Bacton Combined Outfall (2019)
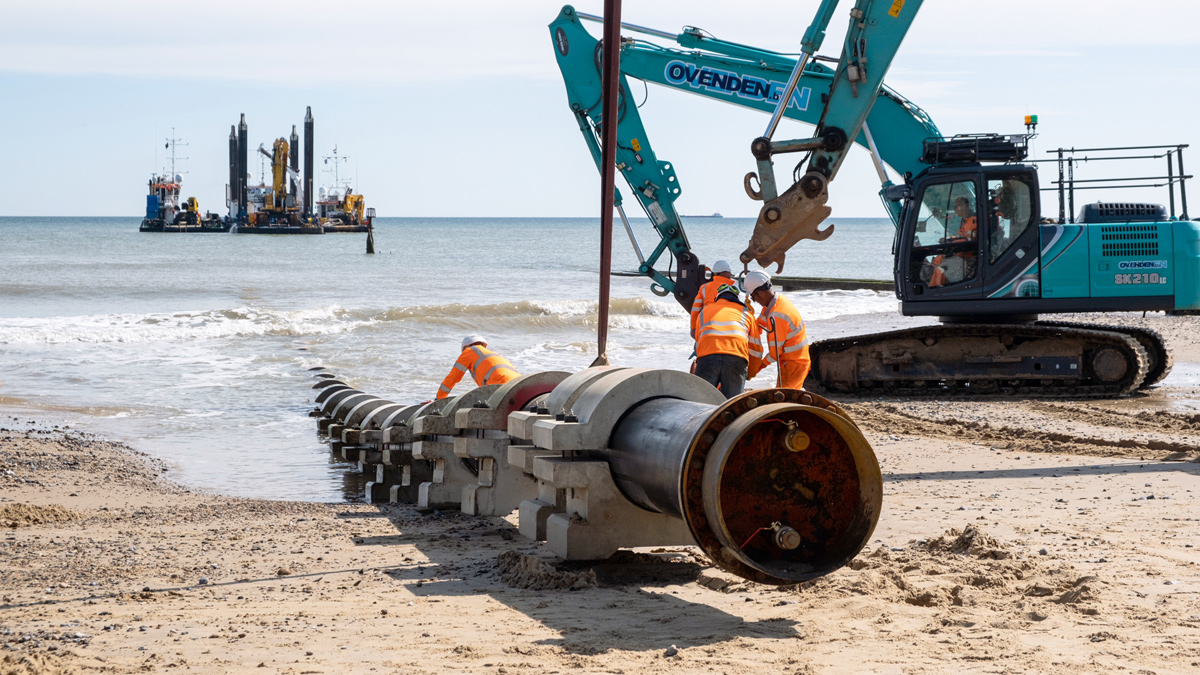
Bacton outfall installation - Courtesy of Royal HaskoningDHV
The North Norfolk coastline has undergone progressive coastal erosion at around the present rate for the last 5,000 years. The cliffs are made of soft deposits, mainly sand and soft clays, which are very vulnerable to erosion. This long-term coastal change puts pressure on communities, infrastructure and business in the coastal zone. The Bacton Gas Terminal is situated on the North Norfolk coast with infrastructure near the cliff edge, within the cliff and under the beach. It is an item of nationally important critical infrastructure, supplying up to one third of the UK’s gas demand from the North Sea extraction fields and from the continent.
Background
To provide long-term protection to the coastline and the Bacton Gas Terminal, a coastline stabilisation project has been implemented that includes a large-scale beach nourishment operation. The scheme will place approximately 1.8 million cubic metres of sand along the coastline to protect the gas terminal and local villages and is the UK’s first sandscaping project.
The Bacton Gas Terminal infrastructure includes three existing outfalls that currently discharge below the low tide level. Implementing the sandscaping project would have buried the existing outfalls under approximately 6-7m of sand as well as significantly extending the location of low water offshore. Therefore, the extension or replacement to facilitate discharging beyond the extent of the sandscaping, was incorporated into the project scope to maintain the existing outfall discharges for the remaining life of the terminal.
Existing outfalls
At present, three separate outfalls operate at the Bacton Gas Terminal outfall and discharge treated process effluent and surface drainage water beyond the low tide level. Each outfall is owned and operated by a separate company (two of which are Shell and Perenco) who occupy separate areas of the terminal. All three of the existing outfalls show signs of damage and corrosion on the foreshore and have minimal asset life remaining. The three outfalls are separated by approximately 750m, where the Shell outfall is the most southern and the Perenco outfall is in the middle. These existing outfalls can be summarised as follows:
- Shell outfall: The Shell outfall was constructed in 1968. It is a 177m long 24” steel and cast iron pipeline which is routed from a storage facility within the terminal, through the coastal cliffs and continues along the beach supported within a piled timber trestle structure.
