Davyhulme Biomethane Utilisation Project (2016)
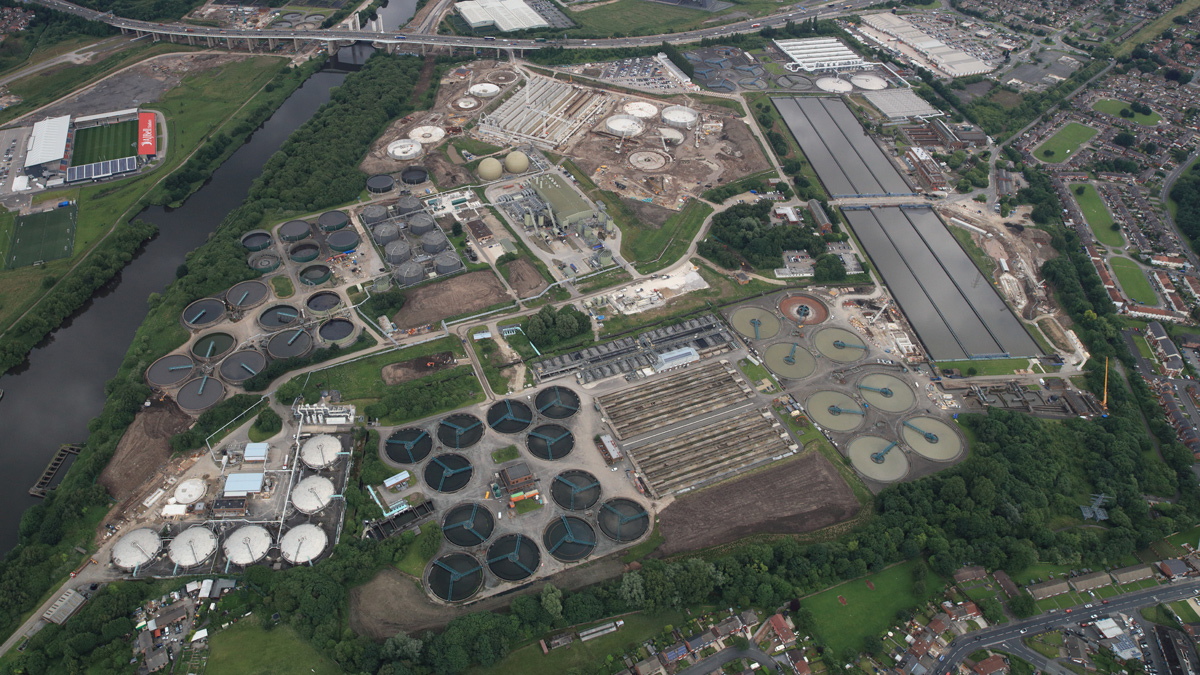
Davyhulme WwTW - Courtesy of United Utilities
Davyhulme WwTW is the location for United Utilities’ sludge balanced asset programme (SBAP) facility. This centralised treatment hub for sludge processes all of the indigenous sludge from Davyhulme which serves over one million people along with sludge imports from other United Utilities WwTWs. The centralisation of sludge treatment at Davyhulme has taken place through a strategic programme of works which led to development of the SBAP. This centre processes both liquid and cake sludge using thermal hydrolysis and digestion to produce an enhanced digestate. Prior to March 2016, the biogas generated from digestion has been used to fuel combined heat and power (CHP) engines and steam boilers to provide electricity, steam and hot water for the SBAP and wastewater operations at Davyhulme.
Introduction
The SBAP facility has the capacity to process over 90,000 tonnes (dry solids) of sludge per annum. The biogas generated from the digestion of this sludge enables electricity generation of over 8MWe with sufficient steam and hot water to meet the thermal needs of the site.
Integrated heat and power delivery to maximise the value from sludge processing is central to our approach to meeting our core value of maximising benefits to improve our services to Customers. Therefore, through on-going optimisation activities, the opportunity to integrate biomethane production into the SBAP is the next piece in the jigsaw to deliver further benefit.
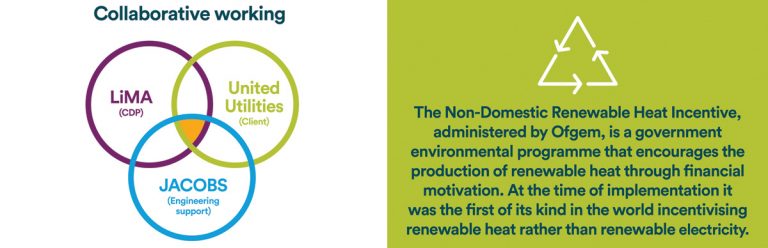
(left) Collaborative working between client, engineering support and contractor and (right) short explanation of renewable heat incentive for biomethane – Courtesy of United Utilities
Team
The approach adopted for project delivery was to form a working partnership between United Utilities, Jacobs Engineering and LiMA (a Laing O’Rourke and Atkins partnership.) This partnership was the cornerstone to delivering the project successfully within a condensed timescales. Early contractor engagement facilitated development of a joint engineering, construction and commercial team from across both client and contractor organisations.
