Bray Keleher WTW (2020)
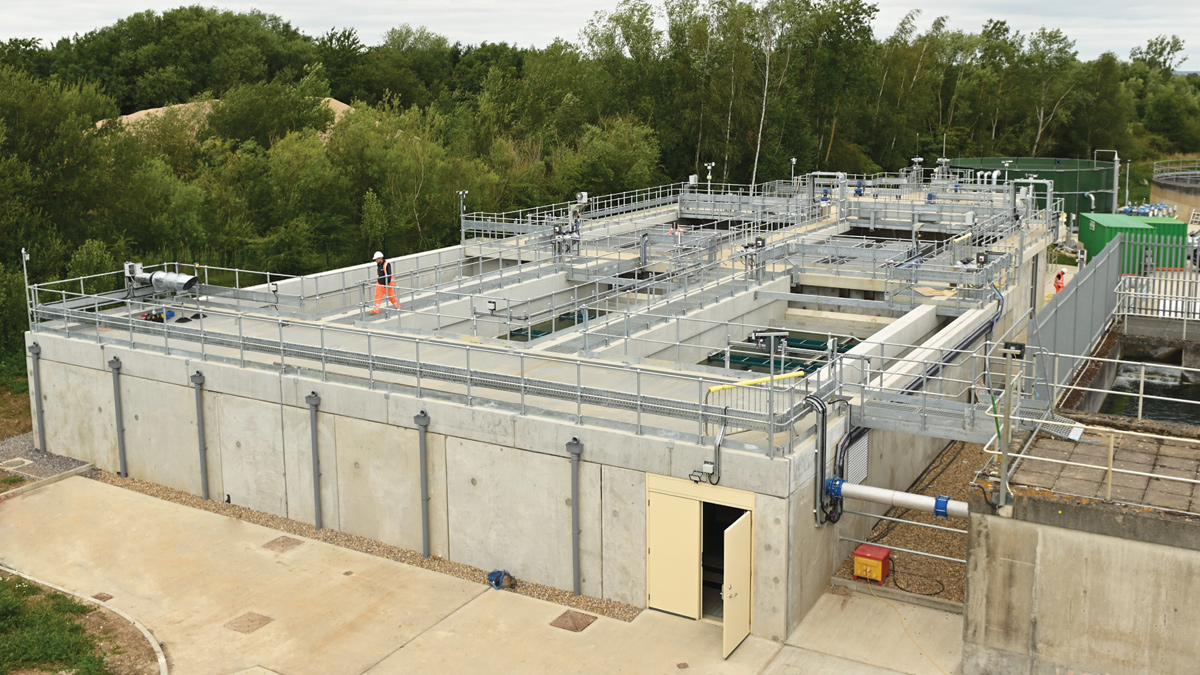
The new RGF, clarifiers and flocculators at Bray Keleher WTW - Courtesy of South East Water
The Bray Keleher Water Treatment Works (WTW) abstracts and treats a maximum of 45 Ml/d of river Thames water and is located on Monkey Island Lane, Bray, between Windsor and Maidenhead. The works is of strategic importance in maintaining supplies to the western region of South East Water (SEW). As part of the final determination of the AMP5 cycle, provision was made to increase the production capacity of the site form its then capacity of 45 Ml/d to the maximum Environment Agency abstraction licence of 68 Ml/d. This strategic vision was driven by the Water Resources Management Plan (WRMP) which seeks to identify measures required to ensure supply can be maintained while accounting for the long-term forecasts of consumption demand.
