Glentworth Water Recycling Centre (2016)
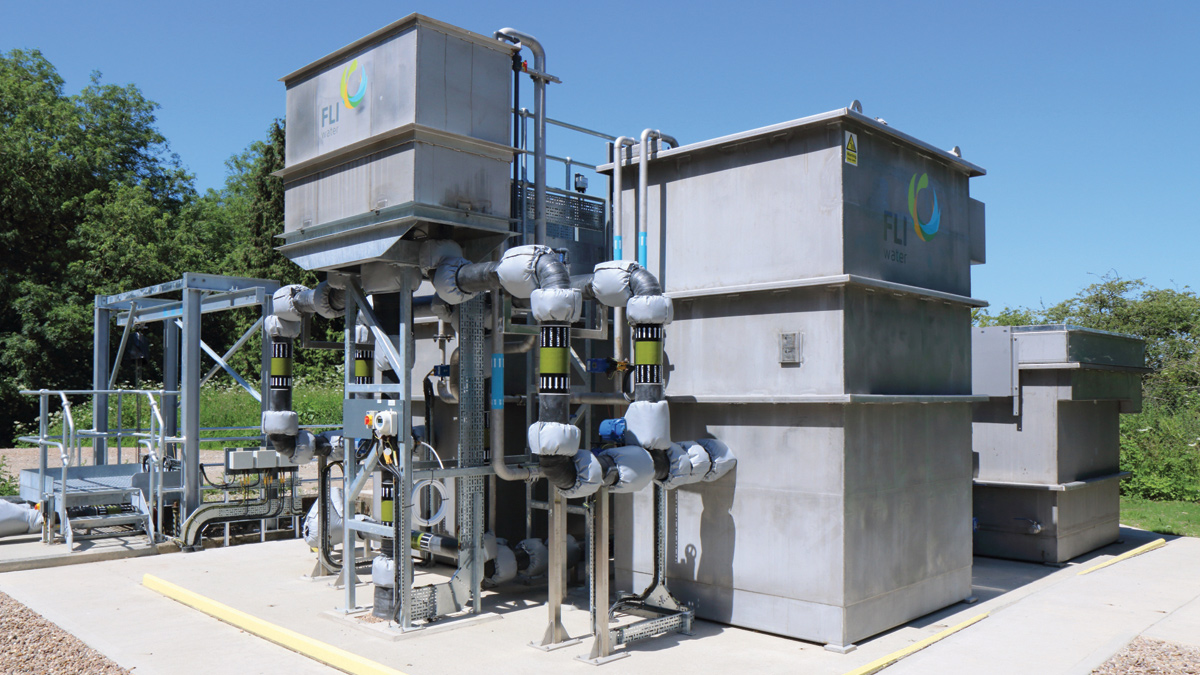
Tertiary treatment plant with dirty water pump station in background - Courtesy of FLI Water
The village of Glentworth is approximately 10 miles north of the city of Lincoln and one mile south-west of Caenby Corner. The water recycling centre (WRC) is located near the village in the West Lindsey district of Lincolnshire, and falls under the control of Anglian Water. Glentworth WRC serves a catchment area of 1250 PE and treats all flows from the surrounding villages of Fillingham, Glentworth, Harpswell and Hemswell. A section of sewer network 3.5km north of Glentworth WRC is owned by Severn Trent Water Company and includes four pumping stations: Hemswell Weldon Road, Hemswell Church, Hemswell Caravan Park and Harpswell Village. As part of AMP5, FLI Water was engaged to design, manufacture and install a new two-stage tertiary treatment plant at Glentworth.
The site
The work was carried out to ensure that the plant maintained works compliance of ammonia and suspended solids. To provide additional suspended solids removal, a temporary HSAF was installed at Glentworth a number of years ago. This unit was fed by a duty/standby arrangement of surface mounted Gorman Rupp pumps, which pumped flow from the pebble bed clarifier. Effluent from the HSAF solids filter was discharged downstream from the pebble bed clarifier to final effluent.