- Perenco outfall: The Perenco outfall is a 188m long 500mm diameter cast iron pipe also routed through the coastal cliffs and crosses the beach in a piled timber trestle. Previously in 1997, to extend the remaining asset life of the cast iron outfall, the section of pipe through the cliff and offshore was slip lined with a 400mm polyethylene pipe.
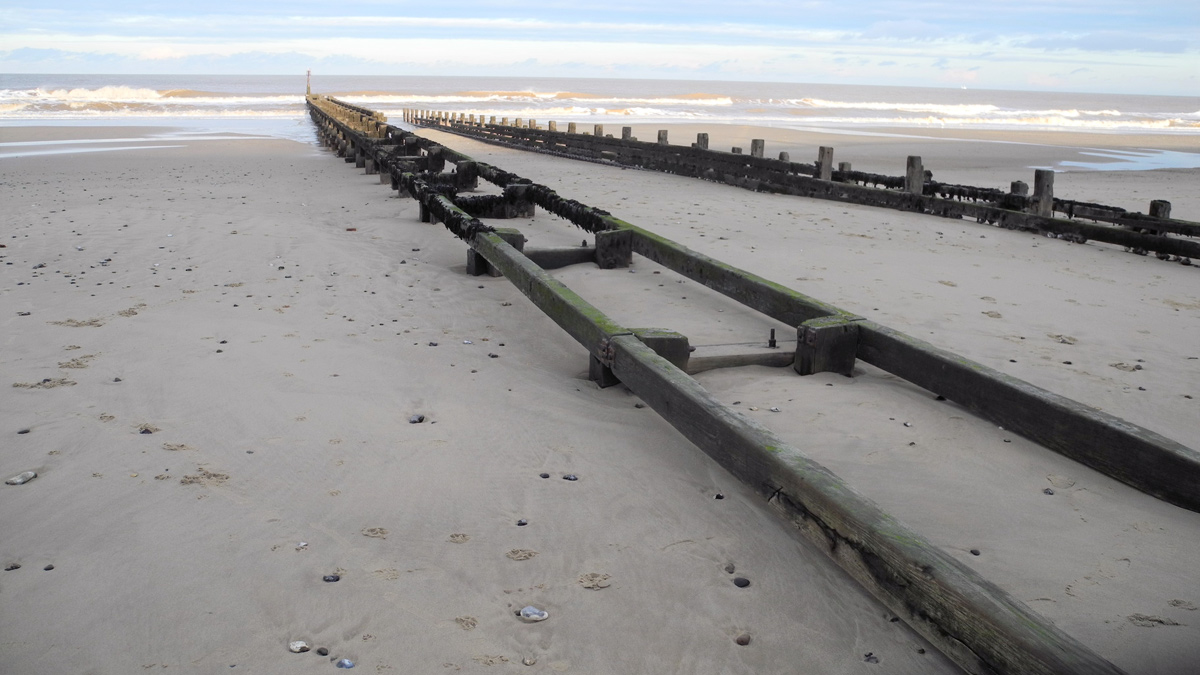
Existing Shell outfall – Courtesy of Royal HaskoningDHV
The solution
The concept design phase commenced in Spring 2018 and considered options for each individual outfall including repair, extension or installation of new outfalls alongside the existing. The option to combine all three outfalls into a single outfall discharging beyond the sandscaping was proposed by the Royal HaskoningDHV design team at an early stage of the concept design.
This solution would collect the three separate discharges either within the terminal, or at the top of the beach above the high tide level, requiring an inter-connecting pipeline to be constructed. Hydraulic analysis of the combined system was undertaken to confirm the pipe diameters, assess any transient conditions and confirm the air venting requirements. In addition, an Environment Agency H1 assessment was completed for the combined discharge to confirm compliance with dispersion and water quality requirements.