Treatment stages
It was decided early in appraisal stage to take advantage of the visionary design of the Bray WTW, carried out in the early 1990s, which made allowance for the future expansion up to 68 Ml/d. This allowance took the form of available space in the footprint of the WTW as well as provision made in some of the structures for this expansion. To take advantage of this, the flow and process would be passed forward through the following treatment stages:
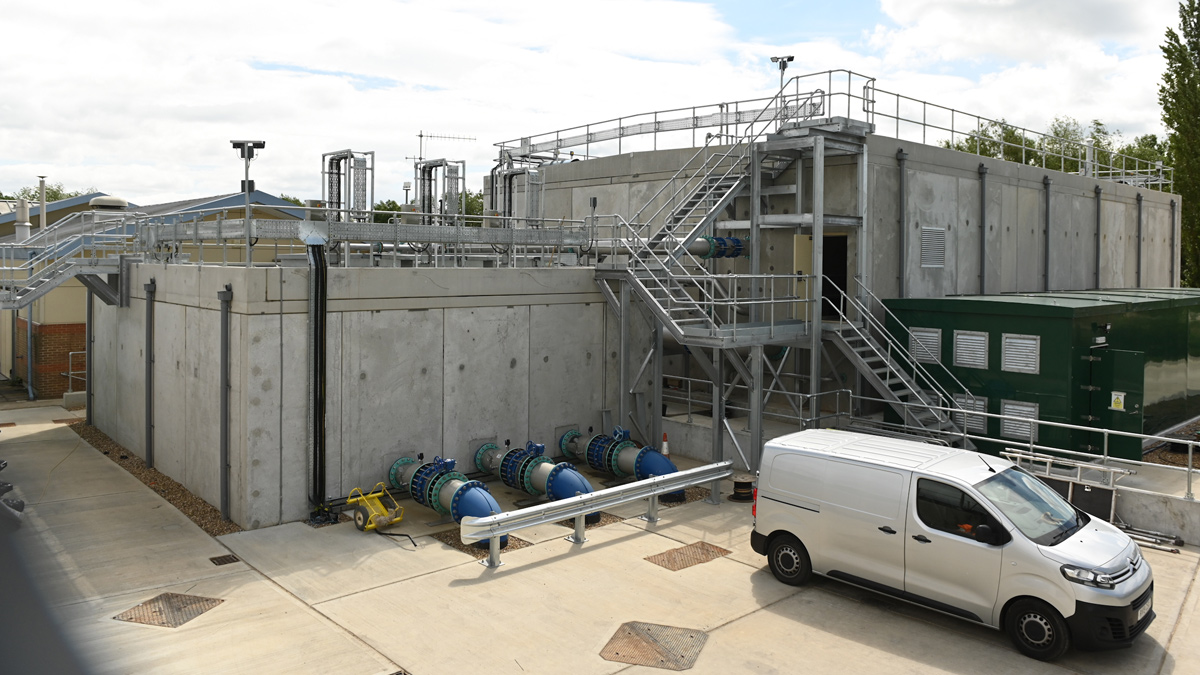
Clean backwash tank and GAC filter – Courtesy of South East Water
- The River Thames intake screen and associated apparatus allows flows of 68 Ml/d to be passed forward under gravity to the Bray WTW low level pumps, located further down Monkey Island Lane at Bray Gravels PS. It was recognised that this low-level pumping station would require an additional submersible pump to lift the additional flows to the Bray WTW. The twin 700mm rising main from Bray Gravels allows for the increased flow rate to the WTW.
- At Bray WTW, the first process unit is the pre-ozonation stage which again allowed for the increased flow rate, although it was recognised that the ozone tank and ozone aerator would require improvement.
- After ozonation, flows are then passed forward to the flash mixer; a larger mixer is required to treat the increased flow rate.
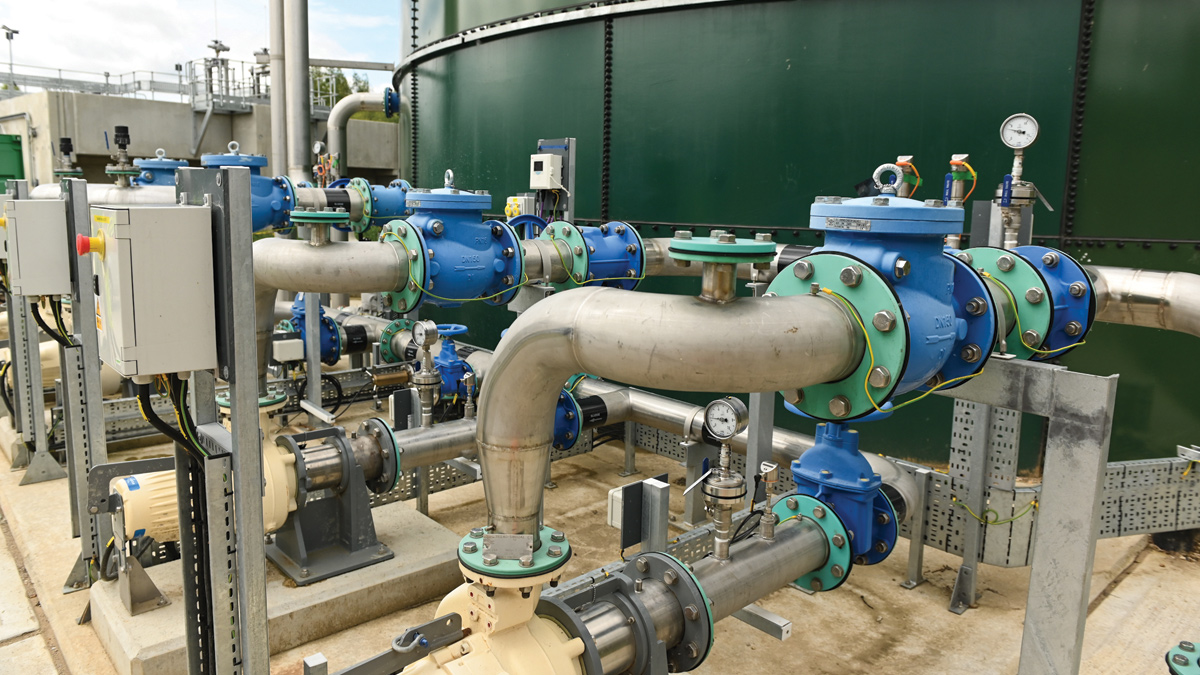
Sludge mixers – Courtesy of South East Water
- On leaving the flash mixer, water divides with 45 Ml/d being passed forward to the existing works and the increased flow being passed forward to the new flocculators, clarifiers and rapid gravity filters (RGFs).