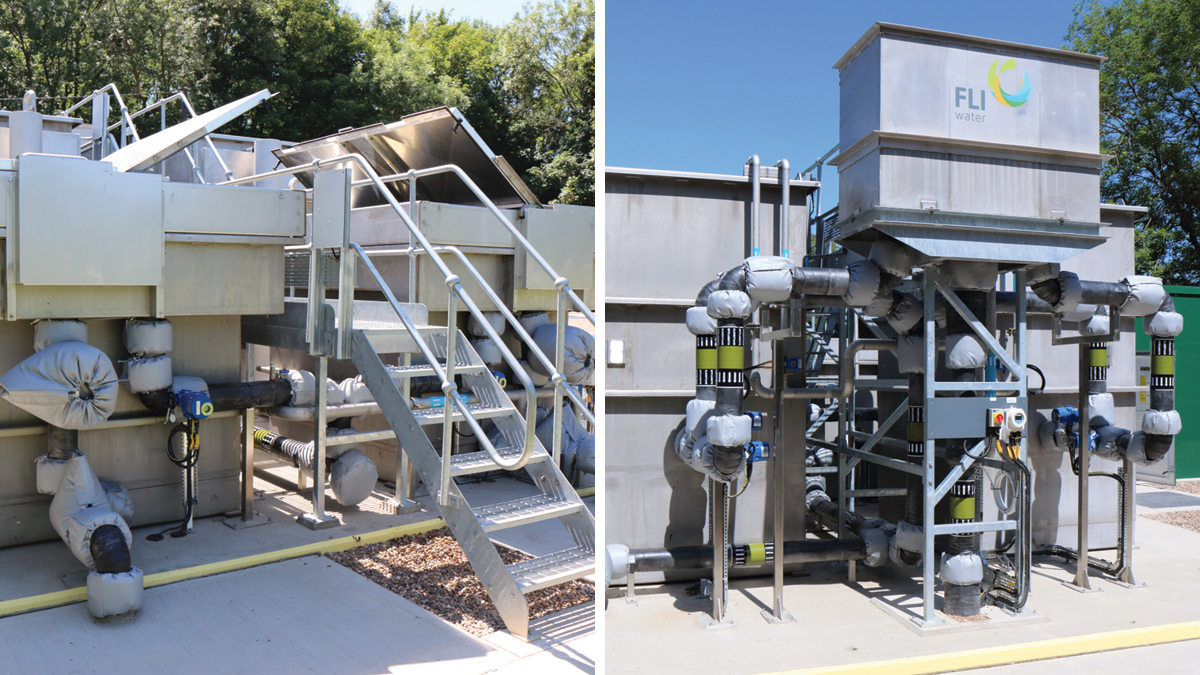
(left) Outlets with twin Filtabead treatment streams and (right) Flow Splitter and twin HSAF treatment streams – Courtesy of FLI Water
Dirty water produced from the routine automatic HSAF® cleaning cycle discharged into the existing return liquor sump, where it was pumped back for co-settlement in the primary tank.
Glentworth WRC was identified as a site which required environmental improvements to reduce BOD and ammonia, in order to deliver compliance with river water quality ecosystem (RE) targets. The scheme was identified to ensure no deterioration in the current classification as a result of increased volumes of discharge (historic), as required by the WFD.
The PR09 driver was flow compliance. It was proposed to change the DWF consent from 125 to 220m3/d and the discharge consent from 25/15/- mg/l to 25/8/5 mg/l TSS, BOD and NH3, in April 2015.
The 95%tile feed design concentrations were determined at 37.1/25.1/7.7 mg/l TSS, BOD and NH3.
The total scheme was valued at ~£900,000 and the contract was awarded in late 2014 with a prospective completion date of 31 March 2015. The contract was awarded in various packages and a design order was placed in October 2014. This was subsequently followed by an order for the process equipment in December 2014 and the installation contract – incorporating principal contractor duties – was awarded at the end of January 2015.
