Exmouth Offshore Project (2024)
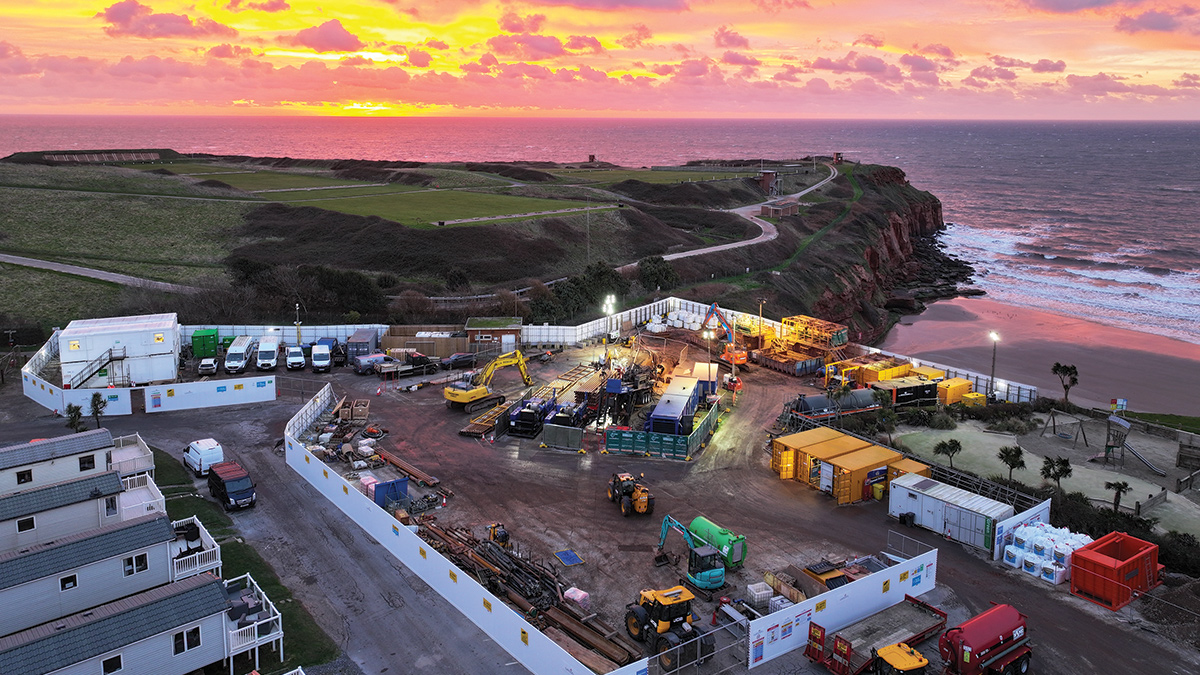
View of the works compound with the 500 T drilling rig - Courtesy of South West Water
The Exmouth Offshore Project is a key element of the wider Exmouth programme of works to deliver no more than 10 significant (>50m3) spills per annum from the aggregation of Maer Road Sewage Pumping Station (SPS) Combined Sewer Overflow (CSO) and Phear Park SPS CSO. The output from the programme will reduce spill frequencies for better environmental conditions as a long-term solution with a positive impact on the bathing waters. The works were undertaken in Sandy Bay Devon Cliff Holiday Park in Exmouth and was delivered around Sandy Bay’s winter maintenance window, compressing 15,000 working hours within just 13 weeks. Overrunning the programme would have directly impacted Sandy Bay’s tourist season, with significant revenue loss (approximately £2m/day). The works were located only 4 meters from a Blue Flag beach.
Introduction & background
The Exmouth Offshore Project required the installation of an 804m long, 900mm diameter, gravity long sea outfall, to achieve an increased flow rate of 991 litres per second.
The works took place in Sandy Bay Devon Cliff Holiday Park (Exmouth), one of the UK’s largest caravan sites, with over 2200 units and 10,000 visitors per week in the summer season and were only permitted during the Sandy Bay winter maintenance period.
South West Water contracted Galliford Try as principal designer and contractor for the project.