- Flows are them combined in the existing intermediate pumping station, which required modification to direct 45 Ml/d towards the existing granulated activate carbon (GAC) filters and 23 Ml/d towards the new GAC filters. It was recognised that this modification would also involve the construction of a replacement clean backwash tank.
- Flows will then be combined prior to the UV treatment stage and then onto the existing contact tank and treated storage tanks; these all required little modification.
- The existing high lift pumping station which pumps treated water to the Surrey Hill Service Reservoir for onward distribution to the network, required an additional pump to enable 68 Ml/d to be disinfected and passed forward to the network.
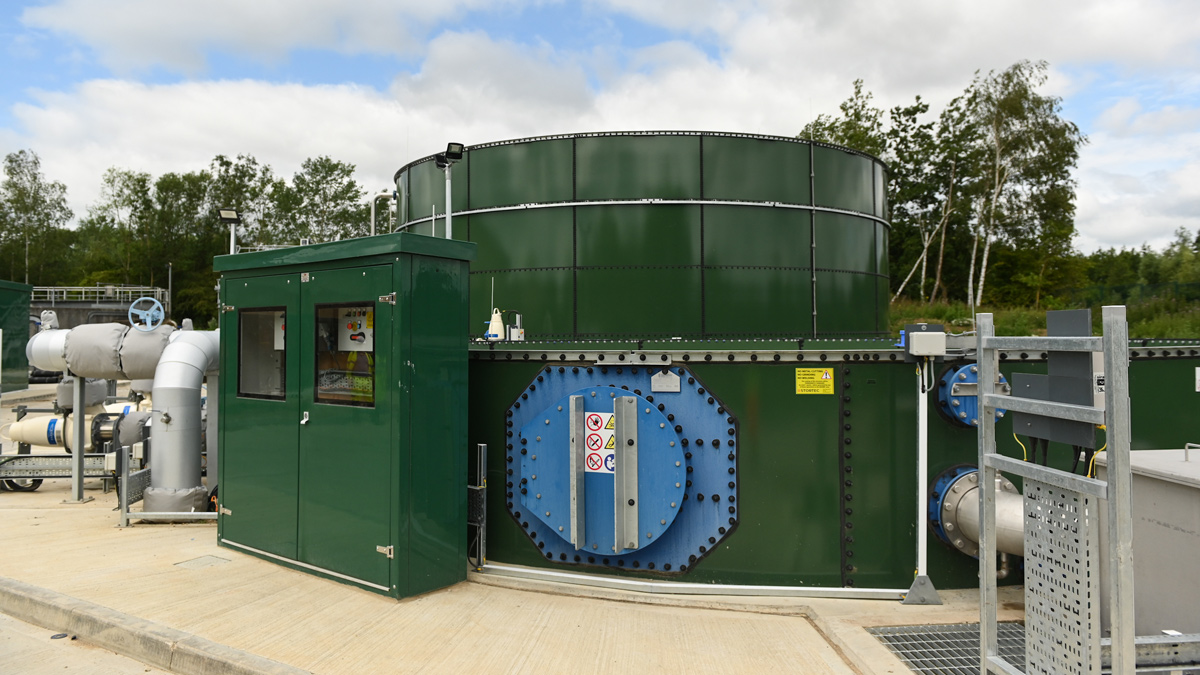
Sludge treatment plant – Courtesy of South East Water
The result of this design ensures that the old and new treatment streams are fully integrated such that the production teams will be able to operate and maintain one works rather than a combination of two separate units. It also meant that throughout the construction, installation and commissioning stages, close liaison was maintained between SEW and the delivery contractor; Bam Nomenca Joint Venture (BNJV), to address any challenges that would inevitably arise during the construct period. In order to generate this collaborative working the main Bray Board and meeting room was converted into a joint working office allowing both parties to be stationed there for the remaining lifetime of the project.