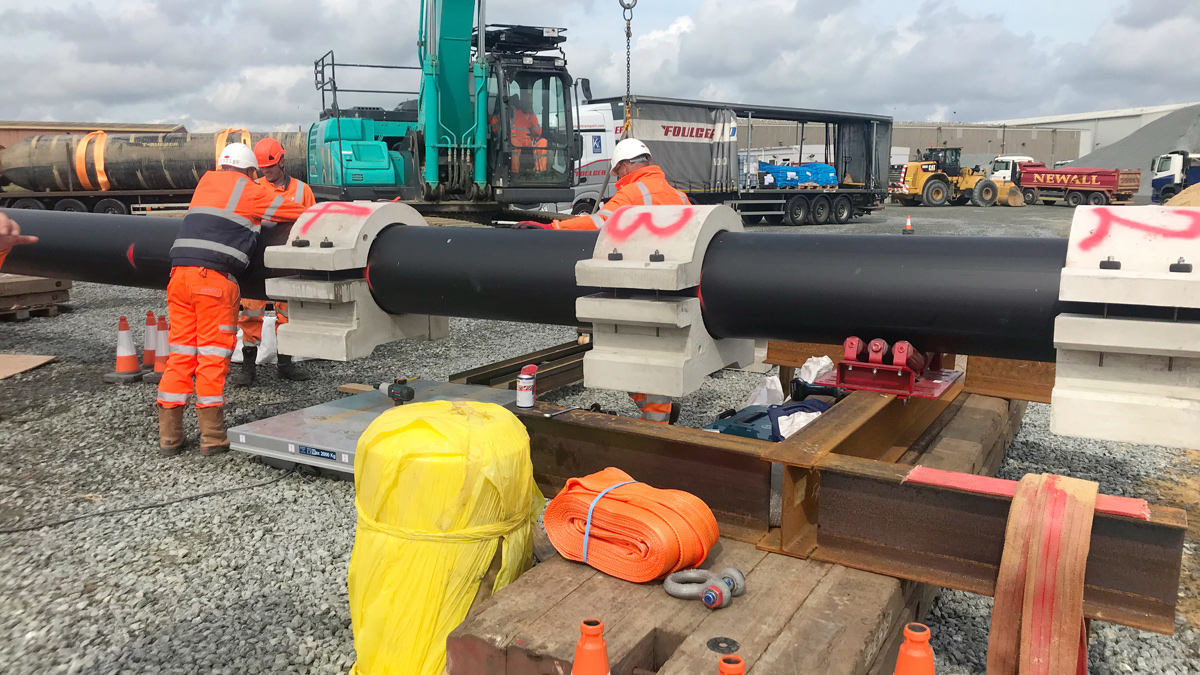
Outfall pipe concrete collars being fitted in Great Yarmouth – Courtesy of Royal HaskoningDHV
Taking into consideration the various advantages and disadvantages for each of the design options and cost estimates produced, it was recommended and agreed with all three terminal companies that a combined outfall would be the most cost beneficial and lowest risk solution.
The agreed project scope consisted of 747m of solid wall polyethylene pipe (HDPE) 250mm outside diameter (OD) increasing to 500mm OD laid at the top of the beach to interconnect the existing outfalls. The beach location was chosen because connection within the terminal was not possible due to the limited space available in proximity to existing services and incoming gas supply pipework.
The interconnecting pipe connects to a new 500mm (OD) outfall adjacent to the Shell outfall at the southern end of the terminal before extending an additional 152m beyond the existing outfall and terminating in a 2-port diffuser with a concrete protection dome. The outfall and interconnecting pipe were to be constructed off-line to allow existing discharges to continue prior to final connections being completed.
To combat flotation and provide stability under environmental loadings, the polyethylene pipes were fitted with concrete weight collars prior to installation and additional concrete kennels provided where additional weight and protection was required.
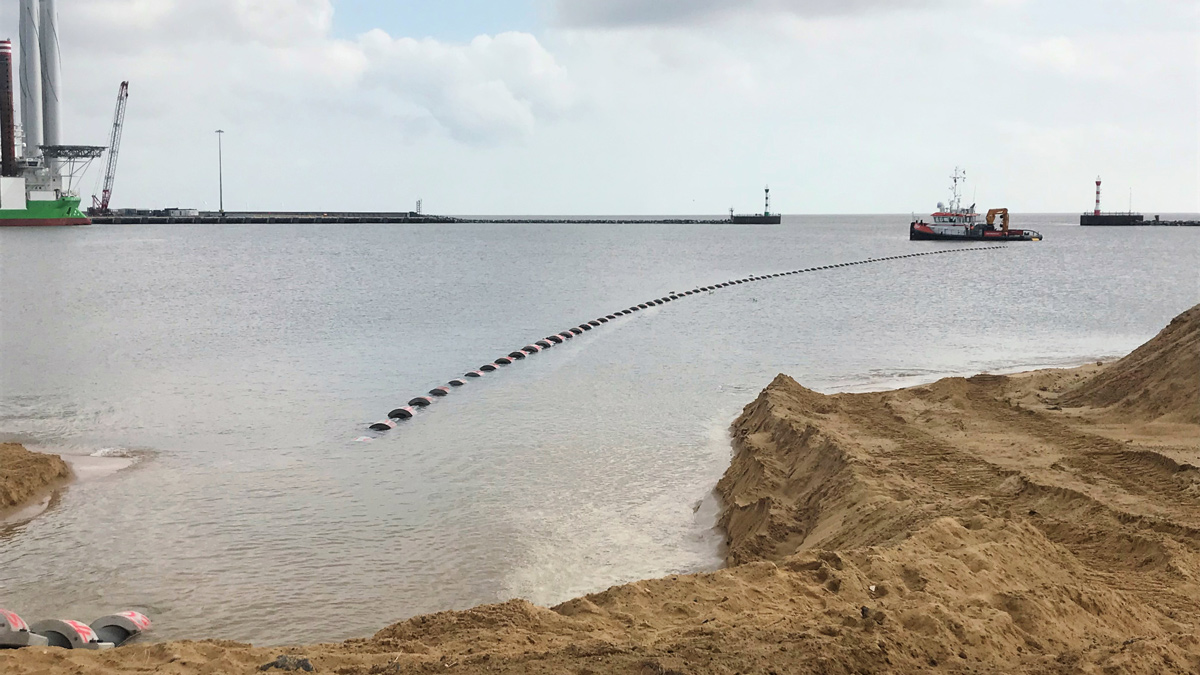
Outfall pipe floated in Great Yarmouth prior to installation – Courtesy of Royal HaskoningDHV
Site investigation
Site information was provided by the terminal operators from two ground investigations undertaken in 1988 and 2005 at the gas terminal, as well as information from the BGS website borehole archive that included relevant land-based and over-water boreholes.
