Knostrop STW (2023)
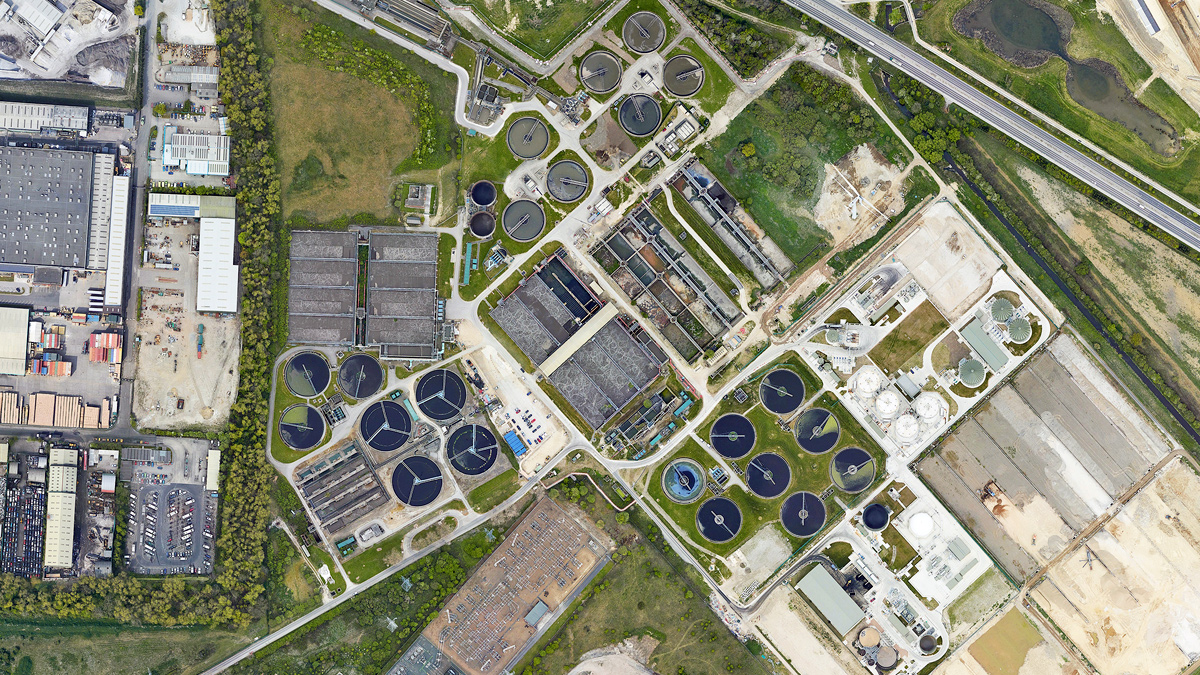
Overview of Knostrop STW - Courtesy of Yorkshire Water and Ward & Burke
Knostrop Sewage Treatment Works (STW) is Yorkshire Water’s largest wastewater treatment site, serving a population equivalent of 990,000 and a full flow to treatment (FFT) of 5600 l/s. The WINEP Programme requires Yorkshire Water (YW) to achieve compliance with the new Total Phosphorus and Total Iron permit levels at 80 wastewater treatment works, including Knostrop. YW has adopted the concept of converting the existing ASP treatment works to remove the phosphorus using bacteria. This new AMP7 project underwent Partnership for Yorkshire’s (P4Y) Project Lifecycle and the biological removal concept was reviewed and selected by the collaborative project team comprising Yorkshire Water, Stantec UK and Ward & Burke. The resulting solution is to introduce enhanced biological phosphorus removal (EBPR) processes into the biological treatment stage, with a tertiary solids removal (TSR) plant built to treat the final effluent. The £60m upgrade will comply to the new Water Framework Directive of 0.4 mg/l Total Phosphorus and 4 mg/l Total Iron consent.