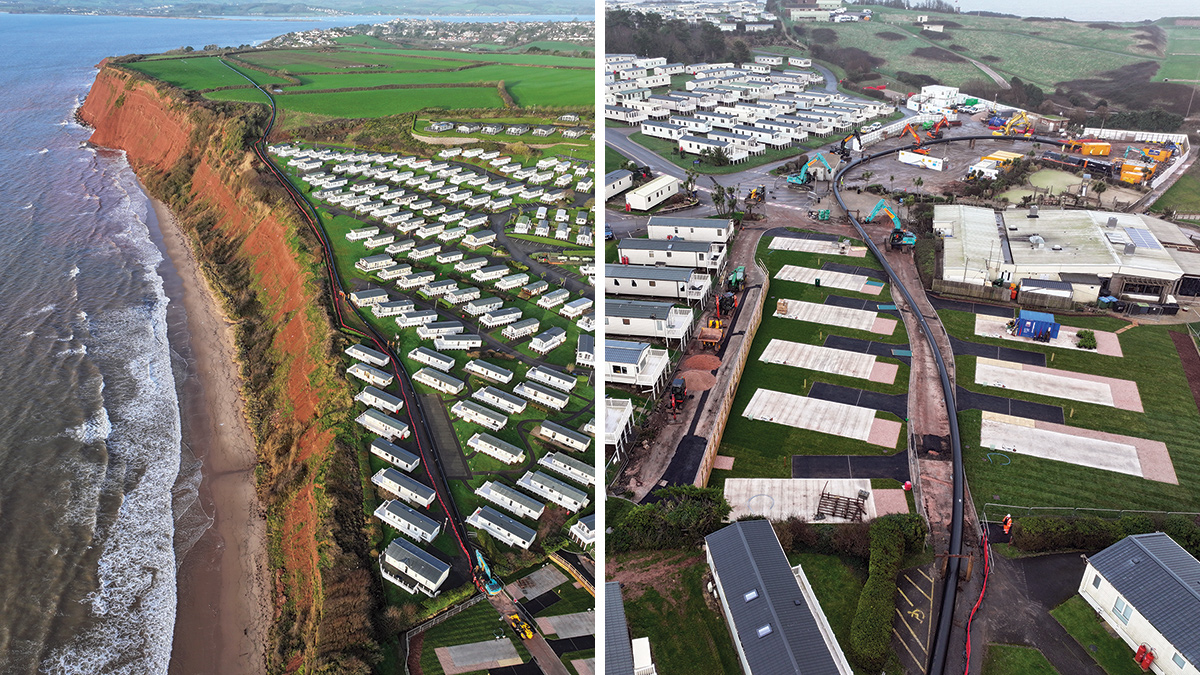
(left) Pipe string along coastal path and (right) Pushing pipe lower car park and compound – Courtesy of South West Water
Construction
To meet this challenging programme, specialist horizontal directional drilling (HDD) contractor Peter McCormack & Sons mobilised one of the largest and most powerful drilling rigs ever used in the UK, to complete the largest forward reaming (48”) operation in the country.
The works required 18 months of planning and the programme challenge included expediting the specialist reamers, 1.2m in diameter manufactured in America and imported to precise programme requirements. The methodology and accurate planning minimised programme risk by minimising the use of marine spread.
This relied on forward reaming (pushing the pipe from land), which is an unconventional method for the length and diameter of pipe of this scale, but reduced the reliance on marine support in winter sea conditions reducing weather risk.
Early marine trenching support was mobilised to clear boulders at the exit point at seabed over two days. Survey marine vessel continued throughout the project to confirm HDD exit point.
818m of HDPE pipe was welded on land, stretching in a single length at strategically high ground to slide the pipe. This allowed to fully pressure test the pipe to give complete confidence in the weld quality. The project team considered both the safety of the public accessing the coastal footpath adjacent to the works and maintenance operations within the holiday park with accurate interface management. In addition to this, the project team worked closely with landowners to agree a route for the welded pipeline to be positioned, in readiness for the pipe push with regular communications with landowners.
