of the outfall.
The requirement for further site investigations were identified and these included magnetometry, sub-bottom profiling and unexploded ordinance (UXO) surveys to determine the mitigation measures required to be undertaken prior to the proposed works and construction of the pipeline.
Arklow LSO : Supply chain – key participants
- Arklow WwT Project delivery contractor: Ward & Burke
- Long sea outfall design/build: Van Oord Ireland Ltd
- Van Oord designer: Royal HaskoningDHV
- HDPE pipe: Pipelife Norge AS
- Concrete collars & kennels: Tracey Concrete
- Tideflex S35 valves: MeasurIT Technologies
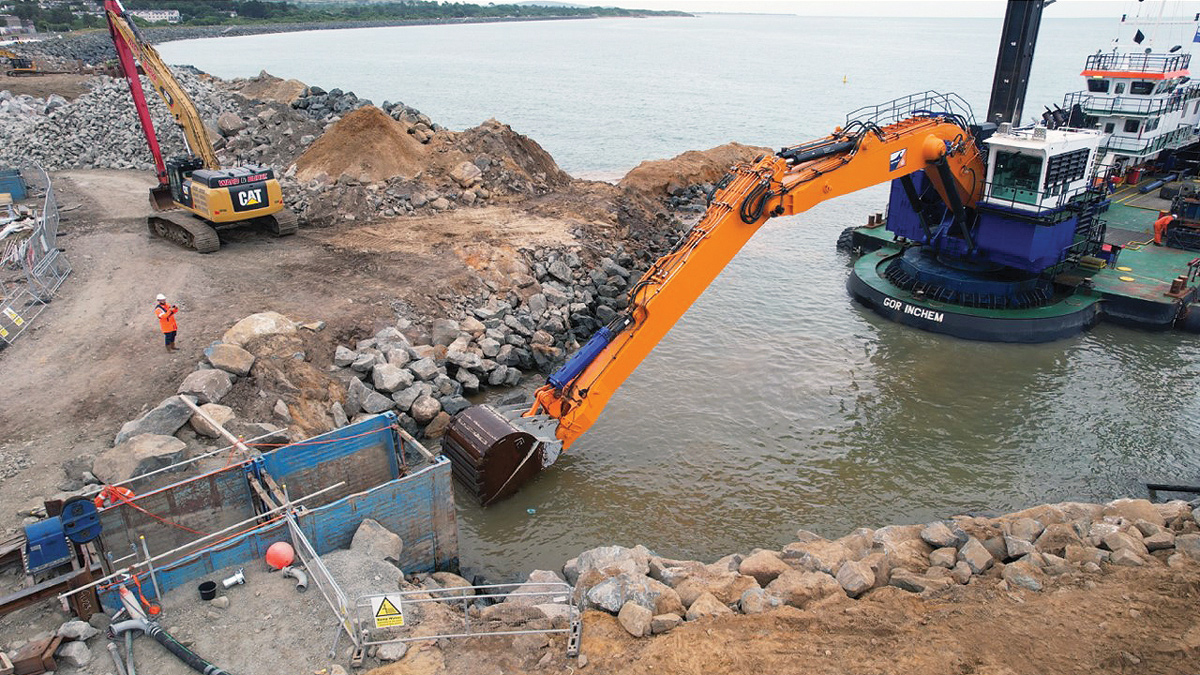
Excavation of trench at the onshore connection point using the backhoe dredger ‘Razende Bol’ – Courtesy of Van Oord Ireland
Marine works
A total length of 927m of polyethylene pipe (630mm OD SDR 17 PE100) was manufactured by Pipelife Norge AS, in three lengths of 309m which were then towed from Norway by sea to the dock in Arklow, Ireland for preparation and assembly.
Along the quay wall, concrete collars, each weighing 1 tonne were installed around the pipe strings at 3.5m centre to centre distances. The collars were lifted from land with special lifting equipment and the two halves of the collar were connected from the water using small workboats. Flanges were fitted with the assistance of a marine tug boat and the on board crane. During these operations the HDPE pipe was lifted out of the water. The lifting operations of the pipeline where analysed in detail to predict stresses in the material and the bending radius of the pipe. Using this analysis the lifting operations could be adjusted to prevent buckling or damaging the HDPE pipe.