Existing works
The existing site processes consist of two inlet works (inlet screens, grit removal, fine screens) and two sets of primary settlement tanks (PSTs). From here, flows combine into a distribution chamber that diverts the flow to three activated sludge plants (ASPs). ASP 1 and 2 have a shared selector tank while ASP3 has a dedicated selector tank. There is a pre-anoxic zone before each lane in all the ASPs. ASP1 is surface aerated, while ASPs 2 and 3 are driven by fine bubble diffusers.
Following this biological treatment, the flow splits into seven final settlement tanks (FSTs) for ASPs 1 and 2, and eight dedicated FSTs for ASP3. The treated water then flows to the river, while the sludge is recycled into two independent return activated sludge (RAS) streams, one for ASPs 1 and 2, and one for ASP3. This RAS flow is pumped back to each selector tank, while any surplus activated sludge (SAS) is sent to sludge holding tanks.
In 2018 a new sludge treatment facility incorporating anaerobic digestion (AD) was commissioned at Knostrop, which treats both the indigenous primary sludge and the surplus activated sludge (SAS) as well as imported sludges from the smaller wastewater treatment works in the Leeds and Tadcaster catchment area. This facility has a capacity to treat 90 tDS/day and generates 2660 kW energy from the biogas. A gas to grid scheme is currently under design within Yorkshire Water.
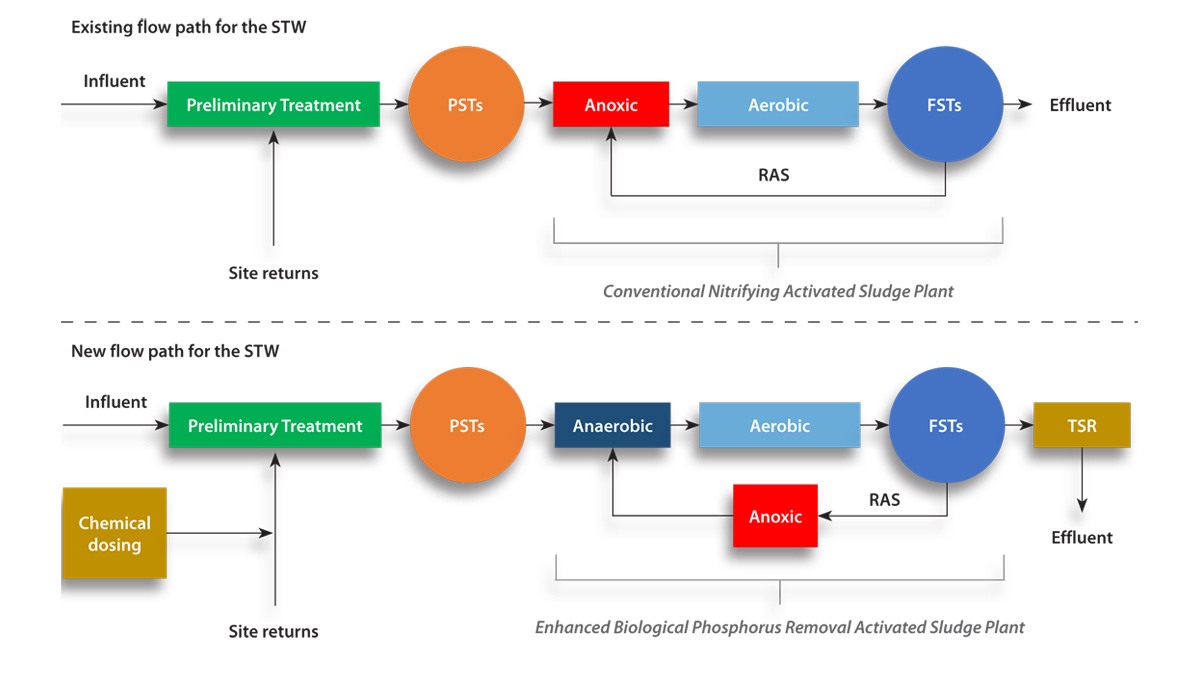
An overview of the changes to the process flow path
Enhanced biological phosphorus removal (EBPR) process
The EBPR process relies on the selection of polyphosphate accumulating organisms (PAOs) to take up large amounts of phosphorus from wastewater which reduces the levels of phosphorus in the effluent. The existing nitrifying ASPs’ biological environment needs to be reconfigured to increase the PAOs population, and for this scheme a modified Johannesburg configuration is chosen as the EBPR design.