Key to ensuring delivery in a short timescale, a number of project acceleration techniques were employed to successfully decrease the definition and implementation phase. This enabled the project to progress from the initial project kick off meeting with the joint team, to start on site within 4 months. During this time, the team worked collaboratively to bring together the required design, construction and operational knowledge needed to effectively plan for success.
A robust governance structure was established early in the definition stage to guarantee senior sponsorship support. This allowed any issue to be escalated and resolved in real time which proved crucial in protecting the schedule.
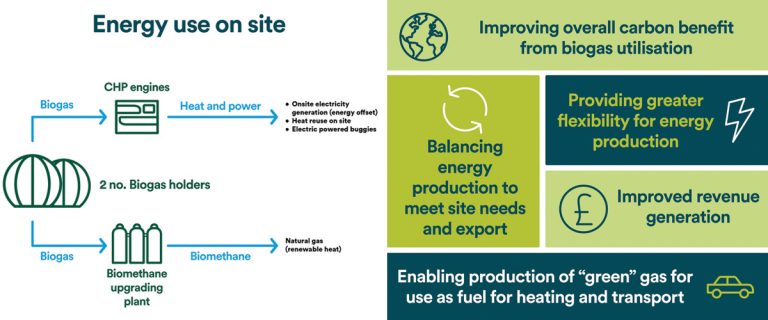
Energy use on site
Biomethane concept and definition
The concept phase for the project was undertaken in early 2015 and defined a critical path for delivery. Central to this was the need to align delivery with the Government incentive for biomethane production which is through the Renewable Heat Incentive (RHI). The RHI is the mechanism introduced by the Government to stimulate development of renewable heat projects which includes producing biomethane and injecting this into the natural gas supply network.
The development of the project requirements in the first quarter of 2015 defined success as having the biomethane plant commissioned by end of March 2016. This led to developing an accelerated programme of work to take the project through to completion in less than twelve months.
United Utilities and Jacobs Engineering identified that early collaboration with Laing O’Rourke, with their previous experience of delivering biomethane projects, was key to delivering a fit for purpose asset in the tight time scales required. Joint development of the project through to contract award was undertaken to accelerate this phase of works and establish a collaborative partnership with fully aligned objectives.
The sponsorship and delivery of the projects required a number of external stakeholders to agree on the biomethane solution. Our approach allowed these stakeholders to become an extension of the core project delivery team. These stakeholders included:
- Entering into early engagement and collaboration with National Grid to agree on operating principles and methods for on-site operation as well as the connection to the natural gas network.
- Working with the Environment Agency was imperative to delivering a project that delivers environmental benefit and ensuring continuous compliance to support the accelerated delivery.
- Trafford Borough Council who supported the project planning request and its delivery including highway works in early 2016.
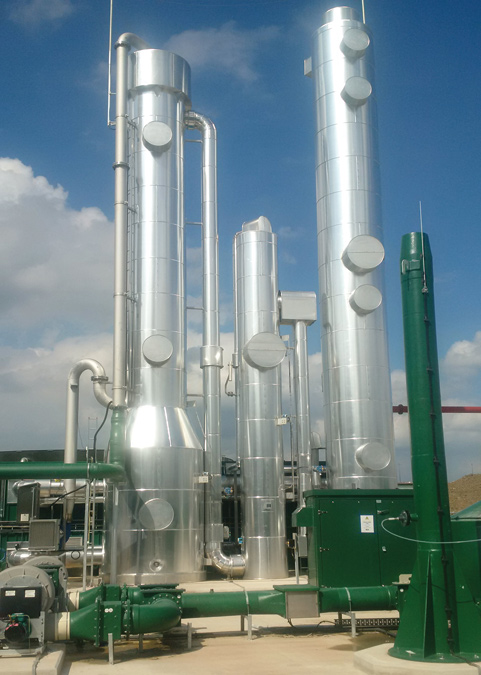
Malmberg wash water plant scrubs the biogas – Courtesy of United Utilities
Alongside the above the most important stakeholder are the local residents to the Works and communication providing detail of the project its value to customers and explaining the benefits and impacts of temporary work was a central activity.
Achieving the project outcomes would not have been possible without the complete buy-in and support from the above parties.