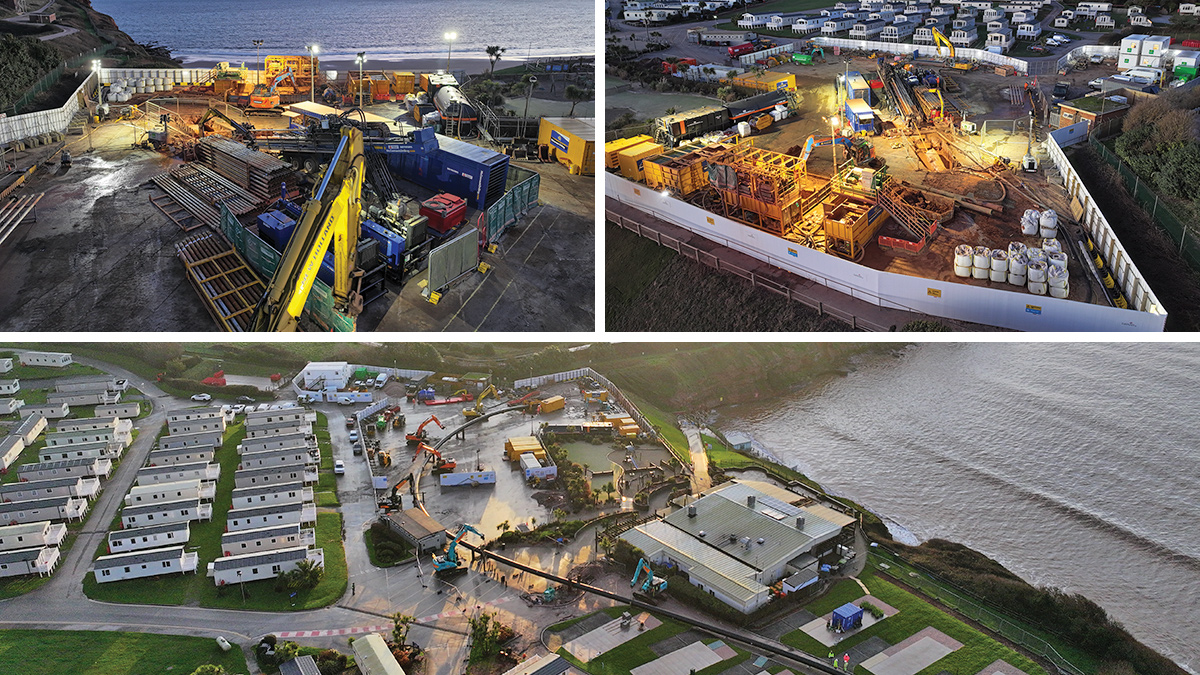
(top left) 500t drill rig compound and entry point and (bottom) pipe pushing operation at sunrise – Courtesy of South West Water
The works naturally attracted attention, and allowed the team the opportunity to explain the work that were undertaking and the long-term benefits South West Water outfall would provide to wider Exmouth storm overflow project.
The project compressed 15,000 working hours within 13 weeks which equates to 10 months of normal working hours. This could only be achieved by running a continuous 24×7 drilling operation. Despite the intensive nature of this challenge, the team completed the HDD works ahead of programme, on budget with zero harm to the team, zero pollution incident, and minimal impact to the public. This pipe is a wider part of Exmouth stream of works including storm overflows to achieve long term goal.