This design introduces an anoxic tank for the RAS flow before it is re-introduced and mixed with the incoming flow into the selector tanks. This existing selector tank will become an anaerobic tank, with the existing pre-anoxic zones becoming an extension of this anaerobic tank. New RAS anoxic tanks will be built to facilitate this. Once the bacteria have established, the theoretical biological phosphorus removal rate can be twice as high as in a conventional nitrifying activated sludge plant.
Tertiary solids removal (TSR) process
The TSR chosen is a high-rate ballasted clarification design utilising the CoMag® technology designed by Evoqua Water Technologies. This is similar to conventional chemical phosphorus removal, where ferric sulphate is mixed into the wastewater to bind to the soluble phosphorus to form solid precipitates ready for solids separation. In CoMag®, ferric sulphate combines with the wastewater and an inert iron ore called magnetite and a polymer are then mixed in to bind to the flocs. This acts as a ballast, which causes high-rate settlement. This process is key for large treatment works due to the reduced area required for the settlement process.
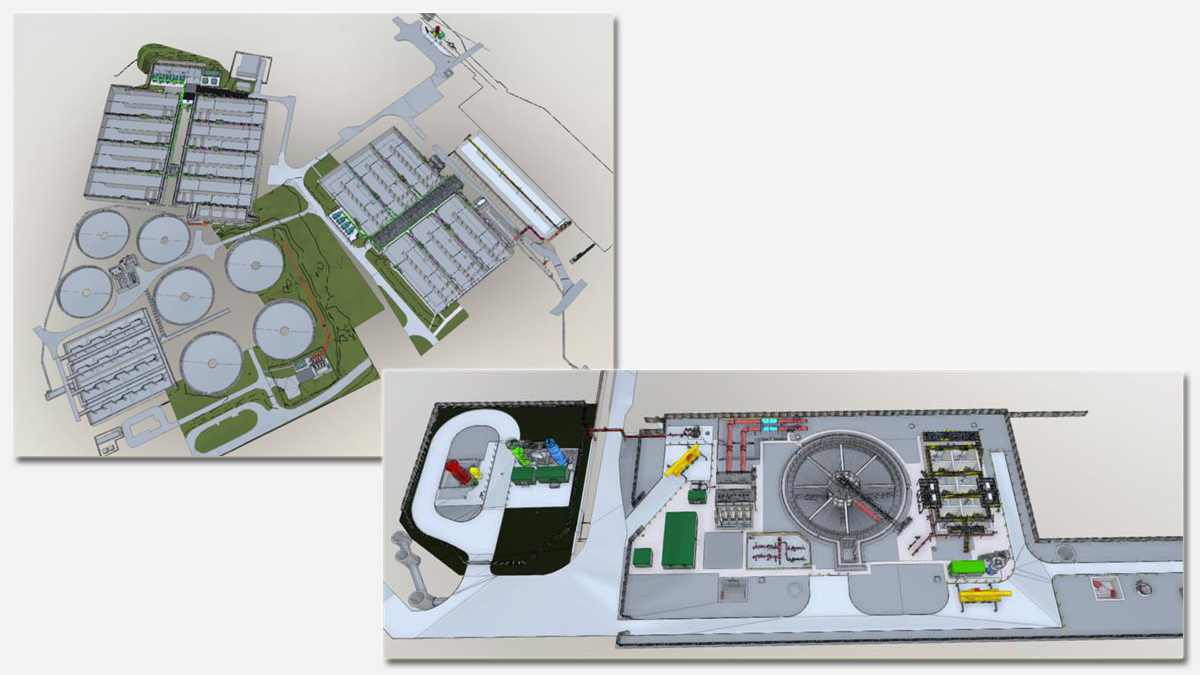
(left) 3D model image of the EBPR 1 & 2 site layout and (right) 3D model image of the future TSR site layout
To put this into context, fifteen 40m FSTs are existing to act as the final settlement for the sites full flow to treatment, however 75% of this flow will be able to pass through one 32m high-rate clarifier designed for the CoMag® technology. The required surface area to treat 75% of the flow in a traditional FST is therefore 14,136m2 versus the 804m2 required for the high-rate ballasted clarifier (ie. 17.5 times more efficient). The treated water will then weir over and discharge to the river, while the sludge is recovered and passed through a magnetic drum recovery unit, and the magnetite is recycled.