The ground investigation indicated that the ground conditions generally comprised of a variable sequence of coarse soils overlying chalk. The offshore investigation data indicated that there is a significant variation in the level of the top of the chalk along the coast; but this was estimated to below the proposed dredged trench.
The requirement for further site investigations were identified and these included magnetometry, sub-bottom profiling and Unexploded Ordinance (UXO) surveys to determine the mitigation measures required to be undertaken prior to the proposed works and construction of the pipeline.
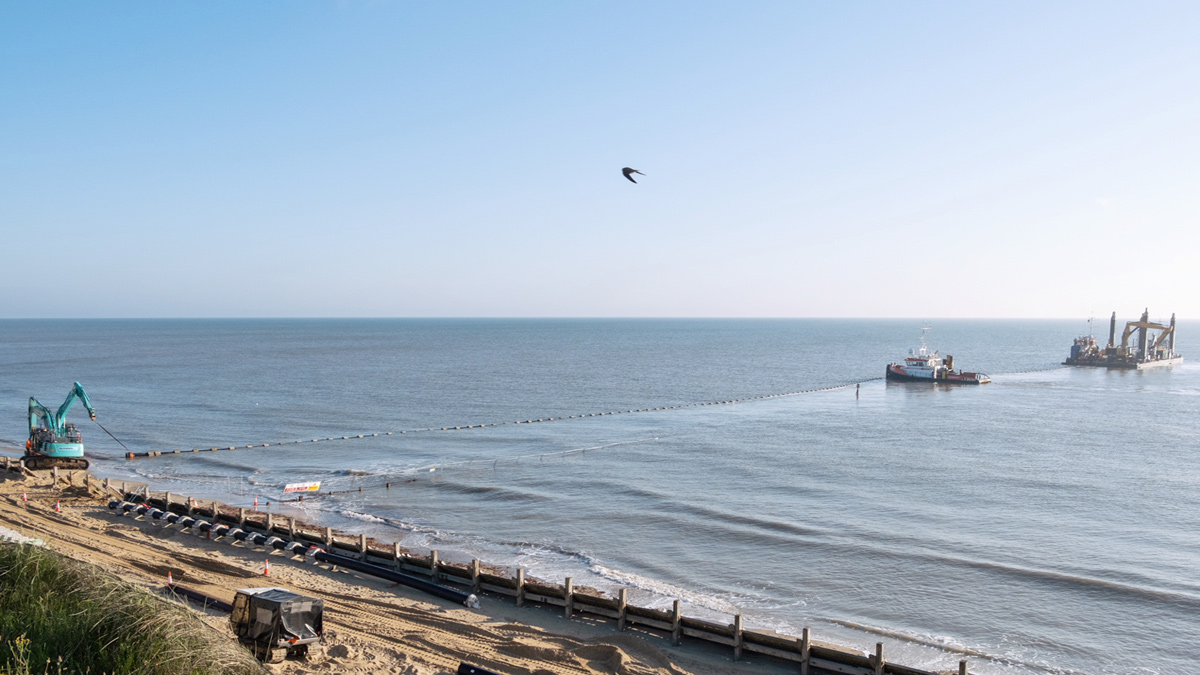
Outfall pipe aligned prior to flooding – Courtesy of Royal HaskoningDHV
Constraints
The North Norfolk coastline has undergone progressive coastal erosion and the cliffs at the Bacton directly in front of the gas terminal are made of soft deposits, mainly sand and soft clays, which are very vulnerable to erosion and instability. All three of the existing outfalls pipes were previously installed through the cliff and concerns were raised early in the project with regards to replacing these sections of pipe. Maintenance inspections and non-destructive testing of these pipes has been previously undertaken to confirm their condition and sufficient remaining asset life. It was agreed with all three terminal operators that the existing sections of pipe through the cliff would remain with the interconnecting pipe located downstream on the beach.