Exmouth Outfall: Supply chain – key participants
- Client: South West Water
- Principal contractor: Galliford Try
- Design: Pell Frischmann
- Design of outfall route & drilling specialist/sub-contractor: Peter McCormack & Sons Ltd
- Topographic, GPR & boreholes: AGS Ground Solutions
- Unexploded ordnance survey report: 1st Line Defence
- 900MM PE pipe supplier: Egeplast international GmbH (Germany)
- HDD 500t kit & drilling tools: American Augers (USA)
- Pipe pusher: VanLeewen Trenchless Technology (Netherlands)
- Welding plant supplier: Ritmo remedy 1000FA (Italy)
- Concrete: Aggregate Industries
- Welding plant operator: Pipe Force Martin Woodcock
- Fiberglass systems: Pipex px
- Crane hire: Spence Crane Hire Ltd
- Plant hire: Plantforce Rentals Ltd
- Plant: Sunbelt Rentals Ltd
- Aggregate: Steve Wills Haulage
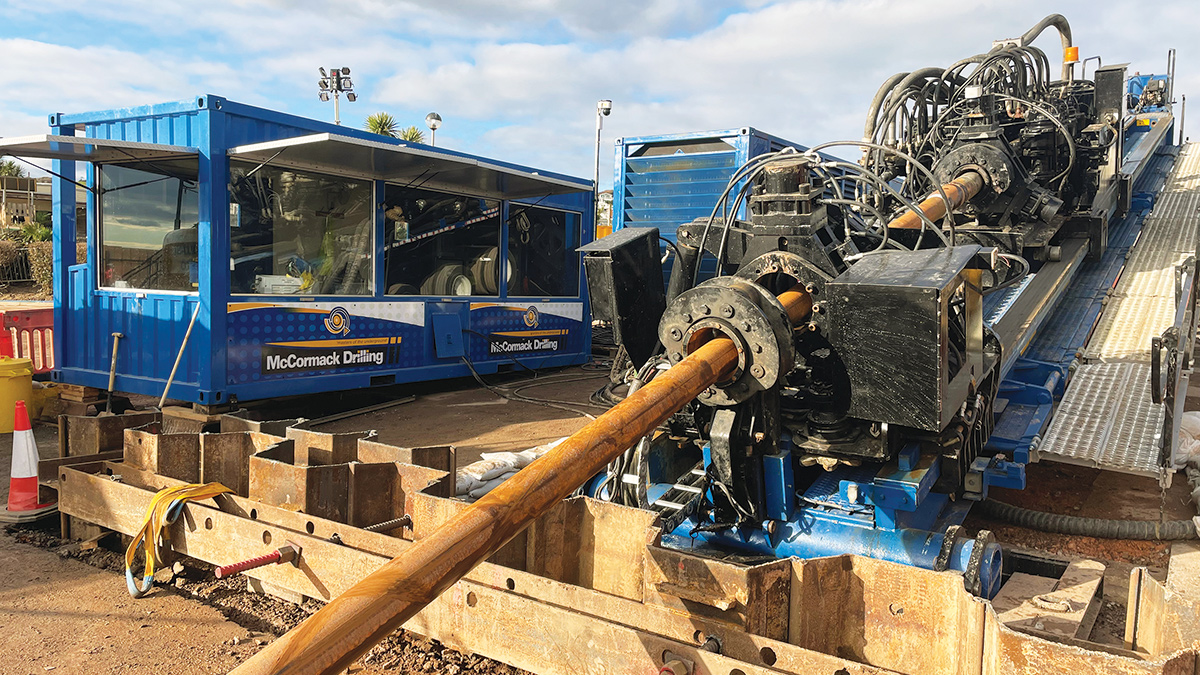
500 T drilling rig – Courtesy of Galliford Try
Teamwork and Inclusion
Working collaboratively towards a common agenda, multiple partners were involved including the pipe supplier, drillers, pipe pushers, pipe welders, crane operators, mud pump operators, water tank suppliers, fuel suppliers etc.
A mutually inclusive team worked. Collaborative teamwork environment with no risk-taking policy with a culture of everyone working on site and delivery people have same respect with different roles and responsibilities.
Cultural Behaviour Safety videos were shared on regular basis to remind site team safety, culture, and respect aspect. Site team was well trained and fully skilled to follow safety rules religiously. No one was either bigger or lower than anyone which was demonstrated by actions through a mutually inclusive respectful culture. Shift change and intermittent toolbox talks were carried out. Several graduates and other interested people were taken to site for their learning. One of the UK’s Water Plcs were visited the site for their learning.
