Cardiff & Afan Wastewater Treatment Works (2024)
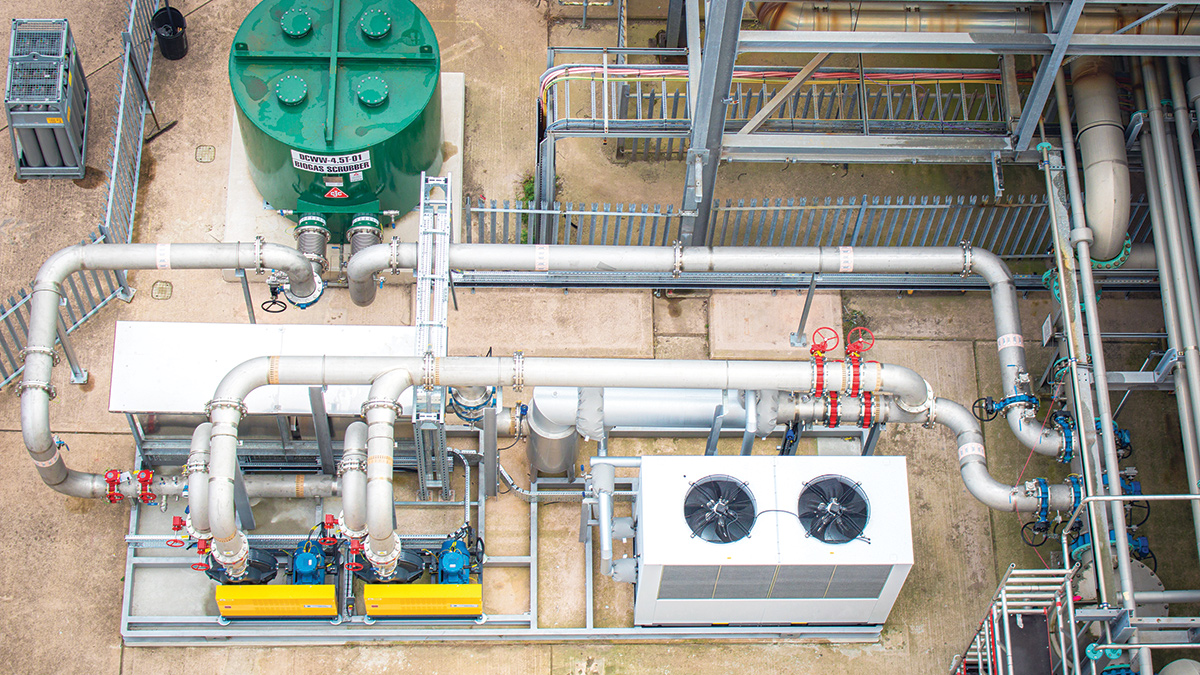
Carbon scrubber and biogas booster set skid at Cardiff WwTW - Courtesy of Morgan Sindall
Cardiff and Afan WwTWs are in South Wales and are owned and operated by Dŵr Cymru Welsh Water. The Cardiff WwTW serves a population equivalent of 974,869 with a flow to full treatment of 6,060 l/s, and Afan WwTW located on the TATA Steelworks site at Port Talbot, has a flow to full treatment of 2,423 l/s – a combined flow capable of filling an Olympic size swimming pool in just five minutes. At both sites, surplus activated sludge is pumped to a sludge treatment building where it is mixed with polymer, thickened, and then pumped (along with imported sludge) to a Cambi advanced aerobic digestion (AAD) process for further treatment. Methane produced in the Cambi AAD is used in the CHP engines to produce electricity.
Background
The CHP plants at both Cardiff and Afan treatment works were constructed in 2010, however the CHPs and associated ancillary assets at both sites face continued degradation, exposing Operations to volatile energy prices and increased maintenance costs. These assets are not currently performing to their designed capability, meaning the potential energy recovery savings are not being fully realised.
Samples of the biogas entering the CHPs have highlighted that the siloxane composition is at unacceptable levels, causing a risk to the CHP condition. The scope will include for replacing the existing siloxane plant with a new carbon filter which will increase delivered pressure of biogas to the CHPs and boilers to help increase performance.