The gas terminal is supplied from North Sea extraction fields and from the continent via several gas pipelines that are routed inshore and also through the cliffs and connect to the terminal. The existing three outfall pipelines, the proposed interconnecting and combined outfall pipes were all located in proximity to the various gas pipelines. Safe working distances, minimum separation distances within the trench and plant crossing protection measures all had to be agreed with the terminal companies and a protocol developed for adoption by the contractor.
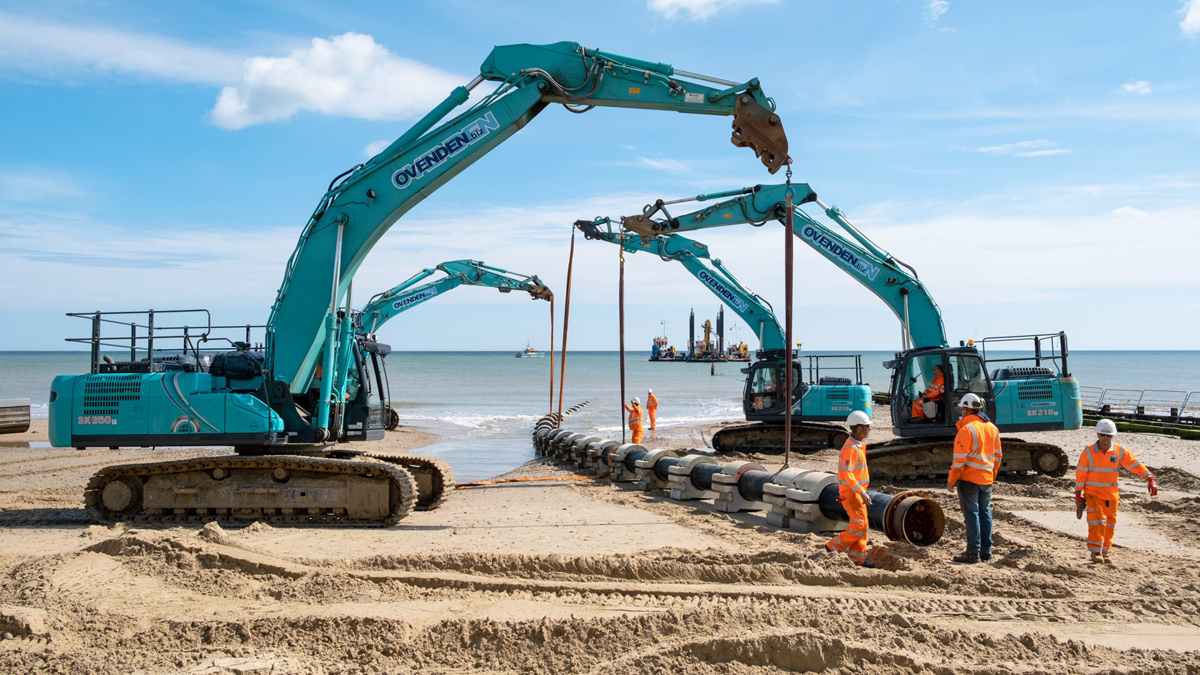
Final alignment of the outfall following float and flood installation – Courtesy of Royal HaskoningDHV
Design progression
Royal HaskoningDHV undertook the detailed design of the combined outfall and interconnecting pipe. Stability and protection to the pipelines was provided through the use of 126kg and 494kg fixed weight collars on the 250mm diameter and 500mm diameter pipes respectively. The design of the collars, in terms of its spacing and sizing, was optimised to provide consistent ballasting throughout the length of the pipeline assembly, enabling practical installation. The combined outfall pipeline assembly was installed using the float and flood methodology with all the concrete collars pre-installed. Due to the location of the combined outfall in the high energy inter tidal zone the weight per metre required for stability could not be achieved with collars whilst still allowing the pipeline to float. Additional weights in the form of 835kg concrete kennels would be installed after the outfall pipeline was in place to provide the additional weight needed to stabilise the pipe.
The hydraulic analysis of the combined outfall system using a WANDA hydraulic model was completed to determine the transportation of air and any vent requirements. The profile of the inter-connecting pipe was constrained due to the relative levels of the existing outfall pipes and other pipelines. Two air vents consisting of a 180mm internal diameter pipe stack venting 3m above the final sandscaped beach level was required and included in the scope.