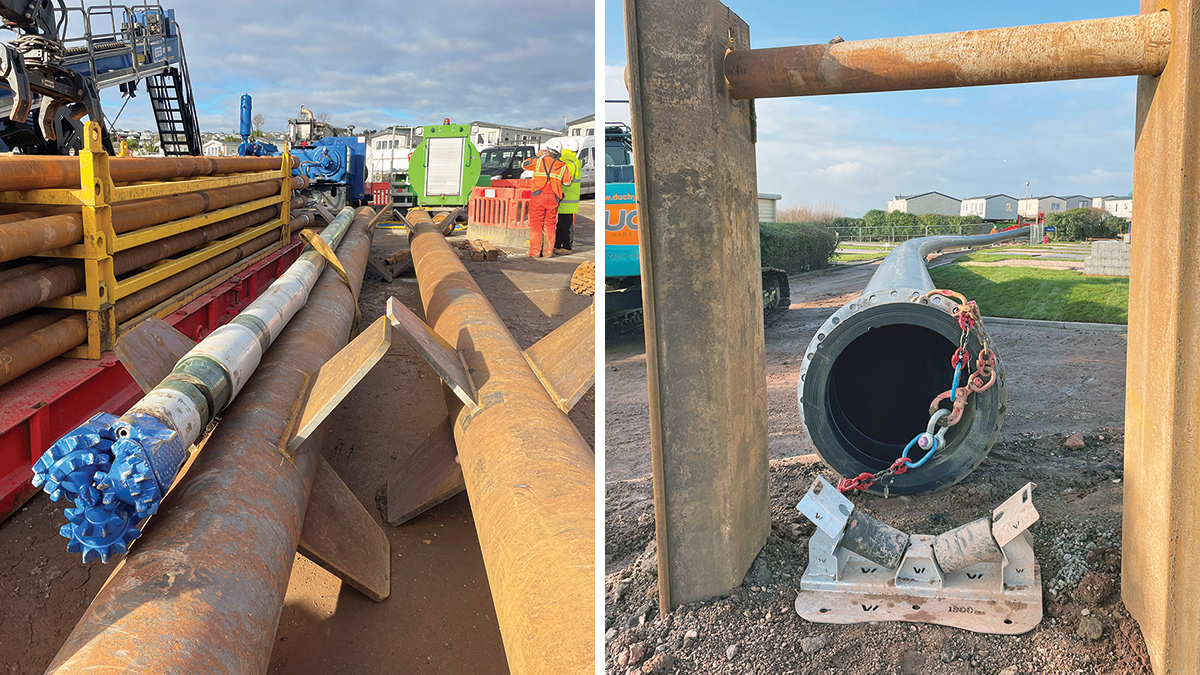
(left) Drill pipe and pilot drill bit and (right) outfall pipe, roller and guide – Courtesy of Galliford Try
Health & Safety considerations
Accurate and realistic RAMS were produced. Uninterrupted CCTV monitoring was placed. Each shift had a team of 25 highly skilled and well-trained site team with zero risk taking policy. Specific H&S steps:
- Strict one-way system with separate entry and exit points for plant and construction vehicles.
- Separate entry and exist of South West Water Operators to make existing pumping station in safe operation.
- Detailed interface management plan of each operational activity including regular on site maintenance of drilling rigs.
- An hourly check of whole plant, Noise barriers and vibration control equipment for public safety and wellbeing with fully secured fence – large visible metal sign boards and multiple laminated signs in and around the Sandy Bay for public awareness.
- On duty several field marshals to navigate foot path users. Same drilling team was kept. Compressed programme 15,000 working hours within 13 weeks. Injury free 15,000 working hours into 13 weeks. No near miss. No pollution incident.
Noise barriers and vibration control equipment was installed for the safety and benefits of local community and footpath users. This was checked daily by the site team and the environmental manager to ensure there were zero environmental and H&S incidents.
Protecting the Blue Flag beach
To protect the Blue Flag beach, the entire working area was surrounded by flood barrier to prevent drilling fluids from escaping the site to avoid any risk of pollution of sea. All drilling fluids were recycled by using a recycling centrifuge system. This sustainable innovation allowed the drilling arisings to be fully dewatered, allowing transportation of the inert material without the risk of silt on the road network, causing unnecessary nuisance to the travelling public. This initiative minimised water use and mitigated 364 lorry movements through Exmouth, saving 92T eCO2.