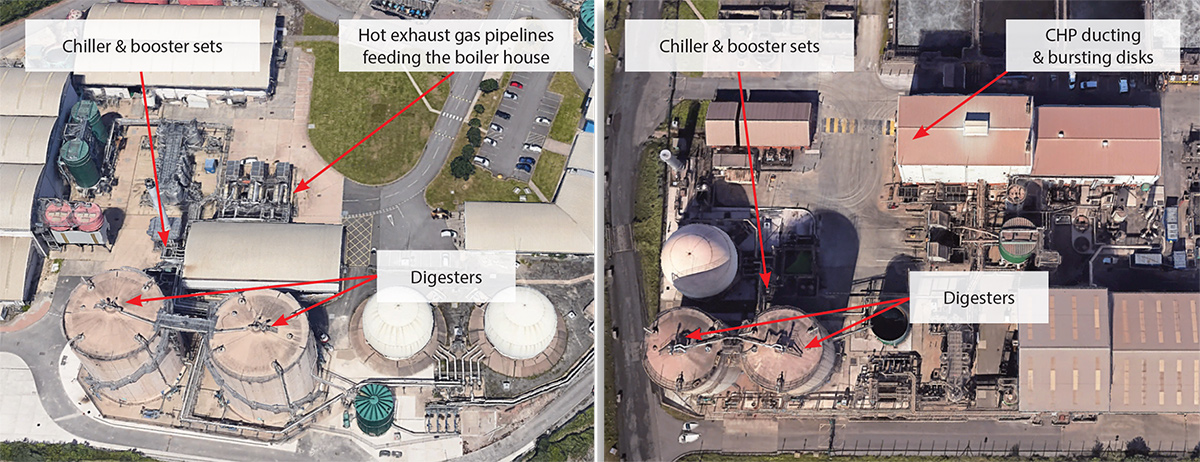
(left) Cardiff WwTW and (right) Afan WwTW – Courtesy of Google Earth
Project drivers
Morgan Sindall Infrastructure was appointed as principal contractor and principal designer to successfully deliver a scope of work at both sites to meet the following main drivers for the project:
- Increased CHP plant availability.
- Ability to run all CHP engines and boilers while using the gas clean-up equipment.
- Operational health & safety: the ability to work safely on boilers while the associated CHP boiler is running.
- Reduce energy and maintenance costs.
- Operational health & safety at Afan WwTW: relocate the CHP exhaust bursting discs to outside of the operational building.
Being one of the designers working for Morgan Sindall Infrastructure on Welsh Water’s AMP7 framework, and because of their previous experience on similar projects, Arcadis were selected by Morgan Sindall as the design consultants for the Cardiff and Afan WwTWs CHP Optimisation Project.
Due to the commonality between the two sites, both projects were developed using the same principal contractor, design consultants, sub-contractors, and supply chain. This helped realise significant design and programme savings across the two sites.
CHP process description
For both sites, at each CHP engine the hot exhaust gases are directed to a dedicated composite steam boiler to recover heat. Each CHP package includes a biogas booster pump which is used to increase the pressure of the biogas supplied to the CHP engine.