Undertakings
A NEC3 construction contract was awarded to BNJV in January 2018, to deliver the works in accordance to the accepted design laid out in the earlier Professional Services Contract for feasibility and design services. A hectic period of sub-contractor procurement, land remediation, civil construction utilising precast concrete structures followed (as described in the 2019 edition of this publication), until eventually the mechanical and electrical installation could begin. The supply chain key participants are:
- Civils contractor: BAM Nuttall
- Civils design: Pick Everard
- M&E design & contractor: Galliford Try
- CFD Modelling: The Fluid Group
- Technical documentation: 3rd Light Media
- Land remediation: Provectus Remediation Ltd
- Earthworks: BAM Nuttall
- CFA piling: Suttle Projects
- Precast concrete: Kijlsta (Netherlands)
- Precast panel installation: Quadro Services Ltd
- Above ground pipework: ABC Stainless
- MCC & software: Blackburn Starling Ltd
- Glass coated tanks: Stortec Engineering Ltd
- Water quality monitors: SWAN Analytical UK Ltd
- Air blowers: Aerzen Machines
- Centrifugal pumps: Xylem Water Solutions
- Flocculators: Nov Chemineer
- Lamella plates & scrapers: Hydro International
- Ozone plant: Xylem Water Solutions
- Penstocks: Ham Baker
- Flow controls: Auma Actuators
- Sludge thickening progressive cavity pumps (Bray): SEEPEX UK Ltd
- RGF & GAC floors: Xylem Water Solutions
- Sludge conveyors: Spirac
- Sludge mixers: Xylem Water Solutions
- Valves: Glenfield Invicta
Work commenced on several work fronts, starting with the sludge treatment zone, moving quickly onto the power upgrade from 1.6 MVA to 3.2 MVA, flocculators, clarifiers and the 3 (No.) RGFs.
And then came 23rd March 2020…
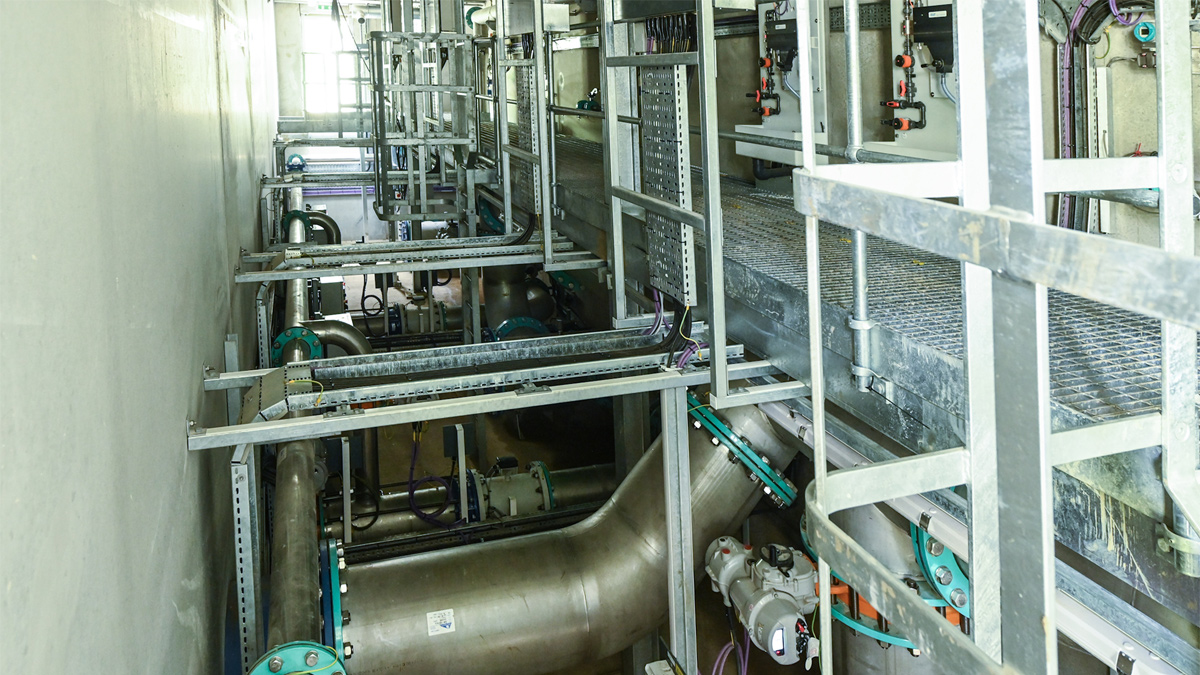
Filter gallery – Courtesy of South East Water