An additional ferric sulphate dosing system will also be installed and dosed upon the filtrate returns from the AD plant. This is prior to the returns discharging into the high-level PSTs.
Using this design, EBPR has the potential to reduce the Total Phosphorus down in the wastewater to 0.4 mg/l. The TSR will then remove the Total Phosphorus down to <0.4 mg/l. Introducing EBPR prior to a TSR for phosphorus removal greatly reduces the chemical cost used in the TSR.
Knostrop STW: Supply chain – key participants
- Outline design: Stantec UK
- Detailed design & delivery contractor: Ward & Burke
- Design assurance: Yorkshire Water
- Design assistance & hazard study facilitators: Sweco
- COMAG® technology: Evoqua Water Technologies (Xylem Water Solutions)
- Electrical installation: Circle Control & Design Systems
- Transformers & HV works: Integrated Utility Services
- MCCs & systems integration: Saftronics
- Piling/grouting: Van Elle
- Precast concrete: FLI Precast Solutions
- Access metalwork: Galliford Try Fabrications
- Coated steel pipework: Freeflow Pipesystems
- Stainless steel pipework: Franklyn Yates Engineering
- Ductile iron pipework: Saint Gobain PAM UK
- Blowers & mixers: Sulzer Pumps Wastewater Ltd
- Ferric & polymer dosing: NPS Engineering Group
- Pumps: Xylem Water Solutions
- Diffusers: SSI Aeration
- Kiosks: Morgan Marine
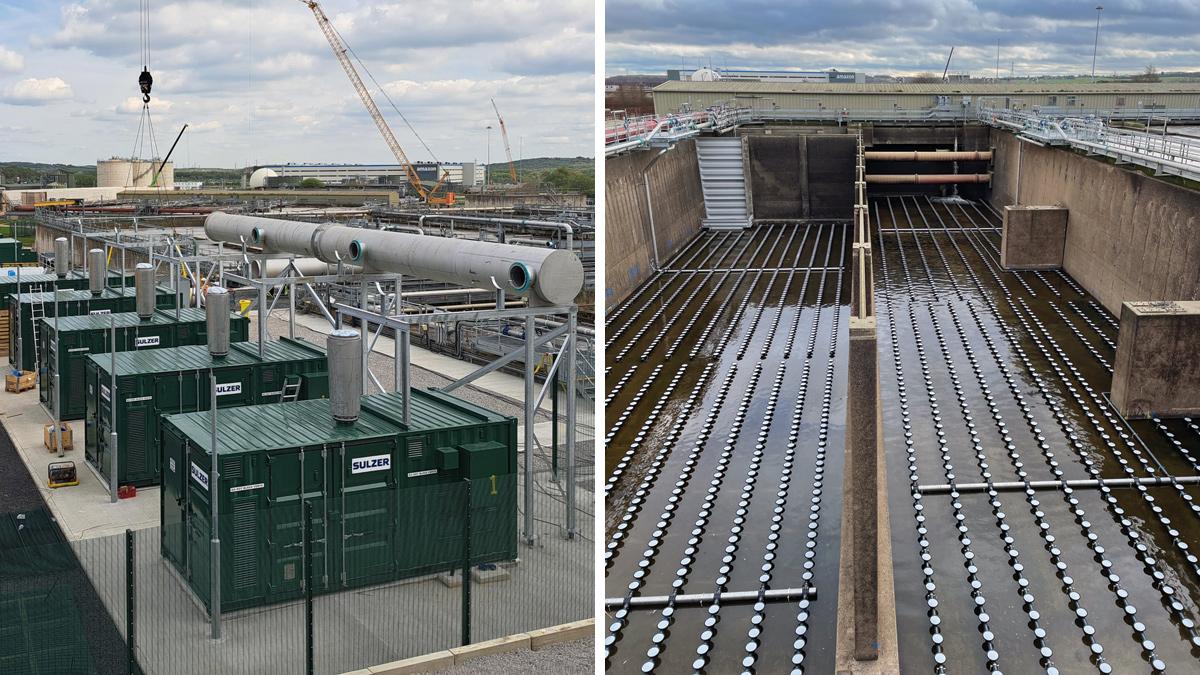
(left) Progress of the new ASP2 blower slab, MCC and transformer area and (right) installation of the diffusers in the new activated sludge lane – Courtesy of Yorkshire Water and Ward & Burke
Scope of works