For the installation of six riser feet on the pipe, a spreader beam was used to lift the pipe 1m out of the water. The usage of the spreader beam followed from the analysis done for the lifting.
Excavation of the trench was carried out using land-based excavators on the revetment and Van Oord’s backhoe dredger ‘Razende Bol’ for the marine trench. A minimum cover of 1.5m above the crown of the pipe was required for the outfall pipeline through its entire route. The excavated trench material was cast adjacent to the trench for re-use as backfill material upon completion of installation.
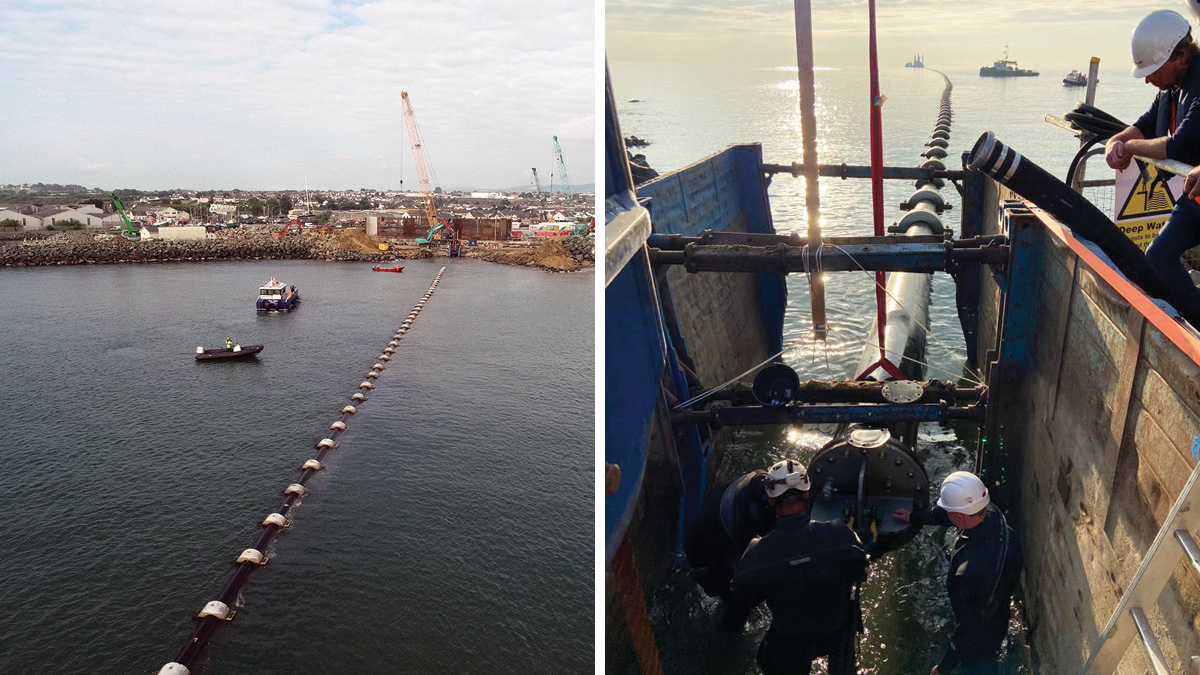
(left) Outfall pipe during sinking operation and (right) outfall pipe aligned prior to sinking operation – Courtesy of Van Oord Ireland
Installation
After pipe preparations were completed and the trench was excavated, the pipe installation commenced. The three separate pipe sections were connected with flange connections next to the quay wall in Arklow in order to create one long pipe length of 927m. Bend restrictors to prevent over-bending at the flange-flange interface were also installed. The finished pipeline was manoeuvred out of the port using two tugs and multiple small work boats. The pipe was anchored overnight just outside the Arklow port.
Before the sinking operation, the pipes were aligned and brought into the onshore connections point where pumps were set-up to flood and sink the pipe. The pipes were pulled into the shore using a pre-installed pull wire and an onshore drum winch. The polyethylene pipelines were installed using the ‘float and flood’ method starting from the fixed onshore end.