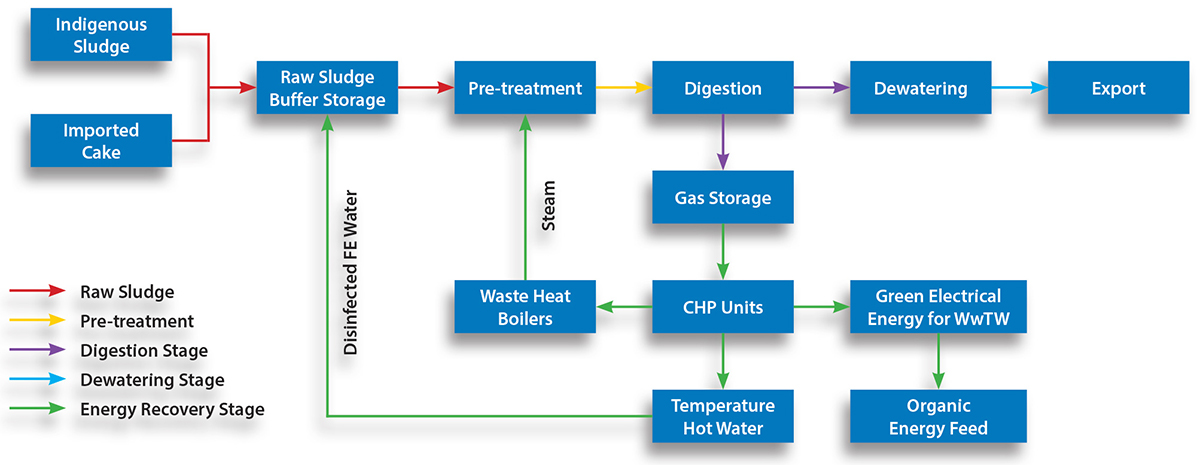
ADD process diagram – Courtesy of Dŵr Cymru Welsh Water
The pipework from the biogas booster pump to the container includes connections for a gas analyser and an in-line gas meter, as well as a safety slam-shut valve. The gas analyser monitors the levels of methane, carbon dioxide, oxygen, and hydrogen sulphide in the biogas. The readings are used by the CHP control system to adjust the engine performance, or to trip on high levels. The in-line gas meter monitors the flow rate of biogas to each CHP engine and the gas slam-shut valve is used to isolate the container in the event of a gas leak or fire alarm.
Design solution for both sites
- Removal of siloxane plant and installation of carbon gas cleaning.
- Chiller installation to include:
- Shell and tube heat exchanger.
- Recuperator.
- Lagging to exchanger and recuperator.
- Inlet and outlet temperature probes.
- Condensate pot (drained locally).
- Parker WFB2380CSB3180A-316 biogas cooler/separator.
- Parker ICE183B4003501P15FF0LA000 biogas process chiller.
- Parker HDF220BE biogas float drains.
- Gas booster to ensure boiler and combined heat and power operation, to include:
- Control panel booster and chiller with SCADA access and HMI.
- Gas booster motor 1 and 2 starters.
- VSD control.
- Pressure and temperature protection.
- Pipework and manifolds.