The existing nitrifying activated sludge plants (ASPs 2 and 3) will be converted to two EBPR ASPs while ASP1 will be taken off-line. A full aeration upgrade is being undertaken for both ASP2 and ASP3 to increase the capacity of the site to cope with increased loading up to 2035. This upgrade includes 9” disc diffusers from SSI Aeration, a new control system with four control valves and four dissolved oxygen probes per ASP lane, new aeration feed pipework, new Sulzer Turbo blowers and new monitoring instrumentation. The turbo blowers will be the first of their kind for Yorkshire Water and will offer increased capacity and efficiency compared to the standard rotary lobe type blowers currently installed.
Due to the requirement to maintain the existing process, this upgrade has been designed to only require one of the lanes out of service at any one time, where the diffusers and valves are installed and the new lane feed pipework ties into the existing control valve. Once every lane has been upgraded, the feed pipework is tied into a commissioning valve to enable an aeration changeover from the old blowers and control system to the new system. Ward & Burke have worked closely with Yorkshire Water’s Engineering Design Team and the Knostrop Operations Team to plan this phase of work so there is minimal risk to the process.
ASP1 will be converted to become ASP2’s new RAS anoxic tank. To facilitate this, ASP1 will be taken off-line, the surface aerators removed, and submersible mixers added. The existing control system will be fully decommissioned, and a new control system installed. In addition, a new pumping station must be built to pump 2500 l/s of RAS flow back up to ASP2’s selector tank. To incorporate these new additions into the new system, live tie-ins will have to be made to divert the RAS flow into the newly converted tank. Under pressure hot taps have been selected for the RAS tie ins as this method allows the existing process to continue unaffected while the installation of the new pipework occurs, eliminating the need for large over pumping operations.