During the sinking operation, the offshore end of the pipes were connected to a multicat which was moored alongside the backhoe dredger ‘Razende Bol’ for proper positioning. The controlled pumping of seawater into the onshore pipe end, initiated the sinking process which caused the pipe to form an S-curve of approximately 20m long between the seabed and seawater surface. Two tug boats (shoal busters) were used in order to position the pipe correctly at the location of sinking.
As a contingency measure and to ensure the installation process was well controlled, a foam pig was pre-installed in order to create a seal between the pipe section filled with air and the section filled with water, in case the pipe had to be re-floated due to inclement weather. Once the pipe sections were completely installed in the trench, the profile was checked by a multibeam survey to verify the final pipe position.
Post pipe installation, the foam pig was removed from the pipe. A Type II pressure test of 2.25 bar was performed in accordance with the procedure set out in IGN 4-01-03, to 1.5 x the maximum internal working pressure.
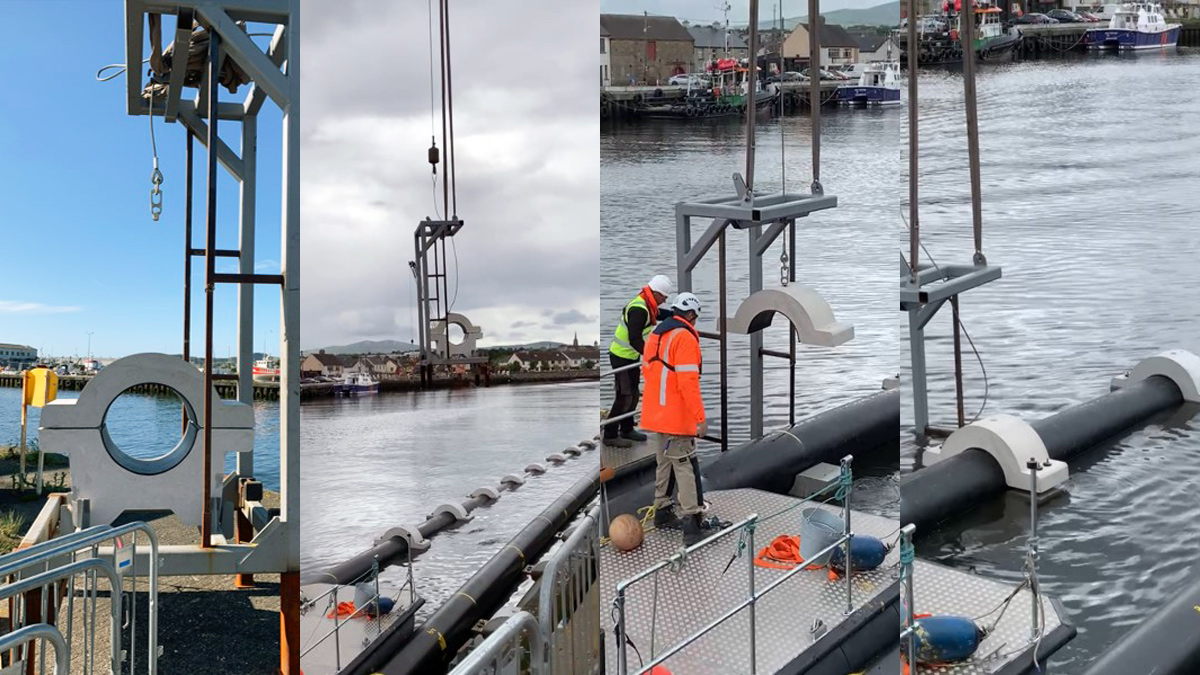
Outfall pipe concrete collars being fitted in water with special lifting equipment – Courtesy of Van Oord Ireland
Once the outfall pipeline had been sunk to the sea bottom and pressure tested, concrete kennels, each weighing 1 tonne were placed in between the concrete collars at 3.5m centre to centre spacings to provide additional permanent weighting. Additionally, six diffusers were installed from the backhoe dredger platform by divers. Each diffuser comprised of a flanged PE pipe, fittings and a riser with a four-port crosshead, each with a flange allowing for Tideflex S35 valves to be fitted directly. Included as part of the diffuser installation, was a removable access flange at the top of the riser to enable access inside the riser.