- Interconnecting pipework between the booster set and chiller including valves and purge points.
- Safety measures to enable a CHP to be operated and allow boiler safe isolation.
- Gas flow meter installation (on each digester).
- Afan Works only: Relocation of the CHP exhaust bursting discs to outside the existing boiler house.
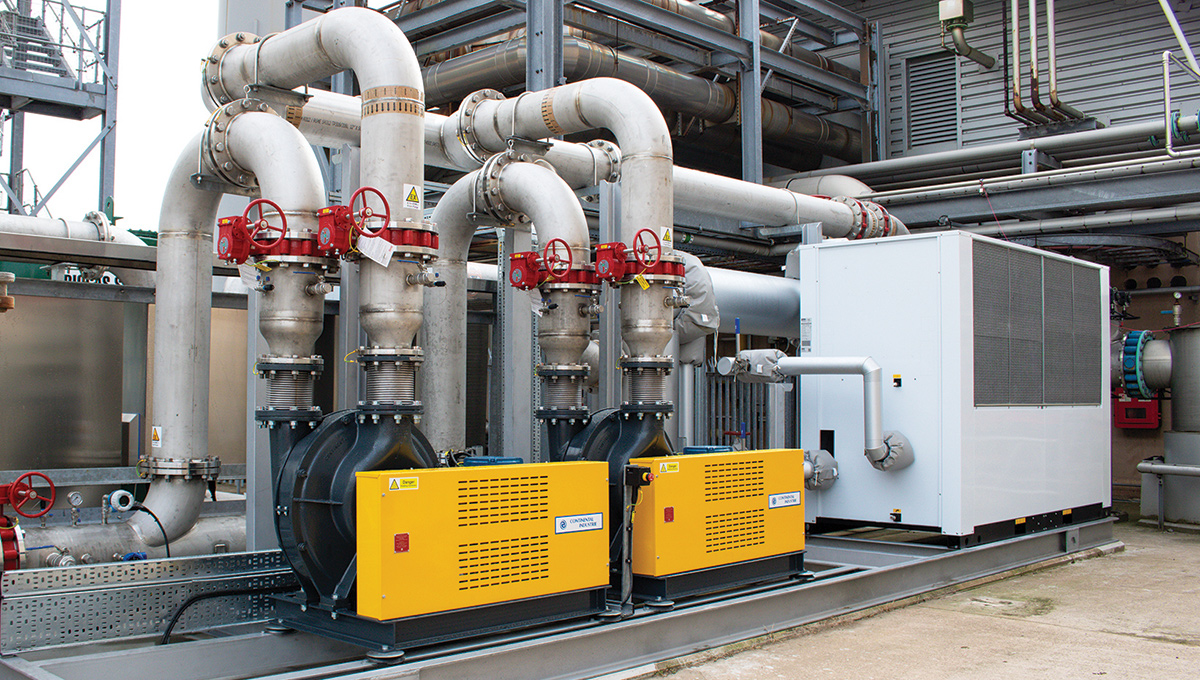
New biogas booster set install at Cardiff WwTW – courtesy of Morgan Sindall
Design figures
- Maximum biogas throughput:
- Cardiff WwTW: 3,000 Nm3/hour.
- Afan WwTW: 2,500 Nm3/hour.
- Assumed biogas composition:
- CH4/CO2/N2/O2): 65/35/0/0 %.
- Assumed biogas methane content range: 60-70%.
- Dehumidified gas temperature from chiller: 5⁰C.
- Combined siloxane level required following carbon filter treatment: 10 ppm.
Supplier selection
Early in the project it was recognised that the management of multiple key suppliers and lead-in times of up to six months were two key risks to a successful delivery. Selecting the same suppliers, contractors and designers across both projects, together with a clear collaborative approach from the start helped mitigate these risks.
- Endress+Hauser was selected as suppliers of the biogas flow meters due to their proven accuracy at a similar project completed at Five Fords WwTW in North Wales.
- CC Jensen Ltd was selected as a specialist carbon filter supplier they based on their work on previous CHP installations.
