Dunphy Combustion Ltd
Burner components are designed and manufactured in materials which resist corrosion thus reducing expensive maintenance downtime. Design options also include sluice burners, retractable heads and web based software for the remote management of burners and boilers.
Our factory laboratories have facilities to test the critical fuel characteristics of recovered sewerage biogases – including key calorific variations. This data then informs the engineering design of burners and boiler shells to optimise specific site combustion efficiency.
Dunphy also specialise in the off-site manufacture of modular boiler houses for wastewater treatment sites. Our assembly hall adjacent to our main factory complex allows the construction of double tier containerised plant rooms which are delivered to site fully equipped and tested. The plant is ATEX compliant and we prepare all FDS reports, DSEAR analyses, SIL and risk assessments. Examples of our prefabricated energy centres can be seen on Thames Water, Severn Trent and Scottish Water sites – as well as municipal waste to energy locations.
Dunphy customers benefit from direct contact with our engineers through the processes of project design, equipment manufacture and testing, installation and commissioning thus by-passing the alternative, lengthy third party contractual chain. Our customers include:
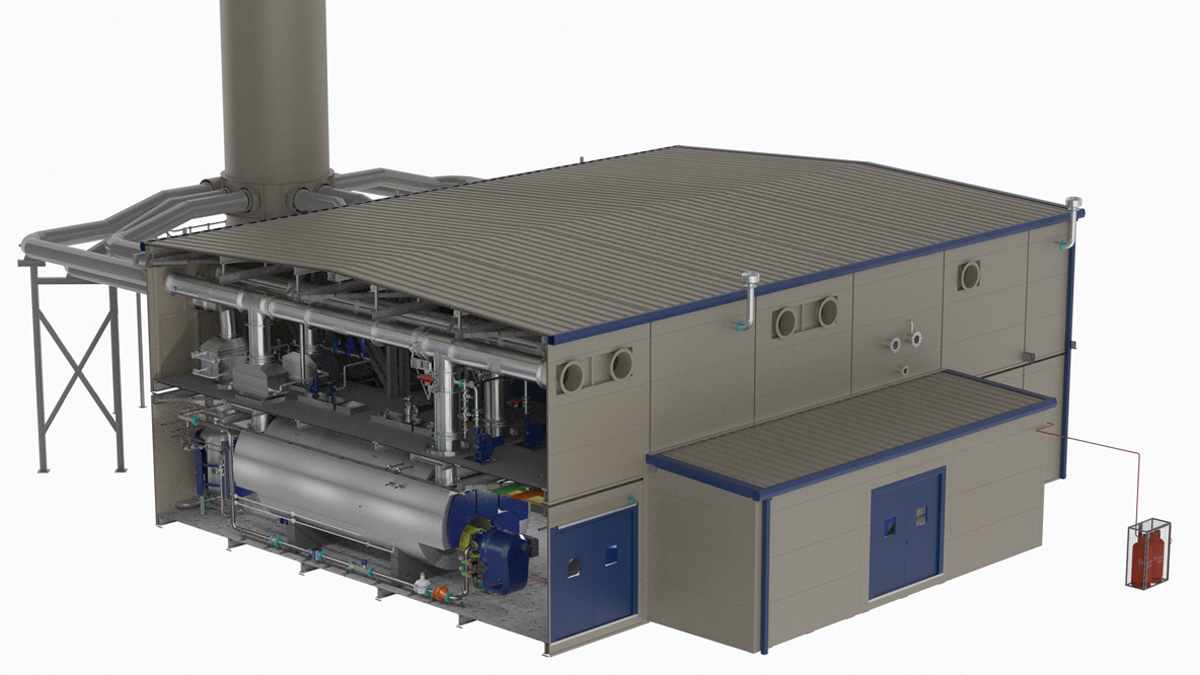
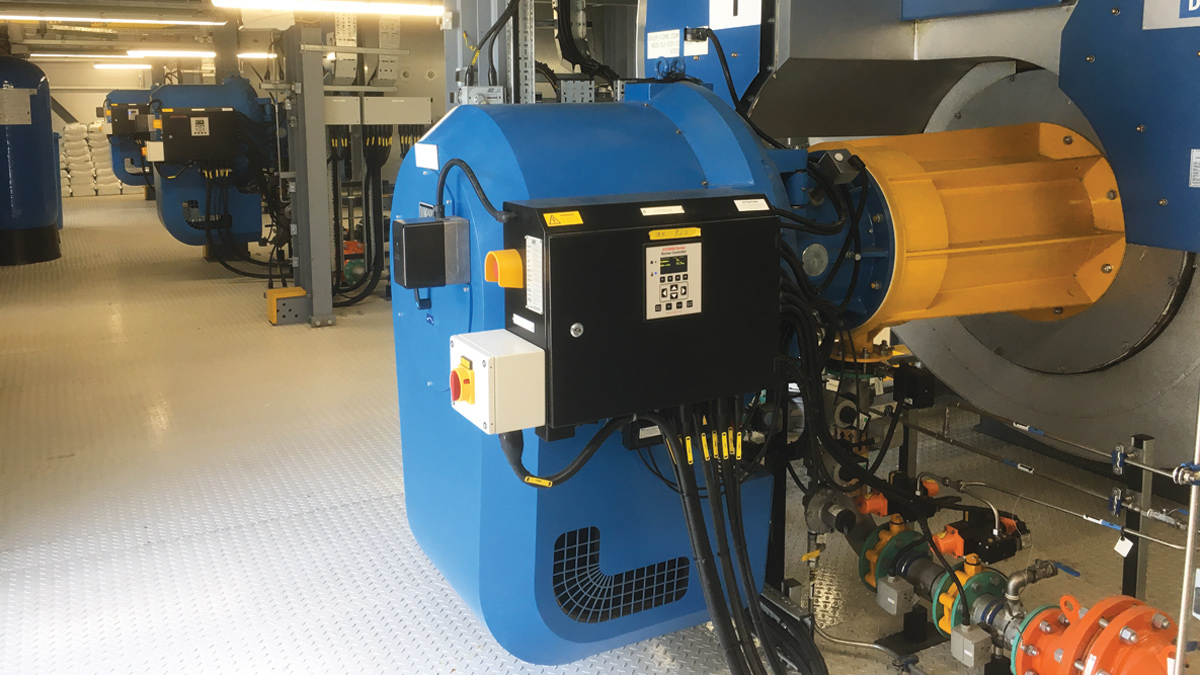