Working through a pandemic
As in common with many construction projects, the construction stage of the project would be heavily dependent on a variety of visiting tradesmen who need overnight accommodation for the period they are required on site. After the announcement of the Covid-19 lockdown requiring hotels, restaurants etc to close, many of the trades people were unable to attend site, which had an immediate effect on construction activities. This can clearly be seen by the fact that in the run-up to the Government’s announcement the site had around 54 trades on site compared to less than 10 on the day after the announcement was made.
Once the initial impact cleared it soon became apparent that in order to proceed a variety of additional safety measures would be required by both SEW and BNJV. These would range from designating all the project staff as key workers, providing additional personal protective equipment (PPE), following social distancing requirements, and providing additional welfare and accommodation facilities. BNJV set up a Covid-19 command team with the SEW team members, who met every day to plan routes to and from each work front, and additional cleansing measures that would be required for each work activity.
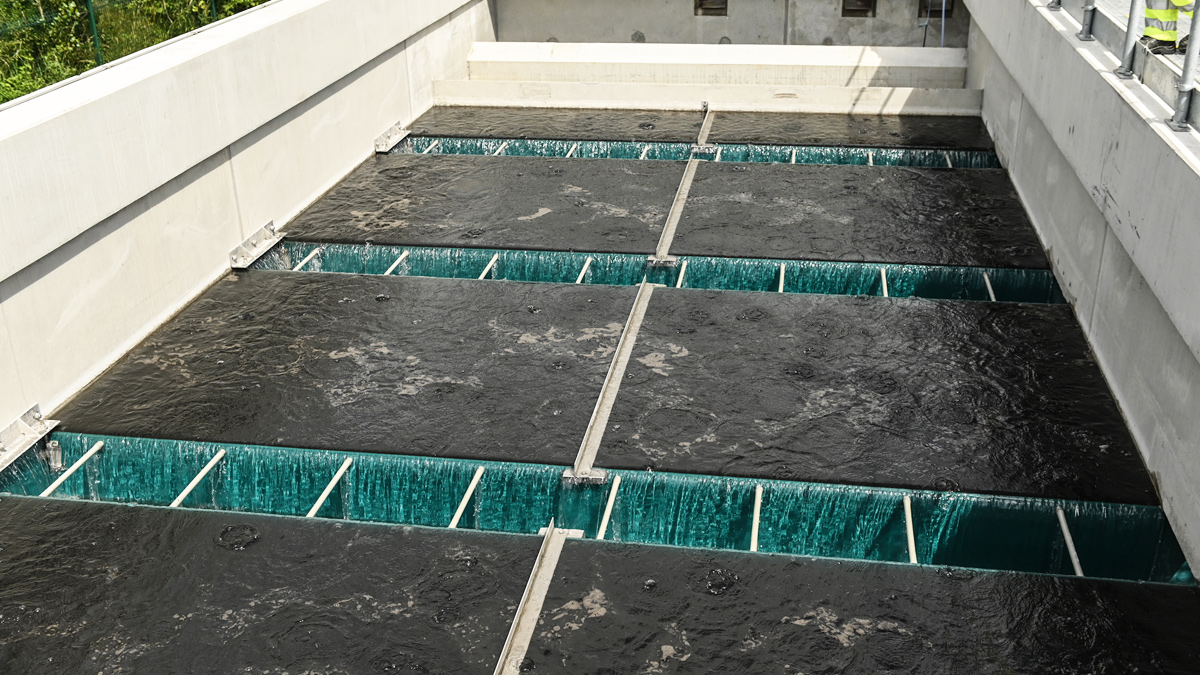
RGF backwash – Courtesy of South East Water
Key to the project success during this period was the physical separation between the SEW engineering team, the production team and BNJV teams with many meetings being conducted via video conferencing. It is a testimony to the efforts made by all parties that the on-site production was restored to manageable levels within 5 weeks, and that enough Covid-19 measures were in place to allow the remaining two mechanical and critical work fronts to be resumed.