- Dunphy Combustion Ltd was selected based on their technical capabilities and previous performance at Cog Moors WwTW.
- Uniflare Group was selected based on programme delivery and the previous work undertaken at Cog Moors WwTW.
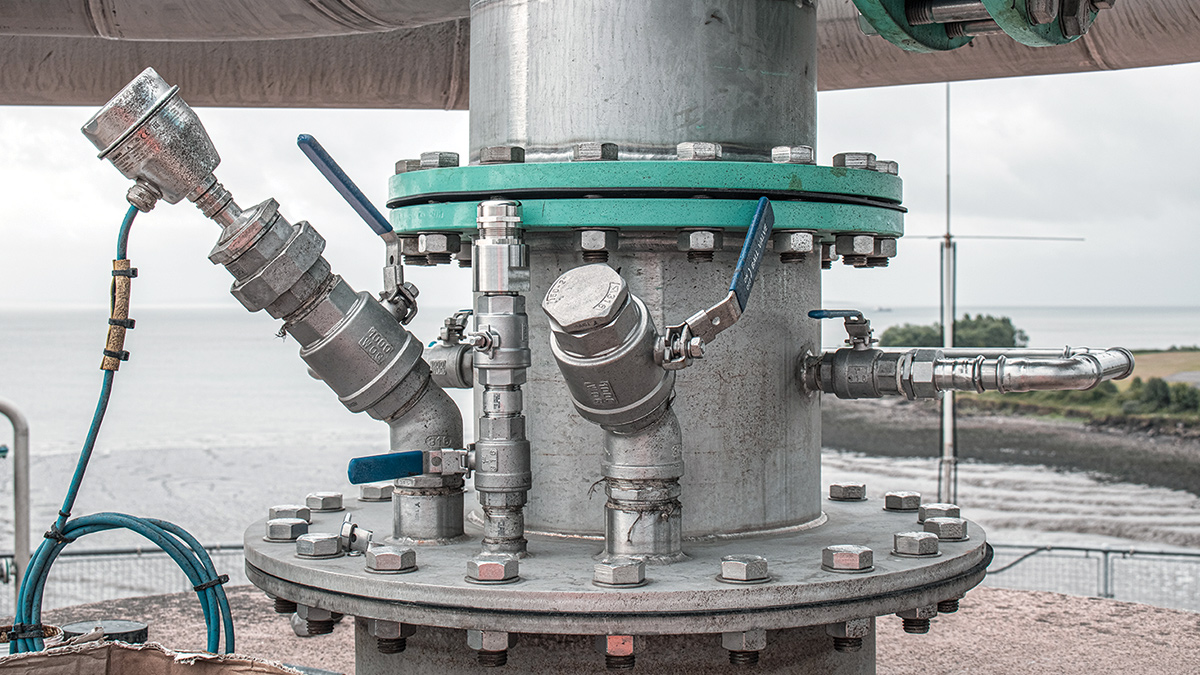
Installation of foam probe and suppression nozzles at Cardiff WwTW – Courtesy of Morgan Sindall
Cardiff & Afan CHP Optimisation: Supply chain – key participants
- Principal contractor & designer: Morgan Sindall Infrastructure
- Consulting designer: Arcadis
- Mechanical installation & biogas scrubber supplier: CC Jensen Ltd
- Electrical installer: Protocol Control Systems Ltd
- Biogas flow meter installation: Marches Biogas Ltd
- MCC modifications: GPS Group
- Systems integration: GPS Links
- Biogas boosters & chillers supplier: Uniflare Group
- Steam boiler dampers & ducting supplier: Dunphy Combustion Ltd
- Biogas flow meter & control panel: Endress+Hauser
Project benefits
As part of its response to climate change, and to reduce greenhouse gas emissions, Welsh Water have invested in a renewable energy generation and energy efficiency portfolio, split as follows:
- 45% hydro electric
- 45% Combined heat & power
- 5% wind energy
- 5% solar energy
Source: latest figures taken from dwrcymru.com – June 2024
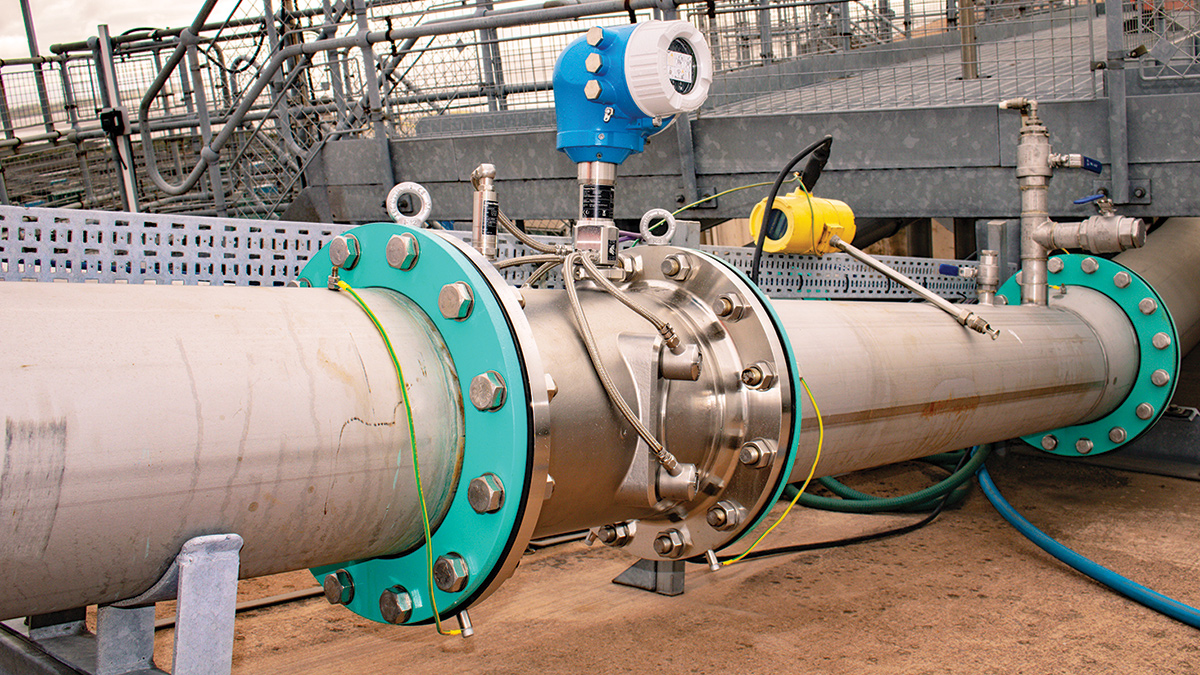
Installation of new Endress+Hauser prosonic gas flow meters at Cardiff – Courtesy of Morgan Sindall