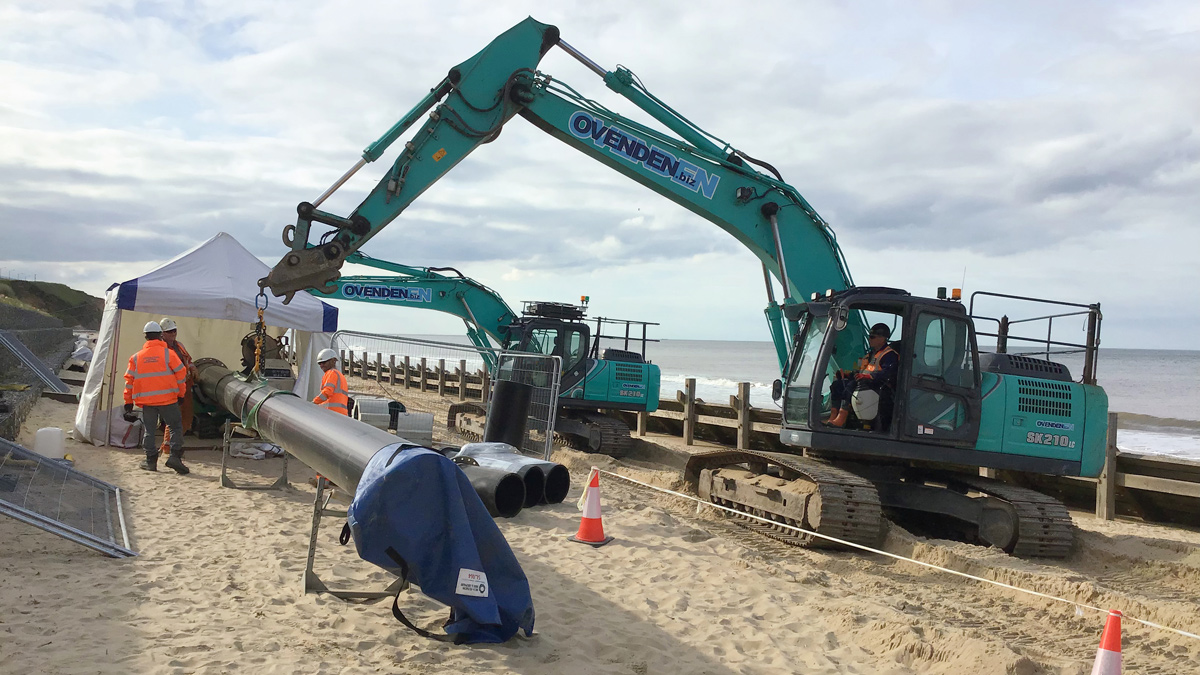
Welding of the interconnecting pipe – Courtesy of Royal HaskoningDHV
The diffuser located at the discharge end of the combined outfall consisted of a single vertical riser with two ports. Due to the inshore location of the diffuser and the high energy environmental forces, a precast concrete protection dome was designed to provide protect from the wave forces and from anchor/fishing damage. The diffuser dome was separated into four sections, bolted together in situ, which reduced the lifting requirements of the marine equipment during construction. As the protective dome structure would be protruding above the seabed and the discharge from the ports, it was considered necessary to protect the area locally from scour with rock armour (200-500kg).
Bacton Combined Outfall – Key participants
- Designers: Royal HaskoningDHV
- Contractor: Team Van Oord
- Pipe supplier: Wolseley
- Precast concrete collars: Subsea Protection System (SPS)
- Duckbill valves: Tideflex
Land works
Following completion of the detailed design and specifications by Royal HaskoningDHV, Team Van Oord were successful in the competitive tender and were appointed in 2019 as Principal Contractor by North Norfolk District Council. The contract scope included both the beach nourishment and coastal protection works as well as the removal of the old outfalls and installation of the combined outfall.
The 250mm and 500mm diameter polyethylene pipes for the interconnecting land section were delivered to site in 12m lengths and butt-welded using automated equipment to ensure strong and consistent joints. The trench for the interconnecting pipework was excavated using conventional land-based plant, with the excavated material side-cast and used as backfill once the pipework was installed. The pipelines were pre-assembled into 48m strings at the top of the beach which were then transported and lowered into the excavated trench. The pipe strings were jointed using flange couplers to avoid the need for welding within the excavated trench. The connections to the existing outfalls where undertaken using a configuration of bends, T-pieces and couplers.