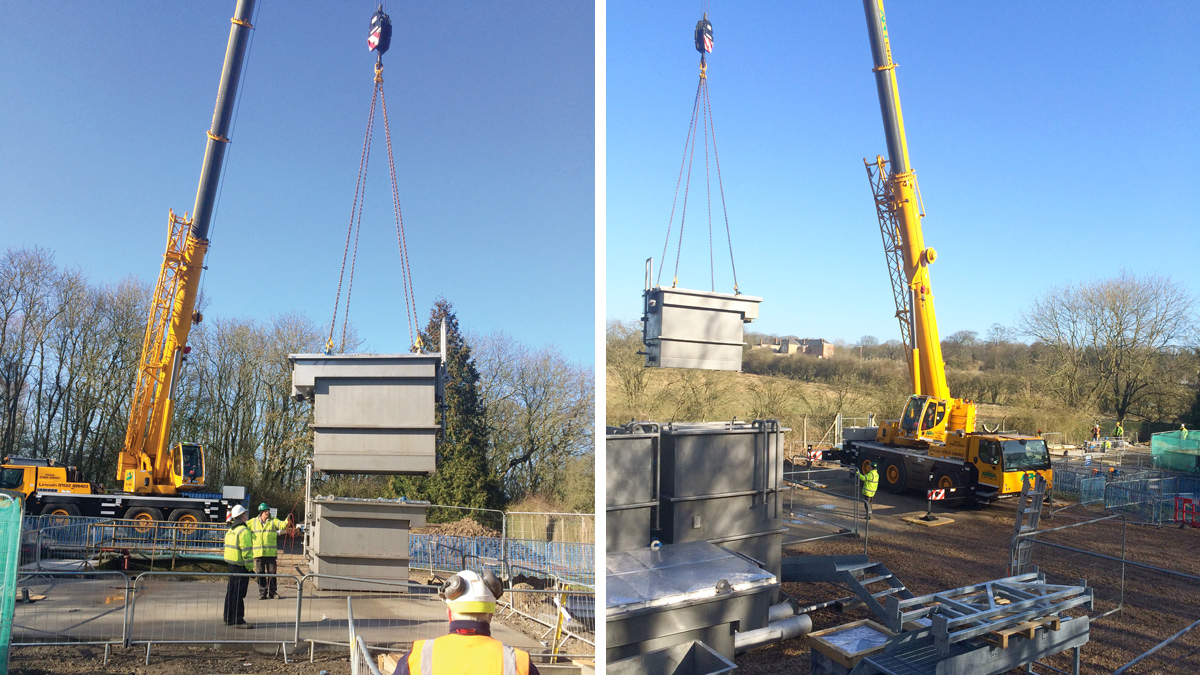
Installation, showing modular construction and off site build – Courtesy of FLI Water
Scope of work
After Risk and Value meetings, the option of a tertiary treatment solution was chosen to meet the new consent requirements. Due to delivery requirements for March 2015, FLI Water was selected to provide the tertiary treatment solution. This comprised of a twin-stream two-stage plant system with 2 (No.) HSAF M3 aerated units in parallel for ammonia removal, followed by 2 (No.) Filtabead M3 units in parallel for solids capture.
FLI Water’s scope of work on the project was as follows:
- Design, supply, install, testing and commissioning of all mechanical, electrical and civil aspects associated with the new works to be carried out at Glentworth WRC.
- Provision of a new feed pumping station, complete with variable speed submersible pumps and associated pipework.
- New two-way feed splitter tank feeding 2 (No.) FLI Water M3 stainless steel HSAFs with BMax® media, followed by 2 (No.) FLI Water M3 stainless steel Filtabead Tanks with Filtabead media. All units to be built off site, to reduce site programme and minimise on-site risks.
- A new dirty water pumping station, complete with submersible pumps and pipework to return to inlet works.
- Provision of a new surface mounted progressive cavity pump for the automated de-sludging of the existing humus tank.
- Associated equipment including air blowers, actuated valves, pipework and chambers.
- New Form 4 MCC, located in a new kiosk, to provide all power, control and telemetry for the tertiary plant.
- Access gantry with walkway and support structures for the tertiary treatment plant.
- Supply, installation and testing of all cables, meter boxes, switch boards and associated equipment, supplying of certification, liaison with ESB, and coordinate permanent connections off permanent ESB connections.
This contract was a flow compliance scheme. The completion date was linked to the site’s change in treatment consent, which was 31 March 2015. A number of factors delayed the immediate commencement of work on site – a combination of bad weather, the delayed contract award and site operation constraints. This resulted in what was already an extremely tight schedule becoming all but un-achievable.