After completing the diffuser and kennel installation, the pipe was backfilled over its full length to provide 1.5m cover. Rock armour protection was further provided extending approximately 7m around the diffuser section from its centre to protect the area around the diffuser from scour. Also provided was a steel protection frame for the diffuser, fitted with sacrificial anodes to allow a 50yr design life for protection from dropped objects, anchors, trawlers and fishing nets. Finally, on the offshore end a marker buoy and on the onshore end a Saint Andrews Cross were installed to mark the pipeline location.
Due to the turbulent weather at the site location, including hold points in the working method, so that each installation step could be paused at planned intervals, allowed Van Oord to work around the weather. Additionally, working with local contractors who helped to adjust and adapt work methods and techniques within the limited amount of space, allowed the team to prepare and install the outfall system using specialised equipment and marine vessels, with minimal disruption to the environment and public. In particular, a bespoke rigging system was designed and fabricated using a local yard to assist with the efficient installation of the collars whilst working from the water.
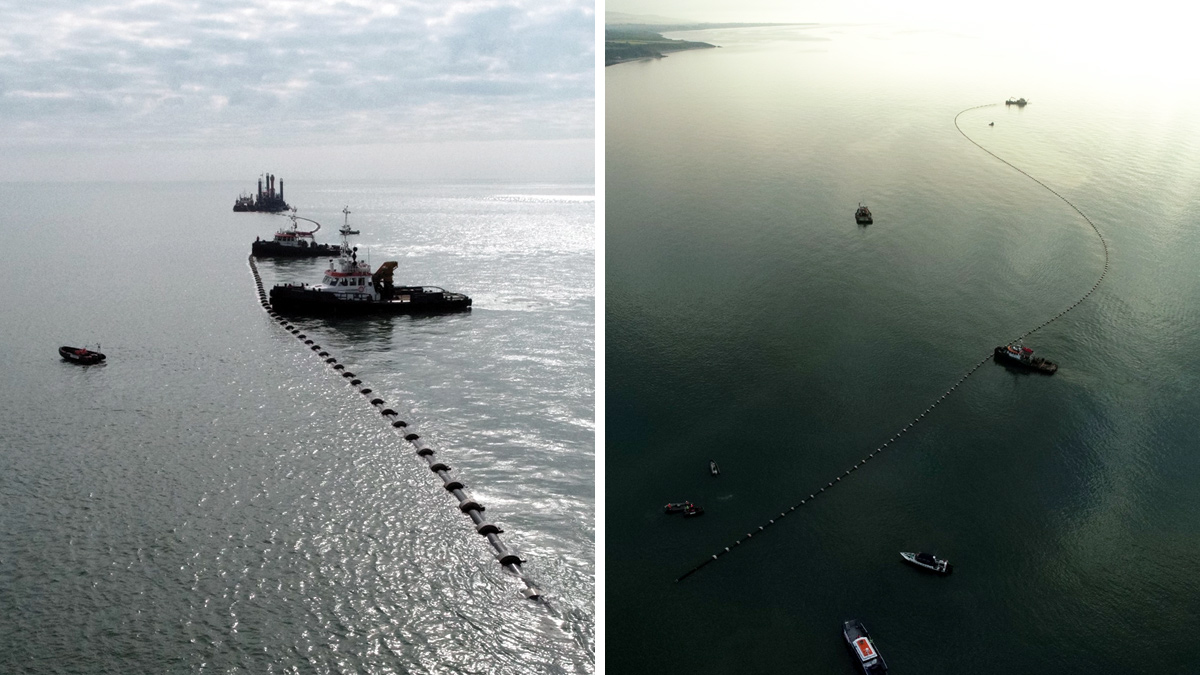
Outfall pipe during sinking operation – Courtesy of Van Oord Ireland
Conclusions
The successful completion of this project will allow treated effluent to be safely discharged from the new Arklow WwTP once operational and bring benefits in terms of health, environmental integrity and facilitate economic and social development for Arklow town and its surrounds, which had been constrained by the lack of adequate wastewater treatment capacity.