At Cardiff WwTW, the current average power generation is 20.25 GWh, and at Afan WwTW is 10 GWh. The target to achieve a 3 GWh improvement at each site will generate a combined revenue of £930,000 per annum and contribute significantly to Welsh Water’s renewable energy totals while reducing greenhouse gas emissions. The carbon benefit is assessed to be approximately 1,000 tonnes/year for both sites combined.
Project status
At the time of writing (June 2024), both projects are progressing well, and at Cardiff WwTW the civils works are now complete. The mechanical installation is expected to be complete by the end of June, with handover back to Welsh Water targeted for August 2024.
The Afan project trails Cardiff, providing the opportunity to benefit from any lessons learnt during the Cardiff installation. The work at Afan WwTW is scheduled to be commissioned in August and handed back to the Welsh Water to operate in October 2024.
These projects will meet all the client drivers to improve operational health & safety, reduce energy and maintenance costs, and increase CHP availability and output. The carbon benefits will also contribute to Welsh Water’s overall carbon reduction strategy and journey to net zero.
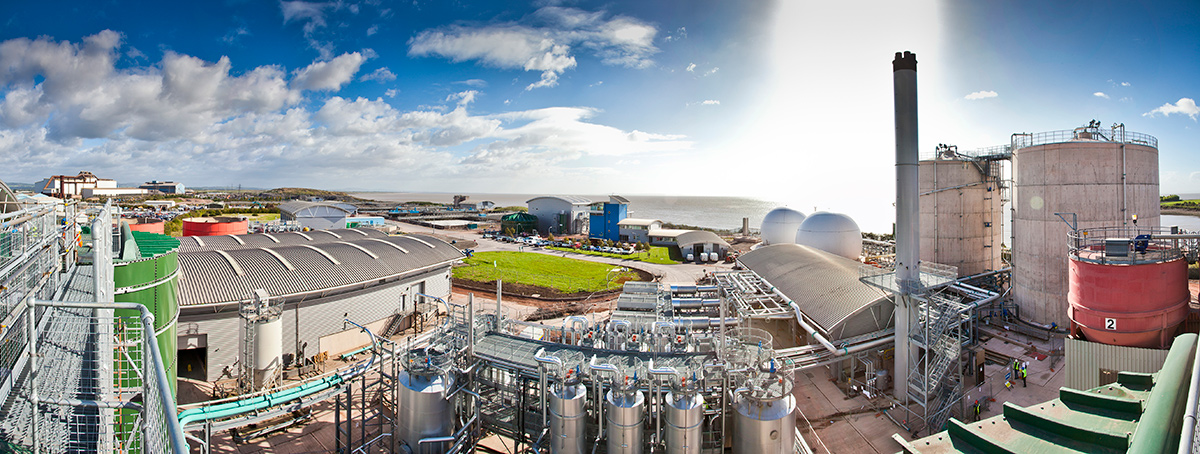
Cardiff WwTW - (left) hot exhaust gas pipeline and (right) view of digesters - Courtesy of Welsh Water