Outfall installation
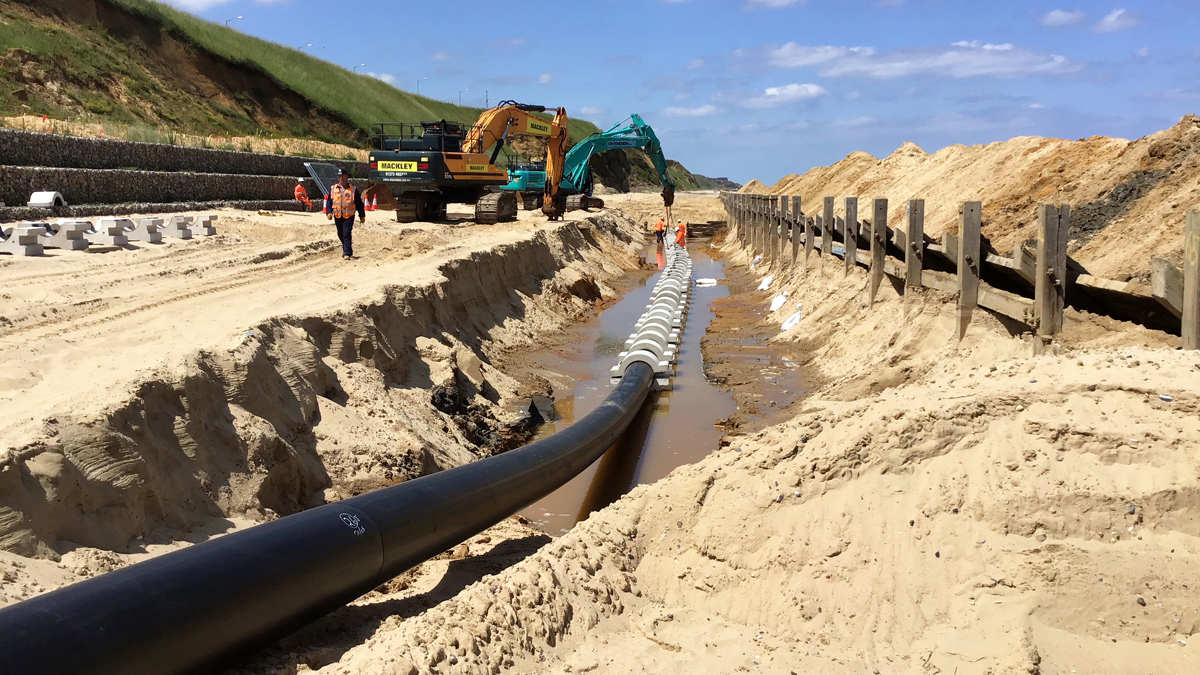
Interconnecting pipe installation – Courtesy of Royal HaskoningDHV
A backhoe dredger was used to excavate the trench in the tidal area to provide sufficient depth for the outfall pipe with a minimum cover depth of 1.5m for the future predicted profile of the seabed profile. As with the interconnecting pipework trench, the excavated material was side-cast and used as backfill once the pipework was installed.
The marine outfall pipeline was welded into a single, approximately 300m long section in Great Yarmouth prior to the concrete collars being fitted. The 300m outfall pipeline was installed using the ‘float and flood’ method. with the offshore end of the pipeline controlled by a backhoe dredger fixed in position. The controlled pumping of seawater into the onshore pipe end initiated the sinking process which caused the pipe to form an s-curve between the seabed and seawater surface and descend into its final position.
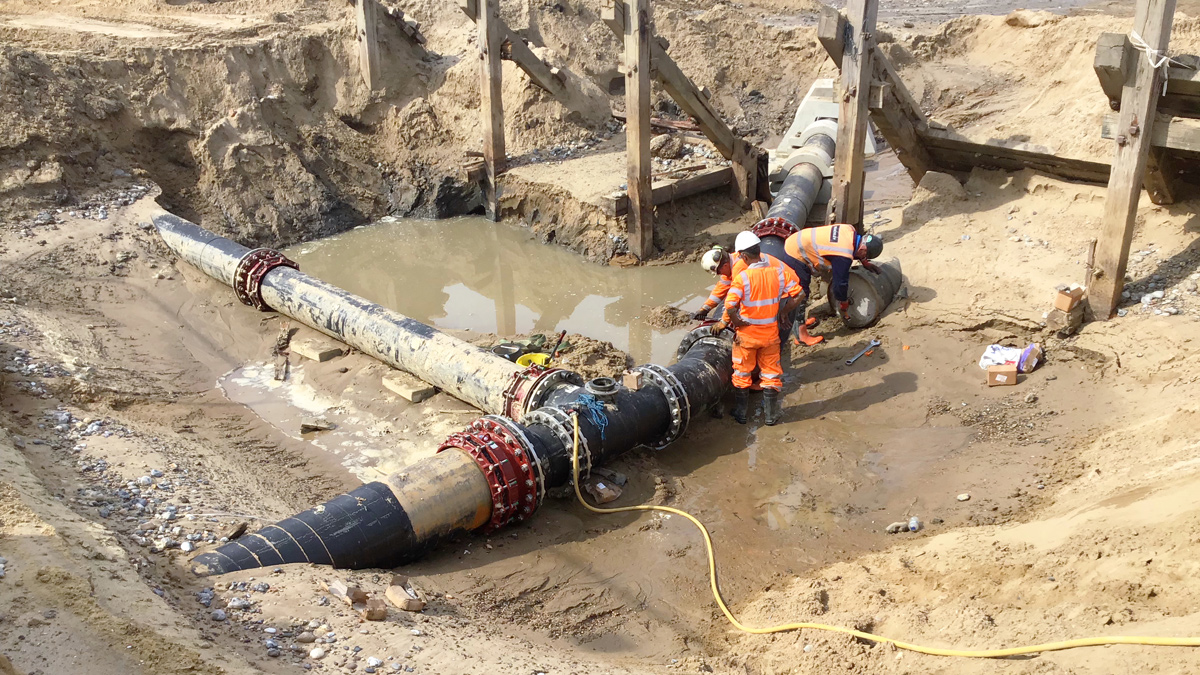
Final pipe connections between existing outfalls, interconnector and new outfall – Courtesy of Royal HaskoningDHV
Once the outfall pipeline had been sunk to the sea bottom and tested, the diffuser was installed from the backhoe dredger platform by divers. The diffuser comprised of a flanged HDPE pipe, fittings and a single riser with a four-port crosshead, each a nominal 250mm outside diameter, allowing for Tideflex check valves to be fitted directly. A removable access flange at the top of the riser was included as part of the diffuser installation to enable access inside the riser pipe for future maintenance.