Remaining work fronts
The remaining two mechanical work fronts were the GAC inlet and outlet galleries, and the modifications required to the intermediate pumping station. These work fronts had to be completed before any benefit of the capital investment could be realised and had to be achieved given a backdrop of what would turn out to be a summer of unprecedented high demand.
Using enhanced PPE together with other Covid-19 measures, work could recommence on both the GAC filters to completion. At the same time, commissioning of the sludge treatment zone was restarted and was put into operation to enable the treatment of backwash water from the existing works as well as all the backwash water from the new RGF and the GAC filters that was being generated by the fine removal process.
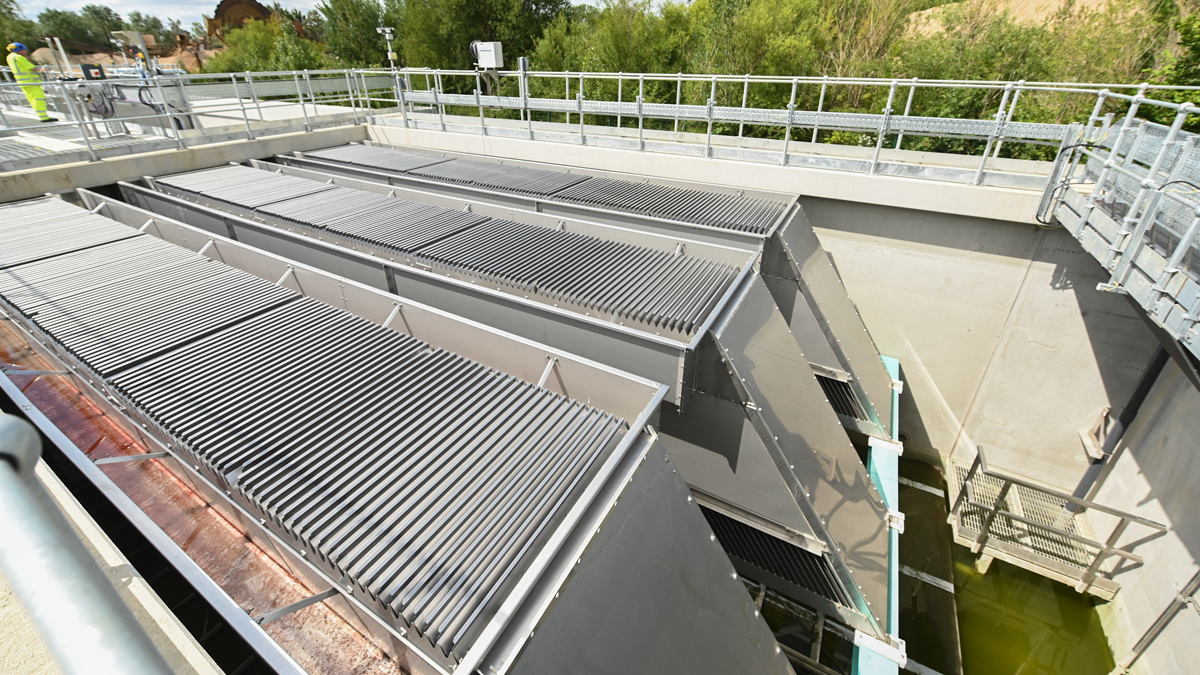
Clarifier lamella plates – Courtesy of South East Water
The introduction of the sludge zone was a significant moment as it generated efficiencies in the production process as well provided an increase resilience in the water treatment works.