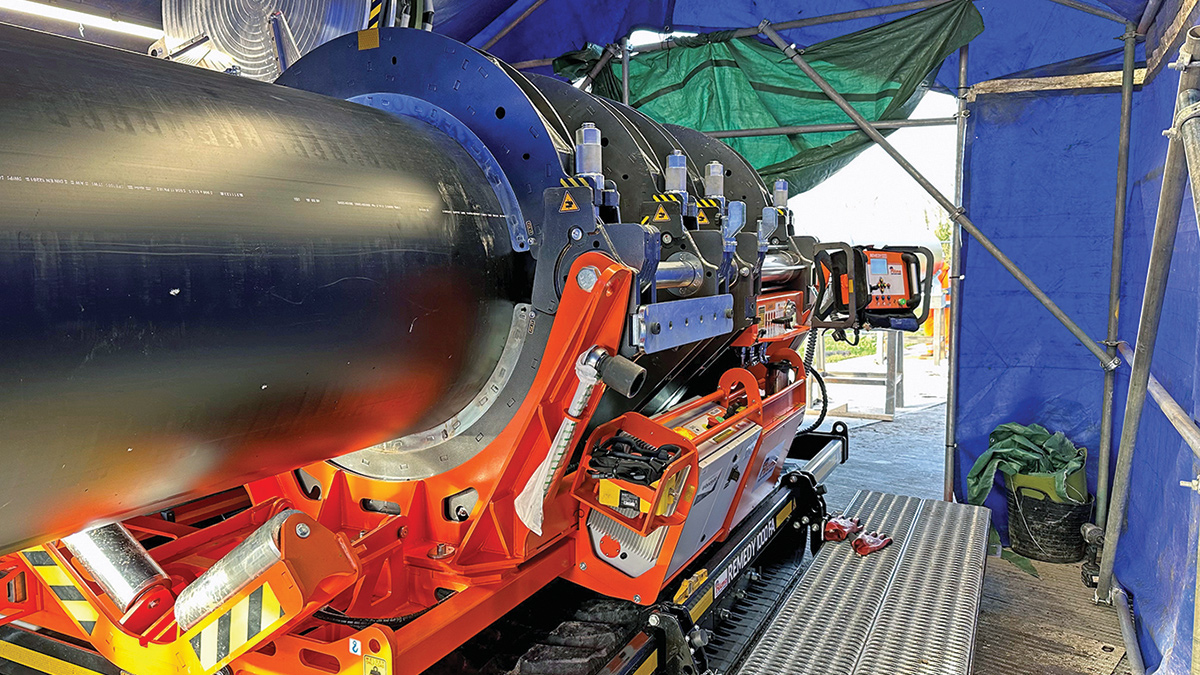
900mm diameter pipe welder – Courtesy of Galliford Try
Conclusion
Despite the intensive nature of this challenge, by running a continuous horizontal directional drilling operation over a 24/7 operating pattern, the works were completed on budget and ahead of the programme. There were no time delays, no environmental impacts to the blue flag beach (just 4m from the site), and any impacts to the Holiday Park were minimal.
South West Water have showcased this project through the media and LinkedIn focusing on the engineering challenges the team faced and promoting both construction and the wider environmental benefits of this scheme.
The team have produced a presentation given by Galliford Try’s team to over 250 employees nationally to share the best practice and learnings from this project across their entire business.
South West Water are extremely pleased with progress of these works to meet their commitments with the Environment Agency. Relationships with the Holiday Park management are extremely good, and the owners are grateful for the efforts the team and SWW have made to complete these works with minimal disruption to their business.