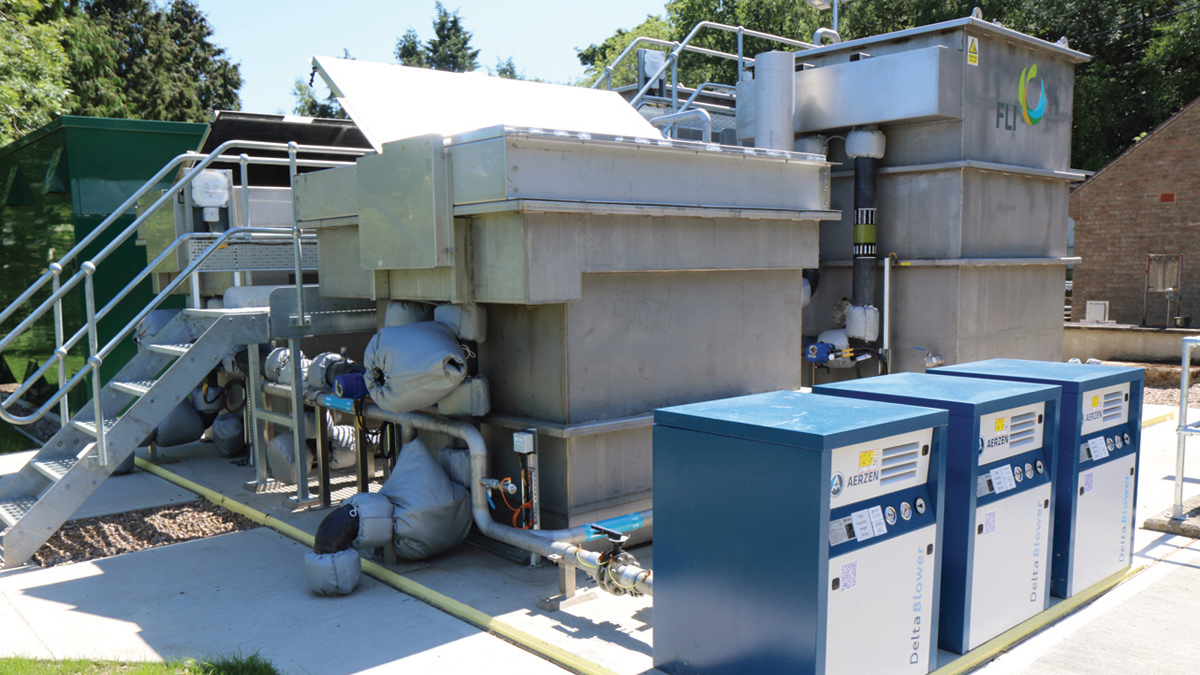
Tertiary treatment plant air blower units – Courtesy of FLI Water
Innovative thinking
With the timescales tight and the scope of work extensive, all parties were aware of the challenges that faced them over the next three months. During the project planning phase it became clear to FLI Water that even with good weather and everything going smoothly, the time remaining to get the plant fully built, operational and biologically seeded to meet the EA consent was too short.
FLI Water demonstrated innovative thinking during the Glentworth WRC scheme delivery. This project was one of the latter ones commissioned during AMP5. For various reasons a decision on the scheme was not finalised until January 2015, accompanied by a required completion and compliance date of 31 March of that year. The clients’ initial approach was to impose liquidated damages by means of tankering site flows for each day that exceeded the date that the scheme wasn’t completed. This was an arrangement that was not acceptable to either FLI or the client, so a plan for mitigating this needed to be put in place.
At this point, FLI Water’s own specialists reviewed the design of the new plant internally. Between the design and site delivery team, FLI challenged the issue programme, to see where time savings could be made to the schedule. When it was found no significant programme efficiencies could be made, the team had to look for alternative approaches.
As part of the solution, the design team revised the scheme design to incorporate the installation of a temporary treatment plant that could be installed alongside the new equipment. This enabled FLI to have the temporary treatment in place prior to the end of March 2015. Thus the client achieved its compliance output date and then subsequently agreed to an extension to the end date for completion of the scheme. This allowed the new plant to be installed, commissioned and tested offline, while the temporary plant ensured the works remained compliant.