The precast concrete protection dome was then lifted into position and a marker buoy installed for identification. The final connections between the new combined outfall, existing outfalls and the interconnecting pipe work were undertaken to allow for success commissioning. The dredging and creation of the sandscaping commenced immediately after the outfall works to ensure completion before the end of the summer weather period.
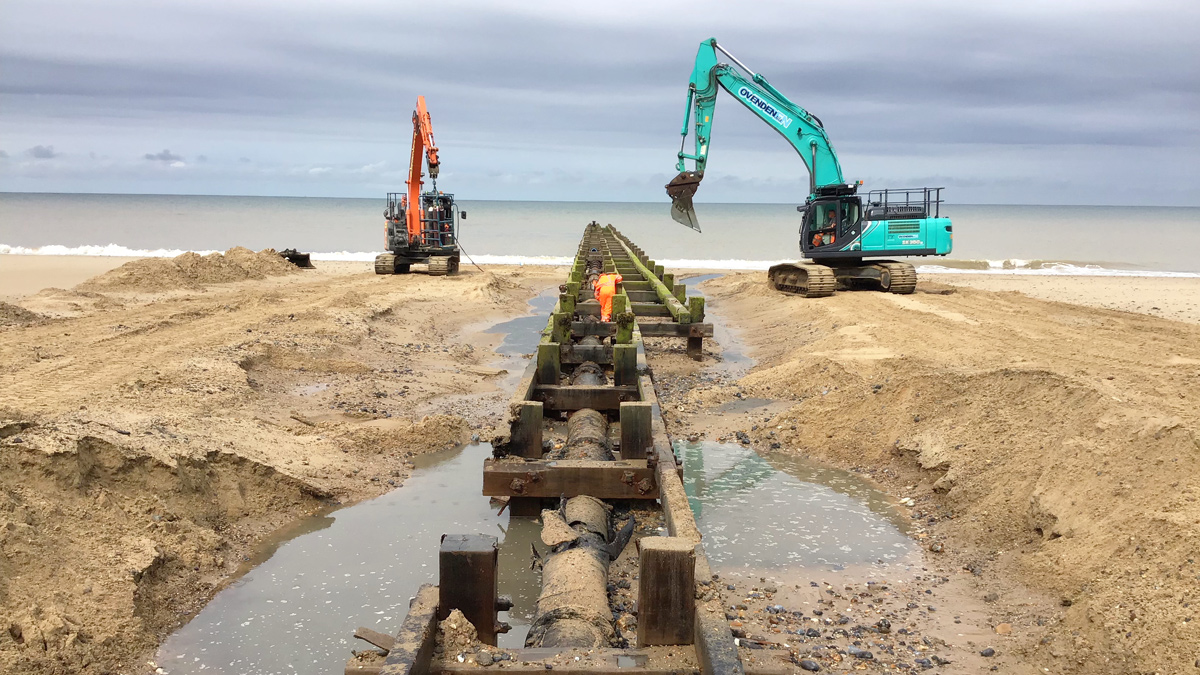
Existing outfall removal following completion – Courtesy of Royal HaskoningDHV
Conclusion
The installation of the combined outfall system was completed at the end of June 2019. The successful completion of this project and the wider coastal protection works will allow stormwater and processed effluent to be safely discharged throughout the remaining design life of the Bacton Gas Terminal.
The editor and publishers would like to thank Martin Berry, Design Manager, and Sean Burn, Engineer, both with Royal HaskoningDHV, for providing the above article for publication.