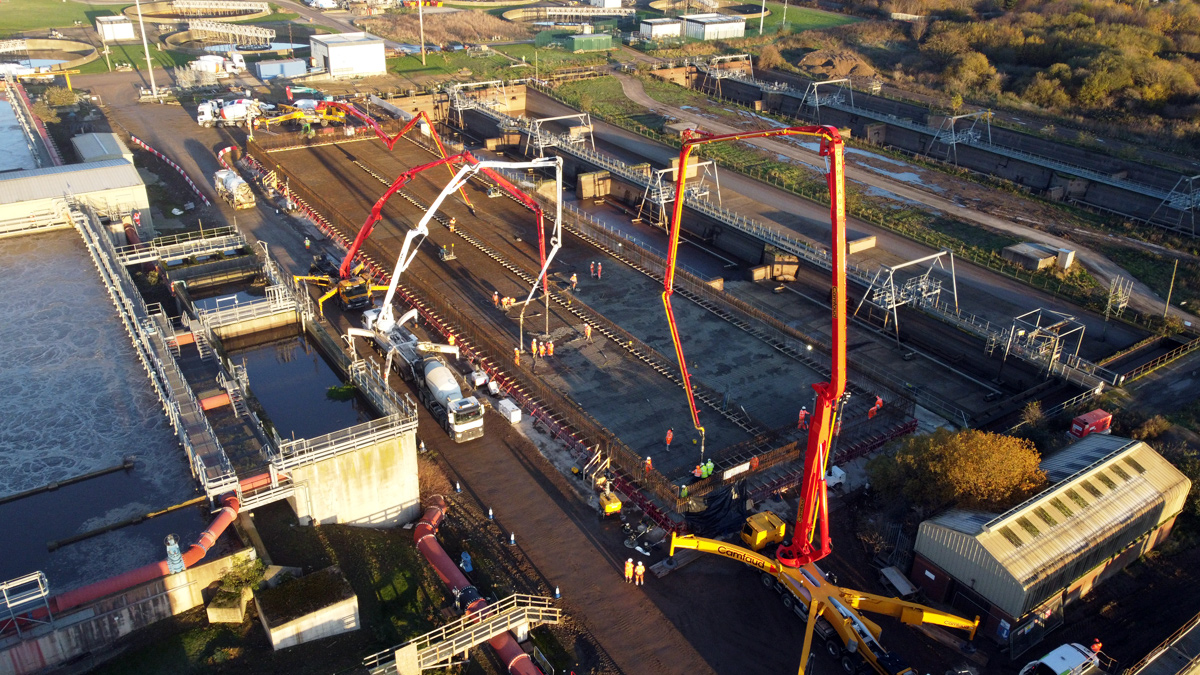
Base pour of the new RAS anoxic tank for EBPR2 – Courtesy of Yorkshire Water and Ward & Burke
Similar to ASP2, ASP3 will require a new RAS anoxic tank. This 14,000m3 tank is built on the foundations of old decommissioned sludge beds and both grouting and CFA piling were required in this area due to the presence of coal seams.
The flow from the existing RAS pumping station will be diverted to this new anoxic tank, where the tank will then discharge back into the anaerobic zone of ASP3. Again, an under-pressure hot tap will be used for the RAS tie-in, and a limpet dam used to discharge into the anaerobic zone.
With the addition of these new anoxic tanks, the biological stage of Knostrop STW will be changed to two EBPR ASPs. Commissioning of this system is forecast for November 2023 (ASP3) and February 2024 (ASP2), and a predicted 6-month seeding/climatisation period is assumed before the POAs have established.
The new Total Phosphorus consent is 0.4mg/l which will require a further solid associated phosphorus removal after the exiting FSTs. The final effluent will be diverted into a tertiary solids removal (TSR) plant, where a new pumping station will lift 75% of the sites FFT into a new reception chamber.
The wastewater then flows down duty/duty pipelines through in-line mixers, where the ferric sulphate is dosed prior to a reaction tank. The reaction tank is split into two streams, each with four tanks connected by under and overflow baffle walls. Submersible mixers enable the coagulation of the phosphate with the ferric sulphate, while further dosing of magnetite and then polymer occur in tanks 3 and 4 of the reaction tank to create the ballasted particles.

Construction of the new RAS anoxic tank for EBPR2 – Courtesy of Yorkshire Water and Ward & Burke
The flow then passes through a 32m diameter clarifier, complete with a fixed bridge and sludge scraper system. The clarifier is built of precast concrete panels to improve construction time.
A return chamber brings the wastewater back into the original final effluent line, and a new final effluent sampling chamber will be built downstream of this. Within the TSR, a sludge recycle system will be installed, along with a sludge return pumping station which will send the waste sludge back to the high-level PSTs.
Ferric sulphate, polymer and magnetite dosing systems will be designed and built off-site and then installed and commissioned, and a new control system will be installed for the entire TSR. The completion of this TSR is predicted for October 2024.