Technology selection, construction and commissioning
The biomethane plant delivered at Davyhulme is only the 5th facility in the UK processing biogas derived from sewage sludge. Therefore, a key consideration was utilising robust core technologies. The biogas upgrading technology (BUG) selected is the Malmberg GR09 and the grid entry unit (GEU) is a bespoke Elster design especially commissioned for the Davyhulme project.
The Malmberg BUG facility ‘washes’ the biogas to remove carbon dioxide and other trace components to provide a methane rich product gas. This is then analysed and propane added to meet the specification for supply to National Grid.

ERG odour control unit to ensure no detriment to Davyhulme WwTW – Courtesy of United Utilities
The process employed to produce biomethane to meet National Grid’s specification comprised:
- Pre-treatment of the biogas through dehumidification and removal of bulk contaminates using activated carbon.
- Malmberg BUG unit which pressurises the biogas and then washes this to remove carbon dioxide (CO2) and hydrogen sulphide (H2S). The off-gas from this process is treated to move the H2S prior to release to the environment.
- The purified methane rich gas exiting the Malmberg facility is then passed to ‘polishing’ units containing activated carbon to remove any final contaminates.
- The biomethane is then analysed to confirm its composition and calorific value with propane enrichment before being supplied via a dedicated pipeline to connect to the National Grid supply infrastructure.
Delivering the overall facility was based on a modular Design for Manufacture and Assembly (DfMA) approach enabled greater concurrent working benefits, resulting in civil construction occurring with the off-site manufacture of the process units. This resulted in a short duration of M&E fit out with limited on-site assembly and enabling the project to be delivered against the tight programme and challenging schedule: The parallel delivery of the construction programme through DfMA and site activities enabled the team to successfully build the gas cleaning plant and laid over 2km of gas main through the existing Davyhulme works, delivering gas to the grid on the 24th March 2016.
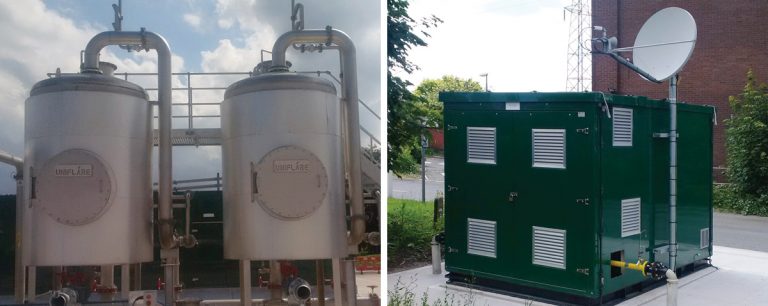
(left) Gas boosters increase the pressure to support the treatment process and (right) National Grid’s remote operated valve is linked to their Distribution Network Control Centre – Courtesy of United Utilities
The off-site manufacture of the process units helped mitigate the risk associated with constructing such a complex system on a busy live site. This contributed to an excellent health and safety record with no major health or safety incidents despite the complexity of the project.
Outcomes
The integration of biomethane production to Davyhulme’s SBAP is enabling the following:
- Improved revenue generation.
- Improving overall carbon benefit from biogas utilisation.
- Providing greater flexibility for energy production.
- Balancing energy production to meet site needs and export.
- Enabling production of “green” gas for use as fuel for heating and transport.
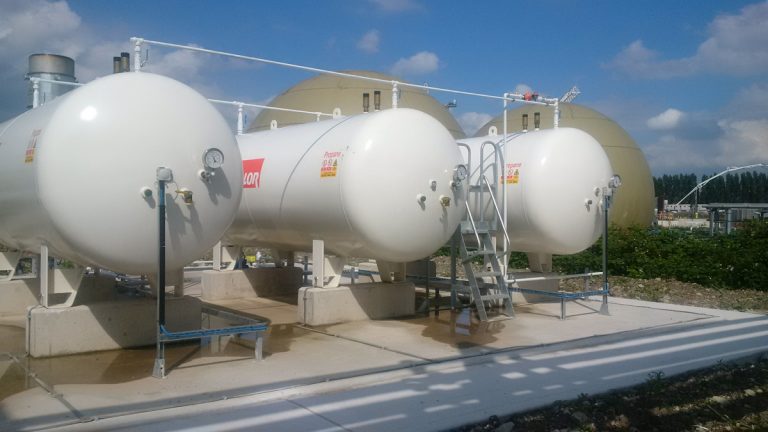
Calor Gas Propane tanks dose the biomethane to a set calorific value – Courtesy of United Utilities
The above benefits means that we are now in a position to improve our overall site operations our delivering lowest sustainable cost for treatment.