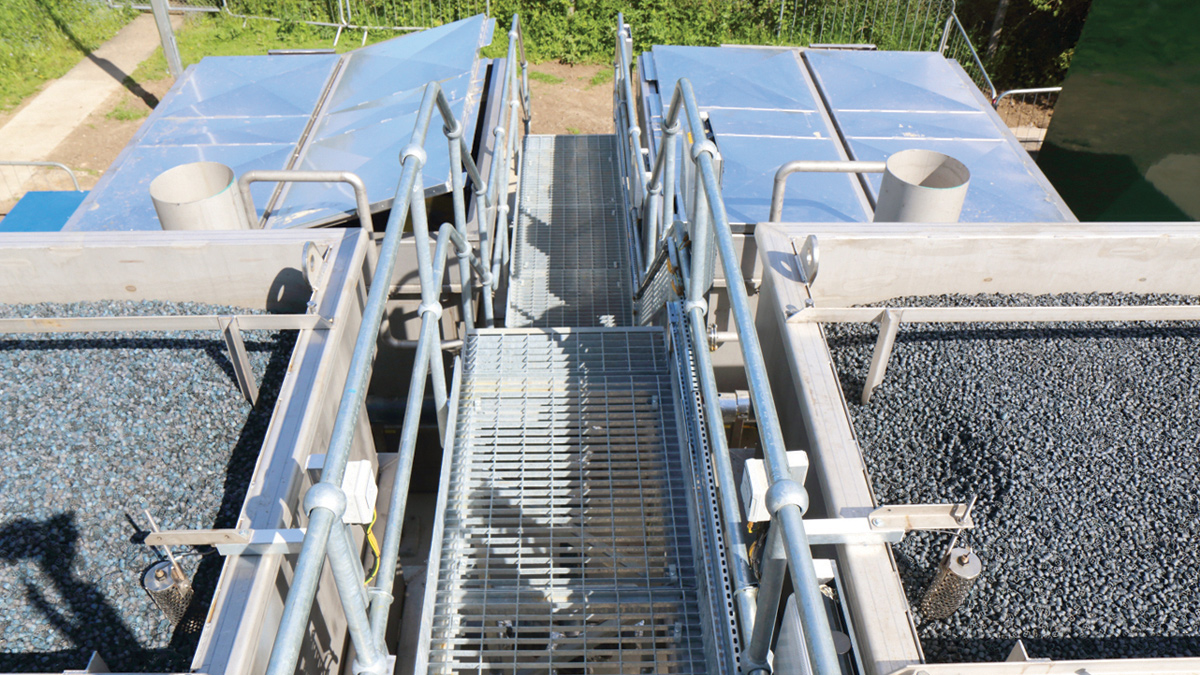
Surface of HSAF and Filtabead solids removal units – Courtesy FLI Water
A timely solution
When Anglian Water pushed harder to introduce a pain/gain element with liquidated damages being enforced should FLI Water not deliver the requirements, FLI Water suggested a plan that would meet the capital spend rules and the environmental consent by the deadline date of 31 March, but with minimal increase in cost to Anglian Water. Furthermore it would reduce risk to FLI Water and Anglian Water during the project build.
Firstly, FLI’s proposal was to install a temporary treatment plant (an FLI Water supplied and managed unit) in mid-February 2015. This facility would acclimatise with the effluent during the period prior to the consent change and then remove any peak loads during the building and commissioning phases of the project. In this way, it would take care of one of the delivery requirements, which stipulated that effluent compliance was to meet the new consent on 1 April 2015.