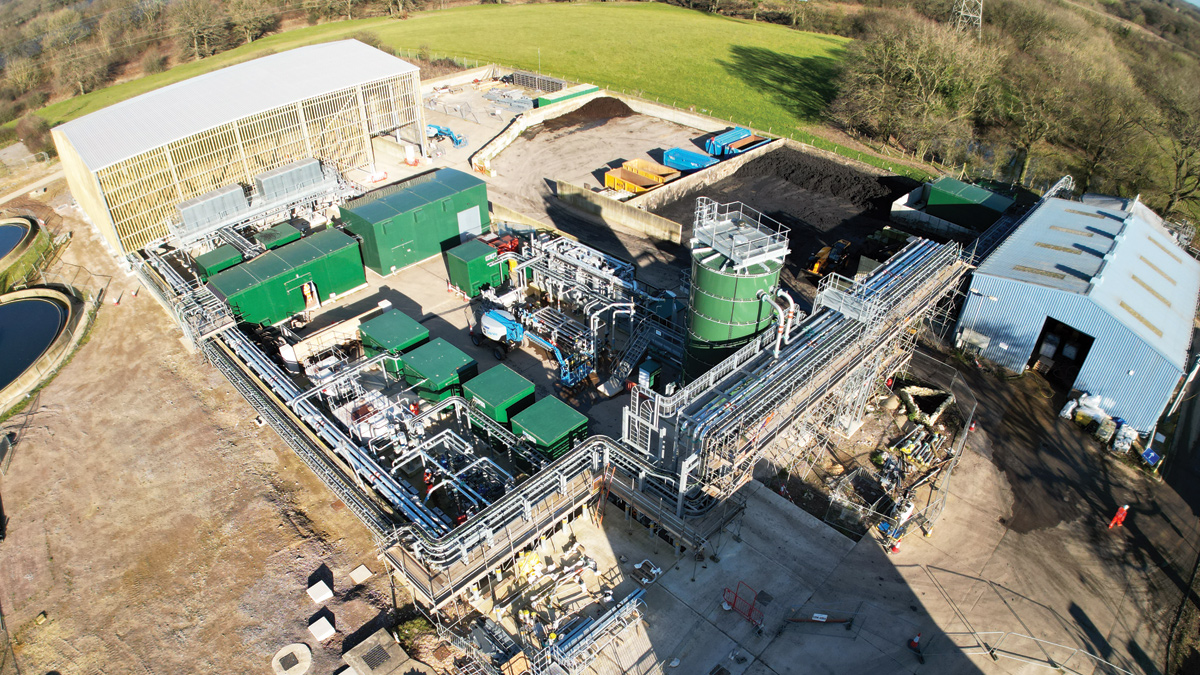
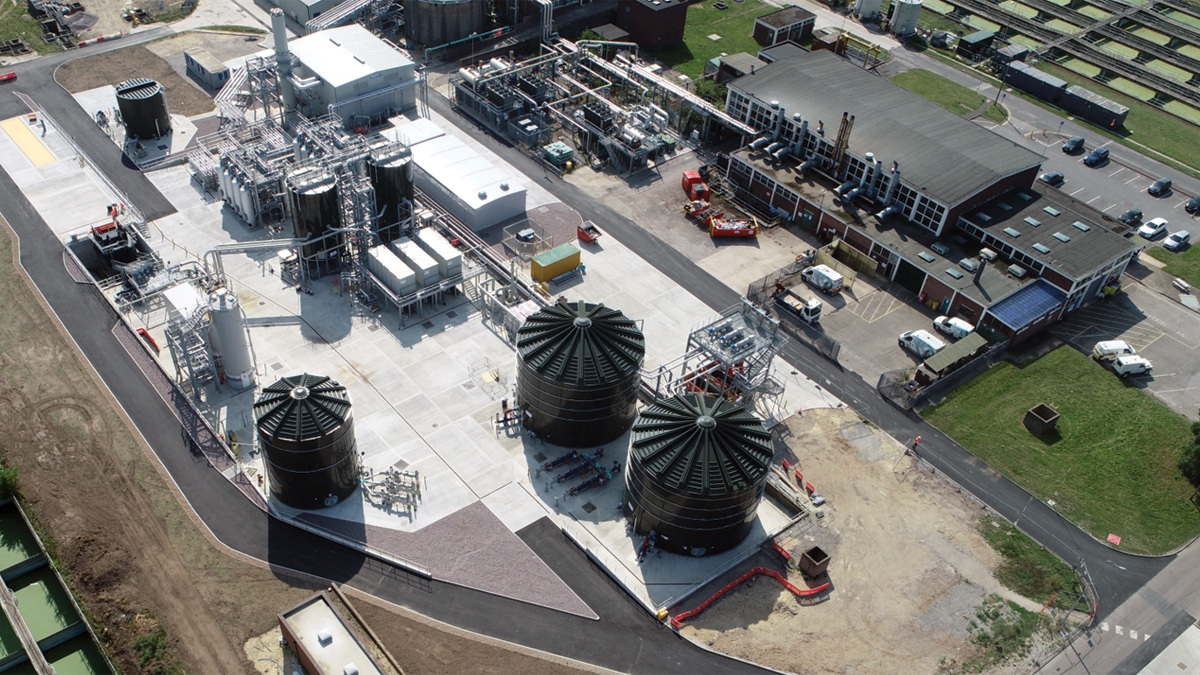
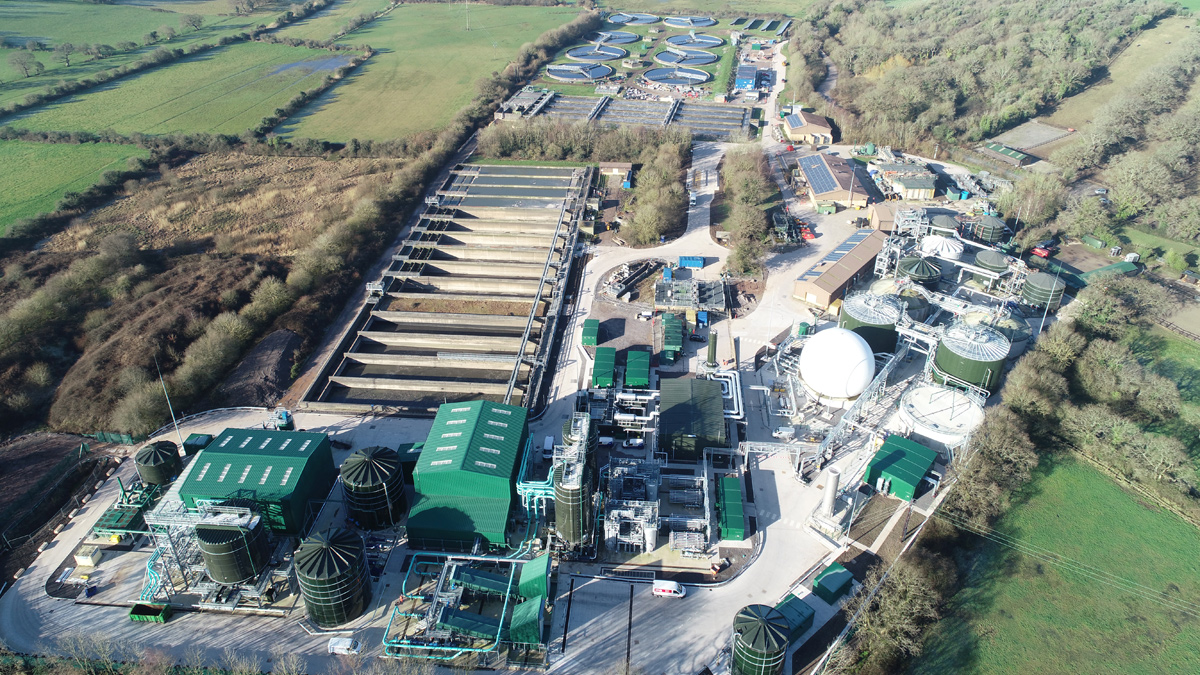
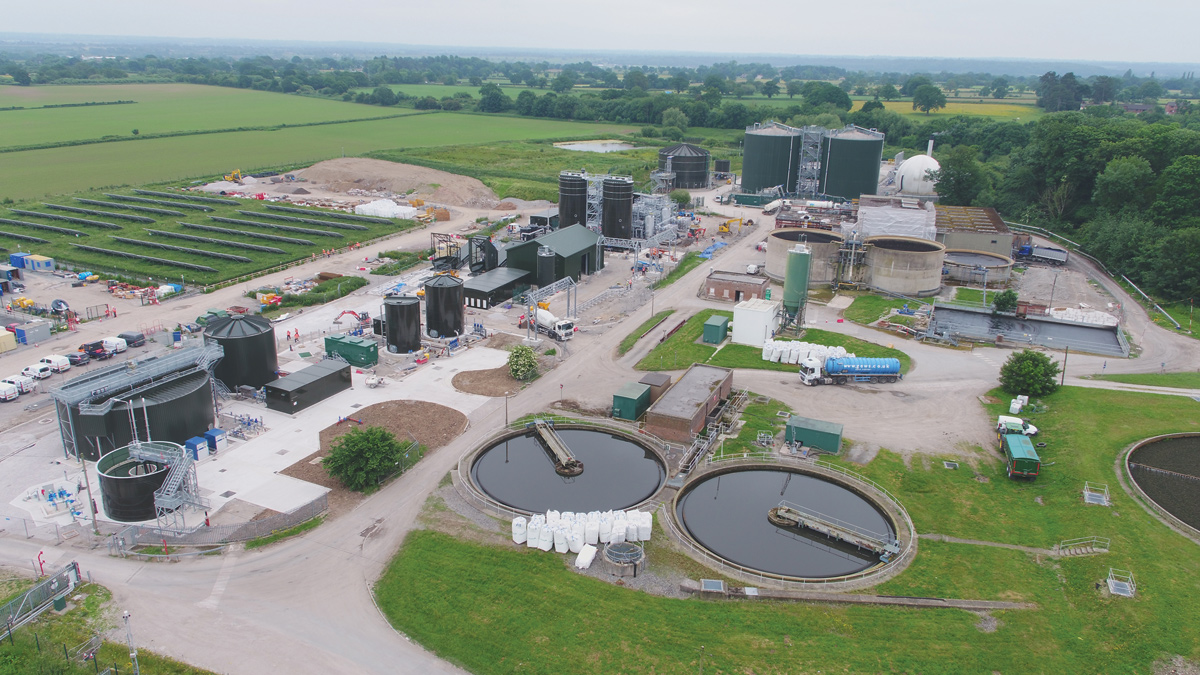
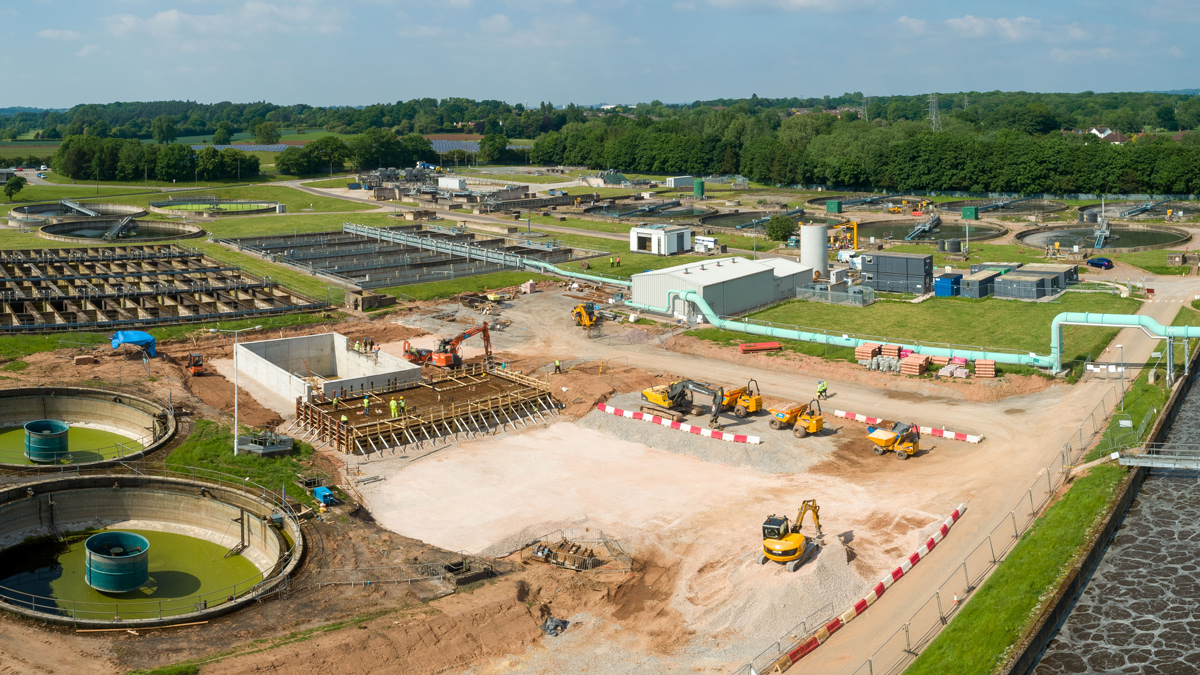
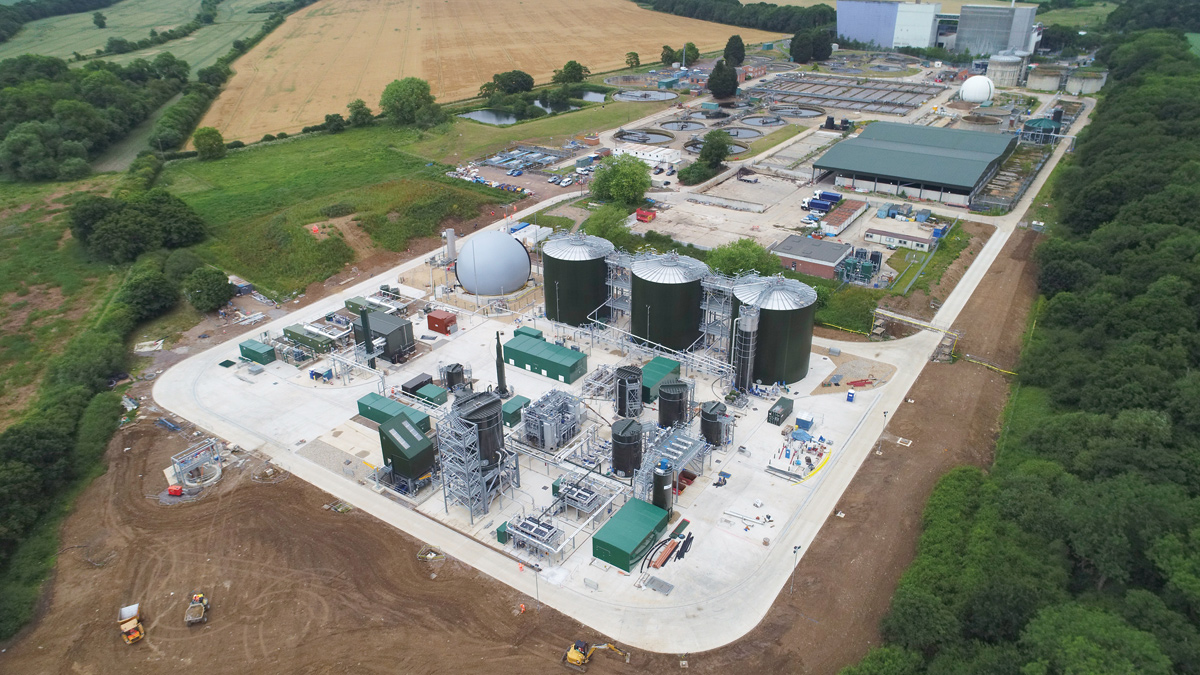

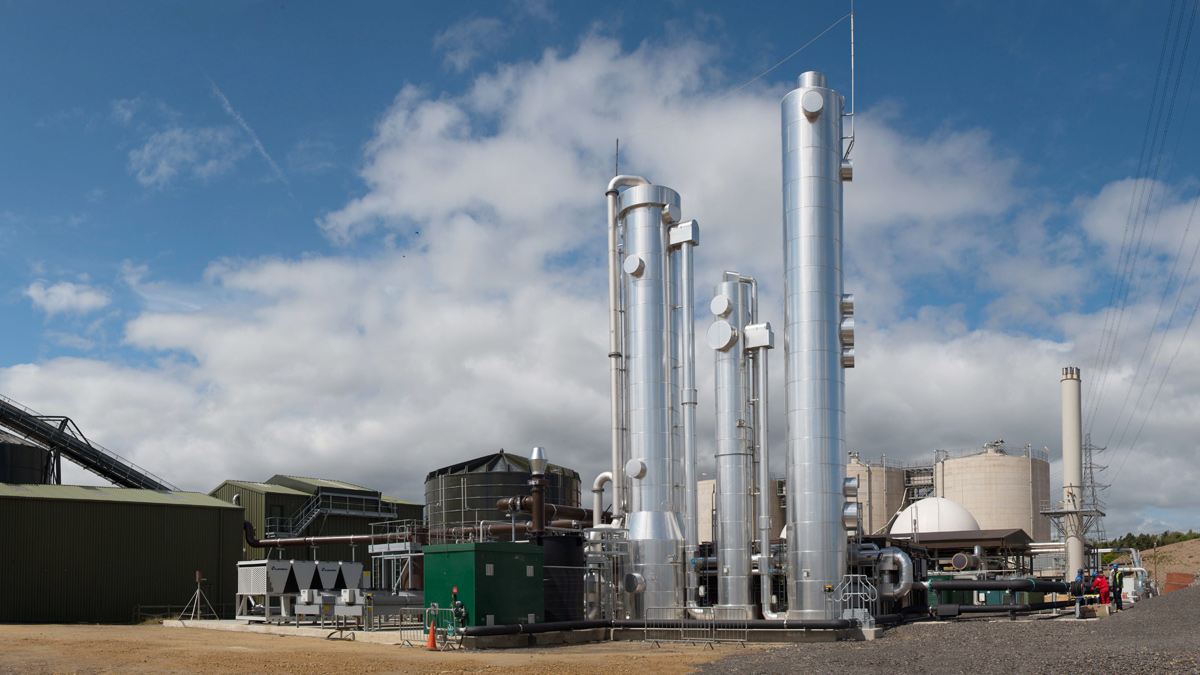