Another significant moment was the introduction of the new clean backwash tank and associated backwashing equipment which allowed all the site existing and new filters to be backwashed in cycle which in turn allowed the existing pumps to be removed from the intermediate pumping station. This led to process improvements both in the GAC filters and the disinfection process. This in turn allowed the new intermediate pumps to be installed into the wet well allowing the additional 23Ml/d to be transferred onto the new pre-ozone tank and GAC filters. With all final connections made, this final piece of work completed the new treatment stream and process testing and water quality monitoring could begin.
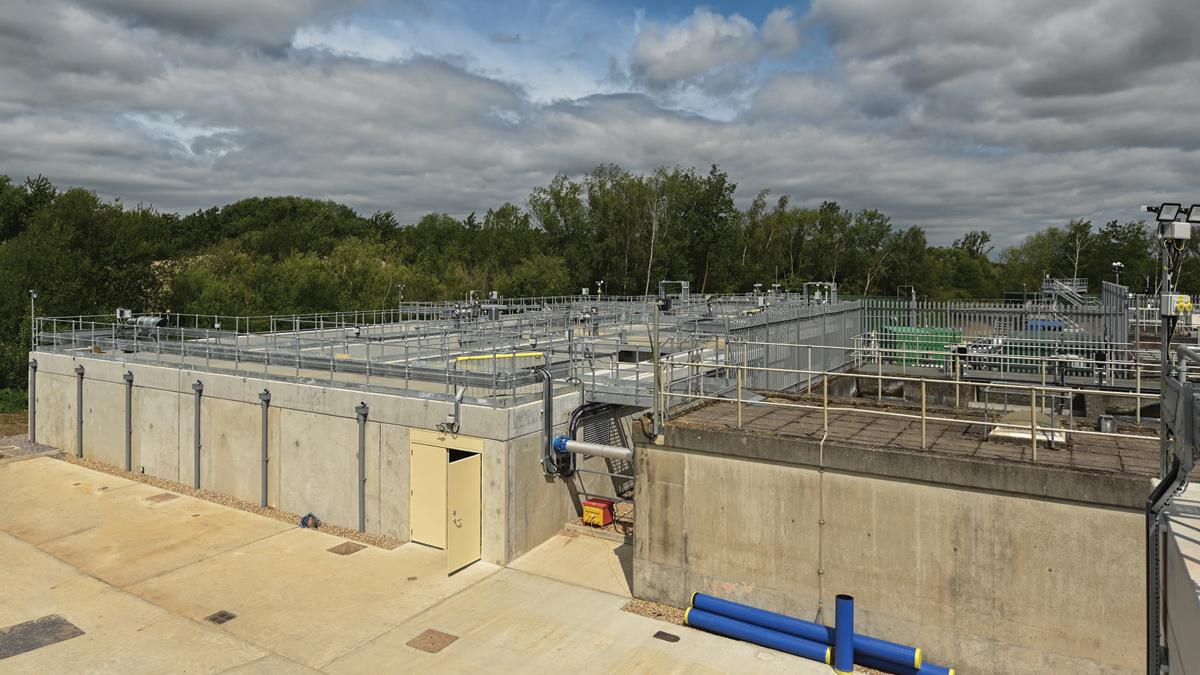
The old and new Bray Keleher WTW – Courtesy of South East Water
Process testing and water quality monitoring
At the time of writing (September 2020), flow is being passed through the flocculators, clarifiers and the RGFs to enable the water quality sample regime to begin. At the same time, water quality testing on the sludge supernatant was successfully completed allowing the supernatant to be returned to the head of the works.
Once all the above sampling has been successfully completed, treated water will be allowed to pass forward to the intermediate pumping station and then onto the GAC filters where a further sampling regime will commence. If proven successful, water from the GAC will be recombined with the existing stream just prior to the point of disinfection and full process testing, reliability checks and performance tests can begin. It is expected that this will begin in October enabling the contract to be completed in early December 2020.