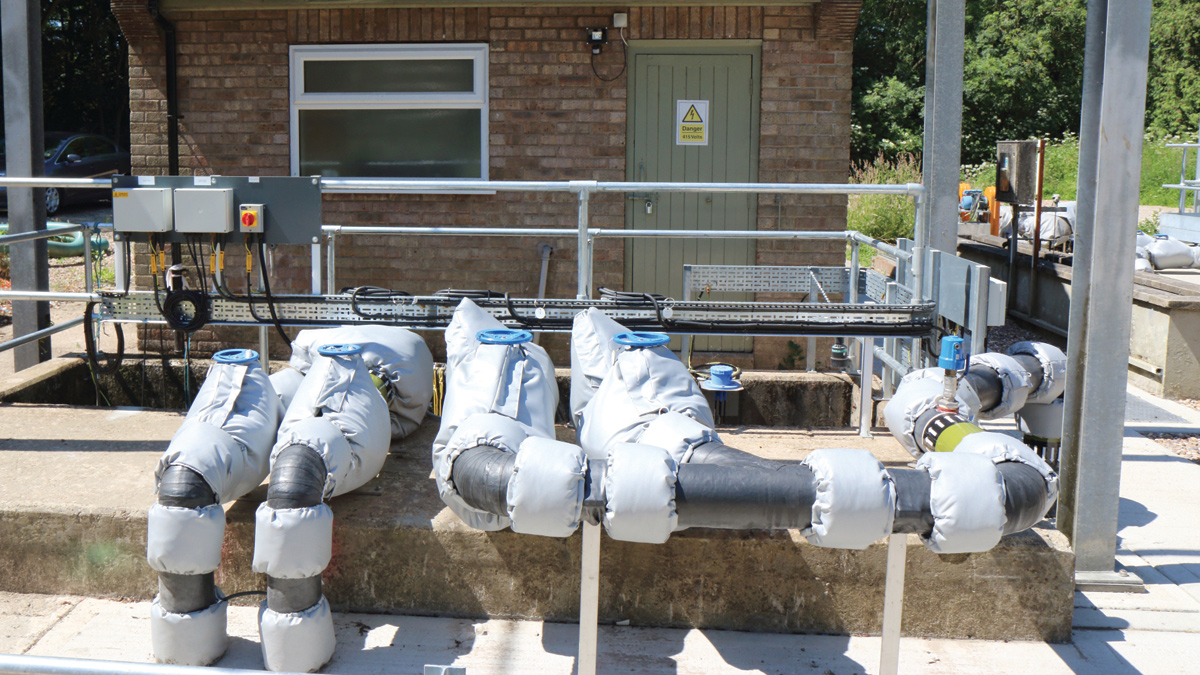
Feed and Recirculation pump station (reused) – Courtesy of FLI Water
Secondly, FLI Water undertook to build as much of the plant as was feasibly possible off site, reducing the impact of inclement weather and considerably benefitting safety compliance on the site. The benefits of off site construction also included improved efficiency, sustainability as a result of less machinery used and the finished product only needed to be transported to site, resulting in less disturbance to nearby residents during the construction phase.
The civil construction and electrical installation activities were carried out by subcontractors that have worked closely with FLI Water in the past. These included Bloom & Wake Electrical Contractors and Paktronic Engineering Company Ltd for the MCC and HMI. The mechanical installation and the process commissioning were carried out by FLI Water employed staff.
Anglian Water took on the responsibility of site mobilisation and gave assistance where possible in other areas. Ultimately during the project build phase, FLI Water had full control of the site.
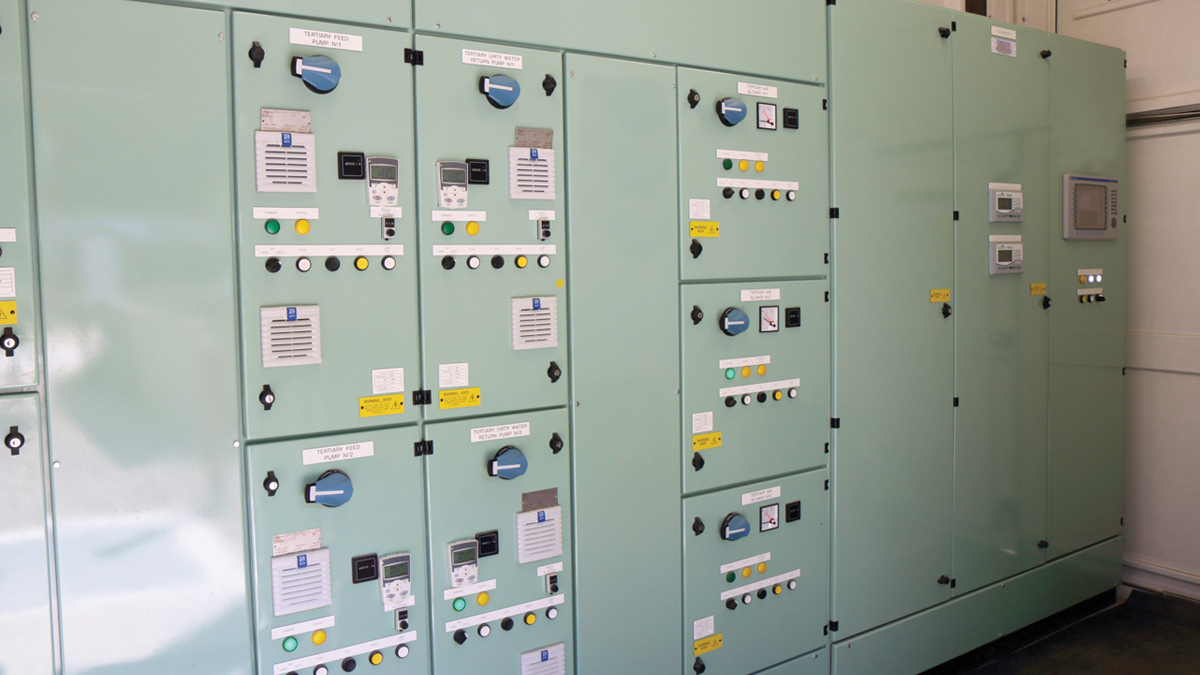
MCC from Paktronic Engineering Company Ltd – Courtesy of FLI Water