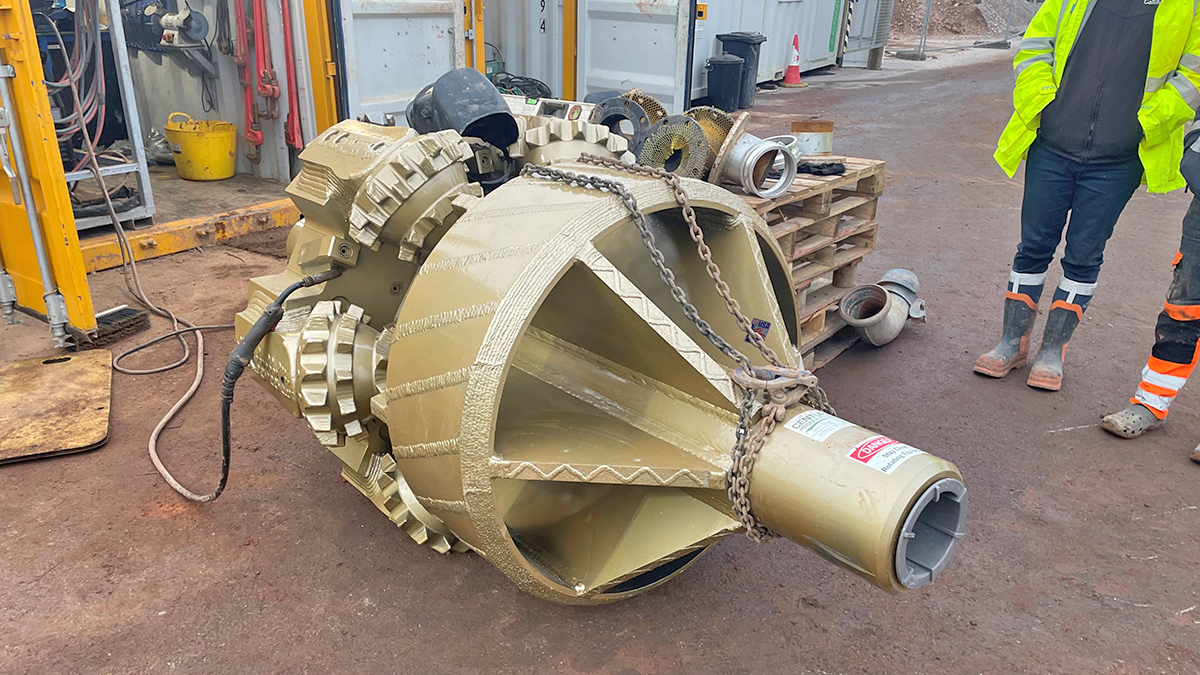
48" drill bit reamer - Courtesy of Galliford Try
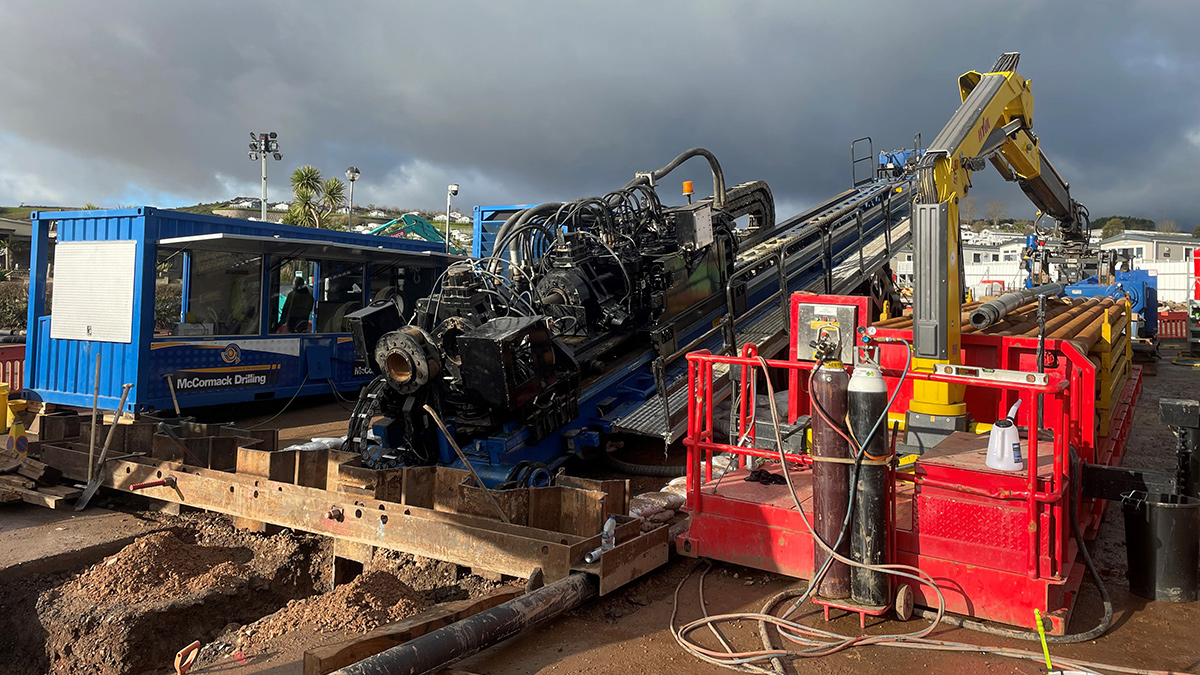