Progress
Currently the scheme is 1 year into construction works. At the time of writing (April 2023), the aeration upgrade of ASP2 has been completed ahead of schedule and the new control system is being commissioned. Aeration changeover to the new blowers is forecast for June 2023. The new RAS pumping station concrete structure has been constructed, and the pipework is currently being installed.
ASP1 is still functioning as a surface aerated ASP and is planned to be taken off-line in July. Once this has been upgraded and the RAS tie-ins completed the changeover to EBPR can occur, forecasted January 2024. ASP3s aeration upgrade is 90% complete. The new RAS anoxic tank for ASP3 is currently under construction, with the concrete walls cast and the access metalwork under fabrication. ASP3s EBPR conversion is currently planned early November 2023.
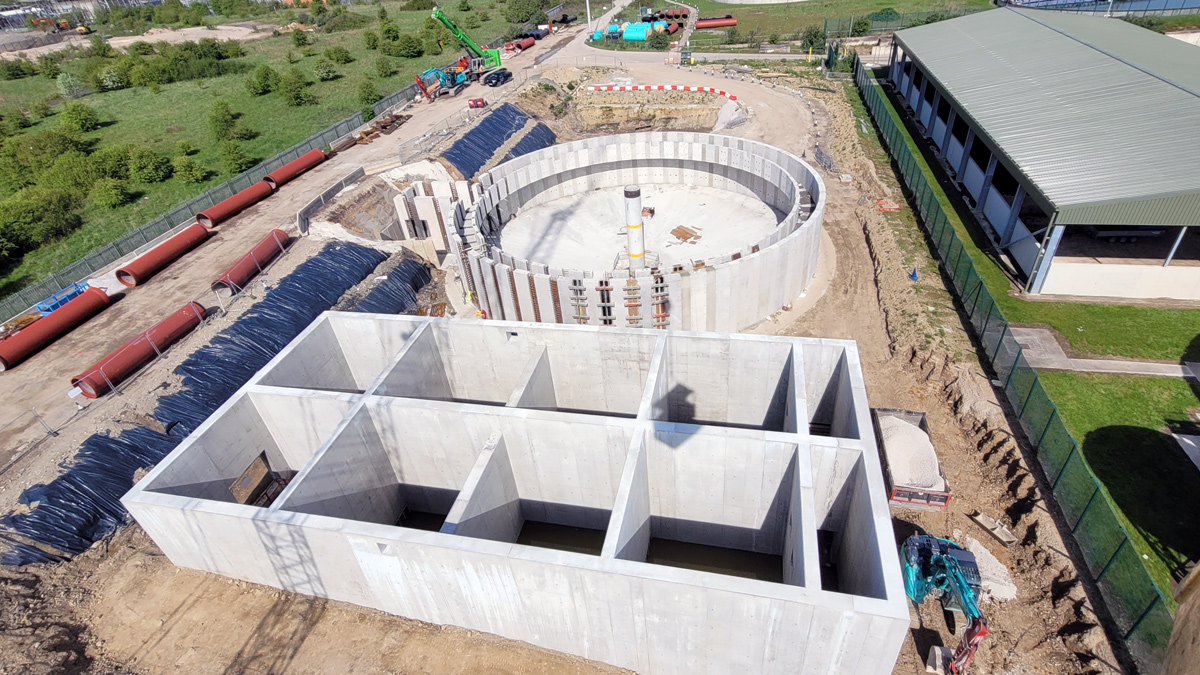
Progress of the new tertiary solids removal area (April 2023) – Courtesy of Yorkshire Water and Ward & Burke
The TSR is still under civil construction, with the reaction tank and clarifier concrete works completed, and the new lift pumping station and reception chamber under construction. Pipework, electrical ducting, and surface drainage is also ongoing in this area. The ferric sulphate, polymer and magnetite storage and transfer silos are currently under fabrication off-site.
The scheme has a targeted beneficial completion date of October 2024. This is when the site will be meeting the Total Phosphorus and Total Iron consent levels via use of the TSR, with both ASPs changed over to the EBPR configuration.