Thirdly, FLI Water identified during the Risk and Value stage that there was scope to reuse some existing site assets. Proposals for the opportunities were well received by the project team and resulted in the reuse of a redundant recirculation pumping station for the tertiary feed pumping station and the pebble bed clarifier was reused as the dirty water pumping station.
These changes resulted in a three to four week reduction in project programme and a saving of £80,000, as well as improving site safety by removing the requirement for deep excavations.
On the installation of the tertiary treatment plant, FLI Water received good feedback on the scheme from the @One Alliance/Anglian Water Project Delivery Manager Jamie Edwards, who commented:
“It was an extremely positive project, even more so considering the short notice with which FLI was engaged. Of particular worthy mention was the thought that had been given to commissioning the plant in the detail design, which meant that commissioning was extremely smooth and didn’t add unnecessary costs.”
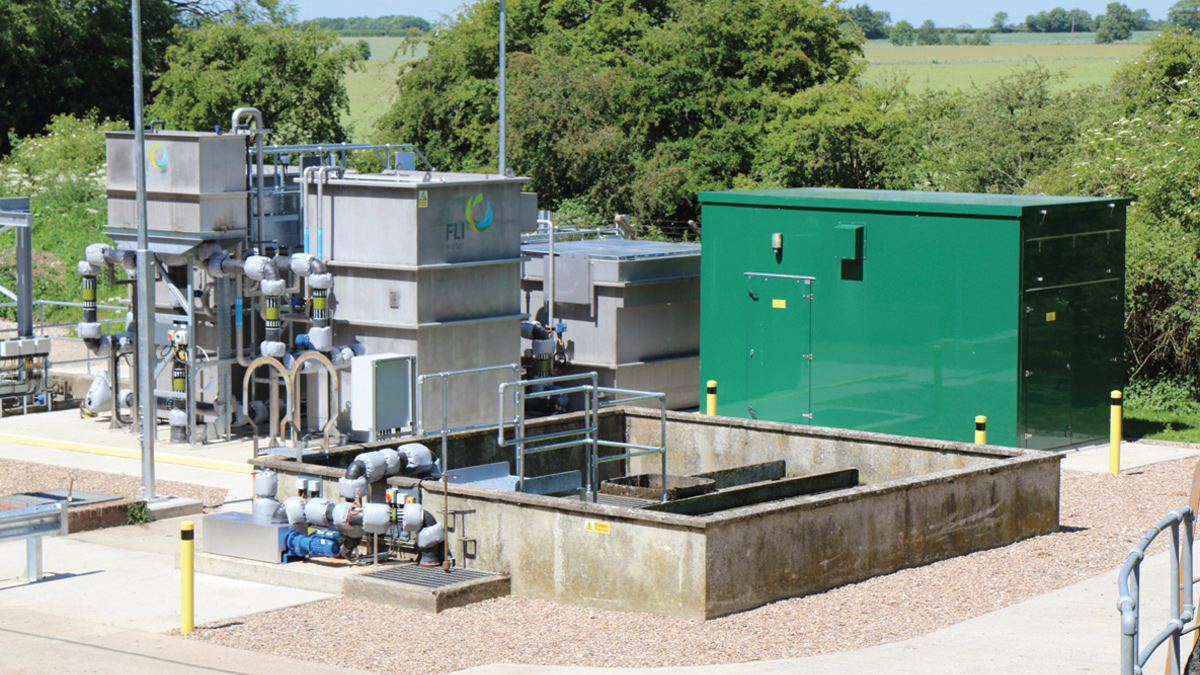
Tertiary treatment plant MCC kiosk – Courtesy of FLI Water
Conclusion
The Glentworth Water Recycling Centre project was completed on time and on budget. Having a high degree of control over the project allowed FLI Water to achieve the delivery of the new plant on site with the ability to take full flow by the end of March. This allowed Anglian Water to meet its capital rules and environmental consent by 31 March 2015 through the use of temporary treatment apparatus to maintain compliance.