500 T drill rig and control cabin - Courtesy of Galliford Try
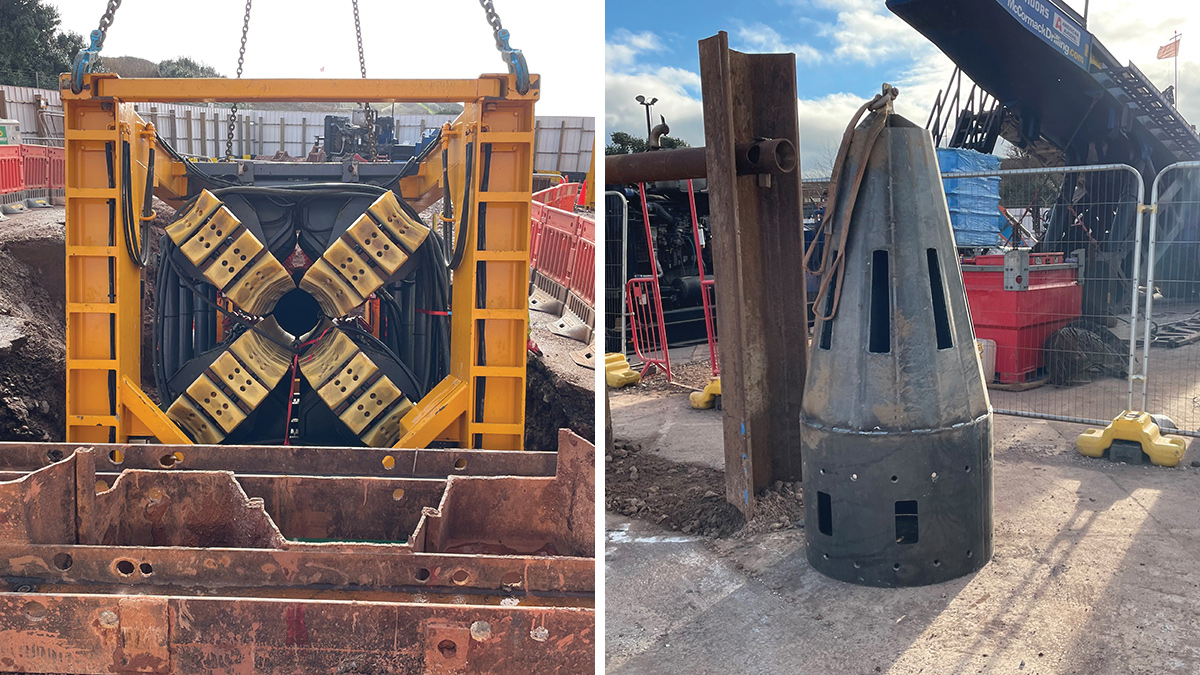
(left) Pipe pusher and (right) pushing head - Courtesy of Galliford Try