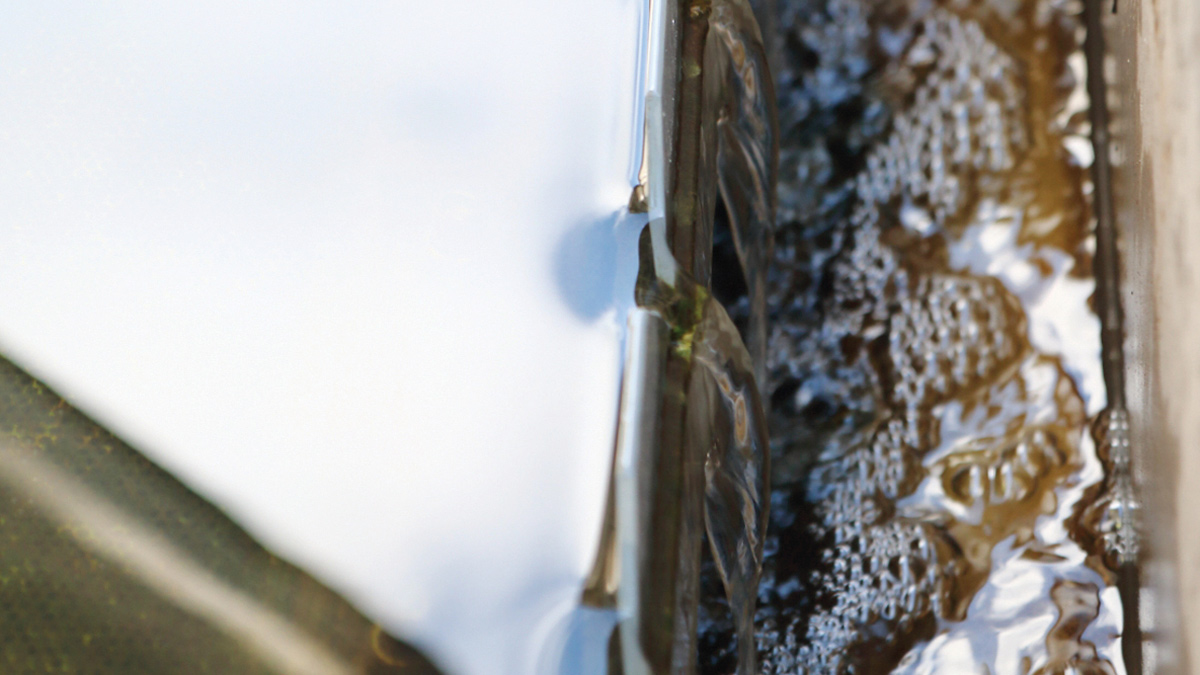
Final effluent – Courtesy of FLI Water
Post-March, the remainder of the project was successfully completed and met all the targets set by Anglian Water and importantly ensuring that no liquidated damages applied to FLI Water. This project was a good example of where collaborative working, innovative thinking and a different approach to delivery resulted in a win-win for all parties.